7 diseños complejos logrados con impresión 3D
Aprovechando la flexibilidad de diseño que ofrece la impresión 3D, los ingenieros pueden hacer realidad incluso las ideas más desafiantes.
La impresión 3D es una tecnología que puede producir formas y características inalcanzables con los métodos de fabricación convencionales. Para mostrar el poder de la tecnología, exploramos 7 ejemplos de diseños impresionantes que se lograron solo con la impresión 3D.
1. Pinza de freno de titanio impresa en 3D de Bugatti
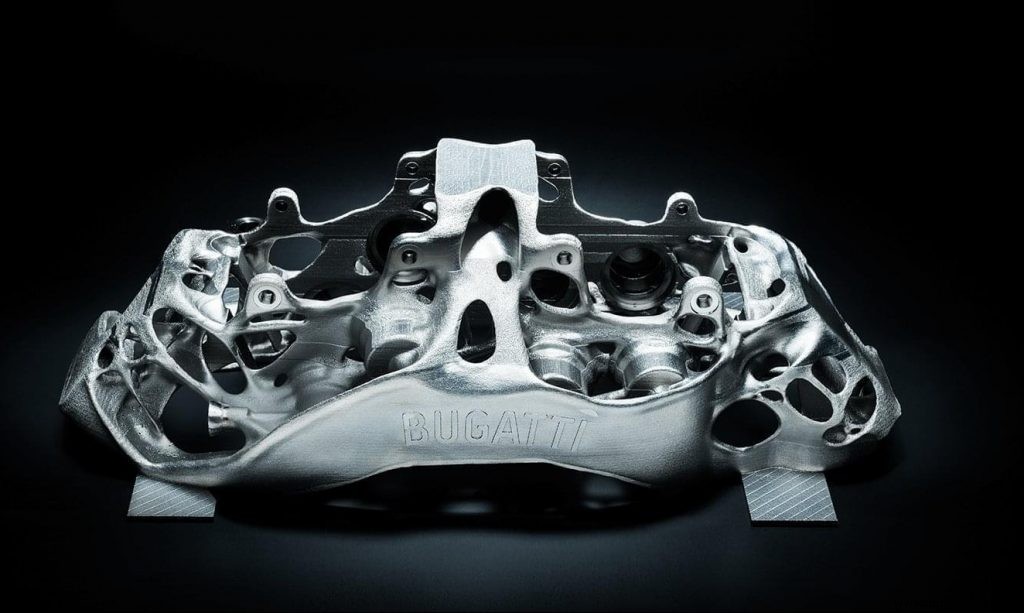
Aplicación:automoción
Beneficios:Aligeramiento, mayor fuerza
El fabricante de automóviles francés Bugatti aprovechó la libertad de diseño de la impresión 3D para su último superdeportivo Chiron, produciendo lo que se dice que es la pinza de freno más poderosa del mundo:impresa en 3D en titanio.
Si bien la pinza de freno funciona como una pinza normal, la combinación de impresión 3D y titanio significa que es mucho más resistente y aproximadamente un 40% más ligera que la pieza de aluminio que se utiliza actualmente.
Usando un proceso de impresión 3D de metal llamado Selective Laser Melting, el equipo de Bugatti pudo experimentar con una variedad de geometrías y espesores de pared inalcanzables con las técnicas de fabricación tradicionales.
El resultado:una pinza de freno de forma intrincada con espesores de pared entre 1 mm y 4 mm.
A finales de 2018, Bugatti probó con éxito la pinza con cargas elevadas, y la empresa se está preparando ahora para poner el componente en producción.
Sin embargo, Bugatti no es la única empresa que está revolucionando el diseño de pinzas de freno. La empresa británica de tecnología automotriz, Carbon Performance, también está utilizando la impresión 3D para "generar diseños sostenibles" para piezas de automóviles impresas en 3D, incluidas las pinzas.
Para lograr esto, Carbon Performance está utilizando su nueva plataforma de software impulsada por IA. La plataforma ayuda a diseñar componentes que pueden, por ejemplo, mejorar la eficiencia de combustible de un automóvil.
