larguero trasero VBO fuera de autoclave, varillas termoplásticas objetivo Wing of Tomorrow
Airbus (Toulouse, Francia) se encuentra en medio de un amplio esfuerzo para trabajar con fabricantes de aerocomposites en el desarrollo de estructuras fuera de autoclave (OOA) para el programa Wing of Tomorrow (WOT) de la compañía. Estas estructuras se entregarán a Airbus en 2021 y se ensamblarán en un ala de demostración que se probará y evaluará para su uso potencial en un avión de pasillo único de próxima generación. Se desconoce cuándo podría anunciarse un programa de este tipo, y es objeto de mucha especulación, pero toda la cadena de suministro de aerocomposites se está posicionando para ser parte de la próxima generación de fabricación de aviones, ya sea para Airbus o Boeing, o ambos.
CW ya ha informado sobre parte de esta actividad de WOT en historias sobre la piel del ala inferior producida por Spirit AeroSystems (Wichita, Kansas, EE. UU.), y las costillas termoplásticas producidas por GKN Aerospace (Hoogeveen, Países Bajos). Se une al esfuerzo de WOT el fabricante de aviones y proveedor de aeroestructuras Daher (París, Francia), que ha desarrollado, fabricado y entregado un larguero trasero OOA y cinco nervaduras termoplásticas para el programa.
“Daher se enorgullece de participar en este programa WOT. Este desarrollo confirma la posición de Daher como uno de los líderes mundiales en tecnologías termoplásticas y en estructuras de funciones integradas termoendurecidas, así como un socio fuerte para los fabricantes de aviones y un Nivel 1 para piezas complejas ”, dice Dominique Bailly, vicepresidente de I + D de Daher.
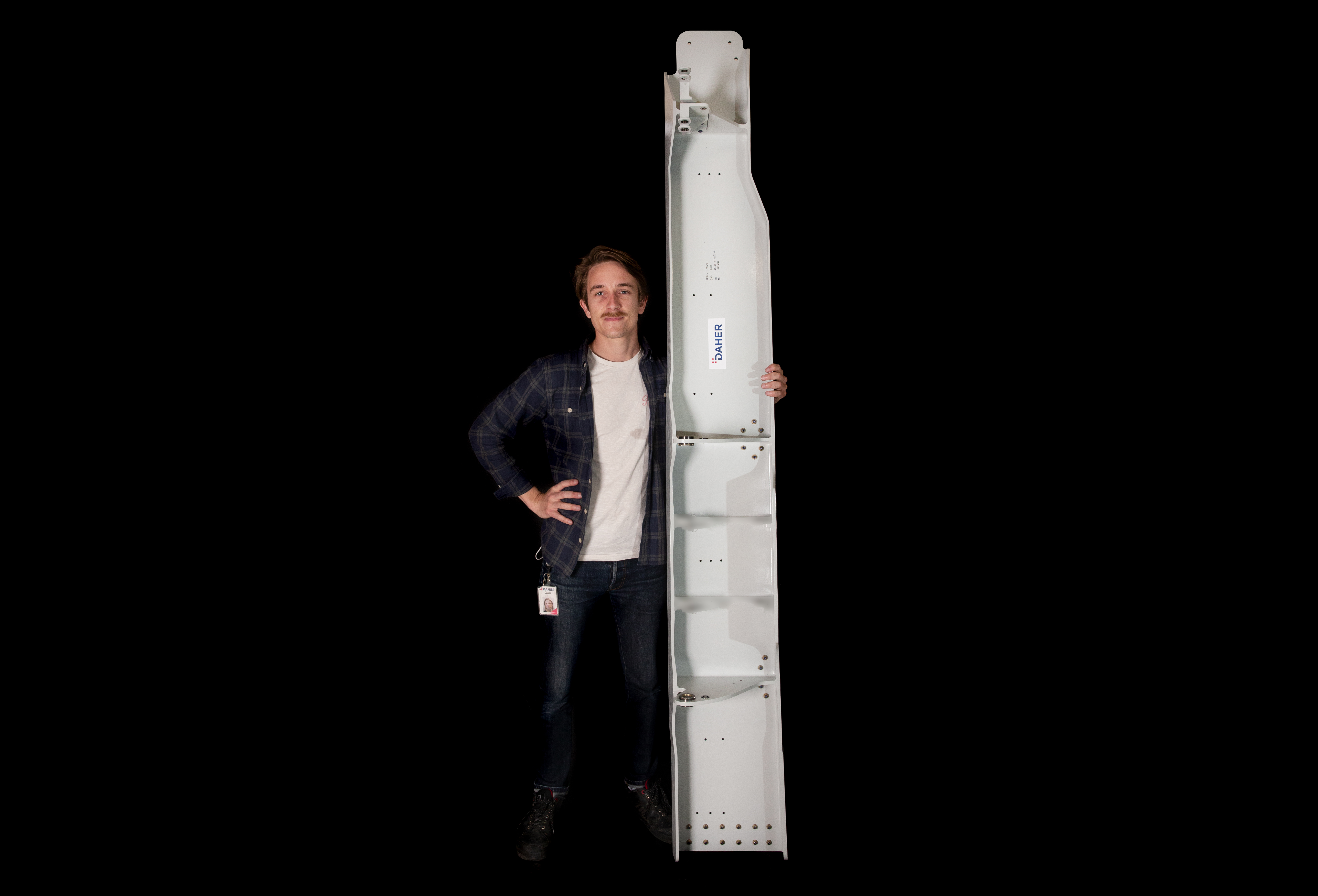
Mástil de alto rendimiento
