Compression RTM para la producción de futuras aeroestructuras
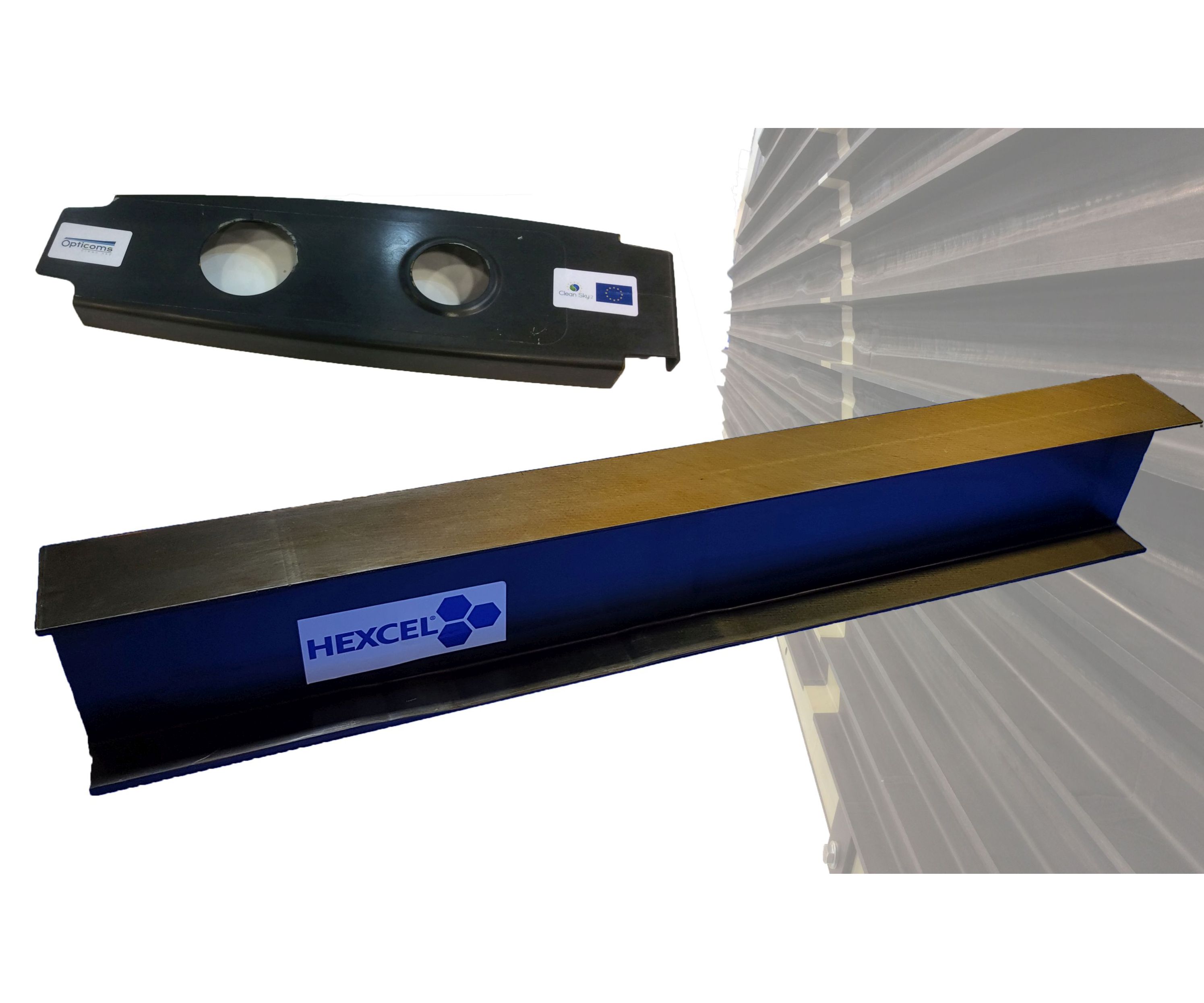
Los materiales compuestos han asegurado un lugar permanente en las estructuras de los aviones comerciales porque permiten estructuras livianas y de alta resistencia que brindan menores costos de mantenimiento en comparación con el metal. Las proyecciones actuales para la próxima generación de aviones de fuselaje ancho y estrecho muestran un crecimiento continuo en los fuselajes compuestos, pero solo si los materiales y procesos pueden cumplir con los objetivos desafiantes de bajos costos y altas tasas de producción. Aunque el preimpregnado epoxi curado en autoclave ha reinado supremo en las células de polímero reforzado con fibra de carbono (CFRP) hasta la fecha, los desarrolladores de aviones de próxima generación están persiguiendo agresivamente tecnologías fuera de autoclave (OOA) con automatización integrada e inspección en línea como habilitadores clave para futura producción de la Industria 4.0.
El proveedor de equipos y automatización Techni-Modul Engineering (Coudes, Francia) y su subsidiaria estadounidense Composite Alliance Corp. (Dallas, Texas, EE. UU.) Se han asociado con las unidades comerciales del Reino Unido y Francia del proveedor de materiales avanzados Hexcel (Stamford, Connecticut, EE. UU.) para demostrar la producción automatizada de OOA de nervaduras y largueros de CFRP. Las piezas están fabricadas con preformado automatizado de refuerzos de fibra de carbono seca Hexcel y un proceso de moldeo por transferencia de resina de compresión (C-RTM) que ofrece una rápida infiltración de resina epoxi líquida Hexcel HexFlow RTM6 para producir piezas con un 60% de volumen de fibra y menos del 1% de huecos. en un ciclo de 2,5 a 3,0 horas que se puede escalar para producir varias piezas para una producción de alta velocidad.
Desarrollo de armaduras en seco
“Consideramos que el moldeado de compuestos líquidos (LCM) ofrece una respuesta al desafío de tres vías para reducir los costos, estar listo para la tarifa y proporcionar el rendimiento de la estructura primaria”, explica Rémy Pagnac, Ingeniero de soporte técnico de Hexcel para moldeo de compuestos líquidos. Hexcel ha desarrollado su tejido no ondulado HiMax (NCF) y sus materiales de fibra de carbono unidireccional (UD) HiTape para abordar las necesidades de rendimiento de la estructura primaria cuando se utilizan procesos LCM. HiMax permite colocar rápidamente estructuras grandes y planas, como pieles de alas, mientras que HiTape permite capas a medida para estructuras grandes y complejas con un mínimo de desperdicio. “Podemos lograr propiedades iguales a las de los preimpregnados UD de última generación”, agrega Pagnac.
Hexcel ha trabajado para reducir el volumen y mejorar la capacidad de drapeado con HiMax NCF, incluido un hilo de puntada fina de 20 dTex. Los materiales HiMax se fabrican en las instalaciones anteriores de Formax en Leicester, Reino Unido, que Hexcel adquirió en 2016. Los multiaxiales ligeros y de arrastre extendido producidos en esta instalación ya tenían una larga historia de proporcionar soluciones para aplicaciones exigentes como yates de carreras, superdeportivos y Formula 1 coche de carreras. Ahora los materiales NCF se han utilizado en un proyecto de demostración de alas completado por Airbus Defence and Space (Airbus DS, Cádiz, España) y Danobat (Elgoibar, España) utilizando la tecnología de colocación automática de material seco (ADMP) de esta última, un tipo de colocación automatizada de fibra. (AFP) para NCF (consulte "Demostración de la viabilidad de la infusión de tejidos secos para grandes aeroestructuras") y en el proyecto ZAero patrocinado por Airbus para estructuras de CFRP sin defectos, como pieles de alas reforzadas con largueros (consulte "Fabricación sin defectos de piezas compuestas ”).
Tanto con HiMax como con HiTape, Hexcel integra capas delgadas de velo de filamento termoplástico de bajo peso que actúan como aglutinantes, eliminando la necesidad de aglutinantes en polvo que se han utilizado históricamente en materiales secos para preformado y moldeado líquido. Para HiMax, este velo está entrelazado entre capas NCF; para HiTape, el velo se aplica a ambos lados de la unitape de fibra de carbono. "Con esto, no es necesario utilizar aglutinante en polvo para mantener las capas de UD en su lugar", explica Pagnac. “HiTape está calibrado y no es una cinta de hendidura, por lo que no hay pelusa y hay menos variación en el ancho para mejorar el procesamiento AFP. El velo termoplástico también agrega dureza al laminado final, y hemos demostrado que podemos lograr altas tasas de deposición de material con la próxima generación de máquinas AFP ”. En un artículo de SAMPE de mayo de 2015, Hexcel describe una preforma de una sola curvatura fabricada con HiTape de 0,25 pulgadas de ancho aplicado con una máquina AFP Coriolis Composites (Quéven, Francia) equipada con láser a una velocidad de laminado de 1 metro / segundo. También ha trabajado con el equipo AFP Electroimpact (Mukilteo, Washington, EE. UU.) Para demostrar tasas de deposición de hasta 150 kilogramos / hora para una aeroestructura de mástil de tamaño completo.
