Aplicación destacada:Cohetes impresos en 3D y el futuro de la fabricación de naves espaciales
La impresión 3D se está convirtiendo rápidamente en una tecnología apasionante para la fabricación de naves espaciales y, en particular, los cohetes. Tanto las empresas emergentes como los fabricantes establecidos están adoptando la impresión 3D para crear componentes de cohetes con un diseño y rendimiento mejorados a un costo menor y con tiempos de respuesta más rápidos.
Esta semana, continuamos con nuestra serie Application Spotlight analizando los beneficios de la impresión 3D para piezas de cohetes, e incluso cohetes enteros.
Eche un vistazo a las otras aplicaciones cubiertas en esta serie:
Impresión 3D para intercambiadores de calor
Impresión 3D para rodamientos
Impresión 3D para la fabricación de bicicletas
Impresión 3D para odontología digital y fabricación de alineadores transparentes
Impresión 3D para implantes médicos
Impresión 3D para la fabricación de calzado
Impresión 3D para componentes electrónicos
Impresión 3D en la industria ferroviaria
Gafas impresas en 3D
Impresión 3D para la producción de piezas finales
Impresión 3D para soportes
Impresión 3D para piezas de turbinas
Cómo la impresión 3D permite componentes hidráulicos de mejor rendimiento
Cómo la impresión 3D apoya la innovación en la industria de la energía nuclear
¿Por qué se utiliza la impresión 3D para fabricar componentes de cohetes?
La carrera por llevar satélites al espacio es cada vez más feroz.
Por esta razón, los fabricantes de naves espaciales se enfrentan al desafío de acelerar el desarrollo y la producción de cohetes, al tiempo que reducen los costos y aumentan la eficiencia.
Sin embargo, en la fabricación de cohetes convencionales, múltiples ciclos de creación de prototipos y etapas de producción hacen que el proceso sea largo y muy costoso.
Por ejemplo, puede llevar entre 10 y 14 meses fabricar una cámara de combustión convencional (un componente estructural de un cohete donde se enciende una mezcla de combustible y aire comprimido).
Para producir estas cámaras de combustión, los fabricantes necesitan fundir y forjar componentes separados. Los canales de enfriamiento deben mecanizarse alrededor la cámara - un proceso muy lento, laborioso y costoso.
Teniendo en cuenta estos desafíos, los principales fabricantes de cohetes ya están comenzando a producir cámaras de combustión con fabricación aditiva. Una vez diseñada, una cámara de combustión impresa en 3D se puede fabricar en unas pocas semanas, lo que permite a los fabricantes reducir significativamente los tiempos y costos de producción.
La fabricación de hardware que se lanzará al espacio requiere un rendimiento y una precisión excepcionales. Para garantizar un lanzamiento exitoso, todas las partes deben trabajar juntas a la perfección.
Con la fabricación tradicional, los ingenieros enfrentan limitaciones al diseñar piezas de cohetes altamente complejas. La impresión 3D de metal permite a los ingenieros superar algunas de las limitaciones de los procesos tradicionales y desarrollar componentes de cohetes más complejos con mayor rapidez.
Las tecnologías de impresión 3D que se utilizan para fabricar componentes de cohetes
A día de hoy, las empresas de naves espaciales han adoptado, en general, tecnologías de impresión 3D de metales basadas en láser, como la fusión selectiva por láser (SLM) para producir piezas de motores de cohetes como cámaras de combustión, inyectores, boquillas, bombas y válvulas. SLM aplica un láser potente y afinado a una capa de polvo metálico, fusionando las partículas metálicas. El proceso se repite para cientos de capas hasta que se crea una pieza.
SLM ofrece alta precisión (puede imprimir capas de hasta 20 micrones) y está optimizado para trabajar con una amplia gama de metales de alto rendimiento. , desde titanio hasta aleaciones de níquel. Esta tecnología se utiliza normalmente para piezas más pequeñas.
Además de SLM, algunas empresas de naves espaciales utilizan la tecnología de Deposición Directa de Energía (DED) para crear componentes grandes. Las impresoras 3D DED funcionan fundiendo material metálico con un láser o un haz de electrones mientras se deposita a través de una boquilla en la plataforma de construcción.
