Salón Aeronáutico de París 2019:Lo más destacado
La exhibición estática del avión militar Airbus A400M de uso intensivo de materiales compuestos en el Salón Aeronáutico de París 2019. Fuente | CW
Las expectativas fueron variadas para el Salón Aeronáutico de París 2019 (17-23 de junio). Se esperaba que Boeing sentara más bases para el nuevo avión mediano (NMA), pero la crisis del 737 MAX ha consumido gran parte de la energía y la atención de la empresa. De hecho, el primer día de la exhibición aérea, Boeing hizo un anuncio muy general sobre las condiciones comerciales y emitió su pronóstico de aviones comerciales a 20 años. Nada en NMA. El mayor revuelo que causó Boeing durante el espectáculo fue la noticia de que había vendido 200 aviones 737 MAX a International Airline Group (IAG).
Airbus, por otro lado, anunció el A321XLR (LR =largo alcance), la última versión del A320neo. Programado para entrar en servicio en 2023, el A321XLR tendrá un alcance de 4,700 millas náuticas, alcanzable a través de una capacidad adicional de almacenamiento de combustible. Airbus dijo que la gama del avión proporcionará a las aerolíneas opciones de pasillo único menos costosas en rutas que ahora son servidas principalmente por aviones de pasillo doble más costosos. Estas rutas incluyen Nueva York-Río, Shanghái-Sídney y Madrid-Dubái.
A pesar de la falta de noticias de la NMA, entre las empresas relacionadas con los materiales compuestos que exponen en el Salón Aeronáutico de París, queda un esfuerzo definitivo para desarrollar y alinear materiales y tecnología de proceso para satisfacer las demandas que Boeing y Airbus coloquen en la cadena de suministro en la próxima década. Esto incluye preimpregnados termoendurecibles tradicionales con curado en autoclave, infusión de resina líquida de fibras secas con curado fuera del autoclave, compuestos termoplásticos y fabricación aditiva. La sensación de expectativa en toda la cadena de suministro es palpable.
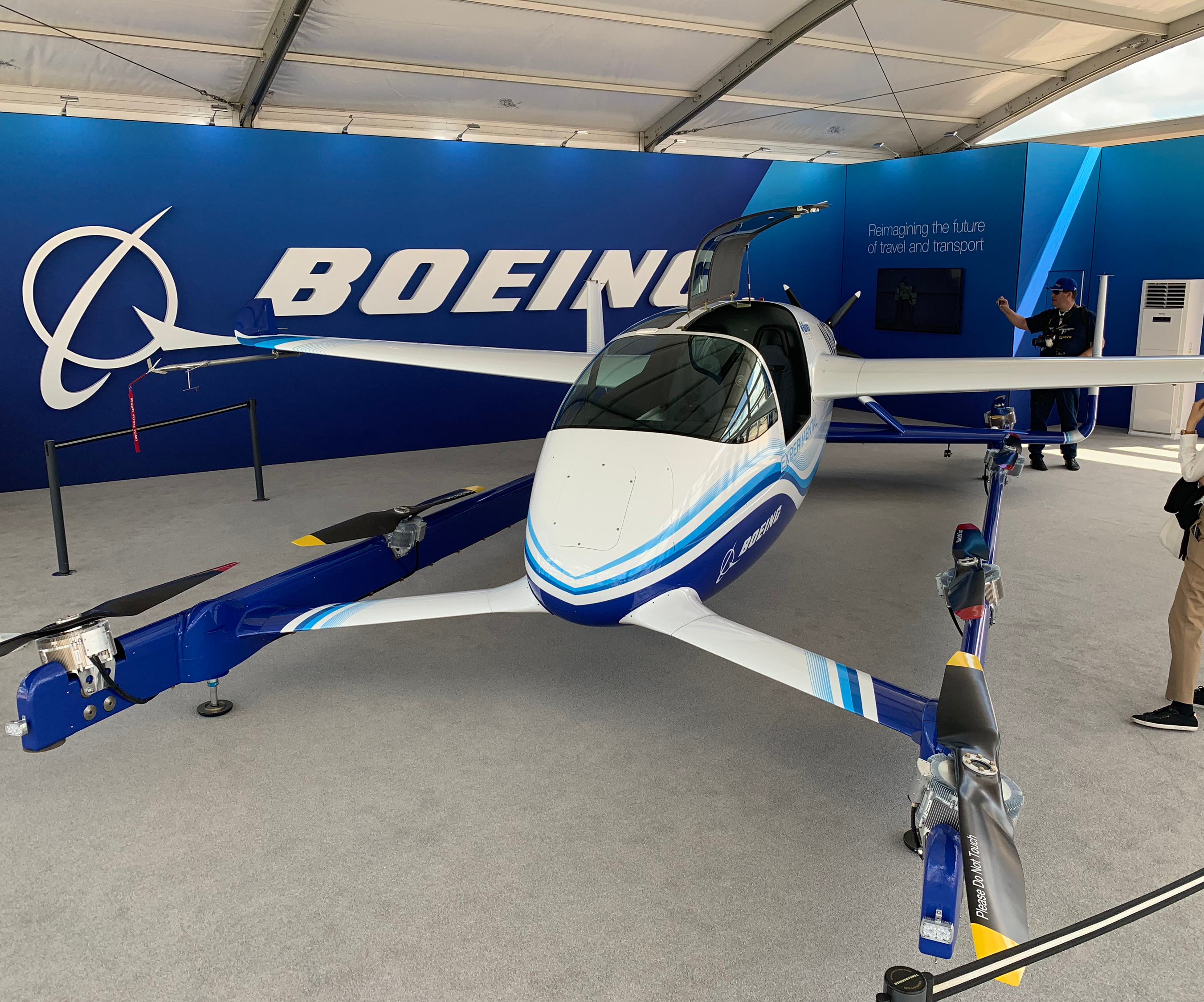
En la línea de vuelo, había la variedad habitual de aviones comerciales, militares y civiles, con demostraciones de vuelo diarias. En el aire se destacaron las demostraciones de aviones de propulsión eléctrica, que eran un marcado y silencioso contraste con el rugido ensordecedor asociado con los aviones de combate y comerciales. En las pantallas estáticas, había varias naves EVTOL (despegue y aterrizaje verticales eléctricos) dirigidas al mercado de la movilidad urbana. Este tipo de avión, en particular, está demostrando ser un objetivo importante de los materiales compuestos, que son una necesidad para los vuelos con propulsión eléctrica. Sin embargo, es probable que los volúmenes de producción de algunas de estas plataformas asciendan a miles por año, lo que impulsa las tecnologías de materiales y procesos más hacia un modelo de producción de tipo automotriz. Dicho esto, los EVTOL están en su juventud, particularmente dados los obstáculos regulatorios, de calificación y de gestión del espacio aéreo que aún no se han superado.