Fig. 1 Compresión RTM
En C-RTM, la preforma seca se coloca en un molde RTM, pero el molde es solo parcialmente cerrado, dejando un espacio entre la preforma seca y la superficie superior del molde. Luego se aplica vacío, se inyecta resina y la prensa cierra el espacio en el molde, empujando la resina líquida hacia abajo en la preforma en la dirección z a través de toda la pieza. Fuente | Hexcel

Adaptación de C-RTM para la industria aeroespacial
C-RTM se introdujo por primera vez con RTM de alta presión (HP-RTM) para compuestos de automoción. Al igual que con el RTM convencional, C-RTM implica colocar una preforma de fibra seca en un molde de metal emparejado, inyectar resina líquida en la preforma y luego aplicar calor y presión usando una prensa accionada. En C-RTM, sin embargo, el molde es solo parcialmente cerrado, dejando un espacio entre la preforma seca y la superficie superior del molde (Fig. 1). Luego se aplica vacío, se inyecta una dosis precisa de resina mezclada y la prensa cierra el espacio en el molde, forzando la resina líquida hacia la preforma en la dirección z a través de toda la pieza. “Esto es mucho más rápido que inyectar la resina en el plano a través de la pieza”, explica el ingeniero de procesos de Techni-Modul Engineering, Thomas Chevallet.
Techni-Modul Engineering vio la oportunidad de adaptar C-RTM para la industria aeroespacial durante su papel como socio en el proyecto Clean Sky 2 “Optimized Composite Structures” (OPTICOMS). Organizado dentro del Paquete de Trabajo B-1.2 ("Estructuras compuestas más asequibles"), OPTICOMS tiene como objetivo reducir los costos de producción de aviones pequeños (por ejemplo, aviones regionales) a través de estructuras integradas y fabricación automatizada, explorando métodos de resina líquida y preimpregnados. OPTICOMS ha diseñado un demostrador de ala compuesta que comprende un revestimiento de alas superior con tres largueros, producido como una estructura integrada en un proceso de un solo disparo. El ala a gran escala (Fig.2) es parte de un Demostrador de Tecnología Innovadora (ITD) AIRFRAME para evaluar y madurar tecnologías hacia el nivel de preparación tecnológica (TRL) 6 para aeronaves de próxima generación en producción a partir de 2025. Israel Aerospace Industries (Lod, Israel) fue seleccionada como coordinadora de OPTICOMS en julio de 2016. El consorcio también incluye al OEM de aeronaves pequeñas Piaggio Aerospace (Savona, Italia), Techni-Modul Engineering y los proveedores de equipos AFP Coriolis Composites y Danobat.
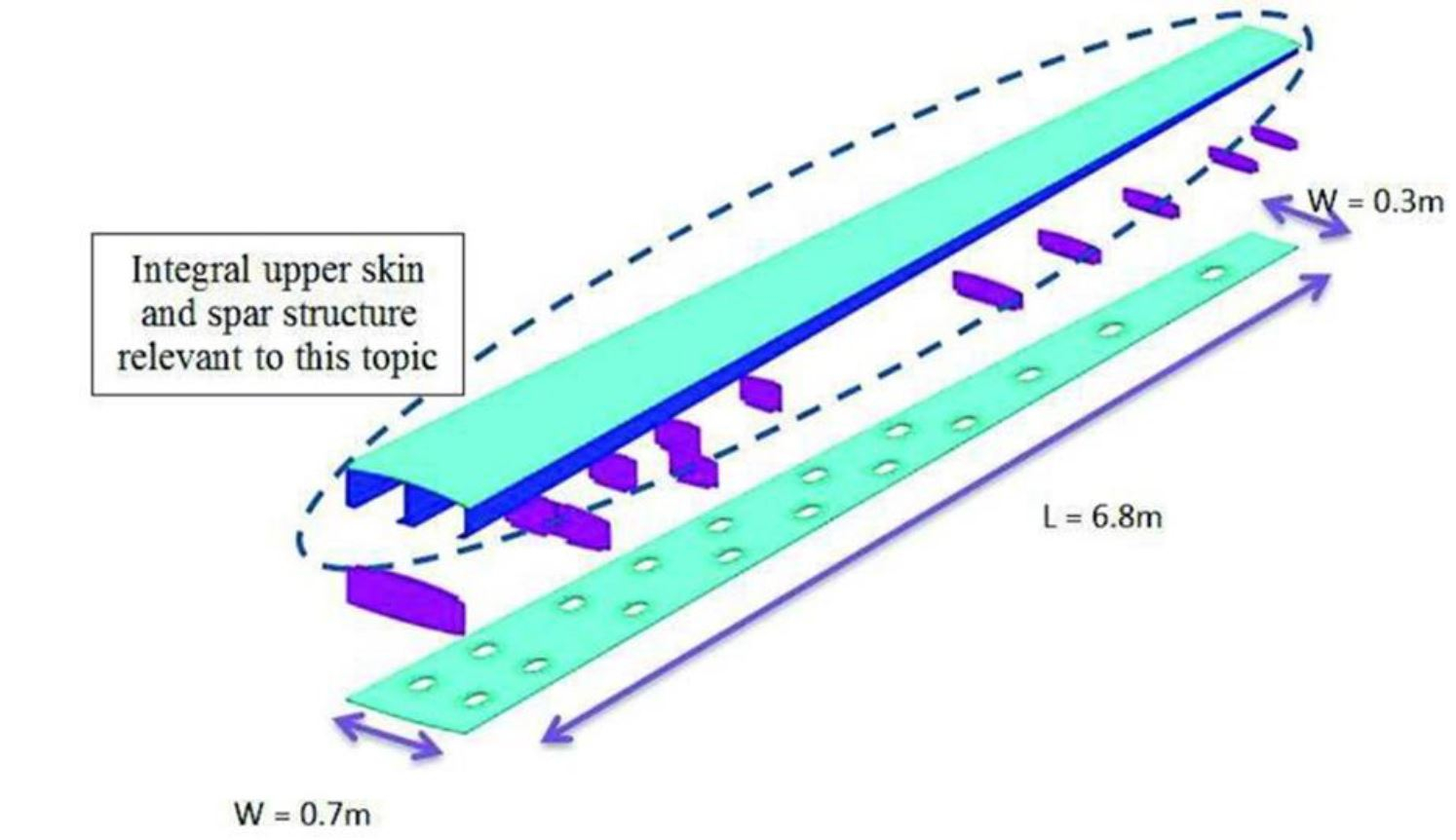
Fig. 2 costillas Clean Sky 2 OPTICOMS
Techni-Modul es socio en el proyecto Clean Sky 2 “Optimized Composite Structures” (OPTICOMS), que ha diseñado un demostrador de ala compuesta que comprende un ala inferior, varias costillas y un ala superior con tres largueros. Este último se produce como una estructura integrada en un proceso de una sola vez. El demostrador será evaluado para aviones de próxima generación en producción a partir de 2025. Fuente | Cielo limpio 2
“C-RTM era bien conocido en la industria”, explica Chevallet, “pero con HP-RTM, todavía se necesita una gran prensa. Nuestro desarrollo fue adaptar C-RTM para una inyección rápida utilizando presiones más bajas, lo que permite una producción menos costosa de piezas aeroespaciales con requisitos muy estrictos de alto volumen de fibra, alineación de fibra y pocos huecos. El tiempo de inyección para la nervadura del ala de 0,7 metros de largo por 0,2 metros de ancho en el proyecto OPTICOMS se redujo de 40 a cinco minutos. En un programa de prueba separado para un larguero de vigas en I que mide 900 milímetros de largo y 150 milímetros de alto, el tiempo de inyección se redujo de una hora a menos de cinco minutos.

“Esta reducción en el tiempo de inyección ofrecida por C-RTM sería aún mayor para piezas grandes como alas completas o palas de rotor de helicóptero”, agrega Chevallet. Señala que C-RTM también permite la inyección de resinas de alta viscosidad, así como sistemas de inyección de menor presión y prensas de menor tonelaje, lo que reduce los costos. “La presión del molde durante C-RTM es de solo 6 bar, mucho más baja que la que se usa en HP-RTM”, explica Chevallet. "El proceso logra compuestos de calidad aeroespacial, pero funciona bien para piezas grandes y delgadas y piezas más pequeñas de formas complejas".
Preformado automatizado
Aunque la inyección de resina más rápida y de menor costo y el moldeo OOA son partes clave de este enfoque para una producción de aerocomposites más asequible, la cadena de proceso aún requiere múltiples pasos para cortar y colocar materiales y preformados. “Para nosotros, OPTICOMS también se trataba de automatización”, dice Chevallet. Techni-Modul Engineering suministró no solo un sistema de inyección C-RTM para el proyecto OPTICOMS, sino también un robot pick-and-place y una máquina formadora de cortinas en caliente (HDF), todos integrados en una celda de producción totalmente automatizada.
Poco después de que OPTICOMS comenzara en 2016, la subsidiaria de Techni-Modul Engineering, CAC, ganó el premio ACE Equipment and Tooling Innovation Award en la categoría de fabricación por su celda de preformado 3D automatizada en CAMX 2016 (26-29 de septiembre, Anaheim, California, EE. UU.). Capaz de producir preformas 3D a partir de fibra seca o preimpregnado, la celda utilizó pinzas de succión al vacío para recoger, colocar y doblar las capas cortadas en un molde de preforma calentado. Techni-Modul Engineering y CAC desarrollaron un software para preparar las capas cortadas de materiales 2D para dar forma a superficies complejas y desarrollables. Esta celda se desarrolló aún más en OPTICOMS y el proyecto de prueba de vigas en I.
