Termoplásticos en la búsqueda del ahorro de peso aeroespacial
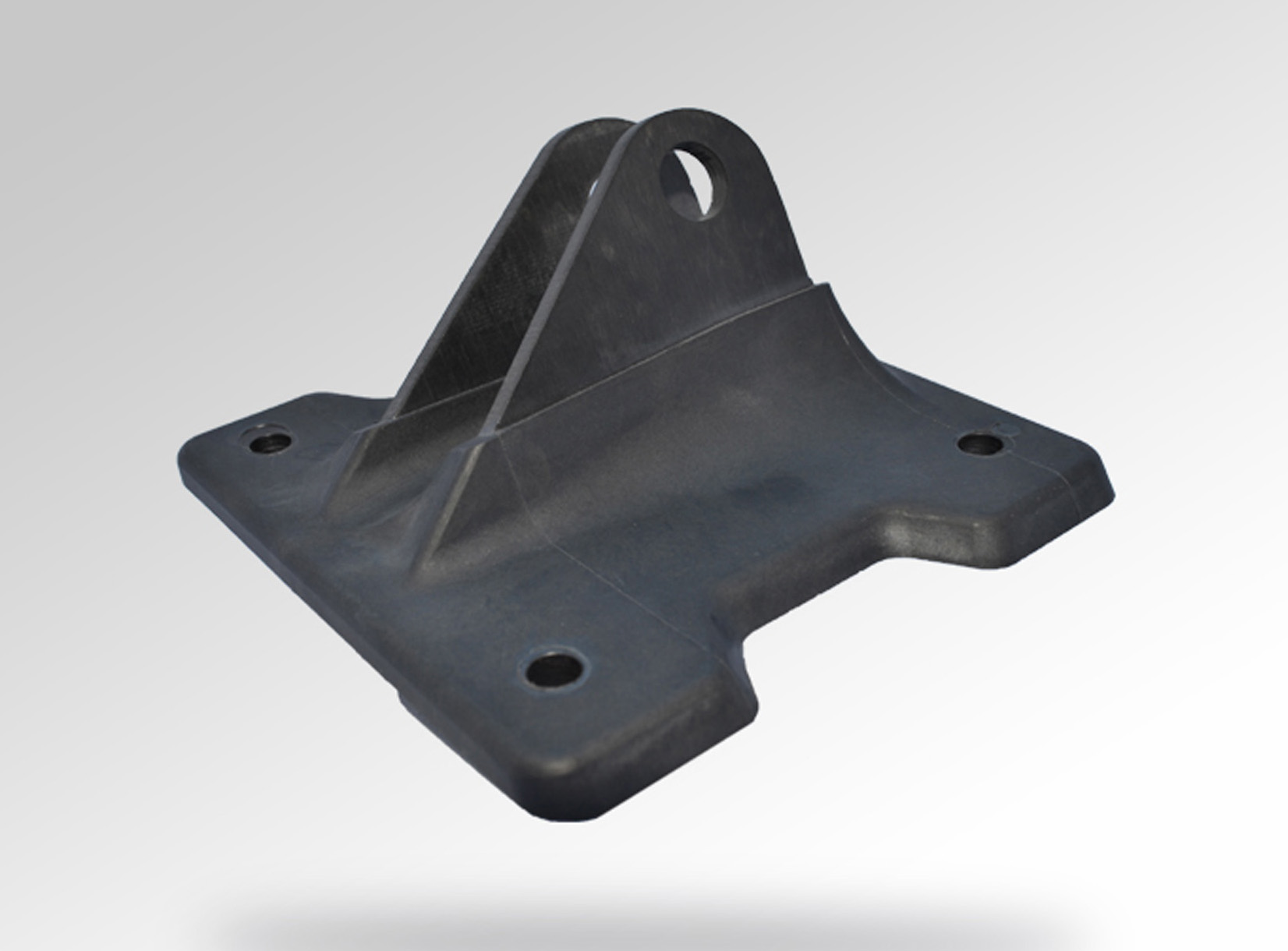
El soporte para contenedores de almacenamiento de aviones desarrollado por Victrex, Tri-Mack y Safran Cabin integra dos inserciones de fibra de carbono / PAEK sobremoldeadas con una resina de PEEK. El resultado fue una reducción de masa del 50%, una reducción de costes del 20% y una mejora sustancial en la relación de compra-venta. Fuente | Victrex
Cuando se trata de la conversión de aeroestructuras metálicas a termoendurecibles compuestos, se ha recogido la mayoría de los frutos más bajos (estructuras de alas, fuselaje y cola). En los aviones de próxima generación, es seguro que los compuestos termoplásticos también desempeñarán un papel importante en las grandes estructuras. Mientras tanto, sin embargo, existen oportunidades de conversión disponibles hoy para termoplásticos.