A continuación se muestran los aspectos más destacados del programa.
Spirit AeroSystems. El constructor de aviones más grande del mundo, Spirit AeroSystems (Wichita, Kansas, EE. UU.), Comenzó el espectáculo la madrugada del lunes con una conferencia de prensa anunciando la introducción de su panel de fuselaje ASTRA (Tecnología de Estructuras Avanzadas y Arquitectura Revolucionaria), diseñado para mostrar cómo un compuesto completamente El fuselaje podría diseñarse para cumplir con los requisitos de rendimiento, tarifas y costos de un avión de pasillo único de próxima generación. El diseño y la fabricación de ese panel se tratan en una historia independiente aquí.
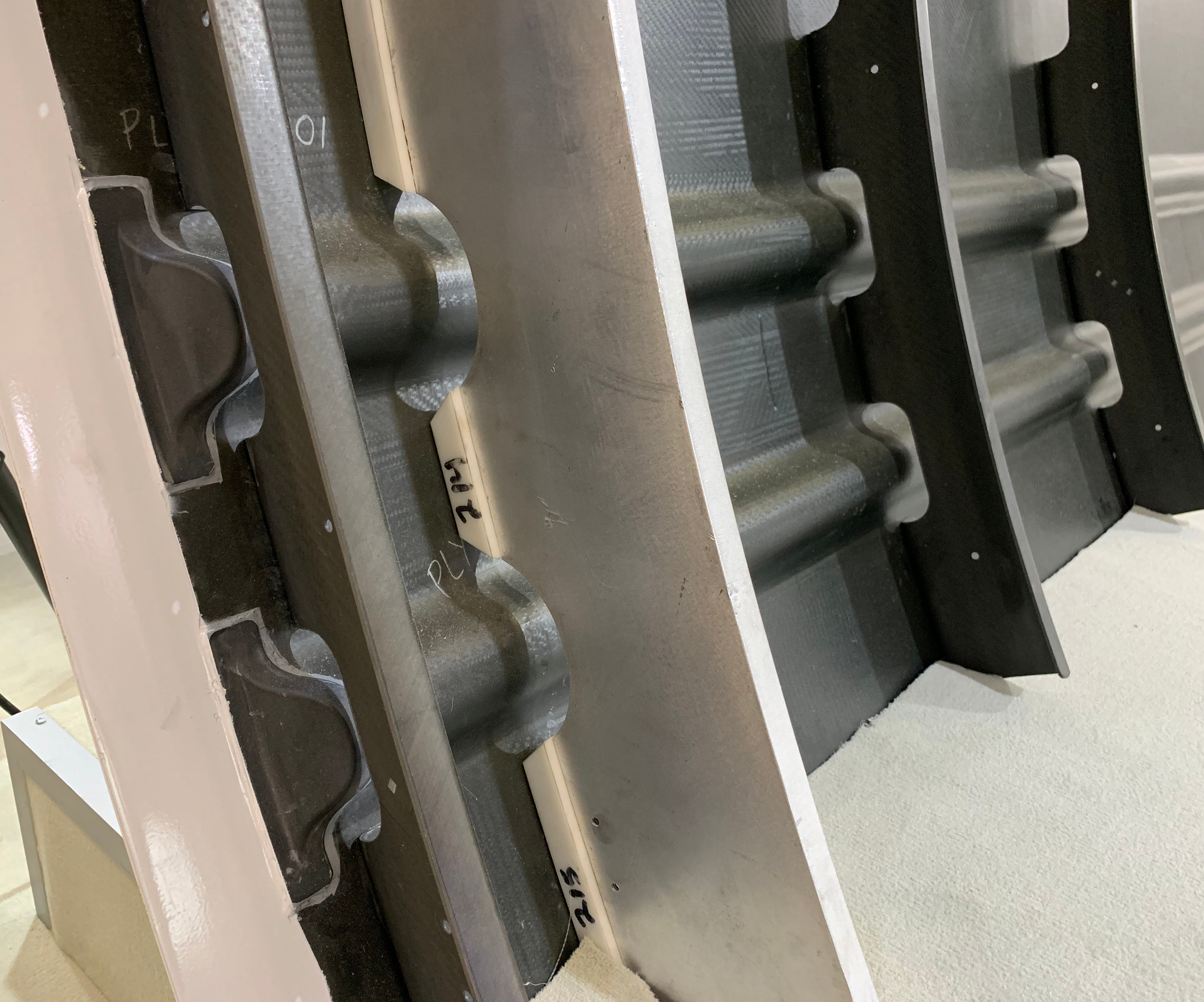
MTorres. Otro panel compuesto destacado de la feria se ha encontrado en el stand de MTorres (Torres de Elorz, Navarra, España). Esta "estructura de rejilla / piel" reforzada con nervaduras, fabricada mediante infusión de resina de fibras de carbono secas, en realidad es una creación de Stephen Tsai, veterano de los composites y profesor emérito de aeronáutica y astronáutica en la Universidad de Stanford, que estuvo en el stand de MTorres para explícalo. Tsai dijo que concibió este diseño hace varios años y lo basó en la estructura de rejilla / revestimiento implementada en la fabricación de Vickers Wellington , un bombardero británico de la Segunda Guerra Mundial fabricado por Vickers-Armstrongs y famoso por mantener la integridad estructural en accidentes. Para darle vida a este diseño en una aplicación compuesta, Tsai diseñó las nervaduras en una estructura de celosía, con cada nervadura de un ancho y alto fijos, y el espacio entre las nervaduras también fijo.
