¿Qué es Formar? Tipos de proceso de formación [Notas y PDF]
El conformado es una de las técnicas de fabricación importantes en la ingeniería moderna. Casi muchos objetos que se utilizan en nuestra vida diaria se fabrican a partir de métodos o procesos de formación.
Algunos ejemplos son la bola utilizada en un bolígrafo, válvulas hidráulicas y neumáticas, recipientes para pasta de dientes, recipientes para cocinar, cadenas, aspas de ventilador , etc.
El conformado de metales se usa ampliamente en todo el mundo debido a sus ventajas positivas, como rentabilidad, propiedades mecánicas mejoradas, alta resistencia, mayor productividad y mejor ahorro de material.
El conformado ha encontrado sus aplicaciones en muchos campos, como las industrias aeroespacial, automotriz y de defensa.
Un vehículo automóvil típico utiliza piezas como las llantas, la carrocería, el chasis y las válvulas fabricadas mediante el método de formado.
En este artículo, estudiaremos qué es la formación y cuáles son los diferentes tipos de procesos de formación ? en detalle. Y a continuación, también veremos las ventajas, desventajas y aplicaciones .
Historial del proceso de formado
El descubrimiento de un colgante de cobre en el norte de Irak alrededor del 8700 a. C. se ha establecido como la primera operación conocida de minería y trabajo de metales industriales. La minería de cobre se ha documentado en las Américas desde 4000-5000 a. C. en el lago Michigan.
Los metales se volvieron cada vez más importantes para sus civilizaciones individuales con el tiempo, se volvieron esenciales para las operaciones de construcción y la metalurgia se convirtió en un componente importante de la sociedad.
El arte de trabajar con metal ahora abarca una amplia gama de profesiones e industrias.
El conformado y moldeado de metales es una especialidad para muchas personas. Desde la antigüedad, las técnicas han evolucionado significativamente y ahora las máquinas realizan la mayor parte del conformado de metales.
Por ejemplo, el perfilado se logra utilizando equipos de perfilado de alta calidad. La formación de rollos es un método para doblar una tira continua de metal en una forma determinada.
Una máquina formadora de rollos se compone de una serie de rollos que doblan el metal para darle forma en un movimiento continuo. Solo una pequeña porción del metal es doblada por cada par de rollos, también conocidos como hebras. El metal se lamina hasta que cumple con los requisitos.
La evolución de la metalurgia se puede ver en el arte de hacer rollos. El uso de una máquina perfiladora y otros equipos perfiladores son ejemplos de cómo la industria metalúrgica ha progresado a lo largo del tiempo.
¿Qué es el proceso de formación?
La formación de metales es un proceso de fabricación de componentes de las formas deseadas mediante la deformación plástica del material, mediante la aplicación de fuerza de compresión, fuerza de flexión o corte, fuerza de tracción o combinaciones de todas estas fuerzas juntas, sin agregar ni quitar material.
Tipos de proceso de formación
Proceso de formación se ha clasificado en dos grupos; Formado a granel y conformado de chapa .
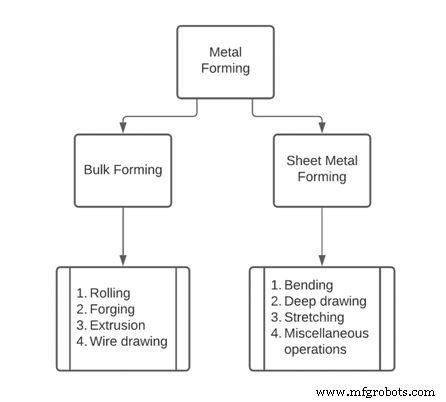
Además, la clasificación detallada del proceso de formación como se puede ver en el diseño de arriba.
Ahora vamos a conocer todos los tipos en detalle.
#1. Formación a granel
La formación a granel es un método para producir materiales en grandes volúmenes de productos cuya superficie es menor que la relación de volumen .
Aquí, para lograr el mecanizado, se procesan fuerzas de tracción, fuerzas de compresión, fuerzas de corte o una combinación de cualquiera de las dos.
