¿Qué es el corte de engranajes? ¿Diferentes tipos de procesos de corte de engranajes?
Hola, espero que estés bien. En este artículo, discutiremos ¿Cuáles son los diferentes tipos de procesos de corte de engranajes? en detalle. Primero, veremos la Introducción, un poco de historia, y luego estudiaremos todos los diversos tipos de procesos de corte de engranajes.
Comencemos con la introducción primero,
Introducción al tallado de engranajes:
Un engranaje es un componente vital de la maquinaria. Es un elemento rígido duro cuyo único propósito es transmitir potencia o movimiento o ambos de un eje de la máquina a otro.
Es una rueda en bruto redonda con un número contable de dientes a lo largo de su periferia. Los engranajes pasan por condiciones de servicio extenuantes. Es importante diseñar un engranaje lo más robusto, confiable, altamente eficiente y económico para satisfacer las amplias demandas en los campos de la maquinaria.
Los detalles en el diseño de los engranajes hacen que su fabricación sea especial. La fabricación de engranajes es un trabajo exclusivamente preciso. Los diseños de engranajes se han mantenido estándar a lo largo de los siglos en todo el mundo.
El tallado de engranajes se realiza en máquinas especiales que sólo están diseñadas para tallar engranajes y nada más. A lo largo de los años, existe una fresadora que aún no ha quedado obsoleta y que puede realizar operaciones polivalentes además del corte de engranajes, pero que no es adecuada para la producción de engranajes a gran escala.
Historia del corte de engranajes:
En la antigüedad, se usaba una especie de ruedas redondas en blanco para transmitir movimiento y potencia. Las ruedas de fricción tenían un diseño simple como se muestra en la fig. 1.0.
Las ruedas eran simples discos redondos fijados en los extremos de cada eje. La transmisión de potencia se lograba haciendo rodar la cara de un eje sobre la cara del otro.
Las partes acopladas giraban entre sí por la fricción que se producía entre ellas. Más tarde, como invención en 1897, Herman Pfuater inventó la máquina que puede cortar engranajes que conducen como base a ruedas dentadas llamadas engranajes.
La técnica de corte de engranajes se practica desde entonces hasta ahora.
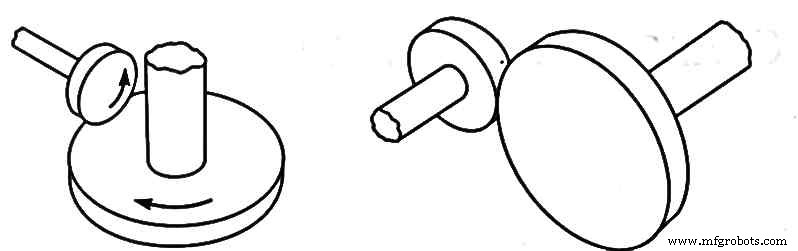
Métodos para fabricar Engranajes:
En la generación de automatización, los engranajes se fabrican mediante tres métodos principales.
- Reparto
- Formación
- Remoción de metales
1. Casting:
Los engranajes se pueden producir mediante varios procesos de fundición; el proceso más común y económico es la fundición en arena. Se pueden fabricar engranajes de gran tamaño y módulos a bajo costo.
Estos engranajes son generalmente ásperos e imprecisos, al igual que sus aplicaciones donde se toleran el ruido de funcionamiento y la precisión del movimiento. La fundición en arena es adecuada para lotes únicos o pequeños. Los engranajes fabricados mediante fundición a la cera perdida tienen un mayor grado de precisión dimensional con un buen acabado superficial.
Estos pueden fabricarse utilizando materiales fuertes para soportar grandes cargas en comparación con los engranajes fabricados por fundición en arena.
El moldeo por inyección también produce engranajes de termoplásticos que pueden usarse para cargas bajas con mayor precisión y movimiento.
El moldeado de carcasa también se usa a veces para producir engranajes pequeños porque es el menos costoso. Sin embargo, la fundición no cumple con los requisitos de la producción en masa de engranajes.
El segundo método es el proceso de formación,
2. Formando:
La fabricación de engranajes mediante el método de formación pone en acción el proceso de formación de rodillos, extrusión y estirado en frío.
2.1 Perfilado:
En este proceso, se monta una pieza bruta de engranaje en un eje y se la obliga a rodar contra matrices rodantes. Se dan varios números de revoluciones. Esta presión del troquel sobre la rueda en blanco hace que la rueda dentada sea sólida.
Los engranajes hechos por este proceso tienen mayor fuerza y excelente precisión. El perfilado se realiza tanto en caliente como en frío dependiendo de la aplicación.
Los engranajes producidos por este método no necesitan ninguna operación de acabado. Este método también ahorra mucho material, pero la maquinaria utilizada para este método de fabricación de engranajes es muy costosa.
La ventaja notable de este método es que el engranaje se vuelve más fuerte tanto en tensión como en compresión debido a la tensión plástica producida en la rueda y los dientes durante el proceso de rodadura.
2.2 Extrusión y estirado en frío:
La extrusión es el mejor método para hacer pequeños engranajes de dimensiones precisas.
En este método de fabricación, una barra se estira en frío a través de un molde de formación para crear engranajes en toda la superficie de la barra a lo largo de su longitud, como se muestra en la fig. 1.1. Luego, se cortan longitudes más pequeñas de la longitud tallada de la barra.
Cada pequeña longitud es igual al grosor del engranaje requerido. Solo se requiere un esmerilado de acabado para completar el trabajo. Anteriormente, se extruían aleaciones de aluminio, latón, bronce y magnesio.
Pero ahora las barras de acero de hasta 60 mm de diámetro. están siendo extruidos en el comercio manufacturero. Los engranajes producidos por este método se usan más comúnmente en relojes, impresoras, máquinas de escribir, etc.
