La fabricación aditiva agrega versatilidad a las grandes estructuras marinas
La capacidad de construir rápidamente diferentes iteraciones de piezas, sin tener que desarrollar o comprar costosas herramientas dedicadas, es la razón por la que la fabricación aditiva (AM) se usa con tanta frecuencia en la creación de prototipos de piezas. Sin embargo, a medida que los materiales y las tecnologías de impresión continúan mejorando, más empresas pueden extender la velocidad y versatilidad de AM también a las piezas de uso final, particularmente para tiradas cortas o aplicaciones únicas en las que la capacidad de producir rápidamente nuevos diseños es una ventaja. .
Recientemente, dos empresas han demostrado que las tecnologías AM compuestas pueden permitir soluciones para personalizar grandes estructuras marinas, como vehículos submarinos autónomos (AUV) y lanchas a motor.
Impresión 3D de gran formato para una producción AUV personalizable
Los vehículos submarinos autónomos son un tipo de vehículo robótico no tripulado capaz de viajar bajo el agua sin conexión física a un barco o control remoto de un operador humano, y a menudo están equipados con cámaras o sensores para varios casos de uso en aplicaciones de defensa, investigación oceánica o estudios en alta mar. Por lo general, los cascos exteriores de los AUV comprenden un gran recipiente a presión de metal o están construidos con plástico termoformado o compuestos. Sin embargo, ambas opciones requieren el desarrollo y la compra de herramientas dedicadas, que pueden ser costosas y limitan la cantidad de personalización que se puede realizar para los clientes de AUV. El fabricante de AUV Dive Technologies (Quincy, Mass., EE. UU.) Ha descubierto que la impresión 3D compuesta resuelve muchas de las limitaciones de la fabricación tradicional.
