Avanzar en la fabricación aditiva para aprovechar la anisotropía
Fundada en 2014 por el director ejecutivo Fedor Antonov, Anisoprint (Esch-sur-Alzette, Luxemburgo) es una de las empresas de tecnología cada vez más numerosas que avanzan en la impresión 3D de materiales compuestos con fibra continua . . Sin embargo, prefiere ser conocido como pionero en alejar la fabricación aditiva (FA) de los metales a compuestos.
"Las propiedades direccionales de los compuestos son una ventaja, no un inconveniente", dice Antonov. “Los compuestos de fibra de carbono unidireccionales son más fuertes y ligeros que los metales. La fabricación convencional y la AM basada en metales consideran la anisotropía direccional de los compuestos como un inconveniente que debe mitigarse. Pero el enfoque de Anisoprint explota esta anisotropía, orientando y colocando fibras para cumplir con precisión las cargas estructurales, reduciendo significativamente el peso de la pieza al tiempo que conserva una alta resistencia y rigidez ".
Habilitación de compuestos más eficientes
Antonov señala que la fabricación de compuestos convencionales generalmente ha utilizado prácticas de la industria de los metales, incluidos laminados cuasi-isotrópicos, perforaciones y sujetadores mecánicos. "Estos anulan las ventajas de peso y rendimiento de compuestos ”, dice Antonov. "La tecnología de anisoprinting proporciona un método automatizado mucho más rápido y flexible para la producción". También ofrece una forma de lograr las estructuras más eficientes que ahora se generan mediante optimización de topología y diseño generativo software.
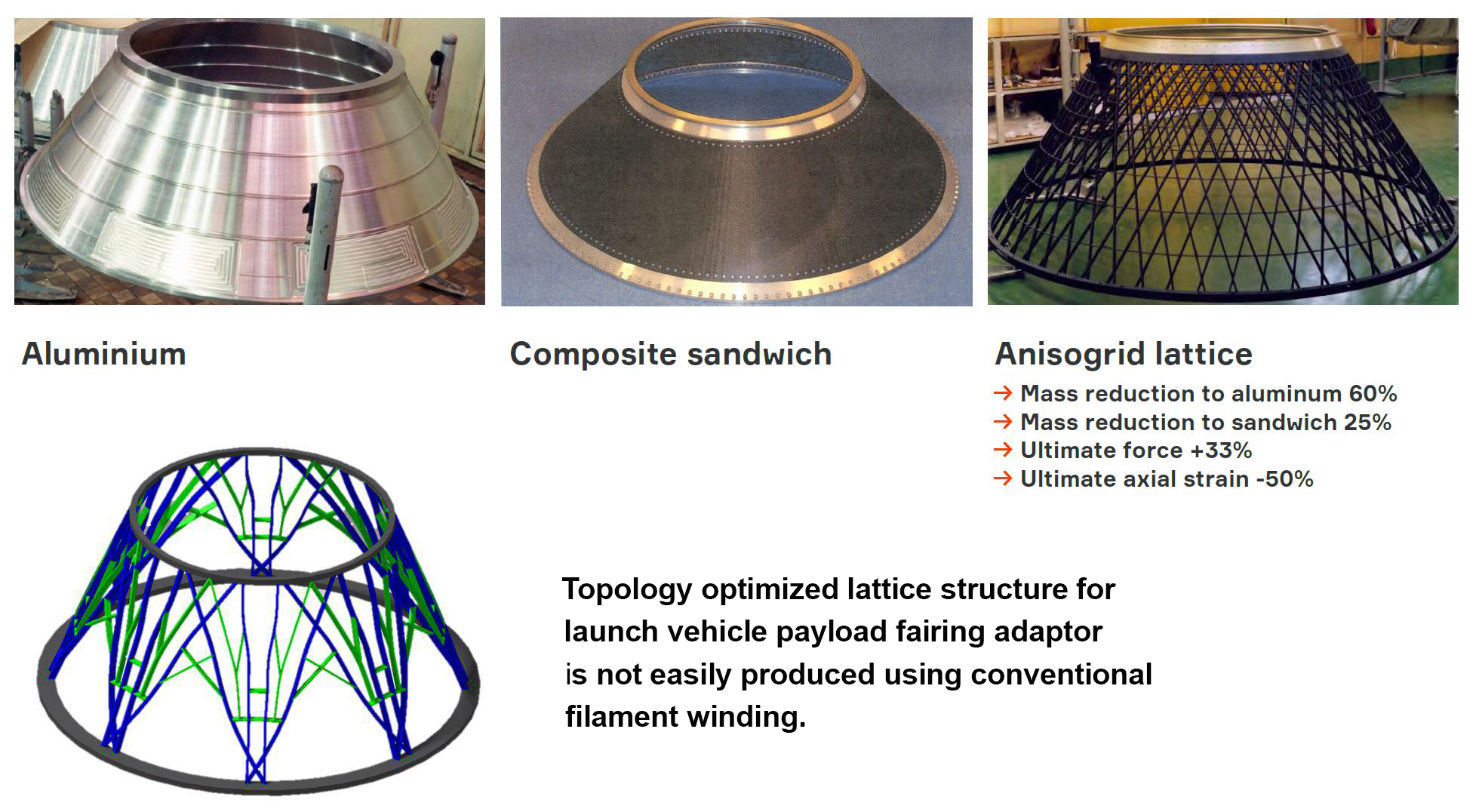
"Las estructuras más eficientes de la naturaleza, como los árboles y los huesos, explotan las propiedades direccionales, orientando el material portador de carga principalmente a lo largo de las rutas de carga", afirma Antonov. Sin embargo, estos tipos de estructuras con topología optimizada son difíciles de producir. Por ejemplo, las estructuras de celosía que han permitido adaptadores de carenado de carga útil resistentes y ligeros para naves espaciales, se producen normalmente utilizando bobinado de filamentos. Sin embargo, una versión optimizada para topología , que ofrece un ahorro de peso adicional del 30% , ya no es fácil de producir con los procesos compuestos convencionales, ni con la colocación automatizada de fibra (AFP) más reciente.
“Las estructuras arrolladas de filamentos de anisomalla convencionales se logran utilizando ranuras en las herramientas, y una fracción de volumen de fibra relativamente baja en las nervaduras permite intersecarlas”, dice Antonov. “Este tipo de estructuras de anisogrid eran nuestro objetivo original. Pero esto no funciona con AFP porque su contenido de volumen de fibra es siempre constante, y no es posible cruzar las nervaduras sin cortar las fibras o las variaciones de espesor local ”.