El demostrador WOT, como cualquier ala de avión comercial, tiene varias estructuras de mástil. El larguero trasero desarrollado por Daher para WOT está fuera del tanque y el segundo más cercano de dos largueros inmediatamente adyacente al fuselaje, ubicado justo encima del tren de aterrizaje. Mide más de dos metros de largo y 10 milímetros de grosor, y debe cumplir con requisitos significativos de resistencia y rigidez:"unas pocas toneladas aplicadas en las características y varias decenas de toneladas para corte y tracción en la dirección del tramo", dice Bailly, dada su proximidad a el fuselaje y el sistema de tren de aterrizaje.
Además, dice Alexandre Condé, ingeniero jefe de Daher que trabajó en el mástil, Airbus buscaba el desarrollo de un proceso de fabricación altamente automatizado que permitiera a la compañía reducir el peso de los aviones y cumplir de manera rentable tasas de producción de aviones de 60 a 100 conjuntos de buques. por mes. Daher propuso un diseño capaz de reemplazar 15 componentes metálicos y sujetadores que eran originales del diseño de larguero compuesto de línea de base. "La idea era integrar la mayoría de las funciones para que sea rentable y ahorre peso", dice Condé.
La estructura del larguero resultante es un subproducto de un larguero termoestable OOA solo con bolsa de vacío (VBO) desarrollado por Daher en 2018 para un jet de negocios de Dassault Aviation (París, Francia). Bailly dice que el mástil de Dassault se fabricó con el preimpregnado a base de resina epoxi M56 de Hexcel (Stamford, Connecticut, EE. UU.), Curado con OOA VBO. Posteriormente, cuando Daher se involucró con el programa Airbus WOT, la compañía decidió adaptar el diseño, los procesos y la justificación del Dassault spar y aplicarlo a la nueva estructura de Airbus WOT, seleccionando el epoxi Hexcel M56 350 ° F curado OOA, preimpregnado en Tejido de fibra de carbono Hexcel AS4 y fibra de carbono IM7 UD.
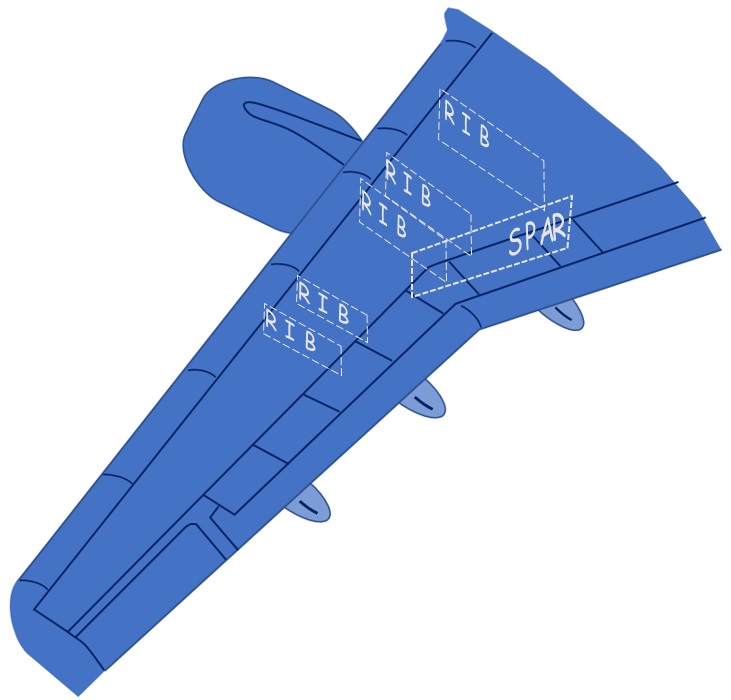
El proceso de fabricación utilizado para fabricar el larguero es la colocación automatizada de fibras (AFP) utilizando un sistema Coriolis Composites (Queven, Francia), que aplica material sobre un molde macho. El curado se realiza bajo bolsa de vacío en un horno. La parte resultante, dice Condé, tiene una porosidad del 0,1%.