Paso 1
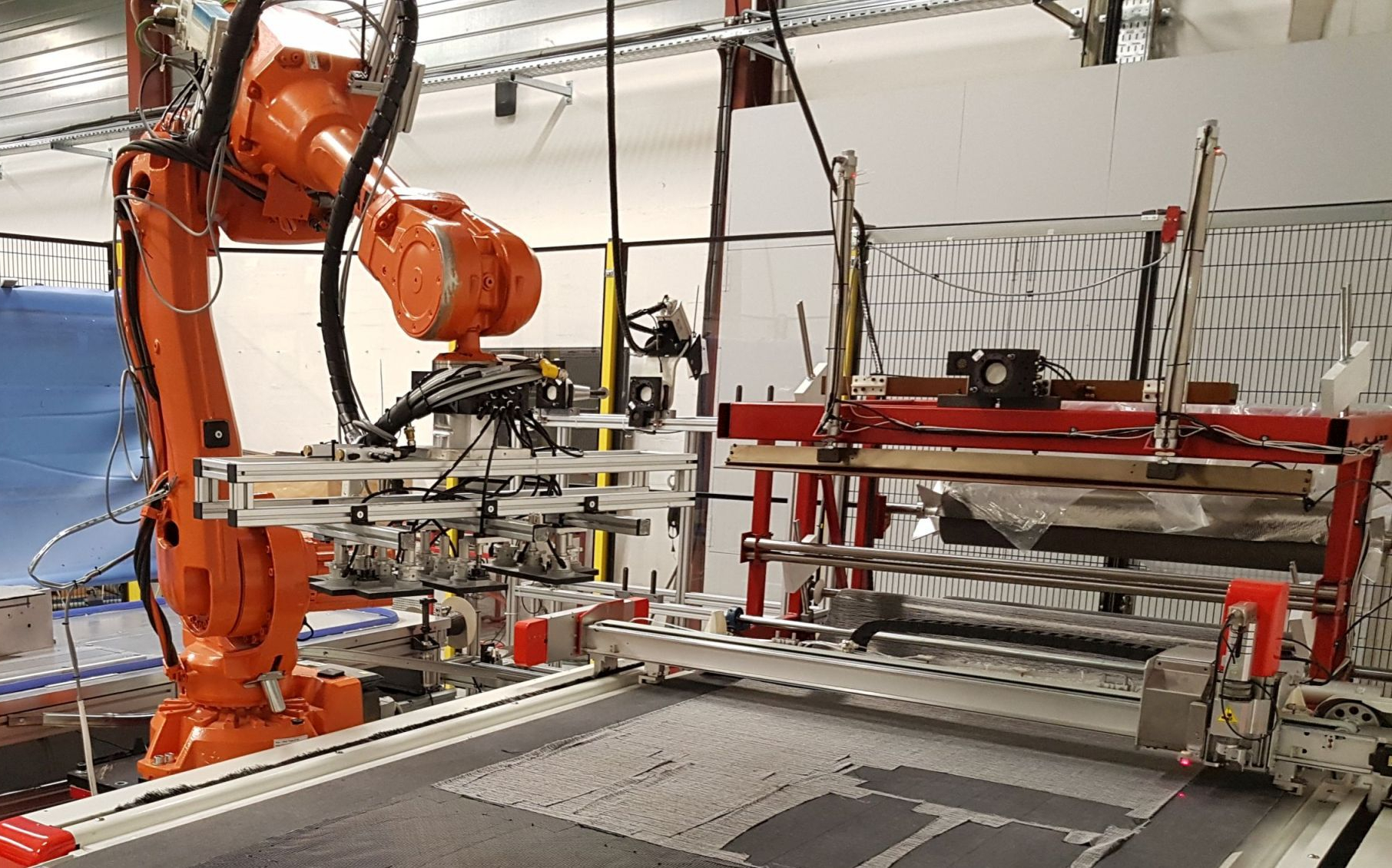
Fuente, todas las imágenes de paso | Ingeniería Techni-Modul
Dentro de la celda automatizada de Techni-Modul Engineering, un robot de recogida y colocación retira las capas de un cortador automático y las aplica a una herramienta de preformado calentada.
Paso 2

Las herramientas de preformado se asientan sobre una mesa de compactación con una membrana de vacío reutilizable con bisagras (azul, a la izquierda) que se usa para completar una reducción de volumen calentada cada 5-8 capas durante la colocación.
Paso 3
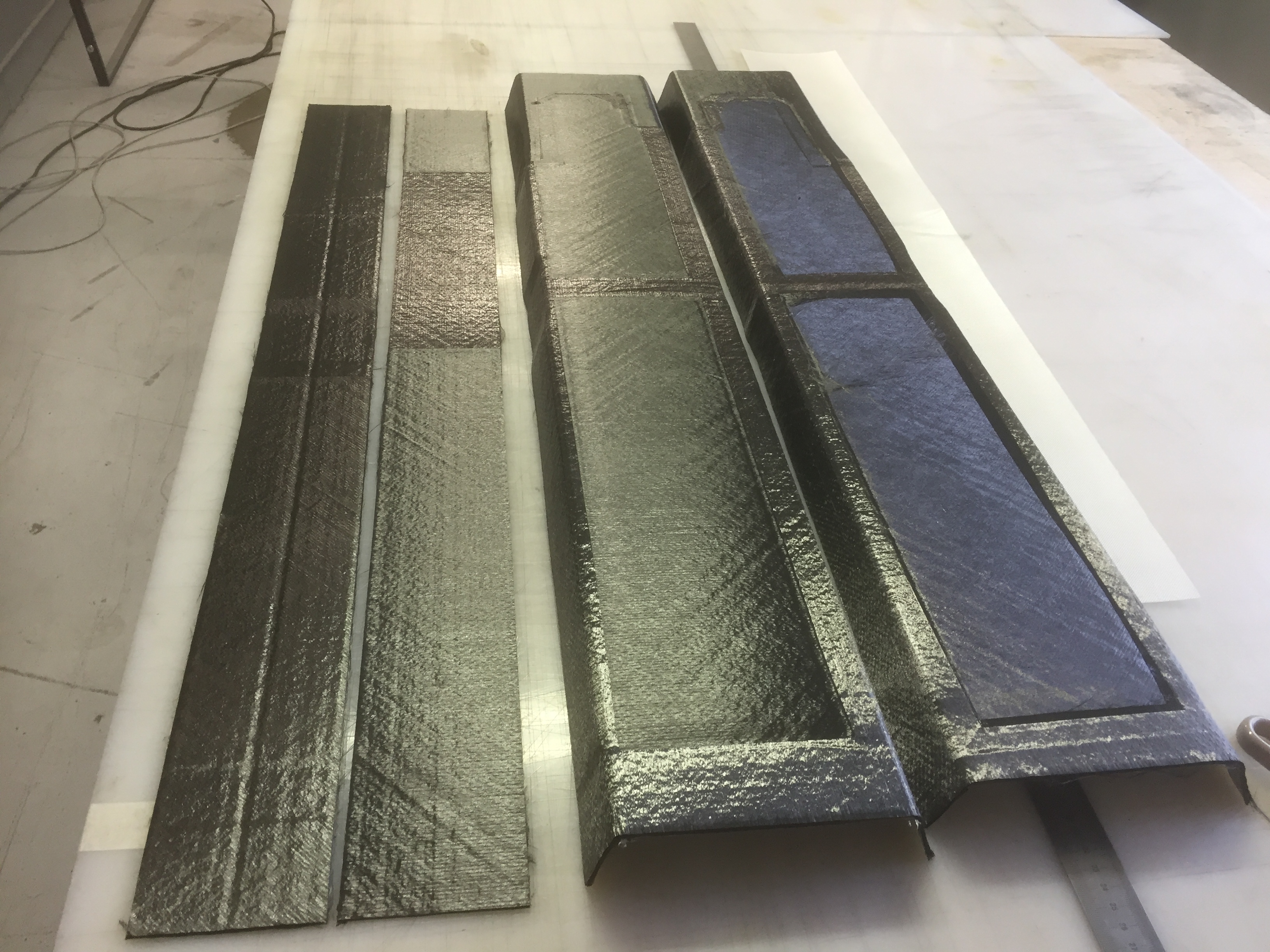
Cada ciclo de preformado de larguero produce una preforma de viga en C (dos comprenden el alma de la viga en I) y una preforma de ala plana. Aquí se muestran dos juegos necesarios para cada larguero de vigas en I.
Paso 4
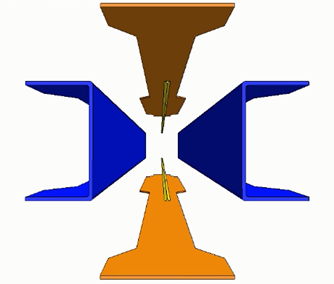
Las cuatro preformas de larguero de vigas en I se colocan en el molde RTM, se aplica vacío y la inyección de resina se completa en 5 minutos.