(Nota:Para obtener más información sobre esto, consulte https://www.researchgate.net/publication/321081593_Anisogrid_Payload_Adaptor_Structure_for_Vega_Launcher)
Dirección de fibra
El direccionamiento de fibra es una técnica que se aplica actualmente a la producción de compuestos utilizando AFP que permite que las fibras se apliquen en trayectorias curvilíneas; AFP ha utilizado tradicionalmente trayectorias lineales rectas. La dirección de la fibra permite optimizar la trayectoria de la fibra y, por lo tanto, la respuesta mecánica del panel compuesto para exhibir un rendimiento más alto que con los laminados convencionales. En un ejemplo, este enfoque produce un panel de sustrato compuesto para una matriz solar de nave espacial que tiene una primera frecuencia natural 44% más alta (minimiza la amplitud de vibraciones y permite una amortiguación más rápida) que un panel convencional equivalente con trayectorias de fibra rectas y la misma masa. Alternativamente, se podría lograr un panel de menor peso para el mismo rendimiento de frecuencia.
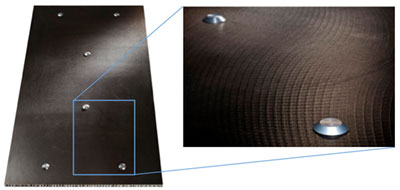
La dirección de fibra permite el diseño y fabricación de piezas como paneles estructurales para satélites o componentes de máquinas de alta velocidad con un rendimiento muy alto. Es un proceso repetible, que logra una calidad alta y constante y permite nuevos diseños innovadores. También se puede utilizar para reducir el peso del mismo diseño geométrico. FUENTE | “Tecnología de dirección de fibra para paneles compuestos avanzados” (el enlace original se proporciona aquí, pero ya no está disponible a través del servidor esa-tec:http://www.esa-tec.eu/space-technologies/from-space/fibre-steering -tecnología-para-paneles-compuestos-avanzados /)
"La anisoimpresión es una combinación de estructuras de celosía y dirección de fibra que se utiliza para lograr piezas con topología optimizada", dice Antonov. “Esta es una tecnología clave para los compuestos impresos. Por ejemplo, ¿cómo se construye un panel de fuselaje para un avión comercial que tiene cortes o agujeros?
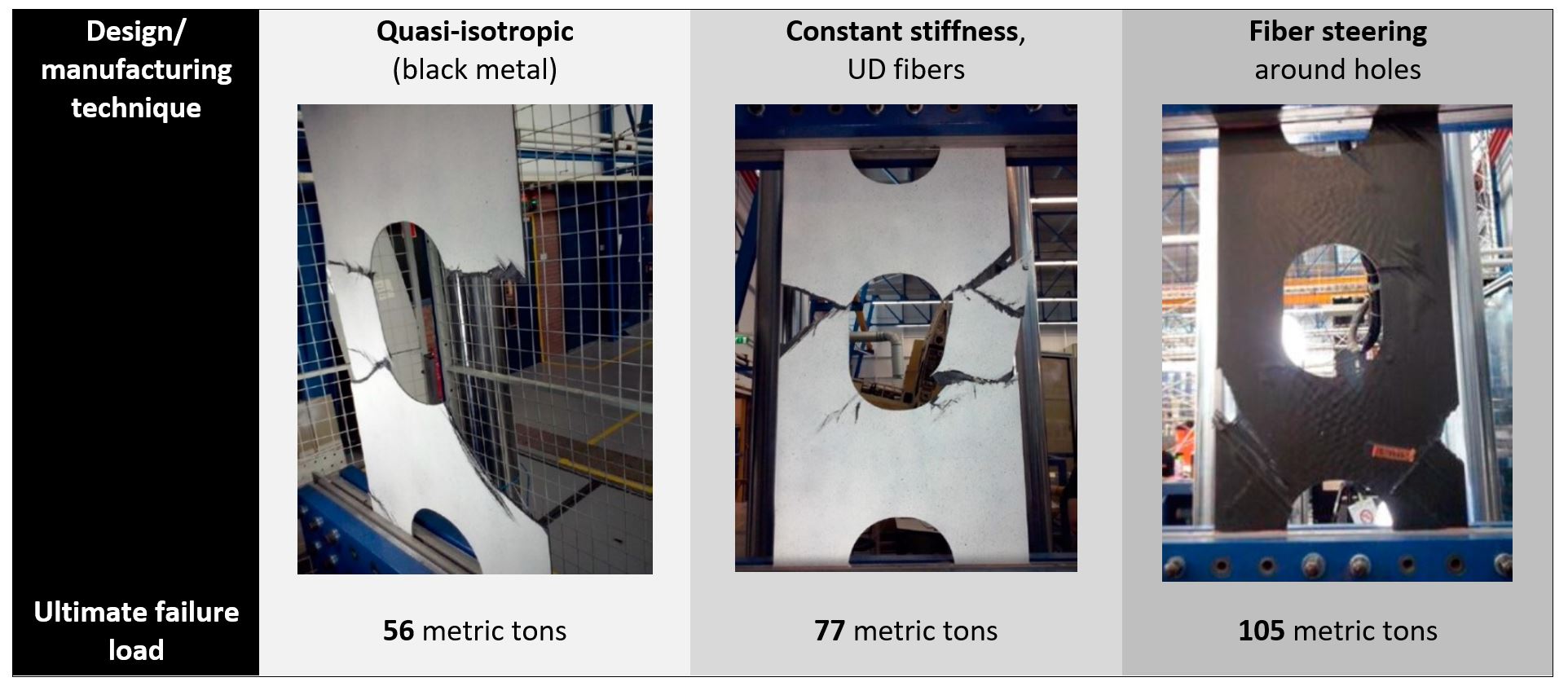
Él da tres técnicas diferentes, que se utilizan para producir muestras compuestas del mismo grosor y peso, cada una con agujeros mecanizados por CNC (ver tabla a continuación). Señala que en las pruebas de compresión, la muestra fabricada con dirección de fibra tiene una carga de compresión máxima dos veces mayor que la de un compuesto cuasi-isotrópico ("aluminio negro") y un 30% más alta en comparación con un laminado UD de rigidez constante. “Por lo tanto, la dirección de fibra es una herramienta poderosa”, dice Antonov. “La anisoimpresión se moverá hacia la dirección de fibra AFP a medida que aumentemos el volumen y la productividad de la fibra, y AFP se acercará a nosotros con más flexibilidad.
La "flexibilidad" a la que se refiere Anotov es una medida de cuánto es posible colocar una fibra a lo largo de cualquier camino en el espacio tridimensional. Arevo, otra empresa que comercializa impresión 3D de fibra continua, afirma tener este tipo de flexibilidad. “La tecnología de Arevo no es muy diferente en comparación con empresas de AFP como Coriolis, Automated Dynamics, Electroimpact, etc.”, dice Antonov. “Simplemente lo han miniaturizado y en lugar de usar una cinta fina y ancha, utilizan una gruesa y estrecha con un cabezal láser AFP. Todo es lo mismo." Tenga en cuenta que la tecnología de impresión 3D de Arevo se ha basado en robots desde el principio. ¿Cómo cambiará la tecnología de Anisoprint a medida que se traslade a plataformas robóticas?
