Arena de moldeo:propiedades, tipos, procesos, MCQ
En este artículo vamos a aprender sobre Qué es la arena de moldeo ,Propiedades de la arena de moldeo y tipos de arena de moldeo .
El principal material utilizado en el taller de fundición para el moldeo es la arena. Esto se debe a que posee las propiedades vitales para propósitos de fundición.
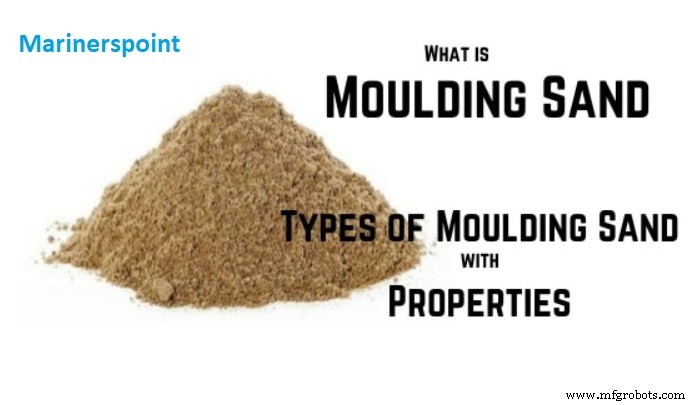
Fuentes
Todas las arenas se forman por la ruptura de rocas debido a la acción de fuerzas naturales como las heladas, el viento, la lluvia, el calor y las corrientes de agua. Las rocas, sin embargo, son muy complejas en su composición y las arenas contienen la mayoría de los elementos de las rocas de las que son fragmentos. Por este motivo, las arenas de moldeo en diferentes partes del mundo varían considerablemente. Hoy en día, la arena se obtiene de lugares que probablemente alguna vez fueron fondos y márgenes de ríos y dunas de arena.
En India, las arenas de fundición se encuentran en el área de Damodar y Barakar, Santhal Pargana (Bihar), Batala (Gurdaspur, Punjab), Bhavnagar (Saurashtra), Londha (Maharashtra), Avadi y Veeriyambakam (Madras), Kanpur, Jabalpur, Rajkot, Guntur , en Ganges y muchos otros lugares.
Ingredientes principales
Los principales ingredientes de las arenas de moldeo son:(1) granos de arena de sílice (2) arcilla (3) humedad y (4) materiales varios.
La sílice en forma de cuarzo granular, en sí misma una arena, es el componente principal de la arena de moldeo. La arena de sílice contiene de 80 a 90 por ciento de dióxido de silicio y se caracteriza por una alta temperatura de reblandecimiento y estabilidad térmica.
Es producto de la fragmentación de rocas de cuarzo o la descomposición del granito, que se compone de cuarzo y feldespato . El feldespato, cuando se descompone, se convierte en arcilla (silicato de aluminio hidratado). Sin embargo, los granos de arena de sílice imparten refractariedad, resistividad química y permeabilidad a la arena. Se especifican según su tamaño y forma promedio.
Arcilla se define como aquellas partículas de arena (menos de 20 micras de diámetro) que no se asientan a una velocidad de 25 mm por minuto, cuando se suspenden en agua. La arcilla consta de dos ingredientes: limo fino y verdadera arcilla . El limo fino es una especie de materia extraña o depósito mineral y no tiene poder de unión.
Es la verdadera arcilla la que imparte la fuerza de unión necesaria a la arena del molde, para que el molde no pierda su forma después del apisonamiento. Se encuentra que la arcilla verdadera está compuesta de agregados extremadamente diminutos de partículas cristalinas, generalmente en forma de escamas, llamadas minerales arcillosos. La mayoría de las arenas de moldeo para diferentes grados de trabajo contienen de 5 a 20 por ciento de arcilla. La humedad, en la cantidad requerida, proporciona la acción de unión de la arcilla.