Condé dice que el preimpregnado se eligió sobre el moldeado de resina líquida por la misma razón que el preimpregnado se ha convertido en un elemento básico de la fabricación aeroespacial durante los últimos 30 años:proporciona un volumen de resina / fibra consistente y confiable que permite la producción de piezas que tienen dimensiones consistentes y confiables. y misa. “Usando esta nueva generación de resina OOA con solo vacío, tiene una perfecta robustez en el contenido de fibra en el espesor del composite después del curado”, dice Condé. “Además, el peso de la pieza es muy estable porque no empuja la resina fuera de la fibra”.
Daher dice que fue el primer socio en entregar, a fines de 2020, un componente WOT (un spar para Airbus en Bristol, Reino Unido) para su integración en el primer demostrador WOT; la empresa está en proceso de entregar dos más. Más allá de esta fase de demostración, Daher también está pensando en la industrialización de la fabricación de largueros y está trabajando en un análisis de diseño de sistema de fabricación (MSD) que estima y simula las operaciones, las instalaciones, el equipo y los requisitos de personal para la producción a velocidad completa de un pasillo único de próxima generación. aeronave.
Varias costillas, varios tamaños
El esfuerzo de Daher para desarrollar costillas para el programa WOT ha sido más complejo y exigente. La empresa ha diseñado cinco nervaduras de distintos tamaños y dimensiones dentro del interior del ala; las otras nervaduras son una combinación de diseños de aluminio y compuestos, incluida una nervadura de compuesto termoplástico diseñado por GKN Aerospace.
En un proyecto anterior con Dassault Aviation, Daher había demostrado su capacidad para diseñar y fabricar nervaduras relativamente pequeñas a partir de compuestos termoplásticos, explica Bailly. Con WOT, la empresa ha tenido la oportunidad de ampliar sus habilidades hacia el desarrollo de costillas más grandes (~ 2 metros de largo) y de mayor carga.
Además, según los objetivos de WOT, Daher apunta a un nivel de preparación tecnológica (TRL) de 6 para fines de 2023. “Al final del programa WOT, cuando hayamos demostrado que estamos en TRL 6 para costillas grandes, entre estos dos programas [WOT y Dassault Aviation], habremos demostrado que podemos cubrir la porción completa de la nervadura del ala, esa es la idea ”, dice Bailly.
“Aprovechamos este programa para buscar diferentes formas de fabricar piezas y comparar comportamientos mecánicos, y también para observar el impacto en la fabricación. Paralelamente, estamos trabajando en la simulación para predecir el comportamiento de los componentes, como el efecto spring-back o el estampado. El objetivo es reducir los ensayos durante el desarrollo, por lo tanto, el costo no recurrente ”, dice Condé.
