Derretir y Verter Metal
Del horno de fundición al molde
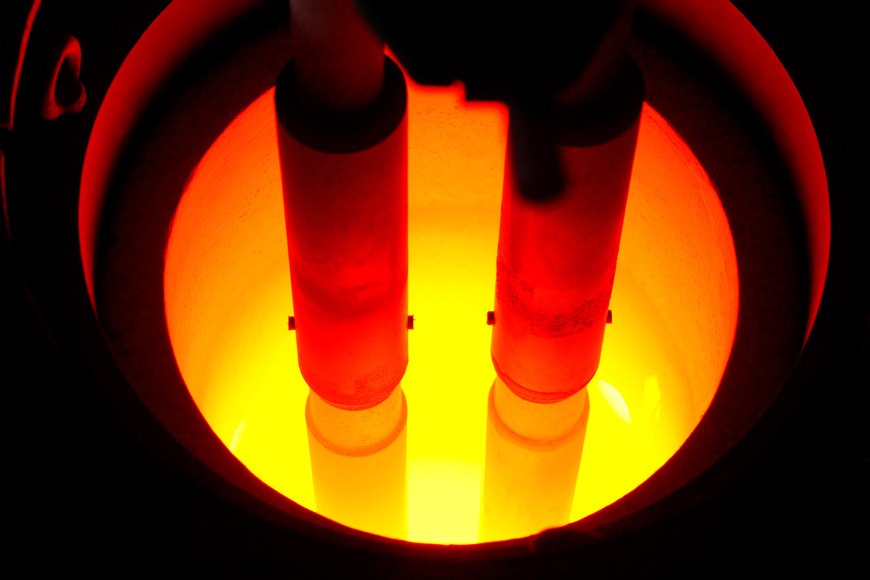
Las fundiciones son dramáticas. Enormes hornos, resplandecientes de calor, transforman trozos de metal en fluidos líquidos ardientes. Cuando está listo, su contenido se vierte en cucharones que esperan en medio de una lluvia de chispas. Los trabajadores guían el flujo de metal desde el horno hasta el molde detrás de escudos térmicos, protegiéndolos contra los peligros de la temperatura y los materiales. El piso de fundición es donde el diseño se vuelve real, en un proceso extraordinario que crea objetos cotidianos. Las innovaciones para crear y mantener las temperaturas requeridas para diferentes aleaciones son parte de la evolución de la metalurgia. El trabajo de fundir y verter el metal parece escenas sacadas de los libros de historia, pero es donde ocurre algo de la ciencia más interesante.
La fabricación de metal fundido se basa en hornos que pueden calentarse lo suficiente como para llevar los metales a un estado líquido. Los primeros minerales de fundición en la historia humana fueron el plomo y el estaño:estos metales blandos se pueden derretir al calor del fuego de la cocina. Para crear metales más resistentes, los metalúrgicos necesitaban algo más que llamas de madera.
Alto calor y avance humano
La Edad del Bronce dependía de la fuerza del cobre. Es posible que el cobre se haya fundido por primera vez accidentalmente en un horno de cerámica, que funciona al menos 200°C más caliente que una fogata. La falta de registros escritos de esa época hace que sea difícil estar seguro. Durante la Edad del Bronce, se usaban hornos similares a hornos para extraer varios componentes elementales de la roca que se fundían a diferentes temperaturas, siendo el cobre el premio más alto para hacer un buen latón y bronce.
Hay evidencia de que los humanos usaron hierro antes de la Edad del Hierro. Sin embargo, estos artículos estaban hechos de hierro trabajado que literalmente había caído del cielo:el hierro meteórico se encuentra en una forma relativamente pura en comparación con el hierro terrestre. Se podía calentar y trabajar como se encontró. Sin embargo, la verdadera Edad del Hierro comenzó cuando las personas descubrieron cómo extraer hierro útil de los minerales, y eso requiere derretirlos hasta obtener estados blandos, parecidos a un caramelo, casi líquidos o líquidos. Este avance llegó a diferentes partes del mundo en diferentes momentos, pero involucró la invención de los hornos de floración y una lenta construcción del conocimiento de la metalurgia ferrosa. Los hornos Bloomery permiten que el hierro se caliente lo suficiente como para trabajarlo hacia la pureza, en lugar de llevar el metal al estado fundido, pero ayudaron con el lento descubrimiento de la química del hierro. Una cosa es fundir hierro:para hacer un metal fuerte utilizable, se necesita la adición correcta de carbono, y los hornos de floración dependían del combustible de carbono. Cuando los hornos se calentaron lo suficiente como para fundir el hierro, los metalúrgicos también necesitaron desarrollar su comprensión de los fundentes, que son aditivos que se usan para ayudar a purificar el metal final evitando la formación de óxido.
