Fabricación de chips de nanofluidos de polidimetilsiloxano bajo el proceso de nanomolienda basado en puntas AFM
Resumen
En el ámbito de la investigación actual, los dispositivos nanofluídicos basados en polidimetilsiloxano (PDMS) se utilizan ampliamente en aplicaciones médicas, químicas y biológicas. En el presente artículo, se propuso una nueva técnica de nanomolinado (que consta de un sistema AFM y un actuador piezoeléctrico) para fabricar nanocanales (con tamaños controlables) en chips PDMS, y el tamaño del nanocanal se controló mediante el voltaje de conducción y la frecuencia introducida en el actuador piezoeléctrico. . Además, se fabricaron moldes de microcanales y nanocanales, respectivamente, mediante litografía UV y nanomolinado basado en puntas AFM, y finalmente, se obtuvieron placas de PDMS con micro / nanocanales mediante proceso de transferencia. También se investigaron las influencias de la relación en peso de PDMS sobre el tamaño del nanocanal. El proceso de unión de losas de microcanales y nanocanales se llevó a cabo en un sistema de alineación casero que consistió en un microscopio óptico monocular y etapas de precisión. Además, se analizaron los efectos del tamaño del nanocanal sobre las características eléctricas de la solución de KCl (concentración de 1 mM). Por lo tanto, se puede concluir que los dispositivos nanofluídicos PDMS con múltiples nanocanales de profundidad por debajo de los 100 nm pueden fabricarse de manera eficiente y económica mediante el método propuesto.
Antecedentes
Debido a su considerable potencial en los campos químico, médico y biológico, los sistemas micro / nanofluídicos se utilizan ampliamente en el análisis de ADN [1, 2, 3, 4], la separación celular [5], la investigación de proteínas [6, 7, 8], seguridad alimentaria [9] y vigilancia medioambiental [10]. Con el rápido desarrollo de la tecnología de nanofabricación, la demanda de dispositivos nanofluídicos con un tamaño unidimensional inferior a 100 nm aumenta continuamente [11]. Los chips de nanofluidos también se pueden utilizar eficazmente para la detección de virus [12], la manipulación de nanopartículas [13] y el estudio de la difusión de iones [14]. Sin embargo, la eficacia de detección y la sensibilidad de los chips de nanofluidos dependen de las dimensiones de las características y la distribución de los nanocanales. Es indispensable controlar con precisión las dimensiones de las características de los nanocanales para la detección sin etiquetas basada en nanofluidos. Cómo fabricar nanocanales con dimensiones y distribución de características controlables sigue siendo un desafío para la aplicación en el campo de los nanofluidos.
Hasta ahora, existen varios métodos que se pueden utilizar para la fabricación de chips de nanofluidos. El grabado con iones reactivos [15], la fotolitografía convencional [16], el procesamiento de haz de alta energía [17], la litografía de interferencia [18], la nanoimpresión [19] y las tecnologías de estampado en caliente [20, 21] son las más utilizadas para la fabricación de dispositivos nanofluídicos; sin embargo, todos estos métodos manifiestan sus propias limitaciones. El grabado con iones reactivos y la fotolitografía convencional son los métodos principales para la fabricación de canales de micro / nanofluidos. Sin embargo, las dimensiones laterales de los canales fabricados dependen de la longitud de onda de la luz incidente, por lo que los anchos de los canales producidos se encuentran a menudo en la escala micrométrica, no en nanoescala [22]. Además, es inconveniente cambiar las fotomáscaras cuando se fabrican micro / nanoestructuras que tienen características diferentes. La litografía de haz de iones enfocado (FIB) y la litografía de haz de electrones (EBL) son métodos de procesamiento de haz de alta energía, que pueden fabricar fácilmente un chip nanofluídico de alta precisión con nanocanales de menos de 100 nm. Sin embargo, la inversión para la instalación de fabricación es extremadamente alta y se requieren estrictos requisitos medioambientales [23]. La litografía de interferencia (IL) es adecuada para fabricar estructuras periódicas simples en un área grande; sin embargo, no es adecuado mecanizar un solo nanocanal [24, 25]. La resolución de procesamiento de la nanoimpresión depende de las propiedades de la plantilla, la cuestión crucial para este enfoque es cómo fabricar la plantilla con nanoestructuras de alta precisión [26]. Además, el moldeo de sacrificio y el método basado en crujidos también se adoptan para fabricar dispositivos a micro / nanoescala [27, 28]; sin embargo, el control preciso del tamaño del nanocanal es muy difícil en estos enfoques. Por lo tanto, se requiere un enfoque de fabricación más factible con las propiedades de alta precisión de mecanizado, facilidad de uso, amplio rango de procesamiento y requisitos ambientales bajos para la fabricación de dispositivos nanofluídicos.
En los últimos años, debido a su alta precisión de mecanizado, los métodos de mecanizado de ultraprecisión, como el nanofresado, el rectificado de precisión y el torneado de ultraprecisión, se utilizan ampliamente en la fabricación de micro / nanoestructuras [29,30,31,32]. Además, desde la invención del microscopio de fuerza atómica (AFM) en 1986, la nanofabricación basada en la punta de AFM es un método poderoso para preparar nanoestructuras [33]. El nano-rayado tradicional basado en puntas posee algunas limitaciones, como un ancho de mecanizado limitado y una baja eficiencia de fabricación. El ancho del nanocanal fabricado por este enfoque depende de la geometría de la punta AFM, lo que significa los nanocanales con ancho controlable que son inaccesibles. Además, la eficiencia de fabricación del proceso de nano-rayado tradicional basado en puntas es relativamente baja, especialmente para el caso de emplear una alimentación en el proceso de mecanizado para ampliar la profundidad y el ancho de la nanoestructura obtenida. Debido a sus importantes ventajas, como el tamaño de mecanizado controlable y la alta eficiencia de fabricación, el nanomolinado basado en puntas se adopta ampliamente para fabricar nanocanales. Gozen y col. [34, 35] fabricaron nanoestructuras en polimetilmetacrilato (PMMA) mediante un proceso de nanofresado. Zhang y col. [36,37,38] prepararon nanoestructuras tridimensionales utilizando AFM y estudiaron los efectos de diferentes parámetros de mecanizado. Park y col. [39] investigó el mecanismo del proceso de nanomáquina y encontró que las intensidades de la fuerza de corte se redujeron significativamente; sin embargo, en el sistema propuesto, se encontró que las instalaciones de mecanizado eran relativamente complicadas y el proceso de eliminación de material no se investigó en detalle. No se estudió la relación entre los parámetros de mecanizado, incluida la frecuencia de conducción y el voltaje, y las dimensiones características del nanocanal obtenido. Además, su trabajo no se centró en la aplicación de los nanocanales fabricados. Por lo tanto, se necesita más trabajo para explorar el alcance de la aplicación de este enfoque de nanomolinado basado en puntas AFM. El policarbonato (PC), debido a su excelente maquinabilidad, se usa comúnmente para la nanofabricación [40]; sin embargo, rara vez se selecciona para fabricar chips de nanofluidos. Por el contrario, el polidimetilsiloxano (PDMS) se usa ampliamente para procesar chips de microfluidos y nanofluidos. Mata y col. [41] estudiaron las influencias de la relación de peso del PDMS sobre la tensión de tracción. Park y col. [42] desarrolló un nuevo método para mejorar la rigidez de PDMS. Las aplicaciones de los chips de nanofluidos en el campo de prueba sin etiquetas dependen principalmente de la conductividad eléctrica de los nanocanales [43], por lo que los resultados de la medición a menudo se ven afectados por los tamaños dimensionales de los nanocanales [44].
