Epoxi de 2 partes para una mayor producción de aeroestructuras compuestas mediante RTM
Este es el tercero de mi serie de blogs sobre tecnologías que debe consultar en CAMX 2019 (23-26 de septiembre, Anaheim, CA, EE. UU.). Hexion (Columbus, Ohio, EE. UU.) Ha desarrollado un sistema de dos componentes (2K) para RTM de aeroestructuras basado en su resina epoxi Epikote System 600. La introducción a continuación explicará por qué este desarrollo es importante. Después de eso, doy más detalles sobre este nuevo sistema 2K y cómo Hexion está cumpliendo con las demandas de los OEM aeroespaciales de garantía de calidad in situ de la resina mezclada. En la parte inferior, también hablo de la infusión 2K / epoxi RTM de Hexion para aplicaciones resistentes al fuego (FR).
¿Por qué resinas 2K para RTM?
A principios de este año, escribí sobre programas en el especialista en herramientas Alpex Technologies (Mils, Austria) y la filial de Airbus Composites Technology Center (CTC, Stade, Alemania) para producir piezas de aviones compuestos utilizando moldeo por transferencia de resina (RTM) . El uso de RTM en la industria aeroespacial no es nuevo. Hay y ha habido una variedad de piezas de aviones fabricadas con RTM, que incluyen:
- Timón para el jet de negocios Gulfstream G250 (Israel Aerospace Industries y North Coast Composites)
- Aspas y caja de ventilador para el motor de avión LEAP turbofan (Albany Engineered Composites)
- Marco de puerta del A350 (Airbus Helicopters Donauworth)
- Demostración de la puerta del pasajero del A350 (Elbit Cyclone)
- Demostración del flap multispar del A320 (Airbus Bremen)
- Matrix Composites produjo más de 6,000 componentes para el F-22 usando RTM.
Sin embargo, la RTM en aplicaciones aeroespaciales ha sido tradicionalmente un proceso de baja presión con tiempos de ciclo medidos en horas. Los programas de Alpex y CTC se centran en aprovechar la automatización, la inyección rápida y los tiempos de ciclo de 15 a 20 minutos ofrecido por RTM de alta presión (HP-RTM). En mi artículo “HP-RTM para la producción en serie de aeroestructuras de CFRP rentables”, hablé del tema del uso de resinas epoxi de 2 componentes (2K) frente a la norma actual de usar sistemas premezclados de 1 componente (1K):
“Schiller [Jan Schiller, líder del proyecto CTC para sistemas de producción y contacto principal para tecnologías RTM] observa que todos los RTM anteriores Las estructuras de las aeronaves solo han utilizado sistemas 1K mezclado por el proveedor, quien luego certifica la mezcla y asume la responsabilidad de asegurarse de que la resina cumpla con los requisitos de calificación. “Ahora estamos considerando sistemas 2K, pero el desafío es garantizar la calidad de la mezcla ," el explica. Los sistemas 1K premezclados requieren envío y almacenamiento en frío para evitar reacciones hasta el procesamiento de la pieza. Por lo tanto, las ventajas de los sistemas 2K incluyen la eliminación de este gasto, así como una mayor reactividad para un procesamiento más rápido ”.
“Sin embargo, un problema es que la garantía de calidad (QA) se transferirá del proveedor de resina al fabricante de las piezas. "Este control de calidad requiere la detección de la proporción de mezcla y la calidad de la resina mixta . Ambos son necesarios para la calificación de Airbus de un nuevo material. Entonces, esto significa mediciones de los dos componentes justo antes de mezclar y de la resina después de mezclar . Hoy en día, solo tenemos sensores antes del cabezal de mezcla, que muestran cuánta resina y cuánto endurecedor se dosificaron en la mezcla. Esto no es suficiente para calificar ”.
Hexion (Columus, Ohio, EE. UU.), Líder en el desarrollo de epoxis de curado rápido para HP-RTM en compuestos automotrices (consulte “HP-RTM en aumento”), anunció en marzo de 2019 que ha desarrollado un sistema 2K para RTM de aeroestructuras basadas en su resina epoxi Epikote System 600. Entrevisté al líder del segmento aeroespacial global de epoxi de Hexion, Jean Rivière, para obtener más información sobre su sistema 2K para la industria aeroespacial y cómo están satisfaciendo esta demanda de control de calidad in situ de la resina mezclada.
Superar las limitaciones de los sistemas 1K
“Al igual que con el preimpregnado, los sistemas 1K para RTM e infusión en la industria aeroespacial deben mantenerse fríos y tener una vida útil limitada”, dice Rivière. “Al usar un sistema epoxi de 2 componentes (2K), elimina estas limitaciones. Hemos visto resinas epoxi 2K y altamente reactivas utilizadas en la fabricación de palas eólicas y estructuras automotrices. Entonces, ¿por qué no en la industria aeroespacial? ”
Rivière explica que después de hablar con muchos clientes sobre esto, Hexion entendió la principal preocupación:necesita una validación de que la proporción de mezcla es correcta en cualquier momento antes de la inyección en el molde. Sin esto, existe un riesgo inaceptable para el fabricante de la pieza ”, señala. Agrega que anteriormente, no había demanda para el tipo de volúmenes de producción que se ven en las palas eólicas y la automoción. Ahora, sin embargo, Airbus y Boeing quieren superar las tasas de producción actuales mientras apuntan a más piezas compuestas por avión. “Por lo tanto, ahora es necesario alejarse de la capa de preimpregnado y optar por un epoxi 2K para infusión o RTM aeroespacial”, dice Rivière.