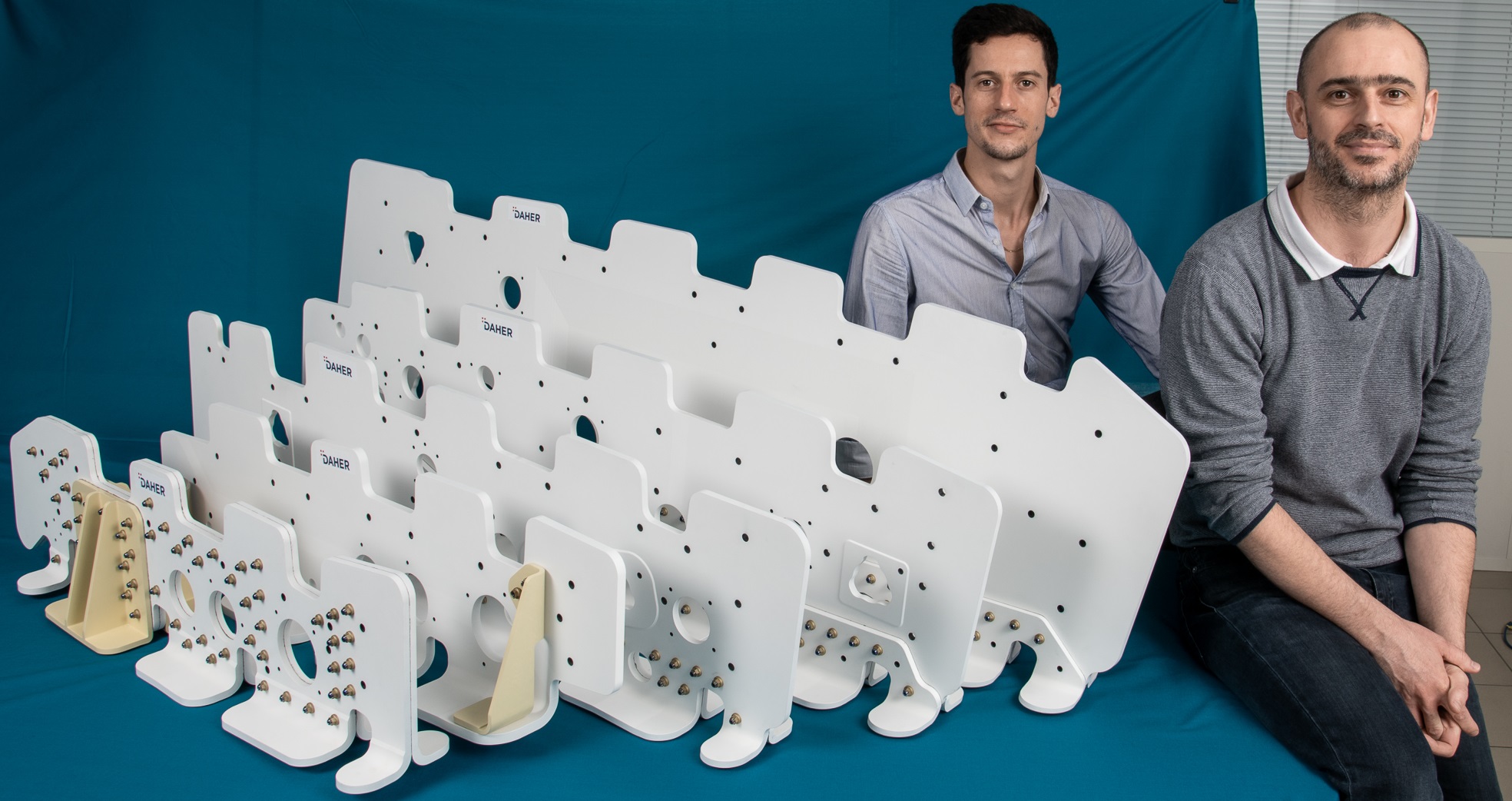
Al igual que el larguero, el desarrollo comenzó a nivel de cupón, elemento y detalle, seguido de la fabricación de piezas de subescala antes de que se construyeran las piezas finales de tamaño completo. Las pruebas se realizaron en cada nivel, señala Condé, incluidas las pruebas específicas desarrolladas por Daher para las características de las nervaduras.
Para las cinco nervaduras, Daher finalmente decidió utilizar cintas de fibra de carbono unidireccionales (UD) / poliariletercetona de bajo punto de fusión (PAEK) suministradas por Toray Advanced Composites (Morgan Hill, California, EE. UU.) Utilizando resina fabricada por Victrex (Cleveleys, Lancashire, Reino Unido). ). Para fabricar las nervaduras, se fabrican espacios en blanco planos utilizando AFP seguido de consolidación en horno; en algunos casos, los materiales se consolidan previamente antes de la formación del sello. Según sea necesario, bridas adicionales u otros componentes se sujetan mecánicamente a las piezas estampadas.