Se realiza en maquinaria que cuenta con un juego de herramientas y troqueles. El uso de una herramienta y el troquel mismo nos hace entender que el troquel tiene la misma forma que el producto a producir y la herramienta se presiona contra el troquel para generar la forma en el material.
El conformado a granel involucra procesos denominados Laminación, Forja, Extrusión y Dibujo como sus procesos de trabajo.
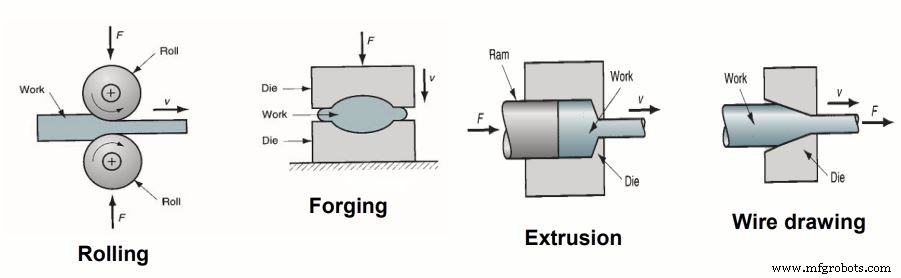
1.1 Rodando
El laminado es un proceso de formación típico que se utiliza para fabricar productos semiacabados, como varillas, láminas y placas, y productos terminados, como ángulos, perfiles en U y perfiles. El enrollado se puede hacer tanto en frío como en caliente.
En este proceso, el tocho en forma de planchón se comprime entre dos rodillos que giran en dirección opuesta, lo que reduce el grosor del tocho y le da una nueva forma. Los rodillos giratorios empujan la losa hacia el espacio y la comprimen. El producto final es el tamaño reducido de la palanquilla.
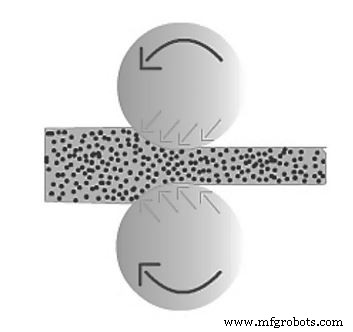
A lo largo del tiempo ha evolucionado una variedad de trenes de laminación para la producción de artículos de diferentes formas. Cada uno se describe a continuación.
1.2 Laminador de dos-altos
El tren de laminación de dos alturas está construido a partir de tres soportes separados con dos rodillos horizontales apilados uno encima del otro.

Uno o ambos rodillos son ajustables en este tipo de molino. El metal pasa entre dos rodillos que giran a la misma velocidad pero en diferentes direcciones durante la operación.
1.3 Laminador de tres-altos
En el caso del tren de laminación de tres alturas, hay tres rodillos, uno encima del otro. Se utilizarán dos rollos a la vez para una sola pasada. En este caso, la dirección de balanceo no se verá alterada.
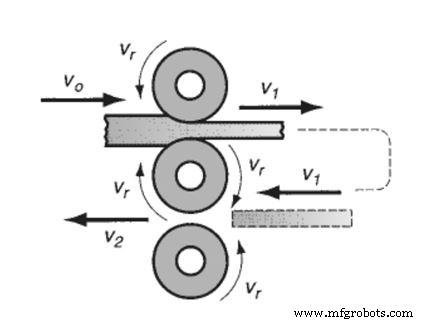
La lámina se reubicará en los dos rollos inferiores para una mayor reducción una vez que se hayan utilizado los dos rollos superiores para la primera reducción. Este ciclo se repite hasta lograr la disminución deseada.
1.4 Four-High Rolling Mill
El tren de laminación de cuatro alturas consta de dos rodillos pequeños que se utilizan para reducir el espesor y dos rodillos de respaldo grandes que se utilizan para soportar los rodillos pequeños.
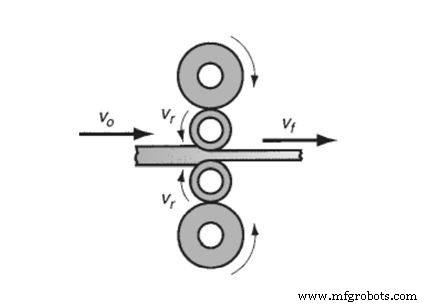
Debido a que el área de contacto entre la hoja y el rollo se reduce con los rollos cortos, se reduce la fuerza del rollo requerida.