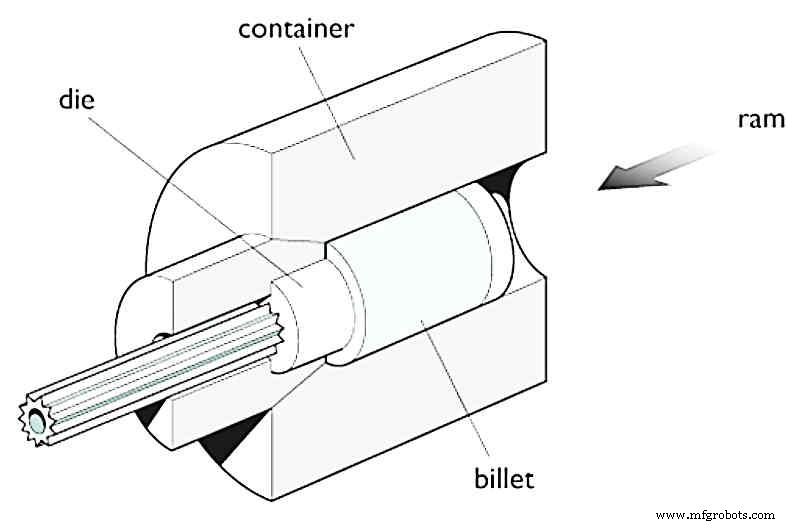
3. Eliminación de metales:
Como el propio nombre nos indica, en este método se mecanizan ruedas en bruto para eliminar el metal de la pieza de trabajo y producir dientes de engranaje a lo largo de su periferia.
Bajo este método de corte de engranajes, los principales métodos son:
- Método de perfilado o cortador de formas.
- Método de generación.
3.1 Corte de engranajes mediante perfilado o método de corte de forma:
En este método, se usa un cortador para quitar el metal de la rueda ciega. En muchos casos, la fresa tiene el mismo grosor, de espacio entre cada diente del engranaje. Para operar, se utiliza una herramienta de corte de un solo punto para la máquina cepilladora y perfiladora.
Mientras que, en una fresadora, se utiliza una herramienta redonda de dientes múltiples para perfilar engranajes en la pieza de trabajo. Este método requiere un cortador especial para fabricar cada perfil de engranaje diferente y no es adecuado para producciones de gran volumen.
Se enumeran varios métodos para cortar engranajes bajo este método:
- Corte de engranajes en una fresadora con fresa de disco formado o fresa de extremo.
- Corte de engranajes en máquina perfiladora o cepilladora con una herramienta de forma de un solo punto.
- Corte de engranajes en una brochadora.
- Corte de engranajes con hojas de herramienta de forma por proceso de velocidad de corte.
3.1.1 Corte de engranajes en una fresadora con cortador de disco formado:
El engranaje recto se puede fabricar fácilmente en una fresadora universal. En este principio de tallado de engranajes, la rueda ciega sólida se monta en el mandril conectado a la cabeza divisoria. El cortador está montado en el eje.
El eje del cortador siempre es perpendicular al eje del engranaje en blanco como se muestra en la figura 1.2. A continuación, el eje vertical de la rueda en blanco se empareja adecuadamente con el eje horizontal del cortador.
Luego, la mesa se mueve hacia arriba usando una manivela de movimiento vertical hasta que la punta del cortador toca la periferia de la rueda dentada. Los movimientos de indexación se calculan previamente y se determinan en consecuencia.
Luego se levanta la rodilla con la altura requerida, es decir, igual a la profundidad de los dientes, y se establece el cero vertical. Simultáneamente, se le da energía al cortador.
En una sola pasada, se acaba un diente y la mesa vuelve a su posición inicial. Este movimiento vertical puede ser menor si el engranaje se va a cortar en dos o más pasadas. Luego, la pieza en bruto del engranaje se indexa para el siguiente diente.
El mismo ciclo de operaciones se repite hasta que se corta el número requerido de dientes a lo largo de la periferia de la rueda dentada.
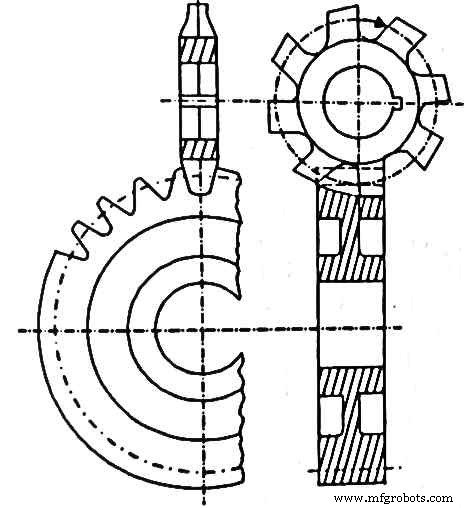
Para la fabricación de engranajes helicoidales o tornillos sin fin en una fresadora universal, un accesorio de fresado en espiral se usa
El ángulo de hélice se obtiene mediante el uso del accesorio para ajustar la cuchilla y la rueda dentada en bruto en una inclinación entre sí. En el corte de engranajes helicoidales se utiliza un juego de dos cortadores.
Uno para desbaste y otro para acabado. Estos engranajes también se cortan mediante la misma secuencia de operaciones discutida anteriormente.
Para fabricar piñones de gran paso, las fresas de extremo se emplean en lugar de las fresas de tipo disco. La fresa de mango se monta en el husillo de la fresadora a través de un mandril.

Producir engranajes en una fresadora es uno de los métodos más simples y económicos. Los engranajes del tipo de dientes rectos, cónicos y helicoidales, así como cremalleras, pueden fabricarse por el método de fresado de engranajes.
La calidad del engranaje producido no puede considerarse precisa ya que el movimiento de indexación no es preciso.