Cada costilla se diseñó de acuerdo con su posición a lo largo del ala, las especificaciones de tamaño y los requisitos de carga (de una tonelada a 50 toneladas), por lo que cada uno es único en varios aspectos. La nervadura más grande mide 2 metros de largo x 1 metro de ancho. Independientemente, cada uno comienza con una red plana, que se estampa en forma de "L" para crear un reborde a lo largo de la parte inferior de la pieza donde se conecta con la piel del ala. Para mayor estabilidad, varias de las nervaduras comprendían dos componentes en forma de "L" sujetados mecánicamente espalda con espalda para formar una forma de "T" con pestañas bidireccionales.
Las características especializadas incluyeron un soporte (fabricado a partir de compuestos termoendurecibles) para la conexión con la pista de la aleta unida a la nervadura, y una serie de orificios o caídas de capas en ciertas nervaduras para reducir el peso de la pieza.
“Durante todo el tiempo que estuvimos diseñando, tuvimos que gestionar la complejidad frente al costo”, dice Bailly. "Eso siempre estuvo en nuestra mente, hacer algo simple pero rentable". La simplicidad también fue clave desde la perspectiva de la tasa de producción, señala Condé. "Si es demasiado complejo, no será competitivo desde el punto de vista del cliente, con las tasas muy altas que quieren tener".
Un desafío que introdujo complejidad en el diseño fue el grosor relativo de cada una de las nervaduras, hasta 12 milímetros para la nervadura más grande. Las telas más gruesas tienden a arrugarse o formarse incorrectamente cuando se estampa, y las piezas más gruesas pueden ser difíciles de mecanizar en la forma final.
Para el mecanizado, Daher utilizó una combinación de corte por chorro de agua y mecanizado mecánico según las necesidades de la pieza, tanto para mitigar los problemas en el grosor de la pieza como para controlar la temperatura. Además, en la nervadura de 12 milímetros de espesor, el equipo diseñó una ventana de caída de capas en el medio del componente para reducir el peso total de la pieza. Además de resolver estos posibles problemas, Condé señala que la ventana de caída de capas también permitió a Daher "probar diferentes tipos de funciones de fabricación en las piezas, para aumentar nuestra comprensión del comportamiento de las piezas".
El proceso de formación de sellos resultó ser un desafío aún mayor. “Tuvimos que imaginar una nueva forma de estampar para mitigar el riesgo de arrugas”, dice Bailly. Daher finalmente desarrolló un método patentado para resolver el problema.
Pasos siguientes
Más allá de WOT, Daher está evaluando métodos de fabricación alternativos para producir nervaduras termoplásticas, mientras hace planes para desarrollar una línea de producción completa para la fabricación de alta velocidad en el futuro.
Por ejemplo, mientras que los demostradores de WOT usan sujetadores, Bailly señala que a través de su adquisición en 2019 de compuestos termoplásticos y el especialista en soldadura por inducción KVE Composites (La Haya, Países Bajos), Daher posee la capacidad para componentes soldados en el futuro. "Estamos trabajando en otro proyecto independiente para alcanzar un nivel de TRL más alto en la soldadura de piezas gruesas UD [para su uso en aviones de pasillo único de próxima generación]", dice.
Daher también está trabajando en el desarrollo de una línea de producción completa para producir nervaduras termoplásticas en el futuro. "Realmente estamos mejorando el concepto y reduciendo la cantidad de máquinas necesarias para todas las tareas y reduciendo los costos del proceso", dice Bailly, con el objetivo de alcanzar los objetivos de producción de aviones de gran volumen.
Resina
- Covestro intensifica la inversión en compuestos termoplásticos
- Lanzamiento de masterbatches termoplásticos reforzados con grafeno
- Solvay expande la capacidad de compuestos termoplásticos
- Compuestos termoplásticos en Oribi Composites:CW Trending, episodio 4
- Suprem expande las capacidades termoplásticas
- Solución de problemas de termoformado de compuestos termoplásticos
- Kordsa expande la línea de productos preimpregnados termoplásticos
- Compuestos termoplásticos LANXESS utilizados en la carcasa del asiento trasero del Audi A8
- Tecnología de producción de paneles de nido de abeja termoplásticos EconCore
- Compuestos termoplásticos:vista panorámica
- Soldadura de compuestos termoplásticos