Normalmente, las máquinas DED tienen altas tasas de deposición de material y pueden trabajar con materiales metálicos en forma de polvo o alambre, creando piezas muy densas con formas casi netas.
Los beneficios de la impresión 3D para cohetes
La capacidad de iterar rápidamente
Una de las mayores ventajas de la impresión 3D para piezas de cohetes es la capacidad de iterar diseños muy rápidamente.
“ Con aditivo, puede pasar por cinco iteraciones de un diseño antes incluso de obtener las primeras a través de un método tradicional, y las cinco juntas probablemente costarán menos de una iteración tradicional , ”Dice Scott Killian, Gerente de Desarrollo de Negocios Aeroespaciales para EOS North America en una entrevista con engineering.com.
Una impresora 3D puede crear piezas de cohetes directamente desde un archivo de diseño sin la necesidad de herramientas. Si una pieza requiere modificaciones, los ingenieros pueden simplemente realizar cambios en un archivo CAD original y crear un diseño nuevo y modificado mucho más rápido de lo que permitirían los procesos tradicionales.
Flexibilidad de diseño
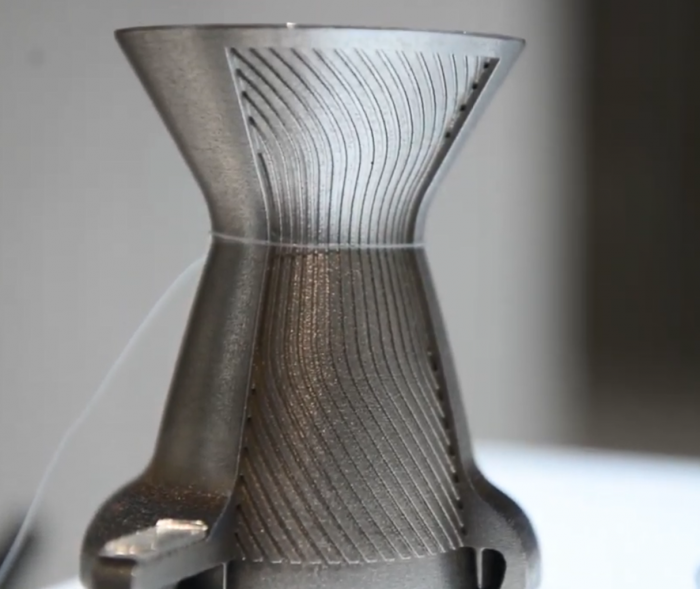
Sin la dependencia de las herramientas, la impresión 3D ofrece a los ingenieros de naves espaciales la flexibilidad de crear formas y geometrías complejas inalcanzables con los procesos convencionales.
Considere las cámaras de combustión. Un componente crucial en todos los motores de cohetes, una cámara de combustión debe soportar un ambiente altamente presurizado y temperaturas de hasta 5,000 ° F (2760 ° C), ya que los propulsores se mezclan y se encienden en el interior.
Para funcionar de manera eficiente, este componente requiere canales de enfriamiento internos complejos que están llenos de gases enfriados a menos de 100 ° F (38 ° C) por encima del cero absoluto.
Tradicionalmente, estos canales de enfriamiento son muy complicados y costosos de desarrollar. Requieren herramientas especializadas para los canales de enfriamiento de la máquina CNC y sueldan la pared exterior de la cámara. Luego, estos segmentos separados deben soldarse en una sola pieza.
La impresión 3D, por otro lado, agiliza el proceso al hacer posible producir toda la cámara directamente. Además, permite diseños de canales de refrigeración complejos, como se muestra en la imagen de arriba, que serían imposibles de mecanizar.
