Fibra de carbono / epoxi para reducción de masa automotriz, producción en masa
El Proyecto 3.2 de IACMI evaluó compuestos reforzados con fibra de carbono infundidos con un novedoso sistema de resina epoxi para desarrollar piezas de compuestos estructurales con geometría compleja para reemplazar metales en aplicaciones de alta carga y críticas para la seguridad en estructuras corporales primarias de pasajeros de gran volumen vehículos. Una de las primeras aplicaciones evaluadas fue el uso de un preimpregnado de fibra de carbono / epoxi en el pilar B de un vehículo de prueba. El material preimpregnado de alto rendimiento redujo directamente la masa en 3 kilogramos y permitió reducir el calibre de la chapa metálica circundante, que luego podría especificarse en aleaciones menos costosas, ofreciendo un peso adicional y ahorros de costos. Fuente | Ford Motor Co.
Los fabricantes de automóviles en la mayoría de las geografías se enfrentan a los desafiantes mandatos de 2025 sobre la reducción de las emisiones del tubo de escape y / o la mejora del ahorro de combustible para los vehículos de pasajeros. Sin embargo, desarrollar tecnología automotriz fundamentalmente nueva para cumplir con estos requisitos es costoso, por lo que en muchos países se están utilizando consorcios para permitir que los miembros de la cadena de suministro compartan los costos de la investigación precompetitiva.
En los EE. UU., Una de esas organizaciones es el Institute for Advanced Composites Manufacturing Innovation (IACMI, The Composites Institute, Knoxville, Tennessee, EE. UU.). Entre las iniciativas de la organización, los miembros de IACMI de la industria, la academia y el gobierno trabajan en proyectos de múltiples frentes, que involucran el desarrollo integrado de materiales / procesos, modelado / simulación, unión de múltiples materiales y reciclaje, para resolver problemas de ingeniería, mejorar la masa del vehículo, reducir la energía. consumo y emisiones, y crear nuevos puestos de trabajo en EE. UU.
Proyecto 3.2 y el sistema de resina imposible
El Proyecto 3.2 fue uno de los primeros proyectos que asumió IACMI cuando se formó en junio de 2015, aunque la tecnología utilizada en el proyecto había comenzado a desarrollarse unos años antes de la creación de IACMI, con una colaboración entre Ford Motor Co. (Dearborn, Mich. , EE. UU.) Y lo que entonces era Dow Automotive (ahora The Dow Chemical Co., Midland, Michigan, EE. UU.). Cuando se formó IACMI y comenzó el Proyecto 3.2, Ford y Dow incorporaron al programa su trabajo anterior sobre un novedoso sistema de resina epoxi. Una vez que se unió a IACMI, el programa se amplió para incluir eventualmente varias fases que representan nuevos usos para esta resina innovadora:un pilar B preimpregnado, una tapa de cubierta de compuesto de moldura de láminas (SMC) y una compuerta trasera de aluminio / SMC.
Llamada VORAFUSE, la familia de resinas desarrollada por Dow para Ford está diseñada para su uso en preimpregnados y SMC, y para procesar en equipos de moldeo por compresión, que están ampliamente disponibles en la industria automotriz de América del Norte. Según los requisitos de Ford, la temperatura de transición vítrea de la resina (T g ) es de 150-160 ° C, se moldea a 145-155 ° C y cura en menos de 2 minutos a 150 ° C (aunque se dispone de un curado de menos de 1 minuto), lo que lo hace lo suficientemente rápido para grandes volúmenes ( 100.000 más / año) producción de vehículos. Alcanza curaciones post-molde de más del 95%. El sistema está libre de solventes y compuestos orgánicos volátiles (COV).
“Los CTQ [requisitos críticos para la calidad] definidos por Ford son únicos y nunca antes se habían logrado en un solo producto comercial”, explica Dave Bank, miembro de Dow Polyurethanes R&D. "Por esta razón, se requirió una química novedosa y una gran cantidad de productos altamente no tradicionales para cumplir con estas exigentes especificaciones".
“La separación termodinámica de la estabilidad en almacenamiento y la polimerización en la mezcla de resina / curativo produce una pasta seca que se puede infundir en la fibra de carbono sin avanzar el curado y producir un compuesto de moldeo seco y no pegajoso”, agrega Bank. "Sin embargo, cuando las condiciones de moldeo alcanzan los 150 ° C, la química está 'caliente' y el curado avanza rápidamente". Dow presentó 21 solicitudes de patente y hasta ahora ha recibido cuatro para la tecnología.
