Compuestos impresos en 3D con 60% de fibra, menos del 1% de huecos
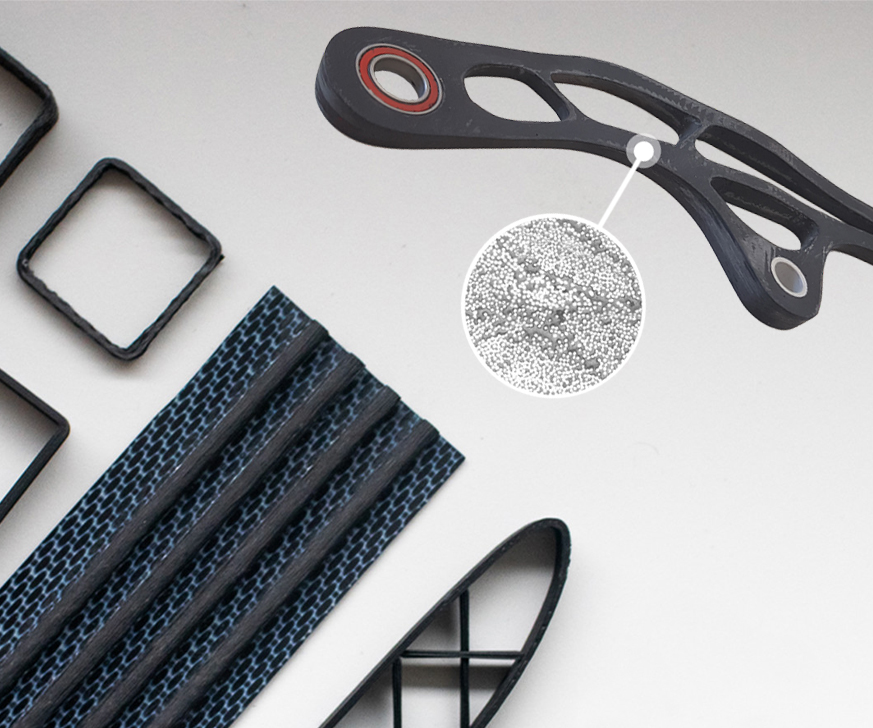
“Nuestro principal objetivo es producir compuestos de fibra continua estructural para la industria”, dice el cofundador de 9T Labs (Zúrich, Suiza), Giovanni Cavolina. "Si habla con personas que fabrican piezas de CFRP (polímero reforzado con fibra de carbono), la mayoría no cree que sea posible lograr un contenido de huecos muy bajo o una buena resistencia al cizallamiento interlaminar (ILSS) entre capas con impresión 3D de fibra continua". 9T Labs, sin embargo, ha desarrollado un posproceso patentado que elimina los huecos. "Ahora podemos imprimir en 3D compuestos de fibra continua con una gran adherencia entre capas y un contenido de huecos por debajo del 1 por ciento, lo que compite con los compuestos fabricados convencionalmente".
A partir de ETH Zúrich
9T Labs comenzó con un proyecto de investigación en el Laboratorio de Materiales Compuestos y Estructuras Adaptativas (CMAS) del Instituto Federal Suizo de Tecnología de Zurich (ETH Zurich). Los cofundadores de Cavolina y 9T Labs, Martin Eichenhofer y Chester Houwink había desarrollado un cabezal de impresión de materiales compuestos, "que montamos en un brazo robótico y fabricamos núcleos de celosía para estructuras tipo sándwich ultraligeras, destinadas a aplicaciones aeroespaciales", explica Cavolina.
