Obtenga un rendimiento sin tiempo de inactividad 'probando la sangre de la máquina'
A mediados de la década de 2000, el sistema de aire comprimido de la planta de Toyota North America en Georgetown, KY, fallaba en promedio más de una vez al año. Eso llevó a algunos en la planta a preguntarse si aprovechar el aprendizaje automático y la IA podría abordar este problema proporcionando detección de anomalías, identificación de fallas y, lo que es más importante, predicción de fallas inminentes antes de que ocurran.
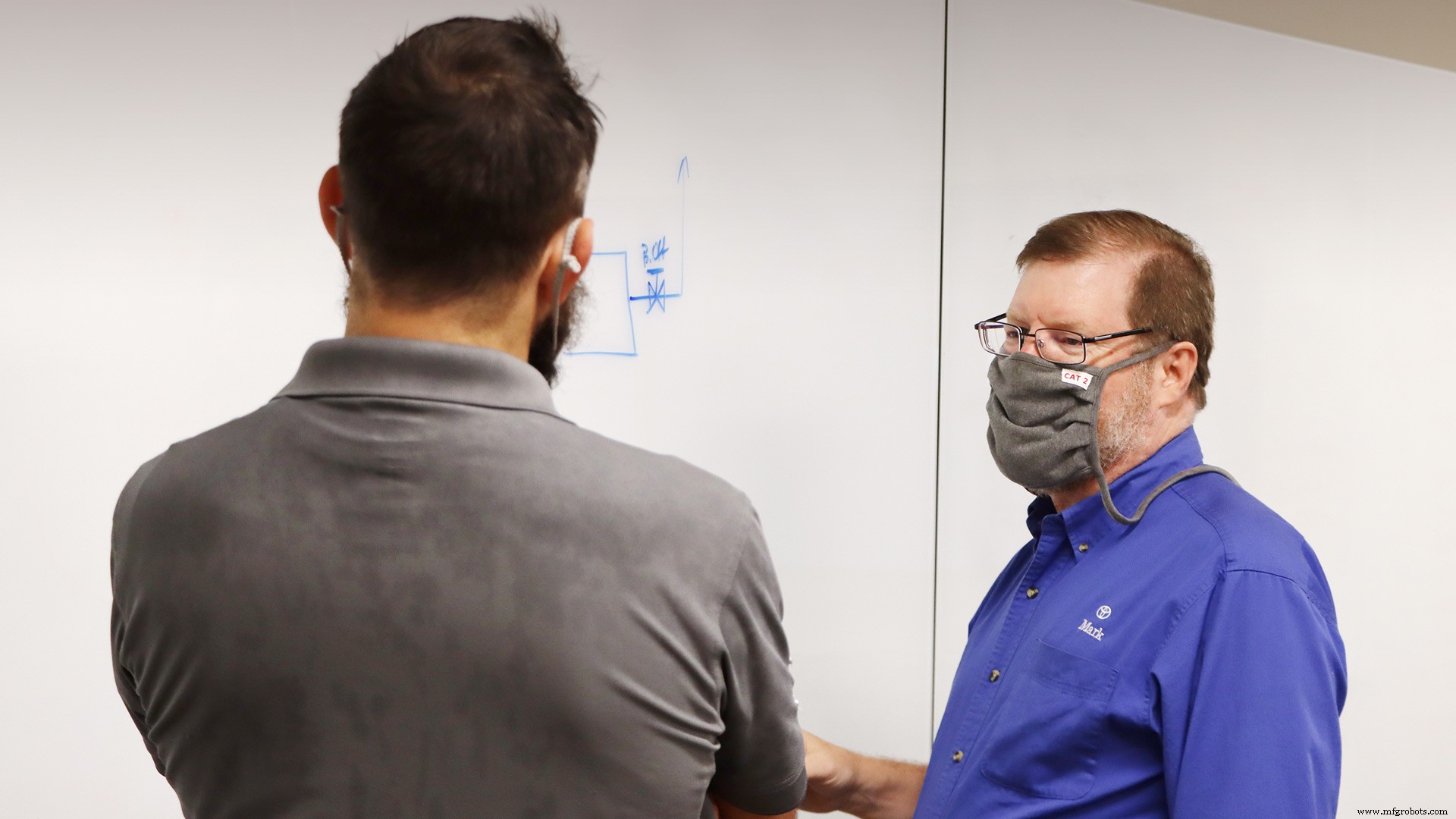
El tiempo de inactividad no planificado del sistema de aire comprimido significaba, por supuesto, que toda la fábrica tenía un problema. El taller de pintura utilizaba aire comprimido para pintar en aerosol vehículos nuevos. El sistema dio vida a las herramientas neumáticas, y nada comparado con el aire comprimido para eliminar el lijado y otros residuos.
