Supere los desafíos actuales del mecanizado de largo alcance
Varias tendencias actuales en la fabricación aumentan la dificultad de crear orificios de precisión y realizar operaciones de torneado con herramientas de longitud extendida. La demanda de tolerancias más estrictas y repetibilidad infalible crece continuamente. Los nuevos materiales de piezas de trabajo de alto rendimiento son más difíciles de mecanizar, lo que aumenta la tensión dentro del sistema de mecanizado. Para ahorrar tiempo y dinero, los fabricantes están consolidando varias piezas en piezas de trabajo monolíticas únicas que requieren mecanizado de orificios profundos y torneado de componentes complejos en máquinas herramienta multitarea.
Los fabricantes que buscan superar estos desafíos deben estudiar todos los elementos de sus sistemas de mecanizado y aplicar técnicas y herramientas que aseguren el éxito. Entre los elementos clave se encuentran la estabilidad de la máquina, la sujeción de la herramienta, la sujeción de la pieza de trabajo y la geometría de la herramienta de corte. En general, las fijaciones sólidas, las herramientas rígidas y la aplicación cuidadosa de las herramientas constituyen la base básica para procesos de mandrinado y torneado de largo alcance precisos y productivos.
Los productores de petróleo y gas, la generación de energía y los componentes aeroespaciales son los principales candidatos para herramientas y técnicas actualizadas porque se ocupan regularmente de piezas grandes y complejas con características que requieren el uso de herramientas de longitud extendida. Muchas de las piezas están hechas de aleaciones resistentes que son difíciles de mecanizar y, por lo tanto, producen fuerzas de corte altas que generan vibraciones. En general, casi cualquier fabricante puede beneficiarse de la mejora de la productividad y la reducción de costos en las operaciones de mandrinado de largo alcance.
FLEXIÓN Y VIBRACIÓN
La perforación profunda se distingue de otras operaciones de corte en que el filo opera en la perforación a una distancia extendida de la conexión a la máquina. Las operaciones de torneado interno de largo alcance presentan condiciones similares, y tanto estas operaciones de mandrinado como de torneado pueden involucrar orificios con cortes interrumpidos, como es el caso de piezas de trabajo como carcasas de bombas o compresores. La cantidad de voladizo resultante de la herramienta depende de la profundidad del orificio y puede resultar en la deflexión de la barra de mandrinar o de la herramienta de torneado de longitud extendida.
La deflexión magnifica las fuerzas cambiantes en un proceso de corte y puede causar vibraciones y vibraciones que degradan la calidad de la superficie de la pieza, desgastan o rompen rápidamente las herramientas de corte y dañan los componentes de la máquina herramienta, como los husillos, y provocan la necesidad de reparaciones costosas y largos períodos de inactividad. Las fuerzas variables son el resultado de los desequilibrios de los componentes de la máquina, la falta de rigidez del sistema o la vibración simpática de los elementos del sistema de mecanizado. Las presiones de corte también cambian a medida que la herramienta se carga y descarga periódicamente mientras se forman y rompen las virutas. Los efectos negativos de las vibraciones del mecanizado incluyen un acabado superficial deficiente, dimensiones de orificio inexactas, desgaste rápido de la herramienta, tasas de material reducidas, mayor costo de producción y daños en los portaherramientas y las máquinas herramienta.
RIGIDEZ DE LA MÁQUINA Y FIJACIÓN DE LA PIEZA
El enfoque básico para controlar la vibración en las operaciones de mecanizado implica maximizar la rigidez de los elementos del sistema de mecanizado. Para restringir el movimiento no deseado, una máquina herramienta debe construirse con elementos estructurales rígidos y pesados reforzados con hormigón u otro material que absorba las vibraciones. Los cojinetes y bujes de la máquina deben estar apretados y sólidos.
Las piezas de trabajo deben ubicarse con precisión y sujetarse de manera segura dentro de la máquina herramienta. Los accesorios deben diseñarse teniendo en cuenta la simplicidad y la rigidez como preocupaciones principales, y las abrazaderas deben ubicarse lo más cerca posible de las operaciones de corte. Desde la perspectiva de la pieza de trabajo, las piezas de paredes delgadas o las piezas soldadas y aquellas con secciones sin soporte son propensas a sufrir vibraciones cuando se mecanizan. Las piezas se pueden rediseñar para mejorar la rigidez, pero dichos cambios de diseño pueden agregar peso y comprometer el rendimiento del producto mecanizado.