Paso 5
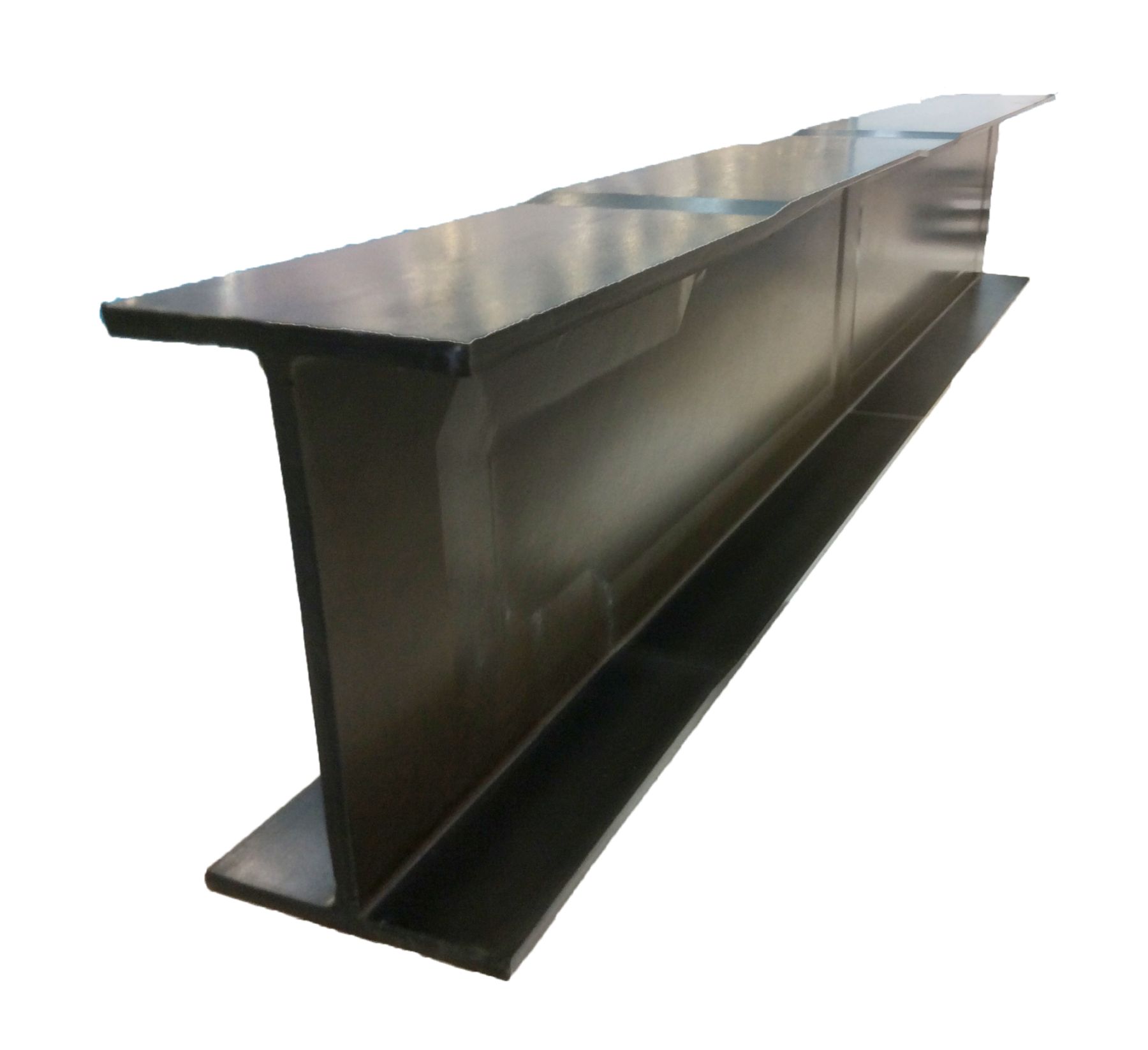
Después de un curado de 90 minutos, se desmoldea el larguerillo y se recorta el destello de resina durante un ciclo parcial completo de 4.5 horas.

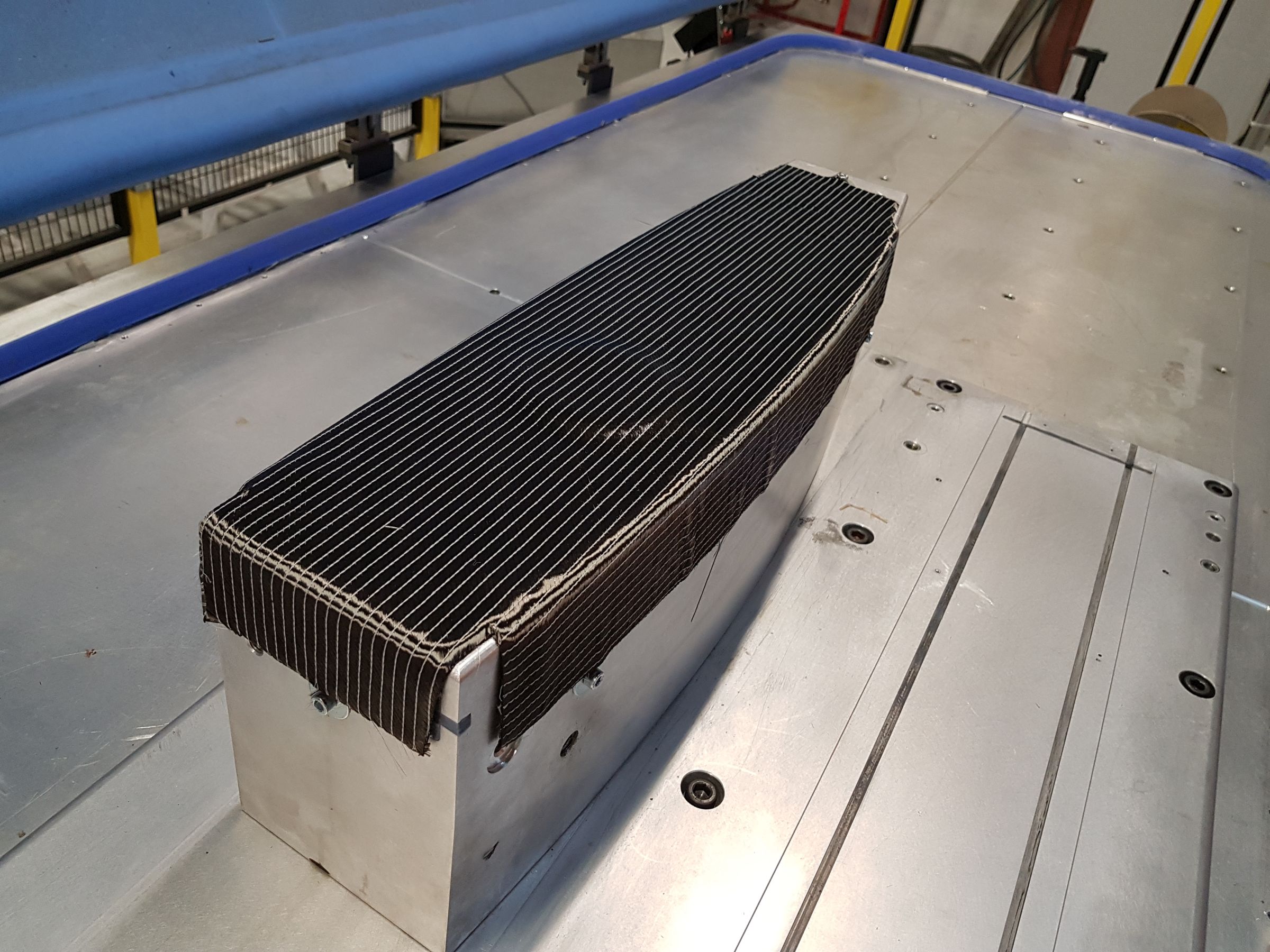
Un robot coloca las capas cortadas en la herramienta de preforma calentada. Cada 5-8 capas, se completa una reducción de volumen calentada para compactar la preforma.

Antes de reducir el volumen, se aplica una película de liberación azul.