Por lo tanto, con el fin de superar las desventajas del proceso de raspado tradicional basado en puntas, se emplea el enfoque de nanomilling para llevar a cabo el proceso de fabricación del nanocanal en este estudio. Además, se seleccionó la lámina de PC como muestra experimental para mitigar el desgaste de la punta y reducir el costo de fabricación. Además, el tamaño del nanocanal en la hoja de PC se controlaba mediante el voltaje de activación y la frecuencia introducida en el actuador piezoeléctrico. También se investigaron las influencias de la relación en peso de PDMS sobre el tamaño del nanocanal. Además, para verificar los efectos de diferentes tamaños dimensionales sobre la conductividad eléctrica de los nanocanales, la prueba de medición de corriente se realizó utilizando una solución de KCl.
Métodos
Configuración del sistema de nanomolienda
El sistema de nanomolienda basado en puntas de AFM propuesto consistía en un AFM comercial (Dimension Icon, Bruker Company, Alemania) y un actuador piezoeléctrico (P-122.01, PI Company, Alemania) (Fig. 1a). Los rangos de recorrido del actuador piezoeléctrico en las direcciones x e y se limitaron a 1 μm. Además, el actuador piezoeléctrico fue impulsado por señales sinusoides con voltajes apropiados (generados a partir de un dispositivo generador de señal comercial (AFG1022; Tektronix, Inc., EE. UU.)) Bajo la amplificación de un amplificador de señal (PZD350A; TREK, Inc., EE. UU.). Se fijó una hoja de PC en el soporte casero (hecho de resina epoxi) mediante un tornillo de fijación. La operación de nanomáquina se realizó utilizando una punta piramidal rectangular recubierta de diamante de 100 nm de espesor (DT-NCLR, Nanosensors, Suiza). El voladizo de la punta (constante de resorte normal de 68 N / m) estaba hecho de silicio (Fig.1b), y se empleó una punta de silicona (radio de 10 nm) (TESPA, Bruker Company, Alemania) para medir las ranuras después mecanizado.
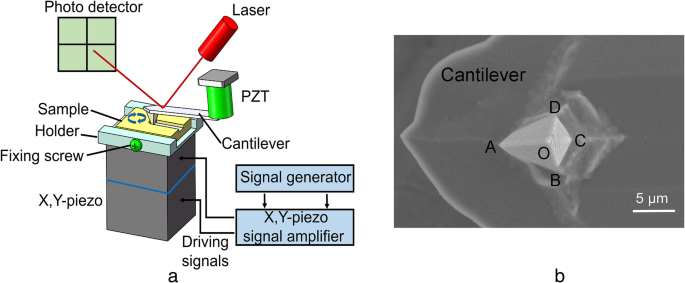
un Diagrama esquemático del sistema de nanomilling. b Micrografía SEM de punta AFM recubierta de diamante
Fabricación de moldes de nanocanales y microcanales
La ruta de fabricación de nanocanales en un chip PDMS se muestra en la Fig. 2. El sistema AFM y el actuador piezoeléctrico se emplearon para fabricar moldes de nanocanales (con tamaños controlables) en hojas de PC. La hoja de PC (peso molecular de 35.000) de tamaño de 15 mm x 12 mm x 1 mm se adquirió de Goodfellow. La media y la desviación estándar de la rugosidad de la superficie (Ra) de la hoja de PC se midieron como 0,6 nm y 0,2 nm, respectivamente (estos valores se obtuvieron escaneando un área de 50 μm × 50 μm de la muestra en el modo de roscado AFM). Para generar un movimiento circular, el actuador piezoeléctrico fue impulsado por señales sinusoides con una diferencia de fase de 90 ° en las direcciones xe y. Los anchos de los nanocanales mecanizados dependían de la amplitud del movimiento circular generado. El rango del voltaje de excitación introducido en el actuador piezoeléctrico se estableció de 30 V a 150 V con una separación de 30 V y, además, se seleccionaron dos frecuencias de buceo de 100 Hz y 1500 Hz. Durante el mecanizado a lo largo de la dirección del borde hacia adelante, los materiales se expulsan en formación de apilamiento y, a menudo, se encuentran distribuidos uniformemente en ambos lados de un nanocanal [45], y ayuda a evitar cualquier fuga de virutas de nanofluidos durante el proceso de unión; por lo tanto, en el presente estudio se seleccionó la dirección de mecanizado de borde hacia adelante. Se fabricaron nanocanales de 80 μm de longitud utilizando el módulo Nanoman del sistema AFM. Cualquier proceso de mecanizado se ve afectado por el valor de avance; por lo tanto, para eliminar esta influencia, la velocidad de alimentación debe variarse con la frecuencia de conducción. En el presente estudio, el valor de alimentación se estableció en 10 nm y las velocidades de alimentación para las frecuencias de 100 Hz y 1500 Hz se calcularon como 1 μm / sy 15 μm / s, respectivamente. La carga normal de la punta dependía del voltaje de salida generado por el fotodetector sensible a la posición (PSD); por lo tanto, las diferentes cargas normales utilizadas en nuestro estudio se lograron estableciendo un voltaje relativo (punto de ajuste). De acuerdo con nuestro trabajo anterior [46], la carga normal de mecanizado se calculó mediante la Ec. (1) y la sensibilidad se midió a partir de la pendiente de la curva fuerza-distancia obtenida [47].
