Soldadura de láminas de metal:métodos comunes y consejos para soldar
Después de cortar las piezas de metal al tamaño deseado, es necesario unirlas para que se adapten a la forma y las especificaciones deseadas. Por lo tanto, la soldadura de láminas de metal es un aspecto importante de la fabricación de metal.
Existen diferentes técnicas de soldadura de chapa, pero ¿sabes cuál es la mejor para tus aplicaciones industriales?
Este artículo proporciona una visión detallada de los diversos métodos utilizados en la soldadura de chapa, incluidas sus ventajas y aplicaciones. También proporciona consejos vitales para tener en cuenta al soldar láminas delgadas de metal para obtener los mejores resultados.
6 Métodos de Soldadura de chapa
Ahora, echemos un vistazo completo a algunos métodos para fusionar láminas de metal.
1. Soldadura MIG
Soldadura de metal con gas inerte (MIG), también conocida como soldadura por arco con gas y metal. Se trata de alimentar un electrodo de alambre sólido continuo en el charco de soldadura con una pistola de soldar. El alambre derretido en la piscina provoca la unión de las piezas metálicas. El gas de protección de la pistola de soldar evita la contaminación atmosférica del charco de soldadura.
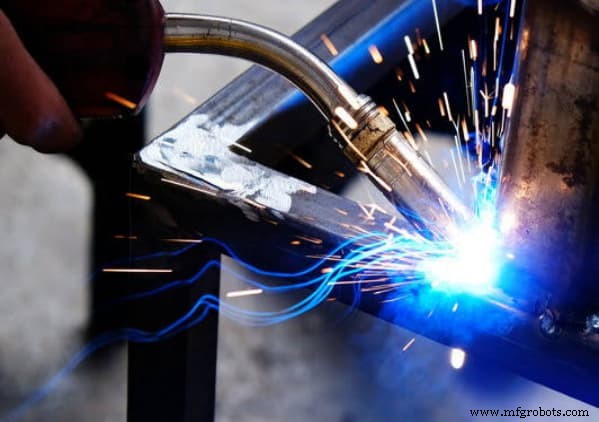
La soldadura MIG crea soldaduras de máxima calidad y es adecuada para la mayoría de las láminas de metal, como aluminio, acero y acero inoxidable.
Este método de soldadura es la técnica de referencia en la industria automotriz y de mejoras para el hogar. Además, es una técnica rentable, ya que no requiere máquinas sofisticadas.
Soldadura TIG
Tungsten Inert Gas (TIG) es una soldadura por arco que implica el uso de un electrodo de tungsteno no consumible bajo CC o CA para producir su soldadura. Al igual que la soldadura MIG, utiliza gas de protección inerte:argón o helio para evitar los contaminantes atmosféricos y la oxidación del electrodo y el charco.
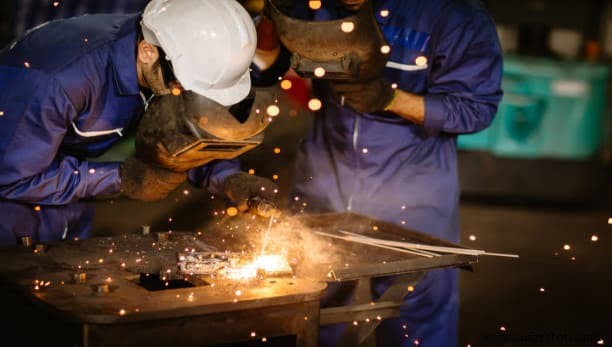
La soldadura TIG es adecuada para soldar metales no ferrosos como aluminio, titanio, cobre, níquel, magnesio, cromo, etc. Es una técnica valiosa para las industrias aeronáutica y aeroespacial. Además, es ideal para fabricar marcos para motocicletas, puertas y comederos.
Este método de soldadura proporciona al soldador un mejor control que conduce a una soldadura limpia y fuerte. Sin embargo, puede llevar mucho tiempo y requiere experiencia por parte del soldador.
[Lectura adicional:Una guía para elegir entre la soldadura Mig y la soldadura Tig]
Soldadura con electrodos
La soldadura con electrodo revestido se conoce como soldadura por arco de metal blindado. Es un proceso de soldadura por arco manual que utiliza una varilla cubierta de fundente como electrodo. Una corriente eléctrica procedente de la fuente de alimentación de soldadura forma un arco entre las piezas que unen los metales y el electrodo. Es adecuado para metales duros como el hierro y el acero.