Una de esas piezas es un tipo que rara vez se ve, pero muy importante:soportes de carga interiores. Estos son los soportes (actualmente de aluminio, acero inoxidable y titanio) que sujetan mamparos, baños, cocinas y contenedores de almacenamiento de equipaje al piso y al fuselaje de una aeronave. Estos soportes vienen en una variedad de formas y tamaños, según lo que se coloque. Por sí mismos, estos soportes no pesan mucho. Pero, debido a que cada avión consume cientos de soportes, el peso total es sustancial.
El especialista en interiores de aeronaves Safran Cabin (Huntington Beach, California, EE. UU.) Reconoció esto y recientemente recurrió al especialista en compuestos termoplásticos Victrex (Thornton Cleveleys, Reino Unido) y al fabricante Tri-Mack Plastics Manufacturing (Bristol, RI, EE. UU.) Para convertir un contenedor de almacenamiento de aluminio. soporte de cabina a un nuevo diseño hecho con cinta unidireccional (UD) de fibra de carbono / poliariletercetona (PAEK) VICTREX AE 250 sobremoldeada con polímero VICTREX PEEK (polieteretercetona) 150CA30.
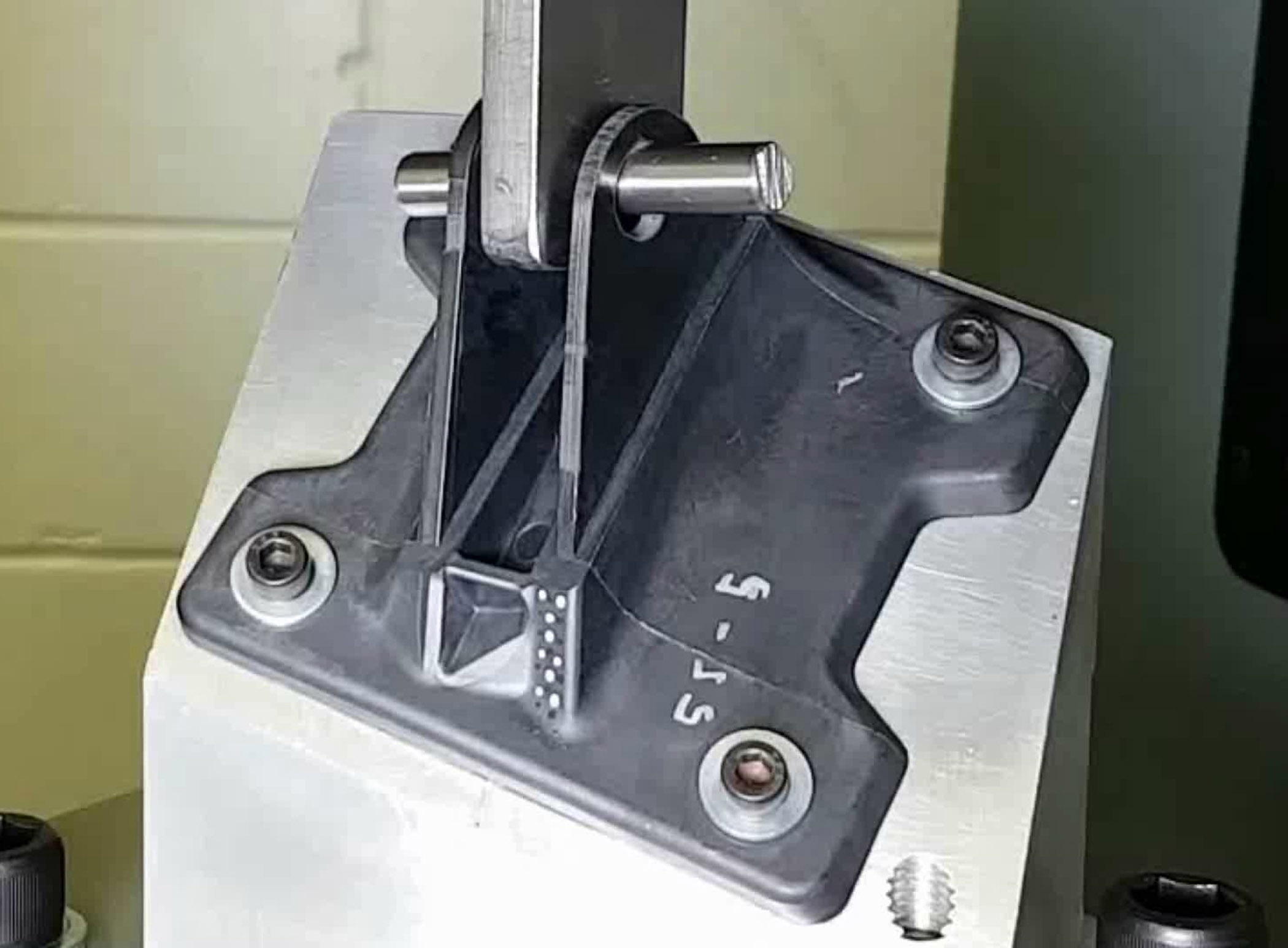
Ensayo físico del soporte sobremoldeado. Fuente | Victrex
El soporte presenta una base rectangular con dos inserciones verticales que sobresalen del centro de la base. La base tiene un orificio moldeado en cada esquina para acomodar los sujetadores; cada inserto también tiene un orificio cerca de su vértice, para acomodar los pasadores de sujeción y otros accesorios. El inserto está hecho con fibra de carbono / material PAEK; la base está sobremoldeada con resina PEEK.
