Construyendo el Museo del Futuro
El Museo del Futuro que se está construyendo actualmente en Dubai, Emiratos Árabes Unidos (EAU), es una de las estructuras más complejas jamás construidas. El edificio de 78 metros de altura alberga siete pisos dentro de un caparazón en forma de toro que se asienta sobre un podio de tres pisos. La fachada exterior del toro comprende 1.024 paneles compuestos ignífugos (FR). Revestido con acero inoxidable, cada panel tiene una forma 3D única e integra caligrafía árabe moldeada. El guión fluido forma poemas que describen la visión del futuro de Dubai de Su Alteza el Jeque Mohammed bin Rashid Al Maktoum, vicepresidente y primer ministro de los Emiratos Árabes Unidos y gobernante del Emirato de Dubai. También sirven como ventanas del edificio, proyectando luz del día a través del interior sin columnas y creando un efecto dramático en la noche a través de 14 kilómetros de iluminación LED integrada.
Concebido por Sheikh Mohammed como una incubadora de innovación e invención, el Museo del Futuro está considerado como uno de los edificios más avanzados del mundo, un lugar donde las personas pueden experimentar e investigar nuevas tecnologías. También es un símbolo de la arquitectura que traspasa los límites a través del diseño digital y el uso de materiales más eficientes. El diseño paramétrico se utilizó para desarrollar la diagrid de acero, una estructura de 2.400 miembros de acero que se cruzan diagonalmente, a la que se unen losas de piso de hormigón compuesto y 17.000 metros cuadrados de revestimiento compuesto, este último utilizando 1 millón de metros cuadrados de vidrio multiaxial y reforzado con fibra de carbono. preimpregnado epoxi.
La firma de Dubai Affan Innovative Structures proporcionó el diseño compuesto para los paneles, así como la fabricación y el soporte para la instalación. "Esta es la primera vez que se lleva a cabo un proyecto de este tipo", dice el director ejecutivo de la empresa, el Dr. Amer Affan. “Y también es la primera vez que se utilizan paneles compuestos para integrar múltiples funciones de construcción a través de formas tan complejas”.
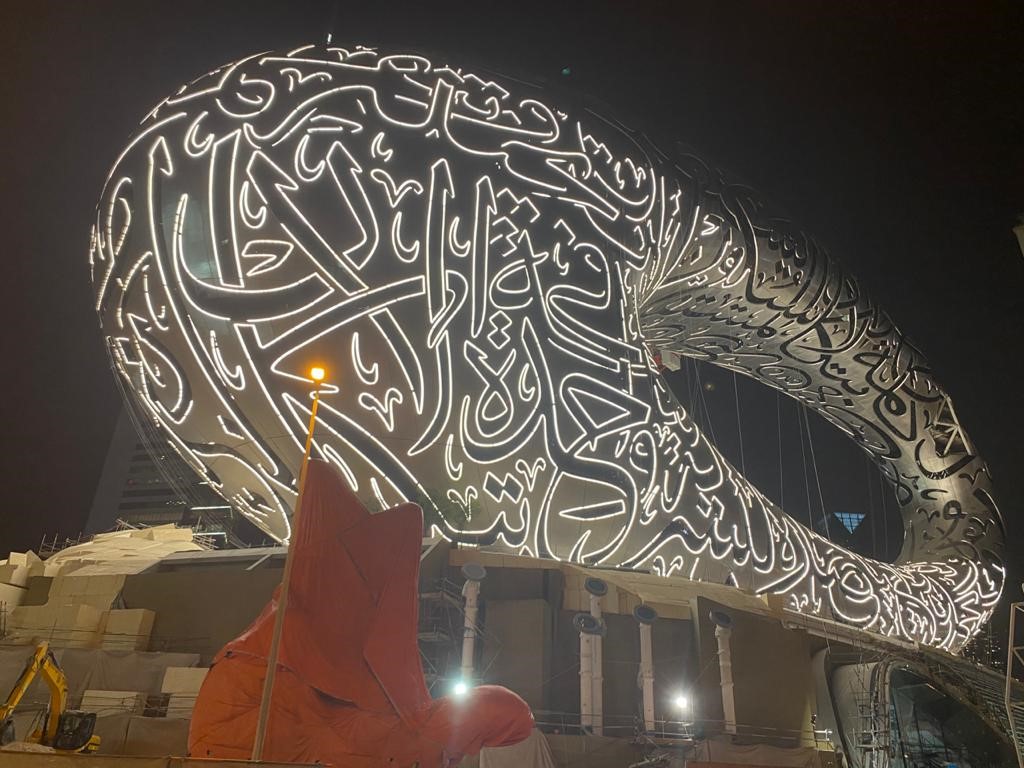
El arquitecto principal, Shaun Killa, explica que estos exteriores complejos son normalmente pantallas de lluvia, con un edificio detrás que contiene el sistema de impermeabilización. "Esto simplifica las cosas porque es un poco más indulgente al crear estas formas tan tridimensionales", señala. “En este edificio, sin embargo, la envolvente está haciendo la impermeabilización, la estanqueidad, la estructura y la iluminación”. Affan admite que para un proyecto tan grande, su empresa es de tamaño pequeño, "pero hemos utilizado nuestra experiencia técnica para lograr algo único y hemos demostrado cómo se construirán los edificios en el futuro".
Capacidad en diseños digitales complejos
El equipo de ingeniería del Museo del Futuro se puso en contacto inicialmente con Affan Innovative Structures. “No había muchas empresas que pudieran hacer el trabajo requerido para el revestimiento exterior”, señala Affan. "El único otro competidor propuso un muro cortina normal con paneles de aluminio o acero inoxidable en el exterior". Los muros cortina, que se utilizan típicamente además de un marco de acero estructural, son delgados y están hechos de marcos de aluminio que soportan paneles exteriores de vidrio, metal y / o piedra delgados (consulte “La envolvente del edificio:fachadas unificadas de FRP”). Esto fue rechazado por el equipo de ingeniería por ser demasiado difícil e incapaz de proporcionar la misma apariencia que era posible utilizando una fachada de panel compuesto multifuncional integrado. Así, este último, propuesto por Affan Innovative Structures, fue seleccionado para el proyecto. “También contamos con una tecnología única que nos permite hacer paneles grandes”, agrega Affan, “de hasta 3 metros de ancho por 9 metros de alto, curvados en ambas direcciones, lo que significa menos juntas”.
Affan Innovative Structures fue especialmente adecuado para este proyecto. Formada en 2004 por el Dr. Affan, la empresa ofrece soluciones completas llave en mano, desde el diseño conceptual hasta la instalación y el mantenimiento de edificios, que gravitan hacia desafíos muy técnicos. El currículum de la compañía incluye la compleja pantalla / revestimiento de aluminio geométrico para el King Abdullah Sports City Stadium (Jeddah, Arabia Saudita), la marquesina de entrada compuesta y 64 tragaluces de acero y vidrio con diseños intrincados para el Yas Mall (Abu Dhabi, Emiratos Árabes Unidos) , el techo compuesto exterior para el Hospital Sidra (Doha, Qatar) y muchos otros proyectos desafiantes. Esta capacidad en conjuntos complejos de acero, vidrio y compuestos sería exactamente lo que se necesitaba para el exterior compuesto multifuncional del Museo del Futuro.