Los avances traídos por la combinación innovadora de horno y química han continuado a lo largo de la historia humana. El avance metalúrgico obviamente marcó el comienzo de las edades de Bronce y Hierro en base a su nombre. La Revolución Industrial nos introdujo en la Edad del Acero. El motor de combustión, los ferrocarriles y las prácticas de construcción modernas no serían posibles sin un avance importante llamado proceso Bessemer, que burbujea oxígeno a través del acero fundido, lo que permite temperaturas más altas y tiempos de producción más rápidos, lo que permite la producción en masa de acero de calidad.
Fusión frente a fundición
La fundición es el proceso de eliminar un elemento metálico de los minerales extraídos. La mayoría de los metales se encuentran como vetas en las rocas o como partes de otros elementos. La fundición es el primer paso de la extracción. La fusión es lo que se hace con aleaciones metálicas o metales puros. La chatarra se funde, el mineral se funde. El arrabio son los lingotes de hierro en bruto creados a partir de la fundición del mineral de hierro.
Altos hornos
Para la fundición se utilizan altos hornos, que son hornos muy altos inyectados con gases a presión. Los altos hornos producen principalmente lingotes de una aleación intermedia, como el arrabio. Estos lingotes luego se envían a fundiciones involucradas en la fabricación.
Las fundiciones de fabricación toman aleaciones y aditivos y los funden para hacer grados específicos de metal fundido en otros tipos de hornos de fusión.
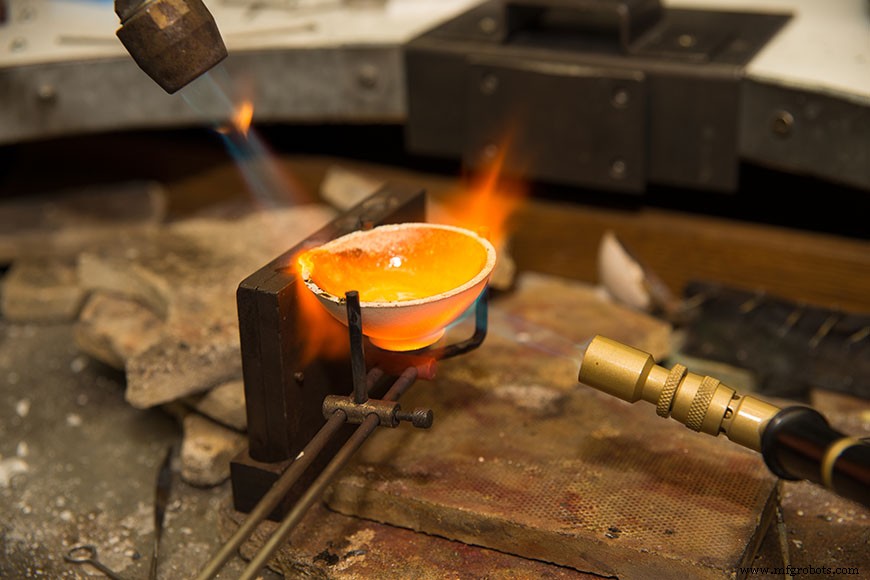
Tipos de hornos de fusión de fundición
Tradicionalmente, los hornos de cúpula y crisol eran las formas más comunes de forjar metales para fundición; en la actualidad, los hornos de arco eléctrico y de inducción son comunes.