Los rodillos de apoyo grandes son necesarios para disminuir la desviación elástica de los rodillos pequeños cuando la hoja pasa entre ellos.
1.5 Molino de racimo
Un Cluster Mill se compone de dos rodillos operativos y cuatro o más rodillos de respaldo.
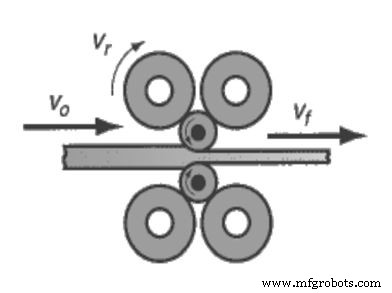
El número de rodillos de apoyo o de apoyo necesarios está determinado por la cantidad de apoyo necesaria para los rodillos de trabajo (diámetro pequeño). Los molinos de racimo se emplean normalmente en operaciones de laminación en frío.
1.6 Ring Rolling
El laminado de anillos es un método de formación que consiste en laminar un componente de anillo de paredes gruesas de un diámetro más bajo en un anillo de paredes delgadas de un diámetro mayor.

A medida que se comprime el anillo de paredes gruesas, el material deformado se alarga, lo que hace que aumente el diámetro del anillo.
1.7 Forja
La forja es un método de formación a granel en el que se aplican fuerzas de compresión y tracción a una pieza de trabajo o palanquilla para convertirla en un producto final utilizando un par de herramientas llamadas matriz y punzón.
Se pueden usar matrices abiertas o cerradas para forjar. En la mayoría de los casos, la forja con matriz abierta se utiliza para dar forma a las materias primas en una forma adecuada para su posterior conformado o mecanizado.
En este proceso, el tocho se comprime entre dos troqueles. Los troqueles contienen un contorno moldeado que se va a generar en el producto final. Al comprimir la palanquilla entre un par de troqueles, se imparte la forma a la palanquilla, obteniendo así el producto final.
1.7.1 Forja en matriz abierta
Para operaciones tales como estirado, adelgazamiento, etc., las piezas forjadas con troquel abierto se realizan con un par de troqueles de cara plana.
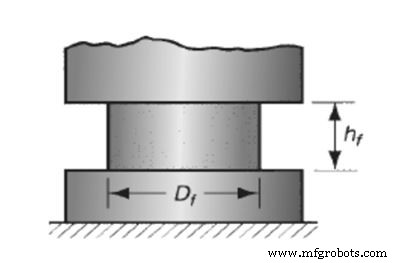
La forja de matriz abierta es una tecnología vital en una variedad de industrias.
Permite el desbastado y acabado de metales, sobre todo acero y aleaciones de acero. Requiere un troquel con lados abiertos que permita que la pieza de trabajo se mueva libremente de manera lateral cuando se golpea. Este diseño también permite forjar piezas muy grandes.
1.7.2 Forja en matriz cerrada
La forja con troquel cerrado se logra comprimiendo un tocho de materia prima en una cavidad producida entre dos troqueles con forma.
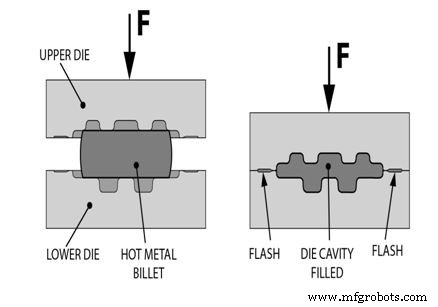
La forma de la cavidad del troquel se logra formando productos. El moldeado cerrado se utiliza para fabricar piezas de válvulas, piezas de bombas, engranajes diminutos, bielas, llaves y otros elementos.
1.7.3 Acuñación
El proceso de acuñación es la aplicación de tensión de compresión a la superficie de la materia prima para impartir formas únicas desde el punzón de estampado.