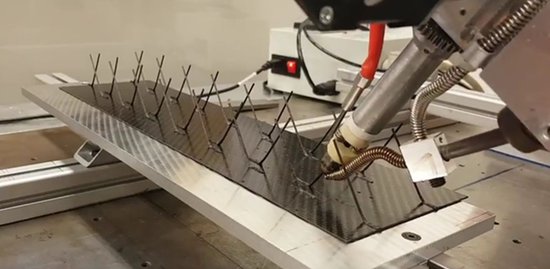
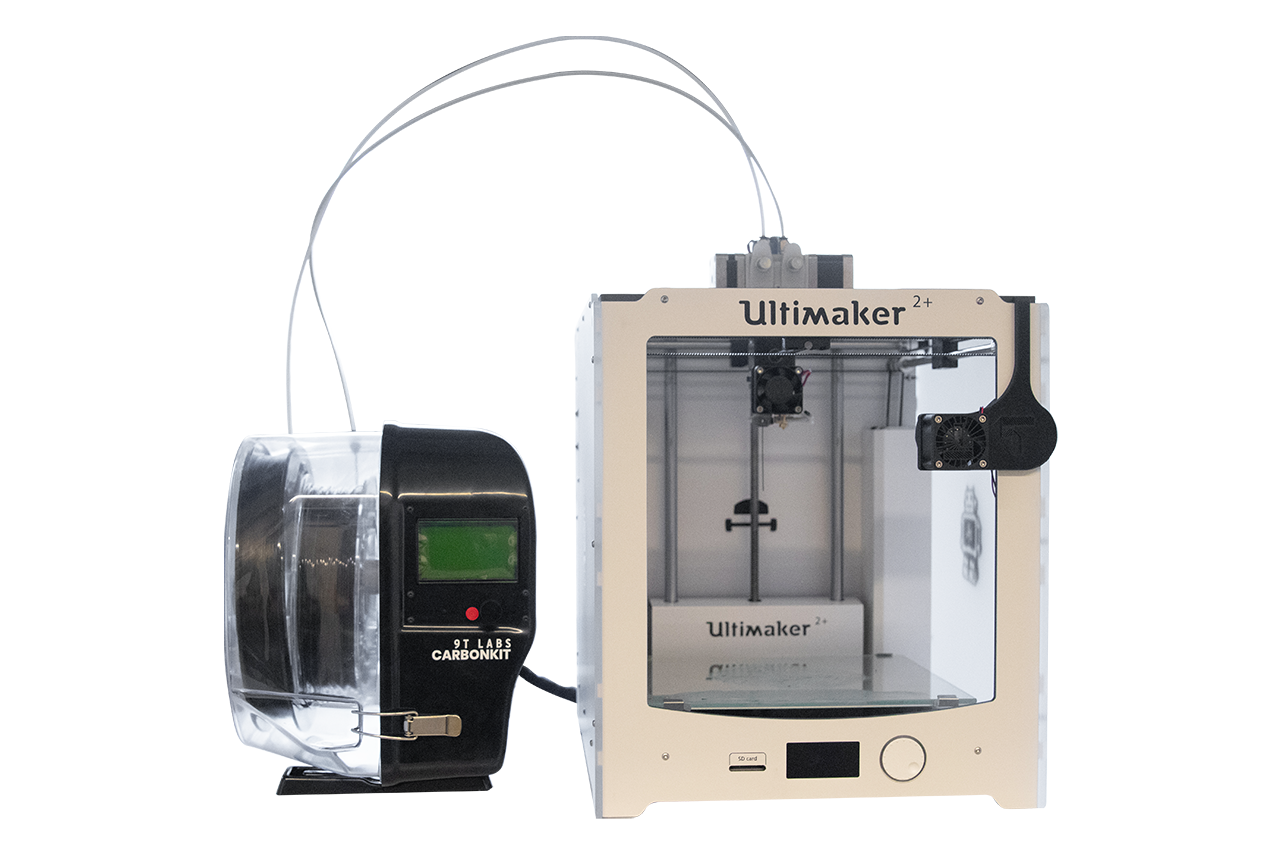
CarbonKit era un producto de lanzamiento limitado que permitía a las impresoras FDM estándar utilizar fibra de carbono continua, pero aún no era la solución adecuada para producir piezas estructurales de CFRP de la industria de costo competitivo. FUENTE | 9T Labs.
CarbonKit
Por lo tanto, 9T Labs se estableció a principios de 2018 para probar el concepto de laminados CFRP monolíticos de impresión 3D que pudieran cumplir con los requisitos de los clientes potenciales. “Nuestro siguiente paso fue CarbonKit”, dice Cavolina. Este es el producto que se presenta en CW Artículo de marzo de 2019 "Llevando la impresión 3D de fibra continua a la producción". CarbonKit transforma las impresoras 3D Ultimaker o Prusa en un sistema capaz de imprimir con fibra de carbono continua. “Le permite usar sus impresoras existentes en combinación con nuestro cabezal de impresión, filamentos y software para colocar fibras continuas, de acuerdo con el caso de carga, con un contenido de volumen de fibra de carbono del 50 por ciento, no del 30 por ciento, que ha sido la norma en la impresión 3D CFRP ”, Agrega.