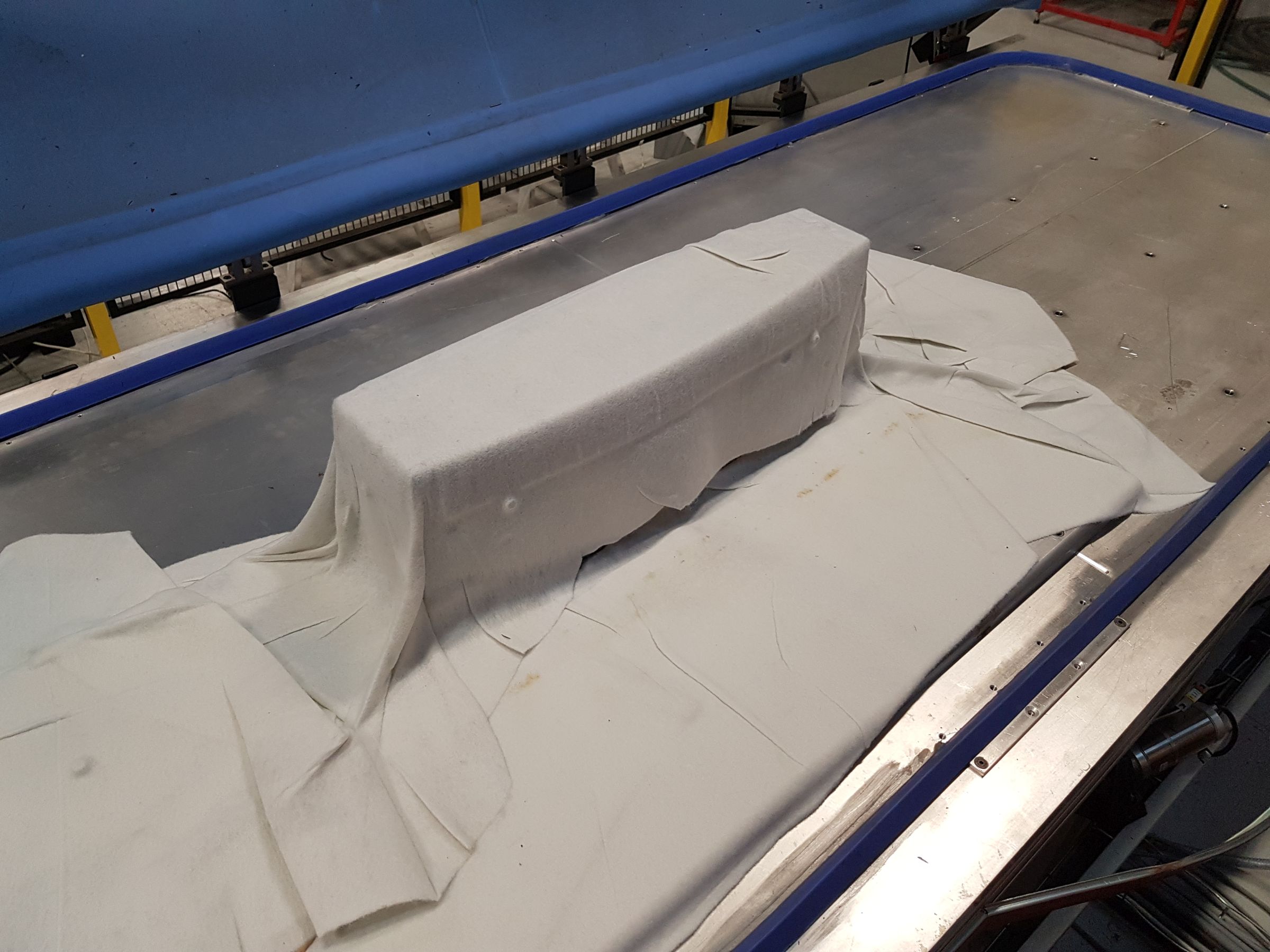
El respiradero se utiliza para extraer aire a través de la preforma.
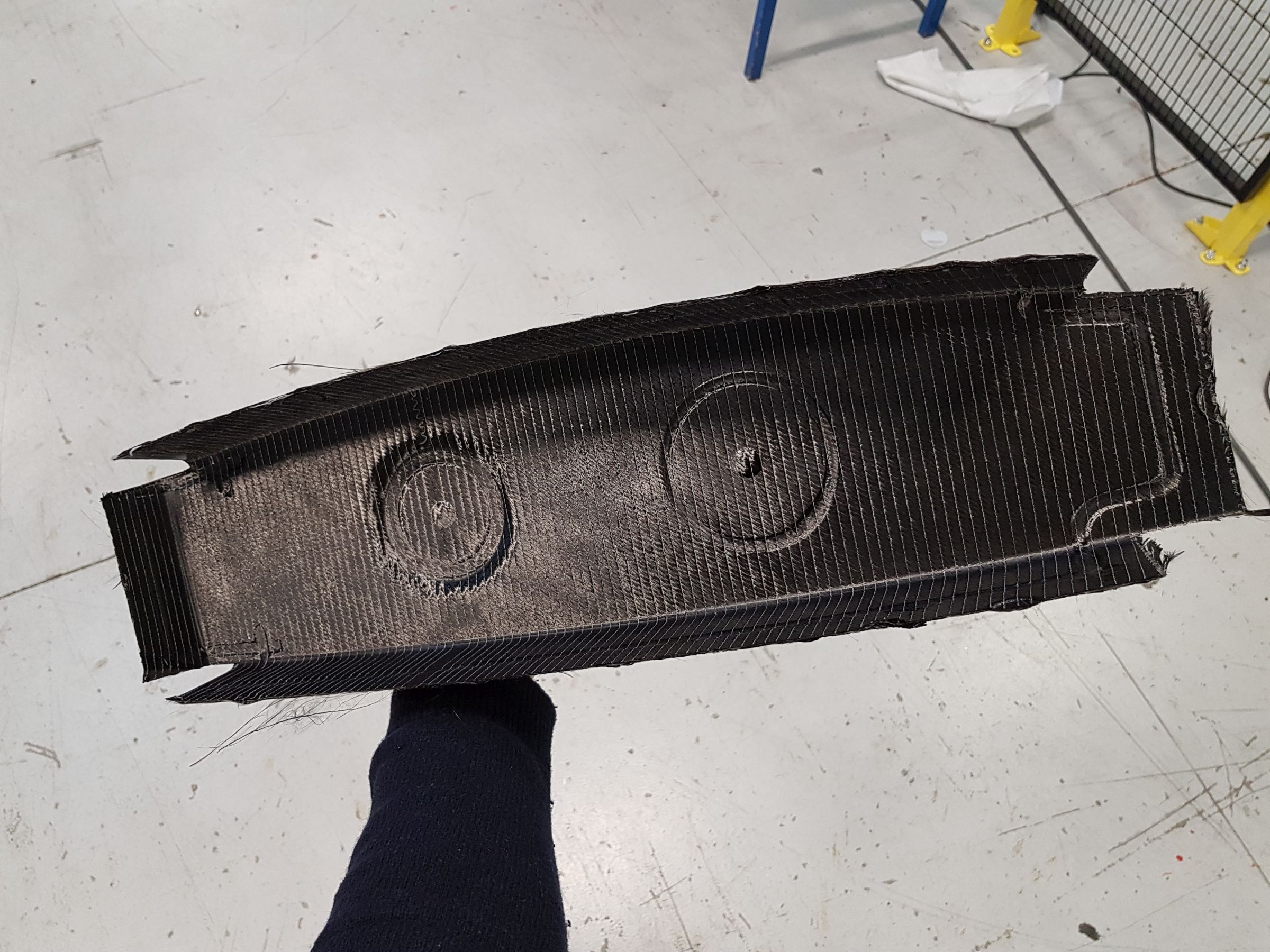
Después de la eliminación final, la preforma se enfría en la herramienta y los cortes se recortan (abajo).