En los siguientes diagramas de la cadena de suministro, la tecnología 2K no solo elimina los pasos de almacenamiento en frío y recalentamiento, sino que también elimina las restricciones sobre el tamaño del contenedor de resina para el envío. “Debe mantener la masa de resina premezclada en 20 litros y mantener esos tambores a muy baja temperatura”, dice Rivière, “o de lo contrario la resina puede comenzar a reaccionar. Para un sistema 2K, los tambores estándar de 200 litros se pueden enviar sin restricciones de baja temperatura. Por lo tanto, hay menos riesgo, no se necesita un enfriamiento fuerte y se necesitan menos precauciones ".
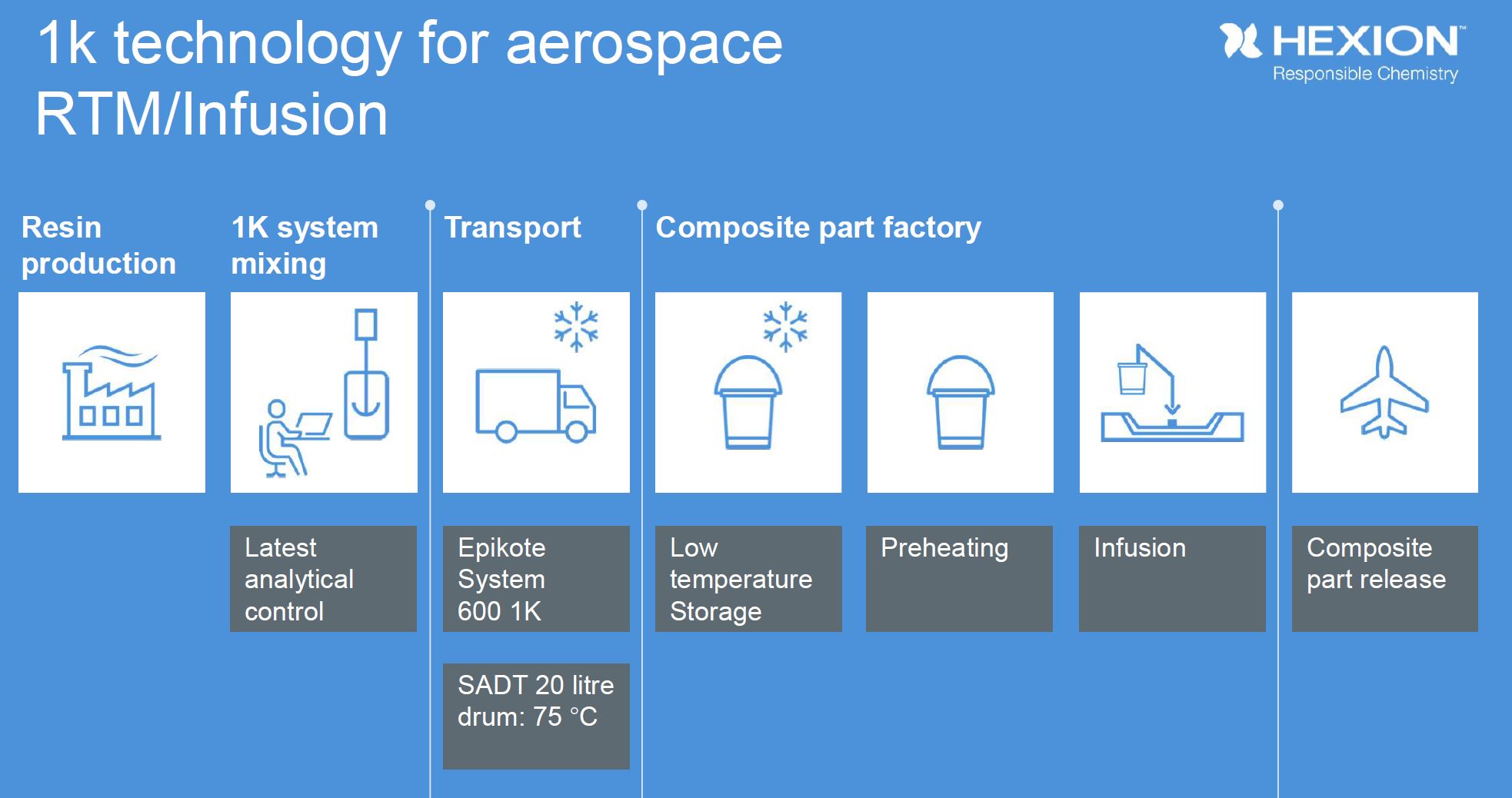
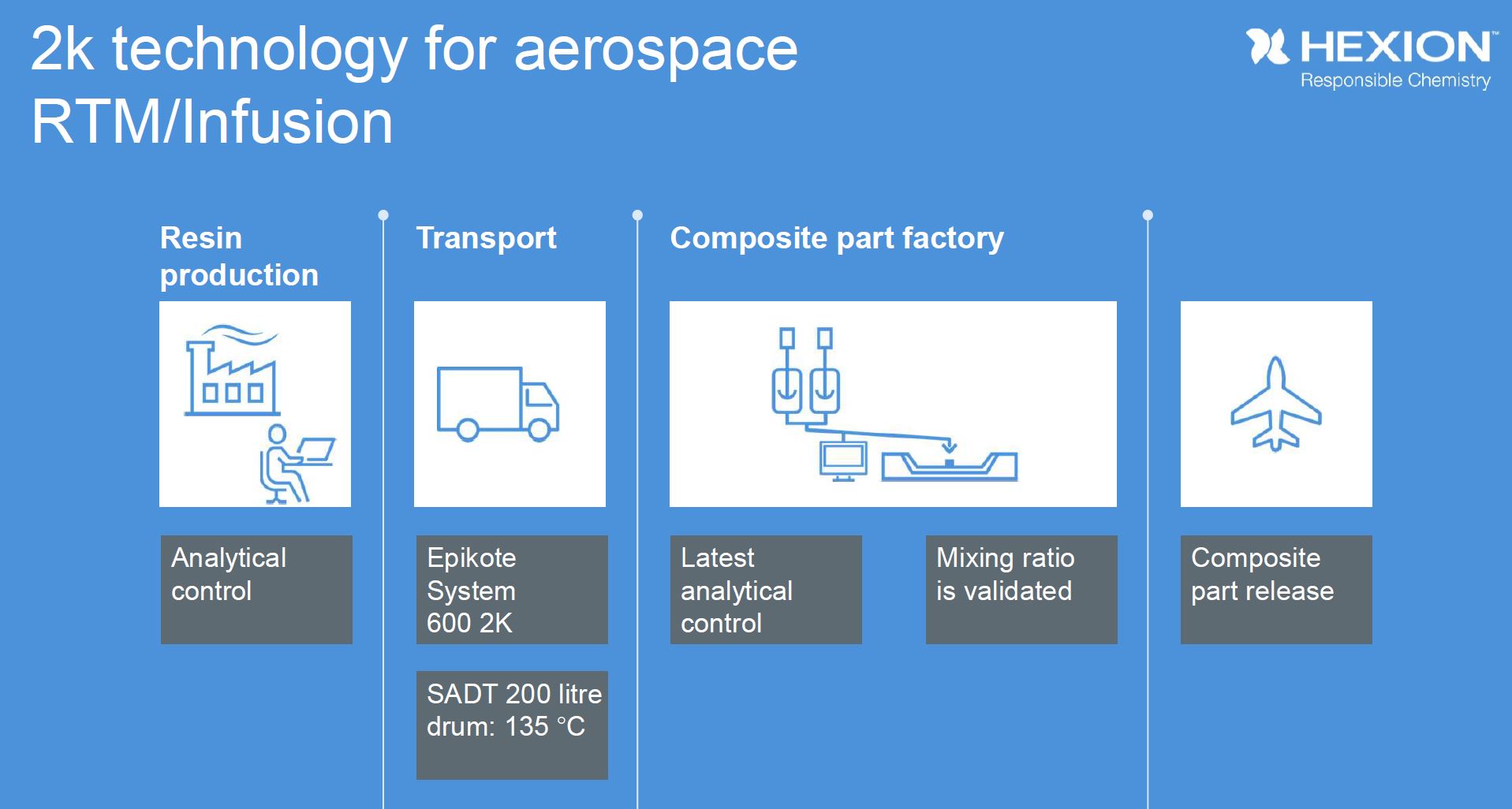
Las cadenas de suministro anteriores muestran cómo cambia el control analítico. Si bien solo se realiza un control inicial en la ubicación de fabricación para los sistemas de resina 1K, el control se implementa en múltiples puntos de control para el sistema 2K. Además del control de los componentes A y B durante la producción en fábrica, la proporción de mezcla A:B también se controla digitalmente en el equipo de mezcla, dosificación y dispensación (MMD) y nuevamente justo antes de la inyección de resina en el molde. FUENTE | Hexión.
Control analítico