Cavolina explica que a pesar de que el interés por este producto era bastante grande, “sólo abastecíamos a 25 clientes. Mantuvimos este producto limitado porque nos dimos cuenta de que con solo un proceso de FDM [modelado de deposición fundida] de un solo paso, no es posible lograr piezas estructurales de uso final para aplicaciones aeroespaciales industriales que también sean competitivas en costos con las tecnologías actuales ”.
Sin embargo, a través de CarbonKit, 9T Labs estableció valiosas relaciones con los clientes. “Pudimos aprender lo que las empresas esperaban y necesitaban, aunque estas piezas en realidad no eran posibles de producir con CarbonKit”, explica. “De hecho, la consolidación in situ es posible con FDM, pero requeriría máquinas mucho más complejas que tienen un costo prohibitivo. Entonces, produjimos un proceso de 2 pasos con una consolidación posterior a la impresión ”.
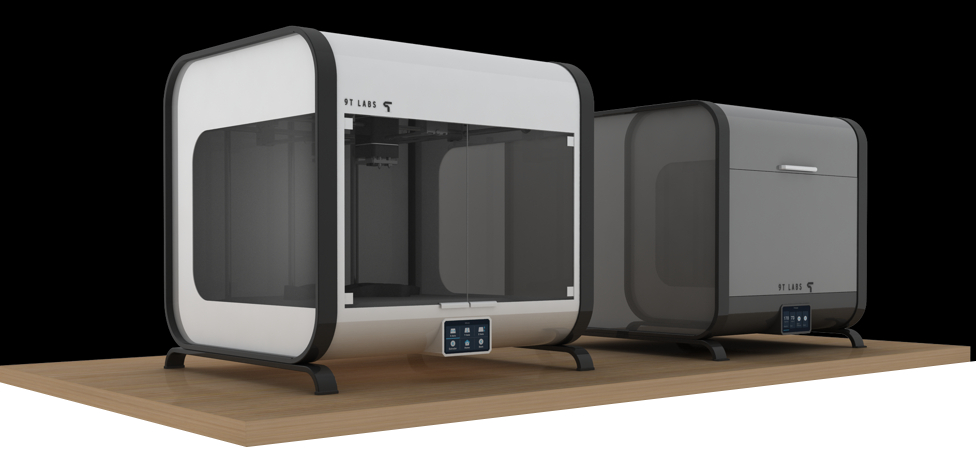
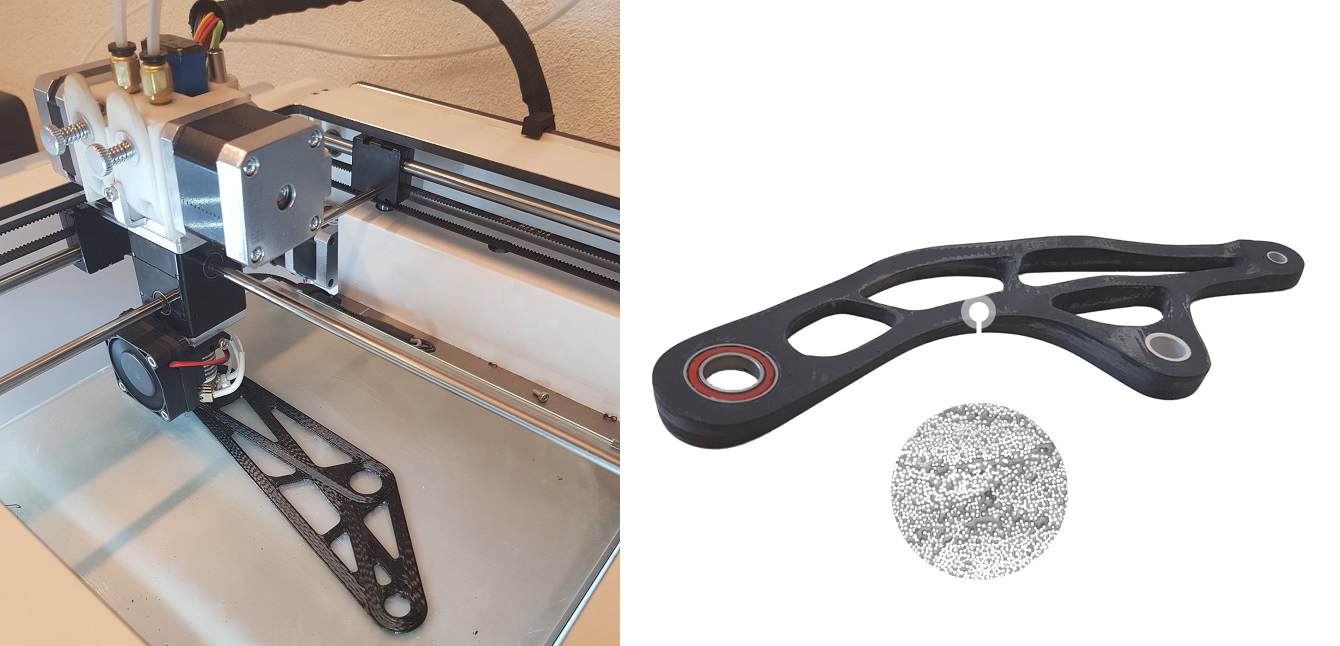
Con Red Series, 9T Labs ha logrado estructuras de CFRP impresas en 3D con> 50% de volumen de fibra y <1% de huecos a un costo asequible en comparación con los métodos de producción de compuestos actuales. FUENTE | 9T Labs.
Serie roja, proceso de 2 pasos
Eso nos lleva a donde está 9T Labs hoy. “Estamos comercializando la Serie Roja, que consta de dos unidades:una unidad de impresión FDM clásica con un cabezal de impresión patentado y una Unidad Fusion adyacente para el posprocesamiento”, explica Cavolina. “No logramos una consolidación in situ completa durante la impresión, sino que imprimimos y luego consolidamos en un segundo proceso. En esencia, estamos imprimiendo una preforma que se coloca en la Unidad de Fusión para su posterior consolidación utilizando alta temperatura y presión para lograr más del 50 por ciento de contenido de volumen de fibra con menos del 1 por ciento de huecos. Este proceso de 2 pasos logra la calidad aeroespacial a un costo asequible ".