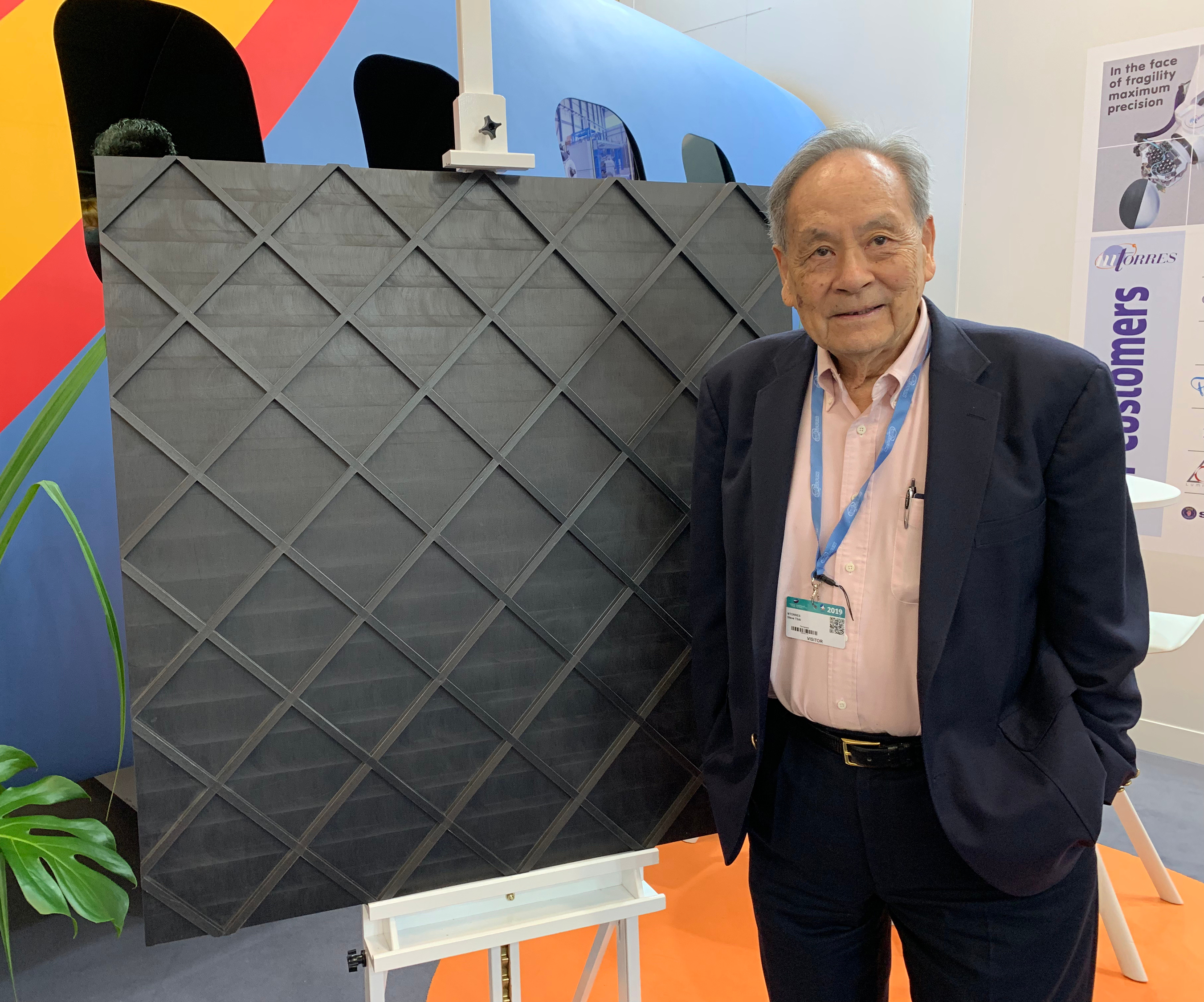
Steve Tsai se para con el panel reforzado con nervaduras que diseñó y MTorres lo ayudó a fabricar. El factor clave es la colocación precisa de la fibra para construir las nervaduras. Fuente | CW
El desafío de su diseño, dijo Tsai, era desarrollar intersecciones de nervaduras que pudieran soportar grandes cargas mecánicas. Lo que se le ocurrió fue una arquitectura de nervadura que utiliza cintas de fibra de carbono colocadas continuamente en una dirección (llámela A) y discontinuamente en la dirección de intersección (llámela B). Luego, para la siguiente capa, las cintas se colocarían discontinuamente en la dirección A y continuamente en la dirección B. Este patrón continuará hasta que se alcance el grosor deseado de la nervadura. De esta forma, cada junta de nervadura estaría siempre atravesada por una cinta continua. Una vez que las nervaduras están construidas en la herramienta, se coloca una piel sobre ella mediante la colocación automática de fibra (AFP) o la colocación automática de cinta (ATL) y toda la estructura se cura conjuntamente.
Las ventajas de este diseño, dijo Tsai, son varias, pero la principal es que es "difícil que el daño vaya más allá del área localizada", lo que significa que una grieta propagada en la piel no puede migrar fácilmente más allá de cualquiera de las costillas que bordean el regiones afectadas. Tsai también dijo que la estructura de rejilla / revestimiento es muy eficiente en cuanto a peso y material. Aún así, señaló, "Esto es fácil de diseñar pero difícil de hacer". Ahí es donde entra MTorres.