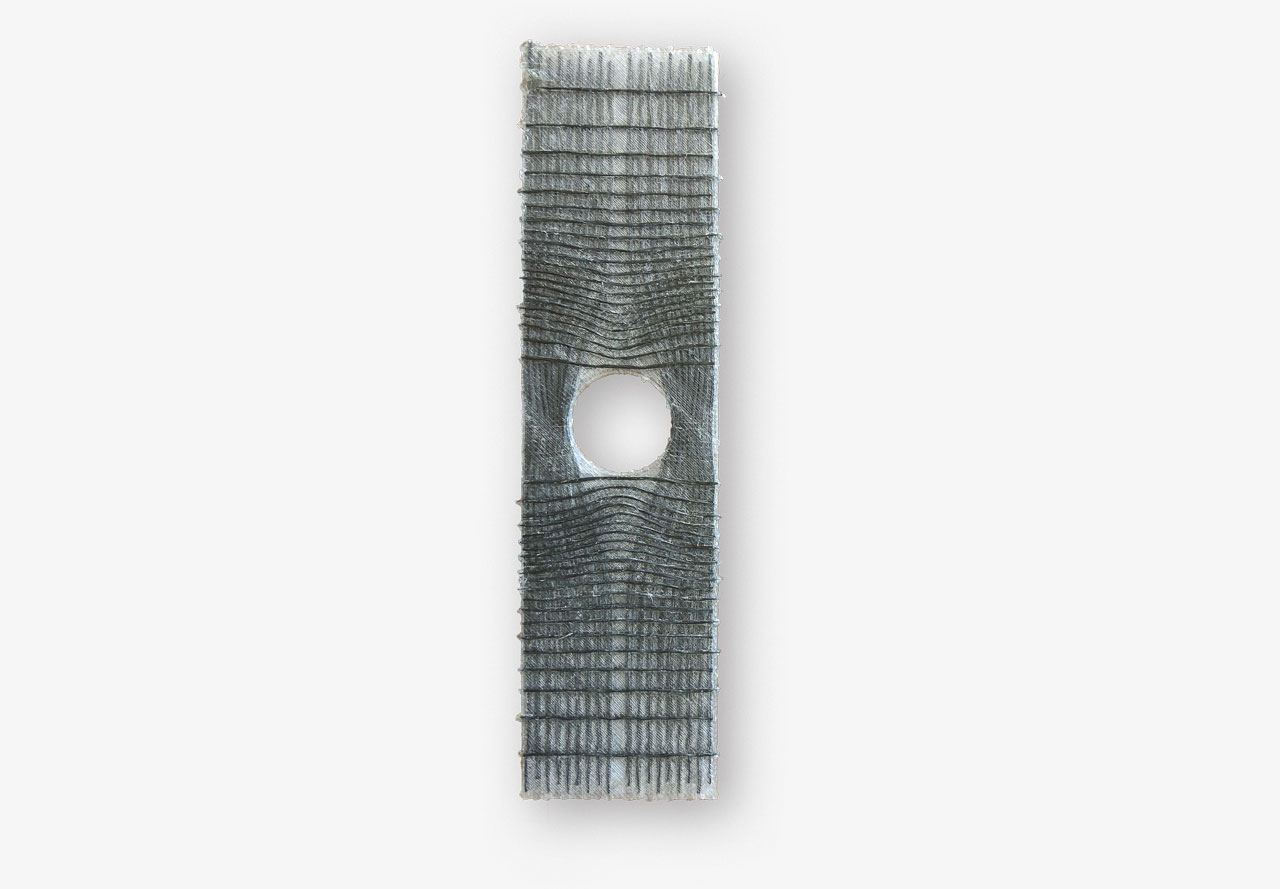
Ejemplo de una muestra compuesta impresa en 3D de Anisoprint utilizando fibra direccional.
Historia de Anisoprint y enfoque de TS-TP
Antonov y sus cofundadores (Andrey Azarov, Alexey Khaziev, Mikhail Golubev y Zafer Gürdal) estaban en una nueva universidad en la parte occidental de Moscú llamada Instituto de Ciencia y Tecnología Skolkovo (Skoltech), que se estableció en 2011. En 2014, Antonov estaba trabajando para construir el nuevo centro de tecnología de compuestos de Skoltech y comenzó a desarrollar la impresión 3D. El director del centro de composites en ese momento era Zafer Gürdal, quien se fue en 2015, regresando al McNair Center de la Universidad de Carolina del Sur. Este último es ahora conocido por su I + D en materiales compuestos e impresión 3D de fibra continua.
“Decidimos separarnos de Skoltech cuando Zafer Gürdal se fue”, explica Antonov. “Habíamos desarrollado un prototipo de cabezal de impresión CFC en el verano de 2015. Nuestro siguiente objetivo era desarrollar una impresora de escritorio”.
Anisoprint presentó su impresora de escritorio Composer en 2017. Similar a las impresoras de fibra continua Markforged, Composer de Anisoprint usa dos boquillas de impresión:una para el refuerzo de fibra continua y otra para la matriz plástica. Alojado dentro de una cámara de impresión de vidrio, la cama de impresión de vidrio de Composer se puede calentar hasta 120 ° C, lo que permite minimizar los efectos de contracción. Actualmente está disponible en dos tamaños:
- A3 (420 por 297 por 210 milímetros)
- A4 (297 por 210 por 147 milímetros)
Con un diámetro de boquilla estándar de 0,4 milímetros, la velocidad de impresión de Composer es de 10 a 80 milímetros / segundo sin refuerzo y de 1 a 20 milímetros / segundo con refuerzo de fibra continua. Anisoprint puede extruir muchos plásticos, incluidos PLA, PETG, ABS, nailon y PC. Puede reforzarlos con sus materiales compuestos de fibra de carbono (CCF) y recientemente lanzó un material de impresión compuesto de fibra de basalto (CBF).