PORTA HERRAMIENTAS
Para maximizar la rigidez, una barra de mandrinado o barra de torneado debe ser lo más corta posible pero lo suficientemente larga para mecanizar toda la longitud del orificio o componente. El diámetro de la barra de mandrinar debe ser el mayor posible que se ajuste al orificio y aún permita la evacuación eficiente de las virutas cortadas.
A medida que se forman y rompen las virutas, las fuerzas de corte aumentan y disminuyen. Las variaciones en la fuerza se convierten en una fuente adicional de vibración que puede interactuar en simpatía con el modo natural de vibración del portaherramientas o de la máquina y volverse autosuficiente o incluso aumentar. Otras fuentes de tales vibraciones incluyen herramientas gastadas o aquellas que no realizan un pase lo suficientemente profundo. Estos provocan inestabilidad en el proceso o resonancia que también se sincroniza con la frecuencia natural del husillo de una máquina o la herramienta para generar vibraciones no deseadas.
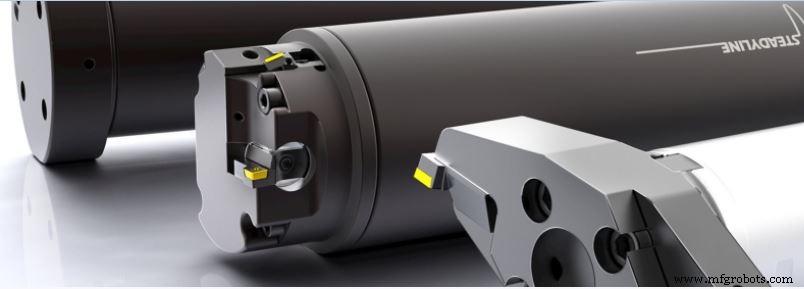
Una barra de mandrinar larga o un voladizo de barra de torneado pueden provocar vibraciones en un sistema de mecanizado. El enfoque básico para el control de vibraciones incluye el uso de herramientas cortas y rígidas. Cuanto mayor sea la relación entre la longitud de la barra y el diámetro, mayor será la probabilidad de que se produzcan vibraciones.
Diferentes materiales de barra proporcionan un comportamiento de vibración diferente. Las barras de acero generalmente son resistentes a las vibraciones hasta una relación de 4:1 entre la longitud y el diámetro de la barra (L/D). Las barras de metal pesado hechas de aleaciones de tungsteno son más densas que el acero y pueden manejar relaciones L/D de barra en el rango de 6:1. Las barras de carburo sólido brindan mayor rigidez y permiten relaciones de barra de hasta L/D de 8:1, junto con la posible desventaja de un mayor costo, especialmente cuando se requiere una barra de gran diámetro.
Una forma alternativa de amortiguar las vibraciones implica una barra sintonizable. La barra cuenta con un amortiguador de masa interno que está diseñado para resonar fuera de fase con la vibración no deseada, absorber su energía y minimizar el movimiento vibratorio. El Steadyline ® sistema de Seco Tools (ver barra lateral) , por ejemplo, presenta un amortiguador de vibraciones preajustado que consiste en una masa amortiguadora hecha de material de alta densidad suspendida dentro de la barra portaherramientas a través de elementos de absorción radial. La masa amortiguadora absorbe la vibración inmediatamente cuando la herramienta de corte la transmite al cuerpo de la barra.
El control activo de vibraciones de herramientas más complejo y costoso puede tomar la forma de dispositivos activados electrónicamente que detectan la existencia de vibraciones y usan actuadores electrónicos para producir un movimiento secundario en el portaherramientas para cancelar el movimiento no deseado.
MATERIAL DE LA PIEZA
Las características de corte del material de la pieza de trabajo pueden contribuir a la generación de vibraciones. La dureza del material, la tendencia al recrecimiento del borde o al endurecimiento por trabajo, o la presencia de inclusiones duras alteran o interrumpen las fuerzas de corte y pueden generar vibraciones. Hasta cierto punto, el ajuste de los parámetros de corte puede minimizar las vibraciones al mecanizar ciertos materiales.
GEOMETRÍA DE HERRAMIENTA DE CORTE
La propia herramienta de corte está sujeta a deflexión tangencial y radial. La deflexión radial afecta la precisión del diámetro interior. En la deflexión tangencial, el inserto es forzado hacia abajo alejándose de la línea central de la pieza. Especialmente cuando se taladran agujeros de diámetro pequeño, el diámetro interior curvo del agujero reduce el ángulo de incidencia entre la plaquita y el agujero.