La Serie Roja utiliza materiales termoplásticos, por ahora. “Imprimimos fibra de carbono con PEI, PEKK, PA (nailon) y también tenemos experiencia con PP”, dice Cavolina. ¿Es la Serie Roja un sistema de materiales abiertos? “La única forma de ser rentable es utilizar materiales existentes con un nuevo proceso de fabricación”, explica. “Si crea su propio material desde cero, excluye la posibilidad de pasar a la fabricación en serie. Por razones de seguridad y confiabilidad de la cadena de suministro, los fabricantes de series no dependerán de una pequeña empresa para sus materiales. Por lo tanto, permitimos que nuestros clientes usen su suministro de materiales existente, asegurándonos de que los materiales funcionen en nuestro sistema ". Explica que 9T Labs prueba los materiales para asegurarse de que la materia prima cumpla con ciertos requisitos y determine los mejores parámetros para la impresión.
¿Qué pasa con el software abierto? “Nuestro software de impresión se combina con un software de simulación estructural”, dice Cavolina. “Como ingeniero, es fantástico colocar fibras donde se necesitan, pero ¿cómo puede estar seguro de que este es el lugar donde deben colocarse? Nuestro software da la libertad de diseñar y luego verificar con una simulación estructural. La otra dirección es definir una disposición orientada a la fibra en una simulación estructural y luego convertirla en una ruta de impresión en nuestro software. Usamos un socio existente, bien probado y conocido para la FEA que se ejecuta en segundo plano. También puede diseñar directamente una pieza en CAD y luego cargar ese archivo en nuestro programa. Allí, usted decide dónde quiere la fibra de carbono y dónde es suficiente el polímero puro ”.