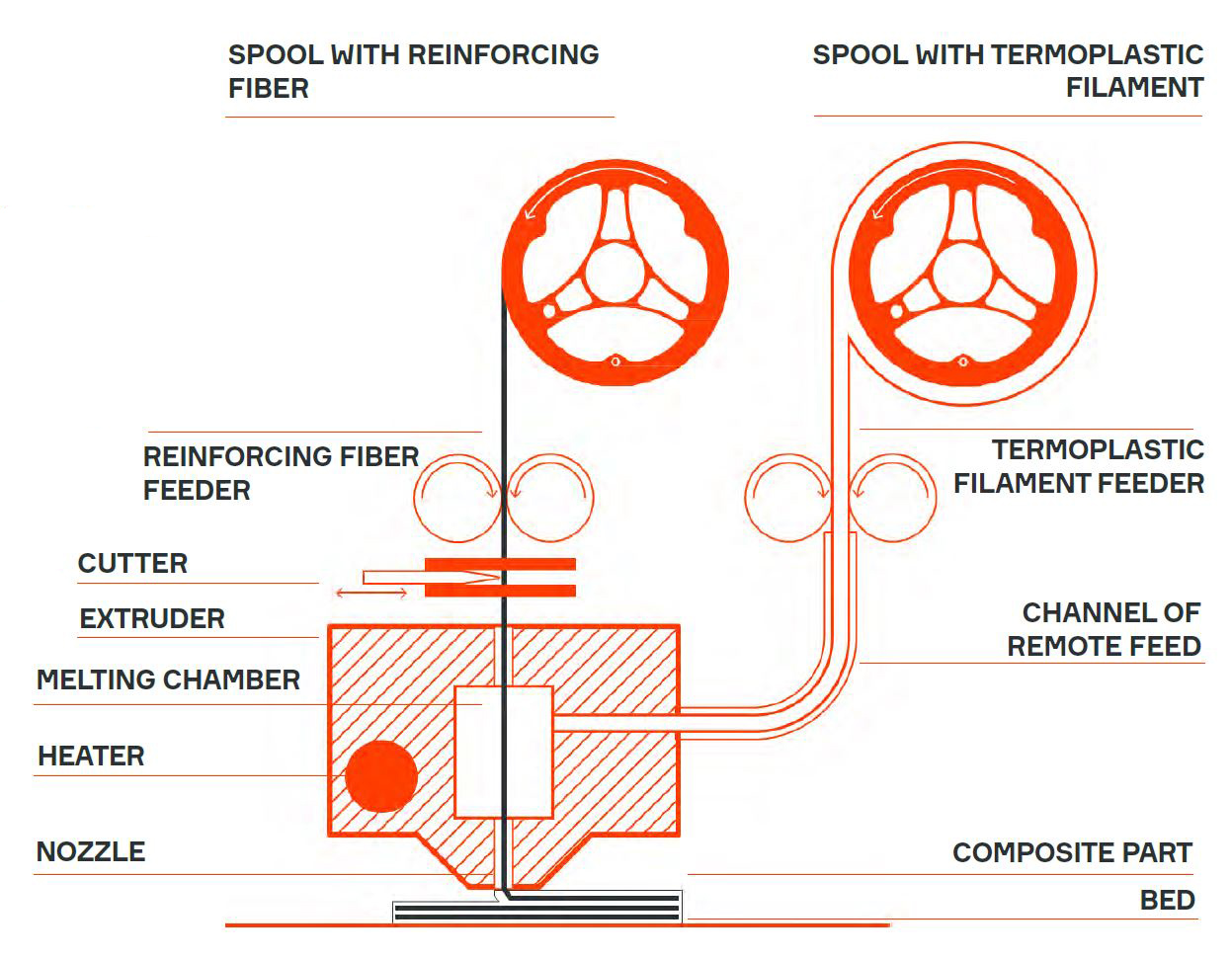
Sin embargo, Anisoprint es bastante diferente de otras tecnologías de impresión 3D de fibra continua porque primero impregna el refuerzo de fibra continua con un termoestable polímero y luego lo extruye en el filamento termoplástico fundido durante la impresión. "Este enfoque de dos matrices garantiza una baja porosidad, una buena adhesión de la fibra al polímero y excelentes propiedades mecánicas", Antonov afirma.
Continúa:“El inventor de la anisogrid enrollada con filamento para el adaptador de carga útil del lanzador Proton M, V.V. Vasiliev, que forma parte de nuestro consejo de asesores, demostró que esta idea de utilizar termoplásticos termoestables de matriz dual (TS-TP) tienen ventajas sobre el uso de una única matriz termoestable o termoplástica. Los materiales de matriz termoendurecible tienen problemas de fragilidad, por lo que la matriz comienza a agrietarse mucho antes de que falle la fibra. Vasiliev demostró que podía mitigar esto con un enfoque de matriz dual ".