$$ {F} _ {\ mathrm {N}} ={V} _ {\ mathrm {setpoint}} \ times sensitividad \ times {K} _ {\ mathrm {N}} $$ (1)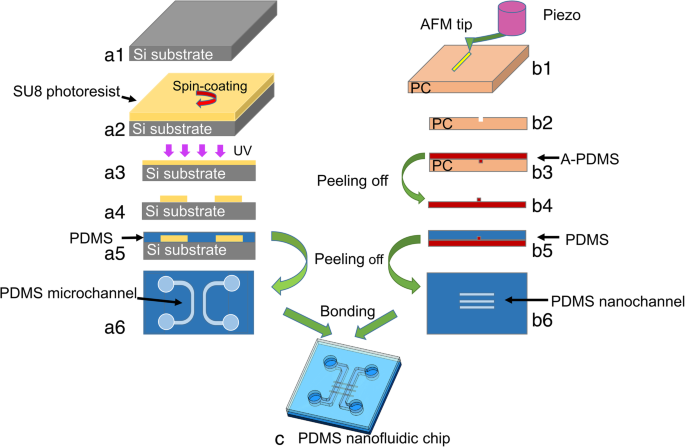
Diagrama de flujo de fabricación de chips de nanofluidos:(a1) - (a6) Pasos de trabajo de fabricación de microcanales en un chip PDMS; (a1) Lámina de silicio utilizada como sustrato de litografía; (a2) Recubrimiento por centrifugación de fotorresistente SU8 sobre sustrato de Si; (a3) Exposición de la capa SU8 a la luz ultravioleta; (a4) Microestructuras convexas obtenidas; (a5) revestimiento de PDMS en molde de microcanal; (a6) Chip PDMS final con microcanales; (b1) - (b2) Pasos de trabajo de fabricación de nanocanales en un chip PDMS; (b1) La punta del AFM está rayada en la hoja de PC; (b2) Molde de nanocanales obtenido después de rayar; (b3) Recubrimiento de A-PDMS en molde de nanocanales; (b4) chip A-PDMS con nanoestructuras convexas; (b5) Recubrimiento regular de PDMS en molde A-PDMS; (b6) Chip PDMS final con nanocanales; (c) Chip de nanofluidos de PDMS después de la unión
Por lo tanto, las cargas normales para el proceso de nanofresado se establecieron en 17 μN y 25 μN. Además, a modo de comparación, los moldes de nanocanales en láminas de PC también se fabricaron sin vibración, este método se llama rayado simple. Las cargas normales para el proceso de raspado simple se establecieron en 25 μN, 33 μN, 42 μN, 50 μN y 58 μN. El diagrama esquemático de la sección transversal del molde nanocanal se muestra en la Fig. 2 (b2).
Los moldes de microcanales se prepararon mediante un proceso de litografía UV. El diagrama de flujo de la Fig. 2 (a1-a4) muestra los detalles de la operación del proceso de litografía. La fotorresistencia (SU-82015; MicroChem, EE. UU.) Se revistió por rotación sobre un sustrato de Si a 500 rps durante 30 sy a 4000 rps durante 120 s. Un par de microcanales en forma de “U” formaron el chip de microcanal (Fig. 2 (a6)), que fue puenteado por nanocanales para formar el chip nanofluídico final. El ancho del microcanal era de 30 µm y el diámetro del depósito era de 1 mm. Además, la distancia entre dos microcanales en forma de "U" era de 50 μm (Archivo adicional 1:Figuras S1 y S2).
Impresión por transferencia de microcanales y nanocanales
El molde de microcanal convexo (Fig. 2 (a4)) y el molde de nanocanal cóncavo (Fig. 2 (b2)) se transfirieron mediante PDMS (Sylgard 184, Dow Corining, EE. UU.) Para preparar el chip nanofluídico final. La Figura 2 (b3) - (b6) presenta el proceso tecnológico de transferencia de moldes de nanocanales, que constaba de dos pasos:primera transferencia y segunda transferencia. Para investigar los efectos de la relación en peso de monómero a agente de curado sobre el tamaño del nanocanal, se emplearon tres relaciones de peso de PDMS diferentes (A-PDMS) durante el primer y segundo proceso de transferencia. Las proporciones de peso de PDMS para el primer proceso de impresión por transferencia se establecieron en 9:1, 7:1 y 5:1, mientras que los valores para la segunda transferencia se establecieron en 10:1, 9:1 y 8:1. La Figura 2 (a5) y (a6) muestra el proceso de transferencia del molde de microcanal utilizando el enfoque de transferencia de un solo paso. Se utilizó la relación en peso PDMS de 10:1 para la transferencia de microcanal convexo. Durante todos los procesos de impresión por transferencia, primero se agitó uniformemente el elastómero PDMS de dos componentes y luego se vertió en una caja para preparar el molde. A continuación, el estuche se mantuvo en un desecador de vacío durante 30 min y se desgasificó de 2 a 3 veces para eliminar todas las burbujas de aire atrapadas. El molde preparado se mantuvo en un horno de calentamiento a 80 ° C durante 4 h, y finalmente, la réplica de PDMS se despegó suavemente del molde.
Unión de chips
Los chips nanofluídicos preparados se unieron mediante tratamiento con plasma de oxígeno (Zepto, Diener electronic, Alemania) durante 32 s bajo una presión de cámara de 1,5 mbar y una potencia de cámara de 81 W (Fig. 2 (c)). Las superficies de microcanales y nanocanales se limpiaron con cintas adhesivas, y los cuatro depósitos en chips de microcanales PDMS se perforaron antes de la unión. Se utilizó agua desionizada para mantener los chips limpios después del tratamiento con plasma, y los chips se mantuvieron alineados mediante un sistema de alineación casero que consistía en un soporte, un microscopio monocular y una platina de precisión unidimensional (TSDT-401S; SIGMAKOKI, Japón ) (Figura 3a). Los detalles del sistema de alineación casero se pueden encontrar en el ESI. Luego, los chips se unieron a una temperatura de 95 ° C durante 20 min para obtener un chip micro / nanocanal cerrado (Fig. 3b).