Hornos de crisol
Los hornos de crisol son la forma más básica de horno de metal. Un crisol es un recipiente hecho de material que puede soportar temperaturas increíblemente altas, a menudo hecho de cerámica u otro material refractario. Se coloca en la fuente de calor como una olla en el fuego. El crisol se llena o se carga con metal y aditivos. En la era moderna, los hornos de crisol todavía están en uso por parte de los fabricantes de joyas, los aficionados al jardín, algunas fundiciones no ferrosas y las fundiciones que realizan trabajos en lotes muy pequeños. Los crisoles pueden variar desde una taza muy pequeña donde los metales se derriten con un soplete, como se podría hacer en una joyería, hasta recipientes grandes que contienen 50 libras de material. Los crisoles más grandes a menudo se colocan dentro de un horno similar a un horno y se pueden levantar para verter, o se puede verter el material desde la parte superior.
Hornos de cúpula
Los hornos de cúpula son largos, en forma de chimenea y están llenos de coque de carbón y otros aditivos. Se enciende el combustible dentro de la cúpula y, cuando el horno está lo suficientemente caliente, se agrega directamente arrabio y chatarra. El proceso de fusión del hierro alrededor del coque y los aditivos agrega carbono y otros elementos y produce diferentes grados de hierro y acero. Los hornos de cúpula ya no se utilizan normalmente en la producción, ya que los métodos de arco eléctrico e inducción son más eficientes para producir el calor necesario. Sin embargo, hay algunos lugares donde la tradición mantiene los hornos de cúpula en funcionamiento, como en este video de Da Shu Hua, donde los trabajadores de fundición chinos arrojan hierro fundido contra una pared para crear chispas dramáticas para dar la bienvenida al Año Nuevo.
Hornos de arco eléctrico
(EAF) entró en uso a finales de 1800. Los electrodos transmiten corriente eléctrica a través del metal dentro del horno, lo cual es más efectivo que agregar calor externo cuando se derriten grandes volúmenes al mismo tiempo. Un horno eléctrico de arco grande utilizado en la producción de acero puede contener hasta 400 toneladas. Una "carga" de este acero a menudo está hecha de hierro pesado como losas y vigas, chatarra triturada de automóviles y otros materiales reciclados, y lingotes de arrabio de una fundición.
Una vez que se llena el tanque, se colocan electrodos en el metal y un arco de electricidad pasa entre ellos. A medida que el metal comienza a derretirse, los electrodos pueden empujarse más adentro de la mezcla o separarse para crear un arco más grande. Se puede agregar calor y oxígeno para acelerar el proceso. A medida que se empieza a formar metal fundido, se puede aumentar el voltaje, ya que la escoria creada sobre el metal actúa como una capa protectora para el techo y otros componentes del horno eléctrico de arco.
Cuando todo está derretido, se inclina todo el horno, para descargar el metal líquido a un cucharón debajo. A veces, las propias cucharas pueden ser hornos EAF más pequeños, encargados de mantener el metal caliente antes del vertido.
Hornos de inducción
trabajar con campos magnéticos en lugar de arcos eléctricos. El metal se carga en un crisol rodeado por un poderoso electroimán hecho de cobre enrollado. Cuando se enciende el horno de inducción, la bobina crea un campo magnético que se invierte rápidamente mediante la introducción de una corriente alterna. A medida que el metal se derrite, el electroimán crea remolinos dentro del líquido que agitan automáticamente el material. El calor en un horno de inducción es creado por la excitación de las moléculas en el propio hierro, lo que significa que todo lo que entra en el crisol es exactamente lo que sale:no hay adición de oxígeno u otros gases al sistema. Esto significa menos variables para controlar durante la fusión, pero también significa que no se puede usar un horno de inducción para refinar acero. Lo que entra, sale. Al igual que un horno EAF, los hornos de inducción a menudo se descargan al inclinarse hacia los cucharones que se encuentran debajo.
Los hornos de inducción son muy comunes y son fáciles de operar cuando se les da una entrada de alta calidad. Los modelos comunes pueden producir 65 toneladas de acero en cada carga.