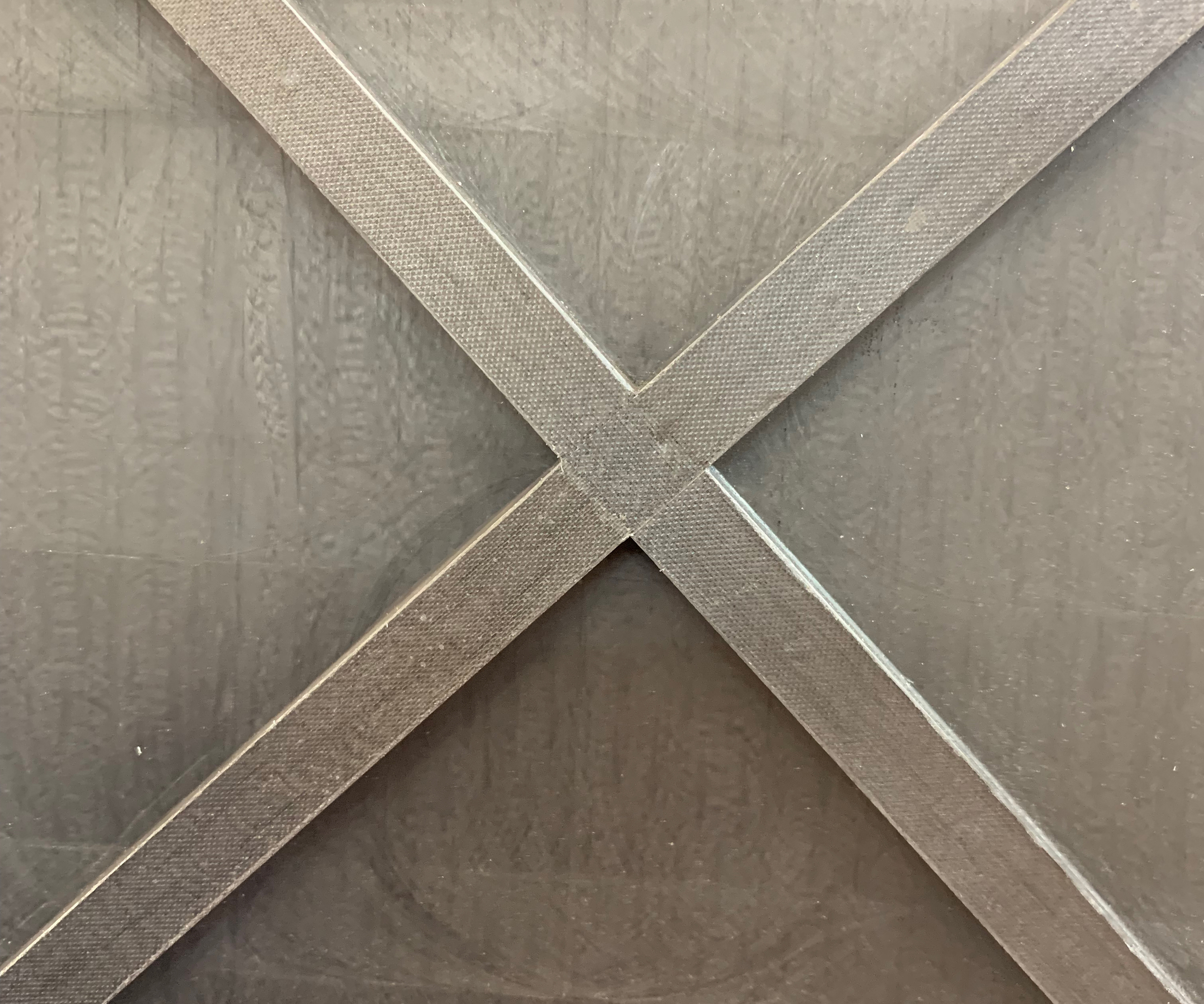
Tsai dijo que el factor limitante en la fabricación de su diseño de panel había sido la colocación de las cintas de nervadura. Para ser completamente industrializados, necesitaban una velocidad de corte y una precisión en la colocación de la cinta que, hasta hace poco, no habían sido posibles. Sin embargo, Tsai se acercó a MTorres con su diseño y le preguntó si el especialista de ATL / AFP podía hacer el trabajo. Iñigo Idareta, jefe del departamento de proyectos especiales de la empresa, y el equipo de composites de MTorres se pusieron manos a la obra y trabajaron con Tsai para adaptar las tecnologías de MTorres a la aplicación. Hubo dos desafíos, dijo Idareta en la exhibición aérea:ajustar la velocidad y precisión de corte de colocación de la cinta, donde la capacidad de corte sobre la marcha AFP de MTorres fue clave para mantener una alta velocidad de laminado constante; y desarrollo de soluciones de herramientas que permitieron la acumulación de cada nervio sin que el nervio perdiera la integridad de la pila. Además, el uso del propio formato de fibra de carbono seco de MTorres para aplicaciones de AFP era necesario para que esta infusión desafiante funcionara. Todo se logró, dijo Idareta. También se logra, según el diseño de Tsai, el uso de la colocación de fibra fuera de ángulo de la piel del panel, que tiene cuatro capas y aproximadamente 1,2 mm de grosor.
