Haciendo olas con la automatización del torno
Como el orgullo del estado Badger, Mercury Marine es conocido localmente simplemente como "Merc". Las raíces de 81 años de este ícono estadounidense le otorgan una rica historia, lo que lo convierte en el orgullo de la comunidad y en el favorito del público náutico. Mientras tanto, su éxito hace que Merc sea la envidia de sus competidores. Mercury Marine es un fabricante líder mundial de todo tipo de sistemas de propulsión marina, una división de Brunswick Corp. con un valor de 2600 millones de dólares que emplea a más de 5200 personas en varios lugares del mundo.
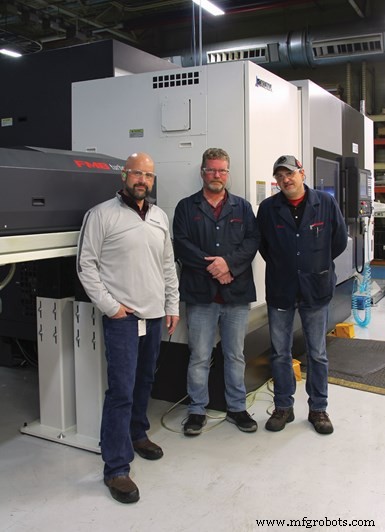
Jason Noworatzky, Bill Cusick y Chris Erke ( L-R) forman parte del equipo que produce todos los engranajes y ejes para las transmisiones internas y externas de Mercury Marine que se utilizan en todo el mundo.
Más de 80 años de desarrollo innovador de motores para embarcaciones han convertido a la ubicación de Fond du Lac, Wisconsin, en un depósito muy conocido de destreza en ingeniería y excelencia en la producción. El extenso campus de hoy junto a la Interestatal 41 cuenta con más de 2,5 millones de pies cuadrados de espacio que contiene todo tipo de disciplinas de ingeniería y fabricación junto con las aproximadamente 3300 personas que hacen que todo suceda.
En la Planta 4, se producen todos los engranajes y ejes para todas las transmisiones internas y externas de Mercury Marine fabricadas en sus plantas de todo el mundo. Esta empresa masiva incluye ejes de propulsión, ejes de transmisión, ejes de dirección, marchas hacia adelante, marchas hacia atrás y piñones para todos los motores intraborda y dentrofueraborda MerCruiser, los dentrofueraborda MerCruser Alpha y Bravo, los motores diésel y dentrofueraborda diésel Mercury, el Mercury SportJet y todos los motores fuera de borda. El hombre responsable del equipo de ingenieros de fabricación, ingenieros industriales y programadores necesarios para esta importante tarea es Jason Noworatzky, director de ingeniería de la Planta 4. Para todo lo que tiene que ver con el proceso de fabricación de ejes y engranajes, el Sr. Noworatzky y su equipo crean y establecen los procedimientos de fabricación y calidad junto con los gastos de capital necesarios para producir las piezas de manera eficiente y, lo que es más importante, para cumplir con las estrictas especificaciones de Mercury. . Luego, seleccionan la mejor maquinaria y automatización en función de la velocidad, el costo de mano de obra y la perfección de la pieza. "Calidad:construimos el proceso en torno a eso", dice el Sr. Noworatzky.
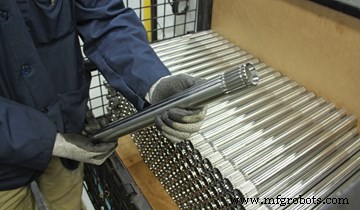
Esta sección del eje de dirección para los fuerabordas de la empresa originalmente se producía en una celda de cinco máquinas con dos operadores, pero ahora se maneja con un torno de dos torretas y dos husillos que se combina con un alimentador de barras y un descargador.
Un componente que requería mucha mano de obra es una sección hueca de los ejes de dirección que se utilizan en los fuerabordas de Mercury Marine. El proceso anterior era una celda multimáquina. El inicio del proceso fue un torno de un solo husillo con una sola torreta y un contrapunto con un alimentador de barras. Luego sería transportado a otra máquina para una operación de taladrado. A continuación, las piezas se trasladaron a otra máquina para una operación de rectificado sin centros y luego se transportaron a una operación de tallado final. Este método de producción de piezas se empleó durante décadas. “He estado aquí durante 25 años y siempre se hizo de esa manera”, dice Bill Cusick, ingeniero de fabricación. Ese proceso de celda de varias máquinas anterior usaba dos operadores.