3.1.2 Corte de engranajes en una máquina perfiladora o cepilladora con una herramienta de forma de un solo punto.
Los engranajes también se pueden fabricar en máquinas perfiladoras, cepilladoras o ranuradoras. En este método de fabricación, se usa una herramienta de forma de un solo punto para marcar los dientes en la rueda en blanco, como se muestra en la figura 1.3.
En todas estas máquinas, la pieza en bruto del engranaje está montada en un mandril ubicado entre el contrapunto y el cabezal divisor. El cabezal divisor de la fresadora se puede atornillar directamente a la mesa de estas máquinas. En producciones pequeñas, la pieza en bruto del engranaje se monta directamente en el mandril como se muestra en la fig. 1.4.
La herramienta está montada de forma segura en el cabezal de la herramienta. En cada una de estas máquinas, el corte de engranajes se logra mediante el movimiento alternativo de la herramienta contra la pieza de trabajo o mediante el movimiento alternativo de la rueda ciega del engranaje más allá de la herramienta de corte de un solo punto.
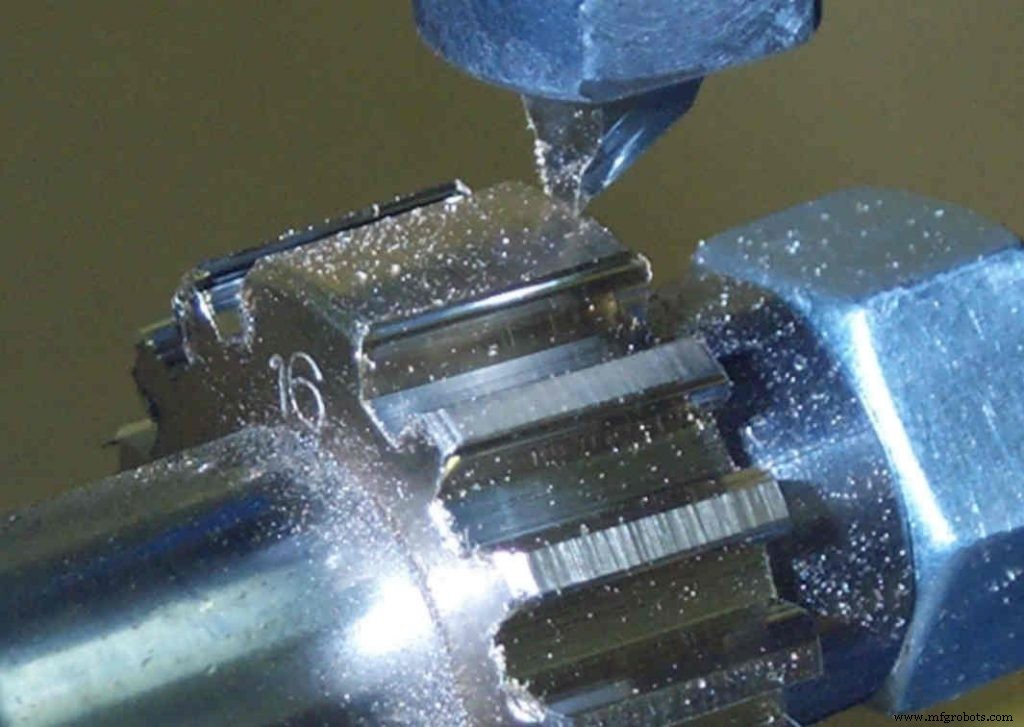
En el caso de las máquinas moldeadoras y ranuradoras, la rueda dentada en blanco permanece estacionaria en el mandril y en el accesorio respectivamente, mientras que la herramienta de corte de un solo punto se mueve alternativamente pasando la pieza de trabajo. La herramienta se fija al pistón de la máquina en ambos casos como se muestra en la fig. 1.4.
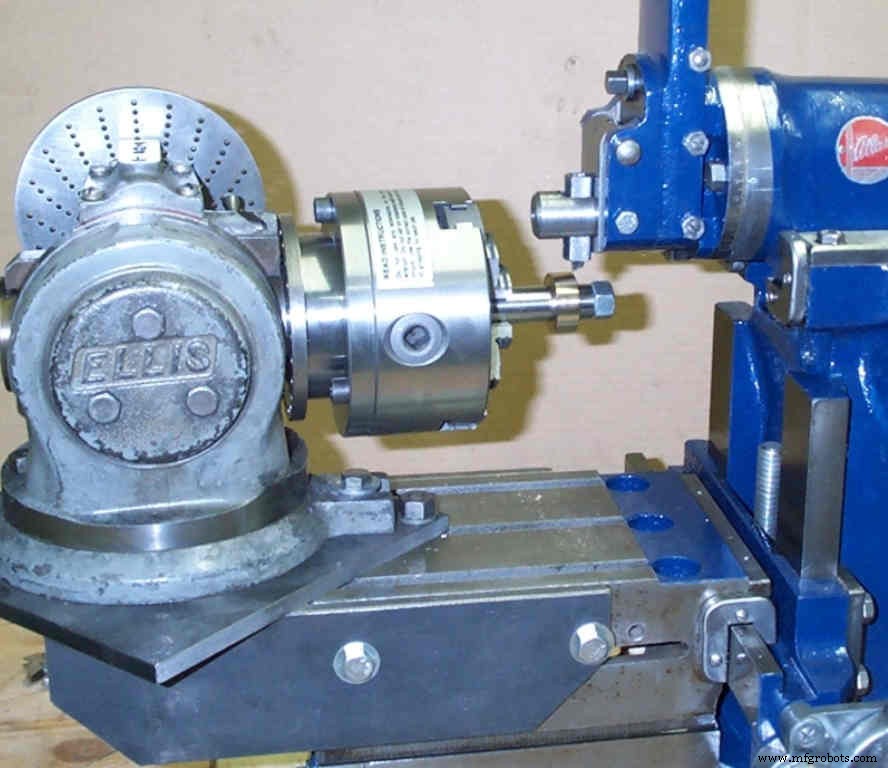
En el caso de la máquina cepilladora, la herramienta de corte de un solo punto permanece estática mientras la mesa que sostiene la rueda en blanco se mueve alternativamente pasando la herramienta. La profundidad de los dientes se ajusta mediante el movimiento del cabezal de la herramienta a lo largo del eje vertical. Después de cortar cada diente, la rueda gira en una dirección mediante la indexación.