Gracias a su software de diseño e impresión 3D, Carbon Performance puede producir pinzas de freno más robustas y ecológicas gracias, en parte, a su menor peso. Poder crear piezas de metal livianas con impresión 3D significa que se requiere menos material y el proceso de producción incurre en menos desperdicio de material que con la fabricación sustractiva.
La creación de diseños ligeros es uno de los beneficios clave de la impresión 3D. A medida que la tendencia hacia vehículos eléctricos y más eficientes continúe creciendo, veremos a más fabricantes de automóviles explorar la impresión 3D en sus esfuerzos por crear componentes de automóviles livianos y de mejor rendimiento.
2. Soporte de asiento de diseño generativo de General Motor
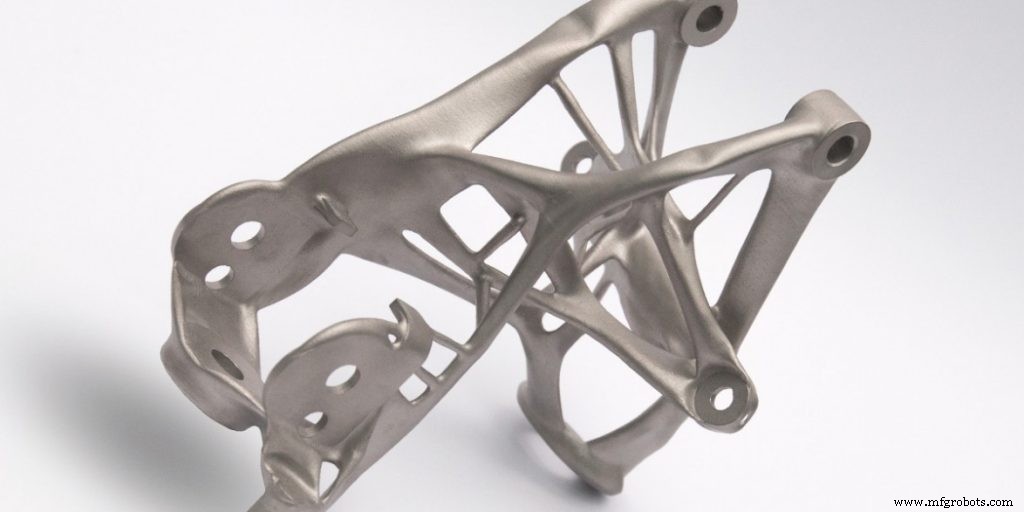
Aplicación:automoción
Beneficio:Ahorro de peso significativo
General Motors (GM) ha creado recientemente una versión impresa en 3D de un soporte de asiento existente utilizando herramientas de diseño generativo.
El software de diseño generativo utiliza algoritmos avanzados para generar automáticamente diseños múltiples. variantes basadas en parámetros específicos como peso, material, tamaño, resistencia y métodos de fabricación. Los diseños posteriores presentan formas orgánicas complejas que a menudo solo pueden cobrar vida con la ayuda de la impresión 3D.
Este fue exactamente el caso con el soporte del asiento de GM. Utilizando el software de diseño generativo Fusion 360 de Autodesk, se produjeron 150 iteraciones de diseño. Luego, GM seleccionó el diseño que ofrecía la mejor compensación entre peso, rendimiento y capacidad de fabricación.
El diseño final apenas se parece al soporte original. Impreso en 3D en metal, el nuevo soporte del asiento es un 40% más ligero y un 20% más resistente que el original. También se ha fabricado como un componente, a diferencia de la pieza original, que debe ensamblarse a partir de 8 piezas independientes.
La capacidad de la impresión 3D para crear piezas complejas más rápidamente y con más flexibilidad hace que la tecnología sea una opción natural para producir el componente rediseñado. El beneficio que se muestra en este ejemplo es la consolidación de piezas:la capacidad de imprimir varias piezas como un solo componente y, por lo tanto, reducir los tiempos y costos de ensamblaje.
Aunque el soporte del asiento de GM sigue siendo una prueba de concepto, la empresa ve un gran potencial en la combinación de software de impresión 3D y diseño generativo. Sin duda, ambas tecnologías desempeñarán un papel clave en el futuro de la fabricación de vehículos al facilitar un diseño y un desarrollo de productos más rápidos, así como la producción de piezas de automóvil complejas.