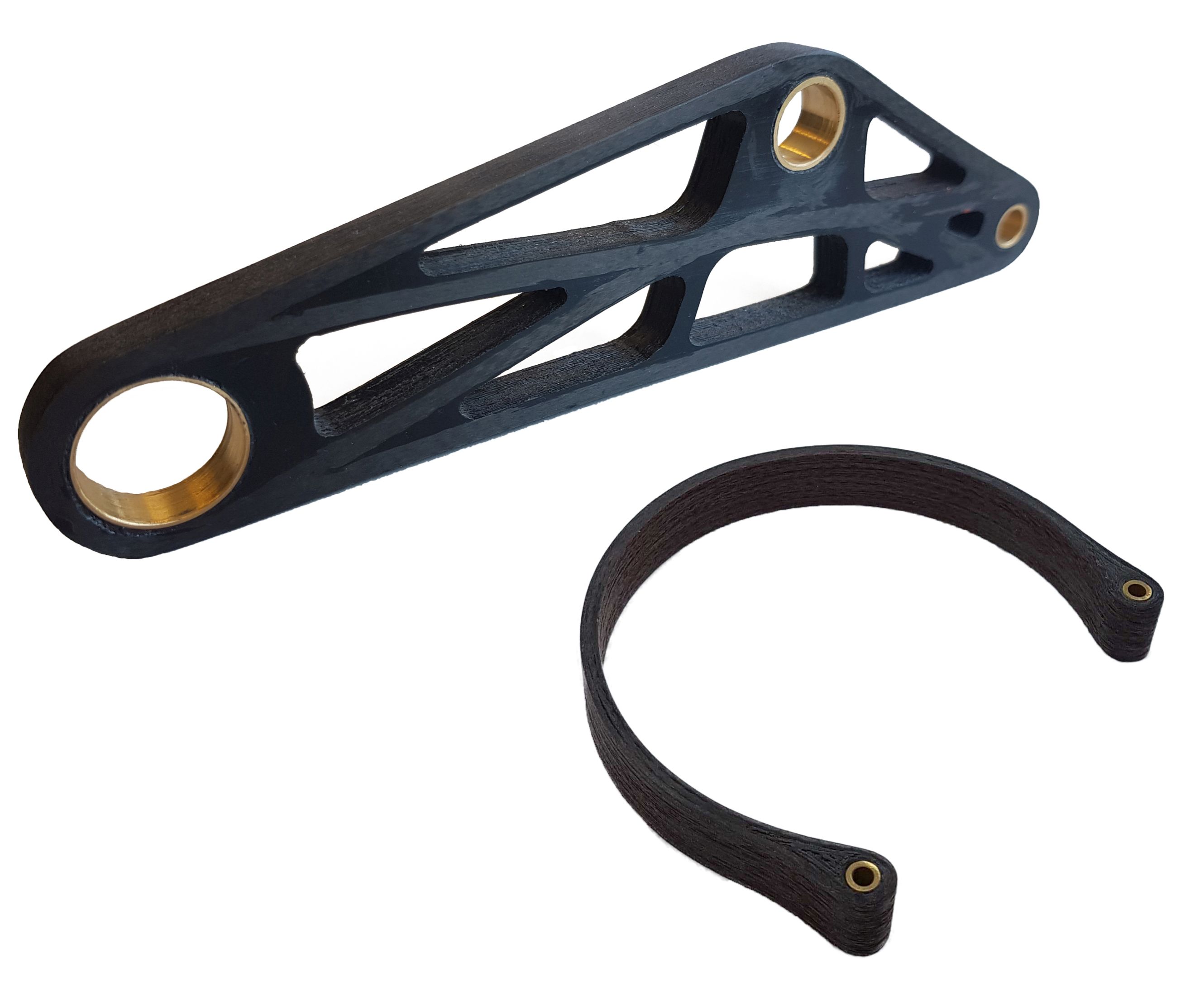
Este soporte de CFRP y balancín para aplicaciones no aeroespaciales en realidad cumple con los requisitos de laminado aeroespacial y cuenta con más de 40 capas, cada capa con una orientación de fibra diferente para aprovechar la anisotropía y optimizar las piezas estructurales que antes no eran posibles. FUENTE | 9T Labs.