La deflexión tangencial empujará la herramienta hacia abajo y lejos de la línea central del componente que se está maquinando, reduciendo el ángulo de incidencia. La desviación radial reduce la profundidad de corte, lo que afecta la precisión del mecanizado y altera el grosor de la viruta. Los cambios en la profundidad de corte alteran las fuerzas de corte y pueden provocar vibraciones.
Las características de la geometría de la plaquita, como la inclinación, el ángulo de ataque y el radio de la punta, pueden aumentar o amortiguar la vibración. Las plaquitas de desprendimiento positivo, por ejemplo, crean menos fuerza de corte tangencial. Pero la configuración del ángulo de ataque positivo puede reducir el espacio libre, lo que puede provocar fricción y vibración. Un ángulo de inclinación grande y un ángulo de filo pequeño producen un filo afilado, lo que reduce las fuerzas de corte. Sin embargo, el borde afilado puede estar sujeto a daños por impacto o desgaste desigual, lo que afectará el acabado de la superficie del orificio.
Un ángulo de ataque de filo de corte pequeño produce fuerzas de corte axiales más grandes, mientras que un ángulo de ataque grande produce fuerza en la dirección radial. Las fuerzas axiales tienen un efecto limitado en las operaciones de mandrinado, por lo que puede ser deseable un ángulo de avance pequeño. Pero un ángulo de ataque pequeño también concentra las fuerzas de corte en una sección más pequeña del filo de corte que un ángulo de ataque grande, con un posible efecto negativo en la vida útil de la herramienta. Además, el ángulo de ataque de una herramienta afecta el grosor de la viruta y la dirección del flujo de viruta.
El radio de la punta de la plaquita debe ser menor que la profundidad de corte para minimizar las fuerzas de corte radiales.
CONTROL DE CHIP
Limpiar las virutas de corte del orificio es un tema clave en las operaciones de perforación. La geometría de la plaquita, las velocidades de corte y las características de corte del material de la pieza de trabajo influyen en el control de la viruta. Las virutas cortas son deseables en el mandrinado porque son más fáciles de evacuar del mandrinado y minimizan las fuerzas en el filo de corte. Sin embargo, las geometrías de plaquitas altamente contorneadas diseñadas para romper virutas tienden a consumir más energía y pueden causar vibraciones.
Las operaciones destinadas a crear un buen acabado superficial pueden requerir una profundidad de corte ligera que producirá virutas más delgadas que magnificarán el problema de control de virutas. El aumento de la velocidad de avance puede romper las virutas, pero puede aumentar las fuerzas de corte y generar vibración, lo que puede afectar negativamente a los acabados superficiales. Las velocidades de avance más altas también pueden provocar la acumulación de filos al mecanizar aceros con bajo contenido de carbono, por lo que las velocidades de avance de corte más altas junto con un suministro óptimo de refrigerante interno pueden ser una solución para el control de virutas al mandrinar estas aleaciones de acero más maleables.
CONCLUSIÓN
El mandrinado de agujeros profundos y el torneado con herramientas de longitud extendida son operaciones de corte de metales comunes y esenciales. Llevar a cabo estos procesos de manera eficiente requiere la evaluación del sistema de maquinado como un todo para asegurar que los múltiples factores involucrados en minimizar la vibración y asegurar la calidad del producto estén trabajando juntos para lograr la máxima productividad y rentabilidad.
Aparecido anteriormente en el sitio de noticias de SECO.
Tecnología Industrial
- Las principales diferencias entre el mecanizado de 3 y 5 ejes
- Desequilibrio:el problema oculto que los talleres mecánicos deben resolver
- Dominar los desafíos del giro brusco
- Mecanizado de titanio:encuentre las herramientas de fresado adecuadas para superaleaciones
- Poniendo la inspección de superficies en manos del operador de máquinas herramienta
- Lecciones de mecanizado de alto rendimiento:no se olvide de los portaherramientas
- La importancia de los refrigerantes en el mecanizado
- Las ventajas del mecanizado CNC de 5 ejes
- El corazón de las máquinas herramienta:los husillos de las máquinas herramienta.
- Comprender el proceso de mecanizado y la máquina herramienta
- El arte de mecanizar acero inoxidable