Compañía de robots crea software compatible con la Industria 4.0
FANUC ha hecho realidad una de las promesas de la Industria 4.0, la del mantenimiento predictivo de los equipos de fábrica, con su solución IoT Zero Down Time. ZDT se puede aplicar a cualquiera de los brazos robóticos de FANUC y sus periféricos.
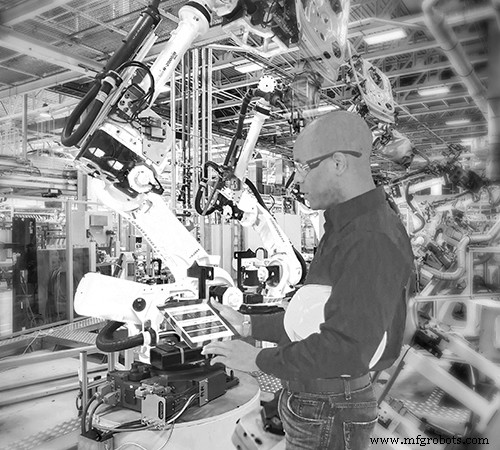
Para ayudar con el resto de la automatización en una fábrica, más adelante este año, la empresa de robótica pondrá a disposición el sistema Intelligent Edge Link and Drive (FIELD) de FANUC, una plataforma gratuita y de código abierto para que los desarrolladores externos la utilicen para escribir aplicaciones que recopilará y analizará datos de otros equipos automatizados.
Fabricación inteligente se reunió con Joe Gazzarato, director de ingeniería de ZDT en FANUC America, para obtener más información.
Joe, ¿de qué se trata ZDT?
"ZDT" significa "Tiempo de inactividad cero". Ahora que los fabricantes trabajan constantemente, las 24 horas del día, los 7 días de la semana, los 365 días del año, tratando de satisfacer la demanda, cualquier tiempo de inactividad inesperado puede costarles producción. Con ZDT estamos monitoreando la salud mecánica, del sistema y del proceso de nuestros robots para eliminar el tiempo de inactividad inesperado.
Tenemos más de 21 000 robots conectados a ZDT en más de 100 ubicaciones de clientes en 16 países diferentes.
Monitoreamos esos robots y si nuestro análisis predice un problema, nuestro sistema ZDT notificará al cliente y a nuestro equipo de servicio para que podamos abordar el problema antes de que ocurra un tiempo de inactividad inesperado. Ya hemos ahorrado a los clientes más de 85 millones de dólares al identificar problemas que creemos que habrían provocado un tiempo de inactividad inesperado.
¿Cómo lograste esto?
Llevamos poco más de cuatro años trabajando en ZDT. Comenzamos con solo 500 robots, con 50 robots en cada una de las 10 ubicaciones.
Creamos software para nuestros robots que producen mensajes que contienen datos importantes. Esos robots envían sus mensajes a un recolector de datos que está dentro de la fábrica del cliente. Los datos ZDT
El trabajo del recopilador es cifrar y enviar los mensajes salientes a nuestro centro de datos en la nube, donde se almacenan y analizan automáticamente mediante programas escritos por nuestros ingenieros.
Si uno de los análisis determina que hay un problema, se envían correos electrónicos al cliente y a nuestro equipo de servicio y uno de nuestros técnicos de servicio llama al cliente para asegurarse de que comprenda el significado de la alerta, cómo confirmarla y cómo abordarla. Además, si el cliente necesita asistencia, el técnico puede hacer arreglos para que se envíen piezas o soporte al sitio para que podamos abordar el problema antes de que ocurra un tiempo de inactividad.
¿Qué tecnologías específicas hacen posible ZDT?
El recopilador de datos ZDT tiene requisitos de ancho de banda muy bajos. Algunas otras implementaciones en torno a big data transmitirán datos constantemente a una velocidad de milisegundos. ZDT no está diseñado así. Recopilamos menos de 500 megabytes de datos del robot en un año. Además, el recopilador de datos puede ejecutarse en una computadora pequeña. No requiere muchos recursos informáticos.