“Dentro de cada panel compuesto, hay un sistema de [paneles] de vidrio plano dentro de la escritura árabe”, explica Affan. “El vidrio está casi empotrado dentro de los paneles, hasta 200 milímetros de profundidad”. Este hueco cambia no solo desde la parte superior del edificio, con menos hueco para evitar que el agua atrape, hasta la parte inferior, donde los paneles verticales y socavados pueden empotrarse profundamente sin atrapar agua, sino también dentro de cada panel, inclinándose y disminuyendo para producir un efecto gradual y natural. borde para el guión. “La ubicación y los bordes del hueco también variaron según la ubicación del vidrio dentro del panel porque el vidrio era plano pero los paneles curvados”, señala Affan. “Esto solo fue posible con el diseño digital y el mecanizado CNC”. Esta precisión también sería necesaria para garantizar que el guión, que variaba de un panel a otro, se alineara con precisión a medida que se instalaron los paneles, de modo que las letras y las palabras fluyeran correctamente por el exterior del edificio.
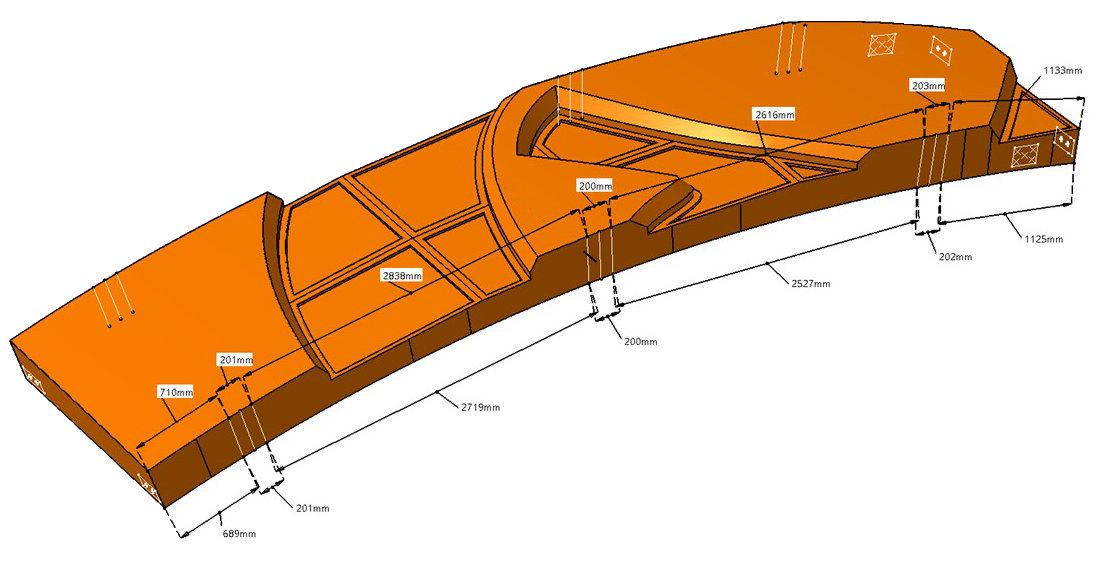
Para Affan, la única solución era moldear la escritura árabe y los huecos en cada panel compuesto. “Los refuerzos se colocarían en moldes mecanizados con precisión CNC”, explica. Afortunadamente, el software CATIA (Dassault Systèmes, Vélizy-Villacoublay, Francia) que Affan Innovative Solutions utiliza para impulsar sus máquinas CNC es también el programa CAD 3D utilizado por la industria aeroespacial para diseñar aeronaves complejas y estructuras compuestas. Además, el equipo de 28 ingenieros de Affan también domina el software Tekla BIM, Rhino 3D (Robert McNeel &Assoc., Seattle, Washington, EE. UU.) Y AutoCAD de Autodesk. “Hicimos todos los dibujos en CATIA, así como el diseño del laminado, lo que nos dio la capacidad de realizar un mecanizado tan complejo”, dice Affan.
Sin embargo, el diseño no era trivial y tenía que cumplir con una variedad de cargas estructurales y de viento. Por ejemplo, el interior del toro creó un efecto de túnel de viento, explica Affan. Estos paneles deben soportar hasta 450 kg / m 2 (92 libras / pie 2 ) de carga de viento. (Tenga en cuenta que el Código de construcción internacional enumera cargas de viento de 71 lb / pie 2 para áreas de alto riesgo de huracanes en West Palm Beach, Florida, EE. UU.). Los paneles compuestos para el Museo del Futuro también están diseñados para minimizar el peso. “Los paneles utilizan de 9 a 13 capas, que varían según la ubicación y la carga”, dice Affan. Agrega que el Composite Technology Center (Stade, Alemania), una subsidiaria de Airbus y un socio desde hace mucho tiempo a través de la organización comercial CFK Valley ev (Stade, Alemania), “proporcionó una verificación de terceros sobre nuestro diseño laminado, deflexión y rigidez cálculos ”.
Una complejidad e innovación adicionales es que los paneles también integraron su propio sistema de fijación. “En los bordes, 24 capas forman la geometría de unión en forma de casete para conectarse al edificio”, explica Affan. Un sistema de casete es un método para unir revestimientos externos, desarrollado originalmente para instalaciones de tipo mampara de lluvia. Aunque los tipos y geometrías varían, los casetes suelen permitir una superficie exterior plana a prueba de lluvia que se asegura detrás de la estructura de carga del edificio. Para los paneles de fachada del Museo del Futuro, no se requirieron piezas separadas para formar los bordes del casete, sino que se mecanizaron en cada molde y, por lo tanto, se integraron en cada panel compuesto.
Fabricación de materiales, moldes y paneles
Aunque los 10.000 metros cuadrados de espacio de fabricación de compuestos de Affan Innovative Structures tienen 16 máquinas de infusión de resina y ocho mesas de infusión de resina a base de acero con tapa de vidrio que miden 3 metros por 20 metros, optó por utilizar preimpregnado. ¿Por qué? "Lograr el rendimiento FR necesario requiere muchos aditivos, por lo que la resina se vuelve espesa y no fluye en la infusión", explica Affan. En este caso, el aditivo fue trihidrato de aluminio (ATH, ver “Resistencia al fuego sin peso”). Continúa:“Por lo tanto, trabajamos con Notus Composites [Ras Al Khaimah, Emiratos Árabes Unidos] para desarrollar un preimpregnado epoxi FR. Utilizamos principalmente fibra de vidrio, pero también fibra de carbono en ciertas secciones donde había problemas de deflexión ”. Aprobado por la Defensa Civil de Dubái, el preimpregnado Notus Composites EPFR-609, en combinación con la película de superficie NE11-FR, ha superado los requisitos contra incendios de NFPA 285, EN13051-1 y ASTM E1098 y E84 Clase A (consulte “Los preimpregnados ignífugos permiten ... . ”Y“ Cribado mejor y más económico de materiales de construcción de FRP ”).
