El dispositivo perimetral LIMS acelera la entrada en la producción y la competitividad de la Industria 4.0
Términos como fábrica inteligente, Industria 4.0 e Internet industrial de las cosas (IIoT) se han convertido en palabras de moda ineludibles, invocadas por todos los desarrolladores de equipos y software relacionados con la fabricación. Muchas discusiones sobre fábricas inteligentes comienzan con pronosticadores que comparten visiones de cómo se transformará la industria manufacturera global.
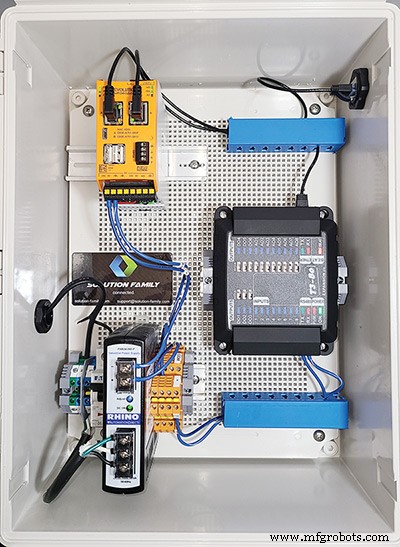
Estas descripciones a menudo se agrupan en tecnologías florecientes como la fabricación aditiva, la simulación visual en 3D y la robótica colaborativa. Todo esto puede parecer fuera del alcance del taller de trabajo promedio, y demasiado costoso para siquiera contemplarlo. ¿Quién realmente lo necesita?
Esa visión popular en toda la industria de la fabricación inteligente es, sin querer, engañosa, similar a responder a la pregunta:"¿Qué es un automóvil?" describiendo el sistema de carreteras interestatales. En ambos casos, la idea central es mucho más simple, y la respuesta a la pregunta de quién necesita realmente la fabricación inteligente es, enfáticamente, el taller de trabajo promedio y cada fabricante que quiera seguir siendo competitivo en el futuro.
Definición de los términos
Una forma útil de entender la fábrica inteligente es comenzar con una tecnología comparativamente simple:el sensor electrónico económico. En el mundo de los sensores previos, el operador de la máquina programa un torno o fresadora CNC para cortar una pieza y la máquina hace todo lo posible para seguir las instrucciones y eliminar el metal. La comunicación es unidireccional, del operador a la máquina.
¿La máquina siguió con precisión las órdenes? A menos que se produzca un desastre obvio, como un accidente, el fabricante no lo sabrá a menos que inspeccione la pieza después de completar la operación, lo que lleva tiempo y cuesta dinero.
Introduzca el sensor. Los sensores modernos colocados estratégicamente en el centro de mecanizado pueden permitir la comunicación bidireccional. Los sensores permiten que la máquina registre o comunique información sobre su propio estado y el estado de la operación mientras trabaja. La medición de vibraciones, la variación de temperatura, el análisis de corriente del motor y otros factores se pueden compartir a través de una red para monitoreo y análisis. El estado de la máquina y cómo ese estado afecta la operación se puede evaluar rápidamente, incluso en tiempo real.
Donde el sensor se encuentra con la máquina es donde el caucho se encuentra con la carretera en el IIoT. Los nuevos equipos de producción generalmente están equipados con sensores apropiados, pero se pueden instalar en equipos más antiguos a un costo relativamente bajo.
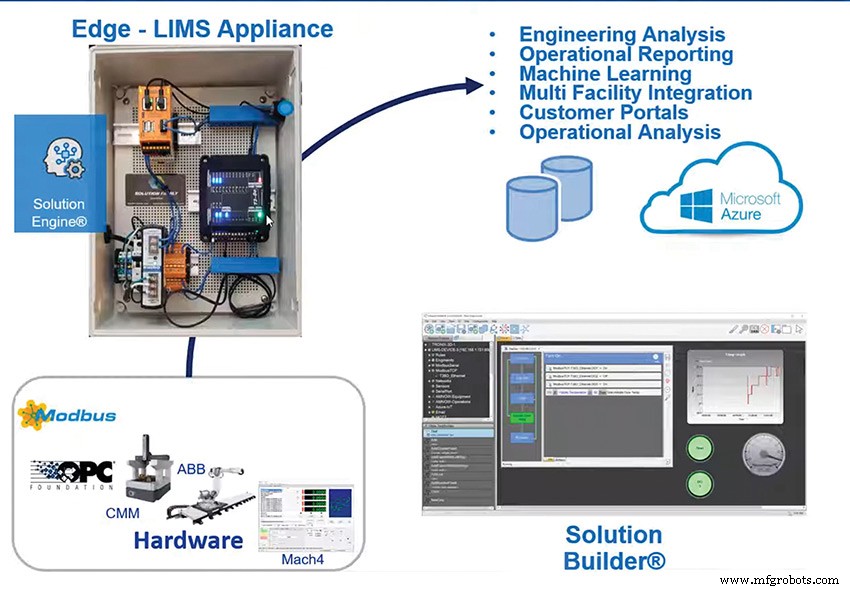
Las máquinas habilitadas con sensores tienen mucho que decir, más de lo que un usuario puede saber qué hacer. Pero el software de análisis puede analizar los datos y usarlos para mejorar la operación, mantener la máquina, mejorar el diseño del producto e incluso mejorar el diseño del propio equipo de mecanizado.