Cuando se agrega agua a la arcilla, penetra en la mezcla y forma un microfilm que recubre la superficie de las partículas de arcilla en forma de copos. La calidad de unión de la arcilla depende del espesor máximo de película de agua que pueda mantener. La acción de unión se considera mejor si el agua añadida es la cantidad exacta requerida para formar la película. Por otro lado, la acción de unión se reduce y el molde se debilita si el agua está en exceso. El agua debe estar entre el 2 y el 8 por ciento.
Los materiales misceláneos que se encuentran, además de sílice y arcilla, en la arena de moldeo son óxido de hierro, piedra caliza, magnesia, soda y potasa. Las impurezas deben estar por debajo del 2 por ciento.
Clasificación
Tipos de arenas de moldeo:Se pueden clasificar generalmente en tres tipos diferentes:(1) arenas de moldeo naturales , (2) arenas sintéticas o con alto contenido de sílice , y (3) arenas especiales .
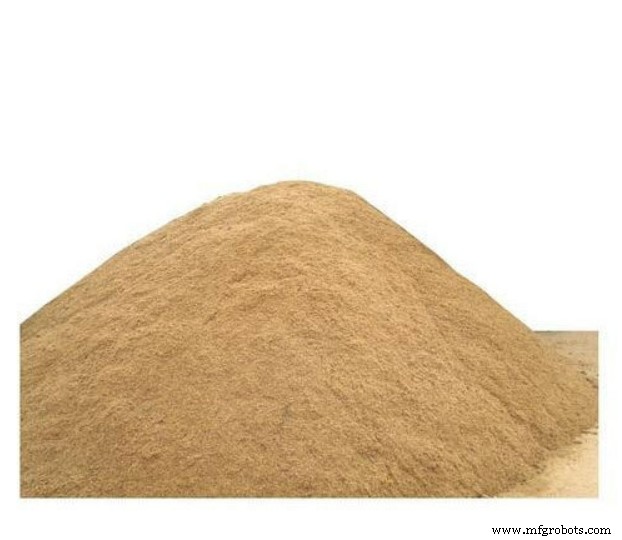
1. Arenas de moldeo naturales
Arenas de moldeo naturales , llamadas arenas verdes, se extraen de los lechos de los ríos o se extraen de pozos. Poseen una cantidad apreciable de arcilla que actúa como aglutinante entre los granos de arena y se utilizan tal como se reciben con agua añadida. La cantidad y el tipo de mineral arcilloso presente afectan la resistencia, tenacidad y refractariedad de la arena.
Estos también se obtienen triturando y moliendo arenisca amarilla blanda, rocas carboníferas, etc. Durante la operación de molienda, los agregados de arcilla se descomponen y las partículas de arcilla se distribuyen uniformemente sobre los granos de arena. Se requiere que la forma del grano de estas arenas sea sub angular a redonda.
Debido a su facilidad de disponibilidad, bajo costo y alta flexibilidad de operación, las arenas de moldeo naturales se utilizan para la mayoría de las fundiciones ligeras ferrosas y no ferrosas. Los requerimientos de estas arenas son satisfechos por IS:3343-1965 , que las ha clasificado en tres grados A ,
2. Arenas Sintéticas
Arenas sintéticas son básicamente arenas con alto contenido de sílice que contienen poco (menos del 2 por ciento) o ningún aglutinante (arcilla) en forma natural. Se presentan como depósitos sueltos o mal consolidados de origen sedimentario, dunas arrastradas tierra adentro desde la costa o depósitos acumulados en estuarios y ríos a lo largo de la costa.
También se fabrican en fundición triturando primero areniscas de cuarcita y luego lavándolas y clasificándolas para producir un grado de arena con la forma y distribución de grano requeridas. La resistencia deseada y las propiedades de unión de estas arenas se desarrollan mediante adiciones separadas, como bentonita, agua y otros materiales.
Esto permite mayores flexibilidades en el contenido de propiedades como resistencia en verde y en seco, permeabilidades y otras que se pueden variar fácilmente a voluntad. De hecho, por lo tanto, las arenas sintéticas son más caras que las arenas naturales.