Debido a que las superficies metálicas externas en Dubái pueden alcanzar temperaturas de 80 ° C (176 ° F) en verano, explica Affan, “curamos el preimpregnado a 120 ° C para asegurar suficiente T g (temperatura de transición vítrea) para resistir la deflexión de la cabeza. Por lo tanto, los moldes se mecanizaron con una espuma de poliuretano que podría soportar esa alta temperatura, que es más cara. Probamos tres o cuatro espumas diferentes, pero solo una podía soportar la temperatura más la presión de vacío y, sin embargo, era lo suficientemente suave como para mecanizar con CNC fácil y rápidamente.
El mecanizado CNC de cada molde tomó de 12 a 72 horas y cada uno de los 1.024 paneles compuestos requirió su propio molde . Las cuatro máquinas CNC de 5 ejes CMS (Zogno, Italia) de Affan Innovative Structures, la más grande con 33 metros de largo por 13 metros de alto por 2,5 metros de alto, eran necesarias para cumplir con la exigente tasa de producción del museo. "Si una [máquina] estaba inactiva por mantenimiento, teníamos las otras funcionando en paralelo", explica Affan.
Las capas preimpregnadas se cortaron y equiparon con un (Bulmer , Mehrstetten, Alemania) cortadora automática. “No usamos núcleos en los paneles porque, a diferencia de hoy, no había núcleos de espuma en ese momento que pudieran pasar los requisitos de FR”, dice Affan. Incluso con tal automatización, la fuerza laboral de la empresa de 250 empleados, un total que había alcanzado en 2015, también era necesaria para cumplir con la producción, con un promedio de cuatro paneles por día. Equipos de seis trabajadores, cada uno con un supervisor y un conjunto equilibrado de habilidades para ser eficientes, colocaron los paneles. "Normalmente, tendríamos dos o tres equipos trabajando en un proyecto", señala Affan, "pero para cumplir con este programa de producción teníamos 20 equipos trabajando en un momento dado".
Pasos de fabricación
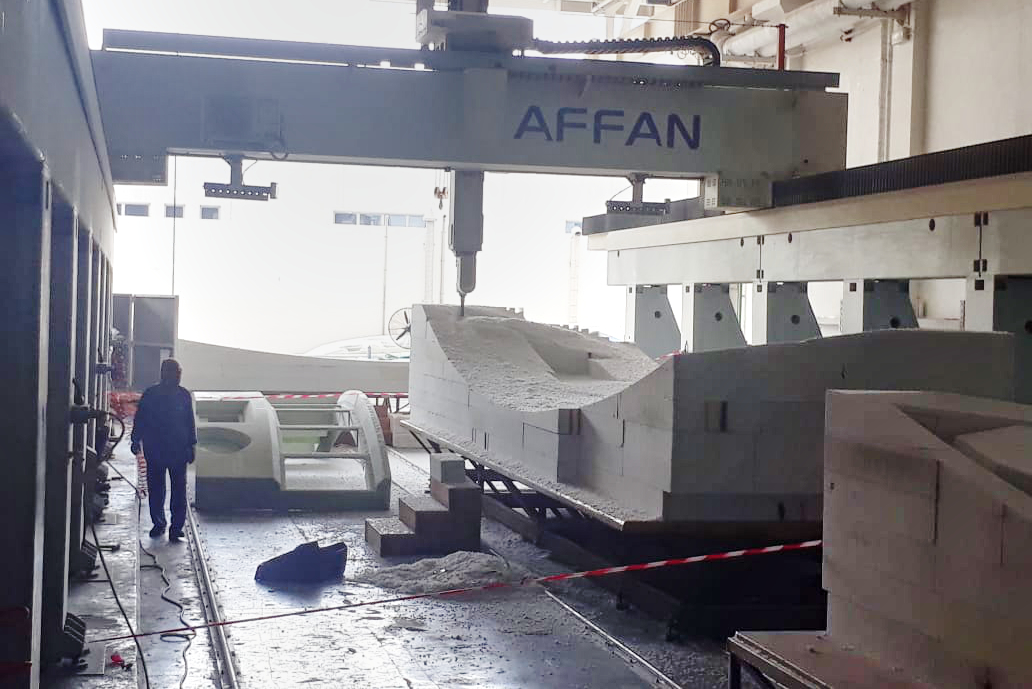
Paso 1 La espuma de poliuretano se muele en moldes de precisión. Fuente de todas las imágenes de los pasos de fabricación | Soluciones innovadoras de Affan
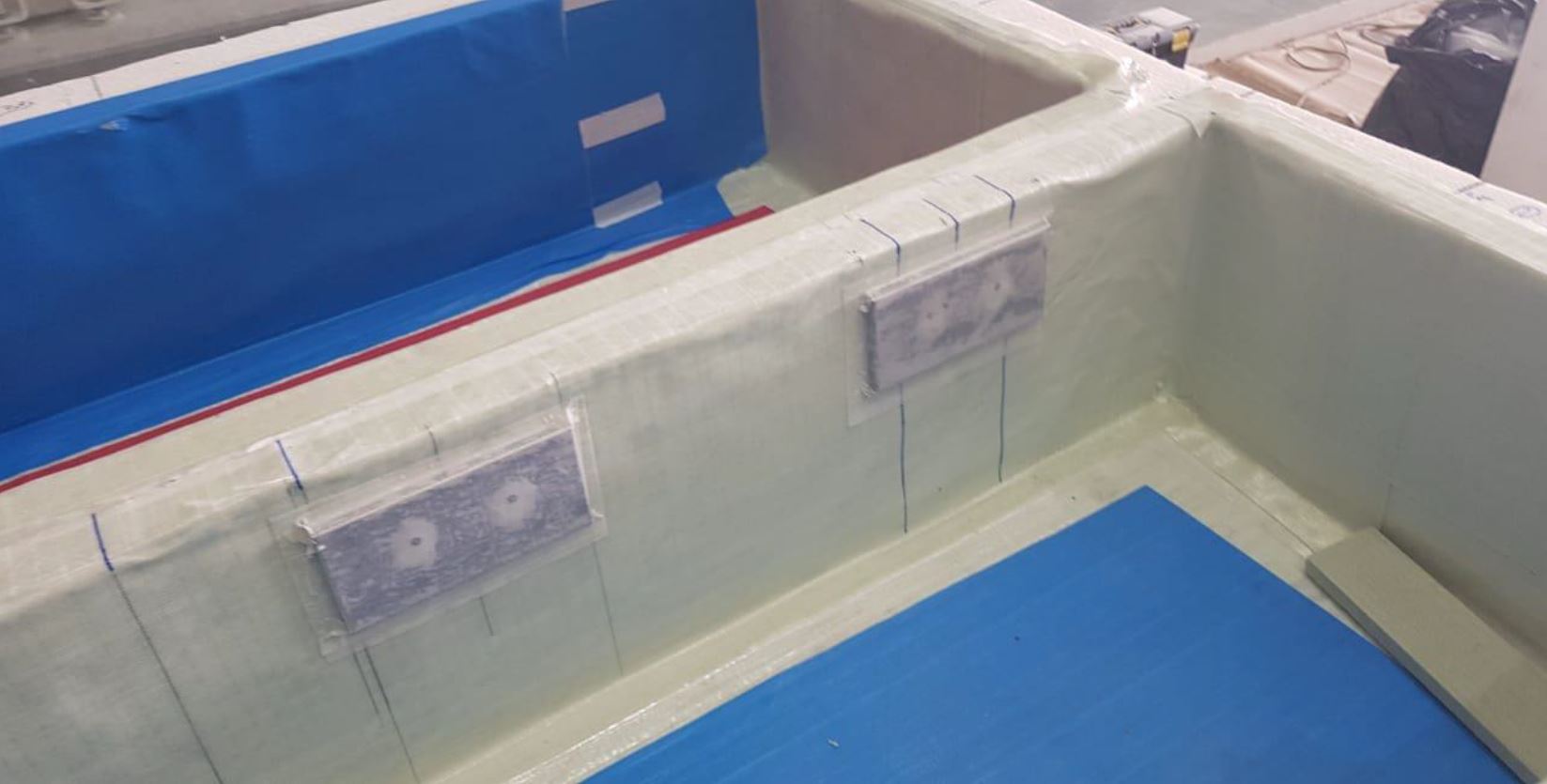
Paso 2 El preimpregnado epoxi / fibra de vidrio se coloca a mano en los moldes.