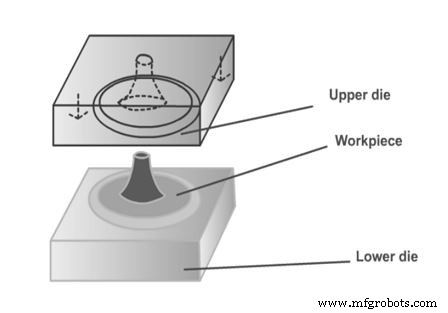
Ejemplos son monedas y medallones de metal impreso.
1.7.4 Impresión de forja en matriz
En la forja por matriz de impresión, las superficies de la matriz tienen una forma que se imparte a la pieza de trabajo durante la compresión, lo que restringe en gran medida el flujo de metal. El material distorsionado adicional fuera de la impresión del troquel se denomina rebaba. Esto se eliminará más tarde.
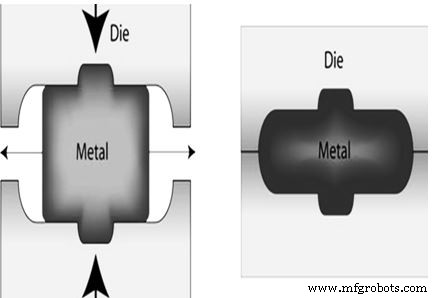
La forja de troqueles de impresión es incapaz de producir productos con tolerancias estrictas.
Para lograr las precisiones requeridas, generalmente se requiere maquinado.
El proceso de forjado produce la forma fundamental del artículo, con mecanizado adicional realizado en aquellas partes de la pieza que requieren un acabado de precisión, como agujeros y roscas.
1.7.5 Flashless Forja
En la técnica Flash Less Forging, la pieza de trabajo está totalmente limitada dentro del dado en la forja sin flash y no se produce flash. La cantidad de pieza de trabajo inicial utilizada debe administrarse con precisión para que coincida con el volumen de la cavidad del troquel.
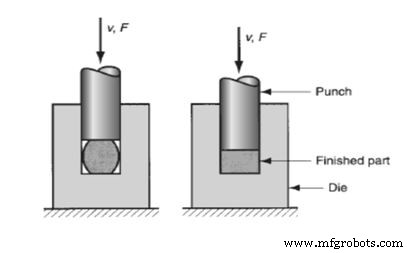
Esta técnica de forjado sin rebabas es apropiada para fabricar piezas geométricas básicas y simétricas, así como materiales de trabajo como Al, Mg y sus aleaciones, debido a las demandas.
1.7.6 Forja de rodillos
La forja con rodillos es un método de conformación que se utiliza para disminuir la sección transversal de una varilla cilíndrica o rectangular pasándola a través de un conjunto de rodillos opuestos con ranuras coincidentes en relación con la forma deseada del artículo terminado. Aunque también combina laminado y forjado, se clasifica como una operación de forjado.
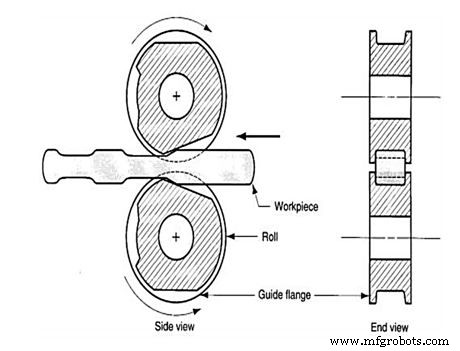
En este proceso, los rodillos giran en parte dependiendo del grado de deformación. Los productos laminados suelen ser más fuertes y tienen la estructura de grano requerida en comparación con el mecanizado del mismo artículo.
1.7.7 Forja orbital
En la forja orbital, la forma se imparte al material en este método mediante un troquel superior en forma de cono que se enrolla y empuja sincrónicamente en el trabajo. Se utiliza un troquel inferior para apoyar el trabajo.
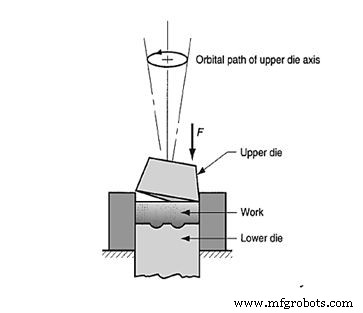
Debido al eje inclinado del cono, solo una pequeña porción de la superficie de la pieza de trabajo se comprime en cualquier punto del proceso de formación.