Así, el nuevo diente se corta repitiendo las operaciones de movimiento alternativo de la herramienta o de la rueda en bruto. Esta secuencia se repite hasta que se fabrica el número requerido de dientes a lo largo de la periferia de la rueda en blanco.
Este método de corte de engranajes es rentable y económico, pero el principal inconveniente es que el método no es adecuado para la producción a gran escala debido a sus lentas acciones de corte. Por lo tanto, este método no se usa mucho para fabricar engranajes.
Comparación de corte de engranajes en máquinas perfiladoras, cepilladoras y ranuradoras:
Máquina moldeadora | Máquina cepilladora | Máquina ranuradora |
La rueda ciega del engranaje permanece estacionaria | La herramienta permanece estacionaria | La rueda ciega del engranaje permanece estacionaria |
La herramienta se desplaza más allá de la rueda en blanco | La rueda en blanco se mueve alternativamente más allá de la herramienta | La herramienta se mueve alternativamente más allá de la rueda en blanco |
La rueda ciega está montada en el mandril | La rueda en bruto se sujeta a la mesa de trabajo | La rueda en bruto se sujeta en un accesorio |
Menos profundidad de corte | Mayor profundidad de corte | Menor profundidad de corte |
3.1.3 Corte de engranajes en máquina brochadora con cortador formado:
El brochado es una operación de mecanizado realizada en máquinas brochadoras. La herramienta que se utiliza para la operación de brochado se llama 'brocha'. Este es un proceso muy rápido, aquí, la brocha de un grosor del engranaje se empuja o tira más allá de la superficie interior o exterior de la pieza de trabajo como se muestra en la fig. 1.5.
Este proceso tiene la capacidad de producir engranajes en un solo paso ya sea interno o externo. Este método es económico y rápido con un gran acabado superficial.
La única limitación de este método es que no se puede adoptar para producciones a pequeña escala debido a su costoso utillaje.
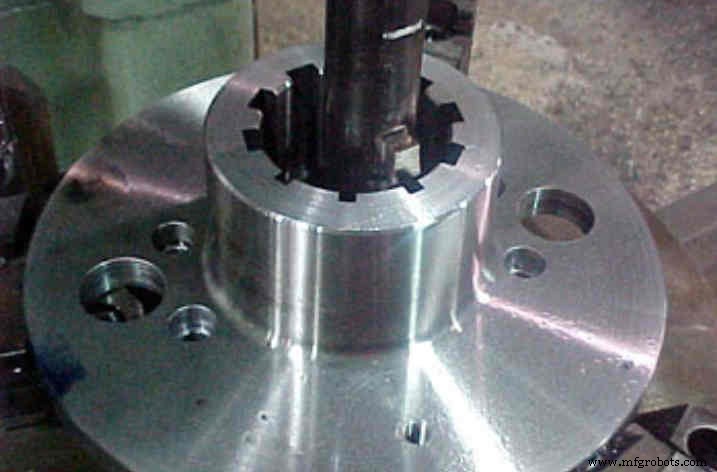
3.1.4 Corte de engranajes con hojas de herramienta de forma por proceso de velocidad de corte:
Como dice el propio título del método, este es un proceso rápido. El tallado de todos los dientes en una sola pasada o en dos o tres pasadas hace que este método sea exclusivamente rápido.
Este método es similar a la técnica de brochado, pero aquí, en lugar de una herramienta de corte de una sola punta, varias herramientas de corte están dispuestas radialmente de acuerdo con la cantidad requerida de dientes para cortar en la periferia de la pieza en bruto.
El proceso produce engranajes tanto en superficies internas como externas. Para cortar engranajes externos, la herramienta radial se monta alrededor de una cabeza hueca. Para cada golpe, la herramienta avanza con una profundidad de corte incremental.
Se proporciona una holgura a lo largo de cada carrera de retardo de la herramienta. Este método se puede adoptar para cortar grandes cantidades de engranajes rectos internos y externos, estrías, dientes de embrague y engranajes especiales.
Comparaciónde corte de engranajes por proceso de brochado y proceso de velocidad de corte:
Método de brochado | Método de velocidad de corte |
Solo se utiliza una herramienta de un solo punto | Se utilizan varias herramientas de las mismas dimensiones |
Se utiliza la herramienta Broach | Se utiliza la herramienta de forma radial |
Se corta un diente para una pasada | Todos los dientes se cortan en una sola pasada |
Proceso rápido | Proceso más rápido |
Costo comparativamente bajo | Herramientas comparativamente de alto costo |
3.2 Generación de engranajes:
En esta era automatizada, la mayor cantidad de engranajes se fabrican mediante el "proceso de generación de engranajes". Los procesos de generación de engranajes básicos e importantes son:
- Corte de engranajes por proceso de tallado.
- Corte de engranajes por proceso de planificación de cremalleras.
- El proceso de tallado de engranajes.
3.2.1. Corte de engranajes por proceso Shaper:
La operación del moldeador de engranajes se puede realizar en dos métodos diferentes. Uno es el método de "cortador moldeador de engranajes giratorios" y el otro es el método de "cortador moldeador tipo cremallera". El principio básico del tallado de engranajes es el mismo para ambos procesos.