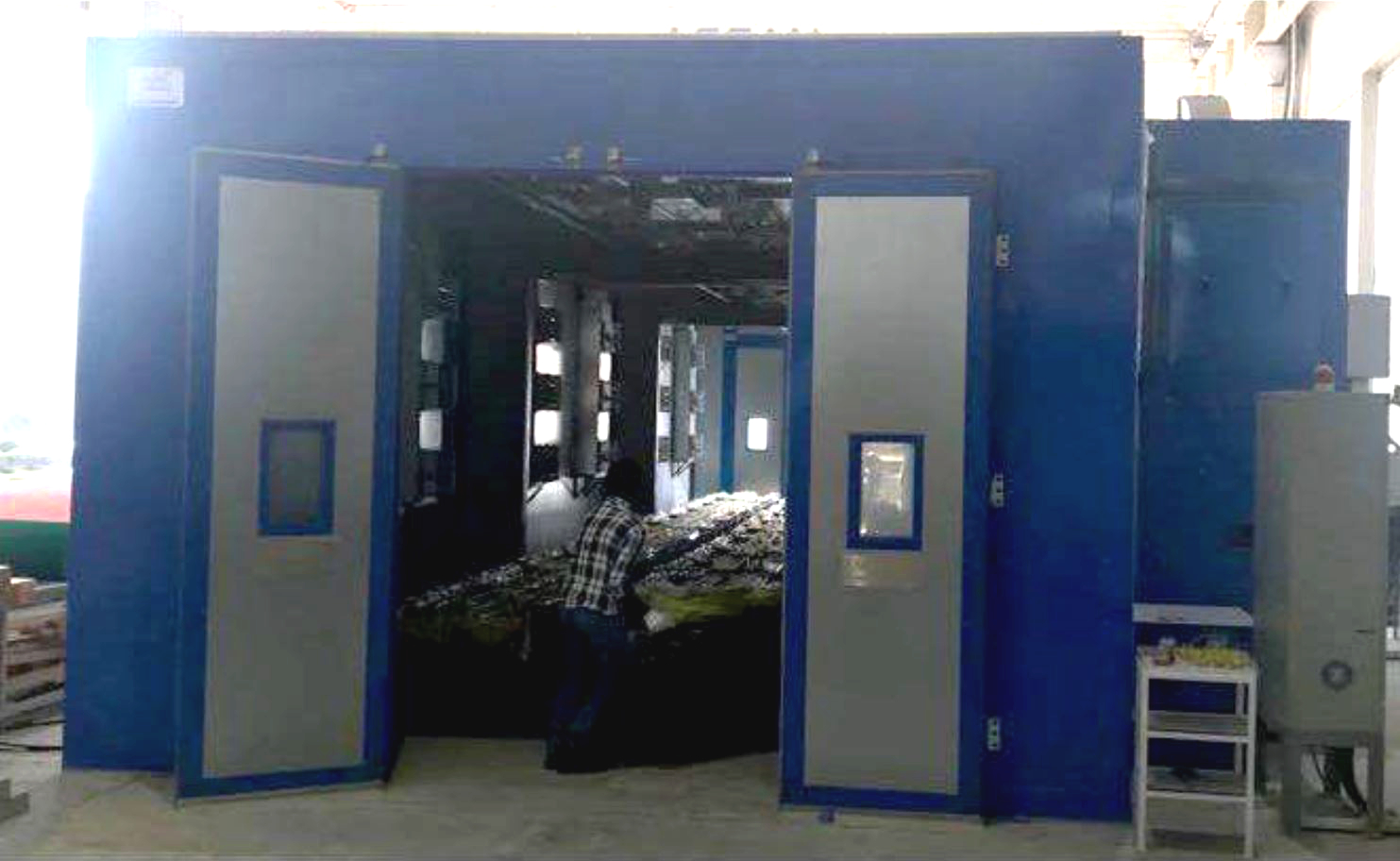
Paso 3 Las capas de preimpregnado se envasan al vacío y se curan en un horno durante 6 horas a 120 ° C.