3. Implante de cadera topológicamente optimizado
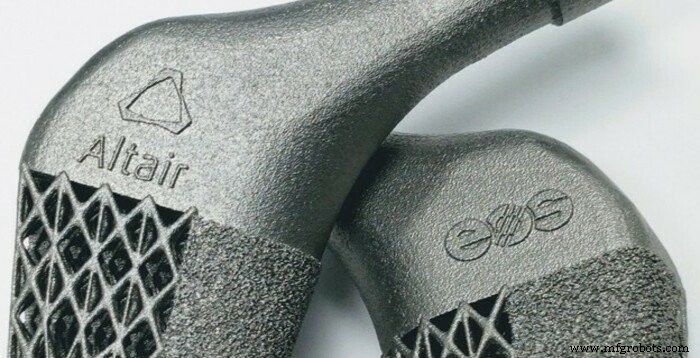
Aplicación:médica
Beneficio:optimización de material
La optimización de topología es una técnica de diseño generativo que permite a los diseñadores aplicar algoritmos avanzados para optimizar la geometría de una pieza. Usando la tecnología, la distribución del material de una pieza se puede optimizar para eliminar cualquier material innecesario del diseño.
Una empresa que aprovecha la optimización de topología es la empresa de TI, Altair, que combinó la impresión 3D con la optimización de topología para crear un implante de vástago de cadera mejorado.
La impresión 3D ofrece una variedad de beneficios para los implantes de cadera, incluida la capacidad de personalizar un implante para las cargas específicas que debe soportar. El software de optimización de topología facilita esto al permitir que los ingenieros tengan en cuenta los diversos casos de carga que un implante de cadera puede ver durante su ciclo de vida.
Al ingresar parámetros como casos de carga y restricciones de diseño, el software optimiza la distribución del material dentro de un volumen de material definido. Este proceso da como resultado un diseño que muestra dónde se puede quitar el material para crear el implante de cadera de mejor rendimiento.
El equipo de Altair utilizó este enfoque para determinar las áreas sólidas y semidensas del implante antes de rellenar las regiones semidensas con estructuras de celosía para aligerar el implante.
En comparación con un fémur intacto o un fémur con un implante estándar, el equipo descubrió que el nuevo diseño ayuda a aumentar el límite de resistencia a aproximadamente 10 millones de ciclos. Esto significa que el implante de cadera podría soportar trotar de Los Ángeles a Nueva York y viceversa, dos veces.
El nuevo diseño también ayuda a reducir la protección contra el estrés en un 57%. La protección contra el estrés se refiere a la reducción de la densidad ósea causada por la colocación de un implante de titanio dentro de un paciente y, en última instancia, puede provocar fracturas y dislocaciones. Por esta razón, diseñar un implante lo más cerca posible del tejido óseo original es clave para reducir la protección contra el estrés y eliminar estos efectos no deseados.
El uso de la impresión 3D como tecnología de fabricación es la única forma de dar vida a estos diseños. No solo hace posibles formas complejas como celosías, sino que también puede producirlas de manera más rentable que los métodos convencionales.
A día de hoy, los implantes impresos en 3D con optimización topológica apenas están comenzando a abrirse camino en casos de uso de la vida real. Los reguladores sanitarios tardarán algún tiempo en desarrollar nuevos métodos de estandarización para estos nuevos diseños de implantes. Sin embargo, mirando hacia el futuro, está claro que la impresión 3D se convertirá en una tecnología clave para crear implantes de cadera de mejor ajuste, más duraderos y de mayor rendimiento para un paciente específico.