Con un vehículo terminado saliendo de una de las tres líneas en la planta cada 25 segundos durante dos turnos, las consecuencias eran significativas si fallaba el servicio de aire comprimido.
“El gasto, si la línea falla, es tremendo”, dijo Mark Rucker, gerente de proyectos y experto en temas eléctricos de la planta. "Por lo tanto, existe un buen incentivo para tener una utilidad buena, confiable y estable".
El sistema de aire comprimido multimillonario está compuesto por una docena de compresores de aire centrífugos Ingersoll Rand, cada uno del tamaño de un pequeño camión. Las palas de la etapa final de cada compresor giran a 20.000 rpm a una fracción de pulgada de su alojamiento. Si una cuchilla funciona un poco fuera de las especificaciones y toca la carcasa, está perdida. La máquina completa debe reconstruirse a un costo de alrededor de $100,000.
Sin embargo, el tambaleo de la hoja no es la causa de un choque; es el resultado.
El accidente, también conocido como un aumento o flujo inverso:sucede cuando algo hace que el flujo normal de aire del compresor a una tubería intente invertirse y el aire en la tubería retroceda.
La frecuencia, el costo y las consecuencias de los choques llevaron a Toyota a llamar a Jay Lee, director fundador de Intelligent Maintenance Systems, para pedir ayuda.
Jay Lee se adelantó a la curva de la Industria 4.0
A principios del nuevo milenio, antes de la llamada de Toyota, Lee era un profesor de ingeniería en la Universidad de Cincinnati que imaginó todas las máquinas en una fábrica conectada y proporcionando datos para un mantenimiento inteligente. En ese momento, sin embargo, gran parte de la tecnología necesaria para hacer realidad la visión de Lee aún no existía.
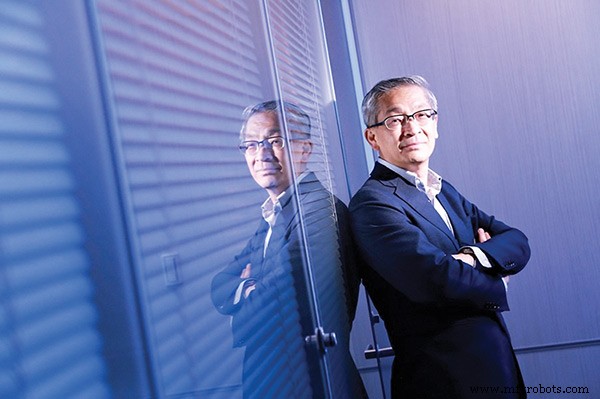
“Hace 20 años, muy pocas personas creían que era posible”, dijo Lee, quien actualmente se encuentra de licencia de la docencia y es vicepresidente y miembro de la junta directiva de Foxconn Technology Group en Wisconsin.
En su visión industrial, las máquinas son como pacientes y los datos recopilados de los sensores que monitorean las máquinas brindan información sobre su salud. Los expertos derivan pronósticos al interpretar los datos que recopilan y analizan.
"Dije:'¿Por qué no analizar la sangre de la máquina?' ¿Y cuál es la sangre de la máquina?". Lee dijo. "Datos. La pregunta es, '¿Qué datos quieres obtener?' Depende de lo que quieras analizar. Necesitamos entender el contexto y el contenido, y además formular un modelo de relación entre las incógnitas invisibles”.
Oculto en los datos hay un significado sobre el comportamiento desviado de una máquina o un proceso. Desbloquear ese significado conduce a predecir la calidad, determinar la estabilidad de la máquina o el proceso y prevenir fallas potenciales. “De eso se trata exactamente Industria 4.0 hoy en día”, dijo Lee.
El término "Industria 4.0", por supuesto, no se popularizó hasta la época de la iniciativa del gobierno alemán en 2013.