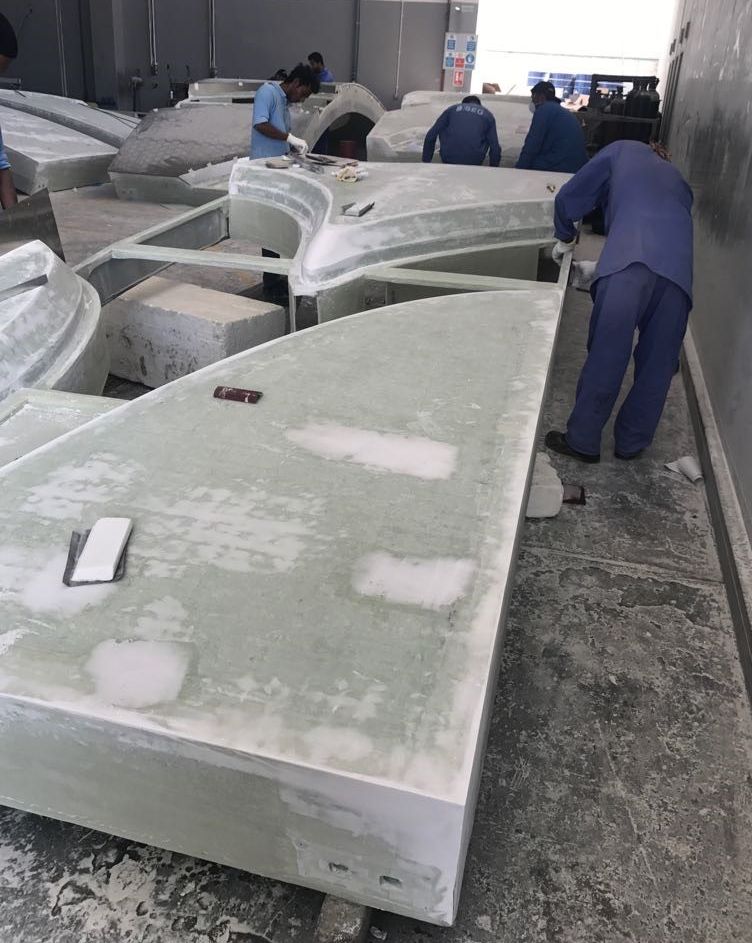
Paso 4 Los paneles demolidos se preparan para la unión adhesiva del acabado de acero inoxidable.
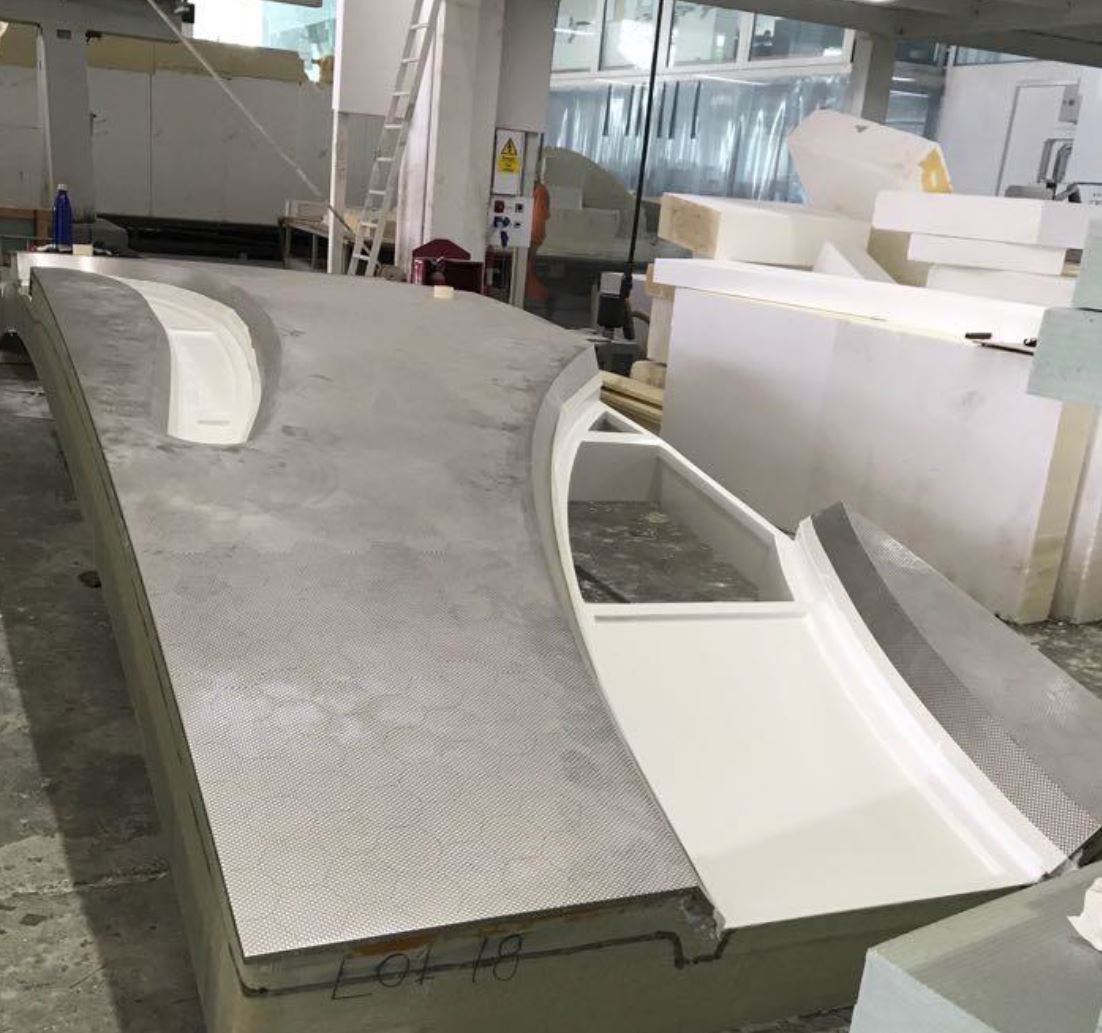
Paso 5 Los hexágonos de acero inoxidable se unen y se sujetan mecánicamente a los paneles de FRP.
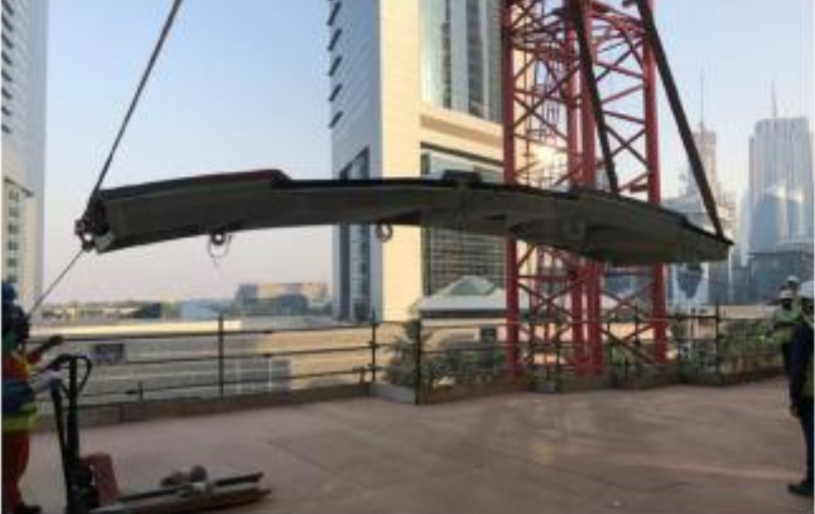
Paso 6 Los paneles terminados se levantan para su instalación.