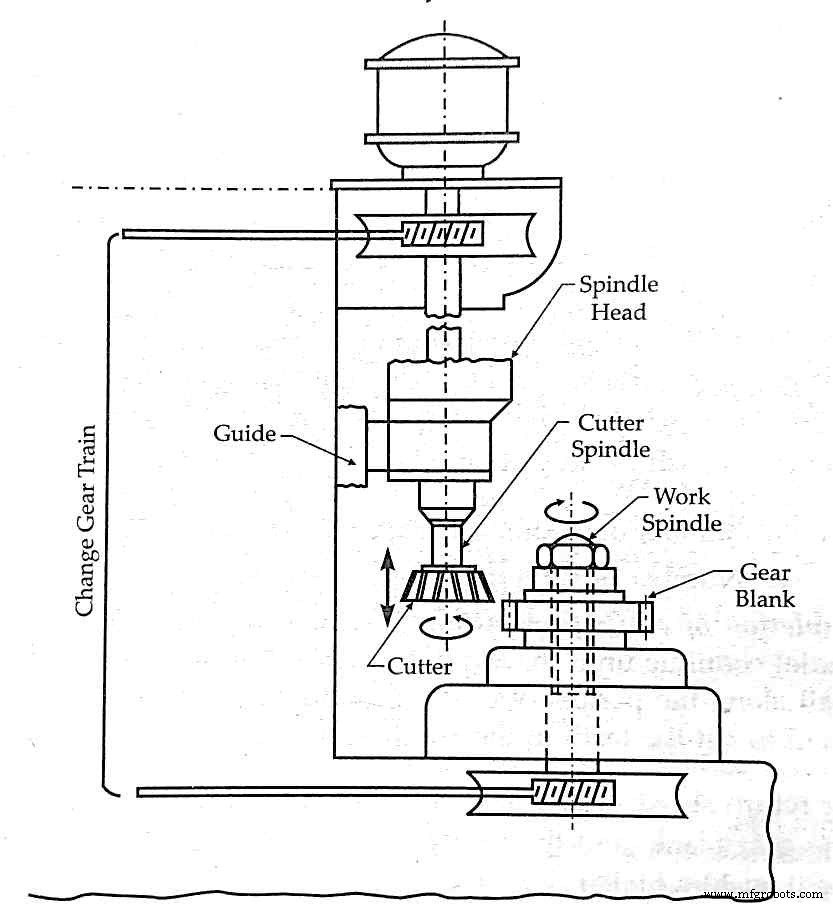
En este proceso, la pieza en bruto del engranaje se atornilla al eje del husillo mientras que el cortador se monta en un eje corto. El eje de esta máquina tiene dos ejes de movimiento. Un movimiento vertical o alternativo y el segundo es rotatorio.
Aquí, se usa un cortador en forma de piñón para trazar el metal de la rueda en blanco. El cortador está diseñado con un espacio libre en la cara y los lados del diente.
Para cortar el diente, el cortador se mueve en vaivén a lo largo del eje vertical en contacto con la rueda en blanco, por lo que se elimina el metal de la rueda en blanco. El movimiento lineal hacia abajo del cortador en el que se corta el metal se denomina movimiento de corte. y el movimiento lineal ascendente del cortador para retirar este último se denomina carrera de retorno .
No se elimina metal en los golpes de retorno. Junto con cada corte, se da una velocidad relativa de rotación al cortador y la rueda en blanco. La lenta rotación relativa entre ellos se llama feed de indexación .
Los trenes de engranajes conectados entre el eje del árbol y el eje del husillo giran el cortador y la rueda ciega lentamente en direcciones opuestas entre sí para lograr el movimiento de indexación como se ilustra en la figura 1.6.
La indexación y la acción recíproca del cortador continúan hasta que se corta el número requerido de dientes en la rueda en blanco.
En el caso de cortador de engranajes giratorios , el cortador utilizado para decorar los engranajes a lo largo de la periferia de la rueda ciega es un piñón giratorio como se ilustra en la fig.1.7.
El diente en el cortador es del mismo número que se cortará en la rueda en blanco. Este método se usa ampliamente para generar engranajes debido a su mayor rendimiento y la capacidad de cortar todo tipo de engranajes, excepto tornillos sin fin y ruedas helicoidales.
El cortador de engranajes rotativos también se puede adaptar para cortar engranajes internos con el mismo principio de funcionamiento. Las máquinas formadoras de engranajes rotativos están ampliamente disponibles en tipos de husillo vertical y horizontal.
Por lo general, las máquinas cortadoras y moldeadoras de engranajes rotativos horizontales tienen dos ejes potentes. Cada uno corresponde dentro y fuera el uno hacia el otro.
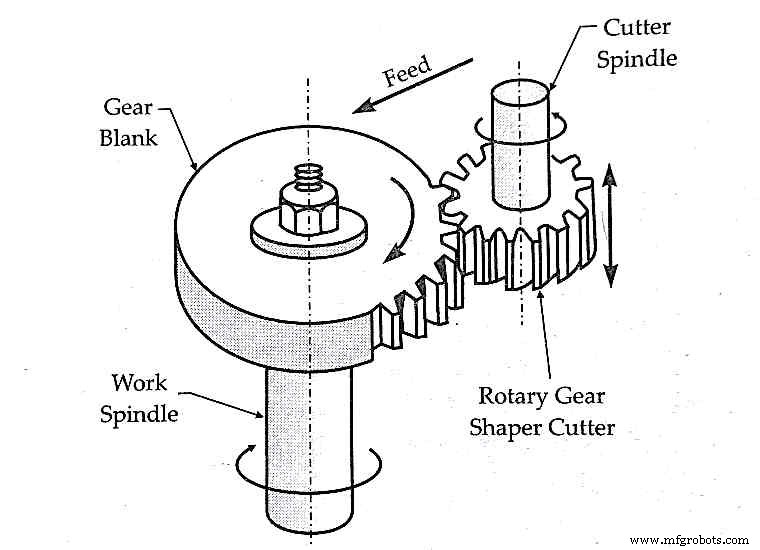
En el cortador moldeador de engranajes tipo cremallera método, se utiliza un cortador tipo cremallera para quitar el metal de la rueda en blanco y hacer los dientes. El principio de funcionamiento es el mismo que el principio básico de la cortadora de engranajes.