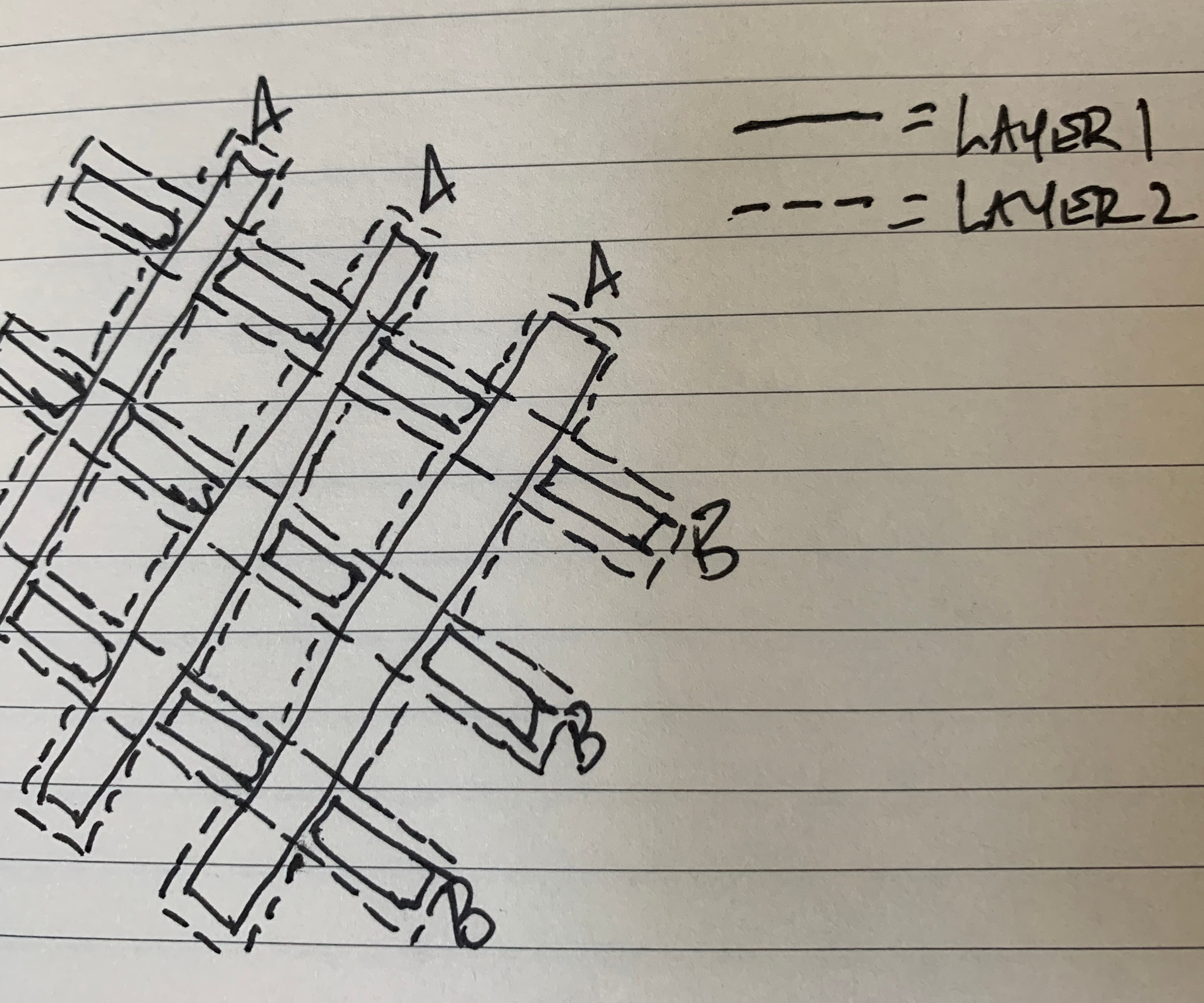
La fibra de carbono utilizada fue un material seco 50K de Mitsubishi Chemical Carbon Fiber &Composites Inc. (Sacramento, California, EE. UU.), Elegido principalmente porque resultó ser el material que MTorres tenía a mano. La resina era un epoxi endurecido de grado industrial "estándar". Idareta dice que el panel fue probado por Alan Nettles en la NASA y funcionó bien. La unión entre costillas y piel en particular, dijo, fue excelente. Tsai admitió que el punto débil del panel es la junta de nervadura, que es un laminado de capas cruzadas [0/90]. Las costillas eran todas [0]. De modo que las juntas tenían aproximadamente la mitad de la resistencia a la tracción uniaxial y un poco más de la mitad de la resistencia a la compresión uniaxial. Incluso con esa debilidad, la resistencia de la rejilla / revestimiento es más del doble de la tecnología de aluminio actual del mismo diseño, sin contar el peso adicional más ligero de los compuestos. Tsai también dijo que el aluminio, para lograr las mismas propiedades de resistencia que proporciona su diseño, pesaría tres veces más.
¿Qué sigue para esta tecnología? Tsai dijo que está "listo para su aplicación" y enumeró varios tipos de piezas posibles:estructuras de fuselaje, carrocerías de vehículos de lanzamiento espacial, paneles de automóviles, cajas de baterías. Idareta dijo que MTorres está trabajando en la iteración del diseño, incluido el desarrollo de un panel curvo y un panel de barril completo. Ambos, dijo, están al alcance.
Además, hay varios aspectos del diseño de Tsai que podrían modificarse para adaptarse a una variedad de casos de carga. Estos incluyen el ancho de la nervadura, la altura de la nervadura, el ángulo de intersección y el espacio entre las nervaduras. Además, aunque MTorres usó infusión para hacer el panel que se exhibió en la exhibición aérea, podría fabricarse usando preimpregnados termoestables tradicionales.
GKN Aerospace. El especialista en alas comerciales GKN Aerospace (Redditch, Reino Unido) anunció en la exhibición aérea que ha fabricado las primeras piezas para su parte del trabajo en el programa Airbus Wing of Tomorrow, un programa de cinco años (2018-2022), multiempresa, Reino Unido. Esfuerzo de Catapult para desarrollar materiales y tecnologías de proceso para la fabricación de alta velocidad (100 por mes) de alas compuestas de fibra de carbono con infusión de resina que se desplegarán en un avión de pasillo único de próxima generación.
Paul Perera, vicepresidente de tecnología de GKN Aerospace, estuvo en la exhibición aérea y brindó más detalles sobre el programa. Dijo que GKN actualmente tiene 60 personas trabajando en el larguero y las costillas del ala, y que la mayor parte del trabajo se realiza desde el Centro de Tecnología Global de GKN, que se mudará a nuevas instalaciones en Filton, Reino Unido, a finales de este año.
El larguero será fibra seca colocada por GKN y luego infundida. Las nervaduras se fabricarán tanto con compuestos termoplásticos como con aluminio. El National Composites Centre (Bristol, Reino Unido) está trabajando en varias tecnologías para Wing of Tomorrow, incluido iCAP (programa de adquisición de capacidad digital) para desarrollar soluciones de automatización basadas en datos, así como sistemas de colocación y corte de fibra automatizados desarrollados por Loop Technology (Poundberry , Dorchester, Reino Unido) que se empleará en la fabricación de alas. Northrop Grumman (anteriormente Orbital ATK, Clearfield, Utah, EE. UU.) Está desarrollando larguerillos para el programa. Los revestimientos de las alas inferiores serán fabricados por Spirit AeroSystems en sus instalaciones de Prestwick, Escocia; Airbus fabricará los revestimientos de las alas superiores. El objetivo es la entrega de tres conjuntos de buques a la planta de alas de Airbus en Broughton, Reino Unido, para su ensamblaje en los próximos 18 meses, el primero en junio de 2020, el segundo a fines de 2020 y el tercero a principios de 2021. En última instancia, si el programa avanza Como estaba planeado, demostrará que la infusión de resina es un proceso viable para la producción de alta velocidad de un ala compuesta para un pasillo único de próxima generación. Perera dice que las secciones de larguero de 1 metro producidas y evaluadas en las instalaciones de GKN en la Isla de Wight, Reino Unido, muestran que los materiales y el proceso se ajustan bien a la aplicación.