Para desarrollar esta tecnología 2K, Hexion trabajó con Hübers (Bocholt, Alemania), un fabricante de equipos de mezcla, medición y dispensación (MMD), y Composyst (Hurlach, Alemania), que tiene una licencia exclusiva para el proceso asistido por vacío patentado por Airbus ( VAP) para infusión. Hübers tiene una sólida reputación por los sistemas MMD de alto rendimiento utilizados en la fabricación de componentes eléctricos y electrónicos (por ejemplo, resina fundida y componentes impregnados para transformadores, etc.) mientras que Composyst es un experto en inyección e infusión de resina para aplicaciones Airbus y, por lo tanto, , comprende lo que buscan los fabricantes de equipos originales (OEM) de aeronaves con respecto al procesamiento y aseguramiento de la calidad (QA) de resinas mixtas.
“El control analítico entra en juego después de que los componentes A y B del epoxi hayan sido mezclados con precisión por el equipo Hübers y se estén preparando para ser introducidos en el molde”, explica Rivière. Los tubos negros entre el sistema MMD de Hübers y la configuración de infusión de VAP envasada al vacío en la imagen a continuación son un componente clave de este sistema de control analítico. “Aquí es donde tenemos un dispositivo analítico que controla la proporción de mezcla en tiempo real”, dice Rivière. “Hemos demostrado la medición de la relación de mezcla cada 12 segundos, pero también es posible realizar mediciones más frecuentes. De hecho, la tecnología permite un control continuo de la proporción de mezcla, que se informa y registra ”.
