Fabricación de la mitad superior del demostrador de fuselaje multifuncional (MFFD)
Este blog es una continuación de una presentación del Centro Aeroespacial Alemán (DLR, Stuttgart y Augsburg) en el simposio TU Munich el otoño pasado y CW El resumen publicado durante el mismo período de tiempo, "Avanzando en el demostrador de fuselaje multifuncional (MFFD)". El proyecto también se describió en una presentación realizada por Lars Larsen a las 9:35 el día 3 de ITHEC 2020:“Avance impulsado por datos de proceso de soldadura ultrasónica continua basada en robots para el ensamblaje sin polvo de futuras estructuras de fuselaje”.
Como explicó Larsen, "el mayor desafío es demostrar que los costos de producción se pueden reducir significativamente mediante el uso de la automatización". Para la mitad superior del MFFD, esto incluye la consolidación in situ mediante colocación automática de cinta / colocación de fibra (ATL / AFP) para evitar el autoclave y la soldadura sin polvo / sin polvo para el ensamblaje. “Esto debería permitir cambiar la secuencia de las líneas de ensamblaje final y de componentes en el futuro”, dice Larsen, “permitiendo que los sistemas se integren antes montaje." Esto se debe a que, a diferencia del mecanizado para los orificios de los sujetadores, la soldadura no produce virutas ni escombros que puedan dañar los sistemas preinstalados, como la energía eléctrica distribuida, los accesorios interiores, etc.
Este blog se basa en mi entrevista con Sebastian Nowotny, jefe de diseño de componentes y tecnologías de fabricación en el DLR Institute of Structures and Design (BT, Stuttgart) y Frederic Fischer, líder técnico para la producción de compuestos termoplásticos en el DLR Center for Lightweight Production Technology ( ZLP, Augsburgo). Fischer también es el director de proyectos de la mitad superior del MFFD en DLR.
NOTA:En la imagen de arriba, los largueros con forma deslizante se refieren a un proceso desarrollado dentro de Clean Sky 2 por Applus + Labaoratories (Barcelona, España), consulte mi blog de 2017 sobre conformado por deslizamiento, y los clips prensados en caliente se refieren al estampado, consulte:
- Acelerar los compuestos termoplásticos en la industria aeroespacial
- Los compuestos termoplásticos "recortan" el tiempo, el trabajo en piezas pequeñas pero cruciales
- Dentro de un semillero de compuestos termoplásticos
Combinando estructura, cabina y sistemas
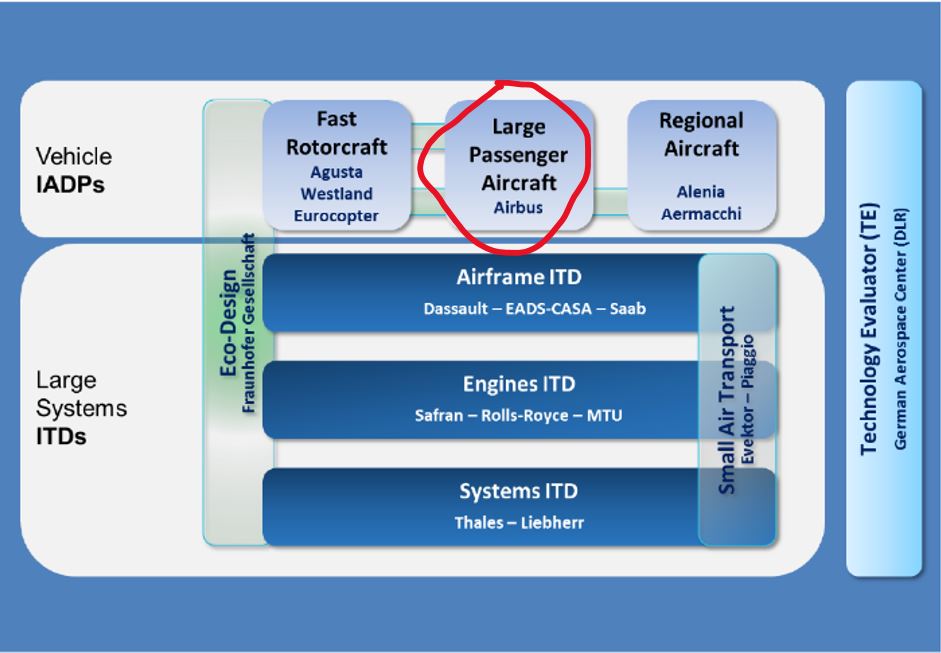
Le pregunté a Nowotny sobre la historia de la mitad superior del MFFD. “Cuando comenzó Clean Sky 2, se emitió la primera convocatoria de propuestas”, responde. “Creo que comenzamos en 2015 y ganamos la licitación para el proyecto llamado ICASUS, que era un proyecto de co-socio para el programa de aviones grandes de pasajeros (LPA). El foco principal fue el diseño de un fuselaje multifuncional. En ese momento, no era un compuesto termoplástico. El objetivo principal era combinar el fuselaje, la cabina, los sistemas y la estructura en un proceso de diseño. Básicamente, el trabajo que se hizo allí es lo que ahora se ha convertido en el demostrador de fuselaje multifuncional (MFFD) y es el soporte tecnológico para nuestro trabajo en el proyecto de capa superior ”.