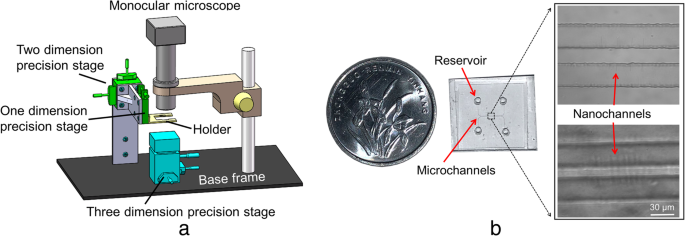
un Diagrama esquemático del sistema de alineación casero y b chip de nanofluidos
Resultados y discusión
Trayectoria rotatoria del actuador piezoeléctrico
El actuador piezoeléctrico bidimensional es un componente crítico para realizar el movimiento giratorio en un sistema de nanomolienda basado en puntas AFM. Por lo tanto, para caracterizar sus movimientos bajo un rango de tensiones y frecuencias de excitación, se llevaron a cabo pruebas preliminares de rayado. Bajo el modelo de contacto con un rango de escaneo de 0 nm, la punta AFM primero se acercó a la superficie de la hoja de PC bajo una carga normal dada y se mantuvo estática. La rotación del actuador piezoeléctrico bidimensional fue controlada por una frecuencia y voltaje preestablecidos. Después de completar el proceso de rayado, la punta de AFM se levantó de la superficie de la hoja de PC. Por tanto, la amplitud de movimiento del actuador piezoeléctrico se obtuvo en función de la tensión y la frecuencia de activación. Los voltajes de activación se establecieron en el rango de 30-150 V con un espaciado de 30 V, mientras que las frecuencias de activación se establecieron en 100 Hz y 1500 Hz. La relación entre las amplitudes medidas y los voltajes de conducción a dos frecuencias de conducción se muestra en el archivo adicional 1:Figura S3. Es evidente que los valores de amplitud de mecanizado aumentaron con los voltajes de excitación crecientes, y el valor de amplitud de mecanizado a 1500 Hz fue mayor que el de 100 Hz. Se encontró que los anchos del nanocanal fabricado por nuestro método propuesto variaban de 350 nm a 690 nm.
Fabricación de moldes de nanocanales en hoja de PC
Las relaciones entre el tamaño del nanocanal y los parámetros de mecanizado bajo rayado simple y nanomolienda se presentan en la Fig. 4a yb, respectivamente. Los anchos y las profundidades de los nanocanales mecanizados están representados por W 0 y D 0 , respectivamente (Fig. 5a).
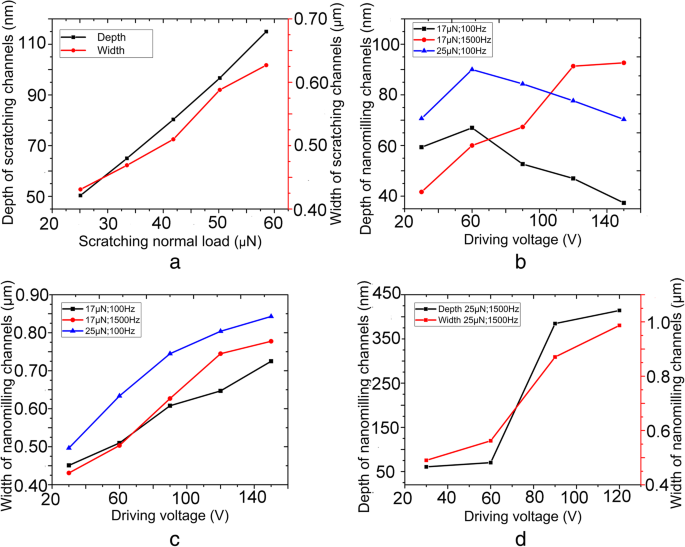
Relación entre el tamaño del nanocanal mecanizado y los parámetros de mecanizado: a rayado simple con cargas normales que oscilan entre 25 μN y 58 μN, b profundidad y c ancho de los canales mecanizados cuando se fabrican con cargas normales de 17 μN, 25 μN y frecuencias de activación de 100 Hz, 150 Hz, d la profundidad y el ancho de los canales mecanizados cuando se fabrican con una carga normal de 25 μN y una frecuencia de conducción de 1500 Hz
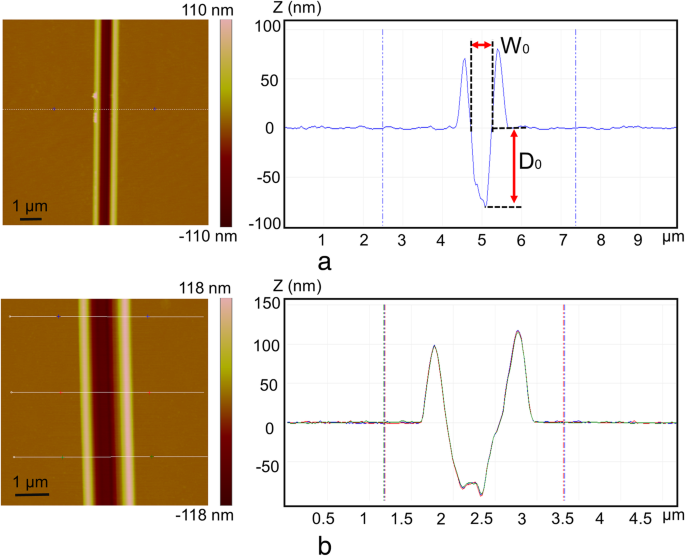
Imágenes AFM típicas del nanocanal mecanizado con diferentes parámetros de mecanizado: a Rayado bajo una carga normal de 42 μN. b Nanomilling con una carga normal de 25 μN, una frecuencia de 100 Hz y una tensión de conducción de 60 V
Se puede observar en la Fig. 4a que los anchos y las profundidades de los nanocanales fabricados aumentaron con el aumento de las cargas normales. La imagen AFM típica de rascarse bajo una carga normal de 42 μN se muestra en la Fig. 5a. Se nota que los materiales fueron expulsados del nanocanal para formar acumulaciones, que se distribuyeron uniformemente en ambos lados del nanocanal. Porque la forma de la punta AFM es simétrica a la superficie que fue formada por el borde "OA" durante el proceso de mecanizado (Fig. 1b). Por lo tanto, los materiales fueron expulsados uniformemente por el borde frontal de la punta durante el rascado del borde hacia adelante. Las figuras 4b, cyd ilustran la relación entre el tamaño del nanocanal mecanizado y el voltaje de activación. Es evidente en la Fig. 4b que la profundidad del nanocanal aumentó al principio y luego comenzó a disminuir bajo una frecuencia de 100 Hz con cargas normales de 17 μN y 25 μN. La hoja de PC utilizada en nuestro estudio fue un polímero amorfo, que presenta un comportamiento elástico-viscoplástico en combinación con un endurecimiento por deformación exponencial a niveles de deformación elevados [48, 49]. La carga normal durante el mecanizado se calculó mediante la Ec. (2), donde \ (\ overrightarrow {n} \) y \ (\ overrightarrow {t} \) son la unidad normal y la unidad tangente al vector de línea de flujo, respectivamente, p y τ significa presión local normal y esfuerzo cortante, respectivamente, y \ (\ overrightarrow {z} \) es la unidad vertical [50].