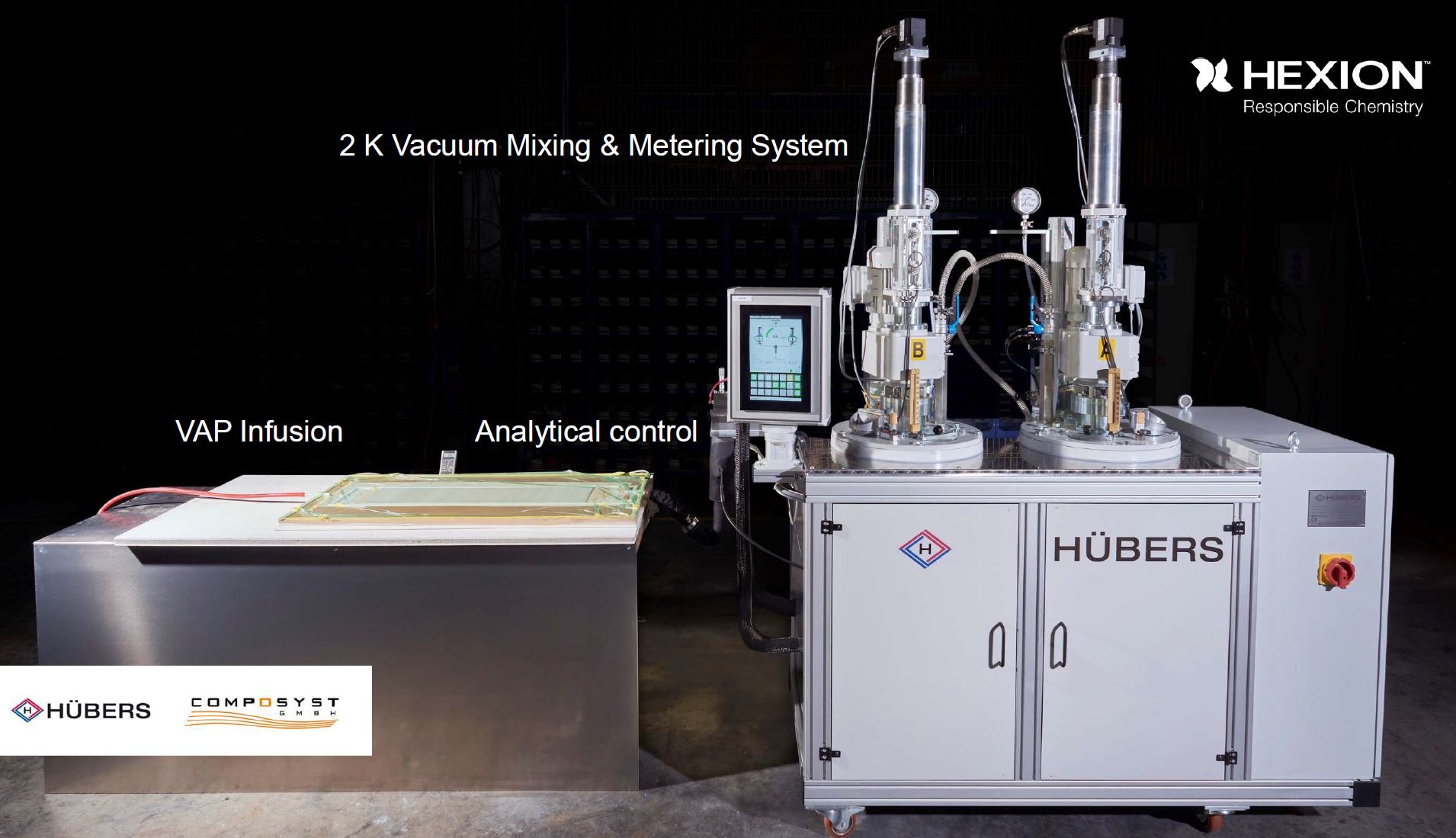
Observe el tubo negro entre el equipo MMD de Hübers y la configuración de infusión VAP donde Hexion ha desarrollado una medición en línea de la proporción de la mezcla de resina antes de la inyección. Hexión
“Con este sistema”, continúa, “hay un doble control:el control normal en la unidad MMD y nuestro control analítico de preinyección en la parte superior. En primer lugar, Rivière señala que las máquinas MMD de Hübers son conocidas por su precisión y exactitud. “Tienen un sistema de bombeo doble para los dos componentes y deben mantener la precisión en volumen y temperatura, así como la proporción de mezcla para las aplicaciones a las que suministran. Luego, nuestro sistema agrega una segunda medición después de la mezcla y justo antes de la inyección, donde puede establecer objetivos para las alarmas ". Si la proporción de mezcla medida no cumple con los objetivos y activa la alarma, el sistema evacuará la resina mezclada a un recipiente separado, sin pasar por el molde para que no introducido en la parte infundida. “Entonces es posible recuperar el proceso y continuar con la inyección”, señala Rivière.