Características adicionales del sistema VORAFUSE:
- Es estable a temperatura ambiente durante más de 50 días, pero ofrece curado instantáneo a 150 ° C o más. No requiere almacenamiento en el congelador antes de cortar y moldear el kit, siempre que la temperatura de almacenamiento no supere los 40 ° C.
- Su química sin pegajosidad es ideal para el manejo automatizado. Debido a que carece de la adherencia del preimpregnado tradicional, no causará acumulación ni problemas relacionados con robots y otros equipos de manipulación automatizada.
- Contiene un novedoso agente desmoldeante interno (IMR) para que los procesadores puedan moldear 1.000 piezas antes de tener que aplicar desmoldeante externo a las superficies de la herramienta. El epoxi normalmente es antitético a la IMR porque es un adhesivo muy eficaz para los metales.
- El producto sin curar se puede reciclar en piezas de alto valor cortando y devolviendo el material a los sistemas de moldeo como un compuesto reforzado con fibra discontinua que es ideal para moldear geometrías complejas como nervaduras / protuberancias. A diferencia del preimpregnado epóxico convencional y el SMC, toda la chatarra sin curar se puede reutilizar, lo que hace que el material sea más sostenible y ahorra pérdidas de chatarra que aumentan los costos de las piezas.
Fase 1:pilar B de preimpregnado
Después de que VORAFUSE se incorporó al Proyecto 3.2, IACMI comenzó a trabajar en una aplicación automotriz que se convertiría en la Fase 1 del proyecto general. Los miembros del equipo incluyeron a Ford, Dow, DowAksa US LLC (la rama estadounidense de DowAksa BV en Tucson, Az., Una empresa conjunta 50/50 entre Dow Chemical y Aksa Akrilik Kimya Sanayii A.Ş., Çiftlikköy-Yalova, Turquía); Universidad Estatal de Michigan (East Lansing, Michigan, EE. UU.); Universidad de Purdue (West Lafayette, Indiana, EE. UU.); Universidad de Tennessee-Knoxville (Knoxville, Tenn., EE. UU.); Plásticos estructurales continentales (CSP, Auburn Hills, Michigan, EE. UU.); y el Laboratorio Nacional de Oak Ridge (Oak Ridge, Tennessee, EE. UU.).
En la primera fase, los investigadores desarrollaron preimpregnados reforzados con fibra de carbono continuos (tejidos trenzados y no rizados) impregnados con epoxi. La resina VORAFUSE P6300 fue formulada para ser compatible con la fibra de carbono de módulo estándar DowAksa A42 D012 24K. El objetivo del equipo era utilizar el preimpregnado de fibra de carbono / epoxi para desarrollar piezas compuestas estructurales con geometría compleja para reemplazar el metal estampado en aplicaciones críticas para la seguridad de alta carga en estructuras de carrocería primarias de vehículos de gran volumen.
Para el demostrador de tecnología, el pilar B en un lado de un Ford Fusion Se utilizó un vehículo de prueba. La viabilidad se evaluó primero mediante simulación y luego las piezas físicas se moldearon y se sometieron a todas las pruebas requeridas, incluidos los choques de vehículos a gran escala. Las piezas pasaron con gran éxito, reduciendo la masa en 3 kilogramos por lado en comparación con los metales existentes. La chatarra sin curar se recicló para formar las complejas estructuras de nervaduras del pilar. El compuesto de alto rendimiento permitió reducir el calibre de la chapa metálica circundante, que luego podría especificarse en aleaciones menos costosas, ofreciendo un peso adicional y ahorros de costos.
Habiendo superado todos los requisitos de Ford, el primer uso comercial del material fue para un cabezal de techo delantero y un panel de cierre del piso delantero en el Ford GT intensivo en compuestos de carbono. superdeportivo.
No es sorprendente que el preimpregnado de fibra de carbono / epoxi tenga una prima de costo, por lo que es mejor para vehículos con importantes requisitos de reducción de masa que pueden pagar una prima por oportunidades significativas de ahorro de peso.