Piezas de cohetes menos caras
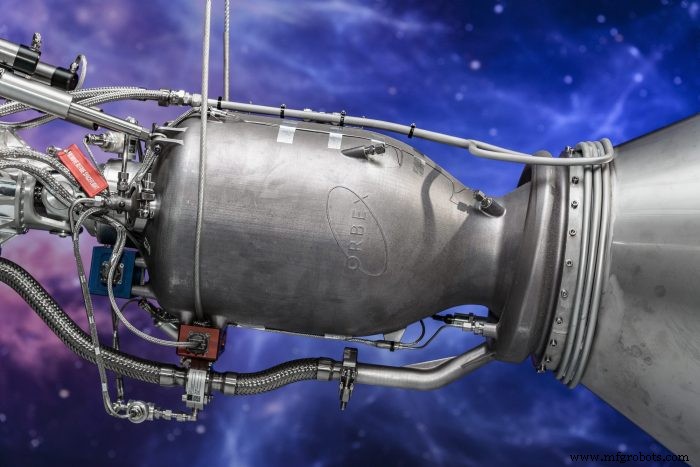
Los motores son la parte más cara de un vehículo de lanzamiento (un vehículo propulsado por cohetes que se utiliza para lanzar satélites u otras naves espaciales al espacio). El costo de un motor puede representar hasta el 40% del costo de todo el cohete. Al utilizar la impresión 3D para crear piezas de motor cruciales, los fabricantes de cohetes pueden reducir drásticamente los costos generales de una nave espacial.
La impresión 3D permite a los ingenieros optimizar la producción de componentes de motores de cohetes, sin pasar por una serie de pasos de producción. Cuantos menos pasos, menos equipo y ajustes se necesitan, lo que en última instancia da como resultado costos de producción más bajos.
Además, la automatización del proceso de producción con impresión 3D significa que la mayoría de los costos laborales se eliminan de la ecuación .
Por ejemplo, la empresa aeroespacial británica, Orbex, utilizó tecnología SLM y una aleación de níquel para imprimir en 3D un motor para su lanzador Prime. La impresión 3D de metal permitió a Orbex reducir su tiempo de respuesta en un 90% y reducir los costos en un 50% en comparación con los procesos de producción más tradicionales, como el mecanizado CNC.
La empresa espacial comercial privada de Elon Musk, SpaceX, ha también adoptó la impresión 3D para reducir costos y ofrecer una mayor flexibilidad en el proceso de producción de sus propulsores Draco y SuperDraco. La empresa utiliza una impresora 3D de metal basada en SLM para crear cámaras de combustión de Inconel.
Según Musk, “ a través de la impresión 3D, se pueden crear piezas de motor robustas y de alto rendimiento en una fracción de el costo y el tiempo de los métodos de fabricación tradicionales . "
Montaje simplificado
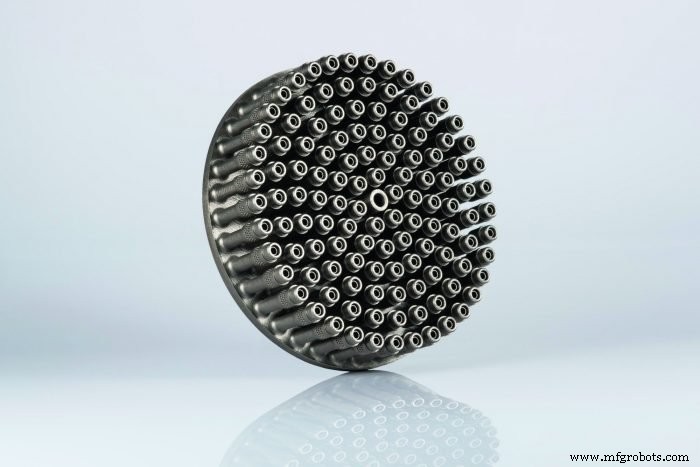
Además, los ingenieros también pueden reducir en gran medida la cantidad de pasos en el proceso de ensamblaje. Esto se puede lograr mediante la impresión 3D de piezas de cohetes hechas de múltiples componentes como una sola pieza.
Tome una cabeza de inyector como ejemplo. Una cabeza de inyector es uno de los elementos centrales de un módulo de propulsión, que fuerza la mezcla de combustible hacia la cámara de combustión.