En 2018, los cofundadores de Dive Technologies, Bill Lebo, Jerry Sgobbo y Sam Russo, decidieron formar su propia empresa para diseñar y lanzar un nuevo AUV más capaz que satisfaga las demandas de los clientes de resistencia prolongada y gran capacidad de carga útil.
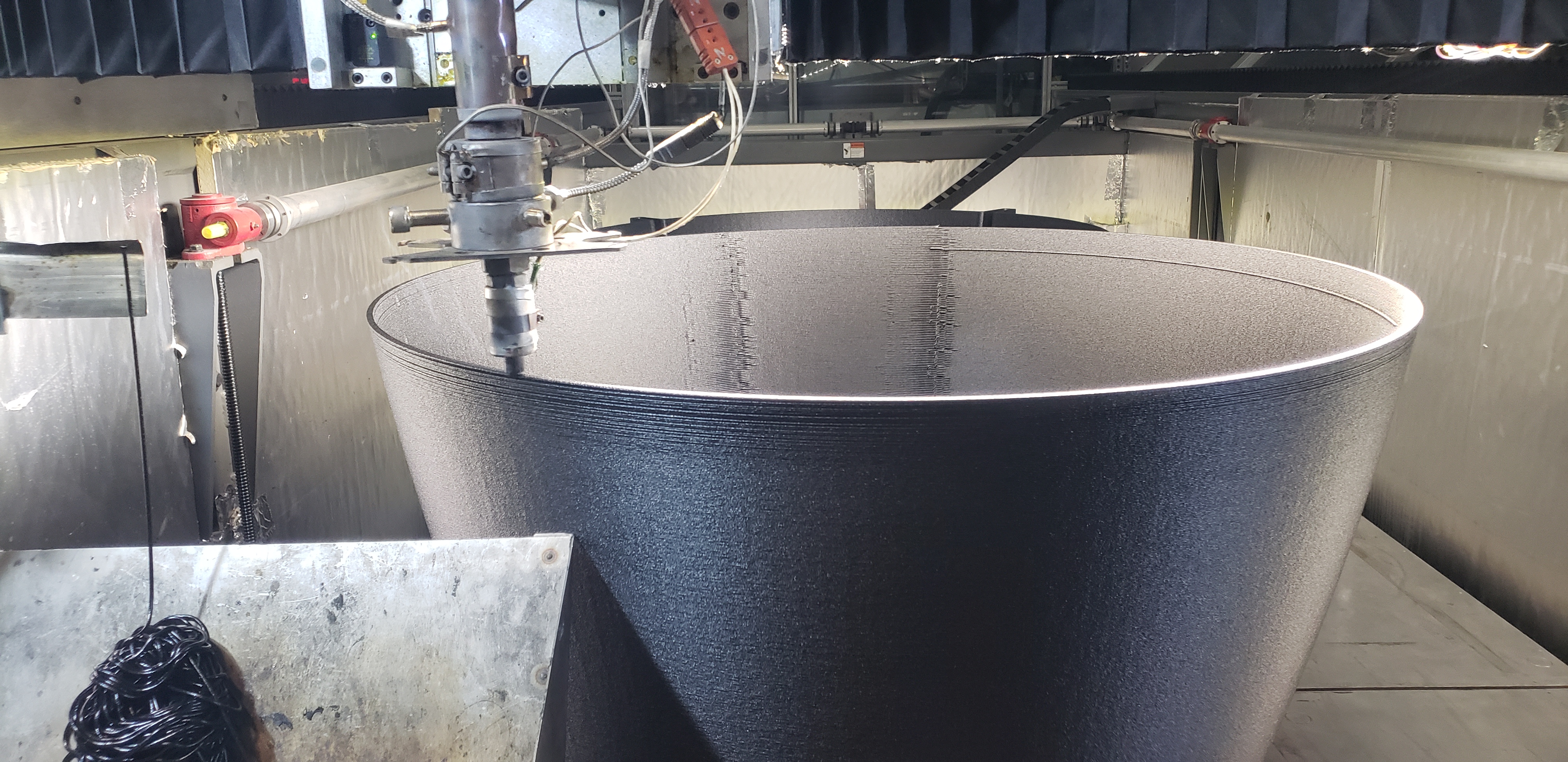
Lo que ellos y su equipo desarrollaron es el DIVE-LD, un AUV comercial de 19 pies de largo y 4 pies de diámetro capaz de bucear a 6.000 metros y viajar hasta 500 millas, con una carga útil de hasta 1 metro cúbico. Originalmente, el equipo asumió que la estructura final de su vehículo utilizaría plásticos termoformados para el casco exterior. Para explorar y probar el diseño, Dive Technologies habló con el Laboratorio Nacional Oak Ridge (ORNL, Oak Ridge, Tennessee, EE. UU.) Sobre el uso de la impresión 3D para la creación rápida de prototipos. A través de ORNL, el equipo de Dive conoció al especialista en fabricación aditiva de gran formato (LFAM) Additive Engineering Solutions (AES, Akron, Ohio, EE. UU.), Y comenzó a trabajar con el equipo de AES en un proceso de fabricación para sus formas de casco AUV.
Sin embargo, durante el trabajo en los prototipos impresos en 3D, Dive Technologies se dio cuenta del potencial de LFAM para producir rápidamente terminados componentes, no solo prototipos. Los componentes del prototipo impresos en 3D no solo cumplieron con los requisitos de las piezas mejor de lo esperado, sino que la adopción de AM para los vehículos de producción también ahorraría costos de herramientas, permitiría a Dive producir productos finales más rápido que con los métodos tradicionales y permitiría un nuevo y más alto nivel de personalización rápida para clientes.
