Solución de problemas de termoformado de compuestos termoplásticos
Nota:información e imágenes de este artículo se obtuvieron del curso “Conformado Avanzado de Composites Termoplásticos” impartido por el Centro de Investigación de Compuestos Termoplásticos (TPRC).
Los compuestos termoplásticos (TPC) obtuvieron ventaja por primera vez con la demanda de tasas de producción más rápidas en la industria aeroespacial y otras aplicaciones ligeras. La producción de piezas en cuestión de minutos hizo que el termoformado (también conocido como estampado) sea el proceso de compuestos termoplásticos más común y el primero en producir piezas voladoras en masa (consulte "Dentro de un semillero de compuestos termoplásticos" y "Tiempo de corte de compuestos termoplásticos ...").
El proceso comienza con un blanco - un laminado compuesto termoplástico preconsolidado con la orientación de la capa requerida - y comprende los siguientes pasos (Fig.1):Preparación del blanco (corte y fijación), blanco calentamiento, transferencia a molde, posicionamiento en bruto, conformado, enfriamiento, desmoldeo de la pieza y recorte / acabado. El proceso de termoformado es un concepto simple, pero implica complejidades y desafíos que deben abordarse para lograr piezas de composite repetibles y de alta calidad.
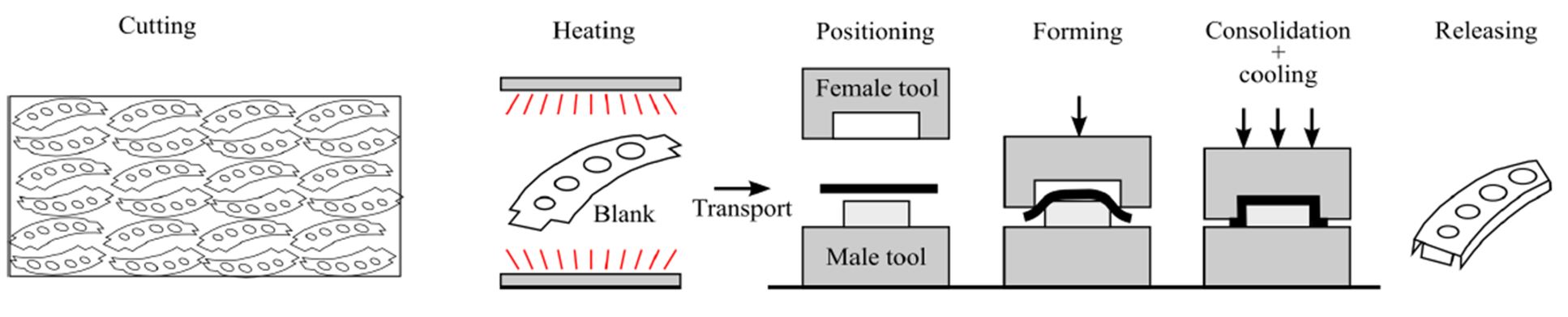
Evitar arrugas
Una arruga es visual y defecto funcional. Puede describirse como una flexión fuera del plano del material. La causa principal son las deformaciones por cizallamiento insuficientes, como el deslizamiento entre capas y el cizallamiento entre capas, durante el procesamiento. Las arrugas se producen predominantemente en superficies doblemente curvadas. Considere las siguientes acciones para minimizar las arrugas.
Precalentamiento suficiente y transferencia rápida. Durante la formación del blanco, la temperatura debe permanecer por encima de la temperatura de fusión (T m ) de la matriz de TPC para permitir la deformación por cortante. Tenga en cuenta que durante la transferencia de la etapa de precalentamiento al molde, la temperatura puede bajar significativamente, posiblemente hasta 40-50 ° C en tres segundos. Por lo tanto, el precalentamiento debe ser lo suficientemente alto como para que el polímero permanezca por encima de T m - o temperatura de transición vítrea (T g ) para polímeros amorfos, después de la transferencia y durante la formación. Una pieza en blanco fría no se deformará correctamente y desarrollará arrugas. Sin embargo, tenga cuidado de no sobrecalentar el blanco para evitar la degradación del polímero.