$$ {F} _ {\ mathrm {N}} =p \ cdot \ int \ overrightarrow {n} \ cdot \ overrightarrow {z} ds- \ tau \ cdot \ int \ overrightarrow {t} \ cdot \ overrightarrow {zds } $$ (2)En el presente estudio, los tamaños dimensionales de los nanocanales fabricados se encontraron a nanoescala, por lo que los valores de la presión normal local y el esfuerzo cortante se asumieron constantes. Además, Eq. (2) se convirtió a la forma simplificada de la ecuación. (3), donde S n y S h respectivamente son las proyecciones horizontal y vertical de la interfaz entre la punta AFM y la muestra.
$$ {F} _ {\ mathrm {N}} =p \ cdot {S} _n- \ tau \ cdot {S} _h $$ (3)La relación entre S n y S h se expresa en Eq. (4), donde α y β respectivamente son los ángulos incluidos entre la superficie de la punta y los planos vertical y horizontal.
$$ {S} _ {\ mathrm {n}} =\ frac {S _ {\ mathrm {h}}} {\ cos \ alpha} \ cdot \ cos \ beta $$ (4)La carga normal se calculó mediante la ecuación. (5).
$$ {F} _ {\ mathrm {N}} =\ left (p \ cdot \ frac {\ cos \ beta} {\ cos \ alpha} - \ tau \ right) \ cdot {S} _h $$ (5 )Es evidente a partir de la ecuación. (1) que los valores de carga normal fueron constantes durante todo el proceso de mecanizado. Según Briscoe et al. [51], el valor de la tasa de deformación media se calculó mediante la ecuación. (6), donde V y w significan la velocidad de la punta y el grosor de la viruta sin cortar, respectivamente. El valor máximo de espesor de viruta sin cortar se encontró en ~ 10 nm.
$$ {} _ {\ varepsilon} ^ {\ bullet} =\ frac {\ mathrm {d} \ varepsilon} {\ mathrm {d} t} \ approx \ frac {V} {w} $$ (6)Además, los valores de la velocidad punta se obtuvieron de la ecuación. (7), donde f es la frecuencia de la señal de entrada.
$$ V =\ pi \ cdot {W} _o \ cdot f $$ (7)Los valores de la tasa de deformación media a 100 Hz se encontraron en el rango de 1,42 × 10 4 s -1 ~ 2,27 × 10 4 s -1 . Los valores de la presión normal local ( p ) comenzó a aumentar con el aumento de las tasas de deformación cuando las tasas de deformación oscilaban entre 1,42 × 10 4 s -1 hasta 2,27 × 10 4 s -1 [52]. El valor de τ era mucho más pequeño que el de p , significa que la carga normal dependía principalmente de p . Por tanto, para mantener los valores de carga normal (F N ) constante durante todo el proceso de mecanizado, los valores de la profundidad de mecanizado deben ser menores a tensiones de accionamiento mayores. Sin embargo, el tamaño dimensional final del nanocanal fabricado se vio afectado por la recuperación del material de muestra. La recuperación de la muestra disminuyó con el aumento de las velocidades de mecanizado en el rango de 142 ~ 227 μm / s [53]:por lo tanto, indica que se produjo una mayor recuperación elástica a 30 V. En consecuencia, la profundidad del nanocanal fabricado a 30 V (~ 142 μm / s) fue menos profundo que el de 60 V (~ 161 μm / s). Archivo adicional 1:La Figura S4 (a) y la Fig. 5b son las imágenes AFM típicas del nanocanal mecanizado a 100 Hz bajo cargas normales de 17 μN y 25 μN, respectivamente. Es obvio que el amontonamiento en el lado derecho del nanocanal es más grande que el izquierdo. El movimiento rotatorio de la muestra durante el proceso de nanofresado es en sentido antihorario y el ángulo de corte del filo principal cambia con la rotación. El grosor de la viruta sin cortar es demasiado pequeño para formar virutas al principio y al final de un ciclo de proceso de nanofresado. El grosor de la viruta sin cortar en medio de un ciclo de proceso de nanofresado es relativamente grande; sin embargo, el pequeño ángulo de ataque contribuye a la formación de choques. Por lo tanto, se empujan más materiales hacia el lado derecho del canal y los amontonamientos son asimétricos . Los detalles de la formación de amontonamientos asimétricos se pueden encontrar en nuestro estudio anterior [54].
Se puede observar en la Fig. 4b yd que la profundidad del nanocanal comenzó a aumentar con los voltajes de excitación crecientes a 1500 Hz bajo cargas normales de 17 μN y 25 μN. La Figura 4d muestra que la profundidad del nanocanal aumentó bruscamente de 60 V (~ 2.64 mm / s) a 90 V (~ 4.10 mm / s) bajo una carga normal de 25 μN. Según Geng et al. [55], el estado de remoción de material se ve afectado significativamente por la velocidad de corte. Los materiales se expulsaron del nanocanal en forma de acumulación durante el mecanizado a una velocidad de 2,64 mm / s, mientras que el estado de eliminación de material se cambió de acumulación a viruta a 4,10 mm / s (Archivo adicional 1:Figura S4 (b)) . Por lo tanto, el aumento de la profundidad de mecanizado a 90 V (~ 4,10 mm / s) se puede atribuir al cambio en el estado de eliminación de material. El ancho del nanocanal fabricado comenzó a aumentar con los voltajes de conducción crecientes. La Figura 6 muestra el diagrama esquemático de la trayectoria de la punta de AFM durante el nanofresado, las elipses punteadas, las elipses negras sólidas y las flechas azules representan el proceso de mecanizado terminado, el proceso de mecanizado en curso y la dirección de movimiento de la punta de AFM, respectivamente. El ancho ( W 2 ) del canal mecanizado en la Fig.6 (b) era más grande que eso ( W 1 ) en la figura 6 (a). AS 1 y AS 2 (líneas continuas rojas) representan la longitud de contacto entre la sección transversal de la punta AFM y el material de muestra. El valor de AS 1 resultó ser mayor que el de AS 2 cuando el ancho de mecanizado “ L 1 "Era igual a" L 2. ”
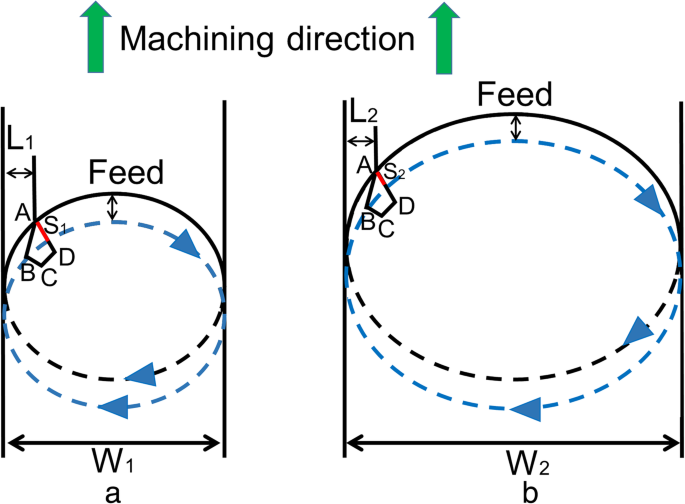
Representación esquemática de la trayectoria de la punta del AFM durante el proceso de nanofresado:el ancho mecanizado del nanocanal ( a ) es más pequeño que el nanocanal ( b ) y las elipses punteadas, las elipses negras sólidas y las flechas azules representan el proceso de mecanizado terminado, el proceso de mecanizado en curso y la dirección de movimiento de la punta del AFM, respectivamente
El valor de S h en Eq. (5) se obtuvo mediante la Ec. (8), donde D y AS son respectivamente la profundidad del canal mecanizado y la longitud de contacto entre la sección transversal de la punta AFM y el material de muestra.