Él dice que el sistema de control analítico de preinyección y posmezcla de Hexion proporciona un registro independiente de trazabilidad y también se puede integrar en la unidad MMD, según las necesidades del cliente. Rivière señala que la unidad MMD de Hübers también realiza una desgasificación completa de la resina, que es requerida por la industria electrónica, donde no puede haber huecos ni porosidad en los componentes de la aplicación. “Este sistema también proporciona un control portátil de la presión sobre el molde mediante la gestión del flujo de resina en niveles altos o bajos”, señala. “Puede lograr una impregnación muy buena con este tipo de control, y también puede acortar el tiempo del proceso de infusión al tiempo que cumple con los requisitos de calidad aeroespacial en términos de porosidad y volumen de fibra”.
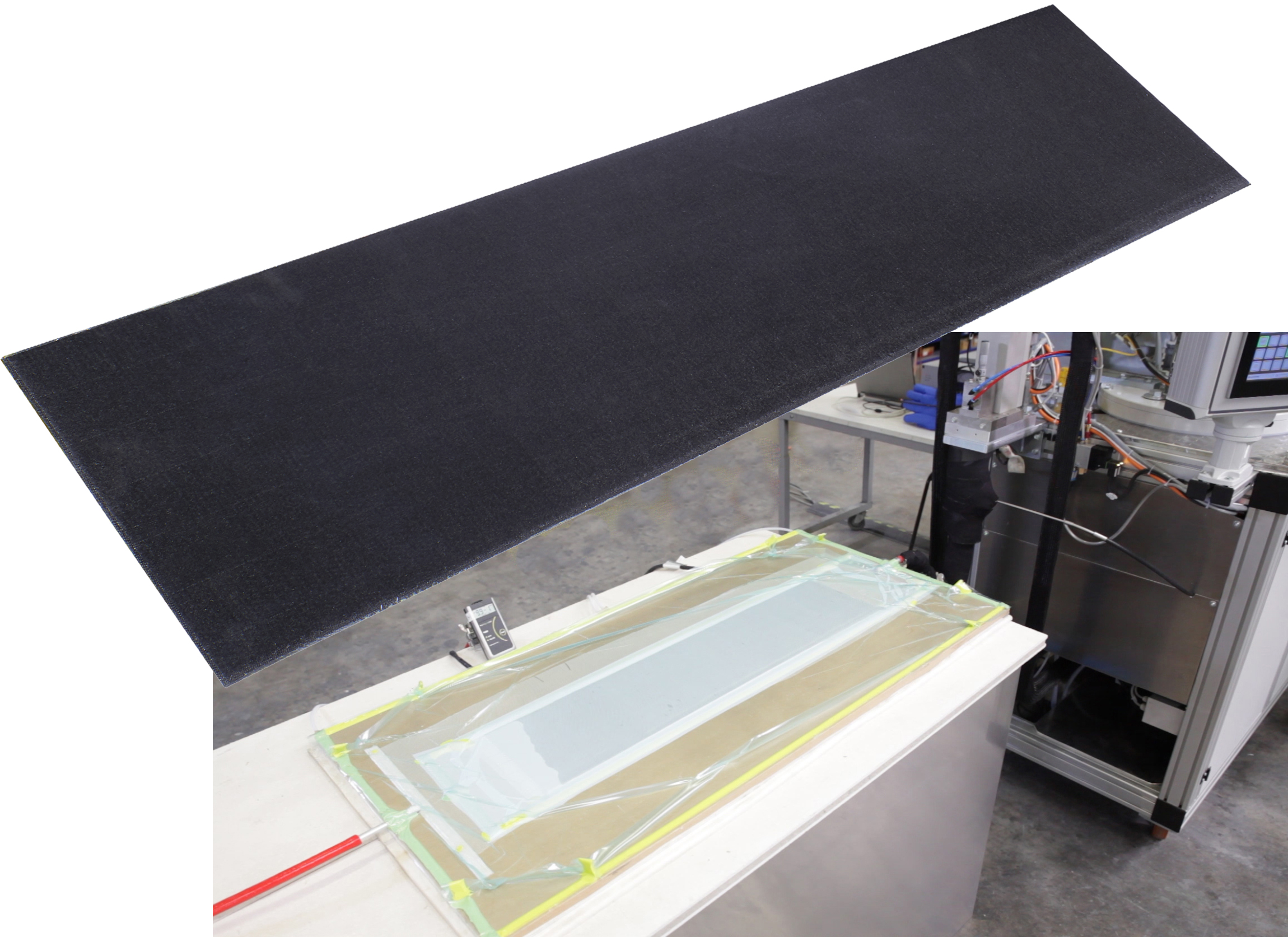