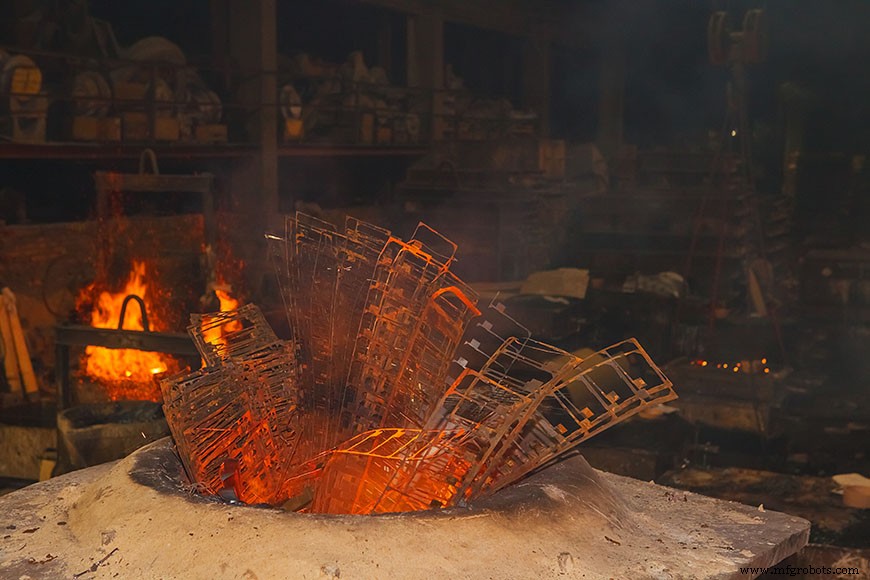
Todos los hornos de la planta de fundición se enfrentan a un enemigo fatal:el vapor. El agua, incluso en pequeñas cantidades, puede provocar salpicaduras o explosiones, por lo que todas las chatarras y ferroaleaciones, así como todas las herramientas utilizadas en la producción, deben estar secas antes de su uso. La chatarra no debe tener áreas cerradas en las que pueda haber quedado atrapado agua o vapor. Incluso las herramientas utilizadas por los trabajadores de la fundición deben estar libres de condensación o humedad. Muchas fundiciones tienen un horno de secado para asegurarse de que la chatarra y las herramientas estén totalmente secas antes de que nada toque el horno de fundición.
Cucharas de fundición
Una vez fundido el metal, debe introducirse en el molde. En fundiciones más pequeñas, todo esto puede ocurrir en una sola etapa:un crisol basculante o extraíble puede llevar el metal del horno a la arena. Sin embargo, esto no es práctico cuando un horno contiene muchas toneladas de metal. Por lo general, en la fabricación de metales ferrosos, las cucharas transfieren porciones más pequeñas de la masa fundida desde el horno principal.
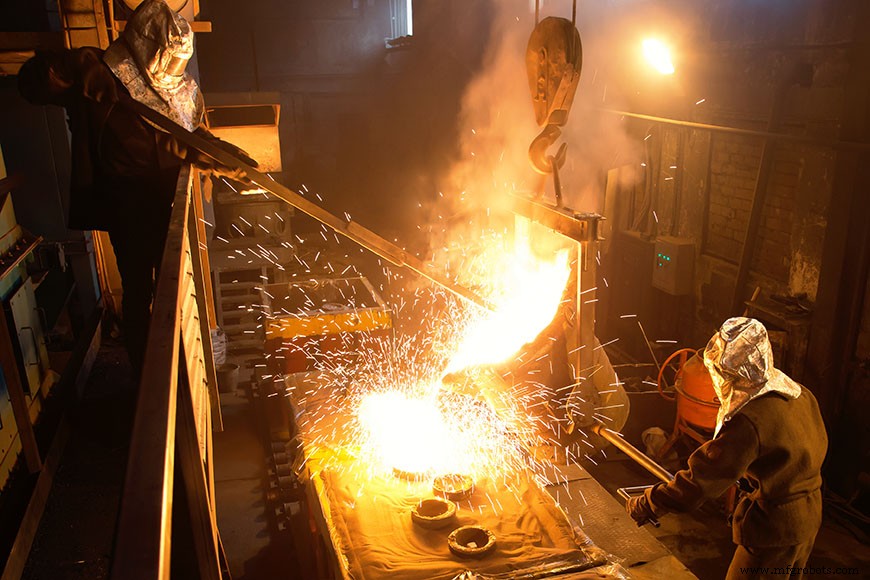
En estos sistemas, una cuchara puede llevar el metal directamente al molde. Sin embargo, una cuchara de transferencia podría llevar el líquido a un tanque de retención oa un horno secundario. Los cucharones de tratamiento son otro tipo disponible, que se utilizan para romper la masa fundida en porciones, como un panadero podría separar una masa básica para usarla como base para otras recetas. Por ejemplo, al hierro fundido líquido se le pueden agregar agentes en la cuchara de tratamiento para hacer que el carbono que contiene tenga una forma esférica, en lugar de escamas, creando un metal más maleable llamado hierro dúctil.