ES:1987-1974 cubre los requisitos de la arena con alto contenido de sílice para su uso en fundiciones y la clasifica en tres grados según el contenido de sílice.
3. Arenas Especiales
Arenas especiales son ideales para obtener características especiales, que ordinariamente no se obtienen en otras arenas. El circón, el olivino, la chamota, la cromita y la cromo-magnesita se utilizan a menudo como arenas especiales. Las arenas de circón son adecuadas para núcleos de fundición de latón y bronce. Algunas fundiciones usan arena de olivino para fundiciones no ferrosas de naturaleza intrincada. La chamota es valiosa para fundiciones de acero pesado.
Las arenas de cromita y cromo-magnesita son particularmente útiles cuando se debe aumentar la tendencia al enfriamiento para controlar la solidificación. También son adecuados como materiales de revestimiento en moldes para fundiciones de acero.
Tipos de arena para moldear
Las arenas de moldeo pueden volver a clasificarse, según su uso, en varias variedades. Estos se describen a continuación.
Molduras en arena verde
Es una mezcla de arena silícea con 18 a 30 por ciento de arcilla, teniendo un total de agua de 6 a 8 por ciento. La arcilla y el agua proporcionan el enlace para la arena verde. Es fino, suave, ligero y poroso. Al estar húmedo, cuando se aprieta en la mano, conserva la forma, la impresión que le da bajo presión. Los moldes preparados en esta arena se conocen como moldes de arena verde.
Moldeado en arena seca
La arena verde que se ha secado u horneado después de hacer el molde se llama arena seca. Son adecuados para fundiciones más grandes. Los moldes preparados en esta arena se conocen como moldes de arena seca.
Marga Arena
La arena franco tiene un alto contenido de arcilla, hasta un 50 por ciento más o menos, y se seca con fuerza. Esto se emplea particularmente para el moldeado de marga, por lo general para fundiciones grandes.
Frente a la arena
La arena de revestimiento forma la cara del molde. Se utiliza directamente junto a la superficie del patrón y entra en contacto con el metal fundido cuando se vierte el molde. En consecuencia, está sometido a las condiciones más severas y debe poseer, por tanto, alta resistencia y refractariedad.
Está hecho de arena silícea y arcilla, sin adición de arena usada. Se utilizan diferentes formas de carbón para evitar que el metal se queme en la arena. A veces se mezclan con 6 a 15 veces más arena fina para moldear para hacer revestimientos.
La capa de arena de revestimiento en un molde suele oscilar entre 20 y 30 mm. Del 10 al 15 por ciento de la cantidad total de arena de moldeo utilizada en la fundición es arena de revestimiento. Una mezcla de arena de revestimiento para el moldeo con arena verde de hierro fundido puede consistir en un 25 % de arena fresca y especialmente preparada, un 70 % de arena vieja y un 5 % de carbón marino.
Respaldo Arena
Se utiliza arena de respaldo o arena de piso para respaldar la arena de revestimiento y para llenar todo el volumen del matraz. Para este fin se emplea principalmente arena de moldeo vieja y repetidamente utilizada.
La arena de respaldo a veces se llama arena negra debido a que la arena de moldeo vieja y repetidamente utilizada es de color negro debido a la adición de polvo de carbón y se quema al entrar en contacto con el metal fundido.
Sistema Arena
En las fundiciones mecánicas donde se emplea el moldeado a máquina, se utiliza el llamado sistema de arena para llenar todo el matraz. En las unidades mecánicas de preparación y manipulación de arena no se utiliza arena de revestimiento. La arena usada se limpia y reactiva mediante la adición de aglutinantes de agua y aditivos especiales. Esto se conoce como arena de sistema. Dado que todo el molde está hecho de arena de este sistema, la resistencia, la permeabilidad y la refractariedad de la arena deben ser superiores a las de la arena de respaldo.