La región bajo compresión forma círculos a medida que gira el dado superior. Hay una reducción significativa en la demanda de carga de la prensa causada por el contacto de tensión parcial en cualquier paso de la formación.
1.7.8 Forja isotérmica
La forja isotérmica es una técnica de forja en caliente en la que el trabajo se mantiene a una temperatura alta durante el proceso de formación. Los troqueles de forja también se mantienen a la misma temperatura alta. Al eliminar la frialdad del trabajo que entra en contacto con las superficies frías del troquel, el metal fluye más fácilmente y se reduce el esfuerzo requerido.
La técnica es más costosa que la forja tradicional y generalmente se usa para metales difíciles de forjar como Ti, superaleaciones y formas de componentes complicadas. Para evitar una rápida oxidación del material de la matriz, la operación se realiza en vacío o ambiente inerte.
1.8 Extrusión
La extrusión es un procedimiento de formación a granel que consiste en forzar o comprimir el metal de trabajo a través de un orificio de troquel para producir la forma de sección transversal deseada.
La extrusión se distribuye típicamente en dos formas de trabajo. Uno como extrusión directa o hacia adelante y el otro como extrusión indirecta o hacia atrás.
1.8.1 Extrusión directa o forward
En la extrusión directa, primero se carga un tocho de metal en el contenedor. El recipiente tiene un orificio de troquel de contorno conformado. Luego se usa un ariete para forzar el tocho de metal a través del orificio del troquel para producir el artículo.
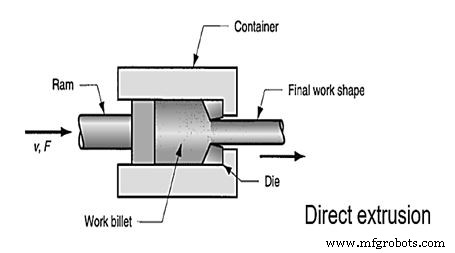
Los productos extruidos incluyen tubos, latas, copas, engranajes de tamaño pequeño, ejes, etc.
Siempre queda una parte del tocho al final de cada extrusión y se llama tope.
1.8.2 Extrusión indirecta o hacia atrás
En lugar de montarse en el contenedor, la matriz se monta en el ariete. El metal fluye a través del orificio de la matriz en el lado del ariete en la dirección opuesta al movimiento del ariete mientras es comprimido por el ariete.
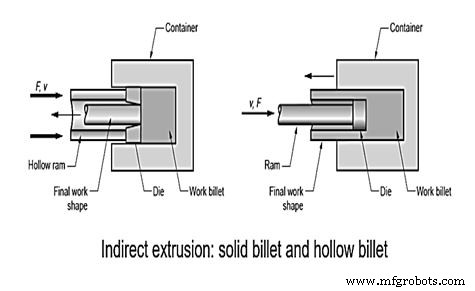
No hay fricción en el contacto ya que no hay movimiento relativo entre la palanquilla y el contenedor, por lo que la fuerza del ariete es menor que en la extrusión directa.
1.9 Trefilado:
El proceso de trefilado se utiliza para fabricar alambres de diámetro pequeño a partir de varillas reduciendo su diámetro y estirando su longitud con fuerza de tracción.
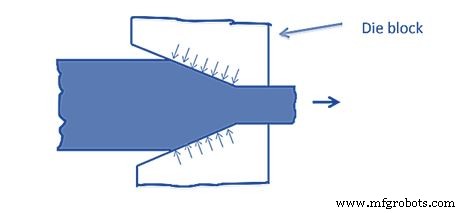
El trefilado se utiliza para fabricar cuerdas musicales. El dibujo de tubos se puede utilizar para crear tubos sin costura.
En este proceso, se tira de una varilla o barra a través de un orificio de troquel para formar el grosor deseado de alambre, reduciendo su área de sección transversal.
2. Extrusión por impacto
La extrusión por impacto se realiza siempre en frío. La extrusión por impacto hacia atrás permite paredes muy delgadas. Fabricación de tubos de pasta de dientes, por ejemplo, o cajas de pilas.