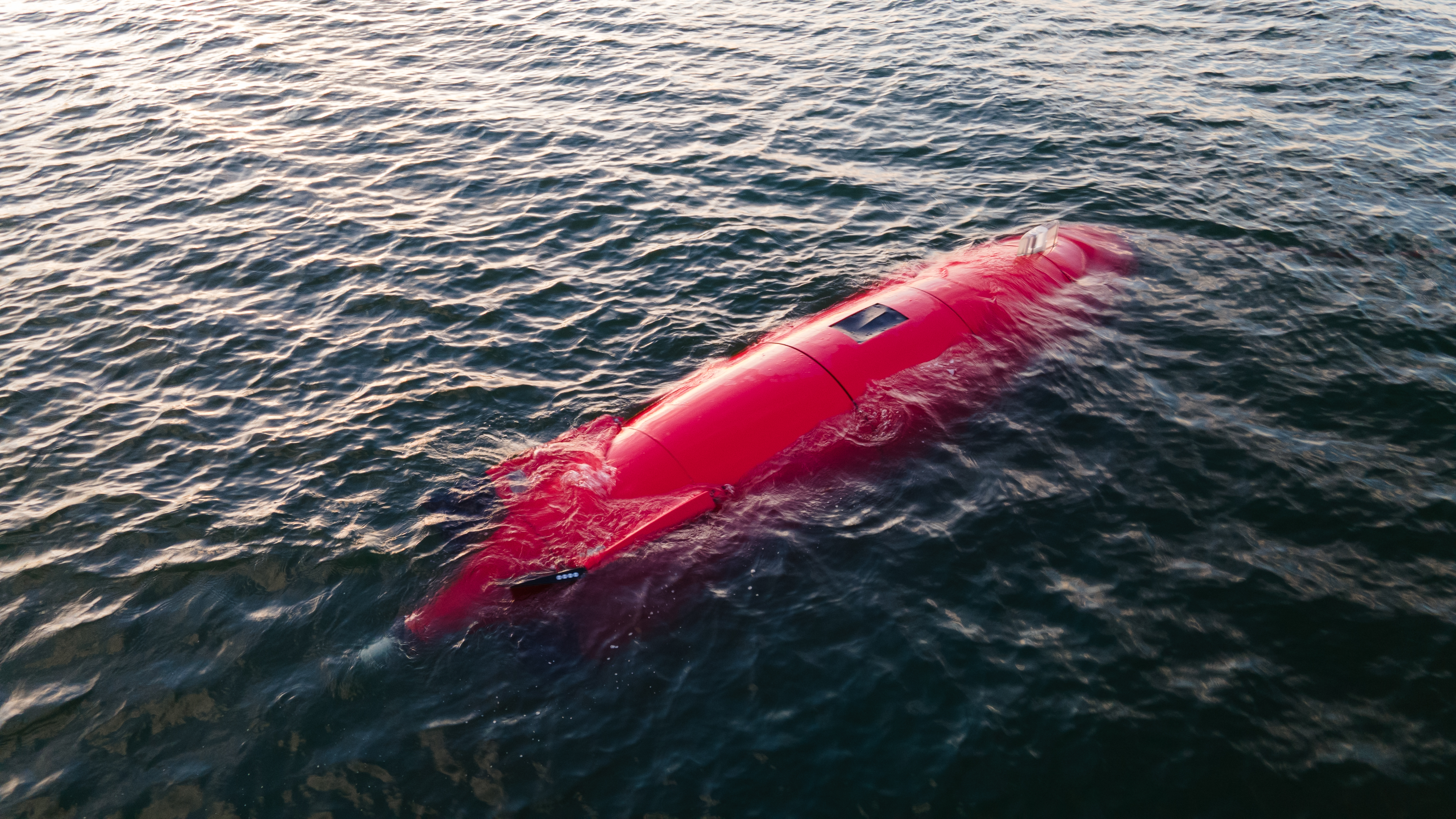
El casco exterior del DIVE-LD comprende nueve carenados en forma de tubo impresos con una de las cuatro impresoras 3D de AES Cincinnati Inc. (Cincinnati, Ohio, EE. UU.) Big Area Additive Manufacturing (BAAM). Estos carenados están impresos con ABS relleno de fibra cortada suministrado por Sabic (Riyadh, Arabia Saudita). Según el cofundador y vicepresidente de AES, Andrew Bader, AES puede imprimir todas las piezas para un casco completo en menos de dos días. Una vez entregados a Dive, los carenados impresos en 3D se sujetan mecánicamente con cuatro sujetadores por carenado y se recubren para producir una superficie exterior suave e hidrodinámica. Después de las pruebas iniciales exitosas en 2020, Dive está construyendo los primeros vehículos para clientes esta primavera y entregará el primer pedido en junio de 2021.
Según Russo, AM se ha convertido en una parte fundamental de la propuesta de valor de Dive Technologies para los vehículos y productos del futuro. La asociación con Dive también es un gran paso para AES y la impresión 3D compuesta. Bader agrega:"Por lo general, cuando la gente piensa en la impresión 3D, piensa en prototipos, accesorios y herramientas, por lo que esto muestra de qué otra cosa es capaz la impresión 3D".
Para leer más sobre Dive Technologies y AES, lea "La impresión 3D de gran formato permite una producción rápida y sin herramientas para AUV".