Partida arena
La arena de separación se usa para evitar que la arena verde se adhiera al patrón y también para permitir que la arena en la superficie de separación de la cofia y el arrastre se separen sin adherirse. Se trata de arena de sílice limpia sin arcilla que sirve para el mismo propósito que el polvo de separación.
Núcleo Arena
La arena utilizada para fabricar núcleos se llama arena para núcleos, a veces llamada arena de aceite. Se trata de arena de sílice mezclada con aceite central que se compone de aceite de linaza, resina, aceite mineral ligero y otros materiales aglutinantes. Se puede usar brea o harina y agua en núcleos grandes por razones de economía.
Propiedades de la arena de moldeo
¿Cuáles son las propiedades de la arena de moldeo?
La arena de moldeo adecuada debe poseer seis propiedades. Propiedades de la arena de moldeo son:debe tener porosidad, fluidez, colapsabilidad, adhesividad, cohesión o resistencia y refractariedad.
- Porosidad :- La propiedad más importante de la arena de moldeo es la porosidad, también conocida como permeabilidad. Se refiere a la capacidad de la arena de moldeo para permitir el paso de los gases. Durante el vertido de metal fundido en la cavidad de arena, se producen gases y vapor. Esta propiedad se ve afectada no solo por la forma y el tamaño de las partículas de arena, sino también por la cantidad de arcilla, material aglutinante y humedad en la mezcla.
- Fluibilidad :- La capacidad de la arena para llenar pequeños huecos en el patrón. La alta fluidez produce un molde más preciso y, por lo tanto, es útil para fundiciones detalladas.
- Colapsabilidad :- La capacidad de la mezcla de arena para colapsar bajo la fuerza. Una mayor colapsabilidad del molde permite que la fundición de metal se encoja libremente a medida que se solidifica, evitando que se rompa o se agriete en caliente.
- Adhesividad :- La adhesividad es la propiedad de la arena que hace que las partículas de arena se adhieran a los lados de la caja de moldeo. La adherencia de la arena permite el correcto levantamiento de la cofia junto con la arena.
- Cohesión :- La cohesión de la arena es la capacidad de sus partículas para permanecer juntas. Es la resistencia a la tracción de la arena de moldeo. Esta propiedad es fundamental para conservar las formas intrincadas del molde. Una resistencia inadecuada puede hacer que las partículas del molde colapsen durante la manipulación, el giro o el cierre. La adición de arcilla y bentonita mejora la cohesión.
- Refractariedad :- La refractariedad de la arena se refiere a su capacidad para soportar altas temperaturas del metal fundido sin fusión ni ablandamiento. Las arenas de moldeo con baja refractariedad pueden incendiarse cuando se vierte metal fundido en el molde. Los moldes de arena normalmente deberían poder soportar temperaturas de hasta 1650 °C.
- Fuerza :- La fuerza del soporte que ha sido secado u horneado se llama fuerza seca. Debe tener entonces fuerza para soportar las fuerzas erosivas que le obligan a fundir el metal y conservar su forma.
Proceso de moldeo en arena
Fundición en arena , también conocido como fundición por moldeo en arena o Proceso de moldeo en arena , es un proceso de fabricación basado en la fundición que utiliza un molde de arena. Con él se fabrican artículos y componentes metálicos de varios tamaños y formas. Para poner su prevalencia en perspectiva, la fundición en arena representa más del 60% de todas las fundiciones de metal. Las seis fases principales de la fundición en arena se describen en detalle a continuación.
Paso 1:Coloque el patrón de molde en la arena
La colocación del patrón del molde en arena es la etapa inicial de la fundición en arena. El molde tiene un impacto directo en el tamaño y la forma de la fundición. Como resultado, los fabricantes deben desarrollar nuevos moldes para producir artículos y componentes metálicos en tamaños y formas específicos.