Estilo y disposición de tejido de la tela. Las telas de satén arnés (HS) tienen una mejor capacidad de drapeado debido a una deformación por cizallamiento más fácil en el plano, lo que ayuda a prevenir las arrugas. La capacidad de drapeado de las telas tejidas, de mayor a menor, es la siguiente:8HS> 5HS> sarga 2 x 2> tejido liso. La tela 5HS suele ser un buen punto de partida porque equilibra la capacidad de caída y el rendimiento mecánico. Los espacios en blanco hechos con refuerzos unidireccionales (UD) tienden a arrugarse más que las telas HS debido a la alta fricción entre las fibras que resiste el cizallamiento en el plano. Permitir el corte en el plano es la clave del éxito con la formación de piezas en bruto UD, especialmente con superficies doblemente curvadas.
Orientaciones de capas como [0, 90, ± 45] s que se encuentra en una capa cuasi-isotrópica puede inhibir la deformación por cizallamiento, lo que mejora las arrugas. Alternativamente, las capas de capas cruzadas (p. Ej., [0, 90]) ayudarán a evitar las arrugas porque el corte no está restringido por otras capas.
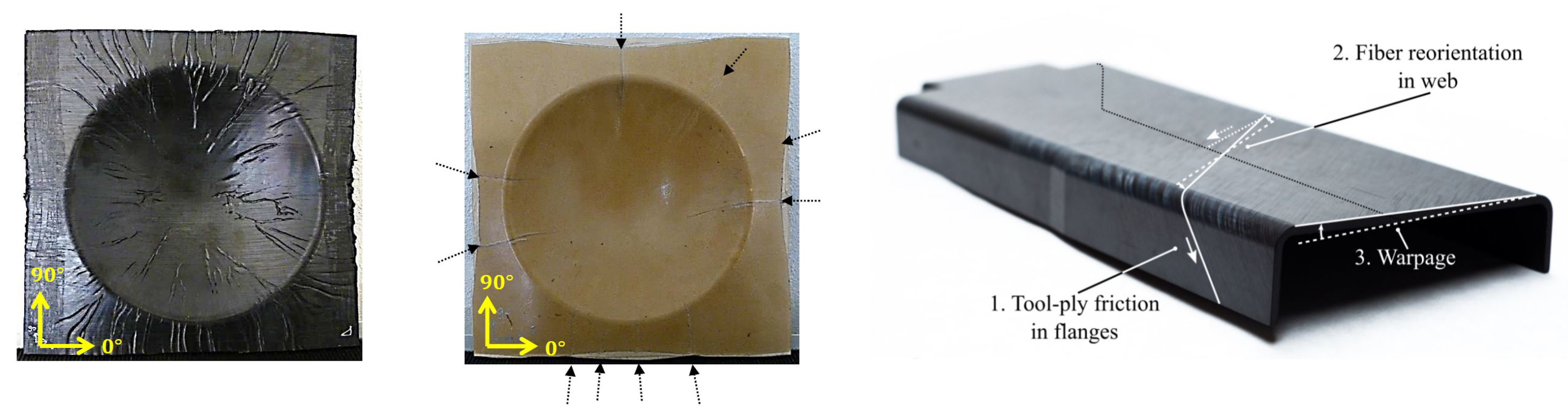
Fig. 2. Evitar arrugas y deformaciones
La parte hemisférica muestra muchas arrugas pequeñas y grandes usando un UD en blanco (izquierda) , mientras que solo las arrugas grandes son visibles usando un espacio en blanco 8HS (derecha) . El alabeo en este larguero compuesto resultó de la reorientación de la fibra debido a la fricción de la capa de la herramienta en las bridas. Crédito de la foto:"Formando límites de compuestos termoplásticos" por D.J. Wolthuizen, et. Alabama. ( izquierda ) y “Fabricación rápida de compuestos termoplásticos a medida mediante laminado automático y estampado” por Tjitse K. Slange ( derecha ).