Ningún accidente desde 2006
Una vez en Toyota, Lee y su equipo de analistas de datos se unieron a Rucker y un grupo de trabajadores de mantenimiento calificados e ingenieros de planta para abordar el problema del sistema de aire comprimido.
La simplicidad de sus preguntas desmentía la complejidad de la tarea que tenían por delante.
“¿Podemos predecir un problema de flujo inverso antes de que provoque un choque?” Rucker dijo. "¿Podemos ver algo en desarrollo a tiempo para hacer algo al respecto?"
Durante meses de prueba y error en 2005, el equipo recopiló y analizó datos de alta fidelidad de uno de los compresores y buscó anomalías. A veces, el equipo creaba una sobretensión o una condición de aproximación a la sobretensión para poder obligar a la máquina a comenzar a exhibir un comportamiento desviado y ver cómo se veía en el conjunto de datos.
Finalmente, el trabajo del equipo dio sus frutos. Sus miembros vieron que el mejor predictor de una condición de sobretensión incipiente ocurrió en la etapa dos (de las cuatro etapas por las que pasa el compresor que progresan desde la presión normal hasta 120 libras de presión por pulgada cuadrada, o PSI).
"¿Cuál es la física detrás de eso, por qué es este el predictor?" dijo Rucker. “No sé, no me importa. Acabamos de ver que esto predice de manera confiable un aumento repentino en el futuro, y lo predice con segundos de advertencia”.
El siguiente paso fue colocar un sensor diferencial en cada compresor y crear un algoritmo de aprendizaje automático para la unidad de control central. Las pruebas confirmaron que tan pronto como la etapa dos comenzara a "tambalearse", el compresor comenzaría a retroceder.
“Cada vez que lo probamos, nos mantuvo fuera de problemas”, dijo. "No hemos tenido accidentes desde 2006".
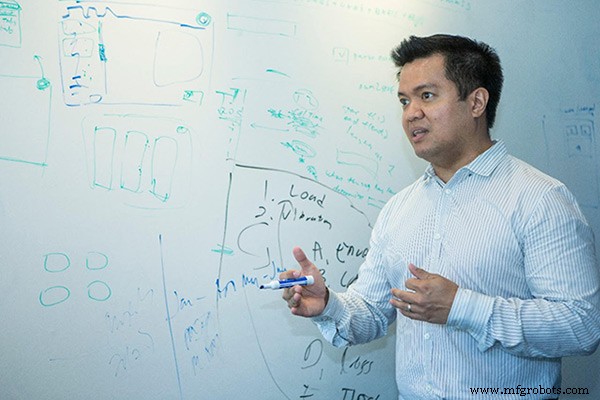
Si bien el proyecto de sobretensión del compresor fue un éxito, fracasó otro que se centró en tratar de predecir la vida útil de los cojinetes en los gigantes de aire comprimido. El equipo no pudo encontrar suficientes datos de mantenimiento confiables y emparejarlos con datos operativos de la máquina para establecer correlaciones útiles, dijo Rucker.
“Esa es probablemente la combinación correcta de I + D”, dijo. “Intentas cosas y no sabes si funcionarán o no. Y si la mitad de las veces recupera su dinero, eso es una victoria. Y de vez en cuando encuentras uno que paga todo lo demás, como el control de sobrevoltaje”.
La flexibilidad es clave
Posteriormente, Lee publicó un artículo sobre el proyecto Toyota y, en 2013, ayudó a cofundar Predictronics con Patrick Brown, un empleado de Intelligent Maintenance Systems, y dos de sus estudiantes universitarios, David Siegel y Edzel Lapira. Marrón. Lapira y Siegel forman la suite Predictronics C.
Al igual que Rucker de Toyota pidió ayuda a Lee con IA, las empresas acuden a Predictronics en busca de ayuda con sus aspiraciones de tiempo de inactividad cero.
“Diferentes clientes suelen estar en diferentes niveles de madurez”, dijo Lapira, quien es directora ejecutiva. “Tenemos algunos clientes que ya cuentan con una estructura de recopilación de datos:tienen un lago de datos pero no saben qué hacer con los datos. También tenemos algunos clientes que tienen que empezar de cero”.
Los clientes con activos de 50 o 60 años deben comenzar en una etapa aún más temprana.