Paso 2:establecer un sistema de activación
Se utiliza un sistema de inyección en casi todos los procesos de fundición, y la fundición en arena no es una excepción. Canaliza el molde fundido en la cavidad del molde utilizando una copa de vertido y túneles o "puertas" al molde. Las empresas de fabricación instalarán un sistema de compuertas como este después de colocar el diseño del molde en la arena.
Paso 3:se debe eliminar el patrón de moho
Las empresas de fabricación pueden luego eliminar el patrón de moho de la arena después de que el sistema de compuerta esté en su lugar. En este momento, el patrón del molde es irrelevante. La arena toma la forma del patrón del molde cuando se coloca en su interior. Como resultado, es posible eliminar el patrón de moho.
Paso 4:Vierta metal fundido en la cavidad del molde
Ahora es el momento de verter el metal fundido en la cavidad del molde. El hierro, el acero, el aluminio, el bronce, el magnesio, el zinc y el estaño son solo algunos de los metales y aleaciones que se pueden colar en arena. Es posible que las organizaciones de fabricación necesiten calentar metales o aleaciones hasta 3000 grados Fahrenheit, según el metal o la aleación exactos empleados. El metal o la aleación se vierte en la cavidad del molde una vez que se ha transformado de sólido a líquido.
Paso 5:Espere a que el metal se enfríe
Las empresas de fabricación deben esperar a que el metal fundido se enfríe una vez que se ha colocado en el orificio del molde. Nuevamente, los diferentes tipos de metal requieren cantidades variadas de tiempo de enfriamiento. El metal fundido se enfriará y pasará de una forma líquida a una sólida.
Paso 6:rompa el molde para retirar la fundición de metal
Romper el molde para extraer la fundición de metal recién generada es el sexto y último paso en la fundición en arena. Los patrones de moldes suelen ser reutilizables, pero los moldes en sí no lo son. Como resultado, cada vez que una empresa de fabricación desea fabricar un nuevo producto o componente de metal mediante fundición en arena, debe desarrollar un nuevo molde.
Colapsabilidad de la arena de moldeo
Colapsabilidad de la arena de moldeo se refiere a la capacidad de la arena para ser removida fácilmente de la fundición una vez que se ha solidificado. Las arenas con una colapsabilidad baja se adherirán tenazmente al yeso. Una arena con poca colapsabilidad inducirá el agrietamiento y el desgarro en caliente en las piezas fundidas de metal que se flexionan mucho mientras se enfrían o tienen rangos de temperatura de congelación prolongados. Para mejorar la colapsabilidad, se pueden introducir ciertos aditivos.
MCQ
A. para mantener unidos los granos de arena
B. para permitir que los gases escapen fácilmente del molde
C. resistir el calor de fusión sin mostrar ningún signo de ablandamiento
D. ninguna de las anteriores
Respuesta: Opción B
A. Para que entren gases
B. Para que entre agua
C. Para que escapen los gases
D. Para que escape el agua
Respuesta:Opción C
Explicación: Una arena de moldeo se define como una arena que tiene agujeros y puede contener una cierta cantidad de humedad. Una moldura debe contener poros y ser porosa para que los gases puedan escapar libremente.
Se trató de la arena de moldeo, donde cubrimos todos los temas, como ¿Qué es la arena de moldeo?, describimos las propiedades de la arena de moldeo, el proceso de moldeo con arena verde, la arena seca, la colapsabilidad y algunos MCQ basados en estos temas.
Tecnología Industrial
- Tipos y propiedades de polvo de tantalio
- Arena de moldeo:tipos y constituyentes | Casting | Metalurgia
- Propiedades de la arena de moldeo | Materiales | Casting | Metalurgia
- ¿Qué es Formar? Tipos de proceso de formación [Notas y PDF]
- ¿Qué es la arena de moldeo? - Tipos y propiedades
- Tipos de proceso de soldadura por arco
- Tipos de arena utilizados en el proceso de moldeo
- Definición, proceso y tipos de máquinas de fresado
- Proceso de fabricación Significado y tipos
- Tipos de equipos de fundición en arena
- AMPCO® 25 Fundición en arena