ICASUS
El proyecto ICASUS tiene como objetivo desarrollar soluciones multifuncionales y altamente integradas para el fuselaje multifuncional de próxima generación, cabina y sistemas integrados de fuselaje. En la actualidad, el proceso de fabricación y montaje de aeronaves de pasillo único se basa en pasos secuenciales costosos y que requieren mucho tiempo. Especialmente el ensamblaje de componentes principales (MCA) y la línea de ensamblaje final (FAL) son cuellos de botella que impiden procesos más rápidos y acelerados. Por esta razón, ICASUS desarrollará un nuevo concepto para la fabricación y el montaje de futuros aviones de pasillo único dirigidos a:
- Producción de alta tasa de 60 aviones / mes;
- Reducción del coste recurrente del fuselaje de 1 millón de euros en comparación con la referencia A321 ACF ("Advanced Cabin Flex");
- Reducción del peso del fuselaje de 1 tonelada métrica en comparación con el A321 ACF.
El enfoque será combinar las disciplinas originalmente autárquicas de cabina / carga, sistemas y estructura para terminar con la combinación e integración más prometedora de las respectivas funciones y requisitos. Esto se logrará mediante el uso de materiales avanzados y la aplicación de principios de diseño innovadores en combinación con la arquitectura del sistema más avanzada en combinación con la cabina de próxima generación.
El factor principal es reducir significativamente el consumo de combustible mediante la aplicación de sistemas de bajo peso y arquitectura / integración de sistemas. Esto requiere un procedimiento de optimización global multidisciplinario, así como el desarrollo y la aplicación de un enfoque holístico de la Industria 4.0. Se utilizará el diseño para la fabricación automatizada, la automatización, la sensorización, el análisis de datos y el intercambio seguro de datos. Los principales objetivos de la fabricación del MFFD incluyen la verificación de la producción rentable y de alto volumen de estructuras compuestas multifuncionales y la contribución a los conceptos de certificación para juntas de CFRP termoplástico (por ejemplo, soldadura).
¿Cómo se combinan la cabina del fuselaje, los sistemas y la estructura en uno? “Aún tendrías esas disciplinas con sus respectivos requisitos, pero creo que el objetivo principal es el enfoque para colaborar ya en una etapa temprana”, explica Nowotny. “Ha habido reglas estrictas para el proceso de diseño del fuselaje de la aeronave que han creado restricciones y han impedido un diseño de aeronave totalmente optimizado. La idea inicial de combinar estructura, cabina y sistemas fue tener un proceso de diseño que reúna estos tres aspectos y luego trate de encontrar el óptimo global, no solo uno primero para la cabina y luego uno para la estructura y luego uno para los sistemas. . Pero, por supuesto, hay muchas reglas y este no es un proceso fácil porque también involucra la certificación ”.
“Es un proceso continuo, en el sentido de que se ha establecido una plataforma digital y todos los socios europeos aportan información sobre ese diseño digital único”, dice Fischer. “Avanzar en este diseño integrado para el MFFD es lo que ha estado sucediendo durante los últimos años. Nuestro equipo entregará la mitad superior con provisiones para la cabina y la instalación del sistema. La visión es revolucionar el ensamblaje final mediante la entrega de componentes principales totalmente equipados ”.