4. Puente peatonal impreso en 3D de MX3D
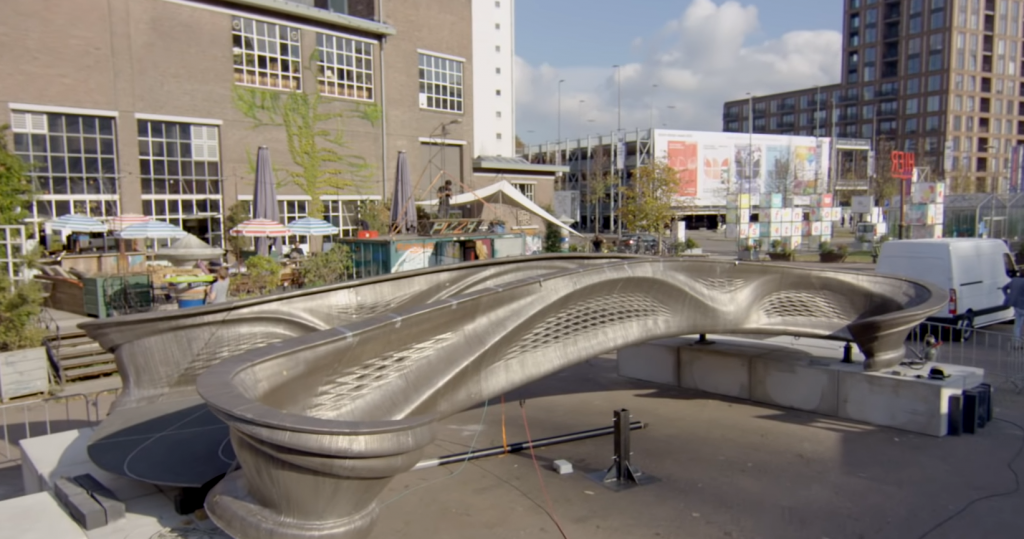
Aplicación:Construcción
Beneficio:Diseño innovador
Presentado en la Dutch Design Week en 2018, el puente peatonal de acero inoxidable impreso en 3D de MX3D es uno de los proyectos de diseño más emocionantes en el espacio de la impresión 3D.
Al instalar máquinas de soldar en brazos robóticos, el equipo MX3D pudo imprimir en 3D un puente de 12 metros de largo, logrando una apariencia y forma únicas. Por ejemplo, el diseño del puente es orgánico y similar a una tela, con muchas curvas y características intrincadas. La superficie del puente se ha dejado sin alisar, dejando visibles las capas de acero depositado que le dan al puente un acabado áspero e inusual.
Curiosamente, la impresión 3D no fue la única tecnología de vanguardia utilizada para este proyecto. Para garantizar la seguridad y el rendimiento optimizado del puente, la estructura de acero impresa en 3D está equipada con una red de sensores para monitorear el estado del puente, registrando la cantidad de personas que lo cruzan y tomando medidas de cosas como la dispersión de peso y calidad del aire.
Todo el proyecto tardó casi cuatro años en ejecutarse y ahora el puente terminado se instalará en Ámsterdam a finales de este año.
5. GE Research desarrolla un intercambiador de calor de inspiración biológica
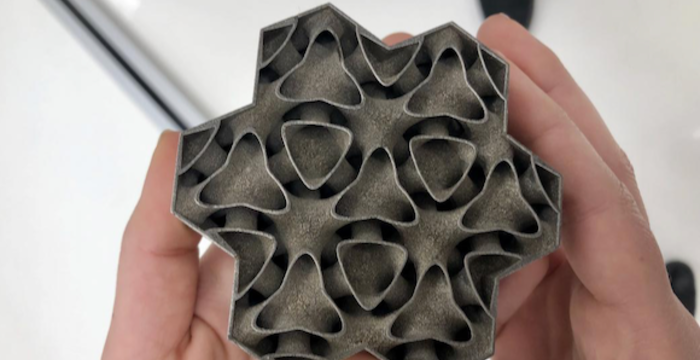
Aplicación:Energía
Beneficio:rendimiento mejorado
GE Research está desarrollando un intercambiador de calor ultraeficiente y de bajas emisiones para equipos de generación de energía como turbinas de gas. Sorprendentemente, para lograr esto, el equipo ideó un diseño innovador inspirado en los pulmones humanos.
Los pulmones humanos son uno de los intercambiadores de calor más eficientes y compactos. El órgano realiza su función de intercambio de calor con una red de capilares, que dividen el flujo de sangre en pequeños chorros. Esta red calienta el aire más frío que inhalamos, al tiempo que regula la temperatura corporal.