Eventualmente se hizo evidente que las máquinas en estas celdas tendrían que ser reemplazadas. En busca de una solución moderna, el Sr. Cusick investigó maquinaria nueva y moderna. “La tecnología finalmente se puso al día, por lo que ahora podíamos emplear todos los procesos en una sola máquina”, señala el Sr. Cusick. "Ya no teníamos que ejecutarlos en las viejas máquinas talladoras".
Chris Erke, programador sénior, opina sobre el tema de la calidad. "Es difícil mantener la posición real y el descentramiento al pasar de una máquina a otra en lugar de hacerlo todo en una sola máquina donde se puede controlar".
Un buen equilibrio
“Una gran parte de este movimiento para nosotros ha sido la calidad”, dice el Sr. Cusick. “Eso significa hecho en una sola máquina”. El equipo tuvo que hacer un buen acto de equilibrio entre la capacidad y las capacidades de la máquina, la cantidad de máquinas y los requisitos de producción proyectados. Después de crear una especie de marcador, una solución ganó. El Sr. Cusick fue al distribuidor local de máquinas-herramienta de confianza de la empresa, Morris Midwest, e inició un diálogo sobre el reemplazo de las viejas celdas de cinco máquinas. “Creamos una SOW (Declaración de trabajo) que explicaba que queríamos un torno que completara nuestro proceso de mecanizado”, dice el Sr. Cusick. "Teníamos una idea bastante clara de lo que pensábamos que implicaría obtener el tiempo de ciclo necesario al agregar las operaciones adicionales".
El Sr. Cusick y el Sr. Erke le dijeron a Morris Midwest que creían que un torno con dos torretas y dos husillos, combinado con un alimentador de barras y un descargador, funcionaría. “Con las nuevas tecnologías, no pensamos que sería un problema producirlo, así que entra por un extremo y sale listo”, comenta el Sr. Erke. "Prácticamente sabíamos cómo hacerlo completo, pero Morris Midwest seleccionó la máquina adecuada, hizo toda la ingeniería y manejó todas las escorrentías".
El ascenso de Frankenlathe
En 2017, se entregó a la Planta 4 la primera celda combinada de alimentador de barras/torno/descargador. Debido a su tamaño y capacidades, el nuevo Okuma LT3000 EX fue apodado cariñosamente como "Frankenlathe". Poco después, se colocó una segunda celda (un duplicado exacto de la número uno) junto a la primera y el personal de la tienda se refirió rápidamente como "La novia de Frankenlathe".
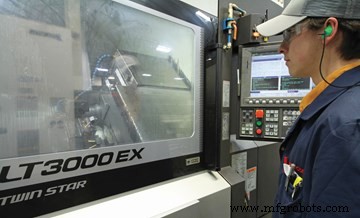
Tres tornos Okuma LT3000 EX, con alimentadores de barras y descargadores, se agregaron para manejar la producción de los ejes.
Los "Frankenlathes" están ambos flanqueados por la maquinaria de Edge Technologies que hace que el proceso sea una verdadera ventaja tecnológica única. La automatización empleada en esta configuración actual era la pieza que faltaba para producir la pieza "de una vez" con la calidad requerida. El Okuma LT3000 EX es un torno de arquitectura abierta, un centro de torneado de dos husillos altamente flexible en la clase de plato de 8 pulgadas. Esta máquina multifunción horizontal de doble husillo integra funciones de torno y fresado/taladrado en todas las torretas.
Las dos primeras celdas estaban equipadas con alimentadores de barras FMB Turbo 5-65. Estas son unidades estilo revista que alimentan barras de hasta 12 pies y cuentan con canales llenos de aceite que crean un efecto de cojinete hidrodinámico alrededor de las barras giratorias para un funcionamiento suave. La capacidad de almacenamiento del cargador es de 11 pulgadas en las unidades estándar. Con la longitud de la pieza y el tiempo de ciclo para esta sección del eje, Okuma puede procesar bastantes pies lineales de tubería durante un turno, por lo que Edge Technologies agregó Edge BarLift, un sistema de carga de cargador extendido que cuenta con 28 pulgadas adicionales de material para más tiempo sin que el operador tenga que cargar manualmente el alimentador.