Tradicionalmente, los cabezales de los inyectores se fabrican a partir de docenas o incluso cientos de piezas, que deben mecanizarse y soldarse entre sí. Por el contrario, la impresión 3D puede producir componentes como una sola pieza.
Investigadores del Centro Aeroespacial Alemán (DLR) utilizaron la impresión 3D para crear un nuevo diseño de un cabezal inyector para un pequeño lanzador de satélites.
El resultado es una pieza monolítica un 10% más ligera. Al reducir la cantidad de componentes de 30 a solo uno, el equipo de investigación también eliminó los puntos de falla conocidos en los sitios de sujeción. Finalmente, se dice que el nuevo diseño optimizado mejora el rendimiento de la pieza y extiende la vida útil de la pieza.
De manera similar, el especialista en impresión 3D de metal, EOS, simplificó el ensamblaje de un cabezal de inyección para su lanzador Ariane 6 , desarrollado por ArianeGroup, una empresa conjunta de Airbus Group y Safran.
El uso de la tecnología SLM permitió al equipo rediseñar un cabezal de inyección como un componente en lugar de los 248 componentes necesarios para un diseño tradicional. Las ventajas adicionales incluyeron una reducción de costos del 50% y plazos de entrega tres veces más bajos.
Ejemplos de piezas de cohetes impresas en 3D
Motor Rutherford impreso en 3D de Rocket Lab
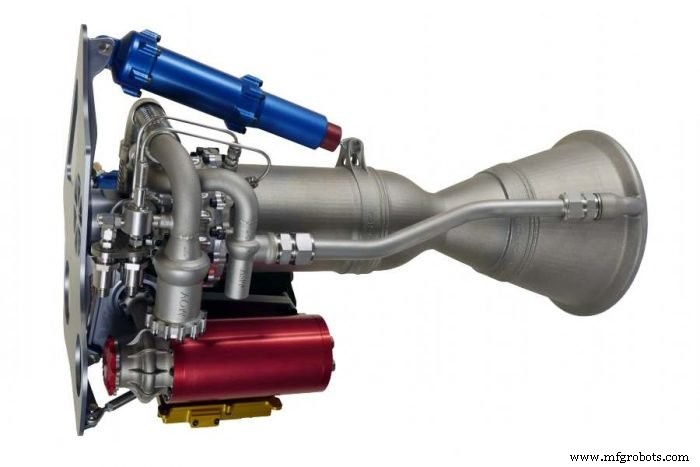
En julio, Rocket Lab, una empresa aeroespacial con sede en California, completó el motor de cohete Rutherford número 100 impreso en 3D. La empresa ha estado utilizando la impresión 3D para todos los componentes primarios de su motor (incluidas las cámaras de combustión, los inyectores, las bombas y las principales válvulas propulsoras) desde 2013.
Nueve motores de propulsión líquida Rutherford impulsan el cohete Electron de Rocket Lab. que está hecho de materiales compuestos y puede transportar hasta 225 kg de carga útil. Las piezas del motor se imprimen en 3D utilizando la tecnología de fusión por haz de electrones (EBM), que se dice que produce piezas de motor más baratas que los procesos convencionales.
Recientemente, Rocket Lab demostró una vez más la confiabilidad de los motores impresos en 3D, lanzando con éxito cuatro satélites en órbita con su lanzador de electrones.
Para 2020, la compañía planea realizar dos lanzamientos por mes. Con la impresión 3D que permite a Rocket Lab producir un motor en cuestión de días en lugar de meses, el equipo está bien posicionado para poner este plan en acción.