El proceso no utiliza ningún gas de protección. A medida que se genera calor, se desintegra el fundente que cubre el electrodo, formando una escoria que protege el baño de soldadura de la contaminación.
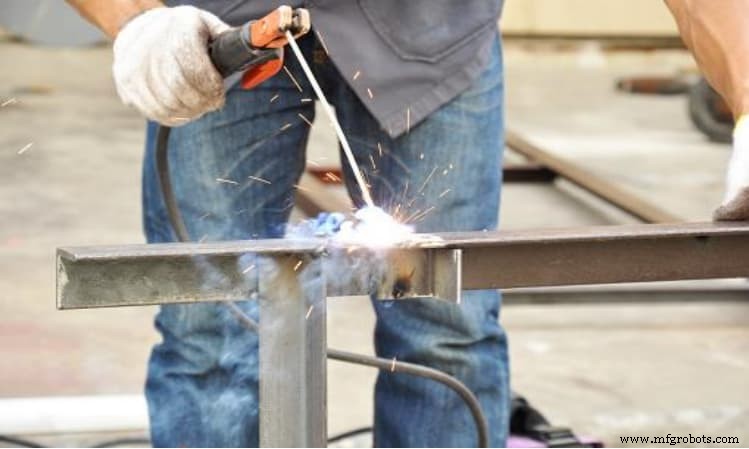
Esta técnica de soldadura es quizás la más conveniente, ya que su equipo es compacto y portátil, fácil de transportar. Es una técnica común en las industrias de la construcción, la construcción naval y la fabricación de acero.
Soldadura por arco de plasma
La soldadura por arco de plasma es similar a la soldadura TIG en que utiliza un electrodo de tungsteno. Sin embargo, utiliza un pequeño arco y permite colocar el electrodo en el cuerpo del soplete. El gas presurizado forma un plasma caliente que funde los metales para crear soldaduras sólidas.
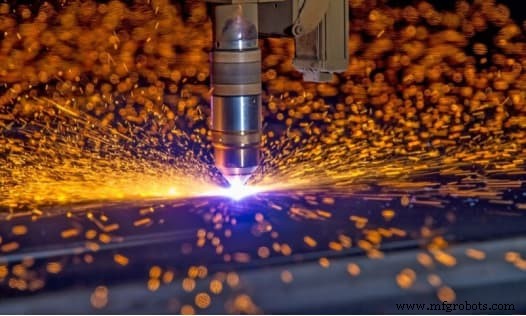
Esta técnica de soldadura requiere poca potencia y trabaja a alta velocidad. Además, produce soldaduras precisas, lo que lo hace ampliamente aceptado en las industrias de la aviación y la marina.
Al igual que la soldadura TIG, la soldadura por arco de plasma no requiere materiales de relleno. Además, produce soldaduras de alta calidad con menos necesidad de acabado.
Soldadura por haz de electrones y láser
Como sugiere el nombre, la soldadura por láser y haz de electrones utiliza láseres y haces de electrones como fuente de calor para fusionar y unir piezas de metales. A diferencia de la mayoría de los otros métodos, esta técnica de soldadura requiere una máquina sofisticada o robots automatizados.
Es una técnica de soldadura de alta precisión, lo que la hace adecuada para operaciones con detalles intrincados. Los rayos láser pueden enfocarse en las sustancias más diminutas para una soldadura de precisión extrema.
Además, es adecuado para soldar metales duros como acero al carbono, titanio, acero inoxidable y aluminio. La técnica también es adecuada para termoplásticos. El método produce productos de gran atractivo estético, reduciendo las necesidades de postproducción.
Soldadura con gas
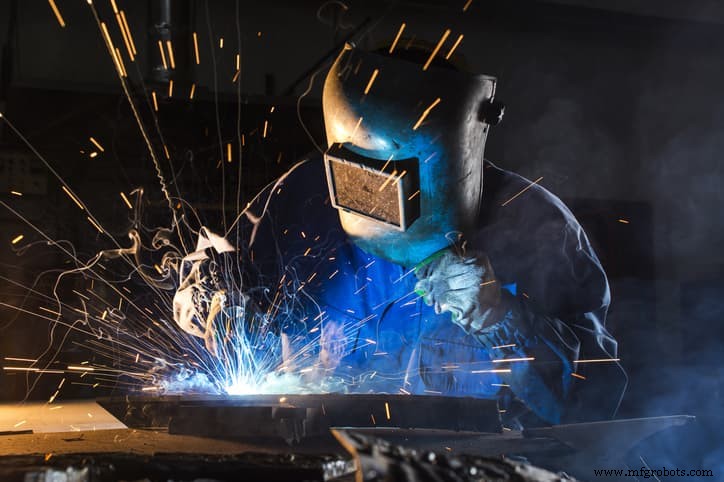
La soldadura a gas es una de las formas tradicionales de soldadura por calor. Implica el uso de calor generado por la quema de combustible (gasolina), oxígeno u oxiacetileno para unir piezas de metales. La quema de estos combustibles producía llamas muy calientes que derriten las superficies metálicas durante la unión.