Perera señaló que una parte importante del programa Wing of Tomorrow girará en torno al desarrollo de la automatización. De hecho, dijo, la automatización será un habilitador clave de la infusión de resina para la fabricación aeroespacial de próxima generación.
Materiales compuestos Solvay. Si está buscando evidencia de cómo el enfoque en la industrialización de la fabricación aeroespacial y la eficiencia de la producción está llegando a los proveedores de materiales, no busque más allá de Solvay Composite Materials (Alpharetta, Ga., EE. UU.), Que se encuentra en medio de un período de varios años. Esfuerzo para reevaluar dónde y cómo produce resinas, cintas y preimpregnados de grado aeroespacial. El énfasis de Solvay está en el desarrollo de una estrategia de operaciones centrada en instalaciones que producen menos números de productos en equipos altamente especializados que pueden cumplir con los requisitos de velocidad y calidad de los aviones de próxima generación. Marc Doyle, vicepresidente ejecutivo aeroespacial de Solvay, dice que las nuevas instalaciones de la compañía en Wrexham, Gales, Reino Unido, son un símbolo de este esfuerzo. Esa planta, que se inauguró en septiembre de 2018, produce solo dos números de producto (adhesivos), pero en un entorno altamente estructurado, altamente optimizado y dominado por la automatización, diseñado para cumplir con los requisitos justo a tiempo de sus clientes. La compañía espera seguir este modelo con todas las nuevas instalaciones y también intentará convertir las plantas heredadas.
En el frente de la innovación de materiales, Solvay destacó dos esfuerzos notables, uno centrado en los termoplásticos y el otro en las fibras de carbono. Mike Blair, vicepresidente ejecutivo de investigación e innovación, dijo que uno de los mayores desafíos / oportunidades de los termoplásticos es su delta de alta temperatura; es decir, las altas temperaturas de proceso de los termoplásticos pueden causar problemas de coeficiente de expansión térmica (CTE) en las piezas a medida que se enfrían, en particular las piezas grandes. ¿La meta? Modificar la química de la policetona para reducir las temperaturas del proceso, sin afectar la transición vítrea (T g ) temperatura. La compañía también está buscando formas de impulsar la procesabilidad y la manipulación en equipos automatizados de sus termoplásticos. “Nuestros materiales PEEK y PEKK estándar funcionan realmente bien”, dijo Blair. "Solo tenemos que modificarlos para que sean más adaptables".
La innovación que rodea a las fibras de carbono es igualmente intrigante. En 2017, Solvay adquirió al fabricante de poliacrilonitrilo (PAN) de remolque grande European Carbon Fiber GbmH (Kelheim, Alemania), lo que le dio a Solvay un nuevo y saludable suministro de PAN para fibra de carbono de remolque de 50K. Ante esto, se planteó el desafío:¿Se puede formatear una fibra de carbono de remolque grande para proporcionar las características de rendimiento de una fibra de carbono de remolque pequeño de módulo intermedio (IM)? Blair dijo que la idea invita a la reflexión, pero no trivial. Señaló que el solo hecho de manipular la fibra de remolque de 50K puede, en sí mismo, dañar la fibra. Entonces, sin revelar demasiado sobre lo que Solvay tiene en mente, Blair dijo que la compañía está trabajando en tecnología de manejo diseñada para evitar daños a la fibra. "Un horario agresivo para esto", dijo, "sería de 18 meses".
Toray Advanced Composites. El antiguo TenCate Advanced Composites ahora ha sido absorbido por completo por Toray y, desde marzo, pasa por Toray Advanced Composites (Morgan Hill, California, EE. UU.). Steve Mead, director gerente, dice que EVOTL es particularmente activo para la empresa en este momento (termoestables y termoplásticos). Señaló que “estamos suministrando material a los programas emergentes de EVOTL” y agregó que “los compuestos son un verdadero facilitador debido al peso parásito de la batería en estos aviones. Los materiales no compuestos no son una opción ". La combinación de fabricación de calidad aeroespacial a tasas automotrices es intrigante, dijo.
Eviación. Entre las presentaciones de más alto perfil en el Salón Aeronáutico de París se encontraba Alice , un avión totalmente eléctrico, totalmente compuesto presentado por Eviation (Kadima-Tzoran, Israel). Alice es un avión de transporte regional de nueve asientos que tiene un alcance de 650 millas / 1000 kilómetros a una velocidad de crucero de 240 nudos. El avión cuenta con una hélice de empuje principal en la cola y dos hélices de empuje adicionales en las puntas de las alas para reducir la resistencia y crear redundancia. Omar Bar-Yohay, director ejecutivo de Eviation, presentó el avión y dijo que las pruebas de vuelo se realizarían en Moses Lake, Washington, EE. UU., Seguido de la certificación de la Administración Federal de Aviación (FAA) de EE. UU. A fines de 2020 o principios de 2021. El avión tendrá un precio de lista de $ 4 millones y Bar-Yohay dijo que la compañía está totalmente financiada a través de la certificación y la producción temprana.