$$ {S} _h =\ frac {1} {2} \ cdot \ left | D \ left | \ cdot \ right | \; AS \ right | $$ (8)Por tanto, la ecuación. (5) se volvió a escribir en la forma de Eq. (9).
$$ {F} _ {\ mathrm {N}} =\ frac {1} {2} \ cdot \ left (p \ cdot \ frac {\ cos \ beta} {\ cos \ alpha} - \ tau \ right) \ cdot \ left | D \ left | \ cdot \ right | AS \ right | $$ (9)Los valores de α y β se mantuvieron constantes durante todo el proceso de mecanizado. Los valores de la tasa de deformación a 1500 Hz se encontraron en el rango de 2,03 × 10 5 ~ 3,66 × 10 5 s -1 ; por lo tanto, se puede suponer que la presión normal local ( p ) alcanzó su valor límite a 1500 Hz. Además, la velocidad de mecanizado no manifestó ningún efecto sobre la recuperación de la muestra durante el mecanizado a 30–150 V (~ 2,03–3,66 mm / s) [53]; por lo tanto, los tamaños dimensionales finales del nanocanal solo se determinaron mediante las dimensiones de mecanizado. Los valores de AS 2 (Fig. 6 (b)) fueron más pequeños que los de AS 1 (Fig. 6 (a)) para anchos mecanizados más grandes, y de acuerdo con la Ec. (9), el valor de D fue mayor para un valor menor de AS. Por lo tanto, los valores de la profundidad de mecanizado aumentaron con los voltajes de excitación crecientes. Una imagen AFM típica del nanocanal fabricado bajo una carga normal de 25 μN, un voltaje de activación de 120 V y una frecuencia de 1500 Hz se presenta en el archivo adicional 1:Figura S4 (b). Es notable que los materiales se eliminaron tanto en forma de astillas como de amontonamiento, y los materiales expulsados se acumularon solo en un lado del nanocanal. Además, los materiales expulsados se acumularon en formación de viruta en la parte inferior del nanocanal durante el mecanizado a 150 V bajo una carga normal de 25 μN. Por lo tanto, los datos de tamaño del nanocanal fabricado durante el mecanizado a un voltaje de 150 V y una frecuencia de 1500 Hz (bajo una carga normal de 25 μN) estaban vacíos en la Fig. 4d.
Es evidente en la Fig. 4c que el ancho del nanocanal comenzó a aumentar con los voltajes de excitación crecientes. Además, cuando los valores de carga normal y voltaje de activación se mantuvieron constantes, el ancho del nanocanal fabricado a una frecuencia de 1500 Hz era más ancho que el de 100 Hz. Además, la profundidad de mecanizado del nanocanal fabricado a 1500 Hz fue más profunda que la de 100 Hz, y se descubrió que el tamaño de la sección transversal de la punta era mayor durante el mecanizado de un nanocanal más profundo. Por lo tanto, los nanocanales se fabricaron más anchos cuando se mecanizó a mayor profundidad.
Primera transferencia de moldes de nanocanales
Se aplicaron nanocanales mecanizados mediante el método de rayado simple bajo cargas normales de 25 μN, 33 μN, 41 μN, 50 μN y 58 μN al primer proceso de transferencia. Además, en el proceso de transferencia también se utilizaron moldes de nanocanales fabricados mediante nanofresado a una frecuencia de 100 Hz en el rango de voltaje de activación de 30-150 V (con una separación de 30 V). Los nanocanales (80 nm de profundidad y 510 nm de ancho) mecanizados mediante el método de rayado simple se denominaron "nanocanal I", mientras que los nanocanales (50 nm de profundidad y 610 nm de ancho, 90 nm de profundidad y 630 nm de ancho) fabricados mediante nanomolinería se denominaron "nanocanal II ”y“ nanocanal III ”, respectivamente. Se utilizaron tres relaciones de peso de PDMS diferentes (5:1, 7:1 y 9:1) en el primer proceso de transferencia.
Las figuras 7a yb revelan los efectos de diferentes proporciones de peso de PDMS en el tamaño de la pared bajo una carga normal de 25 μN y una frecuencia de 100 Hz, y la línea de trazos negros representa el tamaño del nanocanal original antes de la transferencia. La imagen AFM típica y la sección transversal correspondiente de la pared obtenida del nanocanal III en una relación en peso de 5:1 durante la primera transferencia se muestran en la Fig. 7cyd, y esta pared se denominó "pared III". Los efectos de diferentes proporciones de peso de PDMS en el tamaño de la pared bajo un solo proceso de rayado con una carga normal de 17 μN y una frecuencia de 100 Hz se mostraron en ESI (consulte el archivo adicional 1:Figuras. S5, S6, S7 y S8 de ESI para detalles). Las paredes obtenidas del "nanocanal I" y "nanocanal II" se denominaron "pared I" y "pared II", respectivamente. It is evident that the heights of all walls at different PDMS weight ratios were approximately the same. The widths of the walls were larger than the original nanochannel width, and the width at the weight ratio of 5:1 was found to be the largest. Due to the thermal expansion of PC sheet, a small deviation was noticed between final wall size and original nanochannel size. It was also observed that the elasticity of PDMS increased as the PDMS weight ratio decreased from 5:1 to 7:1 [41, 42]. Hence, the wall obtained at the weight ratio of 5:1 was stiffer and its elastic recovery was smaller; thus, the width of the wall obtained at the weight ratio of 5:1 was the largest.