Cada vez más, Predictronics es abordado por clientes con máquinas heredadas. Lapira y sus colegas los envían a comprar componentes como acelerómetros y transductores.
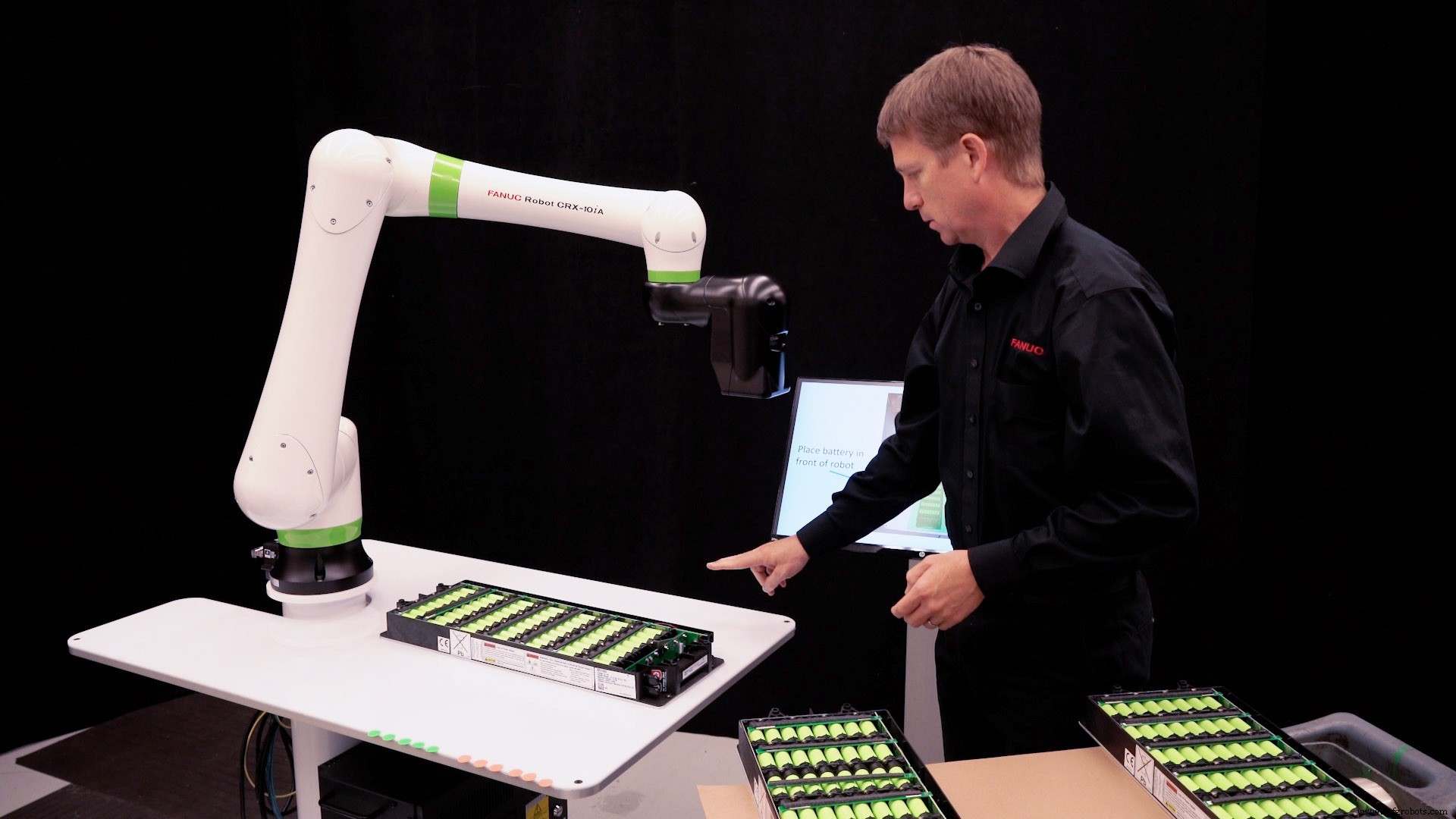
"Estos son los diferentes convertidores de analógico a digital que necesitamos para obtener esos datos", dijo.