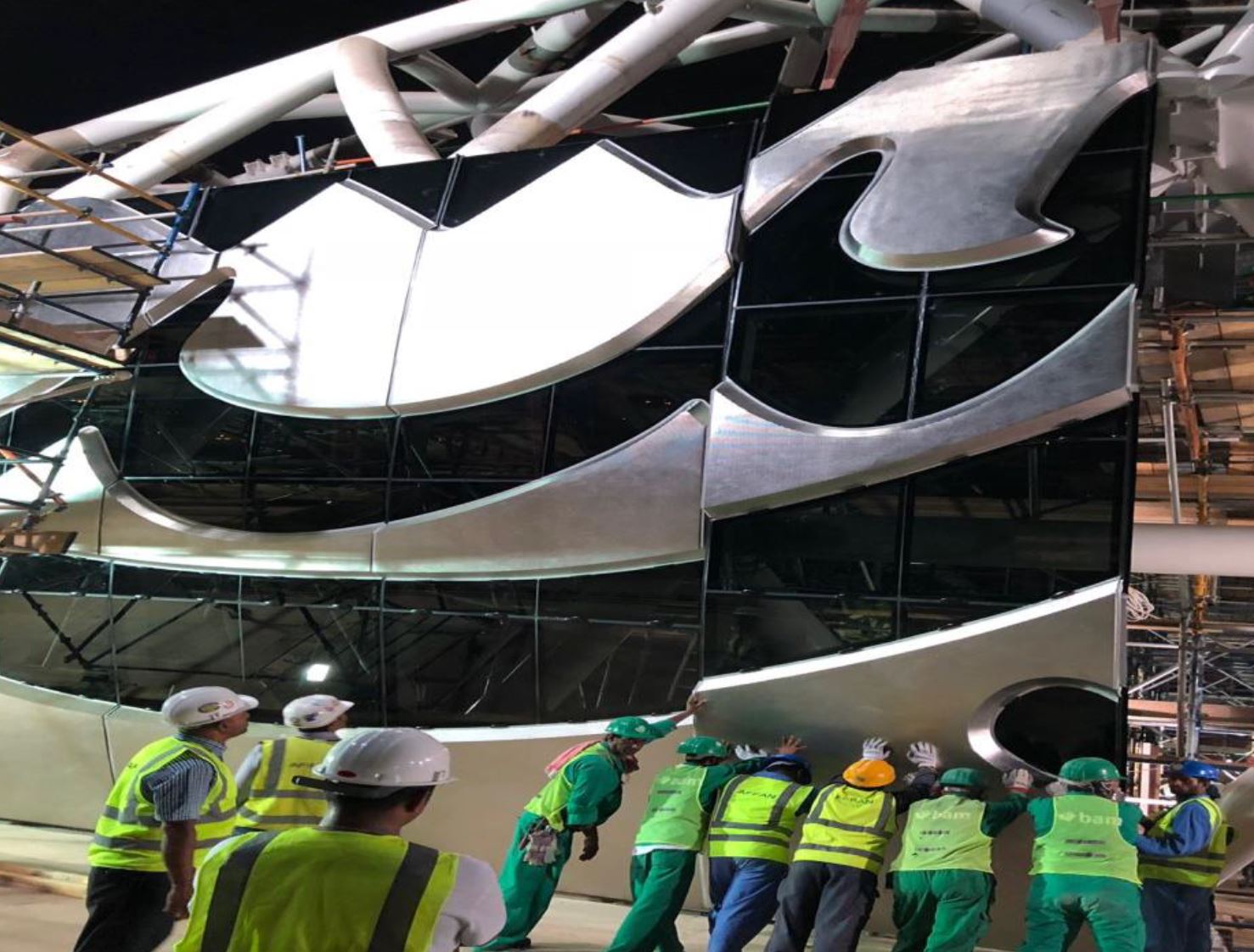
Paso 7 Cada panel se ajusta mediante una “junta universal” 3D única.
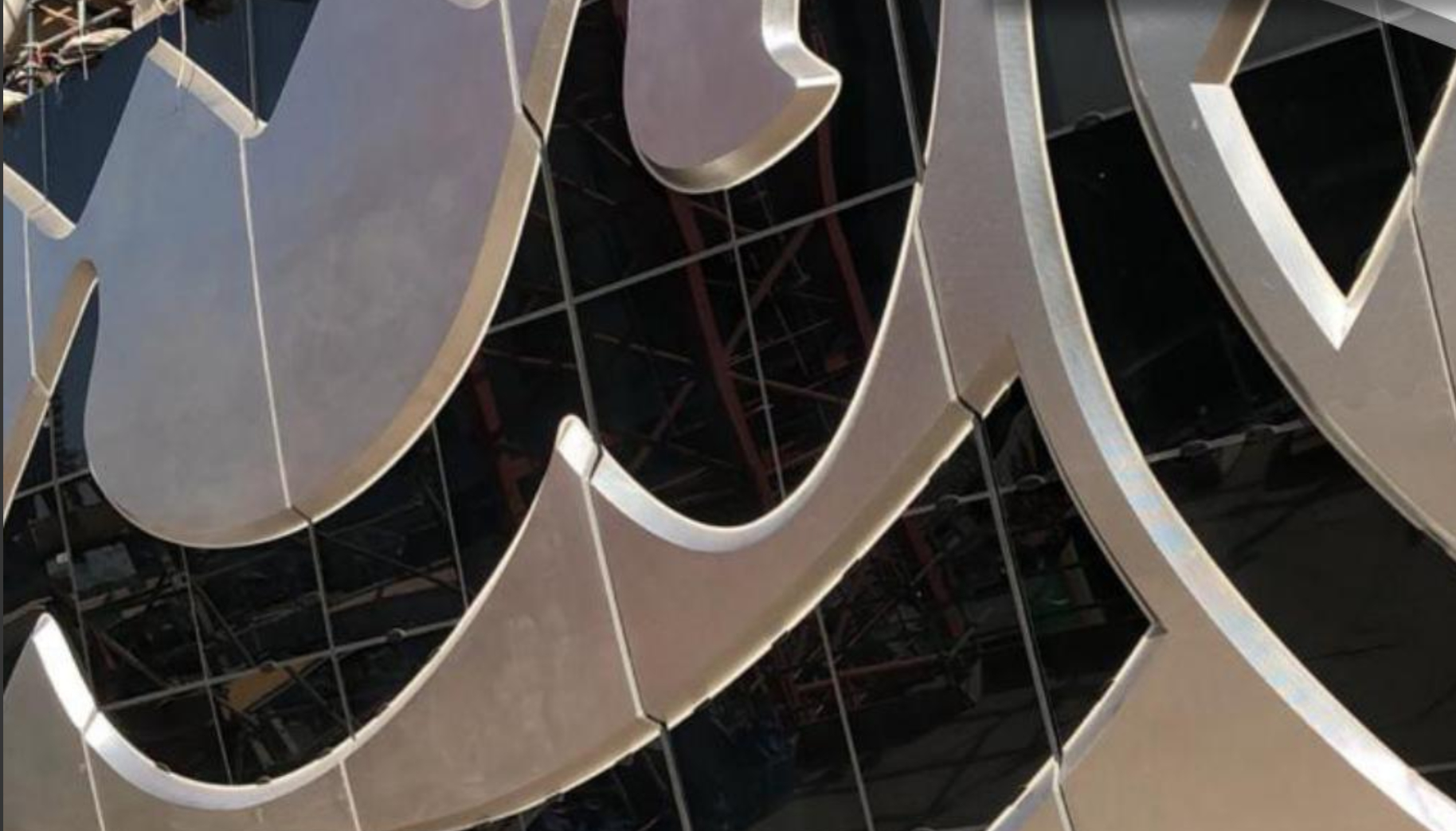
Paso 8 Cada panel se ajusta a través de una “junta universal” 3D única para lograr una fachada exterior perfectamente alineada.