Impresión 3D de cohetes completos
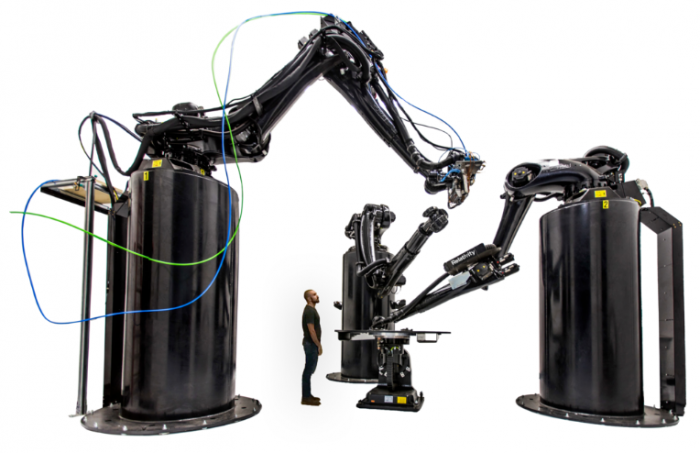
La startup con sede en California, Relativity Space, quiere ir más allá de los motores de cohetes impresos en 3D. La compañía está desarrollando un cohete Terran, del cual alrededor del 95% de los componentes se imprimirán en 3D.
Para lograr esto, la compañía ha desarrollado Stargate, una de las impresoras 3D de metal DED más grandes del mundo. Con la capacidad de crear componentes tan grandes como 2,7 m (9 pies) de diámetro y aproximadamente 4,5 m (15 pies) de alto, Stargate imprimirá todos los tanques de combustible y otros componentes grandes de cohetes.
Al utilizar la impresión 3D para fabricar virtualmente un cohete completo, Relativity Space espera reducir en gran medida el peso del cohete, lo que potencialmente puede reducir el costo de lanzamiento, al tiempo que aumenta la carga útil.
La impresión 3D también reducirá la cantidad de piezas que deben ensamblarse, aumentando así la fuerza y la estabilidad del cohete.
Para piezas más pequeñas, la empresa utiliza tecnología SLM.
Según Relativity Space, la impresión 3D le permite cambiar diseños rápidamente y utilizar menos herramientas y mano de obra de lo que normalmente se requeriría en el desarrollo de cohetes. Al final, esto podría permitir a Relativity Space pasar de la materia prima a un cohete listo para volar en menos de dos meses.
Relativity Space es actualmente la única empresa que aplica tecnologías de impresión 3D para un cohete completo. ¿Será exitoso su concepto de un cohete impreso en 3D? En última instancia, la respuesta estará en las pruebas y el lanzamiento. El lanzamiento de prueba del cohete Terran impreso en 3D está programado para finales de 2020.
El futuro de la impresión 3D en la industria aeroespacial
La impresión 3D ha revolucionado la forma en que se diseñan y producen los cohetes y las piezas de los motores de los cohetes. Es posible que los fundamentos del diseño de cohetes no hayan cambiado, pero la impresión 3D de metal ha desbloqueado nuevas formas de mejorar el rendimiento de los cohetes, ofreciendo una mayor libertad de diseño.
La tecnología puede ayudar a reducir el costo de fabricación de motores, uno de los componentes de cohetes más costosos. Esto se logra reduciendo el número de pasos de producción y permitiendo iteraciones de diseño más frecuentes.
Aunque las capacidades de la impresión 3D más allá de las piezas del motor aún no se han probado, el potencial de la tecnología para impresiones totalmente 3D cohetes en el futuro es realmente emocionante.
La impresión 3D se ha convertido en una tecnología de fabricación clave para la producción de naves espaciales, lo que permite a los ingenieros innovar más rápido y lograr la próxima generación de viajes espaciales.
En nuestro próximo artículo, analizaremos la impresión 3D en la industria del calzado. ¡Estén atentos!
Impresión 3d
- Diseño generativo e impresión 3D:la fabricación del mañana
- Aplicación destacada:Impresión 3D para odontología digital y fabricación de alineadores transparentes
- Aplicación destacada:Impresión 3D para la fabricación de bicicletas
- La robótica y el futuro de la producción y el trabajo
- Los beneficios de la creación rápida de prototipos y la impresión 3D en la fabricación
- Automatización industrial:una breve historia de la aplicación de fabricación y el estado actual y las perspectivas futuras
- El futuro de la maquinaria industrial en 2020 y más allá
- ¿Qué papel jugarán la robótica y la impresión 3D en el futuro de la fabricación?
- ¿Automatización y el futuro de la fabricación digital?
- El futuro de la impresión 3D en la fabricación
- ¿Es la impresión 3D el futuro de la fabricación?