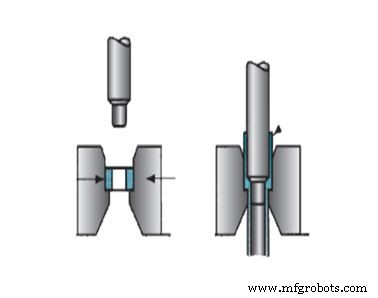
Se realiza a velocidades más rápidas y con golpes más cortos. La presión de impacto, en lugar de ejercer presión, se usa para extruir el tocho a través de la matriz. Sin embargo, el impacto se puede lograr mediante extrusión hacia adelante o hacia atrás o una combinación de ambas.
2.1 Extrusión hidrostática
En la técnica de extrusión hidrostática, el tocho está rodeado de fluido dentro del contenedor durante el proceso y el fluido es presionado por el movimiento hacia adelante del ariete. Debido al fluido, no hay fricción dentro del recipiente y la fricción en el orificio de la matriz es mínima. Se deben emplear fluidos y métodos especiales mientras se trabaja a altas temperaturas.
La ductilidad de un material aumenta cuando hay presión hidrostática sobre él y no hay fricción. Como resultado, este enfoque se puede utilizar en metales que son demasiado frágiles para los procedimientos de extrusión tradicionales.
Este método se utiliza en metales dúctiles, con grandes relaciones de reducción concebibles.
#2. Conformado de chapa
El conformado de láminas de metal implica la aplicación de fuerzas de tracción y cizallamiento para fabricar láminas, placas y tiras con la forma posible deseada utilizando un conjunto de herramientas. El punzón y la matriz se utilizan como herramientas en el proceso de fabricación.
El conformado de láminas de metal está asociado con las operaciones; Doblado, estirado, cizallado, troquelado y punzonado para producir los materiales.
El método de formación de láminas utiliza técnicas de deformación de láminas de plástico, como embutición profunda, corte, doblado, dobladillo, rebordeado, rizado, estirado/estiramiento, estampado.
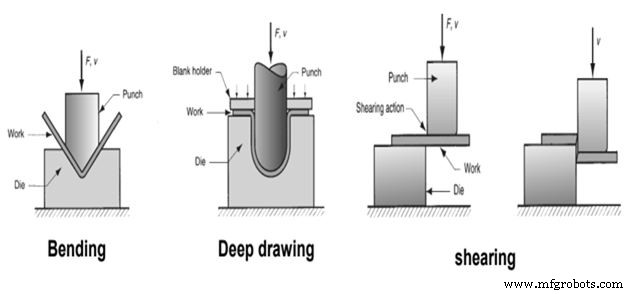
2.1 Dibujo profundo:
La embutición profunda es un proceso de lámina de metal en el que la lámina de metal se fuerza en una copa de forma hueca usando fuerzas de tracción y compresión sin cambiar su espesor.
En este proceso, la lámina se coloca sobre la abertura del troquel y se empuja con un punzón. Se utiliza un soporte en blanco para mantener la hoja plana sobre la superficie del troquel.
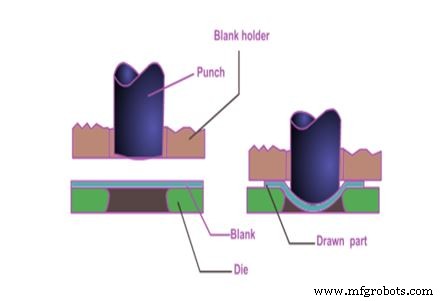
En muchos casos, la alteración requerida para crear esa parte será sustancial (la relación de estirado es muy alta). En tales casos, la formación completa de la pieza requiere más de un paso de embutición profunda.
Cualquier paso de dibujo adicional requerido para completar la operación de dibujo se conoce como Redibujado.
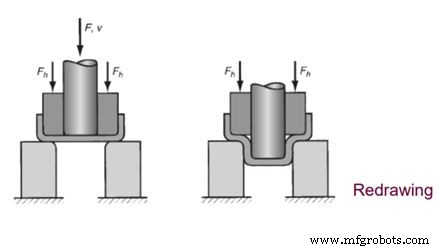
2.2 Doblado de hojas:
La flexión de láminas se define como la deformación del metal alrededor de un eje recto. El metal del borde interior del plano neutro se comprime mientras que el metal de los bordes exteriores del plano neutro se estira durante la operación de doblado. El grosor de la chapa no cambia como resultado de la flexión.