Preparación y fijación del blanco. Se pueden usar pinzas y tensores para mantener la pieza en bruto en tensión en áreas que son propensas a doblarse fuera del plano. Encontrar la configuración optimizada puede llevar mucho tiempo, con múltiples iteraciones requeridas, pero el uso de software de simulación de procesos ayuda. La tensión adecuada de la pieza en bruto también evita que la pieza en bruto se combe, lo que puede causar problemas durante la transferencia y el conformado. Tales problemas incluyen que la pieza en bruto toque el molde demasiado pronto, lo que podría colocar demasiado material en el molde antes de que se produzca el drapeado, lo que resultará en pandeo y arrugas. El blanco también puede combarse y tocar el calentador, lo que puede dañar el blanco o detener el proceso.
Optimizar la geometría final de la pieza en blanco y cortarla a una forma casi neta puede evitar arrugas y reducir el desperdicio. Los cortes y los dardos también pueden ayudar a prevenir la flexión fuera del plano al reducir la tensión de la fibra para permitir una mejor formación.
Superar los desafíos con el diseño de moldes
Durante el termoformado y procesos de moldeo similares, el molde en sí puede presentar desafíos. El diseño adecuado del molde puede ayudar a evitar problemas con los costos del molde, el calentamiento, los defectos de las piezas y el desmoldeo.
Materiales de herramientas de molde. Para elegir el material adecuado para una herramienta de termoformado, considere los materiales utilizados para la pieza final, ya que estos afectarán la temperatura requerida del molde (T molde ). Por ejemplo, siguiendo la regla de oro T mold =(T m + T g ) / 2 , una pieza hecha de PPS reforzado (sulfuro de polifenileno T m =280 ° C) requerirá un T molde de aproximadamente 180 ° C. (Los polímeros termoplásticos amorfos y semicristalinos tienen una T g , pero los polímeros semicristalinos también tienen una T m .) Por lo tanto, se requiere un molde de metal para conducir suficiente calor desde la platina de la prensa calentada o una herramienta calentada para moldear la pieza. La conducción también es necesaria para un enfriamiento eficiente de la pieza. Sin embargo, para una pieza fabricada con PMMA reforzado (polimetilmetacrilato), que tiene una T g mucho más baja (~ 100 ° C), una herramienta de madera o epoxi a temperatura ambiente puede ser suficiente.
Otras consideraciones incluyen la fase de desarrollo actual y el presupuesto disponible, pero también la cantidad de piezas que se fabricarán con la herramienta. Durante el procesamiento, las herramientas de molde están expuestas a fricción, alta temperatura y presión. Debido a que la madera y el epoxi tienen menor resistencia al calor y capacidad de carga en comparación con los metales, los moldes hechos con estos materiales tendrán una vida útil más corta y son más adecuados para la producción de pequeño volumen, mientras que las herramientas de metal serán las preferidas para la producción de alto volumen.