Anterior SiguienteLas bandejas se colocaron a mano, se embolsaron al vacío y se curaron durante 6 horas en hornos que medían 20 metros de largo por 8 metros de ancho por 3 metros de alto. “Cada máquina CNC tenía su propio horno”, dice Affan. “No agrupamos muchos paneles por ciclo de curado. En cambio, cuando cada panel estaba listo, lo curamos inmediatamente para mantener un flujo de producción lo más alto posible. Luego, demolimos los paneles y usamos un escáner 3D para asegurarnos de que el panel tal como estaba hecho coincidiera con el archivo CATIA. Según nuestro sistema de control de calidad total, tuvimos que comparar los archivos digitales en cada paso del proceso ”.
Los paneles terminados recibieron el acabado exterior de acero inoxidable. “El acero inoxidable se adhiere con adhesivo a cada panel y luego se fija con sujetadores mecánicos, lo cual es un arte en sí mismo”, dice Affan. “El metal se cortó en pequeños hexágonos para cubrir los paneles 3D. La rejilla hexagonal variaba de parte a parte dependiendo de la cantidad de curvatura. Aunque tenemos experiencia y confianza en la unión, no podría haber riesgo de que un solo hexágono se rompa durante la vida útil del edificio. Por lo tanto, se tuvo que unir cada hexágono, lo que requería de 200 a 300 accesorios para un solo panel ". Luego, los paneles terminados se enviaron al sitio para su instalación.
Instalación sin problemas con la ayuda de la NASA
De hecho, la instalación la completó la empresa de construcción del edificio BAM International (Gouda, Países Bajos). “Solo proporcionamos supervisores para la instalación para ayudar con el manejo de los paneles”, señala Affan. “La forma en que se levanta cada uno es clave. Los paneles fueron diseñados para ser lo suficientemente fuertes para la posición específica de cada uno en el edificio. Sin embargo, deben levantarse de una manera específica, a través de al menos dos puntos de elevación, al igual que los casetes colgantes en los métodos de construcción más tradicionales ”.
Hubo un problema adicional que Affan estaba especialmente calificado para resolver. “Para que cada panel se asiente sobre la estructura de acero y sin embargo forme la superficie lisa, necesitábamos la capacidad de ajustar el panel en profundidad, orientación y curvatura en 3D; en otras palabras, una especie de junta universal con tres grados de libertad. . En 1985, trabajé como estudiante en la NASA en California en la amortiguación de estructuras de estaciones espaciales. La clave era poder mover cada estructura y ajustarla cuando el transbordador atraca para que la vibración se amortigüe rápidamente, un poco como la cancelación de ruido. Utilicé la misma tecnología para la fijación y el ajuste del panel durante la instalación ”.
Además, debido a que los paneles también proporcionaban el sello hermético del edificio, no podía haber espacios entre ellos. “Los paneles no podrían colgar directamente o podrían agrietarse”, dice Affan, explicando que debido a una alta carga viva de 1,5 toneladas en el voladizo 6 th área de exhibición del piso, la estructura de acero realmente se mueve. “Mantuvimos un espacio con una separación precisa entre los paneles y este se llenó con una junta especial”. Esta junta, lo suficientemente suave para expandirse, pero lo suficientemente rígida para soportar cargas, proporcionó la funcionalidad de sellado al tiempo que permitió la apariencia estética del edificio.
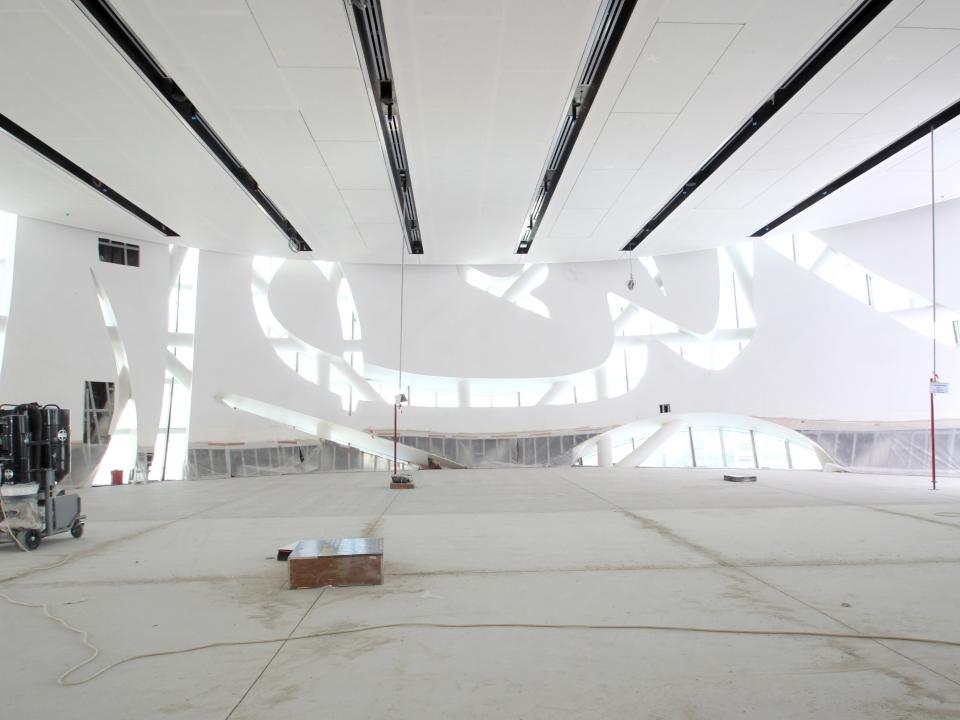
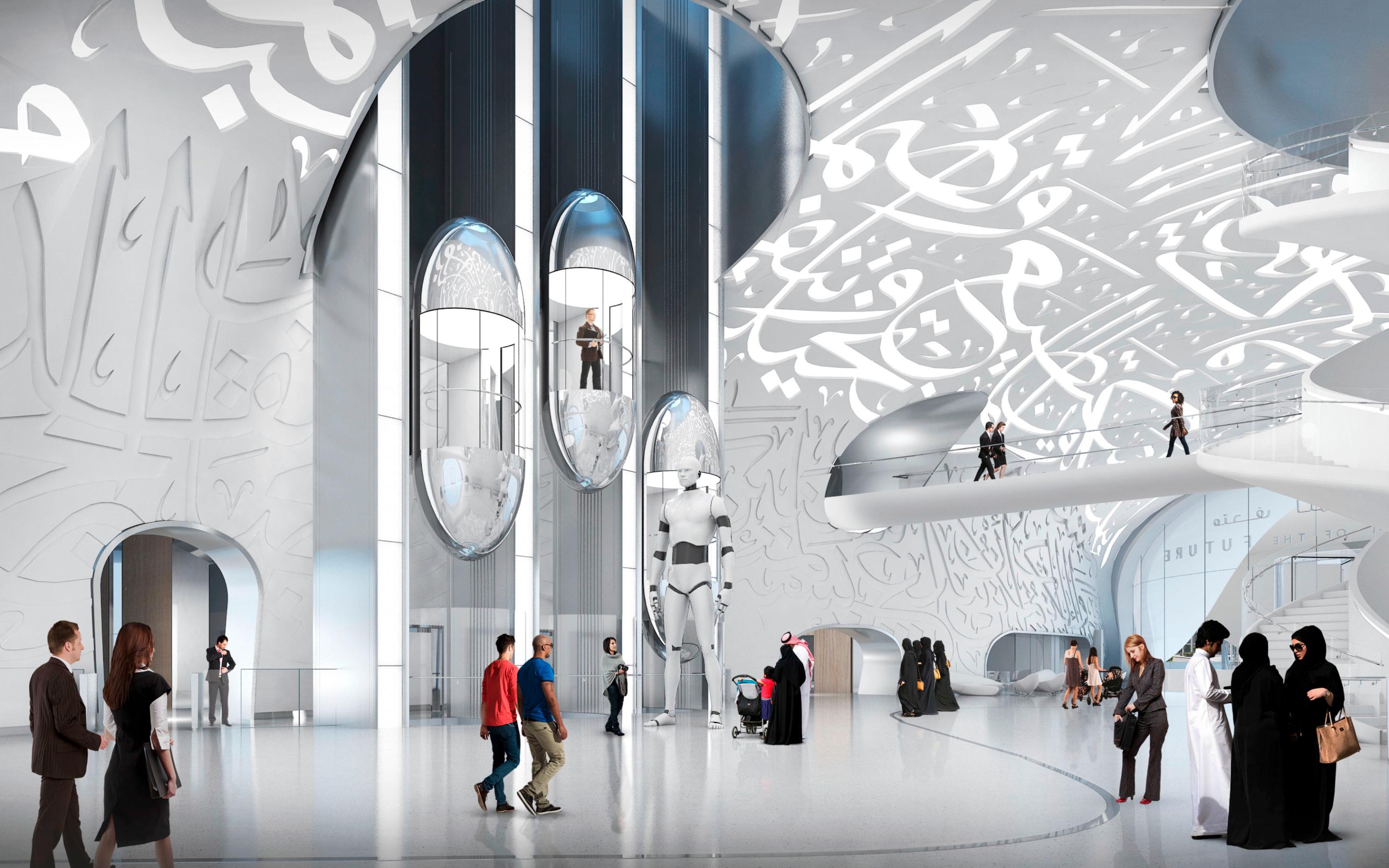