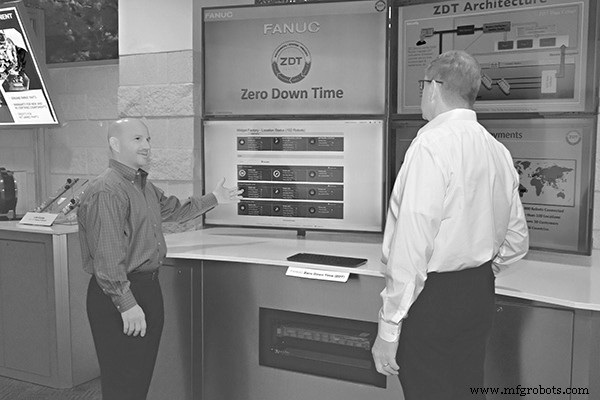
Otra clave es nuestra infraestructura en la nube. Las herramientas que usamos para ingerir y almacenar los datos para el análisis son realmente importantes. Nos aseguramos de que los datos estén organizados de manera que se mantengan seguros cuando se almacenen y sean eficientes para que los utilicen nuestros programas analíticos.
Nuestros análisis son probablemente una de las partes más importantes de ZDT y la clave de nuestro éxito hasta el momento. Están escritos por los mismos ingenieros que desarrollan nuestro software de controlador de robot. Los ingenieros de FANUC con años de experiencia en robótica han escrito los programas analíticos que analizan los datos que hemos recopilado. Su experiencia en la creación de software para robots les ha ayudado a ser muy buenos en la redacción de análisis a partir de los datos producidos por nuestros robots.
¿Hay otros usos para los datos que recopila en el proceso ZDT?
ZDT también hace muchas otras cosas. Hemos creado muchas funciones para ayudar a los clientes a aumentar su productividad, optimizar sus recursos de mantenimiento, reducir su esfuerzo de soporte y extender la vida útil de sus robots.
Un buen ejemplo es nuestra analítica de cambio de proceso. Una experiencia común para muchos de los que hemos trabajado con equipos de automatización es presentarnos en el lugar de trabajo y encontrar que su sistema no está funcionando o está haciendo algo diferente a lo que estaba haciendo el día anterior. Y preguntas y obtienes la misma respuesta. "No lo toqué" o "Nadie cambió nada". Sin ZDT, las personas tienen que realizar su propio análisis para descubrir qué ha cambiado.
Con ZDT, nuestros clientes saben con certeza si se cambió alguno de sus robots porque estamos registrando todo tipo de datos de los robots todos los días. Cuando se cambia un robot, sabrán exactamente qué programa o configuración se cambió, junto con la fecha y la hora en que sucedió, por lo que probablemente puedan determinar quién realizó el cambio y también conocen el valor original. Todo esto hace que sea realmente fácil para el cliente volver a colocar las cosas muy rápidamente.
¿Mis datos están seguros?
El recopilador de datos ZDT, que puede ser bloqueado por el firewall del cliente, encripta los datos a medida que se envían a nuestro centro de datos y es un servicio de salida únicamente.
Además, piense en ZDT como de solo lectura. Solo podemos ver la información recopilada por los robots. No podemos cambiar nada.
Cuando FANUC dice que los usuarios de ZDT pueden acceder a la información de diagnóstico en toda la empresa, ¿se refiere a los robots y no a otros equipos de la fábrica?
Por lo general, pero en realidad diseñamos ZDT para que los clientes puedan rastrear algunos de sus equipos periféricos.
Digamos que el paquete de vestimenta de un robot incluye líneas de aire externas y cables eléctricos que transportan energía hasta el extremo de las herramientas del brazo. Puede asociar el desgaste del paquete del vestido con los datos del robot. Por ejemplo, después de que el robot se haya movido tantos miles de grados o haya torcido la muñeca miles de veces, ZDT puede notificar al cliente que se ha cumplido la condición y puede enviar a alguien a inspeccionar el paquete del vestido.