Fotos que muestran la configuración de infusión con el equipo MMD de Hübers y el control analítico Hexion 2K y un laminado UD de fibra de carbono de 2 centímetros de espesor preparado con esta configuración, logrando más del 60% de volumen de fibra. FUENTE | Hexión
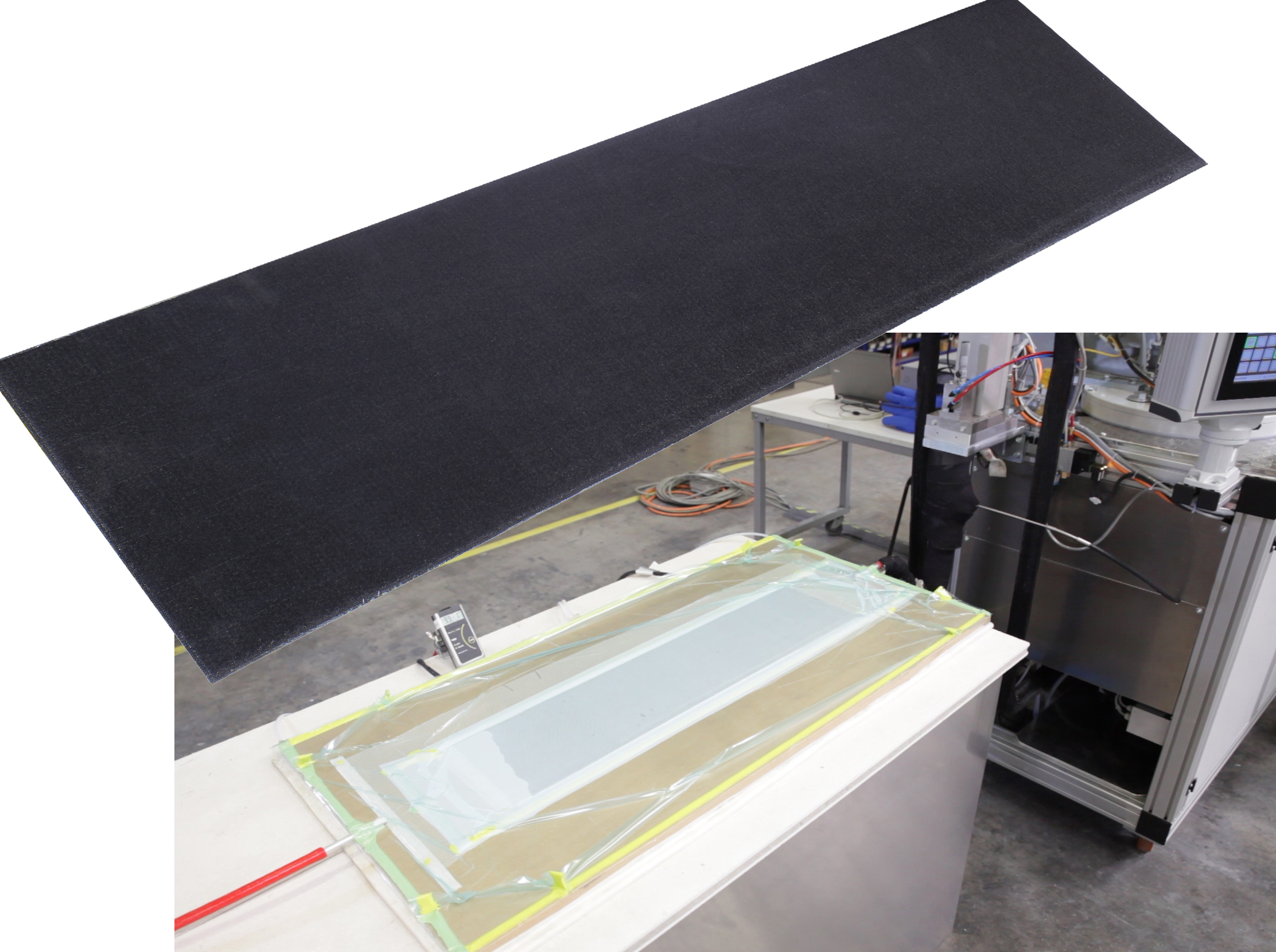
Mejor ventana de procesamiento
"Debido a que la mezcla se realiza con un mezclador estático y en un período de tiempo corto justo antes de la inyección, la mezcla de resina ofrece una vida útil más larga (hasta un 40% en comparación con 1K)", señala Rivière . Esto proporciona una mejor ventana de procesamiento y hemos producido laminados de fibra de carbono gruesos con un 60% de volumen de fibra. El rendimiento mecánico de los sistemas 2K frente a 1K es el mismo porque la química es la misma. Creemos que este será un proceso más confiable y el valor completo es cuando conecta el control de mezcla a la configuración de inyección de resina ”.