Implica la rotación de la rueda ciega dentada mientras que el cortador tipo cremallera se mueve alternativamente a lo largo del eje vertical como se ejemplifica en la fig. 1.8.
La mayor limitación de este método de generación de engranajes tipo cremallera es que el mecanizado debe pausarse cada vez que se utiliza la longitud total de la cremallera, es decir, todos los dientes de la fresa se utilizan para restablecer la posición al primer diente de la fresa. Si bien la mayor ventaja es que se puede hacer cualquier engranaje de cualquier número de dientes.
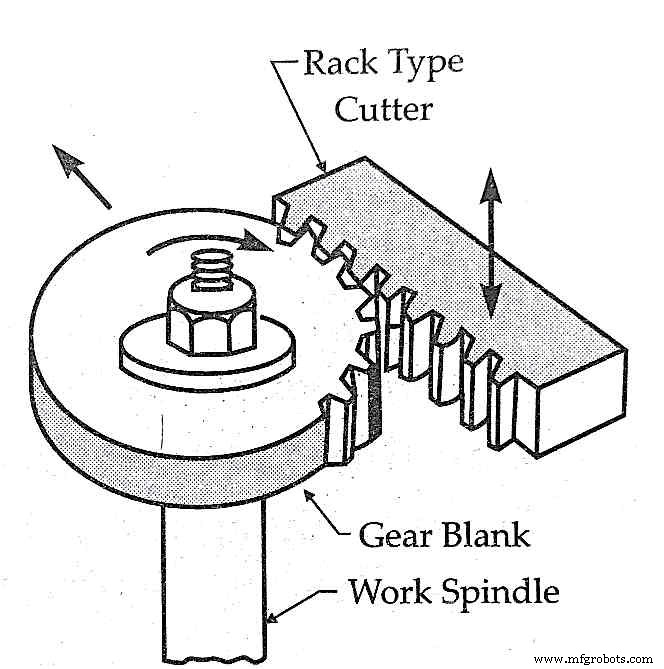
3.2.2 Corte de engranajes mediante el proceso de cepillado de cremallera:
Este proceso se utiliza principalmente para fabricar engranajes de dientes envolventes. Los engranajes rectos y helicoidales son los tipos de engranajes que se pueden fabricar con este método.
Los engranajes por este proceso se pueden hacer en dos máquinas diferentes; Sunderland y el Maag. Ambas máquinas funcionan con el mismo principio de corte, mientras que la construcción es diferente.
En el proceso de planificación de la cremallera, la rueda ciega se atornilla en el husillo del eje horizontal, mientras que el cortador tipo cremallera se atornilla en el eje. Para cortar dientes envolventes en la rueda en blanco, la rueda en blanco se mantiene estática mientras el cortador se mueve alternativamente en las direcciones de avance y retroceso.
El cortador traza dos dientes completos y dos dientes parciales como se muestra en la fig. 1.9. y 1.10.
Se elimina una pequeña cantidad de metal en cada movimiento hacia adelante y hacia atrás. Este tipo de trazado inadecuado de los dientes genera dientes de perfil involuntario. Luego, la pieza en bruto del engranaje se alimenta gradualmente hacia el cortador tipo cremallera, este movimiento hace que los dientes del cortador penetren en la periferia de la rueda en bruto.
A medida que penetran en la pieza en bruto, se da un avance giratorio lento o un avance de indexación a la rueda en bruto, lo que da como resultado la generación de dientes. El principio de generación de dientes de perfil envolvente es como se muestra en la fig. 1.9.
La misma secuencia de operaciones se repite hasta que se hace el número requerido de dientes en la periferia de la rueda en bruto.

3.2.3 Corte de engranajes en el proceso Sunderland:
Este proceso lleva el nombre de su inventor 'Sunderland'. El proceso funciona según el mismo principio discutido anteriormente, el proceso de planificación de bastidores. Además, aquí, en este proceso, el cortador también se mueve junto con el engranaje en bruto y luego se retira repentinamente y retrocede en la misma cantidad a una distancia de paso.
Este movimiento ocurre después de lograr la profundidad requerida del diente. Se hace una disposición de un tren de engranajes para sincronizar el movimiento del cortador y la rotación de la pieza en bruto.
Una vez que el cortador vuelve a su posición, se repite la misma acción de vaivén seguida de la indexación de la pieza en bruto y el movimiento de la herramienta con una retirada repentina.
El principio esquemático de funcionamiento del proceso de Sunderland se ejemplifica en la figura 1.10. y 1.11.
En este método de generación de engranajes, el operador es libre de ajustar la velocidad de movimiento alternativo de la cortadora según el material.