Sin ZDT, puede realizar el mantenimiento periódicamente, pero con ZDT lo inspeccionaría en función de cómo se usa el robot. Por lo tanto, los clientes optimizan el uso de sus recursos de mantenimiento y realizan el mantenimiento cuando es necesario y no solo por el tiempo transcurrido.
Además, aunque ZDT no recopila datos de otros equipos, FANUC se está preparando para lanzar tecnología a finales de este año que está diseñada para hacer precisamente eso.
¿Cómo describiría el sistema FIELD?
FIELD es una plataforma que estamos lanzando en los EE. UU. este año. Está diseñado para recopilar datos de cualquier componente habilitado para la red, incluidos robots, controladores de soldadura, PLC y sensores, y no necesariamente equipos de FANUC. Cualquier dispositivo habilitado para red en una instalación puede compartir sus datos con el sistema FIELD, que se ejecutará internamente en la planta.
FANUC pone a disposición kits de desarrollo de software para que terceros puedan escribir aplicaciones que accedan a esos datos y hagan cosas que brinden valor al cliente. ZDT es un ejemplo del valor que FANUC proporciona mediante el uso de este tipo de datos, pero creemos que hay millones de posibilidades de lo que las personas pueden hacer con los datos de los equipos de fabricación. El sistema FIELD está diseñado para que otras empresas puedan desarrollar sus propias aplicaciones y venderlas a los fabricantes.
Hay dos servidores diferentes disponibles para el sistema FIELD. Uno, el FIELD Base Pro, puede conectar hasta 30 dispositivos. También admitimos un servidor de computación unificado de Cisco que puede admitir hasta 150 conexiones de dispositivos. Se pueden agrupar para que la información se pueda compartir entre los servidores.
Existen muchas plataformas de IoT diferentes, pero el sistema FIELD de FANUC es único por varias de las ventajas que ofrece.
- Funciona dentro de la fábrica. Otros se ejecutan en la nube, como lo hace ZDT. Dado que las aplicaciones FIELD se ejecutarán dentro de la fábrica, las aplicaciones pueden responder mucho mejor. Obtienen sus datos casi en tiempo real y pueden analizarlos y tomar decisiones muy rápidamente. Tampoco dependen de una conexión a Internet.
- FANUC ha hecho que la plataforma FIELD sea completamente abierta. Habrá una Asociación de socios del sistema FIELD donde las personas que deseen escribir aplicaciones o integrar el sistema FIELD en sus sistemas o con sus dispositivos podrán hacerlo. No hay ningún costo por ser miembro.
- El sistema puede conectarse a cualquier dispositivo habilitado para red. Muchas de las otras plataformas que existen admiten solo unos pocos protocolos o un par de protocolos estándar, pero FANUC también incluye la capacidad para que los fabricantes de dispositivos escriban su propio protocolo. Entonces, si no hay un controlador existente para conectar su dispositivo al sistema FIELD, puede crear uno. Y ese kit de desarrollador está disponible gratuitamente para los fabricantes de dispositivos.
La idea es crear esta comunidad de dispositivos y desarrolladores de aplicaciones para mejorar las capacidades de fabricación.
Sistema de control de automatización
- Soluciones de software de Industria 4.0:¿Quién sabe mejor que los usuarios?
- GE lanzará $ 1.2B IIoT Company
- Sepro lanza aplicaciones para mejorar el software del robot
- Collaborative Robot Marketplace agrega software de monitoreo
- El auge de los robots:invertir en automatización disruptiva
- El software de B&R aprovecha mejor el potencial de los robots
- Mitsubishi Electric adquirirá la empresa estadounidense de software Iconics
- Verizon adquirirá una empresa de software de robots móviles autónomos
- El moderno software HMI impulsa la Industria 4.0
- Epson crea un robot autónomo de dos brazos para la fabricación de alta tecnología
- El intercambio de conocimientos en la empresa, en la industria