Aunque DLR ya formaba parte del proyecto de diseño de MFFD, no recibió el visto bueno final para el proyecto de fabricación hasta 2019. El consorcio para construir la mitad superior comprende a Airbus como líder general del proyecto MFFD, Premium Aerotec (Augsburg, Alemania ) como líder del diseño industrial y estructural y proveedor de los marcos, Aernnova (Vitoria-Gasteiz, España) para producir los largueros y DLR como líder para el desarrollo de la tecnología de laminado y soldadura. Durante el año pasado, dice Fischer, "hemos refinado el diseño de la mitad superior para asegurar que se pueda fabricar con las tecnologías seleccionadas".
Consolidación in situ
Mientras que la mitad inferior del MFFD se produce utilizando ATL y AFP seguido de consolidación en autoclave, la mitad superior utilizará consolidación in situ durante ATL / AFP. ¿Por qué? "Para obtener el máximo rendimiento del proyecto de investigación, optamos por desafiar la línea de base", dice Fischer, "y aprovechar la oportunidad de utilizar una tecnología en complemento de la mitad inferior". Nowotny añade:“Demostramos que es un método de fabricación muy prometedor que se centra en la producción ajustada y reduce los pasos de fabricación. Pero creo que está claro que no existe un único método de fabricación que sirva para todos los propósitos. Aún debe decidir, caso por caso, cuál es el proceso de fabricación óptimo para cada pieza ”.
Dos tipos de soldadura
Otra elección hecha para la mitad superior fue el uso de dos tecnologías de soldadura diferentes. “Usamos soldadura ultrasónica continua basada en robot para los larguerillos porque, en nuestra opinión, esa es la tecnología más adecuada para juntas realmente largas, y especialmente para la configuración del larguero”, explica Fischer. Se eligió la soldadura por resistencia para integrar los bastidores del fuselaje. “Estas elecciones son el resultado de análisis intensivos que tuvimos al comienzo del proyecto, junto con Premium Aerotec. Observamos los diferentes escenarios de soldadura, qué se debía unir y dónde ”.
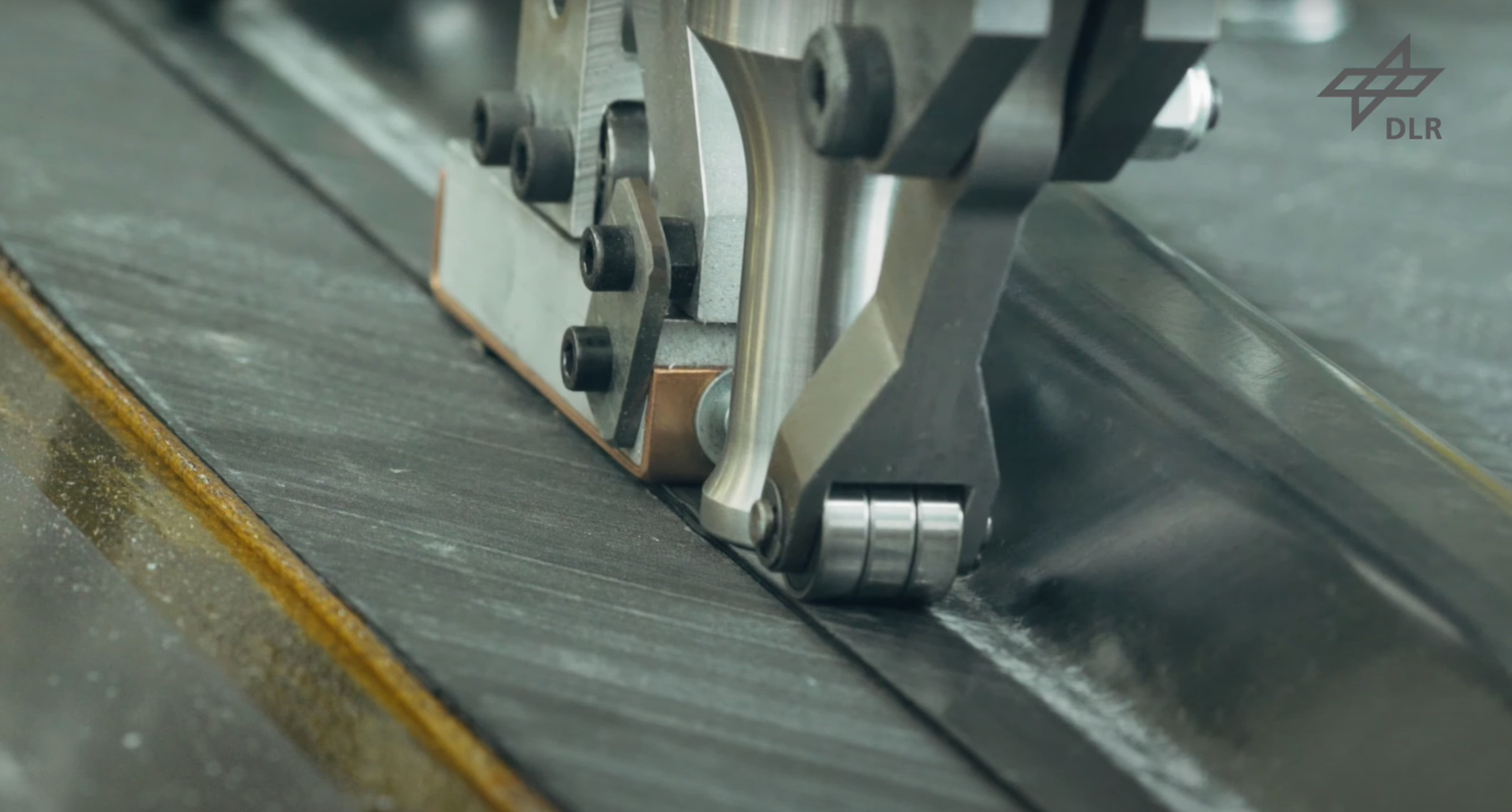