La técnica sigue siendo uno de los métodos de soldadura más utilizados en las industrias. Tiene un amplio campo de aplicación, adecuado tanto para metales ferrosos como no ferrosos. Además, es eficaz y eficiente para soldar tuberías y tubos, reparar sistemas de ventilación y aire acondicionado, etc.
A diferencia de muchas otras técnicas de soldadura, no requiere electricidad. Además, es portátil, muy económico y no requiere los servicios de especialistas.
¿No estás seguro si unes tus piezas de chapa mediante la técnica de soldadura o remachado? Si es así, tenemos una guía sobre cómo elegir entre soldar y remachar.
Tenga en cuenta la superficie al elegir Soldadura de chapa Métodos
A continuación se muestran las superficies que puede encontrar al soldar láminas de metal y los mejores métodos para combinarlas.
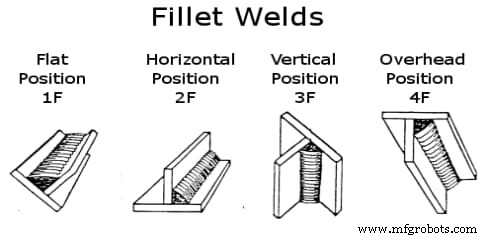
Superficie plana
La soldadura de una superficie plana se denomina soldadura plana. El soldador se acerca a esta superficie desde el lado superior de la junta, permitiendo que la gravedad ayude con el flujo fundido.
Para obtener una buena soldadura en una superficie plana, el soldador debe colocar el ángulo de la punta a 45 grados con respecto a la superficie metálica, apuntando con cuidado la llama hacia el punto de unión.
Los métodos de soldadura MIG y TIG son los más adecuados para superficies planas. Los flujos de alimentación de alambre y gas funcionan excelentemente en una configuración plana.
Superficie horizontal
En una configuración horizontal, las láminas de metal aparecen horizontales al soldador. Sin embargo, puede existir en dos formas.
- Soldadura de filete:la soldadura se realiza en el extremo superior de una superficie horizontal contra una superficie vertical. El área de unión parece ser la unión de dos piezas de metal perpendiculares entre sí en forma de "L".
- Soldadura de ranura:la superficie de soldadura se encuentra en un plano vertical. Ambas piezas metálicas a unir están en el mismo plano.
La soldadura con electrodo revestido es más adecuada para trabajar en una superficie horizontal donde es difícil lograr el equilibrio perfecto entre la soldadura TIG y MIG.
Superficie vertical
La posición vertical del eje de soldadura es básicamente una soldadora vertical orientada hacia la superficie. El metal fundido tiende a fluir hacia abajo y acumularse al soldar. Por lo tanto, el soldador necesita controlar el flujo de metal. Esto implica apuntar la pistola de soldar en un ángulo de 45 grados con respecto a la placa y sostener el electrodo entre la llama y el baño de soldadura.
El mejor método para superficies verticales es la soldadura con electrodo revestido. A menudo, los soldadores simplemente intentan ajustar el eje de soldadura para que parezca plano u horizontal para mayor comodidad.
Superficie aérea
La soldadura de materiales en superficies elevadas es la más desafiante. Como sugiere el nombre, implica soldar una pieza de trabajo colocada sobre su cabeza. El metal fundido tiende a caerse cuando intenta soldar.
Para aliviar la dificultad de la soldadura por encima de la cabeza, minimice el charco de soldadura. Además, asegúrese de usar suficiente material de relleno para tener una buena soldadura.
La soldadura revestida es el método más apropiado para esta configuración. La soldadura de superficies elevadas es relativamente poco común en las instalaciones de fabricación de láminas de metal personalizadas.
