Fabricación de compuestos termoplásticos de alta velocidad y alta tasa
Para acelerar el laminado y aún ofrecer una buena flexibilidad de diseño, SABIC y Airborne tomaron prestada una idea del sistema postal al desarrollar el proceso de laminado de capas para cintas compuestas termoplásticas. Varias bandejas económicas que se mueven en un sistema de transporte (que se muestra aquí) se detienen brevemente debajo de las unidades de alimentación. Cada alimentador corta y deja caer una capa de cinta de las dimensiones y la orientación correctas en la bandeja, que luego avanza a la siguiente unidad de alimentador. Las bandejas continúan girando hacia atrás a través de las unidades de alimentación hasta que se alcanza el número y la orientación adecuados de capas en cada pila para cumplir con los requisitos de diseño de un laminado determinado. Fuente | SABIC
Un nuevo sistema de alta velocidad para producir laminados consolidados a partir de cintas compuestas termoplásticas, la línea de fabricación de compuestos digitales (DCML) promete ser capaz de producir hasta cuatro laminados (con hasta 15 capas cada uno) por minuto y 1,5 millones de laminados por año. desde una sola línea de producción, incluida la inspección completa, que es 100% digital, incluidas las mediciones y el seguimiento de datos, del material entrante y laminados salientes. Esa tasa de producción es, aparentemente, significativa más rápido que cualquier otro sistema comercial de manipulación de cintas disponible (para termoplásticos o termoendurecibles) y este sistema ha sido diseñado específicamente para satisfacer los altos costos de conversión y de alto rendimiento requeridos por la industria de la electrónica de consumo (consulte “Electrónica de consumo:cubiertas compuestas híbridas”). Afortunadamente, las piezas para este mercado no son enormes, no en la escala aeroespacial o automotriz, pero los OEM necesitan muchas de ellas, del orden de decenas de millones por año.
“Realmente se necesitaba un proceso de conversión de cinta termoplástica de alta velocidad porque la tecnología actual es relativamente laboriosa, costosa y lenta”, explica Gino Francato, líder mundial en compuestos de SABIC. “Eso hace que sea difícil justificar económicamente y aprovechar los muchos beneficios de estos materiales para producir piezas delgadas y livianas con alta estética, resistencia al impacto y rendimiento mecánico, además de reciclabilidad, en industrias con volúmenes de producción altos a muy altos. Sin la capacidad de aumentar enormemente las velocidades de producción y utilizar una manipulación e inspección totalmente automatizadas, las cintas termoplásticas seguirán siendo productos de nicho costosos, principalmente limitados para su uso en la industria aeroespacial y automotriz ”.
El DCML es una creación de SABIC (Bergen op Zoom, Holanda) y Airborne (La Haya, Holanda), con tecnología de Siemens AG (Munich, Alemania) y KUKA AG (Augsburg, Alemania). SABIC aportó tecnología de materiales y herramientas de modelado de compuestos para acelerar el desarrollo de materiales personalizados y la creación virtual de prototipos de piezas. Airborne construyó la línea y también contribuyó con su experiencia en automatización, digitalización e industrialización del proceso de producción de compuestos. Siemens contribuyó con software integrado de gestión del ciclo de vida del producto (PLM) y controlador lógico programable (PLC) para mejorar la automatización y facilitar el aprendizaje automático. KUKA contribuyó con robots industriales y soluciones de automatización de fábricas. Si bien el nuevo proceso de alta velocidad ha sido descrito en términos generales en varios eventos de prensa desde 2018, hay muchos detalles que aún no se han divulgado. Esto es lo que sabemos actualmente.