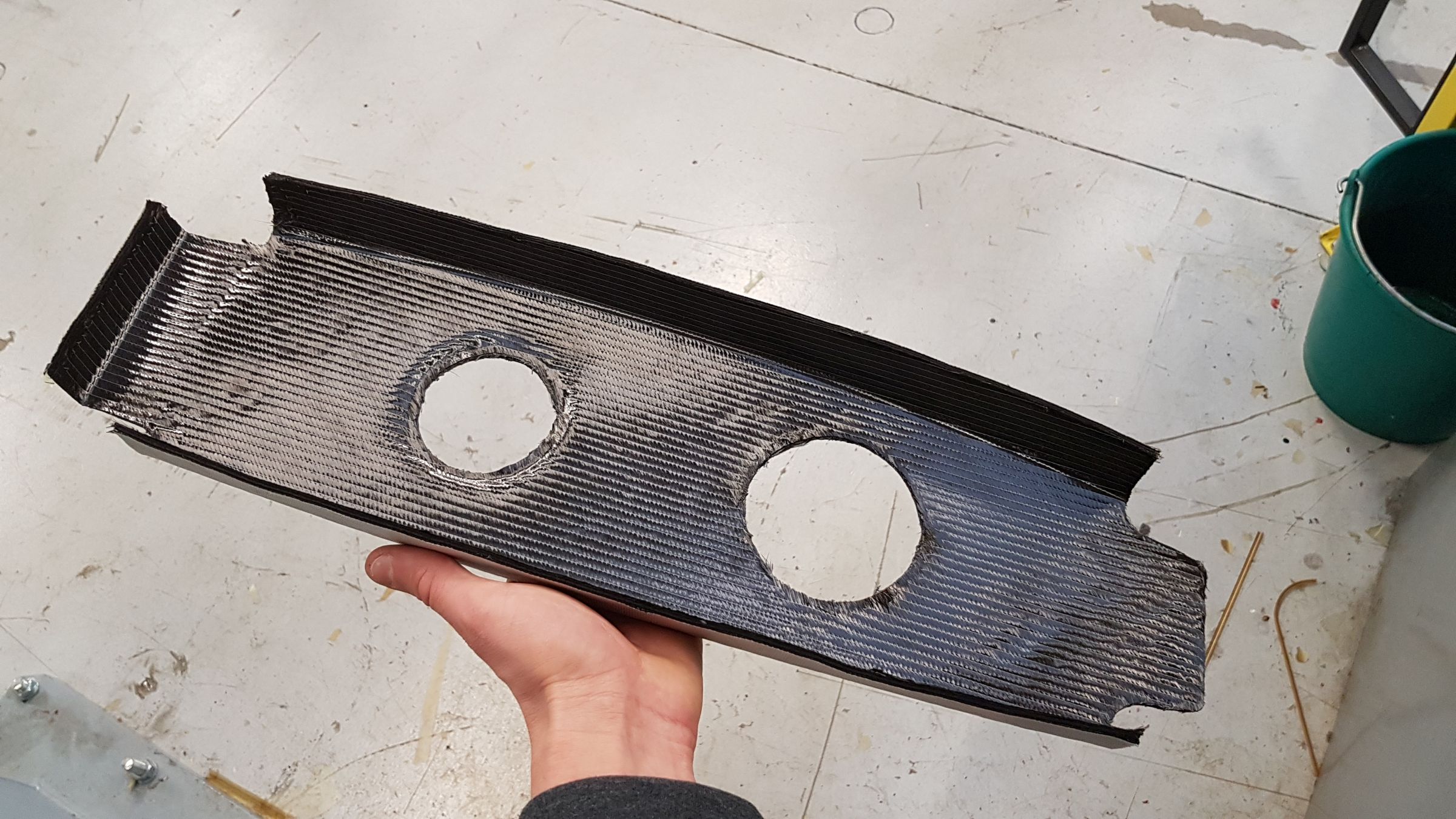
“Hemos automatizado el clásico apilado manual de capas mediante la selección y colocación robótica”, dice Chevallet. “El robot recoge las capas de un cortador automático y las transfiere a la herramienta de preforma calentada que se encuentra en una mesa de compactación [Pasos 1 y 6]”. Se aplica una capa despegable (película azul en el Paso 6), un respiradero (material blanco en el Paso 6) y una membrana de vacío reutilizable con bisagras (azul claro a la izquierda en los Pasos 2 y 6), seguido de vacío y calor para preformar y eliminar el aire del pila textil (formación de cortinas en caliente, HDF) mientras se funden los velos termoplásticos delgados para crear una preforma compacta.
“La cantidad de capas que se pueden compactar a la vez depende de los materiales y la forma de la pieza”, explica Chevallet. “Para piezas con curvatura baja, como una piel de alas, posiblemente podría compactar cada 50 capas. Sin embargo, la nervadura OPTICOMS tiene ángulos de 90 grados y el larguero de la viga en I de prueba tiene forma de T, por lo que debe tener cuidado de no formar arrugas en las capas durante el preformado ". Añade que estas formas complejas pueden requerir compactación cada 5-8 capas, pero aún pueden ser parte de un proceso industrializado de alto volumen:capas apiladas, HDF de 2 minutos compactación, reabrir y apilar nuevamente, seguido de ciclos repetidos de compactación con un enfriamiento final de la preforma en la herramienta antes de transferirla al molde RTM.
“Nuestra celda automatizada puede colocarse a una velocidad de 15 segundos por capa”, señala Chevallet. "La colocación de la nervadura OPTICOMS, con menos de 20 capas en total, se completó en 20 minutos". La bandeja para el larguero de la viga en I fue más larga:45 minutos debido a su forma compleja y apilamiento laminado, incluyendo variaciones de espesor de 1,2 a 6 milímetros. “Esto sigue siendo mucho más rápido que los procesos manuales y reduce el riesgo de error, aumenta la repetibilidad y la calidad al tiempo que reduce los costos”, agrega.
Paso 7
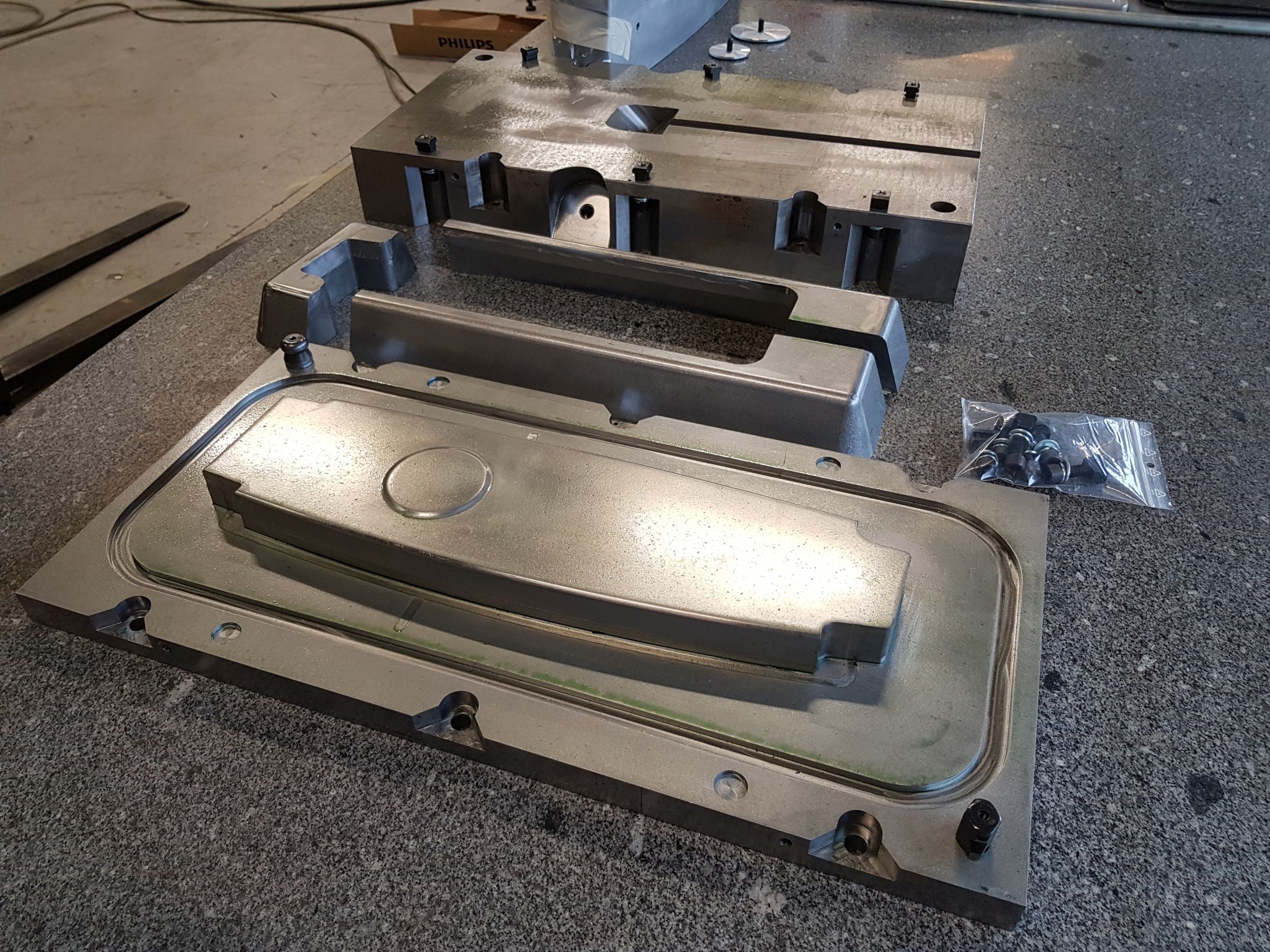
La herramienta RTM para la nervadura OPTICOMS consta de varias partes.