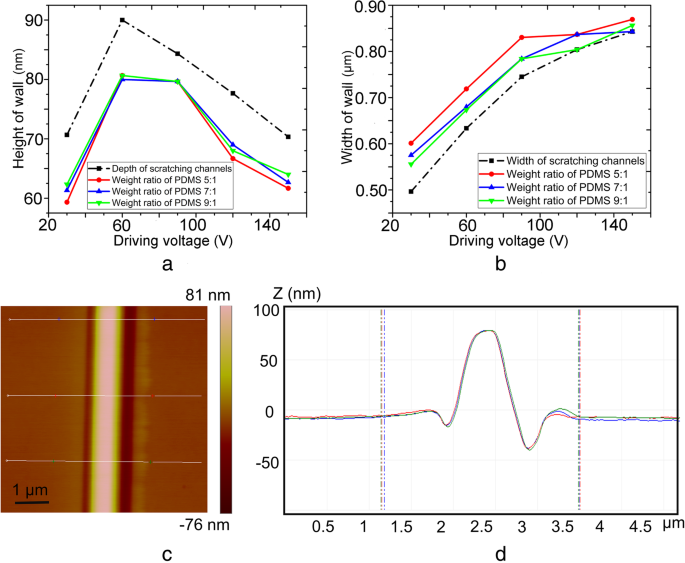
Relationship between a wall height, b wall width, and transfer parameters (various weight ratio of PDMS) during first transfer process, where the channel molds were fabricated with a normal load of 25 μN and a frequency of 100 Hz, and c typical AFM image and d corresponding cross-section of the wall obtained from nanochannel III at a weight ratio of 5:1
Second transfer of nanochannel molds
The final PDMS slabs with nanochannels were obtained during second transfer process based on the wall obtained at a weight ratio of 5:1 in the first transfer process. Three different PDMS weight ratios (10:1, 9:1, and 8:1) were used during second transfer process. Figure 8a and b present the relationship between nanochannel size obtained under a normal load of 25 μN and a frequency of 100 Hz and transfer parameters during second transfer. It is clear from Fig. 8a that the depths of the nanochannels were larger than the original machining size, moreover, the depth at 10:1 was found to be larger than other two ratios. Further, the widths of the wall were also larger than the original size, and the width at 10:1 was found to be the largest (Fig. 8b). Figure 8c and d present a typical AFM image and corresponding cross-section of the nanochannel (120 nm depth and 690 nm width) obtained from wall III at a weight ratio of 10:1 during second transfer, and it was termed as “nanochannel C.” The relationship between the nanochannel sizes obtained under single scratching process with a normal load of 25 μN and a frequency of 100 Hz and the transfer parameters during the second transfer process were shown in ESI (see Additional file 1:Figures. S9, S10, S11 and S12 of ESI for details), the nanochannels obtained from “wall I” and “wall II” were termed as “nanochannel A” and “nanochannel B”, respectively.
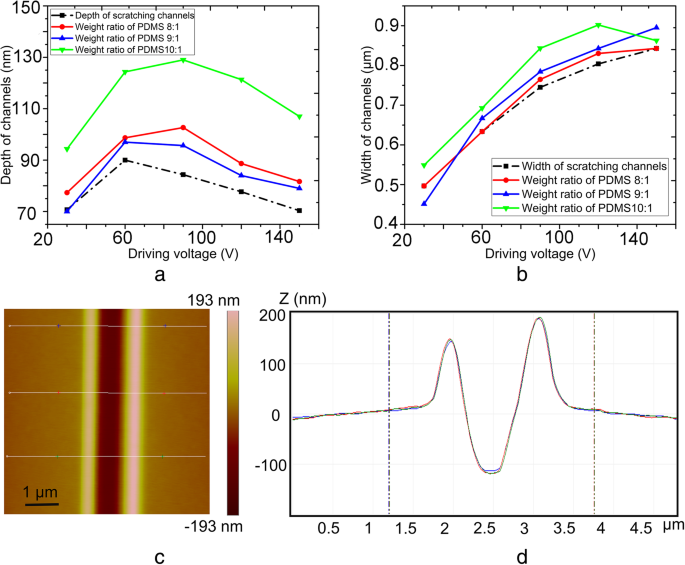
Relationship between a nanochannel height, b nanochannel width, and transfer parameters (various weight ratio of PDMS) during second transfer, where the channel molds were fabricated with a normal load of 25 μN and a frequency of 100 Hz, and c typical AFM image and d corresponding cross-section of the nanochannel obtained from wall III at a weight ratio of 10:1 during second transfer
The depths of nanochannels obtained from walls II and III were larger than the original machining size, whereas the depth obtained from wall I was smaller than the initial machining size. Furthermore, the changes in width were identical to the changes in depth. The aspect ratio of wall I was larger than those of walls II and III, thus each wall manifested different thermal expansion values. Hence, the changing trends of width and depth during second transfer were different though at the same PDMS weight ratio. The values of the depth and width of walls II and III at 9:1 and 8:1 were found to be closer to the original machining size compared with 10:1. Because the elastic recoveries of PDMS at 9:1and 8:1 are closer to 5:1 than 10:1, which indicates an almost similar recovery trend for PDMS at 9:1, 8:1, and 5:1.
Application of nanochannel devices in electric current measurement
Nanochannel devices are often used in the fields of single nanoparticle manipulation, electrokinetic transport phenomena, DNA analysis, and enzymatic reaction detection. The main working principle of nanofluidic chips depends on the variation in electric current; therefore, it is important to measure the electrical conductivities of nanochannel devices. The electrical conductance in a nanochannel can be estimated by Eq. (10) [56].
$$ G={10}^3N\;{}_Ae\frac{wh}{l}\sum {\mu}_i{c}_i+2{\mu}_e\frac{w}{l}{\delta}_n $$ (10)donde μ i is the mobility of ion i , c i is the concentration of ion i , δ n is the effective surface charge inside the nanochannel, and NA and e signify Avogadro constant and electron charge, besides, w , h y l are the nanochannel width, height and length, respectively. It is obvious that the electrical conductance of a nanochannel is affected by the nanochannel feature dimensions and the solution concentration. The electric double layer (EDL) plays an important role in the nanochannel when the ratio of DEL thickness to the nanochannel height increases. The diffuse layer thickness of EDL is 3~5 times of the Debye length (λ D ), which can be expressed by Eq. (11) [57].