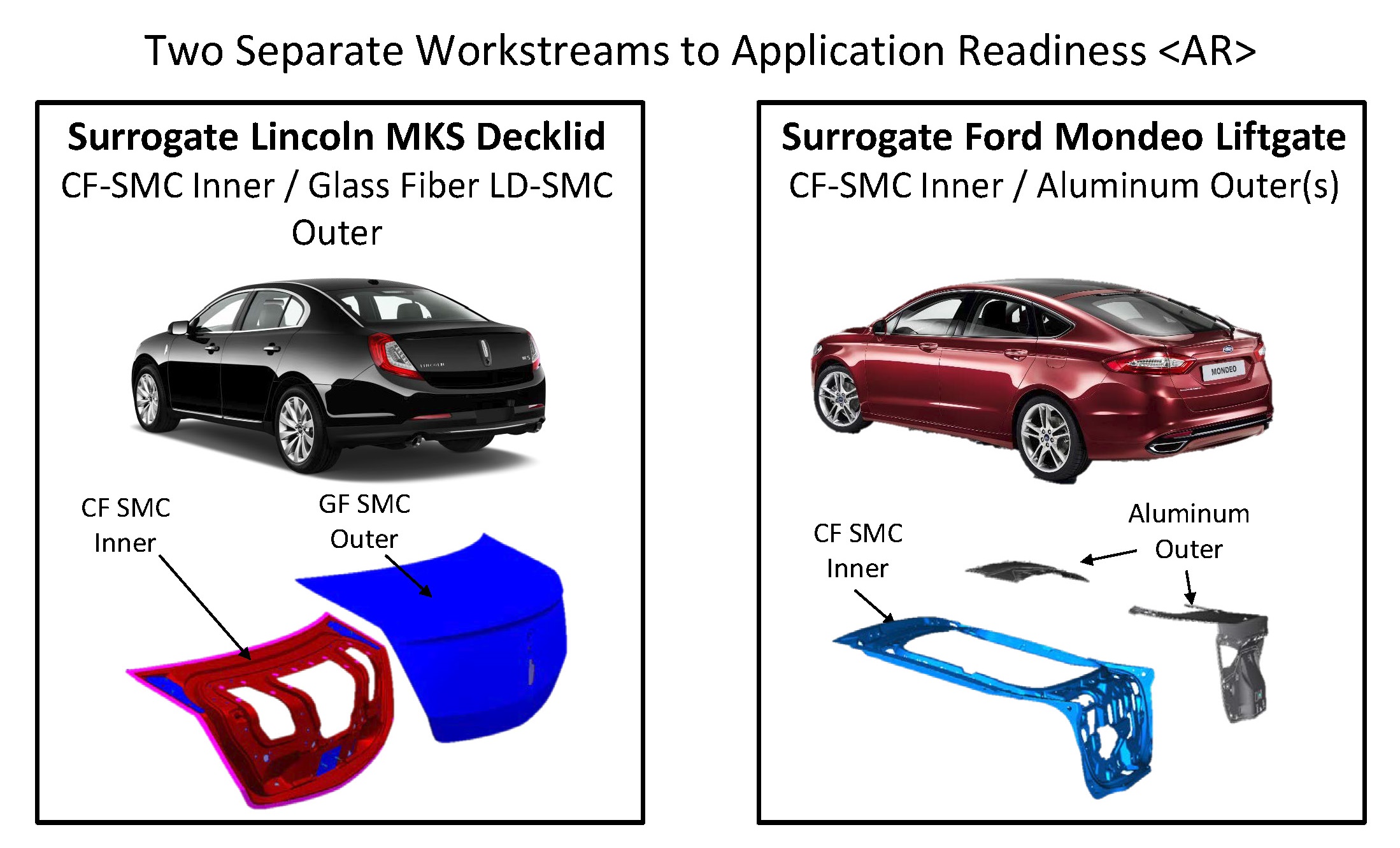
Fase 2 / Flujo de trabajo 1:tapa de la cubierta de todo SMC
Sobre la base de los éxitos del preimpregnado, los investigadores del proyecto exploraron a continuación el SMC discontinuo reforzado con fibra de carbono con la nueva resina epoxi en estructuras 3D complejas con funciones críticas para la seguridad. En un demostrador, el SMC de fibra de carbono / epoxi se utilizó como panel interior / estructural de una tapa de maletero adherida (tapa del maletero), y en otro demostrador se utilizó para el panel interior / estructural de una puerta trasera adherida mucho más grande y compleja ( escotilla trasera / puerta que contiene vidrio de ventana, motores de limpiaparabrisas, luces, etc.). En ambos flujos de trabajo, las restricciones de diseño originales, el hardware, las técnicas de unión y los adhesivos estructurales se mantuvieron sin cambios. Se utilizaron objetivos mecánicos desafiantes de más de 300 MPa de resistencia a la tracción y más de 40 GPa de rigidez a la tracción, comparable al magnesio y aluminio fundidos ya establecidos. SMC también necesitaba un flujo más alto que el preimpregnado, por lo que se desarrolló un grado ligeramente diferente, VORAFUSE M6400.