Victrex y Tri-Mack, en colaboración con Safran Cabin, proporcionaron los materiales, la optimización del diseño de piezas, el procesamiento y la experiencia en herramientas necesarios para realizar las características de diseño y cumplir los parámetros clave de rendimiento. Safran Cabin brindó experiencia en diseño y fabricación para garantizar la aplicabilidad en entornos de certificación y servicio aeroespacial.
Tim Herr, director aeroespacial de Victrex, dice que los insertos se fabrican con una máquina Fiberforge de Dieffenbacher (Windsor, Ontario, Canadá), que coloca cintas de fibra de carbono / PAEK UD para construir un laminado. Este laminado se consolida a presión, se recorta el borde y luego se corta con chorro de agua para hacer las inserciones. Durante el corte con chorro de agua, cada inserto se festonea en su base para crear una superficie de interbloqueo mecánico durante el sobremoldeo.
Luego, los insertos se colocan en una herramienta, seguido de un sobremoldeo por inyección del PEEK. "Cuando sobremoldeamos", dice Herr, "estamos creando una unión muy fuerte entre el inserto compuesto PAEK y el material PEEK moldeado por inyección". La clave de este habilitador, dice Herr, es la combinación única de PAEK y PEEK. El PAEK, señala, tiene una temperatura de proceso de unos 40 ° C menos que la del PEEK. Este delta de temperatura facilita una unión íntima y duradera entre las dos partes. "Sin la invención de PAEK", argumenta Herr, "el moldeado híbrido de este tipo habría sido imposible".