Automatización y AM de fibra continua para un diseño versátil de lanchas a motor
Desde que patentó su proceso de fabricación de fibra continua (CFM) en 2015, Moi Composites (Milán, Italia) ha explorado una gama de aplicaciones para su tecnología CFM de impresión 3D de fibra continua basada en deposición. Los sellos distintivos de CFM incluyen el software de diseño personalizado de Moi Composites, el uso de brazos robóticos, curado UV y fabricación "híbrida":laminación compuesta más tradicional sobre un núcleo estructural impreso en 3D. Recientemente, la compañía ha demostrado su tecnología CFM como una solución para el diseño de estructuras marinas más rentables, más rápidas e innovadoras, a través de una lancha demostradora llamada MAMBO.
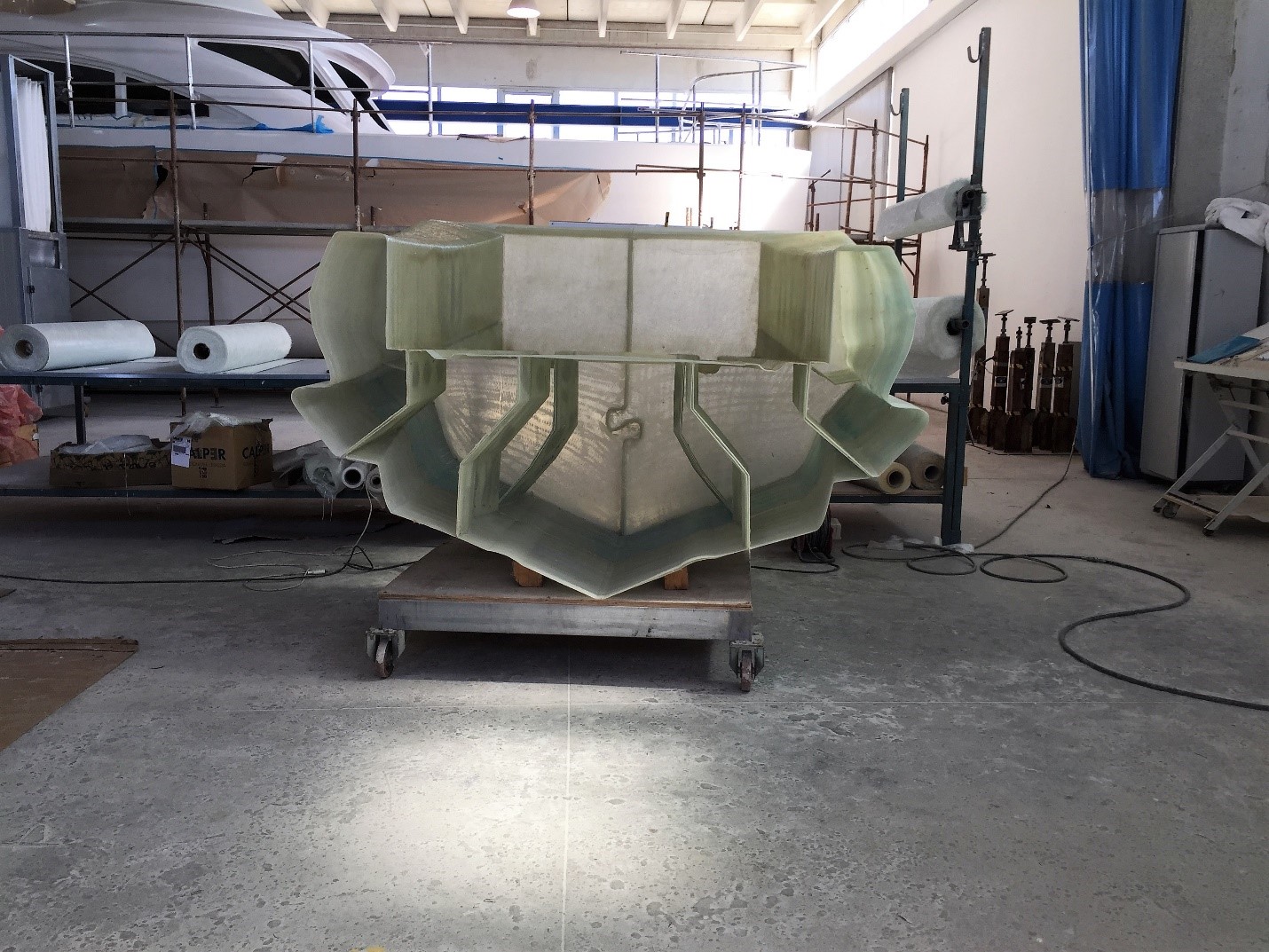
Según Gabriele Natale, cofundador de Moi Composites, él y su compañero cofundador Michele Tonizzo asistieron al Salón Náutico de Génova en 2017 y se dieron cuenta de que los costos de las herramientas y los procesos tradicionales de infusión de fibra de vidrio utilizados para muchos cascos de barcos limitan la capacidad de los diseñadores de barcos para explorar nuevos y diseños más complejos. Al reconocer que su tecnología de impresión 3D de fibra continua y sin molde podría ser una solución habilitante, Natale dice:"A partir de ahí, comenzamos a desarrollar un plan y comenzamos a reunirnos con socios dentro de la industria marina".