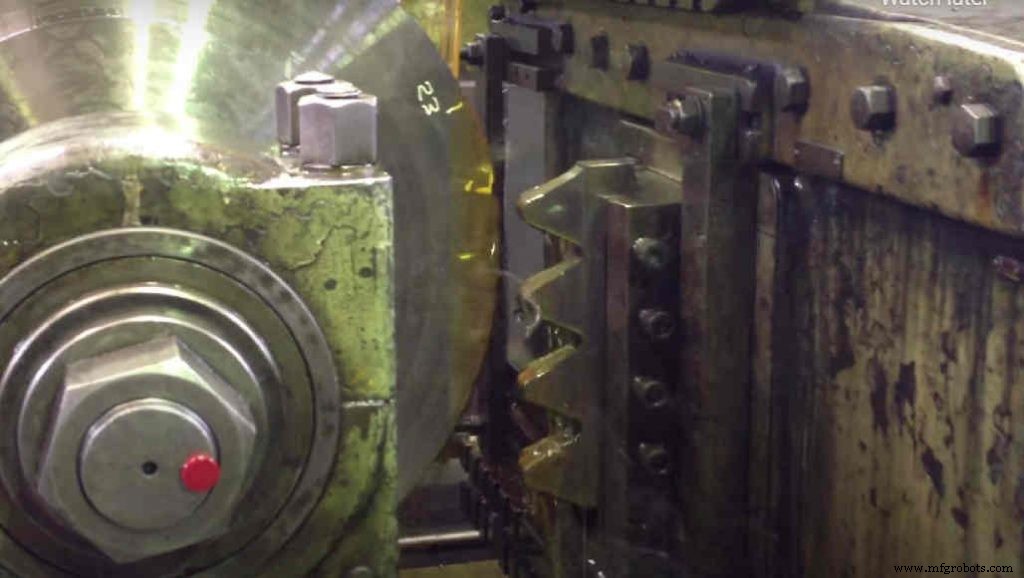
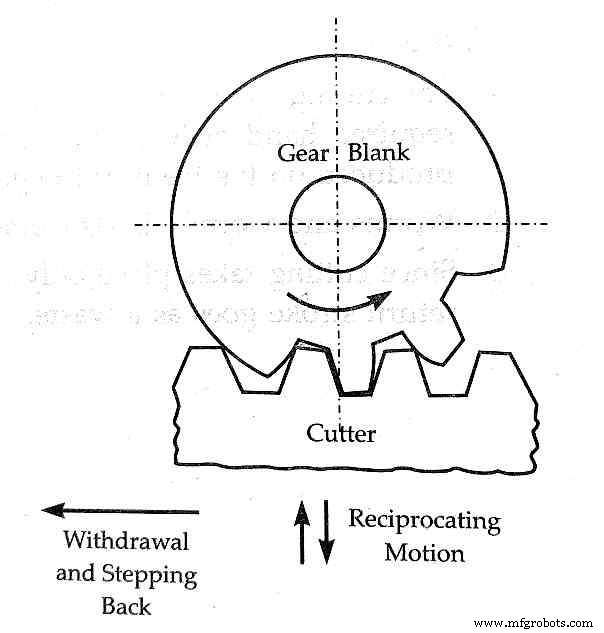
3.2.4 Corte de engranajes en el proceso Maag:
En este proceso, la rueda en blanco se monta en la mesa de trabajo con su eje vertical mientras que el cortador tipo cremallera se monta en una corredera. La corredera es libre de realizar movimientos alternativos a lo largo de su eje.
El proceso Maag también funciona según el principio del plano de cremallera. Además, el cortador se puede ajustar a cualquier inclinación en el plano vertical, por lo que el cortador puede cortar engranajes en cualquier dirección deseada. En la figura 1.12 se muestra una imagen industrial.
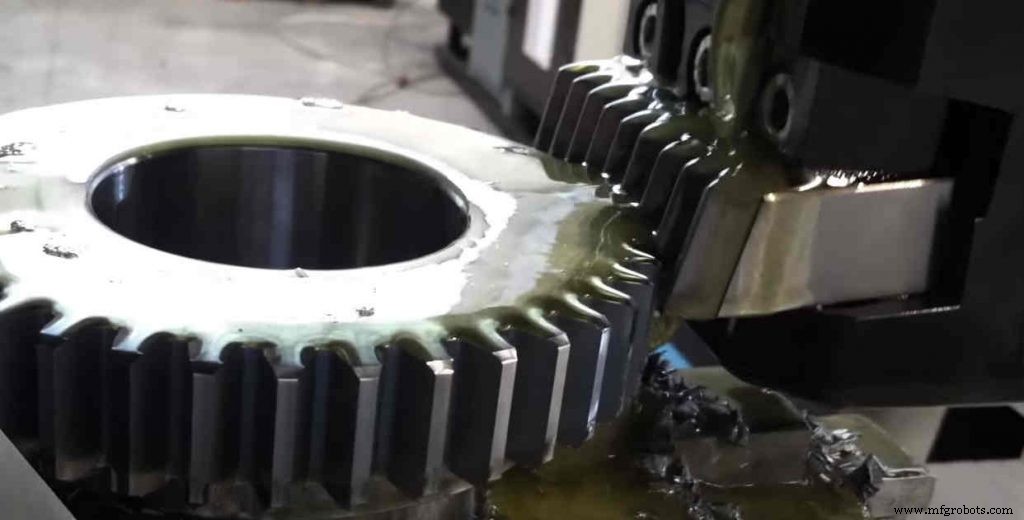
3.3.1 Proceso de tallado de engranajes o tallado de engranajes en una máquina talladora:
En este proceso, la rueda dentada en bruto gira contra un cortador rodante llamado hob. . Una vitrocerámica es una herramienta que parece un gusano pero lleva varias flautas rectas recortadas alrededor.
La encimera se monta en el eje mientras que la rueda ciega se monta en el husillo. El husillo tiene la libertad de moverse en dirección vertical, así como de girar alrededor de su eje central, como se ejemplifica en la figura 1.13.