La nave que se exhibió en la feria era un prototipo no volador ensamblado la semana anterior. Queda por ver dónde y cómo se producirá finalmente este avión. El prototipo, por su parte, fue ensamblado a partir de estructuras compuestas fabricadas por varios proveedores. Una es Multiplast (Vannes, Francia), parte de Carboman Group SA (Vannes), un roll-up de cinco empresas que también incluye Decision (Ecublens, Suiza), SNE SMM (Lanester, Francia), Plastinov (Samazan, Francia) y Plastéol (Samazan). Multiplast, que tiene experiencia en la fabricación de estructuras marinas, fabricó el fuselaje del Alice de autoclave (OOA) mediante estructura sándwich con núcleo de nido de abeja Nomex. El fuselaje se construyó en dos mitades basándose en una configuración de línea central de estribor / babor, con las dos secciones del fuselaje unidas / unidas (ver video secuencial a continuación). Multiplast no sabe si ganará el contrato para la producción en serie de la nave, pero la compañía dice que está evaluando qué se necesitaría desde una perspectiva de materiales y procesos para industrializar la fabricación. Alas y carenados de vientre para Alice fueron suministrados por Composite Cluster Singapore (CCS).
Stratasys. El especialista en máquinas de fabricación aditiva (AM) Stratasys (Eden Prairie, Minnesota, EE. UU.) Estuvo en el Salón Aeronáutico de París enfatizando su capacidad para utilizar AM para la producción de piezas y herramientas. Para la fabricación de compuestos, el énfasis estaba en las herramientas. La empresa tenía en su stand dos moldes realizados con máquinas Stratasys. El material es ULTEM 1010 de SABIC, una polieterimida no reforzada (PEI) que favorece el procesamiento en autoclave. El primer molde fue para la fabricación de un borde de ataque de ala de fibra de carbono y cuenta con electrodos en el molde para aumentar la capacidad de calentamiento del preimpregnado y reducir el tiempo de curado de 1,5 horas a solo 10 minutos. La otra parte fue una herramienta de laminado fabricada por Boom Aerospace (Centennial, Colorado, EE. UU.) Para la producción de piezas pequeñas para Overture avión comercial supersónico que la empresa está desarrollando. Scott Sevcik, vicepresidente de soluciones de fabricación de Stratasys, dijo que Boom ya tiene dos máquinas Stratasys en uso, y una tercera se entregará a finales de este año. Sevcik dijo que se espera que Stratasys introduzca dos nuevos materiales reforzados con fibra de carbono cortada para uso AM a finales de este año; Stratasys, dijo, también está trabajando en el refuerzo continuo de fibra para AM.
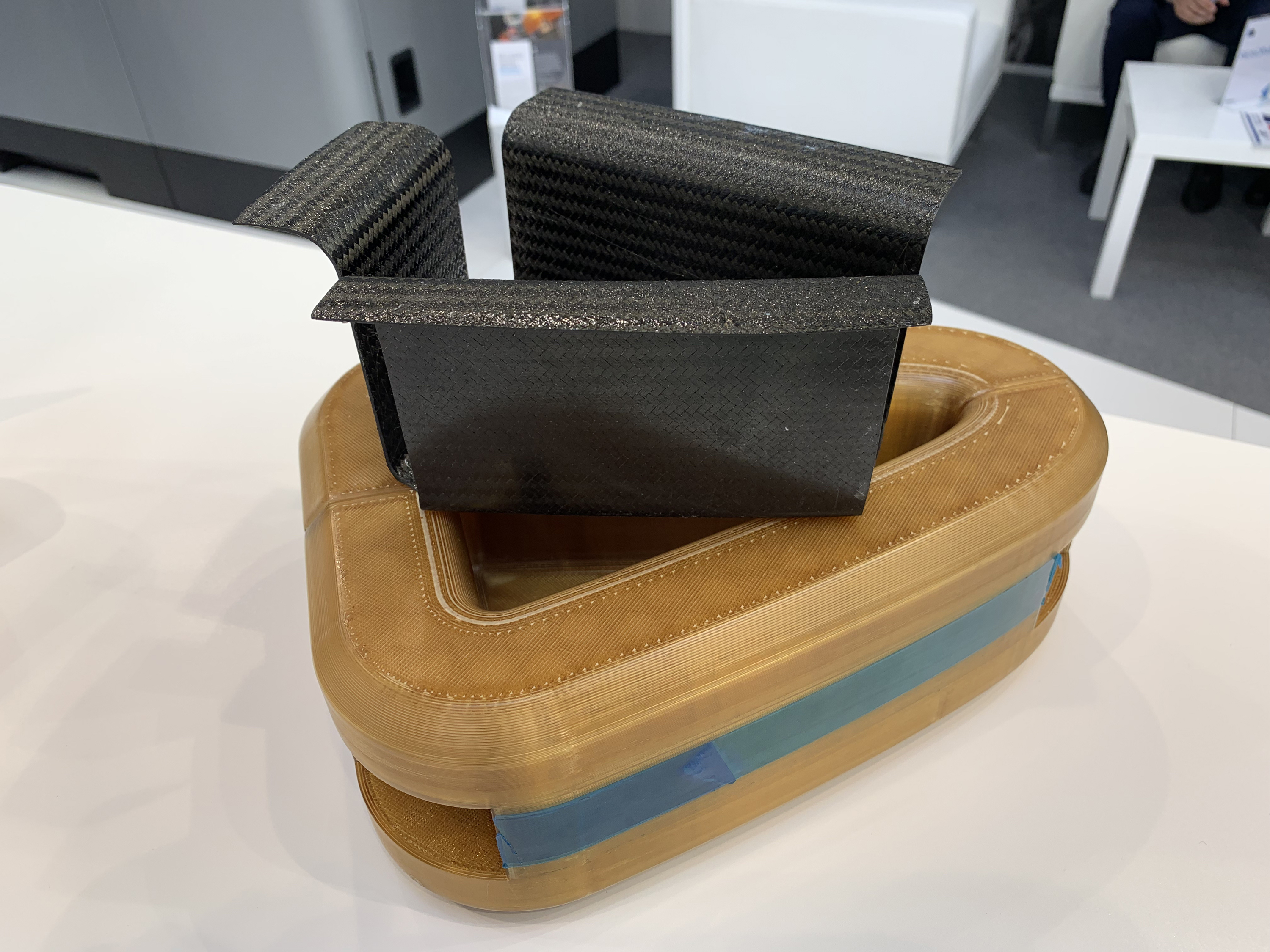
Boom Aerospace. Otro anuncio llamativo en el Salón Aeronáutico de París provino de Boom Aerospace (Englewood, Colorado, EE. UU.), Que, como se señaló, está desarrollando Overture , un avión de pasajeros supersónico completamente nuevo. El CEO y fundador de Boom, Blake Scholl, dijo en una conferencia de prensa que Boom está a punto de finalizar el XB-1 intensivo en compuestos , un prototipo de subescala de la Obertura que se espera que se implemente a fines de 2019 y se realice una prueba en algún momento de 2020. Estos vuelos de prueba, dijo Scholl, están diseñados para ayudar a Boom a evaluar los principios de diseño e ingeniería de la aeronave y aplicar las lecciones aprendidas al diseño final y la producción de Obertura , que se espera que entre en servicio a mediados de la década de 2020. Este es un programa más largo de lo que Boom anticipó por primera vez. “Este es un proyecto ambicioso”, dijo Scholl. "En los primeros días, es fácil ser demasiado optimista".