La soldadura ultrasónica continua desarrollada por DLR utiliza un robot industrial estándar. El efector terminal de soldadura comprende un rodillo de pre-rodaje, un sonotrodo de 25 milímetros de diámetro y una unidad de compactación de seguimiento. El efector final está equipado con varios sensores, lo que permite la supervisión del proceso en línea. Al usar el robot como manipulador, como se muestra en el video a continuación, se pueden soldar una variedad de geometrías, como un mamparo de presión trasero curvo o largueros omega en una piel.
“Entonces, tenemos dos procesos con una gran diferencia”, señala Fischer. "Uno es un continuo proceso y el otro es un discontinuo proceso. Para las juntas de 8 metros de largo de los largueros en Z, optamos por la soldadura ultrasónica continua. Y para el caso de uso altamente complejo, en términos de accesibilidad y gestión de tolerancia, para soldar las bridas adjuntas de los marcos a la piel, elegimos la soldadura por resistencia. Ajustaremos y preequiparemos el elemento de soldadura por resistencia a la geometría del marco y tendremos una herramienta de soldadura similar a una abrazadera que se cierra neumáticamente, hace contacto con los elementos de soldadura y luego activa el proceso de soldadura ”.
Nowotny señala que la soldadura por resistencia tiene la mayor madurez y mayor resistencia, lo que coincide con la mayor carga que se observa en las juntas entre los marcos y los tacos. Señala que este proceso consiste en soldar el marco a la piel y soldando la abrazadera tanto al marco como al larguero.
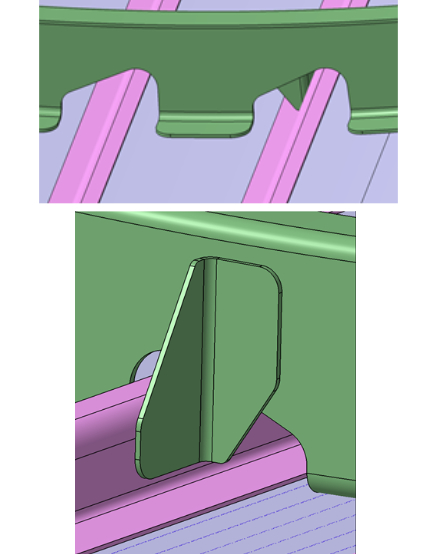
“Mostramos la integración de clips en piezas genéricas en JEC 2017”, dice Fischer. Nowotny añade:“Y de hecho, tuvimos el proyecto HISYS con el departamento de alta elevación de Airbus Bremen en 2005-2008 para la soldadura por resistencia con termoplástico PEEK (polieteretercetona). Trajimos todo el proceso para soldar las nervaduras en la piel hasta TRL 5. Entonces, los conceptos básicos del proceso se comprenden bastante bien, y ahora podemos enfocarnos principalmente en la adaptación, automatización y robustez del proceso ”.