El termoestable que utiliza Anisoprint es un epoxi multicomponente y los laminados impresos finales tienen un contenido de fibra de hasta un 45% según lo probado por la Universidad Técnica de Múnich (TUM).
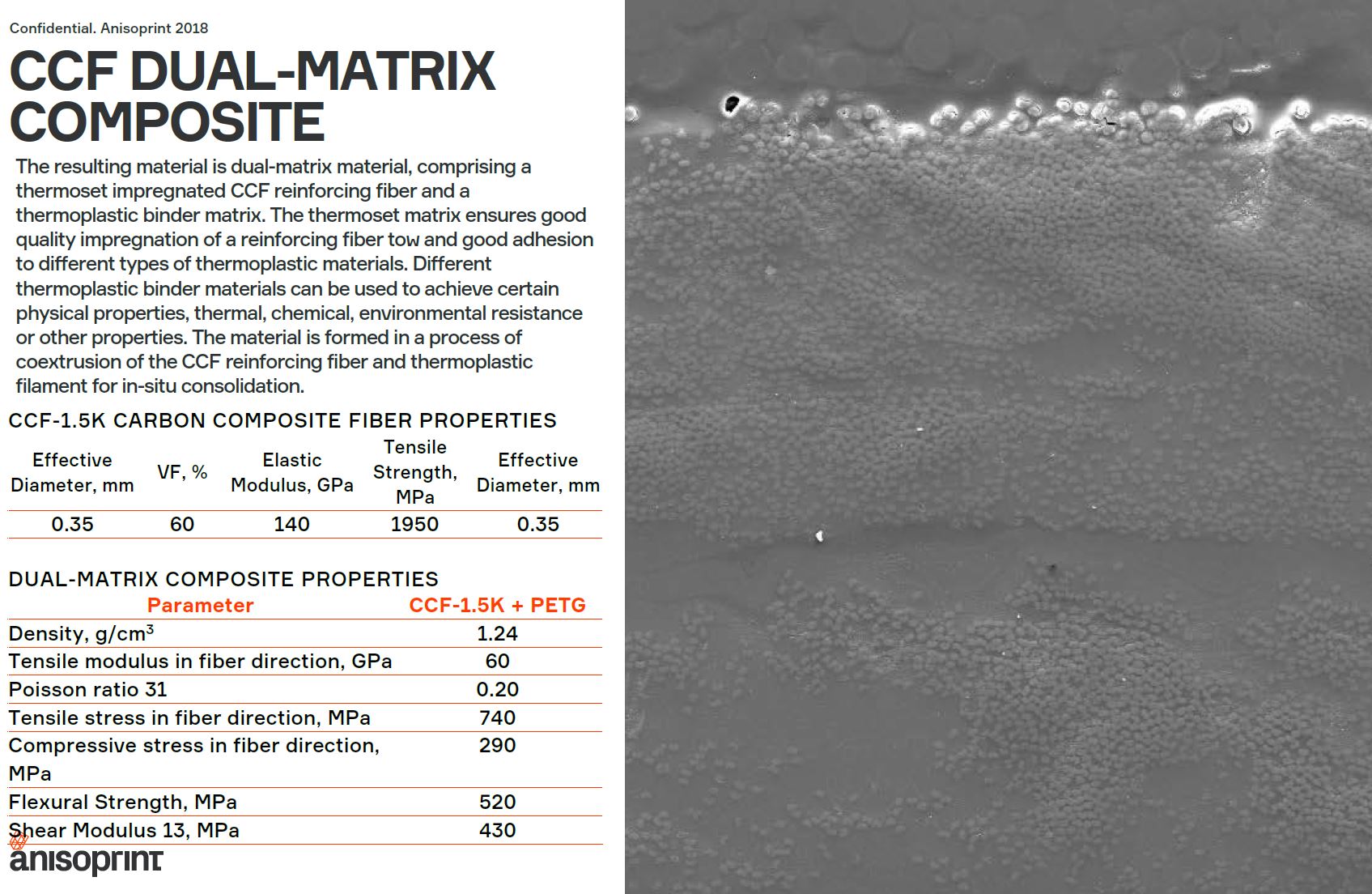
Las ofertas patentadas de Anisoprint incluyen:
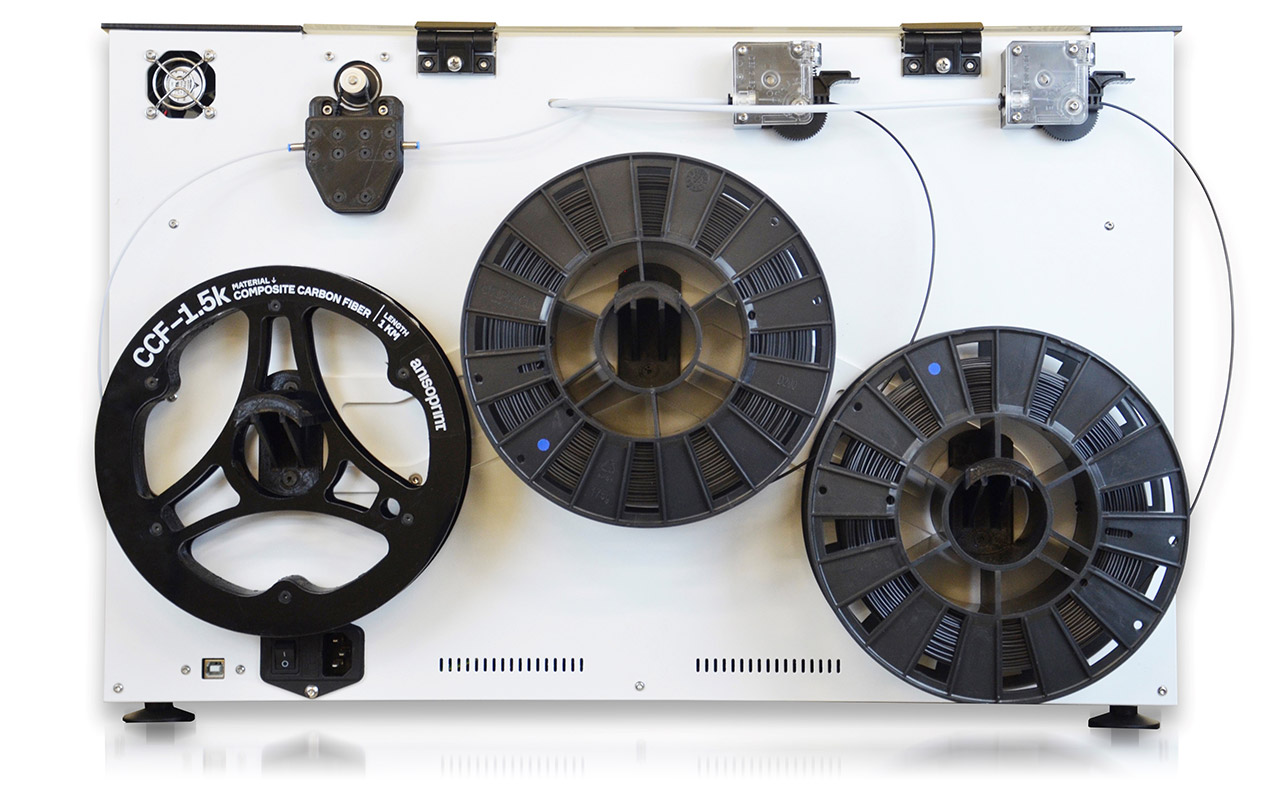
Tecnología de coextrusión de fibras compuestas (CFC) para fabricación aditiva utilizando diferentes polímeros termoplásticos reforzados con fibras continuas (por ejemplo, carbono, basalto) que se consolidan y curan en un proceso automatizado de una sola etapa que no requiere herramientas ni posprocesamiento.
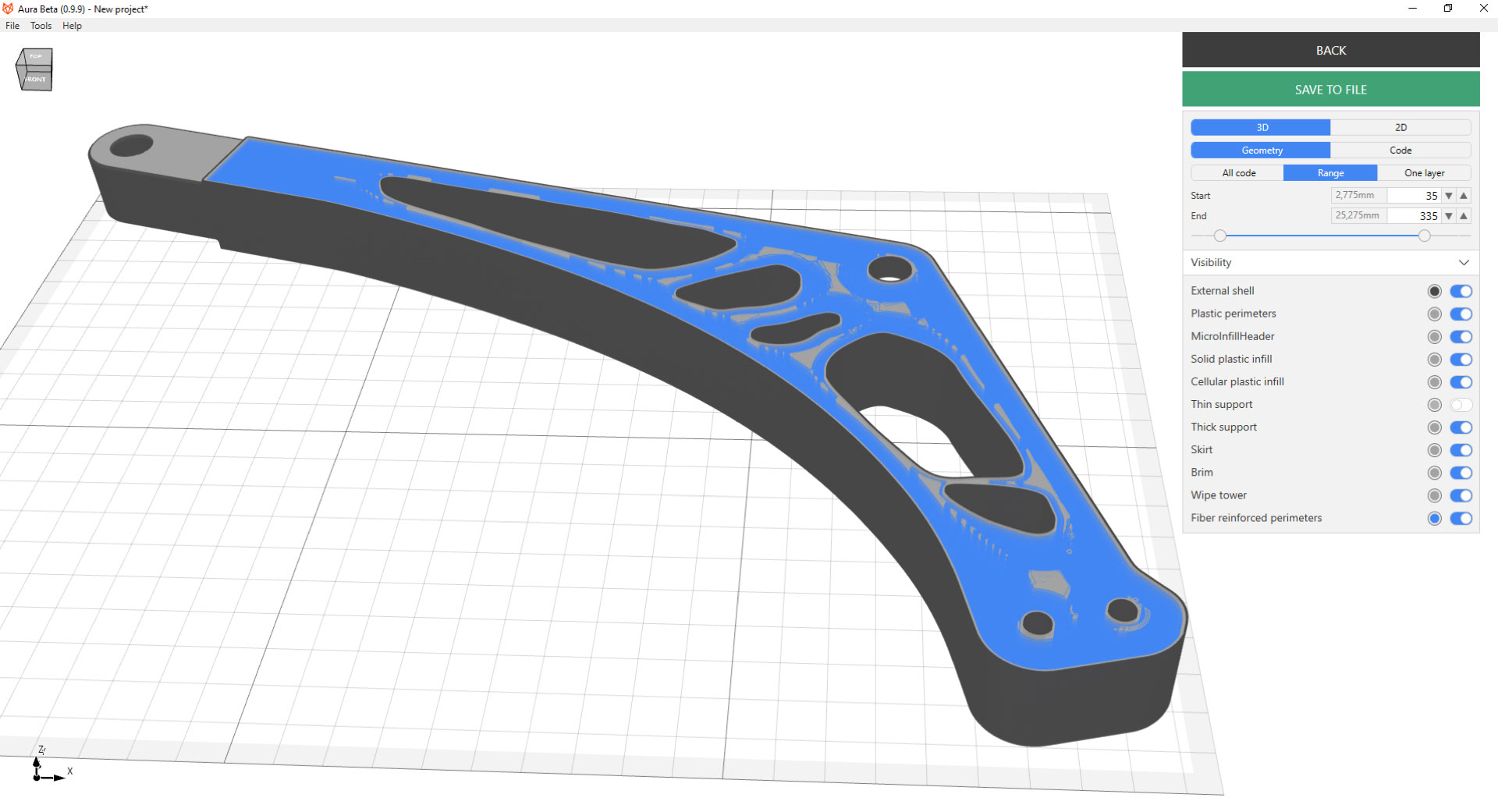
Software de corte Aura que prepara modelos 3D para la fabricación de piezas utilizando la impresora Composer CFC, así como las impresoras FFF convencionales.