Este mismo enfoque de comunicación bidireccional se ha ampliado para crear células de fabricación inteligentes, con automatización y varias máquinas. Aléjese aún más e imagine una instalación completa conectada en red de esta manera, con los datos de fabricación accesibles y utilizables en silos anteriormente separados, comparable a la forma en que se han convertido los datos de planificación de recursos empresariales (ERP).
Esa atractiva visión de una planta de fabricación en la que el equipo puede compartir datos con personas y otros equipos para permitir una producción de piezas y productos más rápida, de mayor calidad y en constante mejora, es la fábrica inteligente.
Pero puede comenzar extrayendo datos derivados de sensores de una sola máquina y usándolos para mejorar su funcionamiento.
Avanzando hacia la fabricación inteligente con LIMS
"Industria 4.0 se trata realmente de cómo puede usar los datos para operar mejor su negocio", dijo Larry Megan. "Y si no tiene los datos, entonces no tiene por dónde empezar".
Megan es vicepresidenta de Advanced Manufacturing International (AMI), Clearwater, Fla., una organización sin fines de lucro con la misión de ayudar a los pequeños y medianos fabricantes (SMM) a comenzar este viaje:la "transformación digital", como se sabe.
“Los problemas que los fabricantes están tratando de resolver son los mismos problemas que la gente ha estado tratando de resolver durante 100 años”, señaló:“‘¿Cómo puedo aumentar la eficiencia? ¿Cómo reduzco el consumo de energía? ¿Cómo maximizo el rendimiento? ¿Cómo abordo los problemas de calidad? Lo que ha cambiado es que ahora tenemos tecnología para hacer visibles rápidamente los datos que pueden proporcionar las respuestas para que puedan usarse como punto de partida para tomar mejores decisiones”.
El trabajo de Megan y AMI con SMM a menudo incluye recomendar el uso de un dispositivo desarrollado por LECS Energy llamado LIMS Appliance.
LIMS, que significa Sistema de fabricación de baja inversión, es una pequeña caja sin pretensiones que consta de una computadora con el software Solution Engine patentado, un concentrador de E/S (entrada/salida) y una fuente de alimentación de 110 V que se conecta a un tomacorriente estándar. Cuando se conecta al borde de un equipo de producción, se convierte en una solución simple para recopilar y compartir datos complejos derivados de sensores. (AMI realizará demostraciones en vivo del sistema LIMS en HOUSTEX, EASTEC, SOUTHTEC y WESTEC en octubre y noviembre. AMI es el distribuidor exclusivo de la caja LIMS).
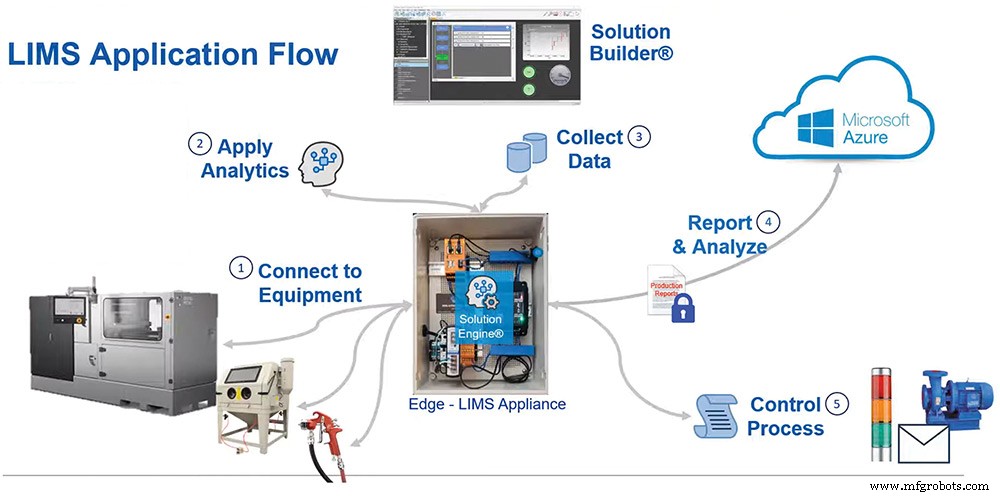
“Para muchos fabricantes, especialmente en el espacio de piezas discretas, automotriz, aeroespacial y otros, creemos que la solución LIMS es un excelente punto de incorporación”, dijo Megan. “Está diseñado para fabricantes que usan un CNC u otra máquina pero no tienen visibilidad sobre la productividad de esa máquina individual, o más ampliamente, lo que sucede en la planta. La solución LIMS es una manera fácil y de bajo costo para que las personas comiencen a obtener datos de sus procesos y los coloquen en un formato que sea útil. Y luego pueden empezar a tomar mejores decisiones con él”.