Tales soluciones son una ventaja, señala Affan. “Debido a que venimos de una experiencia en estructuras, podemos combinar muchos materiales. Esto es muy importante. Los composites son solo un material que usamos. Este no fue solo un proyecto compuesto ". los resultados hablan por si mismos. “La instalación salió bien; no hubo ningún problema ”, dice Affan, quien señala que no había forma de verificar si el panel encajaría excepto para asegurar su conformidad con el archivo digital. "Todavía no hemos tenido un panel que no se haya ajustado o haya tenido la forma incorrecta o la palabra esté mal escrita", testificó el gerente de proyecto de Buro Happold, Bauly, en un artículo de la BBC escrito por Elizabeth Bains.
Construcción modular futura
“Gestionamos todo el proceso juntos”, añade Affan. “El trabajo en equipo dentro de nuestra propia empresa también fue clave; los grupos de diseño y disposición tenían que coordinarse entre sí. Nunca hemos hecho un trabajo tan grande como este y fue un desafío, pero nos gustan los desafíos ".
Desafortunadamente, COVID-19 ha pasado factura. “Terminamos este trabajo justo antes del cierre de la pandemia”, dice. “Ahora nos quedamos menos de 30 personas. Es devastador. Pero esto ha afectado a todos, no solo a nosotros ”. Y, sin embargo, Affan ve esperanza en el futuro y en el papel que jugarán los compuestos para lograr la sostenibilidad y la innovación que el mundo necesita en la construcción. “Especialmente en Dubai y el GCC (Consejo de Cooperación del Golfo), la gente quiere probar nuevas ideas. Está demostrando el futuro de la arquitectura y la construcción ”.
Ese futuro, enfatiza, será para quienes puedan usar sistemas modulares de construcción, “y COVID-19 en realidad está acelerando esto. Las empresas incorporarán módulos y los enviarán al sitio. Esto se desarrollará porque traslada las ineficiencias fuera del sitio a la fábrica, aumentando el control y la calidad. En el lugar, debes coordinar a todas las personas. Es una pérdida de tiempo esperando a otros subcontratistas. También depende del clima y los paros laborales. La fabricación en una fábrica elimina todo esto. Debido a que son lo suficientemente fuertes, livianos y duraderos para transportar e instalar fácilmente, los materiales compuestos permiten este tipo de construcción modular y puede hacer cualquier forma que desee ”.
Affan señala que la construcción modular se ha utilizado en cruceros durante años, donde cada cabina está prefabricada, completa con calefacción / aire acondicionado, sistemas eléctricos y de plomería, y luego se ensambla en el marco de acero del barco como bloques LEGO. “Imagínese cuánto tiempo ahorrará cuando cada módulo ya esté equipado. Ahora estamos ante un proyecto para hacer un edificio de gran altura de esta manera utilizando materiales compuestos ”, dice. "Si tiene resinas FR, no necesita las piezas que antes eran metálicas". Citando un hotel Marriott construido de esta manera y terminado el año pasado en la ciudad de Nueva York, Affan agrega, "ese edificio era de acero y madera, pero podemos construirlo en materiales compuestos".
Resina
- Cloud Security es el futuro de la ciberseguridad
- El futuro del software de corte
- Edge computing:la arquitectura del futuro
- Visualizando el futuro del mantenimiento de la planta
- El futuro de los centros de datos
- Construyendo mejores cadenas de suministro para el futuro
- La automatización inteligente de edificios y el futuro del desarrollo inmobiliario en las ciudades
- Construyendo el futuro de la experiencia del empleado con automatización inteligente
- Cómo Tech Mahindra está construyendo la fábrica del futuro
- El futuro de la impresión 3D en la fabricación
- ¿Es la impresión 3D el futuro de la fabricación?