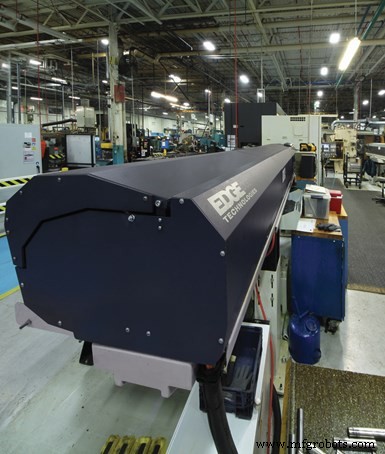
El FMB Turbo 5-65 de 12 pies Los alimentadores de barras estilo revista cuentan con canales llenos de aceite que crean un efecto de rodamiento hidrodinámico alrededor de las barras giratorias para un funcionamiento suave.
“Es posible que hayamos tenido uno o dos tornos que tenían un descargador en el pasado, pero este es, con mucho, el paso más grande en el producto más convencional en el que hemos hecho (un descargador)”, dice el Sr. Noworatzky. “No podemos dejar caer esta parte porque dañaría las estrías. La pieza terminada tiene requisitos de acabado superficial”.
Las celdas uno y dos se instalaron en 2017 y se equiparon con unidades FleXsys LE (carga/extracción) de Edge Technologies para el proceso de descarga de piezas. Esta unidad está diseñada para la automatización de piezas más grandes, específicamente trabajos de eje largo. Está diseñado para alimentar y retraer el material en barra cortado a la longitud de la pieza, de hasta 2,5 pulgadas de diámetro y 37 pulgadas de largo, para la producción con tornos CNC de un solo husillo. El material del tubo de 12 pies se introduce en el husillo principal de Okuma con el FMB Turbo 5-65.
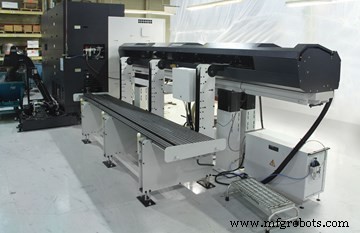
El sistema de carga de cargador extendido Edge BarLift presenta un 28 pulgadas adicionales de stock para un funcionamiento más prolongado sin la intervención del operador.
Frankenlathe 3:El auge de la automatización
La tercera celda llegó a fines de 2019 con el nuevo Rebel 80 Servo Unloader, el sistema automático de extracción de piezas desarrollado más recientemente por Edge Technologies para extraer piezas en un rango de diámetro de 8 a 80 mm. Esta es una unidad más versátil que la versión anterior que se ejecuta en las celdas uno y dos. Las unidades más antiguas no tenían un sistema de control que se comunicara con el torno como lo hacen los alimentadores de barras FMB. Se requirió programación adicional de FleXsys LE. Aunque las unidades funcionaron bien una vez que se ajustaron, Mercury Marine solicitó a Edge Technologies que proporcionara una configuración de descarga actualizada que solucionaría esta deficiencia. El desarrollo del servodescargador Rebel 80 fue la respuesta. Edge había estado trabajando en el nuevo descargador y convirtió el problema de la comunicación en una prioridad principal para la instalación de Mercury. Ahora, en la tercera celda, el Okuma LT3000 EX, el alimentador de barras FMB y el descargador Edge se comunican y funcionan como una sola máquina con optimización de tipo Industria 4.0.
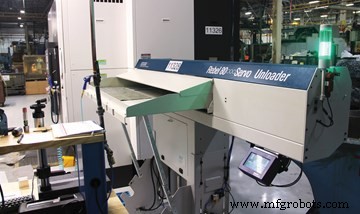
Mientras que los dos primeros tornos estaban equipados con FleXsysLE descargadores, diseñados para la automatización de piezas más grandes, el tercer Okuma tiene el servodescargador Rebel 80, que está diseñado para extraer piezas de 8 a 80 mm de diámetro y cuenta con capacidades de comunicación optimizadas con el alimentador de barras y la máquina herramienta.
El servodescargador Rebel 80 presenta varias formas de retirar piezas con varios métodos para conectar el extractor a la pieza para sacarla del subhusillo. Estos dispositivos se conocen como efectores finales. Los mecanismos efectores finales disponibles incluyen pinzas de barra para agarre de diámetro exterior, pinzas de diámetro exterior de expansión, pinzas de diámetro exterior de tres puntos, dedos de alimentación, pinzas angulares, electroimanes para materiales ferromagnéticos y soluciones de ingeniería especial para material perfilado y de formas irregulares.