La embarcación MAMBO resultante tiene 6.5 metros de largo x 2.5 metros de ancho, con un peso en seco de aproximadamente 800 kilogramos, equipada con sistema de navegación, piso de corcho, asientos de cuero blanco y motor de 115 caballos de fuerza. Moi Composites trabajó con el estudio de ingeniería de diseño marino MICAD (Lecce, Italia) en el concepto de diseño estructural del barco, que combina formas orgánicas en sus elementos estructurales inspirados en el famoso catamarán Arcidiavolo de Sonny Levi. En el diseño y análisis dinámico de fluidos de los componentes se utilizó el software de fabricación aditiva Fusion 360 CAD y NETFABB de Autodesk (San Rafael, California, EE. UU.).
El casco y la cubierta del barco, impresos con vidrio E unidireccional suministrado por Owens Corning (Toledo, Ohio, EE. UU.) Y resina de éster de vinilo, se diseñaron para fabricarse en 50 secciones individuales de diferentes tamaños. La mitad de las secciones se imprimieron en las instalaciones de Moi Composites en Milán, y la otra mitad en las instalaciones de fabricación avanzada (ACF) del socio Autodesk en Birmingham, Reino Unido, la tecnología de impresión CFM 3D de Moi Composites y los robots duales Kuka (Augsburg, Alemania) se utilizaron en ambos instalaciones. Según Dominique Müller, director de investigación del equipo de fabricación aditiva de Autodesk, el sistema CFM del centro tecnológico de Autodesk permitió que el barco se imprimiera rápidamente y también permitió que Autodesk conociera mejor la tecnología que Moi estaba conduciendo de forma remota mediante el software de Autodesk. . El tiempo total de impresión de todos los componentes fue de aproximadamente dos meses.
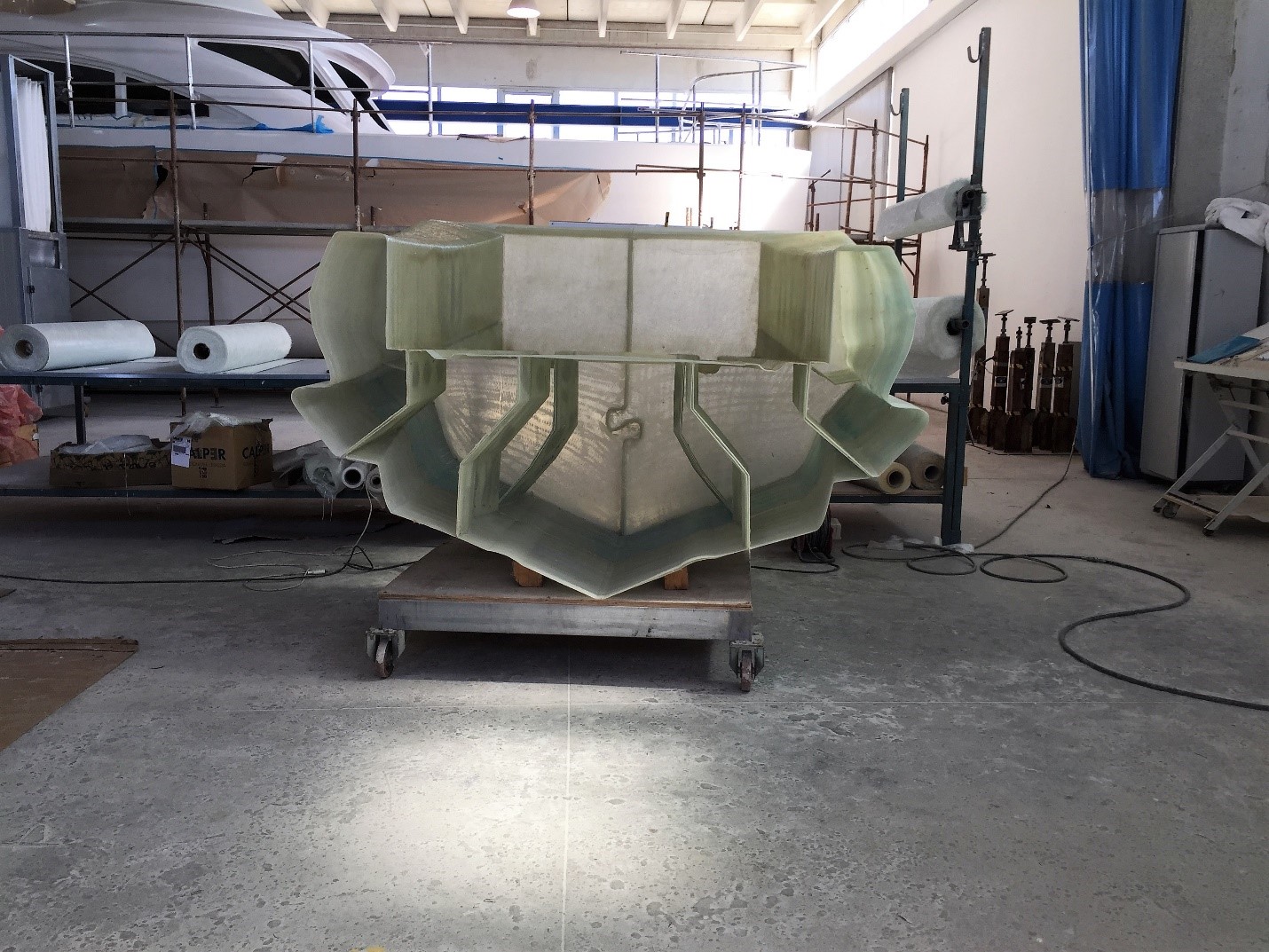