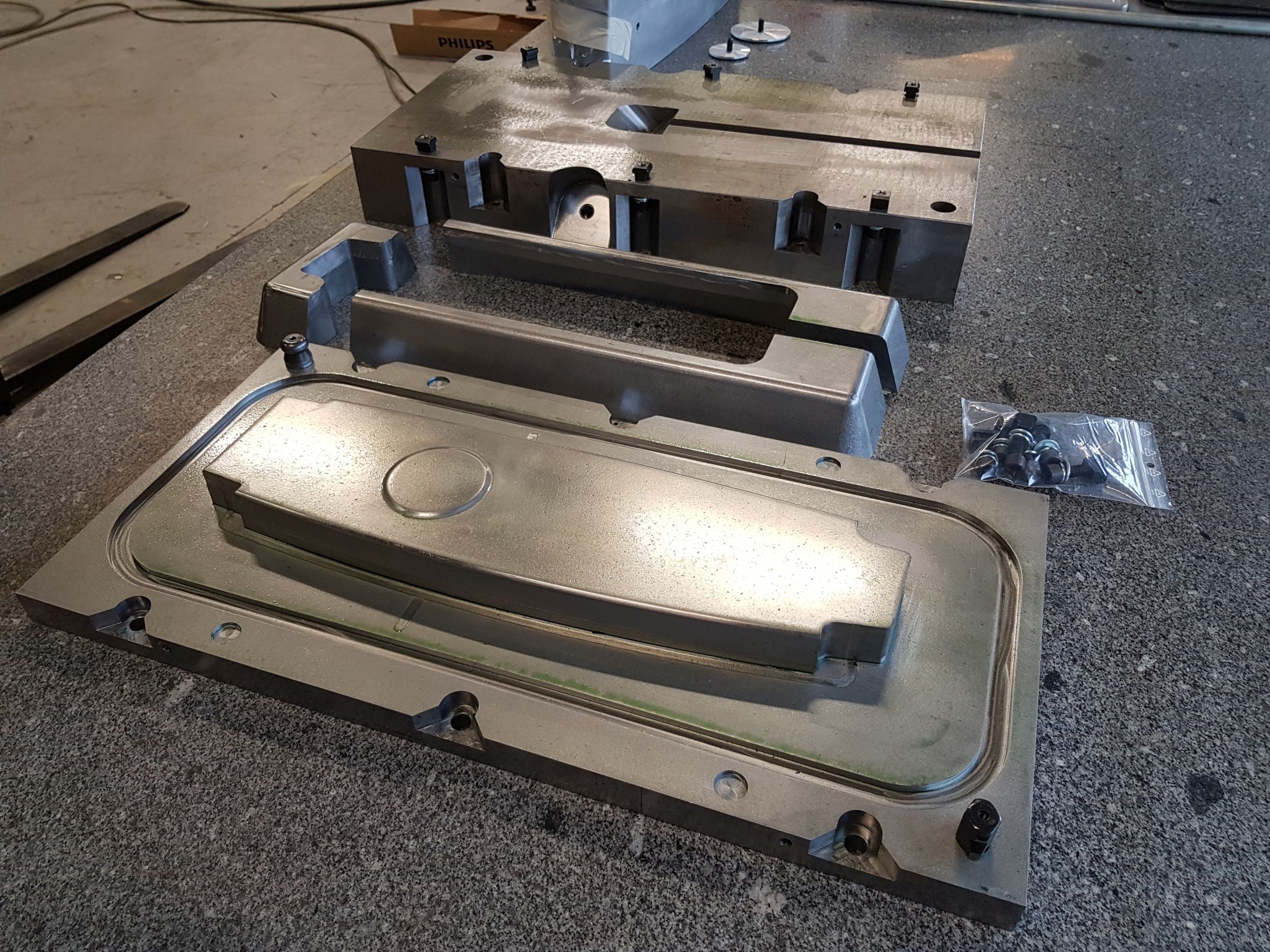
Paso 8
La preforma de nervadura se coloca en la herramienta RTM.
Paso 9
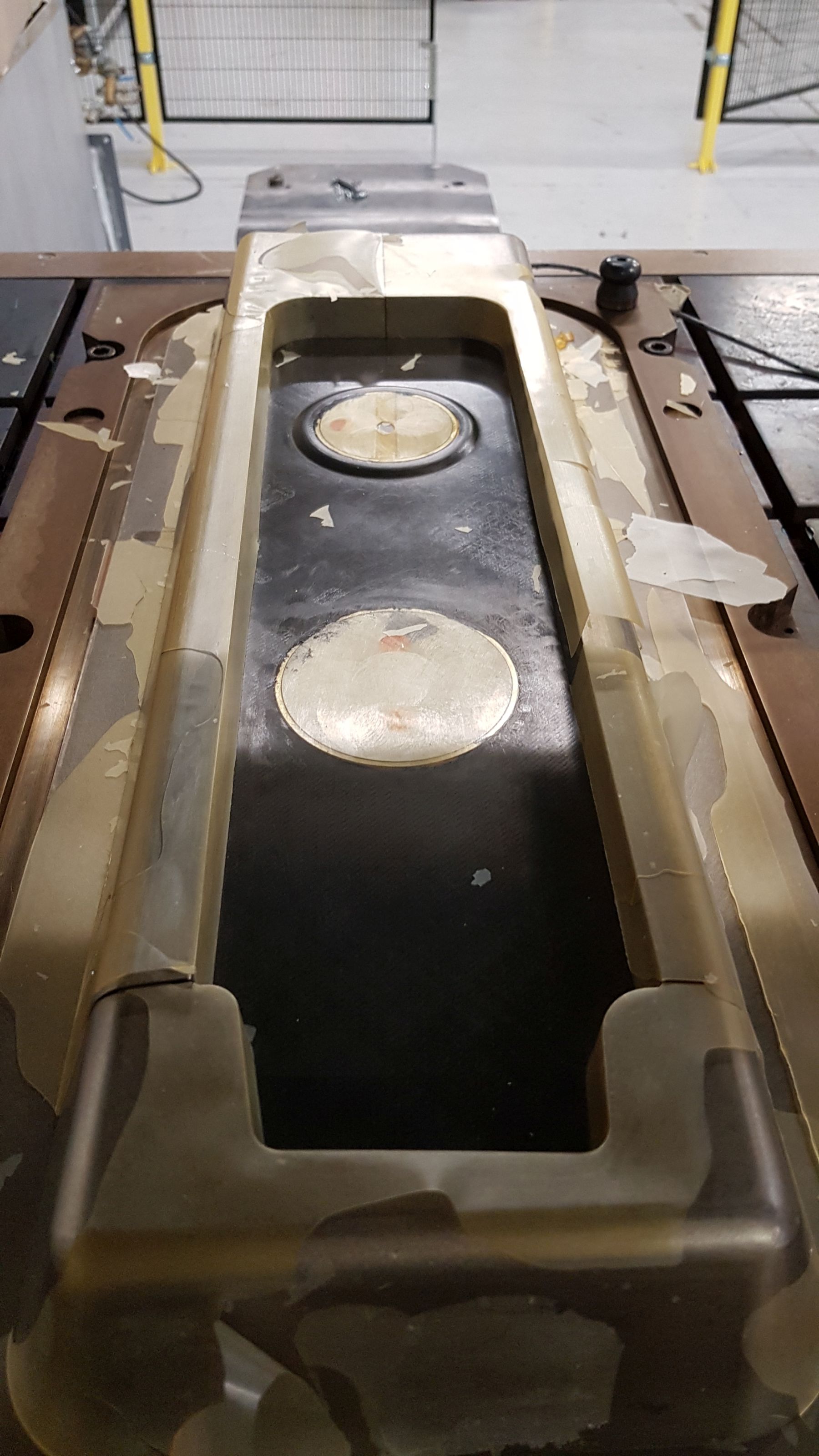
Se aplica vacío, se inyecta resina y se infiltra en la preforma, seguido de un curado de 90 minutos. Aquí, la prensa se ha abierto para revelar la parte curada.
Paso 10
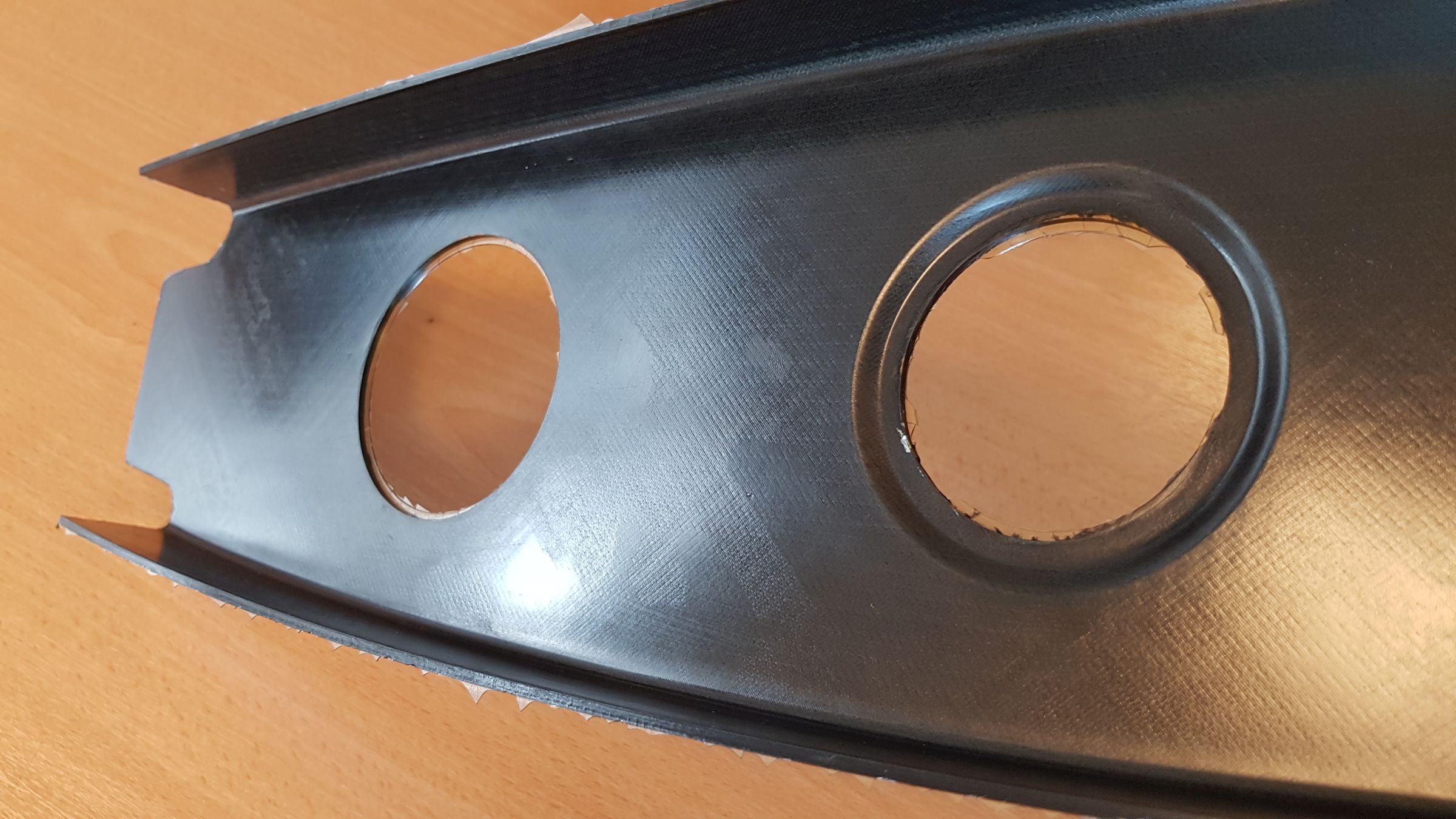
Una vez completado el desmoldeo, se eliminará el destello de resina durante un ciclo parcial completo de 4 horas.