Para proteger los acabados de las piezas, en el caso de las estrías del eje de dirección, la bandeja en V de extracción deposita suavemente los ejes sobre la superficie del cargador, que está cubierta con un material no metálico. La mesa inclinada es ajustable, lo que permite que el descargador "descargue fácilmente" piezas de gran diámetro.
El servodescargador Rebel 80 cuenta con una pista de cambio axial que permite que la unidad se deslice fácilmente fuera del torno para cambiar el revestimiento del husillo y acceder a mantenimiento en la parte posterior del torno. Viene equipado con un control remoto colgante y un control conversacional que cuenta con una pantalla táctil y programación basada en menús. El control también almacena programas de pieza ilimitados.
La tercera celda también se benefició de un avance en la tecnología del alimentador de barras. El FMB Turbo 5-65 vino equipado como un modelo A, con el nuevo sistema de canal de guía de ajuste automático. Los canales de guía de poliuretano se ajustan automáticamente al diámetro adecuado, lo que permite que un canal de guía funcione con diámetros de barra de 5 mm a 65 mm. Esta característica le da a Mercury Marine la capacidad de cambiar rápidamente a diferentes diámetros de eje sin cambios en el conjunto de canales de guía. Este diseño ayuda en las configuraciones rápidas para la producción justo a tiempo.
Junto con el aumento en la calidad de las piezas, estas celdas brindan la ventaja de reducir los costos de mano de obra y ofrecen un mejor uso del espacio de piso. Idealmente, el Sr. Noworatzky tendría una pizarra en blanco para reconfigurar su planta de producción como desee. Explica que las dos cosas que impulsan a su equipo son combinar operaciones y tratar de compartir el trabajo.
En el futuro, el Sr. Noworatzky cree que agregar automatización, como los alimentadores y descargadores de barras que se han empleado con estos tornos, será la norma. “No preveo que entren aquí nuevas celdas a partir de ahora que no tengan algún tipo de automatización. Ya sea un robot FANUC, un sistema de pórtico, un alimentador de barras o descargadores”. Él predice que será algo para minimizar la cantidad de trabajo que se requiere para hacer un trabajo. “La mano de obra es una prima”, concluye Noworatzky.
Debido a la mayor experiencia técnica requerida para operar celdas como estas, Mercury Marine ofrece clases al personal para mejorar sus habilidades. “Requiere que usted tenga un nivel más alto de operador”, dice el Sr. Noworatzky. Para lograr esto, Mercury envía a sus operadores a un colegio comunitario local donde se inscriben en cursos de mecanizado de nivel 1 y nivel 2. Una vez completado, pueden realizar la prueba para recibir la certificación NIMS.
Mercurio Marino | mercuriomarine.com
Tecnologías de punta | 314-692-8388 | edgetechnologies.com
Sobre el autor
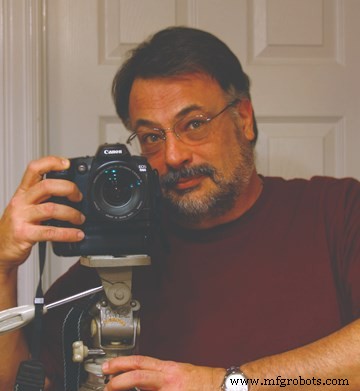
Kevin Shults
Kevin Shults es un profesional de la publicidad y el diseño. Tiene 24 años de experiencia en la industria de máquinas herramienta, los últimos 20 de los cuales se desempeñó como director de marketing de un OEM dentro de la industria del mecanizado de precisión. Póngase en contacto con el Sr. Shults en [email protected].
Equipo industrial
- Ganar dinero con el enrutador CNC
- Evolución de la Automatización de Pruebas con Inteligencia Artificial
- Automatización empresarial con plataformas de bajo código
- Impulsar la experiencia del cliente con la automatización inteligente
- Torno estándar con controles de pantalla táctil
- Torno con CNC
- Torno CNC con sistema de guía lineal hidrostático
- Torno de herramienta múltiple con base de polímero:SNK
- Control de funciones de torno de bancada inclinada con gráficos de verificación
- Torno capaz de operación manual con asistencia CNC
- Torno CNC de cuatro husillos con carga automática de piezas