El intercambiador de calor de GE funciona de manera similar, pero a temperaturas y presiones mucho más altas. El componente presenta una red trifurcada de canales, que toma el aire caliente que sale de una turbina de gas. Esta red está entrelazada con otra red de canales llenos de fluido de trabajo más frío que corre en la dirección opuesta. El aire caliente y el fluido frío no se mezclan entre sí, pero su proximidad permite que el aire caliente se enfríe, mejorando la eficiencia térmica de una turbina de gas.
Fundamentalmente, la impresión 3D fue la única tecnología capaz de producir un diseño tan complejo.
Una vez que se complete el proceso de desarrollo, GE podrá imprimir en 3D un intercambiador de calor que puede operar de manera rentable a 250 ° C (450 ° F) grados más que los intercambiadores de calor actuales. Con una temperatura de funcionamiento significativamente mayor, el componente impreso en 3D representa una nueva generación de intercambiadores de calor de alto rendimiento.
6. Soporte de techo ligero de BMW
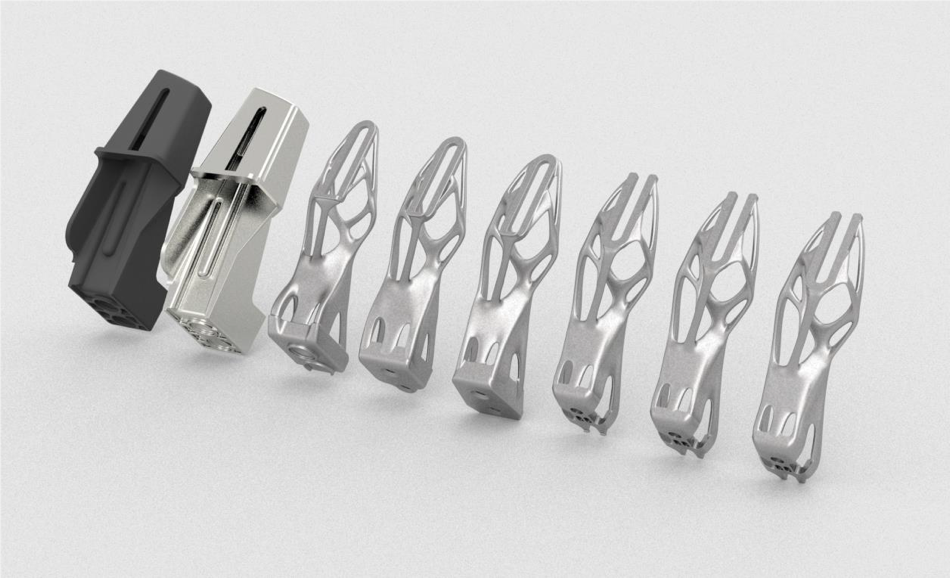
Aplicación:automoción
Beneficio:ahorro de peso
En 2018, BMW lanzó su icónico automóvil i8 Roadster, con un galardonado soporte de techo de metal impreso en 3D.
El soporte de techo, un pequeño componente que ayuda a plegar y desplegar la parte superior del automóvil, requirió un nuevo diseño para maximizar el rendimiento del mecanismo de plegado del techo. Para lograr este objetivo, los ingenieros de BMW recurrieron al software de optimización de topología.
Al usar este software, los ingenieros pudieron ingresar parámetros como el peso, el tamaño del componente y la carga que tomará. Luego, el software generó un diseño que optimizó la distribución del material de la pieza.
El diseño logrado por el equipo de ingeniería fue imposible de fundir. El equipo descubrió que la única forma de hacer posible este diseño era mediante la impresión 3D de metal.
Gracias a la tecnología Selective Laser Melting (SLM), los ingenieros crearon un soporte de techo de metal que es 10 veces más rígido y un 44% más ligero que la alternativa convencional.
La pieza, que ahora se produce en series pequeñas, muestra un enorme potencial de ligereza para los diseños de vehículos cuando se combina con el poder de las técnicas de optimización topológica.