Impresora 3D de escritorio Composer disponible en tres tamaños (A4, A3, A2).
PROM familia de sistemas de impresión industrial con opciones de robot y pórtico, disponible comercialmente a partir de 2020.
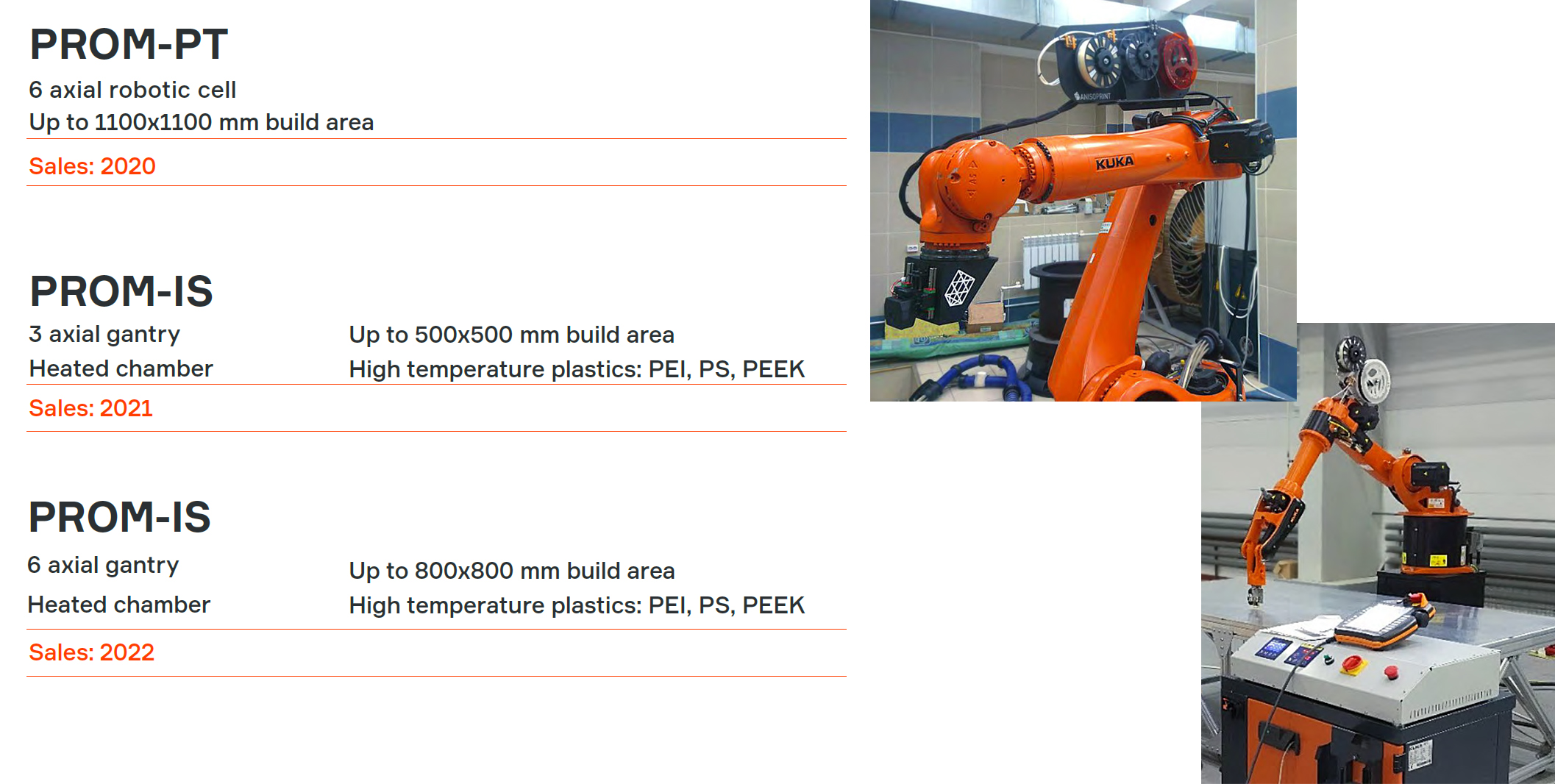
Desarrollo de robots frente a escritorio
“El robot tiene un cabezal de impresión diferente porque es necesario mover el cabezal para que encaje y alcance los espacios reducidos durante la impresión”, explica Antonov. “En un plano 2D, esto no es un problema. Pero en el espacio 3D, es necesario colocar fibra donde ya hay algo de estructura. La accesibilidad ideal se logra con una aguja. Por lo tanto, necesitamos un compromiso, un cabezal de impresión más parecido a una aguja ”.
Señala otras diferencias, como los controles industriales. “Las impresoras de escritorio se basan en productos electrónicos de consumo, como Arduino. Pero para sistemas robóticos más grandes, necesita interfaces y control de movimiento industrial y todo tipo de garantía de calidad in situ, como la medición láser, que Markforged tiene en su máquina más grande. También es necesario modificar los sensores y controles de calefacción / refrigeración ". Agrega que todo esto requiere tiempo y recursos, y su prioridad durante los últimos dos años fue desarrollar la máquina de escritorio, pero ahora también están trabajando en los sistemas robóticos ”.
Software:Aura
Antonov describe el software de Anisoprint como flexible, que permite tanto a usuarios principiantes como avanzados. “El software es fácil de usar, pero es importante que los laboratorios de I + D tengan la capacidad de cambiar los parámetros de impresión”, explica. De hecho, entre los clientes se incluyen el instituto de investigación MFPA (Weimar, Alemania), el Brightlands Materials Center (Geleen, Países Bajos) y la Universidad Técnica de Múnich, así como fabricantes como Schunk Carbon Technology, Airbus y BMW.