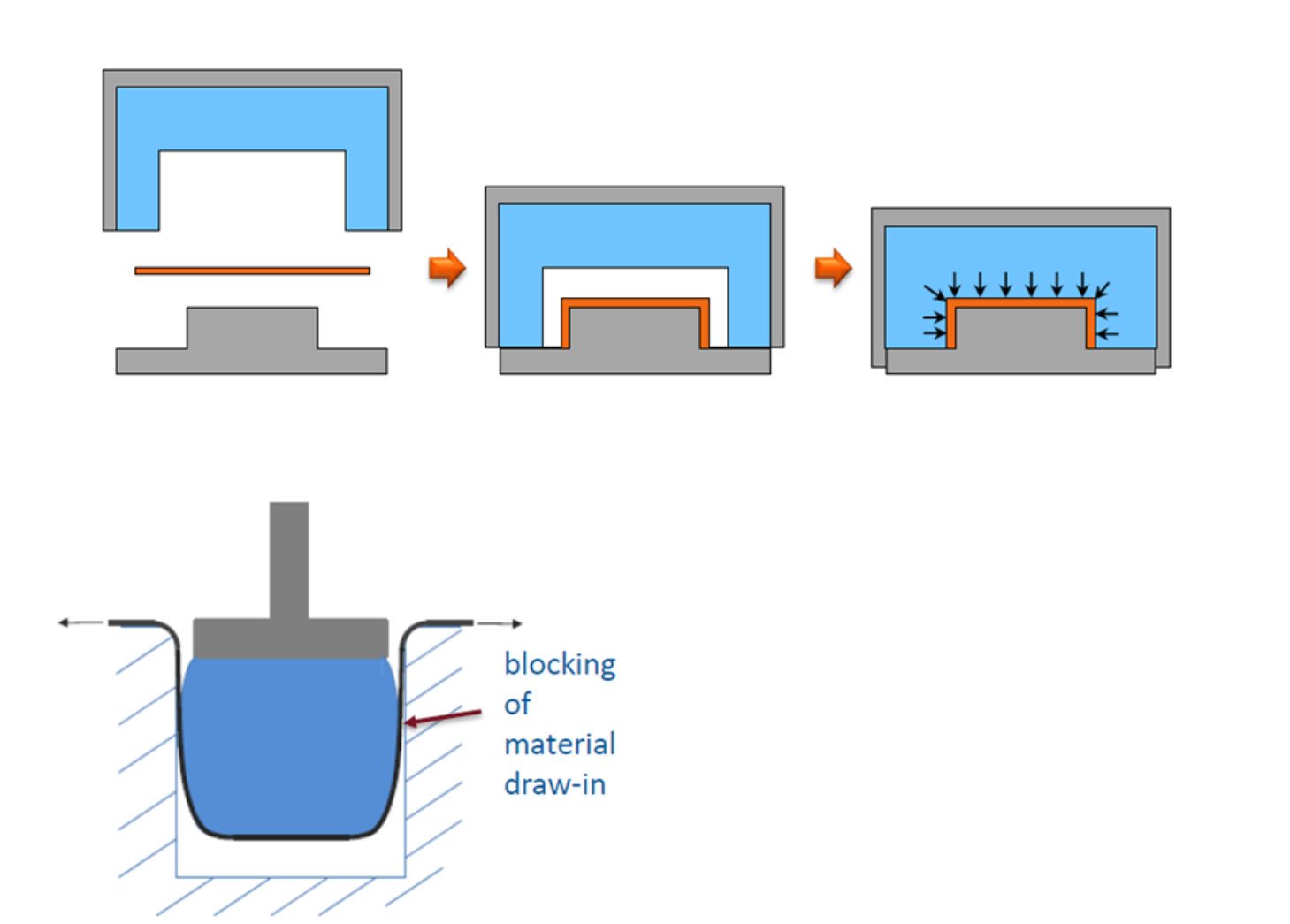
Otro sistema de materiales a tener en cuenta para las herramientas es el caucho de metal , donde la mitad de un conjunto combinado es de metal y la otra es de goma. Esto permite flexibilidad de producción y se puede utilizar para piezas con tolerancias mayores. Una herramienta de caucho y metal también proporciona una presión hidrostática uniforme, lo que es beneficioso en las áreas de las bridas y en los espacios en blanco con variaciones de espesor, típicos de los espacios en blanco hechos a medida hechos con múltiples capas UD.
Esta aplicación inherente de presión hidrostática también es una ventaja cuando la misma pieza se produce en múltiples espesores diferentes, eliminando el costo de moldes separados para cada espesor. Al diseñar una herramienta de caucho y metal, es importante considerar también las siguientes desventajas y desafíos:
- El lado metálico de la herramienta producirá un acabado más suave que el de goma.
- Las herramientas de metal y caucho tendrán un coeficiente de expansión térmica (CTE) de un orden de magnitud más alto que las herramientas totalmente metálicas.