" Uno de los facilitadores clave para las diferentes tecnologías de soldadura, a pesar de que existen desde hace mucho tiempo, es demostrar que están listas para su aplicación comercial en la industria ”, señala Fischer,“ incluida la automatización, la programación y el control de calidad necesarios. . Una de las cuestiones clave que estamos analizando es cómo saber si la soldadura es buena. Queremos asegurarnos de tener los datos del proceso para demostrar que sabemos que la soldadura funcionará a largo plazo y que no estamos solicitando una verificación posterior de END con ultrasonidos, u otra inspección general en el ensamblaje completo. Entonces, uno de nuestros principales objetivos en este proyecto es desarrollar el aseguramiento de la calidad industrial ”.
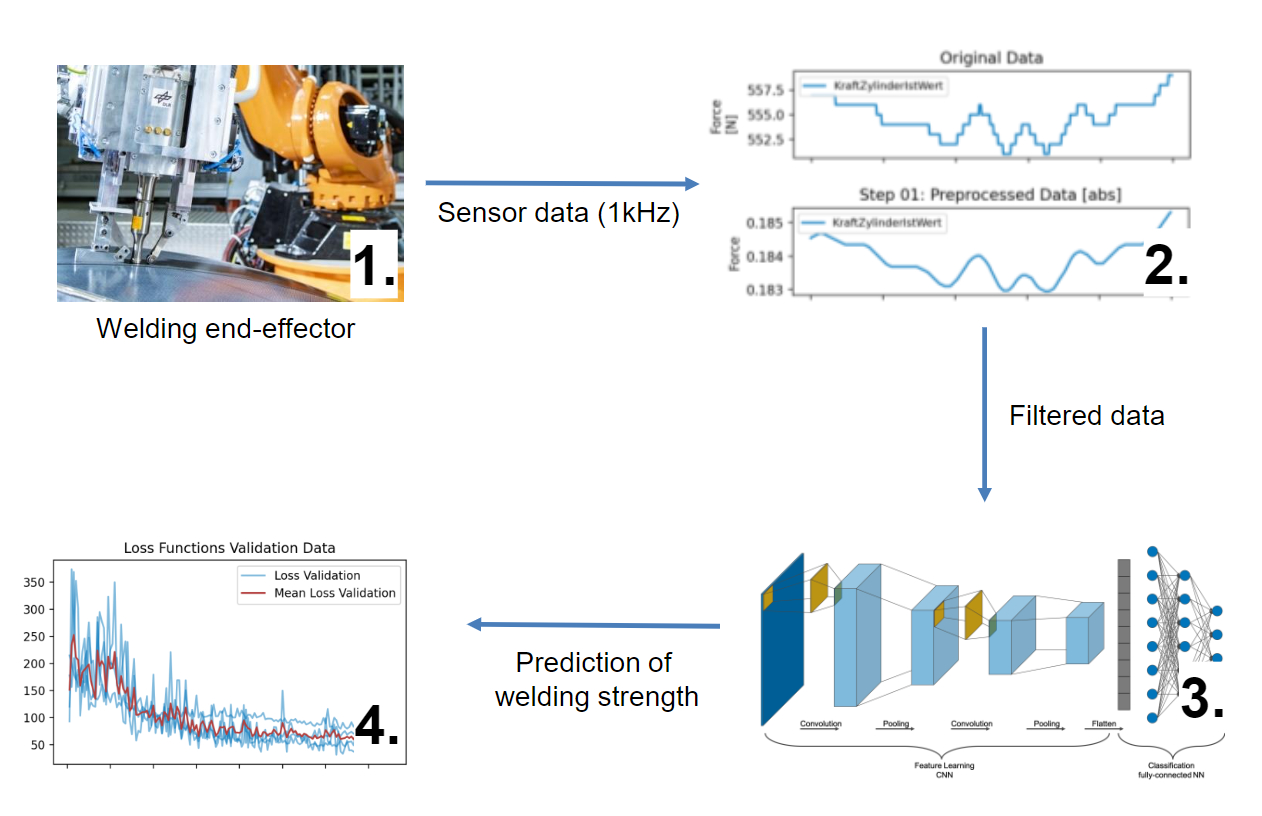
Girar a LM PAEK
Como se explica en mi blog, "Probar la soldadura LM PAEK para demostrador multifuncional de fuselaje", aunque el MFFD comenzó con fibra de carbono / PEKK (polietercetonacetona), en la décima convocatoria de propuestas (CFP10) en marzo de 2019, el material de referencia había sido cambiado a fibra de carbono / PAEK (poliariletercetona). PAEK es la familia general de polímeros dentro de la cual residen PEEK, PEKK y LM PAEK. ¿Cuánta experiencia tiene el equipo de la mitad superior con LM PAEK? “Ya lo hemos usado para varias pruebas de fabricación”, dice Fischer. “El rendimiento del material es bastante prometedor tanto para soldadura ultrasónica como por resistencia. Aún así, el material está en desarrollo y se ha establecido un proceso de intercambio común en términos de lecciones aprendidas y desarrollo de pautas de procesamiento entre todos los socios europeos y el proveedor del material ”.