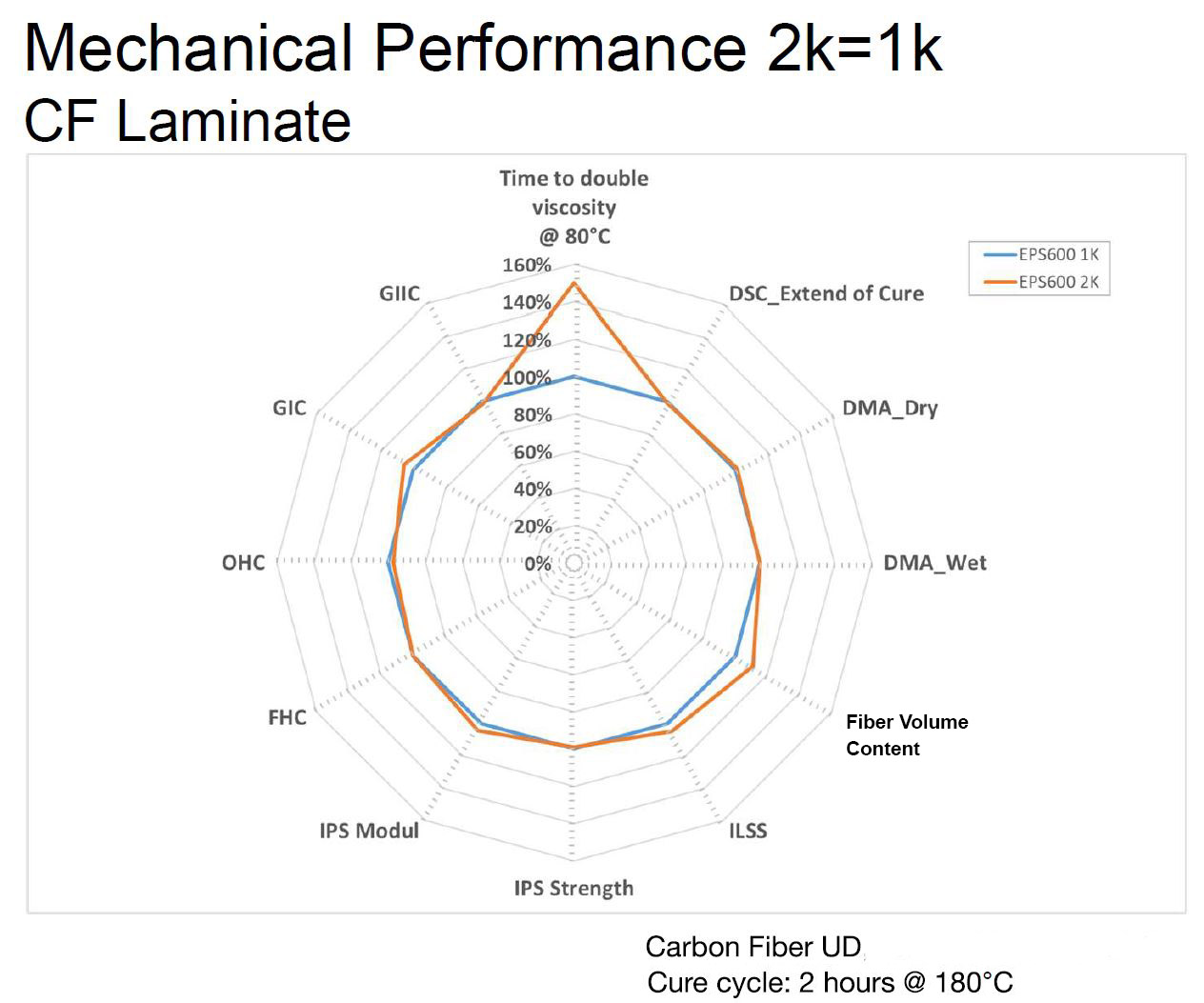
FUENTE | Hexión
Hexion presentará información detallada sobre su sistema 2K Epikote 600 para RTM y su epoxi EPON FlameX para cumplir con los requisitos de fuego, humo y toxicidad de aviones (FST) (ver más abajo) en el CAMX Theater en el piso de exhibición:
- Novedosa tecnología 2K para la fabricación aeroespacial de epoxi
Martes, 24 de septiembre: 11:00 a 11:25 a. M. - Sistemas de epoxi FlameX para aplicaciones de seguridad contra incendios
Martes 24 de septiembre: 11:30 a 11:55 a. M.
También puede obtener más detalles en el stand Y24 de Hexion.
EPON FlameX epoxi para infusión / RTM de composites resistentes al fuego
Hexion también ha desarrollado un epoxi de 2 componentes para infusión / RTM de piezas que deben cumplir con los requisitos de resistencia al fuego (FR) y de llama, humo y toxicidad (FST). Con el objetivo de reemplazar los preimpregnados fenólicos con moldeado líquido epoxi, los impulsores de este desarrollo incluyen:
- Aumento de las tasas de producción
- Regulaciones REACH para sistemas libres de halógenos y no fenólicos
- Resinas más fuertes y resistentes frente a fenólicos quebradizos
- Rentable con compuestos fenólicos pero mucho más baratos que los termoplásticos.
El sistema EPON FlameX de Hexion no utiliza aditivos halógenos o particulados para lograr resistencia al fuego, sino que integra ese rendimiento en la columna vertebral molecular de la resina. No hay filtrado de partículas durante la infusión. La resina se infunde bien con una viscosidad de 250 cps a 60-70 ° C (140-158 ° F) y cura en 1,5 horas a 150 ° C (302 ° F). Se recomienda el poscurado independiente o con soporte de herramienta a 180 ° C para obtener las máximas propiedades estructurales.
Las piezas fabricadas con este sistema pasan lo siguiente sin recubrimientos adicionales ni medidas FR:
- Quemado vertical de los 60 FAR25.853 (a)
- Toxicidad por humo BSS7239
- Densidad de humo BSS7238
También pasará la liberación de calor OSU 65/65, en ciertas configuraciones con una capa o recubrimiento de gel intumescente certificado. Esto es necesario solo para las partes que se pueden tocar durante el rodaje, el despegue y el aterrizaje de la aeronave.