8 Consejos para soldar chapas metálicas
Cuando se unen láminas de metal, el objetivo es garantizar que las piezas soldadas mantengan las propiedades mecánicas suficientes para la aplicación. A continuación, se incluyen algunos consejos que debe tener en cuenta al realizar la soldadura.
1. Seleccione los metales de aporte
Es fundamental utilizar un metal de aportación adecuado que se ajuste a las características mecánicas de su fabricación. El relleno debe ser más delgado que la lámina de metal. Por ejemplo, cuando se suelda un metal delgado de 1 mm, la mejor opción es un relleno de 0,6 mm.
Cuanto más delgado es el alambre, menos calor se requiere para fundirlo. Por lo tanto, menos riesgos de acumulación excesiva de calor y mayores posibilidades de obtener los mejores resultados de su soldadura.
Además, elegir correctamente el metal de aporte reducirá los riesgos de oxidación, agrietamiento y otros posibles defectos.
2. Utilice la técnica de soldadura salteada
La técnica de soldadura salteada implica el uso de una serie de puntadas o soldaduras cortas en puntos críticos para mantener la lámina delgada de metal en su lugar. Después de dejar que se enfríe durante unos minutos, el soldador puede continuar soldando lugares previamente salteados.
Saltar la soldadura ayuda a evitar la distorsión y el alabeo del metal, a menudo causados por una distribución desigual del calor.
Además, al soldar, evite tejer el soplete de soldadura; esto también puede causar un calor excesivo. En su lugar, mueva rápidamente la antorcha a lo largo de un camino recto.
3. Utilice la técnica de soldadura por puntos
La soldadura por puntos es otra técnica excelente para reducir el riesgo de acumulación excesiva de calor y quemaduras.
Las tachuelas son soldaduras menores y temporales que se utilizan para mantener unidas las piezas metálicas hasta la soldadura final. Para evitar quemar agujeros, mantenga las piezas de metal muy juntas a tope con un espacio de 1 mm entre ellas. Luego, cree pequeñas soldaduras por puntos hasta que la junta esté completamente cubierta.
4. Utilice un diámetro de alambre pequeño
Cuando suelde con un electrodo de alambre sólido, como en la soldadura MIG, asegúrese de usar alambres del diámetro más pequeño disponible. Los alambres pequeños brindan al soldador un mejor control y una mayor posibilidad de corregir un error, ya que producen menos depósitos.
Además, cuanto más pequeño es el alambre, menos calor se requiere para fundirlo. Por lo tanto, hay menos problemas de calor excesivo.
Generalmente, cuando se trabaja con láminas de metal de calibre ligero, se recomiendan 0,023 o 0,024 pulgadas. Sin embargo, un alambre de 0,030 pulgadas puede ser ideal para soldar metales de garaje 18 o más gruesos.
5. Usar electrodo pequeño
Asegúrese de usar una varilla que sea menos gruesa que su metal. Utilice electrodos de menos de ⅛ de pulgada. Un electrodo más pequeño funcionará excelentemente con menos calor y corrientes, lo que reducirá el quemado y le permitirá amolar el electrodo a un área pequeña para ejecutar un arco ajustado.
6. Sujete una barra trasera
Sujetar una barra de respaldo al metal de trabajo permite una disipación de calor más rápida que simplemente esperar a que se enfríe. La barra trasera extrae el calor del metal, lo que reduce el riesgo de deformaciones o quemaduras.
Las barras de metal suelen ser de material de cobre o aluminio porque disipan mejor el calor debido a su alta conductividad térmica. Asegúrese de que la barra de respaldo esté firmemente sujeta a la pieza de trabajo para una transferencia de calor adecuada.
7. Utilice gas protector con alto contenido de argón
Al soldar, utilice gas de protección con un alto porcentaje de argón. Un ejemplo de ello es la típica combinación de argón y dióxido de carbono en una proporción de 75 a 25, respectivamente.
Se prefiere un gas de protección con un alto contenido de argón porque el argón emite menos calor. Al realizar soldaduras TIG o MIG de metal de aluminio, es posible que deba usar argón puro como gas de protección.
8. Ajuste y diseño de juntas
La soldadura de láminas de metal delgadas puede ser complicada. Requiere un montaje ajustado y firme, ya que hay poco margen de error. Asegúrese de que los espacios entre los dos metales de unión sean mínimos para evitar que se quemen, ya que los orificios pueden absorber calor.