- Debido a la menor conductividad térmica en comparación con el metal, el enfriamiento tomará un poco más de tiempo y creará un retraso mayor en la respuesta del control de temperatura.
- Un mayor desgaste y envejecimiento dará como resultado una vida útil más corta que las herramientas totalmente metálicas.
Conformado y desmoldeo. El diseño adecuado del molde garantiza una presión suficiente, un drapeado óptimo, ayuda a prevenir defectos y promueve la extracción segura de piezas. Aunque existen muchos problemas relacionados con el conformado y el desmoldeo, algunos de los más importantes incluyen:
- Presión. Durante el termoformado, la baja presión puede provocar una consolidación deficiente, propiedades mecánicas reducidas y dimensiones de la pieza fuera de tolerancia. Para una herramienta de metal-metal combinada, elimine los topes para que la presión continua sobre el laminado no se vea impedida por el espacio que crean los topes.
- Permitir la entrada de material . Para evitar la expansión del lado de goma del molde durante el prensado (conocido como barril), que puede bloquear el movimiento del material durante el prensado (extracción), coloque el caucho en el lado hembra de la herramienta de moldeo (ver Fig.3) .
- Eliminación de piezas . Para piezas en forma de L, diseñe el molde con el ángulo L deseado inclinado a una V, lo que reducirá la fricción con la herramienta y permitirá una fácil extracción de la pieza. Para piezas en forma de caja, use un ángulo de desmoldeo de 1-2 grados para cada lado; Es posible que se necesiten ángulos más altos para partes más profundas.
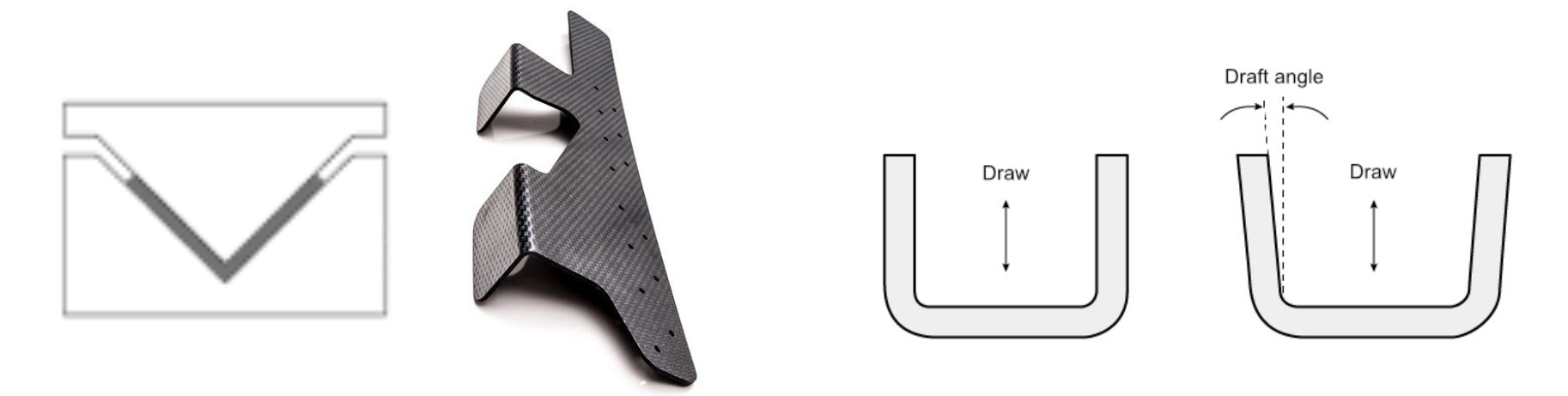
Deformación y resorte
La deformación y el resorte son distorsiones de la forma causadas por las propiedades anisotrópicas del material y el enfriamiento desigual de la resina que ocurren después de que la pieza está moldeada y pueden dar lugar a dimensiones de la pieza fuera de tolerancia, lo que podría dar lugar a problemas con el montaje y hacer que las piezas se desechen. El alabeo ocurre cuando una región de alta tensión de moldeado dentro de una pieza se cruza con una región de baja tensión de moldeado. Ese desequilibrio de tensión se alivia cuando la región de alta tensión distorsiona la región de baja tensión, lo que provoca que el laminado se arquee o se tuerza.