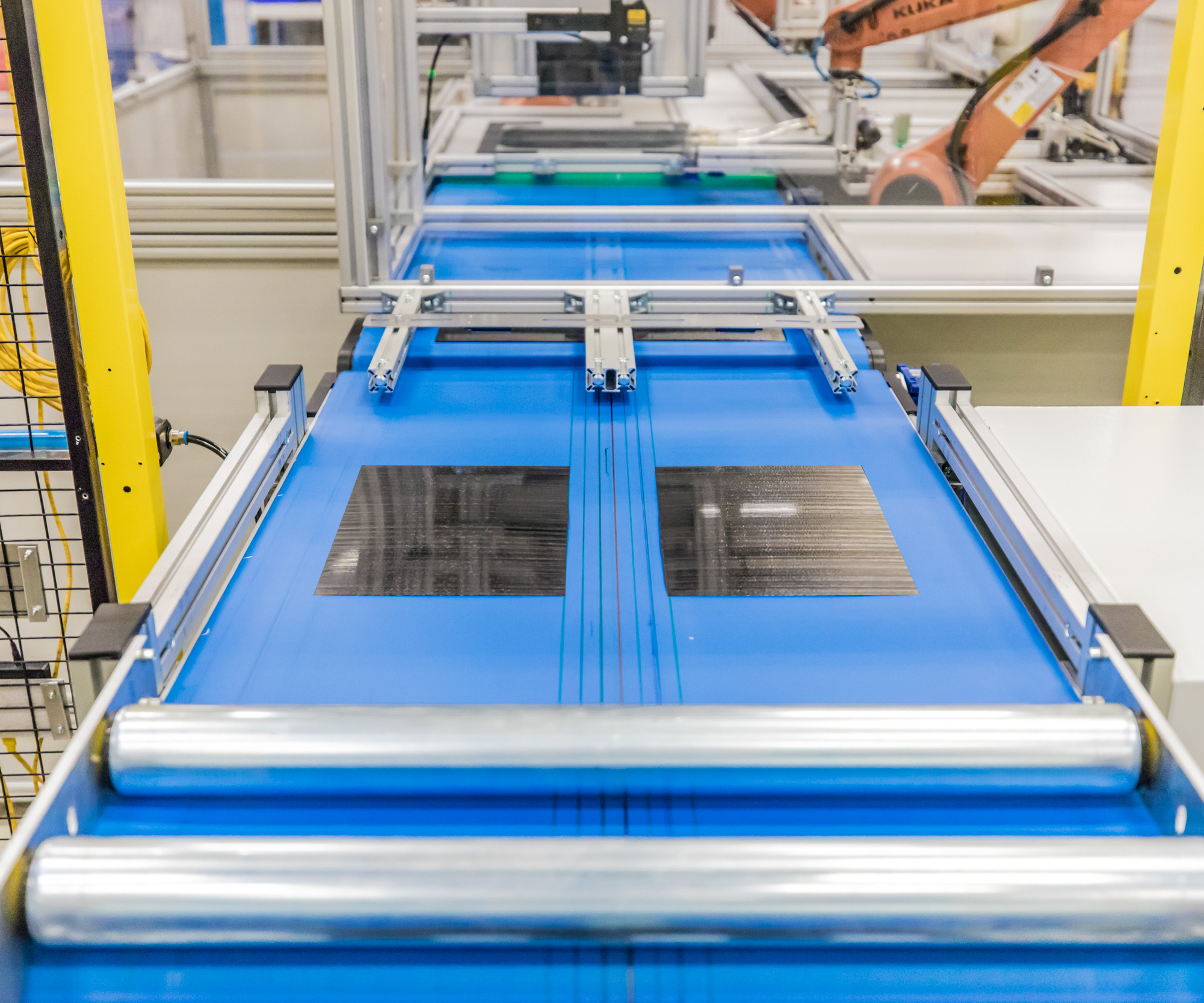
Una vez que la bandeja sale del lazo del transportador, se dirige a la estación de soldadura donde cada pila se suelda por puntos en dos ubicaciones para facilitar el manejo robótico en la estación de consolidación. Después de la consolidación, el laminado pasa al recorte y la inspección (se muestra aquí). Fuente | SABIC
La línea está diseñada para producir laminados planos personalizables con forma casi neta a partir de cintas termoplásticas unidireccionales (UD) y proporciona laminado, consolidación, recorte, inspección digital y visual, liberación automatizada y empaque para su envío a los clientes. Se pueden producir hasta cuatro laminados por minuto, y cada laminado puede tener un programa de colocación, orientación y número de capas diferente y, teóricamente, incluso utilizar diferentes materiales (con diferentes refuerzos y matrices de resina, aunque esto requiere agregar unidades de alimentación adicionales).
Lograr diferentes capas simultáneamente es solo una cuestión de cuántas veces una bandeja determinada (con un diseño laminado específico) pasa por debajo de cada alimentador para lograr el número correcto de capas y orientaciones para completar su programa de capas. Dada la rapidez con que cambian los modelos en la electrónica de consumo, la flexibilidad es fundamental para el sistema, que se puede ampliar agregando alimentadores adicionales en la parte frontal o funcionalidad (por ejemplo, perforación, preformado, etc.) en la parte posterior. Inicialmente, la línea se creó para ejecutar cintas de policarbonato reforzado con fibra de carbono unidireccionales de SABIC, pero, según se informa, el sistema es lo suficientemente flexible para ejecutar cintas termoplásticas que van desde polietileno (PE) y polipropileno (PP) hasta polieteretercetona (PEEK) reforzada con fibra de carbono unidireccional. o fibra de vidrio, o ambos, o incluso tejidos de tela.