Las piezas impresas se enviaron al astillero de Catmarine en Miggiano, Italia, donde se ensamblaron y pegaron. En un proceso de fabricación híbrido similar al que Moi ha usado con prótesis y otras partes, el casco completo se laminó luego a mano con una capa adicional de fibra de vidrio / poliéster con núcleo de espuma de PVC, que, según Natale, varía en grosor a lo largo de la estructura. Después de que el casco y la cubierta estuvieran completamente ensamblados, lijados y recubiertos de gel, los socios de Moi Composites equiparon el barco con propulsión, navegación y otros sistemas para completar el barco.
Las pruebas iniciales en el mar y las pruebas de estabilidad se realizaron en el otoño de 2020, con MAMBO alcanzando hasta 26 nudos; Moi Composites planea continuar las pruebas en el mar en el verano de 2021 para lograr la certificación del barco.

“La fabricación aditiva, la digitalización y la automatización pueden acelerar la creación de nuevos conceptos y proyectos futuristas, porque para cada embarcación que desee diseñar, debe crear un nuevo molde. Con esta tecnología, puede modificar fácilmente su modelo 3D e imprimirlo nuevamente. Esto es perfecto especialmente para barcos de corta duración o de una sola vez ”, dice Natale.
Para obtener más información sobre MAMBO, lea "MAMBO prueba las aguas para la impresión 3D de grandes estructuras marinas".
Resina
- 5 procesos comunes de fabricación aditiva
- Fabricación aditiva frente a fabricación sustractiva
- Ventajas de la fabricación aditiva
- Una encuesta sobre los flujos de trabajo de fabricación aditiva
- Tecnologías de fabricación aditiva:la empresa de posprocesamiento que da forma al futuro de la fabricación
- Henkel ofrece una plataforma de materiales para la fabricación aditiva
- NCAMP lanza el primer programa de calificación de fabricación aditiva
- Se forma una alianza de fabricación aditiva y termoplásticos sostenibles en Colorado
- 5 tecnologías que alteran la fabricación
- Fabricación aditiva en electrónica
- Fabricación aditiva en la industria aeroespacial