El resorte se produce en paneles curvos o en piezas con secciones de esquina cuando la tensión moldeada hace que las secciones de la pared se distorsionen hacia adentro en un ángulo menor que el ángulo diseñado. Esto sucede a menudo en compuestos reforzados con fibra debido a sus propiedades anisotrópicas. La geometría de la pieza también es un factor. La contracción diferencial entre el plano (CTE bajo en la dirección de la fibra) y el espesor pasante (CTE alto de la matriz) puede provocar una disminución del ángulo de 1-3 grados.
Abordar las distorsiones de forma puede resultar costoso y llevar mucho tiempo. Se recomienda encarecidamente utilizar herramientas de simulación y diseño para un desarrollo de piezas más rápido. Busque las siguientes causas posibles y soluciones al enfrentarse a la deformación:
- Parámetros de proceso . La temperatura del molde afecta las propiedades de espesor total asociadas con la cristalización y los efectos viscoelásticos, que pueden afectar el alabeo. La reducción de la temperatura del molde puede reducir el resorte pero aumentar las tensiones internas, lo que puede provocar el resorte una vez liberado. Esta incertidumbre debe examinarse cuidadosamente. La alta presión y la velocidad de formación también pueden reducir el resorte hacia adentro y posiblemente promover el problema opuesto, el retroceso elástico, al limitar el deslizamiento entre capas. Aumentar el tiempo de permanencia puede garantizar que la matriz se solidifique por completo y eliminar el calor residual, lo que reduce la contracción después de la extracción de la pieza y, por lo tanto, el resorte.
- Diseño de molde . La compensación por resorte se puede hacer cambiando los ángulos de las paredes en el molde. Además, como se mencionó anteriormente, los moldes de metal promueven un enfriamiento más uniforme y pueden ayudar a reducir el riesgo de deformación, especialmente en partes gruesas.
- Diseño. Las capas simétricas se utilizan comúnmente para mitigar el alabeo, pero durante el termoformado, puede ocurrir una reorientación de la fibra, lo que lleva a la asimetría y al alabeo. Otra manifestación de asimetría es la migración de resina durante la formación del radio (incluidas las esquinas). Esto provoca la redistribución de la fibra y cambios locales en la fracción de volumen de la fibra, lo que promueve la anisotropía y la deformación. Las diferentes capas y secuencias de capas se comportan de manera diferente a medida que las fibras responden a las tensiones que, a su vez, afectan el alabeo. Las herramientas de simulación y predicción pueden ayudar a abordar este complejo comportamiento del material.
Aunque el proceso de termoformado / estampado involucra múltiples parámetros y comportamientos materiales complejos, existen principios y acciones básicos que pueden guiar el desarrollo exitoso. Con la creciente implementación de piezas termoformadas de TPC, y en particular los espacios en blanco hechos a medida UD, se están abordando nuevos desafíos con soluciones innovadoras y herramientas de diseño / simulación mejoradas.
Resina
- Covestro intensifica la inversión en compuestos termoplásticos
- Reciclaje:compuestos termoplásticos reforzados con fibra continua con policarbonato reciclado
- Compuestos termoplásticos en Oribi Composites:CW Trending, episodio 4
- Compuestos termoplásticos:soporte de parachoques estructural
- Toray Advanced Composites expande las capacidades de los compuestos termoplásticos
- Teledyne CML Composites invierte en capacidad de procesamiento termoplástico
- ACMA lanza el programa Thermoplastic Composites Conference 2020
- Puerta termoplástica por primera vez para compuestos automotrices
- Compuestos termoplásticos:vista panorámica
- Vista previa de CAMX 2018:Compuestos avanzados de TenCate
- Soldadura de compuestos termoplásticos