En palabras del desarrollador principal del dispositivo, Nat Frampton de LECS Energy, “LIMS fue diseñado para tratar de ayudar a los operadores e ingenieros a poder tocar su proceso, analizar y llegar a una nueva comprensión de su proceso:ser capaz de recopilar esos datos, mirarlos históricamente, interactuar o mover los datos a bases de datos y, finalmente, poder obtener los resultados de ese análisis y mejorar su proceso”.
Según Frampton, LIMS es un producto de 20 años de desarrollo, originalmente diseñado en torno a la fabricación de explosivos para el Ejército de los EE. UU. Un objetivo clave desde el principio fue que los usuarios sin conocimientos de programación especializados pudieran instalarlo y operarlo.
“Si comprende su propia operación, si puede trabajar con su equipo, ya tiene todas las habilidades informáticas que necesitará para poder configurar este dispositivo”, dijo Frampton.
El flujo de la aplicación LIMS
LIMS es capaz de realizar una gran variedad de tareas, pero se puede simplificar a un flujo de aplicación de cinco pasos. El primer paso es conectar el sistema a un determinado equipo de producción. El funcionamiento de esa conexión depende del equipo al que se conecte y de la configuración de red del taller, si es que tiene una. LIMS está diseñado para conectarse de la manera más eficiente posible, dependiendo de esas variables.
“LIMS se basa en estándares abiertos”, dijo Frampton. “Entonces, si se está conectando a una máquina relativamente nueva que usa un protocolo de datos estándar como MT Connect, entonces es muy fácil para cualquiera tomar los datos de la red y moverlos a una base de datos. Sin embargo, si la máquina no usa protocolos de datos estándar, pero los datos están disponibles en el PLC [controlador lógico programable] local que está ejecutando la máquina, entonces, por lo general, si es relativamente nuevo, podemos obtener los datos del PLC. Entendemos los protocolos de PLC y tenemos controladores que pueden hacerlo”.
El dispositivo LIMS "habla" sobre 50 protocolos industriales diferentes, señaló. "Solo sepa que si tiene algún equipo que 'habla', probablemente podamos hablar con él".
Y como se mencionó, si nada de eso funciona, se pueden agregar sensores a la máquina de producción y conectarlos al dispositivo LIMS, dijo Megan.
“Hemos tenido casos en los que hemos agregado sensores para permitir ciertos tipos de análisis:temperatura, humedad en el taller, ese tipo de cosas. Esos pueden conectarse como señales cableadas típicas como si entraran en un PLC o cualquier otra cosa”, dijo.
Cualquiera que sea la forma en que se realice la conexión, el beneficio es que "ahora va a aterrizar todo a través de un sistema para que pueda marcar todo con una marca de tiempo", dijo Megan. “Todo será consistente en el tiempo. Podrá aterrizarlo en una base de datos estándar y tener los datos bien organizados, en contexto y en un lugar que pueda usar”.