$$ {\lambda}_D=\sqrt{\frac{\varepsilon_0{\varepsilon}_r{k}_bT}{2{n}_{i\infty }{(ze)}^2}} $$ (11)donde n i ∞ denotes ion density in the solution, ε o is the permittivity of vacuum, ε r is the dielectric constant of electrolyte solution, z is the valency of buffer solution (z = z + − z - = 1 for KCl), and kb y T are the Boltzmann constant and temperature, respectively. In the present study, three different nanofluidic chips were obtained after the completion of transfer process. Nanofluidic chips consisted of nanochannels A, B, and C were termed as nanofluidic chips A, B, and C, respectively. Each nanofluidic chip contained four nanochannels. The widths and the depths of nanofluidic chips A, B, and C were measured as 60 nm and 500 nm, 80 nm and 680 nm, and 120 nm and 690 nm, respectively. The effective length of nanochannels in all chips was calculated as 50 μm. As shown in Fig. 8, pile-ups distribute on the sides of the nanochannels A, B, and C. The pile-ups may fill into the nanochannels and lead to a failure of the preparation for the nanofluidic chips. Thus, in order to verify the reliability of the fabricated nanochannel devices, electrical conductivity measurement test was conducted. KCl with 1 mM concentration was as the electrolyte solution in our study, and the values of electrical current were measured by an electrometer (Model 6430, Keithley, USA). The schematic sketches of the measurements for electric current in microchannel and nanochannel are presented as the inset figures in Fig. 9a and b, respectively. The experiments were carried out under DC power (applied by an Ag electrode) with an increment of 2 V for 3-s duration. Figure 9a presents the measured I - V curves of microchannels in three different nanofluidic chips, and a linear relationship between current and voltage was observed. Moreover, as the effect of EDL in microchannels was negligible and the dimensional sizes of microchannels in different nanofluidic devices were identical, the values of current in different chips were nearly the same. It is evident from Fig. 9b that the values of current in different nanofluidic devices were distinct due to different nanochannel sizes. For KCl solution of 1 mM concentration, the value of λ D was about 10 nm, thus the diffuse layer thickness of EDL was found as 30~50 nm [57]. Consequently, EDL got overlapped along the depth (60 nm) of nanofluidic chip A; however, no overlapping was observed in nanofluidic chip C (depth of 120 nm). However, it was difficult to determine whether EDL got overlapped or not in nanofluidic chip B (depth of 80 nm). It assumes that the effective surface charges (δ n ) in all nanochannels are identical as the charge density of a surface is material property [58, 59]. The concentration of the ions in a nanochannel depends on the EDL field, the stronger the EDL field, the higher the ion concentration in the nanochanel [44]. In the present study, the EDL field in nanofluidic chip A is the strongest as the highest ratio of the DEL thickness to the nanochannel height, which signifies that the ion concentration in the nanochannel of nanofluidic chip A is the highest. Según Eq. (10), the nanochannel of nanofluidic chip A is more conductive due to the higher ion concentration. Hence, the value of electrical current in nanofluidic chip A was the largest, whereas nanofluidic chip C yielded the smallest value. In addition, at larger width sizes, EDLs did not overlap along the width directions of nanochannels. In nanofluidic chip B, when the value of applied electric field was lower than 25 V, a linear relationship was noticed between current and applied voltage; however, a limiting region appeared as the value of applied voltage increased and finally, became liner again as the electrical field increased further, this phenomenon belongs to ohmic-limiting-overlimiting current characteristic [60, 61]. The results of electrical current measurement revealed that the nanofluidic devices fabricated by the proposed method were effective, the pile-ups of the nanochannels A, B, and C had almost no influence on the performance of the nanofluidic devices.
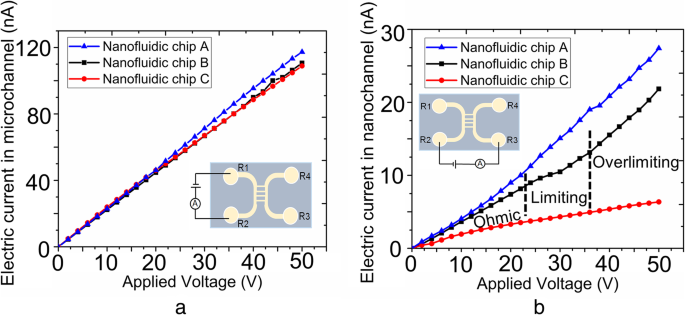
Electric current measurement results based on the fabricated nanochannel devices, the cross-section size (depth × width) of nanochannels for nanofluidic chip A, B, and C are 60 × 500 nm, 80 × 680 nm and 120 × 690 nm, respectively. un Current in microchannels. b Current in nanochannels. The insets display the schematic sketches of the measurements
Conclusiones
In the present research, nanochannels with controllable sizes (sub-100-nm depth) were fabricated by AFM tip-based nanomilling, and for the first time, the machined nanochannels were applied to prepare nanofluidic devices. The multichannel nanofluidic devices were prepared in four steps:(1) fabrication of nanochannels by AFM tip and piezoelectric actuator, (2) fabrication of microchannels by lithography, (3) transfer of micro- and nanochannels, and (iv) bonding. Further, nanochannel sizes were controlled by changing the driving voltages and frequencies inputted to the actuator. The heights of the wall obtained during first transfer were smaller than the original machining size, whereas the widths were larger than the original machining size. The experiment results revealed that during second transfer process, nanochannel sizes affected PDMS weight ratios. Finally, micro-nanofluidic chips with three different nanochannel sizes were obtained by bonding a PDMS nanochannel chip on a PDMS microchannel chip. Moreover, the electrical current measurement experiment was conducted on the fabricated nanofluidic chips, and it was found that the values of current were affected by nanochannel sizes. Therefore, PDMS nanofluidic devices with multiple nanochannels of sub-100-nm depth can be efficiently and economically fabricated by the proposed method.
Compared with other fabrication approach, the proposed method for fabrication of the nanofluidic devices in the study is easy to use and low cost; besides, the nanochannels with controllable dimension size can be obtained easily. However, the commercial AFM system cannot equip with a large-scale high-precision stage due to the spatial limitation; thus, the maximum fabrication length of the nanochannel is confined as 80 μm. In addition, the tip wear cannot be neglected after long-term fabrication due to the high machining speed, which should be investigated in future work.
Abreviaturas
- AFM:
-
Microscopio de fuerza atómica
- DC:
-
Corriente continua
- EDL:
-
Electric double layer
- KCL:
-
Potassium chloride
- PC:
-
Polycarbonate
- PDMS:
-
Polydimethylsiloxane
- PSD:
-
Position-sensitive photodetector
Nanomateriales
- Troquelado:un curso intensivo sobre este proceso de fabricación
- Blog:Comprender el proceso de fabricación de PDMS
- Los métodos de fabricación de composite más populares
- ¿Qué es el proceso de fabricación de chapa metálica?
- Las diferentes formas en que el proceso de acabado agrega valor funcional a los proyectos de fabricación de metales
- Uso de una impresora 3D para mejorar su proceso de fabricación - Video
- Su guía para el corte del proceso de fabricación de metales
- La fabricación de tuberías de proceso requiere una planificación de ruta imaginativa
- La fabricación de tuberías de proceso requiere el cumplimiento de especificaciones exactas
- ¿Cuánto tiempo requiere su proceso de fabricación?
- Los beneficios del arenado para su proyecto de fabricación de metal personalizado