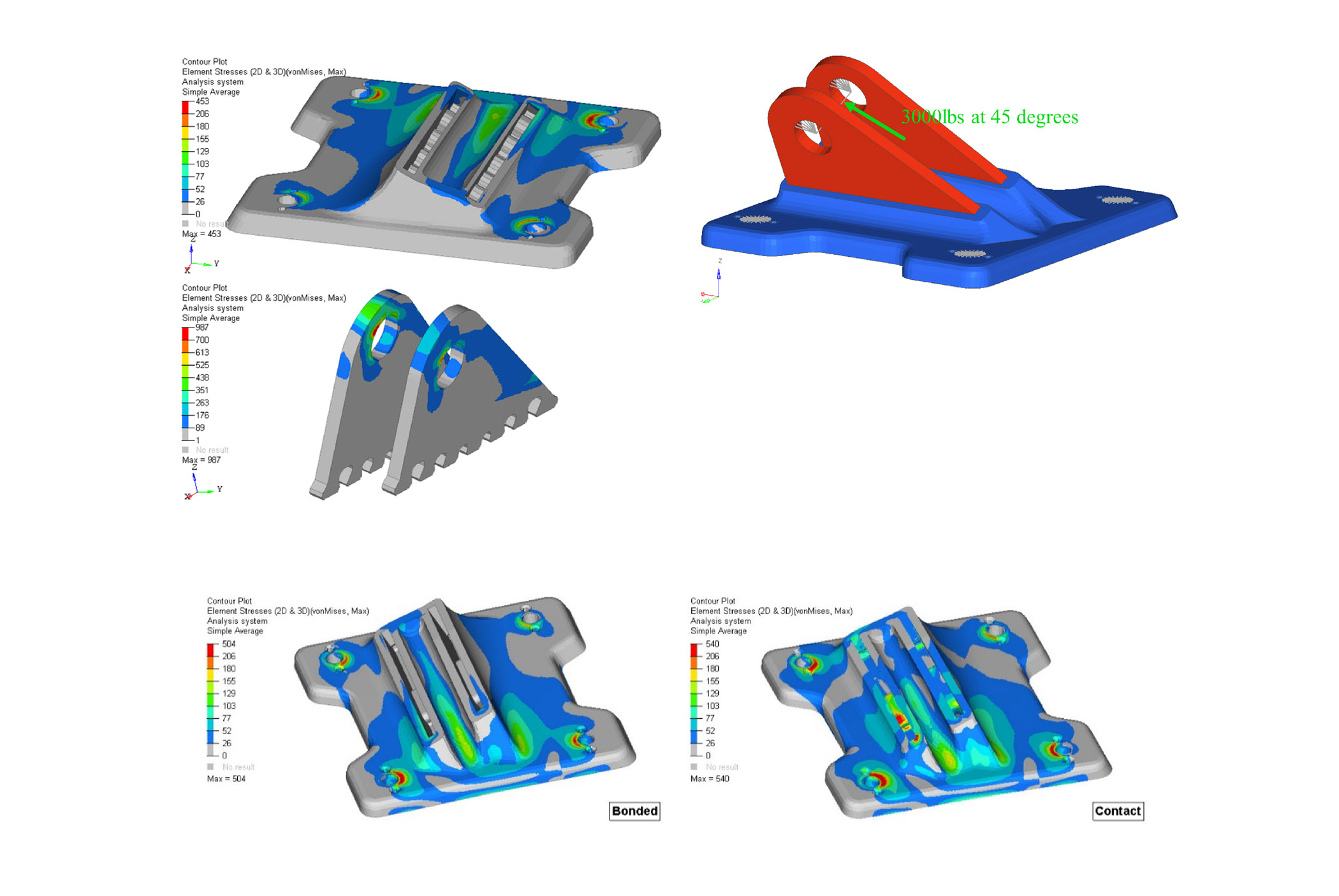
Diseñe imágenes de simulación del rendimiento del soporte en condiciones de carga. Fuente | Victrex
Esta combinación de diseño / proceso requirió una extensa simulación, análisis, creación de prototipos y pruebas físicas, a través de las cuales Victrex identificó varios defectos de diseño y proceso, incluida la deformación del inserto, vacilaciones en el flujo de resina, fallas de unión / interfaz y huecos. Esto hizo que los diseñadores volvieran a la mesa de dibujo para optimizar el diseño, y los ingenieros de fabricación volvieron a la máquina de moldeo por inyección para optimizar el proceso. La combinación de diseño / proceso final superó estos desafíos y demostró la viabilidad de un soporte sobremoldeado de compuesto termoplástico.