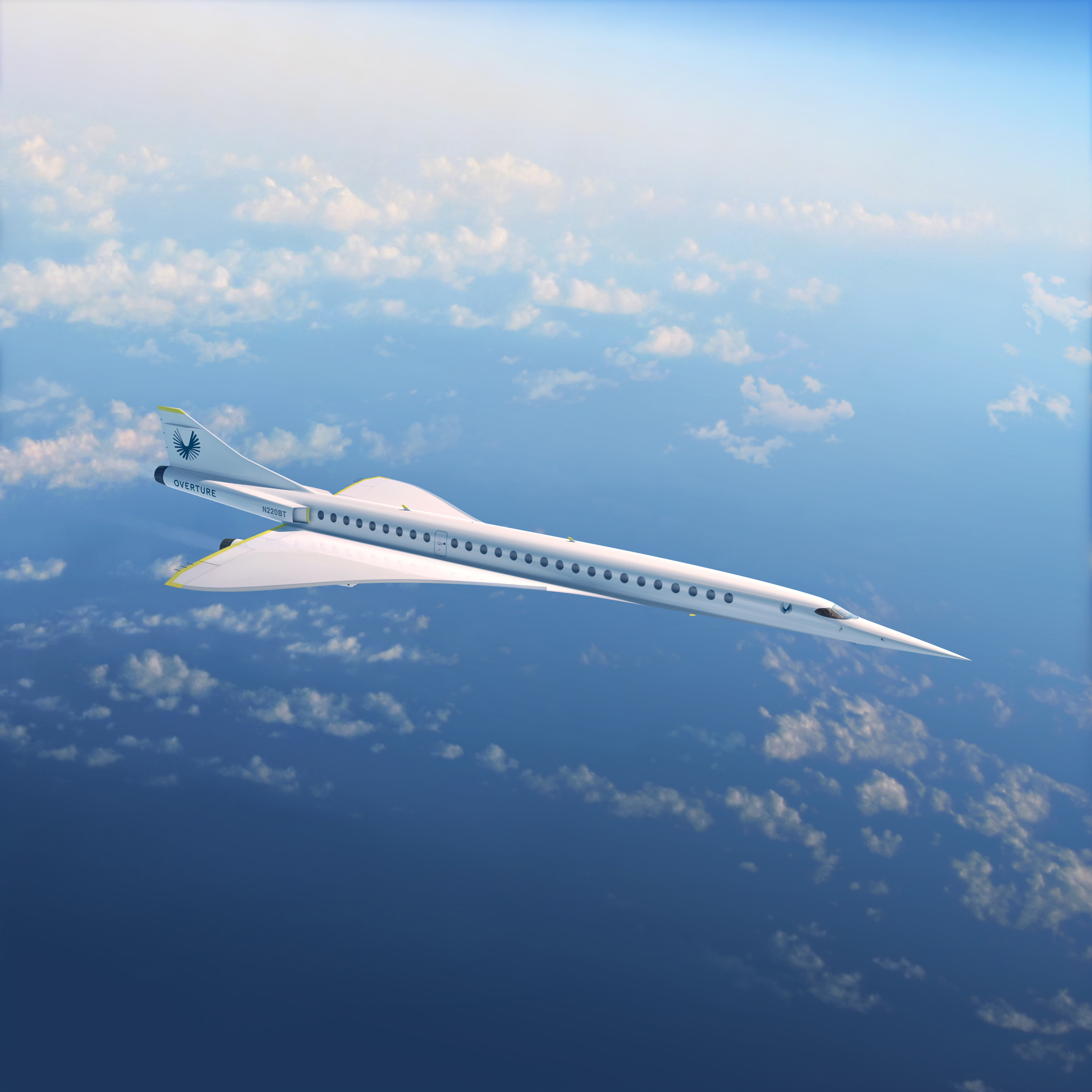
Obertura Se espera que tenga una velocidad máxima de Mach 2.2, una altitud de crucero de 60,000 pies (19,354 metros) y llevará pasajeros (55-75) de Sydney a Los Ángeles en solo 7 horas, o de Washington D.C. a Londres en solo 3.5 horas. Scholl declaró que el costo del boleto en Overture Se espera que sea competitivo, asiento por milla, con los precios actuales de las aerolíneas. Scholl también dijo que Overture Se espera que utilice una tecnología llamada Prometheus Fuels, que convierte el carbono de la atmósfera en gasolina o, en el caso de Boom, combustible para aviones, utilizando electricidad procedente de recursos renovables. De esta manera, dijo, el avión proporcionará un vuelo supersónico de carbono neto cero.
Resina
- Oxígeno
- Renesas destaca la inteligencia de endpoints en el mundo embebido 2019
- Bett Show 2019 - Únase a nosotros en el sitio
- La inspección no destructiva juega un papel clave en la base aérea
- JEC World 2019:Hexcel
- JEC World 2019:Hexion
- SAMPE Summit 19 París
- 3 maneras de mostrarle amor a su sistema de aire comprimido
- Atlas Copco exhibirá en la feria SEMA 2017
- El aire comprimido ayuda a impulsar los viajes de vacaciones
- ¡Y eso es todo en 2019!