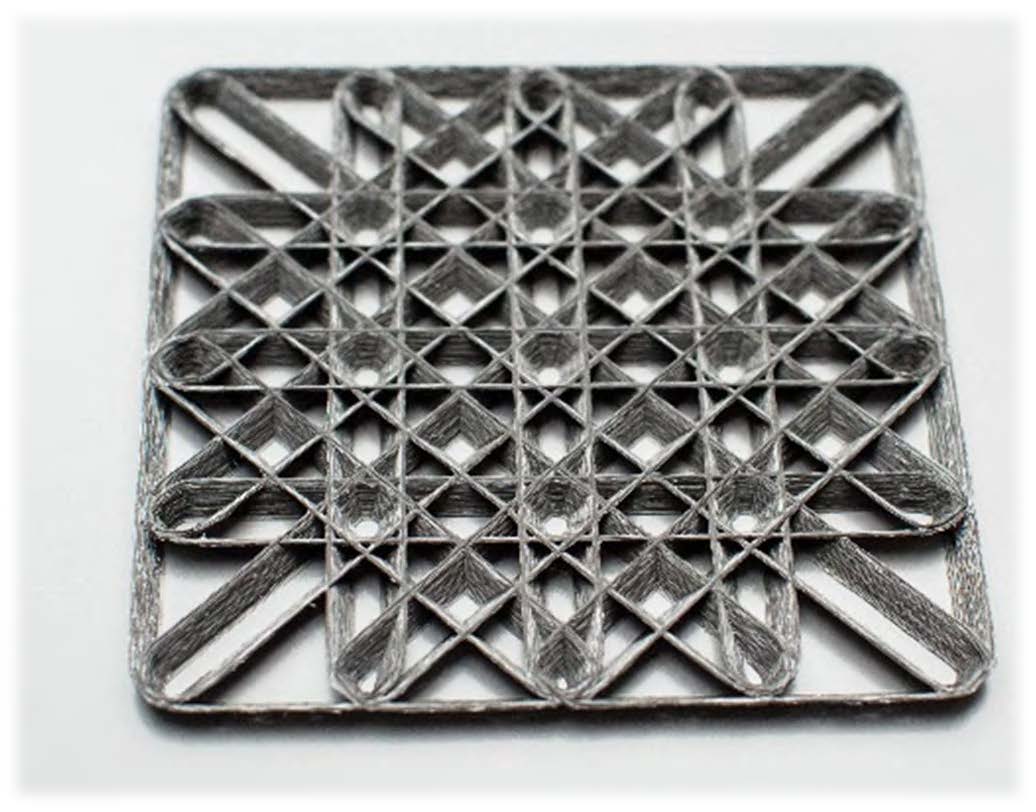
Anisoprint tiene piezas de microsatélites compuestas impresas en 3D con una reducción de peso de hasta un 45% en comparación con los metales livianos.
Asociaciones para soluciones continuas
Anisoprint, que se promociona a sí misma como una plataforma de materiales abierta, también busca desarrollar más asociaciones para nuevos materiales de impresión y piezas. En junio, anunció un acuerdo con Thought3D, con sede en Malta, para utilizar los adhesivos Magigoo de esta última. Éstos pegan la primera capa de impresión a la plataforma de impresión, evitando que la parte se despegue. “La mala adhesión de la primera capa es uno de los problemas más comunes que puede arruinar las piezas impresas, y no necesariamente al comienzo de la construcción”, explica Antonov. “Esto es especialmente importante para nuestro sistema de materiales abiertos, donde el cliente puede elegir entre diferentes tipos de termoplásticos. Cada uno requiere diferentes parámetros de impresión y es por eso que hemos introducido varias configuraciones de primera capa en nuestro software de corte Aura. Esta es también la razón por la que incluiremos barras Magigoo en cada caja de Composer para asegurarnos de que nuestros clientes tengan a mano una solución adecuada para una buena adhesión de la primera capa ”.
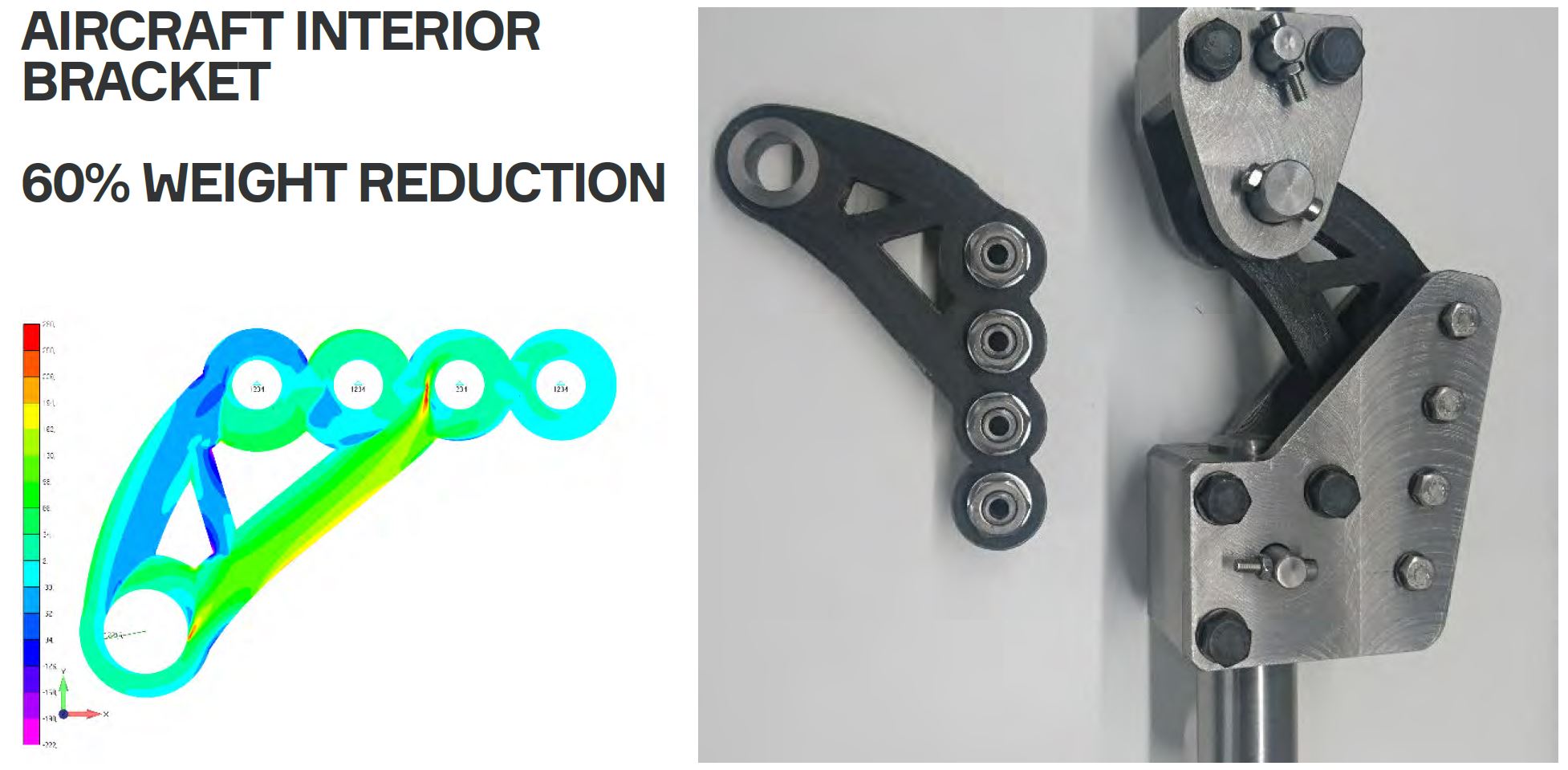
Aplicaciones de anisoimpresión
Anisoprint dice que su tecnología se puede aplicar en muchos campos, desde el aeroespacial hasta los productos de consumo y el cuidado de la salud. Un ejemplo es un soporte de asiento de avión que soporta 1,5 toneladas de carga con una reducción de peso del 40% en comparación con el aluminio. Con 100 accesorios de este tipo en un avión de pasajeros promedio de pasillo único, esta reducción de peso puede sumar un ahorro significativo en combustible y costos operativos generales.