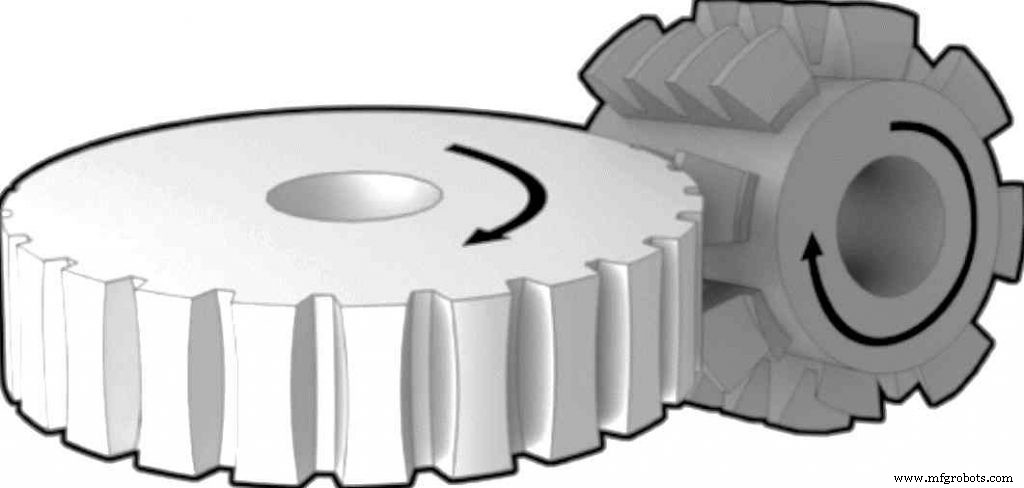
Este proceso se utiliza sobre todo para producir engranajes envolventes de todo tipo. En esta operación se le da a la placa una velocidad adecuada para que gire. Simultáneamente, también se hace que la pieza en bruto gire alrededor de su eje mediante una disposición de tren de engranajes.
Los dientes cortantes de la encimera graban el metal del blanco. Se cortan dientes de profundidad uniforme por cada rotación completa de la pieza en bruto. Una vez que la pieza termina su rotación, se aumenta la profundidad de los dientes y se repite el tallado.
Esta secuencia de operaciones se repite hasta lograr la profundidad de corte deseada. La pieza en bruto también se mueve hacia arriba y hacia abajo para producir cortes de profundidad uniforme junto con el grosor de la rueda.
En la fig. 1.14.
Este proceso puede producir engranajes en varias ruedas ciegas al mismo tiempo montando todas las ruedas una sobre otra.
El tallado se opera continuamente en el conjunto de ruedas en bruto hasta que se producen los engranajes en todas las ruedas. Para cortar engranajes helicoidales, el eje del husillo de la rueda ciega se inclina a un ángulo adecuado.
El método de tallado de engranajes se usa ampliamente en todo el mundo debido a su capacidad para producir una gran cantidad de engranajes de cualquier tipo en menos tiempo. La única limitación del tallado de engranajes es que no puede producir engranajes internos.
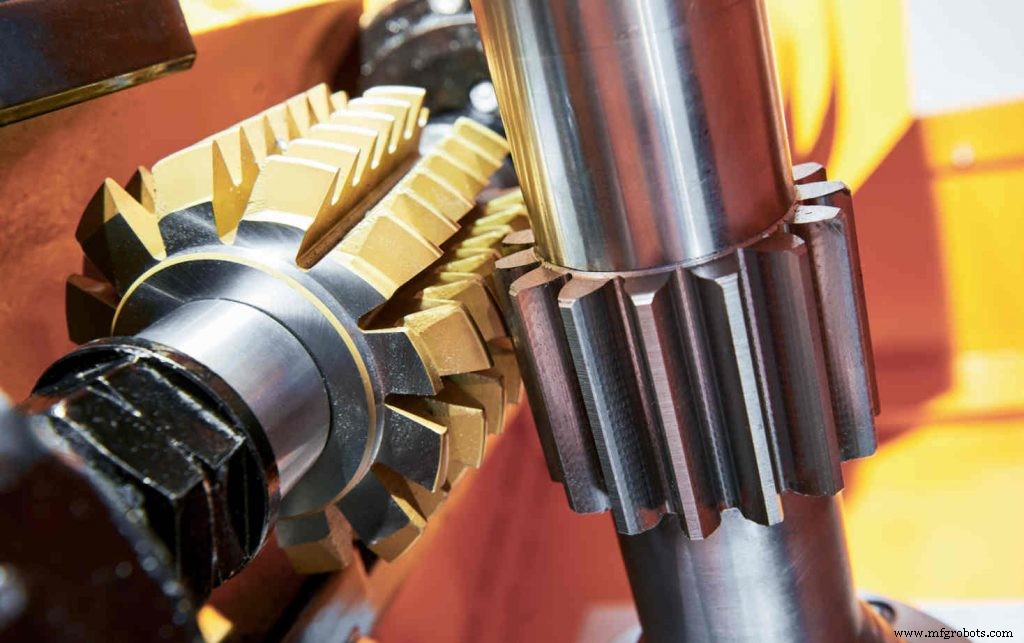
¿Por qué se usa mucho el proceso de tallado de engranajes?
- Este método es económico en comparación con otros procesos de generación.
- Este es un proceso más rápido y continuo.
- Se pueden producir todo tipo de engranajes.
- Se logran dimensiones precisas.
- Se pueden mecanizar varias piezas en bruto al mismo tiempo montándolas una sobre otra.
- Se puede cortar cualquier número de dientes con la misma placa.
Los engranajes producidos por todos los procesos de fundición, formación, corte y generación se envían para rasurado, bruñido, esmerilado y acabado antes de que encajen en cualquier maquinaria.
Tecnología Industrial
- ¿Qué es el suavizado? 6 tipos y métodos diferentes
- ¿Qué es la formación de virutas? - Tipos de virutas en corte de metales
- Tipos de procesos de mecanizado
- ¿Cuáles son los diferentes tipos de doblado de tubos?
- ¿Cuáles son los diferentes tipos de trabajadores de mantenimiento?
- ¿Qué es la velocidad de marcha?
- ¿Cuáles son los diferentes tipos de soldadura?
- ¿Cuáles son los diferentes tipos de prototipos?
- ¿Qué es la reducción de engranajes planetarios?
- ¿Qué son los reductores de engranajes rectos?
- Diferentes tipos de procesos de conformado de chapa