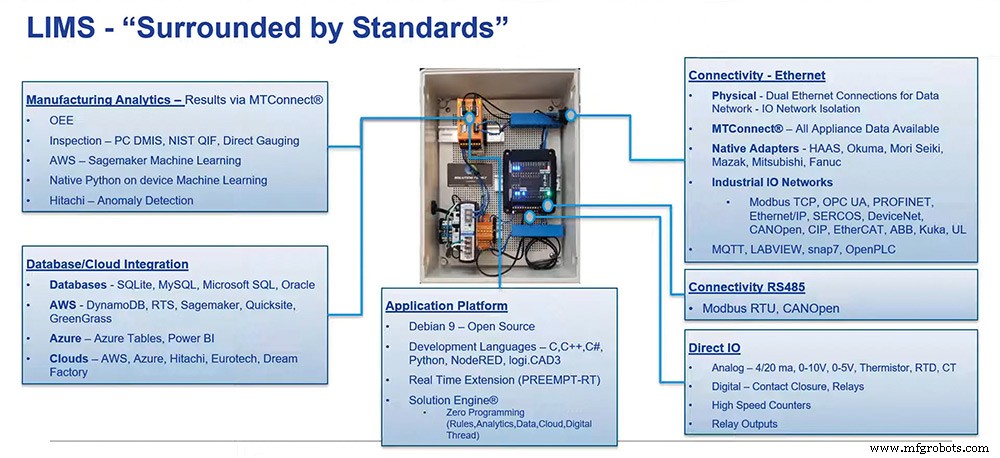
Suavizado, almacenamiento y análisis
Una vez que se realizan las conexiones y los datos pueden fluir al LIMS, el segundo paso es filtrar los datos para reducir el ruido y fortalecer la señal. “Los datos que provienen del equipo no siempre son perfectos”, dijo Frampton. “Puede ser ruidoso”. Por esa razón, el programa Solution Engine incluye un motor de análisis simple que lo suaviza. Por ejemplo, "tal vez tenga una corriente que esté entrando y quiera integrarla en kilovatios hora, para saber cuál es su huella de carbono para una parte en particular". El filtrado permitirá un conjunto de datos más claro y preciso. Este filtrado de datos inicial es diferente de los análisis más complejos posibles una vez que el sistema ha estado en funcionamiento para registrar y almacenar datos durante un período de tiempo más prolongado.
El tercer paso es recopilar los datos y guardarlos en la base de datos que elija el usuario, que puede ser local o en la nube.
“No se requiere ninguna nube”, afirmó Frampton. El usuario podría optar por configurar una base de datos SQL, por ejemplo, y “podría poner esa base de datos en la nube si quisiera, pero no es necesario. Simplemente puede almacenarlo localmente en el dispositivo LIMS”, señaló. El dispositivo LIMS tiene 16 gigabytes de almacenamiento estándar.
Otro punto que distingue al sistema de los demás:“Una de las cosas que no hacemos es monitorear el uso de datos y cobrarle cada vez que almacena algunos datos o le da límites de etiquetas o algo por el estilo. Los datos son tuyos”, dijo Frampton.
El cuarto paso es la generación de informes y el análisis de los datos. Como la mayoría de los operadores de máquinas no son necesariamente expertos en bases de datos, LIMS está diseñado para que la recopilación y el almacenamiento de datos sean tan fáciles como hacer clic con el mouse.
“Si no es un experto en bases de datos o no se siente cómodo con las bases de datos, no se preocupe”, dijo Frampton. “Puede simplemente hacer clic con el botón derecho en esos datos y enviarlos a MS Excel. Soy ingeniero mecánico de formación, por lo que siempre me he asegurado de que nuestras herramientas vayan directamente a Excel".
Sin embargo, si el usuario tiene Azure o Google Cloud u otro sistema basado en la nube, "podemos tomar esos datos y moverlos directamente a tablas en Azure para que pueda verlos en Power BI" u otros programas o formatos similares, él dijo. "También podemos analizar el aprendizaje automático y obtener resultados".
Poner los datos en uso
El quinto y último paso es la razón por la que se implementó el sistema para comenzar:usar la información recopilada para mejorar el proceso.
“Una vez que haya descubierto cómo mejorar el proceso, lo más importante es poder controlarlo, hacer algo al respecto”, explicó Frampton.
La acción deseada puede ser relativamente simple para comenzar, como hacer visible una parte de la información pertinente con la conveniencia de una pila de luces roja, amarilla y verde. Sin embargo, con el tiempo, los datos recopilados pueden permitir al usuario hacer mucho más.
“Posicionamos a LIMS como un punto de entrada para la transformación digital”, dijo Megan. “Por lo general, comienza con esta idea de recopilar los datos y poder realizar una visualización simple. Una vez que tenga eso, con el tiempo puede comenzar a hacer cosas más sofisticadas con él. Pueden subir por la curva de madurez, desde análisis básicos en última instancia hasta soluciones más avanzadas como IA.
"Pero es mejor comenzar de manera simple, y LIMS es un gran punto de partida", concluyó.
Sistema de control de automatización
- Alemania convierte la fabricación en una forma de arte IoT
- Cobot guiado por visión duplica la producción diaria
- 3 ejemplos principales de tecnología de fabricación avanzada de vanguardia
- Por qué la industria manufacturera de EE. UU. está experimentando una recesión
- Industria 4.0:el desarrollo de una ciberseguridad única
- Producción a prueba de futuro:el impacto de COVID en la fabricación
- Cómo EE. UU. dominará la industria manufacturera
- Los 10 principales sitios web de noticias de fabricación
- Dispositivo de fabricación llave en mano que se presentará en IMTS 2016
- STAEDTLER:el valor de la automatización en la industria manufacturera
- Sistema de computación en la nube:sus beneficios para la industria manufacturera