" Sin embargo, ”agrega Nowotny,“ creo que es bueno que ahora tengamos estas opciones de materiales, porque hace muchos años, solo existía Cytec APC-2, y nada más. Especialmente en Europa, a veces podías conseguir el material y otras veces, "no, lo siento". Ahora, contamos con varios proveedores de materiales que trabajan activamente en los materiales, y también para los diferentes procesos. Por ejemplo, Victrex, como vimos presentado en el simposio TU Munich 2020, ahora está buscando la optimización para la fabricación aditiva. También se están realizando algunos trabajos de optimización para la consolidación in situ de AFP y algunos para la consolidación secundaria mediante autoclave, así como varios procesos de fabricación fuera de autoclave (OOA). Entonces, hay mucho más en marcha ahora, y esto aumenta las posibilidades de obtener un buen material para cada proceso ”.
Cronología y próximos pasos
"Básicamente, hemos terminado el proceso de fabricación de diseño para un demostrador intermedio (un A320 de diámetro con dos bahías de bastidor y un ancho de 950 milímetros) y construiremos esa media carcasa más pequeña a principios del próximo año (2021)", dice Fischer. . “Aparte de eso, hemos comenzado a adquirir las herramientas para la mitad superior de la carcasa a gran escala y estamos mejorando nuestras tecnologías para asegurarnos de que seremos capaces de producir la mitad superior de tamaño completo a tiempo en 2022 . ”
¿Qué implica esto? Un problema son las tolerancias de montaje. “Las juntas longitudinales a lo largo de los lados izquierdo y derecho de las mitades superior e inferior del fuselaje se han diseñado durante algún tiempo”, explica Fischer. "A partir de estos, tenemos ciertos requisitos y debemos asegurarnos de que nuestras tolerancias de producción cumplan con esos requisitos".
“La historia básica de lo que estamos tratando de hacer con la carcasa superior es demostrar las rutas más eficientes para la producción de compuestos termoplásticos y allanar un camino que pueda competir con el aluminio para futuros aviones”, dice Fischer. Señala que DLR ya lo ha demostrado en su trabajo con Premium Aerotec para desarrollar un mamparo de presión trasero termoplástico soldado, mostrado en 2018 y 2019 (ver también “Nuevos horizontes en la soldadura de compuestos termoplásticos”). La soldadura y la producción ajustada son habilitadores clave para los termoplásticos. Y ahora debemos sacar estas tecnologías del laboratorio y llevarlas a la industria. Y para que las industrias crean que realmente pueden utilizar estas tecnologías de soldadura, debemos demostrar que pueden ser automatizadas, predecibles y controladas para garantizar la confiabilidad en las tareas de producción reales. Y eso es lo que estamos haciendo ".
Resina
- Los beneficios de la fabricación a corto plazo
- ¿Son los materiales orgánicos el futuro de la fabricación de plástico?
- Cómo elegir el mejor proveedor de fabricación de plástico
- Robots de ensamblaje 101:qué, dónde y cómo de los robots de ensamblaje en la fabricación
- Lo último en reubicación de fabricación
- 15 datos sobre la fabricación en EE. UU.
- El papel de blockchain en la fabricación
- Los 8 desperdicios de Lean Manufacturing
- ¿Qué hay en el proceso de fabricación?
- El futuro de la impresión 3D en la fabricación
- ¿Es la impresión 3D el futuro de la fabricación?