El sistema es compatible con la Industria 4.0 y permite la digitalización de un extremo a otro, desde el desarrollo de productos compuestos hasta la producción física en la planta, con un control de calidad total basado en el aprendizaje automático para lograr mejoras de calidad continuas automáticamente a lo largo del tiempo. La línea se puede monitorear y controlar de forma remota, lo que permite a los fabricantes cambiar la configuración (como los programas de colocación, el número de capas, etc.) sobre la marcha para modificar el diseño y las propiedades del material.
Funcionalmente, hay tres secciones principales en DCML:disposición de capas, consolidación y recorte / inspección.
Excepcionalmente, la sección de laminado de capas no utiliza máquinas de laminado de cinta automatizadas (ATL), que normalmente cortarían las cintas a la longitud deseada y las colocarían en la orientación y ubicación necesarias en una mesa de indexación que se mueve debajo del cabezal de corte. En cambio, el equipo ha adoptado un enfoque novedoso y de alta velocidad, según se informa basado en la forma en que se clasifica y distribuye el correo, para construir pilas de capas. Varias bandejas económicas que se mueven sobre un sistema de transporte se detienen brevemente debajo de las unidades de alimentación. Cada unidad de alimentación corta y deja caer una capa de cinta de las dimensiones y orientación correctas (verificada por cámaras de alta resolución, que inspeccionan las cintas en busca de defectos y cambios, y miden el ancho y el grosor en varias ubicaciones) en la bandeja, que luego avanza a la siguiente. unidad de alimentación. Para reducir los desperdicios y acelerar la colocación, las cintas se producirán con el ancho necesario para un proyecto específico. Las bandejas giran hacia atrás a través de los alimentadores hasta que se deposita la cantidad adecuada de capas en cada pila antes de proceder a la soldadura por puntos en dos ubicaciones para facilitar el manejo en la estación de consolidación. Este enfoque permite que la colocación se produzca rápidamente pero con flexibilidad de diseño.
En la consolidación, un robot levanta cuatro pilas soldadas (dos pilas a la vez) de sus bandejas y las coloca entre un conjunto de placas de metal en un sistema transportador separado. Las placas se calientan y, por lo tanto, calientan y consolidan los laminados (mediante calentamiento por contacto), y luego los laminados se enfrían y se descargan robóticamente en un tercer sistema transportador. Las placas de metal utilizadas en la última operación de consolidación se reciclan de nuevo a la línea de retorno de placas y al sistema de consolidación. Cuatro pilas entran y salen de esta sección cada minuto.
La última parada para los laminados ahora consolidados es la inspección, el recorte y el embalaje. En esta estación, cada laminado se inspecciona en un lado y se recorta, antes de pasar a un segundo robot que le da la vuelta al laminado y lo inspecciona desde el otro lado. No hay detalles disponibles sobre qué tecnología de recorte se utiliza.
El DCML tiene sus limitaciones, como cualquier sistema de fabricación. Principalmente, existe cierto sacrificio en términos de las orientaciones de las capas disponibles, el tamaño y la forma de las capas, el tamaño final del laminado y la capacidad de colocar agujeros / ventanas. Sin embargo, el sistema compensa con creces esto en términos de velocidad, producción, tasa de desperdicio y costos de conversión.
Según se informa, la primera línea comercial a gran escala de Airborne en los Países Bajos comenzará la producción el próximo año, y la empresa producirá laminados termoplásticos de diseño personalizado para clientes de electrónica de consumo. Una segunda línea del tamaño de un laboratorio ya está disponible en el Centro de Desarrollo de Procesamiento de Polímeros de SABIC (PPDC, Pittsfield, Mass., EE. UU.) Para los clientes que desean probar la tecnología y evaluar la calidad del laminado.
Además de la electrónica de consumo, otras industrias que se dice que son objetivos potenciales para la tecnología incluyen la aeroespacial, automotriz, transporte público, artículos deportivos y atención médica.
Resina
- Covestro intensifica la inversión en compuestos termoplásticos
- Compuestos termoplásticos en Oribi Composites:CW Trending, episodio 4
- Solución de problemas de termoformado de compuestos termoplásticos
- Compuestos termoplásticos:soporte de parachoques estructural
- Toray Advanced Composites expande las capacidades de los compuestos termoplásticos
- Teledyne CML Composites invierte en capacidad de procesamiento termoplástico
- Cato Composites amplía la capacidad de producción de compuestos termoplásticos
- Desafíos del bobinado de cinta asistido por láser de compuestos termoplásticos
- Vista previa de JEC World 2019:SABIC
- Compuestos termoplásticos:vista panorámica
- Soldadura de compuestos termoplásticos