Los soportes prototipo iniciales se produjeron en Tri-Mack. En comparación con la pieza de aluminio original, el prototipo de material compuesto logró un 20% de ahorro de costes, un 50% de ahorro de peso y una relación 5 veces mejor entre compra y vuelo.
"Necesitamos responder a muchas demandas de soportes de aeronaves y piezas estructurales similares, y cada caso tiene muchas condiciones de carga, restricción y exposición", dice Tyler Smithson, ingeniero de I + T en Safran Cabin. "La clave del éxito es desarrollar una plataforma compuesta flexible que se pueda utilizar para múltiples proyectos, reduciendo el número de piezas y la complejidad del diseño, reduciendo el tiempo de comercialización y acelerando el tiempo de generación de ingresos".
Victrex dice que el proceso de sobremoldeo híbrido es una tecnología escalable y repetible que tiene el potencial de ayudar a los clientes aeroespaciales comerciales a reducir las tasas de desperdicio, acelerar los tiempos de ciclo, impulsar la consolidación de piezas y reducir las operaciones secundarias.
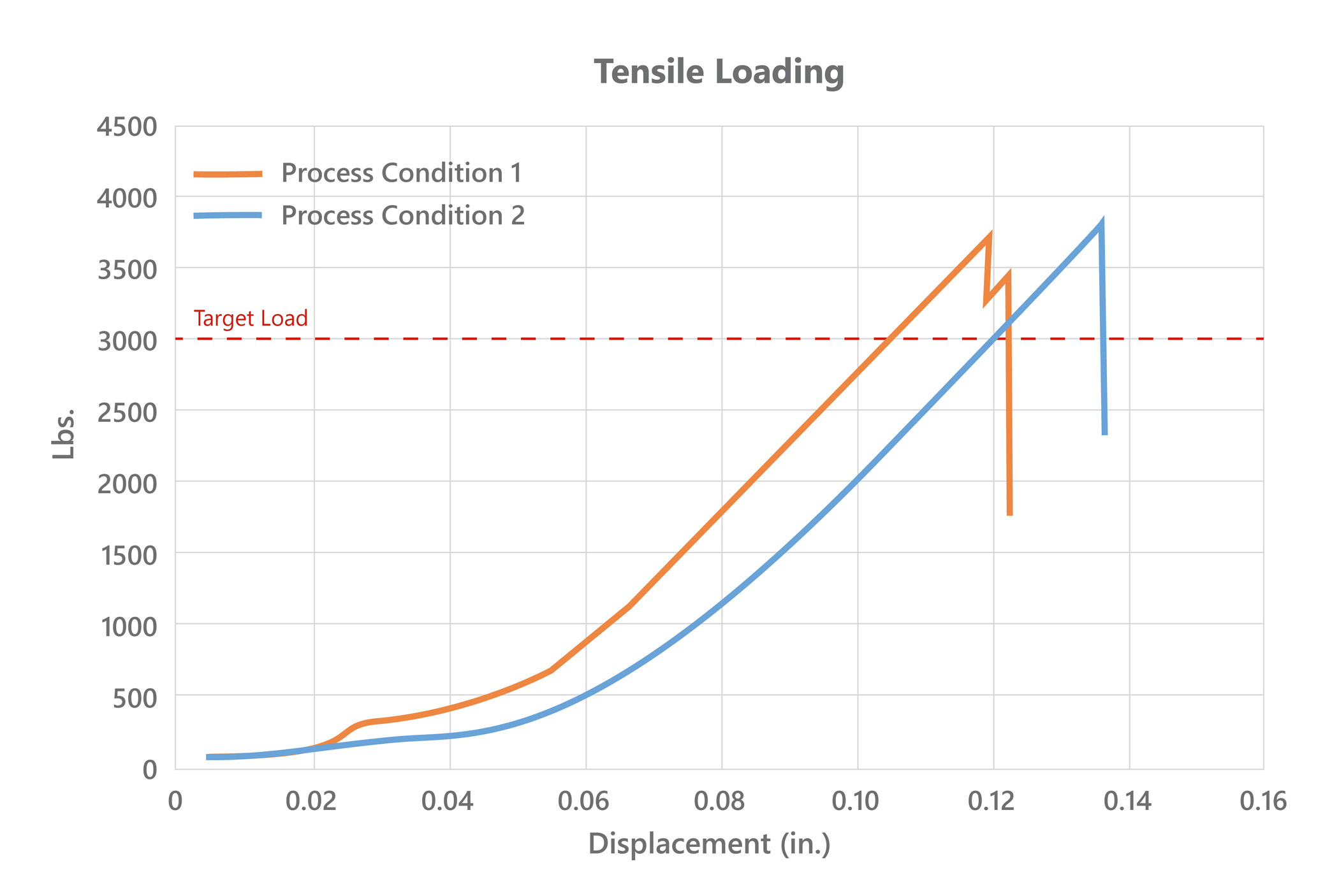
Los resultados de las pruebas que siguieron a la segunda iteración del diseño del soporte mostraron una mejora sustancial en los límites de carga y las condiciones de falla. Fuente | Victrex
"En Victrex, estamos orgullosos de nuestra trayectoria en la introducción de enfoques tecnológicos 'disruptivos' en los sectores que servimos, utilizando nuestro conocimiento en el procesamiento y rendimiento de materiales PAEK para acelerar el proceso de comercialización", comenta