Control inteligente
Otra característica clave de la celda de preformado automatizada de Techni-Modul Engineering es su sistema de control integrado. Conocido como SMART CONTROL, su columna vertebral es un sistema de cámara y un software de usos múltiples que compara las imágenes tomadas durante el procesamiento con la base de datos CAD de la pieza, lo que permite el reconocimiento de la forma de las preformas, el control de la orientación de la fibra, el posicionamiento de las capas y la detección de defectos y restos de objetos extraños (FOD ). La retroalimentación de SMART CONTROL le indica al robot cómo recoger y colocar las capas en la secuencia y el tiempo correctos, pero también alerta al operador de la celda cuando detecta errores. "El sistema se puede configurar para que el operador retire manualmente la capa y reinicie el sistema para reemplazarla", explica Chevallet, "o podemos trabajar con el cliente para crear una solución automatizada para eliminar las capas defectuosas y corregir errores".
Las mismas imágenes ópticas que se utilizan para detectar los bordes y contornos de las capas también se utilizan para controlar la orientación de la fibra. Chevallet admite que si la pieza es muy grande (por ejemplo, 2 metros de largo en comparación con 200 por 200 milímetros), “es posible que necesite una cámara que tome fotografías [desde una] posición vertical más alta para detectar los bordes de las capas y luego acercarse a la pieza para comprobar la orientación de la fibra. Calibra esta secuencia para cada tipo de pieza. Para la detección de arrugas y FOD, existe una base de datos de diferentes defectos y puedes sumar a esta, por lo que el algoritmo de aprendizaje profundo mejora con el tiempo. La idea es tener un sistema que sea adaptable ”.
Duración del ciclo y producción futura
Las preformas para la nervadura OPTICOMS se hicieron usando HiMax, y el larguero de viga en I usó HiTape. El sistema de resina para ambos fue el epoxi líquido de un componente (1K) HexFlow RTM6 de Hexcel, que tiene un ciclo de curado de 90 a 120 minutos a 180 ° C. Este curado es el paso más largo en los tiempos de ciclo de la pieza tanto para el nervio OPTICOMS como para el larguero de la viga en I de prueba, como se puede ver en la Tabla 1.
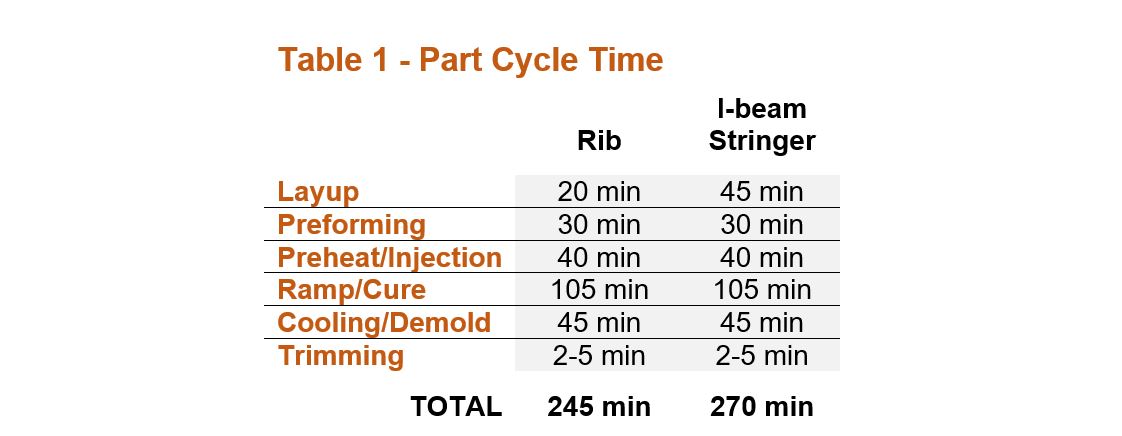
Fuente | Ingeniería Techni-Modul
Hasta la fecha, este ha sido el único epoxi calificado para RTM de estructuras aeroespaciales. Sin embargo, crece el interés en la calificación de sistemas de dos componentes que se mezclan en el cabezal de inyección, lo que ofrece una mayor flexibilidad del ciclo de curado y evita la necesidad de transporte y almacenamiento refrigerados necesarios para evitar la reacción prematura del RTM6 premezclado.
Airbus Helicopters (Donauworth, Alemania) trabajó con Alpex Technologies (Mils, Austria) en el proyecto SPARTA para demostrar un proceso HP-RTM utilizando una versión de dos componentes de HexFlow RTM6 para lograr curados de 30 minutos a 180 ° C para una puerta A350. marco, que es una estructura primaria de forma compleja que mide 2 metros de alto, 200-250 milímetros de ancho y 8-10 milímetros de grosor (consulte “HP-RTM para la producción en serie de aeroestructuras de CFRP rentables”). Airbus también ha demostrado una nervadura CFRP de 1,5 metros por 0,5 metros fabricada con HP-RTM por su filial de Composite Technology Center (CTC, Stade, Alemania), logrando ciclos de moldeo de 20 minutos para piezas con 60% de volumen de fibra y menos de 2 % vacíos. El año pasado, CTC trabajó con varios proveedores de nivel para realizar la transición de las piezas preimpregnadas de laminado manual a HP-RTM para el A320. Sin embargo, los sistemas de resina 2K deben estar calificados para la producción de aeroestructuras, y a CTC le preocupa la capacidad de garantizar continuamente la calidad de la mezcla de los sistemas de resina 2K in situ. Alpex está utilizando sensores en el molde de Netzsch (Selb, Alemania) y Kistler (Winterthur, Suiza) para ayudar a lograr esto, y se están desarrollando otras soluciones (consulte “Epoxi de 2 partes para una mayor producción de aeroestructuras compuestas”).
Incluso sin sistemas 2K, es posible que se produzcan mayores volúmenes de producción. Los marcos de las puertas en el proyecto SPARTA se quitaron después del curado inicial de 30 minutos a 180 ° C y se curaron posteriormente fuera de la prensa, al vacío para eliminar el estrés térmico y garantizar las propiedades mecánicas. Según el jefe de I + D de Alpex, Bernhard Rittenschober, esto requiere juegos adicionales de herramientas, pero solo una unidad de inyección y prensa. Explica que el costo adicional de la herramienta se compensa con un proceso y un costo de prensa más bajos y se puede recuperar rápidamente, incluso con un volumen bajo de 500-1,000 piezas / año.
“El principal logro de estos demostradores es la capacidad de hacer aeroestructuras primarias con una inyección de resina corta en comparación con los procesos RTM aeroespaciales convencionales, donde ha sido un proceso largo y difícil infiltrar resina en piezas tan grandes con refuerzos de fibra de carbono UD”, dice Pagnac. . “Estamos apenas al comienzo de lo que podemos lograr con este tipo de preformado inteligente automatizado y procesamiento C-RTM”, agrega Chevallet. "Tiene el potencial de lograr la producción más rentable y sostenible de estructuras de revestimiento integradas con refuerzos que se prevé para las futuras aeronaves".
Resina
- ¿Materiales de impresión 3D para viajes espaciales?
- Tres formas en las que las empresas están utilizando materiales compuestos en la industria aeroespacial del futuro
- Los 3 materiales más resistentes para sujetadores de plástico
- Henkel ofrece una plataforma de materiales para la fabricación aditiva
- Materiales:Tecnología de producción de nido de abeja ligera en la K 2019
- Materiales:Poliamida ignífuga de alta temperatura para impresión 3D
- Preparándose para un futuro autónomo
- Trelleborg anuncia nuevo distribuidor para materiales de herramientas
- Arkema Inc. construye una planta de producción de PEKK de EE. UU.
- 10 materiales más fuertes para impresión 3D
- Materiales para componentes de Invar 36