Aplicaciones
9T Labs persigue la automatización aeroespacial (interiores, por ahora), biomédica e industrial (por ejemplo, máquinas de embalaje), así como ocio / lujo (por ejemplo, deportes de motor, calzado deportivo, anteojos). Este último mercado, dice Cavolina, “es donde se necesitan materiales compuestos estructurales, pero los requisitos no son tan estrictos como en el aeroespacial”. Él cita el balancín que se muestra arriba. “Este es un soporte para una estructura no aeroespacial que representa una aplicación estructural que puede producir de forma optimizada utilizando nuestra tecnología”, explica. “Proviene de una pieza de aluminio con topología optimizada para ahorrar peso al orientar las fibras de carbono según el caso de carga. Puede ahorrar costos porque puede reducir la cantidad de fibra de carbono utilizada en comparación con otros procesos compuestos. No puede hacerlo por otros medios porque no es posible con otros métodos orientar cada fibra como necesita en alta resolución ”.
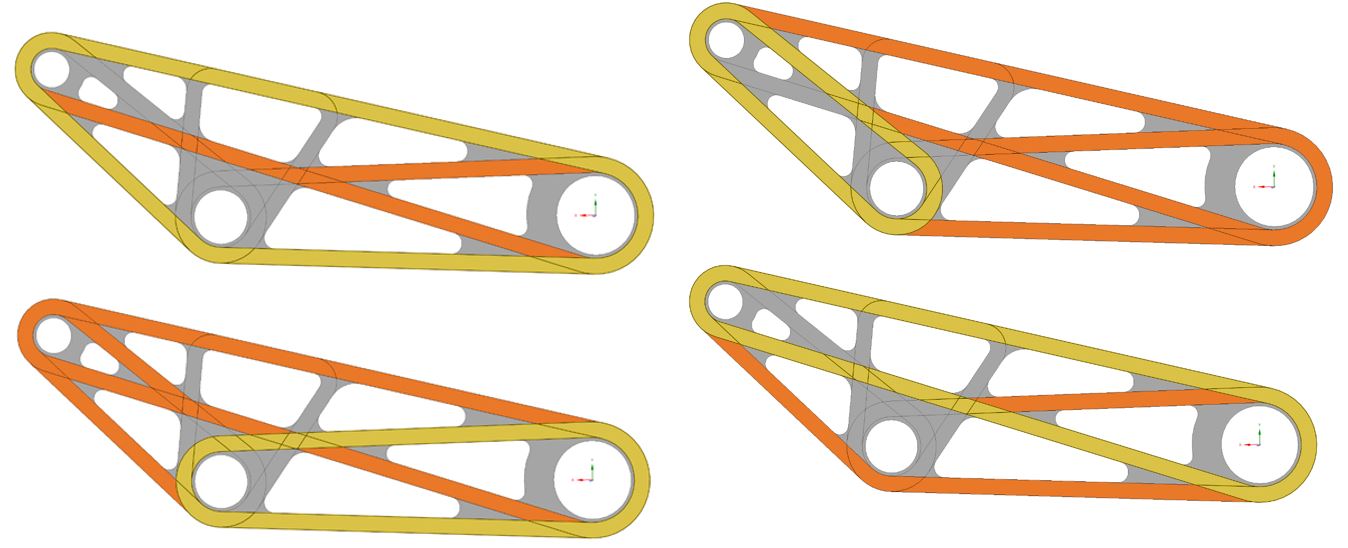
Se alternan cuatro capas continuas diferentes de fibra de carbono a lo largo del grosor del soporte CFRP impreso con la serie 9T Labs Red. FUENTE | 9T Labs.
Cavolina señala que este balancín comprende más de 40 capas de fibra y polímero, “y podemos tener diferentes orientaciones de fibra en cada capa. Probamos cuatro bandejas diferentes, no restringidas a cuasi-isotrópicas. Esta libertad nos permite aprovechar la anisotropía de los compuestos para optimizar aún más la estructura de uso final. No sería posible hacer esto con otros métodos de fabricación actuales ”.
También señala que la impresión 3D CFRP es un proceso automatizado en comparación con la colocación manual. “Nuestra tecnología reduce drásticamente el trabajo manual mediante la colocación automatizada”, dice Cavolina. "Con nuestra tecnología, solo imprime, consolida y listo".