"Hemos demostrado contenedores superiores que actualmente requieren de 10 a 12 horas para fabricarse utilizando procesos convencionales de preimpregnación fenólica, pero se pueden producir en 90 a 120 minutos con infusión o RTM utilizando el sistema FlameX", dice Nathan Bruno, especialista en desarrollo de productos y aplicaciones epoxi de Hexion. . “Además, debido a que no hay rellenos, tiene una densidad más baja en comparación con los epóxicos FR rellenos”.
Las aplicaciones incluyen interiores de aviones, áreas de carga, baños, cocinas y componentes de asientos, así como interiores marinos, ferroviarios y arquitectónicos.
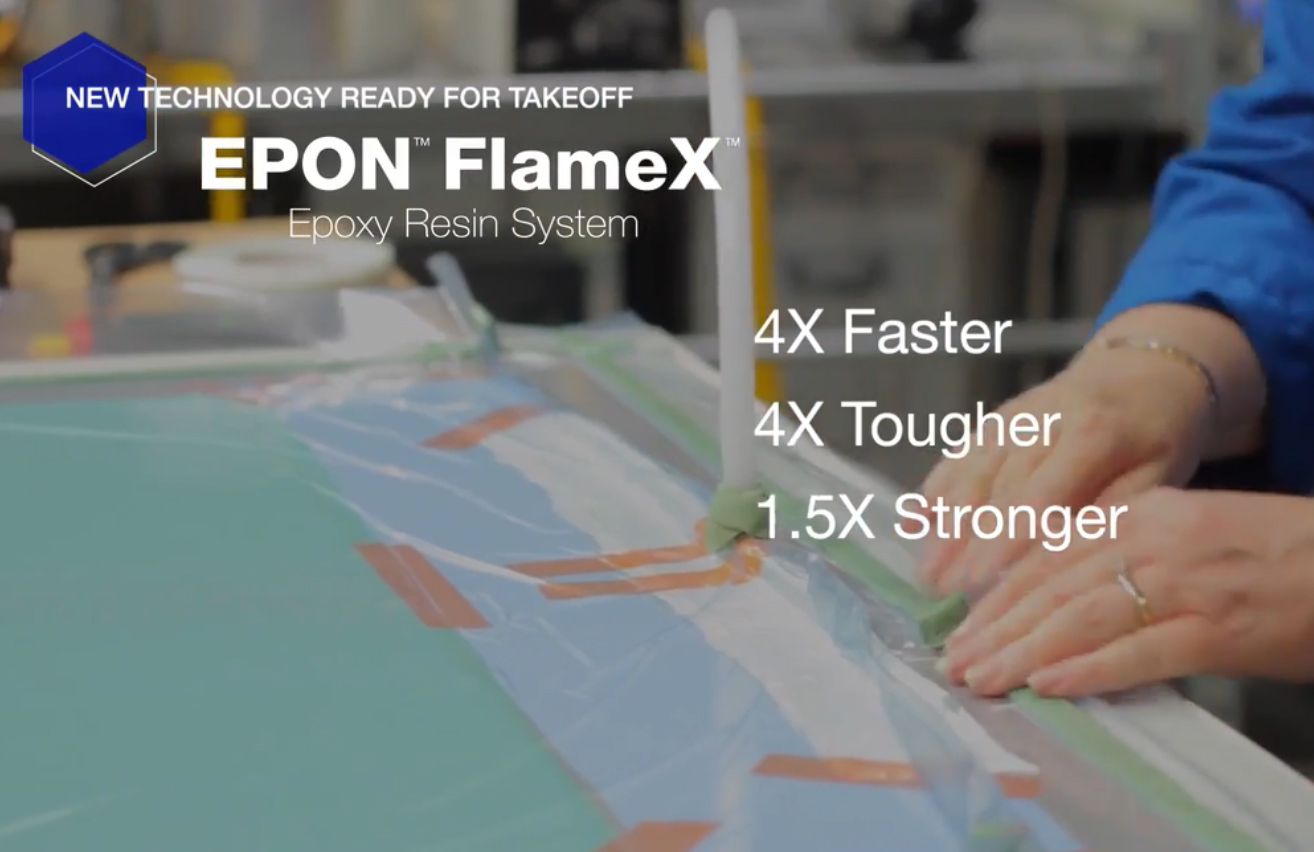
Resina
- Lanxess agrega dos nuevas líneas de producción para material compuesto Tepex
- Compuestos de purga para la producción de empaques de poliolefina de pared delgada
- Los usos de la resina epoxi para el arte están ganando popularidad
- Fraunhofer encarga células de producción automatizadas de Engel para I + D de compuestos termoplásticos
- Las cintas termoplásticas continúan mostrando potencial para aeroestructuras compuestas
- Broetje-Automation amplía la cartera de AFP para la producción de compuestos en serie
- INEOS Styrolution para construir un sitio de producción para el compuesto termoplástico StyLight
- Total Composite Solutions (TCS) lanza la solución preimpregnada epoxi para la industria aeroespacial
- Hexion presenta una solución epoxi de dos componentes para la producción de compuestos aeroespaciales
- Techsil lanza adhesivo epoxi transparente para sustratos compuestos
- Rhodes Interform fabrica prensa compuesta para AMRC