Los cucharones pueden ser muy pequeños y levantados por trabajadores de fundición o pueden contener muchas toneladas de metal y necesitan soporte mecánico. Los cucharones más grandes se mueven a través de una fundición mediante un carro-cucharón o mediante una grúa puente o un sistema de orugas.
Los cucharones de todo tipo están diseñados para proteger al trabajador de salpicaduras, llamas o chispas mientras se vierte. Algunos cucharones vierten sobre el labio superior, o un pico de vertido, y deben inclinarse:a menudo tienen engranajes que permiten al trabajador de la fundición controlar cuidadosamente la velocidad de vertido. Otros cucharones tienen su pico vertedor en el fondo del balde y el vertido se controla quitando y volviendo a colocar un tapón.
Mezcla de aleaciones
Las aleaciones metálicas están formadas por mezclas de elementos estandarizados por una fórmula que especifica los porcentajes de cada tipo así como los pasos seguidos en su fabricación. Los hornos de fusión y los cucharones de tratamiento de una fundición es donde se crean estos tipos de aleaciones para piezas fundidas.
Las fundiciones a menudo se especializan en aleaciones ferrosas, que contienen hierro, o aleaciones no ferrosas específicas, como metales preciosos, aleaciones a base de cobre o aluminio.
Las aleaciones ferrosas se clasifican en hierro y acero. Las aleaciones de hierro fundido incluyen hierro gris, que incluye silicio, y hierro dúctil, que tiene un tipo de carbono esférico. Los grados de acero fundido se definen por los porcentajes de carbono y otros aditivos en la mezcla. El acero inoxidable es un acero que incluye cromo para ayudar a prevenir la oxidación por pasivación.
Las aleaciones no ferrosas incluyen todos los demás metales, por lo que no sorprende que haya una mayor especialización en fundiciones no ferrosas. Algunos lugares se especializan en zinc, algunos en aluminio; otros trabajan principalmente con aleaciones a base de cobre como el latón y el bronce. Sin embargo, hay cruce. Si una fundición en particular trabaja tanto con bronce como con aluminio, por ejemplo, probablemente se especializará en ciertos grados de cada uno.
Independientemente de las aleaciones con las que trabaje una fundición, la premisa de hacer metal fundido y vaciarlo en vacíos para darle forma es la misma. Una idea se vuelve real en el momento en que el metal fluye en un molde.
Publicación anterior:CoreMakingMetal Casting ProcessSiguiente publicación:Sacudido y limpieza
Metal
- Fundición en arena:proceso y características | Industrias | Metalurgia
- ¿Qué es un metal ferroso? – Una guía completa
- Cromo Metal:Elementos, Propiedades y Usos
- ¿Qué es el hierro fundido? Definición, propiedades y usos
- ¿Qué es el tratamiento térmico? - Proceso y métodos
- ¿Qué es la chapa metálica? Definición, tipos y usos
- ¿Qué es la fundición de metales? Definición, tipos y procesos
- ¿Qué es la corrosión? – Definición y Prevención
- Comprensión de las aleaciones metálicas y el límite elástico
- 5 aleaciones metálicas industriales importantes y sus usos
- Guía de calibres y conversiones de chapa