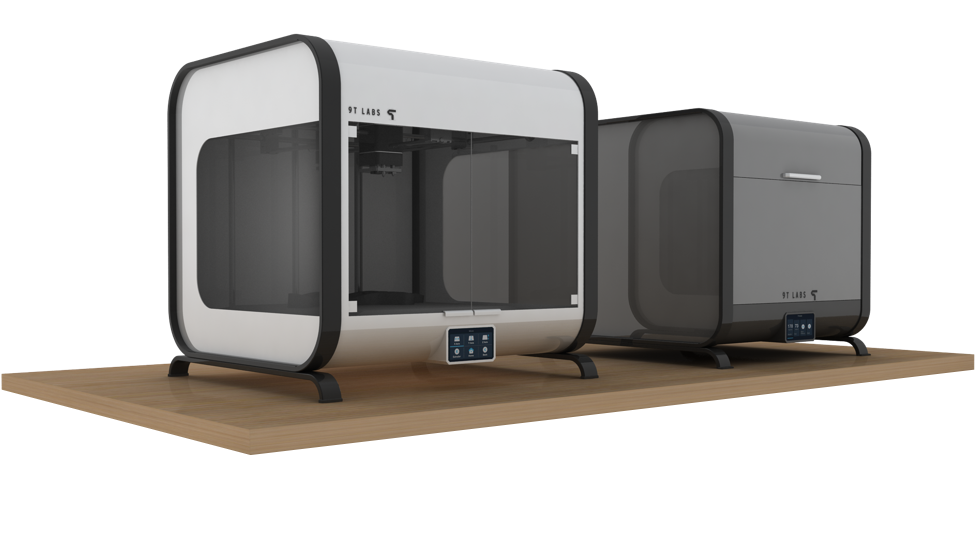
La Serie Roja imprime preformas de CFRP monolíticas, complejas y más pequeñas que luego se consolidan en un segundo paso para la producción en serie industrial escalable. FUENTE | 9T Labs.
Tamaño de impresión, velocidad e inicio completo de Red Series
La Serie Roja está dirigida a piezas monolíticas más pequeñas para la fabricación en serie dentro de un área de impresión de 350 milímetros por 300 milímetros. “Aquí vemos en este momento el mayor valor agregado para nuestros clientes”, explica Cavolina.
¿Qué pasa con la velocidad de impresión? “Estamos hablando de una manera muy concreta acerca de producir en los próximos 1 a 2 años de 4.000 a 8.000 piezas por año para diferentes clientes, lo que se logra con las unidades gemelas de la Serie Roja”, dice Cavolina. "Debido a que hemos desacoplado la producción de preformas complejas y detalladas de la consolidación, ahora es posible aumentar el volumen de producción rápidamente".
“Hemos dedicado mucho tiempo a analizar la estructura de costos de nuestro proceso, incluidos los costos de equipos, mano de obra y materiales”, responde. “Tenemos una estructura de costos de equipos asequible y hemos automatizado el proceso de preformado. Usamos materiales que son los más asequibles y eficientes, y luego reducimos la cantidad de material requerido al orientar las fibras según el caso de carga y usar la optimización estructural. Trabajamos en estrecha colaboración con nuestros socios en la simulación estructural y de procesos y vemos que continuará creciendo como una gran parte del objetivo de producción de utilizar la tecnología de gemelos digitales para permitir el plug and play con las líneas y células de producción 4.0 ".
La Serie Roja se lanzará en 2020. “Ahora, la estamos evaluando a través de nuestros programas de colaboración con socios de producción. Certificamos las piezas y los procesos con ellos, por lo que han reservado las primeras ranuras para las máquinas de la Serie Red y las utilizarán para fabricar sus productos de uso final ”.
Resina
- Refuerzo de piezas impresas en 3D con enrutamiento de fibra eficiente:Parte 1
- Parte de la semana:trípode impreso en 3D con patas continuas reforzadas con fibra de carbono
- Reciclaje:compuestos termoplásticos reforzados con fibra continua con policarbonato reciclado
- Los compuestos de fibra de carbono corta amplían el alcance de los compuestos termoplásticos
- Reducción del costo de los materiales de impresión 3D de fibra continua
- TxV Aero Composites cumple con los estándares AS9100
- Hexcel se asocia con Lavoisier Composites, Arkema
- Reciclaje de materiales compuestos:no más excusas
- Covestro lanza los termoplásticos de fibra continua Maezio
- Fabricación continua de fibra (CFM) con compuestos moi
- Compuestos de impresión 3D con fibra continua