Herr. "El sobremoldeo híbrido y los compuestos VICTREX AE 250 se encuentran ciertamente dentro de esta categoría, pero esto es solo el comienzo. Seguimos probando nuestra oferta de compuestos, con el apoyo de nuestros clientes y socios para demostrar todo el potencial de estos materiales".
Actualmente, el soporte está programado para las pruebas finales y la calificación de las piezas de producción. “El objetivo es poner en servicio el soporte compuesto más adelante en 2019. Hemos hecho todo lo posible para demostrar que este soporte puede funcionar”, dice Herr.
Frank Ferfecki de Victrex, Tyler Smithson de Safran y Chris Bjerregaard de Tri-Mack están dando una presentación sobre el desarrollo del soporte híbrido de Safran en CAMX 2019 en el Centro de Convenciones de Anaheim (Anaheim, California, EE. UU.) El martes 24 de septiembre, 2:30 p. M., En la sala 201D
Resina
- Tecnologías de visualización para aplicaciones aeroespaciales:el Super Hornet F / A-18
- Hamilton Aerospace fue elogiado por su capacitación en mantenimiento
- Vespel®:el material aeroespacial
- Resistencia al fuego sin el peso
- Película de sensores para la industria aeroespacial
- ¡Gracias por los recuerdos!
- ¿Cuáles son los beneficios de usar chorros de agua para aleaciones aeroespaciales?
- El mercado de los componentes aeroespaciales y de los componentes aeronáuticos de precisión
- Fabricación por contrato para la industria aeroespacial
- ¿Cuáles son las pautas importantes para el diseño de PCB aeroespaciales y de aviación? - Yo
- Generación de nitrógeno en la industria aeroespacial