Desde su fundación en 2013, Predictronics ha ayudado a más de 70 fábricas con soluciones de IA, muchas de ellas empresas Fortune 500.
Predictronics trabajó con un cliente, un fabricante de semiconductores, para establecer una solución predictiva de metrología virtual que pudiera aprender la relación entre el sensor y las variables de medición.
El proyecto fue un desafío debido a los cientos de señales medidas emitidas por el equipo de semiconductores.
Pero existen métodos estadísticos bien conocidos para reducir el número de posibilidades, dijo Siegel.
“Además de esos métodos, en los últimos años ha sido más la comunidad de aprendizaje automático la que ha desarrollado métodos que incorporan un algoritmo de regresión de clasificación que tiene una parte de selección de variables incorporada”, dijo. “Eso lo reduce a las 10, o 20 o 30 variables principales. Luego, trabaja con el cliente o usa su propio conocimiento para determinar qué tiene más sentido incluir en el software y el modelo de análisis”.
Ya sea que Predictronics aplique el conocimiento obtenido de la experiencia previa en su enfoque basado en plantillas, lo que ayuda a mantener los costos bajos, o una solución formulada en una parte de una empresa que luego se puede escalar internamente, "encontrar una solución que aborde directamente los problemas más críticos". pero también es lo suficientemente flexible como para aplicarse a otros problemas es clave”, dijo Brown.
IA de diligencia debida
Las fábricas que están buscando un proveedor de soluciones de inteligencia artificial como lo hizo Toyota para su problema de aire comprimido deben hacer su debida diligencia para encontrar la solución adecuada.
Es útil saber qué preguntas hacer, dijeron los expertos de Predictronics:
¿Dónde se han utilizado sus servicios antes?
¿Ha demostrado su solución una clara mejora en las operaciones comerciales en términos de reducción del tiempo de inactividad o aumento de la calidad?
¿Se ha utilizado su solución en mi industria?
¿Tu equipo tiene conocimiento del dominio industrial?
¿Su solución funciona con equipos heredados?
¿Su solución funciona con una variedad de sensores?
¿Su solución utiliza el aprendizaje automático?
¿Cuántos datos requiere para entrenar el modelo?
¿Necesita solo datos de una máquina en buen estado o datos de una máquina degradada o defectuosa también para aprender?
Los robots también quieren IA
Si bien las máquinas herramienta en un taller funcionan mejor bajo la influencia de la IA, no hay motivo por el cual los robots no puedan hacer lo mismo.
Fanuc America agregó recientemente "A prueba de errores de IA" a su controlador de robot y la función de visión de los robots, iRVision, que utiliza el aprendizaje automático (ML) para la inspección de piezas.
Con la capacidad de prueba de errores, un operador usa imágenes para entrenar al ML para verificar dos situaciones distintas, si una tuerca soldada está presente o ausente, por ejemplo, y aceptar o rechazar una pieza.
Debido a que iRVision puede admitir hasta 27 cámaras, la función de detección de errores puede actuar en tantos puntos del proceso de fabricación.
"Desea identificar los rechazos o errores antes de continuar agregando valor a una pieza defectuosa", dijo Josh Person, ingeniero de personal en el grupo de visión artificial de Fanuc.
"A menudo, puedes ver un error en una etapa y la siguiente etapa lo cubriría", agregó.
Durante la configuración, el operador puede presentar varios ejemplos de piezas de trabajo y clasificarlas en dos categorías:buenas y malas. Si el ejemplo no cae en ninguna clase, generará "indeterminado". Luego se pueden agregar ejemplos indeterminados para mejorar el modelo aprendido.
Sistema de control de automatización
- VISTA:Para ciegos
- Evaluación de las ventajas de DevOps para las pruebas de rendimiento de IoT
- Automatización:lo que significa para el futuro de los negocios
- El futuro de la entrega sin contacto
- ¡Gracias por los recuerdos!
- Los beneficios de la automatización para su negocio
- Cómo elegir el filtro adecuado para su aplicación
- Cinco formas de encontrar el compresor adecuado para el aficionado al hogar
- Directrices para seleccionar el proveedor de servicios de aire comprimido adecuado
- Damos la bienvenida a Dorothy Parnell como autora del blog The Compressed Air Blog
- Programa de verificación de rendimiento de CAGI para compresores rotativos