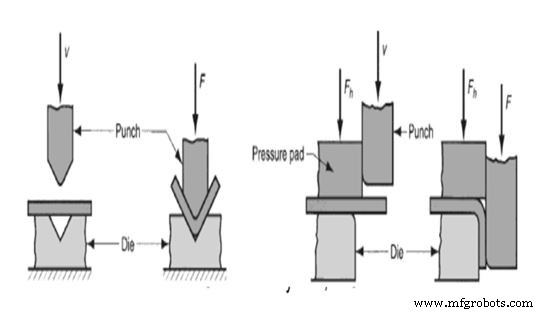
2.3 Estiramiento o estirado formado:
El conformado por estirado es un proceso de conformado de láminas de metal en el que la lámina de metal se estira y dobla intencionalmente al mismo tiempo para cambiar su forma.
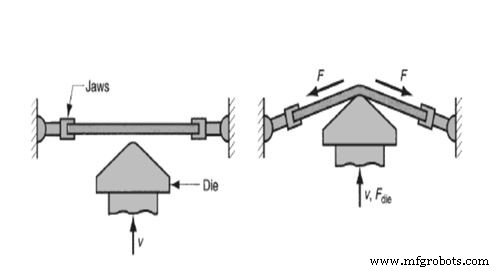
La lámina se sujeta por ambos extremos mediante mordazas o tiradores y luego se estira con un punzón, lo que hace que la lámina se estrese por encima de su límite elástico y se fabrique con la forma deseada.
El metal se ha distorsionado plásticamente cuando se libera la deformación. El impacto combinado de estirar y doblar hace que la pieza tenga una menor recuperación elástica.
Video conferencia sobre el proceso de formación de metales:
Aplicaciones del proceso de formación de metales:
La técnica de formación de metales se utiliza para producir tubos sin costura, varillas y anillos de turbina. También se utiliza para crear hornos de cemento.
Este proceso de formación se puede utilizar para crear cojinetes, placas, láminas de acero y numerosos componentes para un automóvil.
Este método también se utiliza para fabricar componentes de misiles y aeronaves y también para fabricar bisagras, pernos y clavos.
Ventajas del proceso de formación de metales:
Las siguientes ventajas de los procesos de formación son de la siguiente manera:
- Artículos con mayor resistencia.
- Mucho menos desperdicio de material.
- Se pueden fabricar componentes más pequeños con alta resistencia.
- Los artículos producidos tienen dimensiones precisas.
- Tasa uniforme de formación.
- Excelente acabado superficial.
- Menos tiempo de mecanizado en comparación con el método de extracción de metal convencional.
- Propiedades mecánicas mejoradas.
Desventajas del proceso de formación de metales:
Las siguientes desventajas de los procesos de formación son de la siguiente manera:
- El requerimiento de Poder es alto.
- Hay un requisito de fuerzas mecánicas altas.
- El endurecimiento por deformación del material de trabajo es un límite para la cantidad de conformado.
- El material quebradizo no se puede fabricar en este proceso.
- También se utiliza el proceso de tratamiento térmico en la formación de metales algunas veces.
Tecnología Industrial
- ¿Qué es la formación de almohadillas de goma en el trabajo de metales?
- ¿Qué es el proceso de fabricación de chapa metálica?
- ¿Cuál es el proceso de fabricación de chapa metálica?
- ¿Qué es el estampado? - Tipos, operación y aplicación
- ¿Qué es Casting?- Definición| Tipos de fundición
- ¿Qué es el brochado? - Proceso, trabajo y tipos
- ¿Qué es la forja? Definición, proceso y tipos
- ¿Qué es el revestimiento de metal? - Definición, tipos y beneficios
- ¿Qué es la fundición de metales? Definición, tipos y procesos
- Proceso de formación de chapa
- ¿Cuáles son los 4 tipos de procesos de fabricación?