7. KW Micro Power y VELO3D colaboran para innovar un componente de microturbina
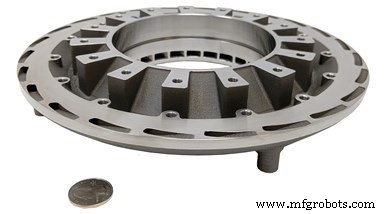
Aplicación:Energía
Beneficio:Funciones internas complejas
Durante algunos años, la empresa de ingeniería, KW Micro Power, ha estado trabajando en el diseño de un generador de microturbina, pero enfrentó desafíos para llevar este diseño a producción. Un desafío clave radicaba en la producción de uno de los componentes del dispositivo.
El componente en cuestión es un disco de titanio con complejos canales internos que ayudan a gestionar los gases de escape de forma más eficiente. Cuando se imprime en 3D en metal, este componente requiere estructuras de soporte para evitar que se caiga o se deforme durante el proceso de impresión.
Sin embargo, la complejidad de las características internas del componente hizo imposible quitar los soportes después de la producción.
Para superar este desafío, la empresa colaboró con VELO3D, un fabricante de impresoras 3D que ha desarrollado su tecnología patentada de impresión 3D en metal, Intelligent Fusion. Esta tecnología permite que la impresora 3D Sapphire de VELO3D imprima piezas con estructuras de soporte mínimas y tensiones residuales reducidas, que a menudo son la causa de deformaciones.
Esto se logra gracias a un repintador sin contacto patentado, que se utiliza para entregar una nueva capa de polvo para fundir y fusionar con un láser. En la impresión 3D de metal a base de polvo, cuando el polvo se coloca encima de otra capa, un repintador podría desalojar la pieza si no está fijada a una placa de construcción.
En el sistema Sapphire de VELO3D, la hoja de recubrimiento no está en contacto con el lecho de polvo. Una vez que se deposita el polvo, se aplica una cuchilla raspadora y un proceso de vacío en la parte superior del polvo para asegurarse de que esté absolutamente nivelado.
Con un repintador que no entra en contacto con la capa anterior de polvo, una pieza no necesita ningún soporte para anclarla a una placa de construcción de metal. Mientras tanto, la simulación y un sistema de control de circuito cerrado que alimenta la impresora permiten imprimir características internas complejas sin soportes.
Para aprovechar toda la potencia de la impresora Sapphire 3D, el equipo de VELO3D ayudó a KW Micro Power a mejorar aún más el diseño del componente del generador. La pieza acabada es un 37% más ligera que el diseño original y se dice que funciona mejor gracias a la reducción de tensiones. Pero lo que es más importante, el diseño que antes se consideraba no fabricable, fue posible gracias a una nueva generación de tecnologías de impresión 3D de metal.
Dar vida a las ideas más complejas
La impresión 3D ofrece una enorme flexibilidad de diseño, lo que permite a los diseñadores e ingenieros experimentar con nuevas formas y características, incluidas formas optimizadas topológicamente, estructuras de celosía y diseños ligeros.
Con tantas oportunidades abiertas por la impresión 3D, la tecnología permite a los fabricantes producir productos innovadores con diseños optimizados y personalizados, lo que sería imposible con la fabricación tradicional.
Sin embargo, para desbloquear este potencial es fundamental seguir los principios de diseño exclusivos de la fabricación aditiva. Solo cuando están armadas con la comprensión de las posibilidades y limitaciones de la impresión 3D, las empresas pueden utilizar la tecnología para hacer realidad sus ideas más creativas.
Impresión 3d
- Introducción a la impresión 3D con plásticos
- Entrevista con un experto:Dr. Alvaro Goyanes de FabRx
- Impresión 3D con silicona:¿llega su momento?
- Introducción a la impresión 3D de cerámica
- Una guía para la impresión 3D con Multi Jet Fusion de HP
- Una breve guía para la impresión 3D con Binder Jetting
- Impresión 3D con resinas:Introducción
- Impresión del fusible 1 con el fusible 1
- KUHMUTE rediseña la movilidad con la impresión 3D SLS
- Impresión 3D de alta velocidad con AION500MK3
- Compuestos de impresión 3D con fibra continua