Como regla general, los soldadores deben medir dos veces y cortar una vez. En algunos casos, es posible que deba rediseñar las juntas para que tengan una mayor resistencia al calor.
Junta a tope
Una junta a tope se refiere a dos piezas de metal colocadas una al lado de la otra para soldar.
La superficie de contacto es el área que se funde durante la soldadura. Es crucial llevar a cabo la preparación del borde en la superficie para aumentar la resistencia de la soldadura. Es posible que el soldador deba doblar uno de los lados para permitir que encajen bien entre sí para una soldadura fuerte.
La soldadura a tope es relativamente fácil de preparar y resiste la tensión mejor que otras uniones soldadas. Es por eso que es la junta de soldadura más común en la fabricación de estructuras. Sin embargo, existen otros tipos de juntas de soldadura.
Junta de regazo
Las juntas traslapadas son una modificación típica de las juntas a tope. Son las juntas de referencia para soldar chapas de distintos espesores.
En la junta traslapada, las dos piezas de metal se unen en una superposición, una colocada sobre la otra. El principal inconveniente de la unión traslapada es que la unión de los dos metales es propensa a la oxidación.
Junta en T
Como su nombre lo indica, la junta en T ocurre donde dos piezas de metal se cruzan perpendicularmente, formando un ángulo recto en forma de 'T'. Se consideran una forma de soldadura de filete.
Cuando utilice esta junta, asegúrese de que penetre adecuadamente en el techo de soldadura. Es posible que también deba agregar un tope para reducir las restricciones conjuntas que a menudo se experimentan en el punto de conexión. La junta en T es común en estructuras con sistemas de tuberías y tuberías.
Junta de esquina
Las juntas de esquina son algo similares a la junta en T en que ambas forman un ángulo perpendicular. Sin embargo, los metales de unión están en diferentes orientaciones. En las juntas de esquina, los metales se unen en la esquina, creando un solo ángulo recto en forma de "L". Las juntas de esquina son piezas estándar de fabricación, especialmente marcos y cajas.
Junta de borde
En las juntas de borde, las láminas de metal se colocan una al lado de la otra y se sueldan en el mismo borde. Ocurre en una pieza de trabajo con bordes ensanchados. Es posible que el soldador deba doblar el borde de cualquiera de las piezas de metal en ángulos adecuados para permitir que encajen bien en la otra para producir una soldadura firme.
RapidDirect:Your Custom Sheet Metal Welding Partner
Are you in need of top-notch welding operations for custom sheet metal fabrication ? Or you don’t know how to weld sheet metal for your manufacturing needs? RapidDirect is just what you need. We offer some of the best services in the industries ranging from welding to laser cutting and other related technologies.
RapidDirect provides outstanding and professional sheet metal services. We just require you to upload your design files. You get a free DfM analysis report on the manufacturing of your sheet metal parts. What’s more? We guarantee high quality at competitive pricing and fast lead times.
Preguntas frecuentes
Which Welding is Suitable for Thin Metals? TIG welding is the most appropriate for welding thin sheets of metals. The TIG welding process is highly precise, not deviating from where it ought to focus welding. Consequently, you have a smooth and delicate finish for the welded parts.
Can I Use AC or DC to MIG Weld Aluminum?Both alternating and direct current MIG welding is suitable for aluminum. However, direct current welding, which is the typical form of MIG welding, is a lot faster as it does not require machines with AC and DC specifications.
What’s the Thinnest Sheet Metal That Can Be Welded?Welding very thin metals requires experts who can optimally control the heat applied to the metal. With good heat control, it’s possible to weld sheet metal as low as 0.8 mm thickness with MIG welding. Besides, TIG allows you to weld as low as 0.6 mm thickness or even lower.
Tecnología Industrial
- Consejos y trucos para soldar Inconel
- 5 consejos para el diseño de chapa metálica
- Una breve descripción general:Sugerencias de soldadura para ahorrar costos para su próximo proyecto de soldadura
- Diseño de chapa:consejos y trucos
- 20 herramientas y equipos básicos de soldadura para principiantes
- Bisagras para gabinetes de chapa metálica
- Uso de chapa perforada para ventilación
- Bisagras para sus gabinetes de chapa metálica
- Prácticas de diseño para ahorrar costos y consejos para gabinetes y piezas de chapa personalizadas
- Diferentes métodos para el acabado de superficies metálicas
- Consejos de diseño para doblar chapa metálica