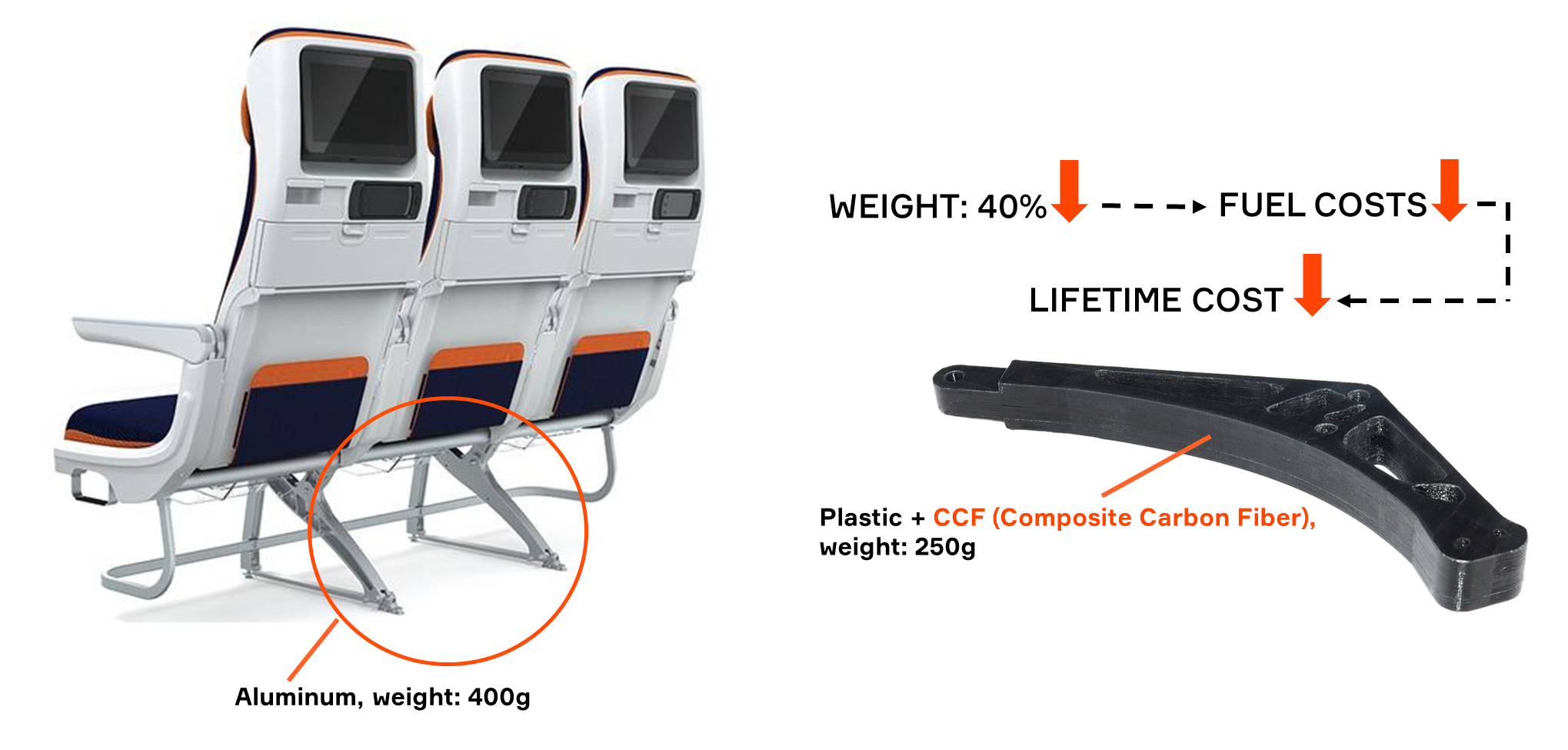
El soporte de asiento de avión compuesto impreso en 3D de Anisoprint logra un ahorro de peso del 40% en comparación con el aluminio.
Otro caso es un pistón para formar tarros de yogur, utilizado en una línea de producción de lácteos. Dichos pistones están hechos típicamente de poliamida fresada, pero reemplazar tales piezas cuando están dañadas toma tres meses, con la línea de producción cerrada mientras dura. Según se informa, la pieza impresa por un compositor Anisoprint tiene una vida útil más larga y reduce el tiempo de inactividad de la línea de producción de 3 meses a 24 horas.
Anisoprint cumplió con los requisitos para un componente de la línea de producción láctea con su pistón compuesto impreso en 3D, pero con un tiempo de reemplazo drásticamente reducido.
“La anisoprinting permite el diseño y la producción de estructuras compuestas óptimas a través de la coextrusión de fibras compuestas”, dice Antonov. “Los polímeros termoplásticos se refuerzan con fibras continuas, se consolidan y curan dentro de un proceso de una sola etapa, totalmente automatizado, sin necesidad de posprocesamiento. Como resultado, obtenemos piezas que son varias veces más resistentes, más ligeras y más baratas que los metales y plásticos tradicionales y superiores también a los compuestos convencionales ”.
Resina
- 5 procesos comunes de fabricación aditiva
- Fabricación aditiva frente a fabricación sustractiva
- Ventajas de la fabricación aditiva
- Una encuesta sobre los flujos de trabajo de fabricación aditiva
- Los 10 principales avances en tecnología de fabricación de materiales compuestos
- Fabricación de materiales compuestos:Fabricación de materiales compuestos
- Episodio 3 del podcast de fabricación aditiva
- Fabricación aditiva con composites en la industria aeroespacial y de defensa
- Henkel ofrece una plataforma de materiales para la fabricación aditiva
- Fabricación aditiva en electrónica
- Fabricación aditiva en la industria aeroespacial