Para el demostrador de la tapa del maletero, que representó un avance incremental sobre la tecnología actual de vidrio / SMC, el SMC de fibra de carbono / epoxi reemplazó el SMC de poliéster insaturado reforzado con fibra de vidrio estructural convencional por un interior de la tapa del maletero en un Lincoln MKS vehículo prototipo. El panel interior de SMC de fibra de carbono / epoxi se unió a un panel exterior de SMC de fibra de vidrio / poliéster de baja densidad (LD, 1,25 SG), que reemplazó a un SMC de fibra de vidrio / poliéster de densidad estándar (1,9 SG). Tanto los materiales del panel exterior nuevos como los antiguos eran compatibles con la Clase A. Las herramientas originales se reutilizaron para moldear tanto el interior de SMC de fibra de carbono / epoxi como los paneles exteriores de fibra de vidrio / poliéster. El encogimiento, aunque ligeramente diferente entre ambos sistemas de resina, fue lo suficientemente cercano como para no causar problemas de ajuste y acabado (en otras palabras, no se observaron cambios dimensionales significativos).
La creación de prototipos virtual sometió el ensamblaje adherido a una serie de casos de carga desafiantes, incluida la rigidez a la torsión, la rigidez de la esquina delantera, la desviación de la cascada y las cargas de los pestillos. A continuación, se moldearon, pegaron y probaron docenas de paneles internos y externos, incluidos desafiantes impactos traseros de 89 kilómetros por hora. Los ensamblados pasaron las pruebas físicas y virtuales sin problemas.
La masa de la tapa de la cubierta se redujo un 30% (de 10,5 a 7,33 kilogramos) en comparación con el punto de referencia. Sin embargo, si los presupuestos hubieran permitido remodelar el panel interior, que podría haberse diseñado más delgado dado su mayor rendimiento mecánico en comparación con el titular, los investigadores calculan que la masa podría haberse reducido al menos un 35% con paredes de 2 milímetros, e incluso más. con paredes de 1,5 milímetros.
El SMC de fibra de carbono / epoxi pasó todos los requisitos de Ford y ahora se puede utilizar en plataformas comerciales, aunque el costo sería más alto que con el SMC de fibra de vidrio / poliéster convencional.
Fase 2 / Flujo de trabajo 2:SMC / puerta trasera de aluminio
Para el último proyecto, los investigadores recurrieron a un escenario verdaderamente desafiante:reemplazar el metal liviano con SMC de fibra de carbono / epoxi para producir un ensamblaje adherido híbrido (metal / compuesto) para compuertas elevadoras más grandes y complejas en Ford Mondeo vehículos de prueba de cinco puertas / hatchback. Para minimizar los cambios en las secuencias de construcción de vehículos, los investigadores diseñaron el ensamblaje para agregarlo a la carrocería en blanco (BIW) antes del tratamiento electroforético de capa de óxido (e-coat) y los ciclos de horneado de pintura asociados.
El SMC de fibra de carbono / epoxi reemplazó al magnesio por los paneles estructurales / internos que se unieron a los paneles externos de aluminio existentes. Dado que se tuvo que crear nuevas herramientas para producir el panel compuesto, la pieza se rediseñó. El espesor del panel se varió de acuerdo con los requisitos de rigidez / resistencia y para agregar nervaduras. Además, se usaron refuerzos metálicos en áreas de sujeción de alta carga para puntales de gas, pestillos, bisagras y cerraduras, todo lo cual hizo que el panel compuesto fuera algo más grueso, algo que permitía el espacio del paquete.
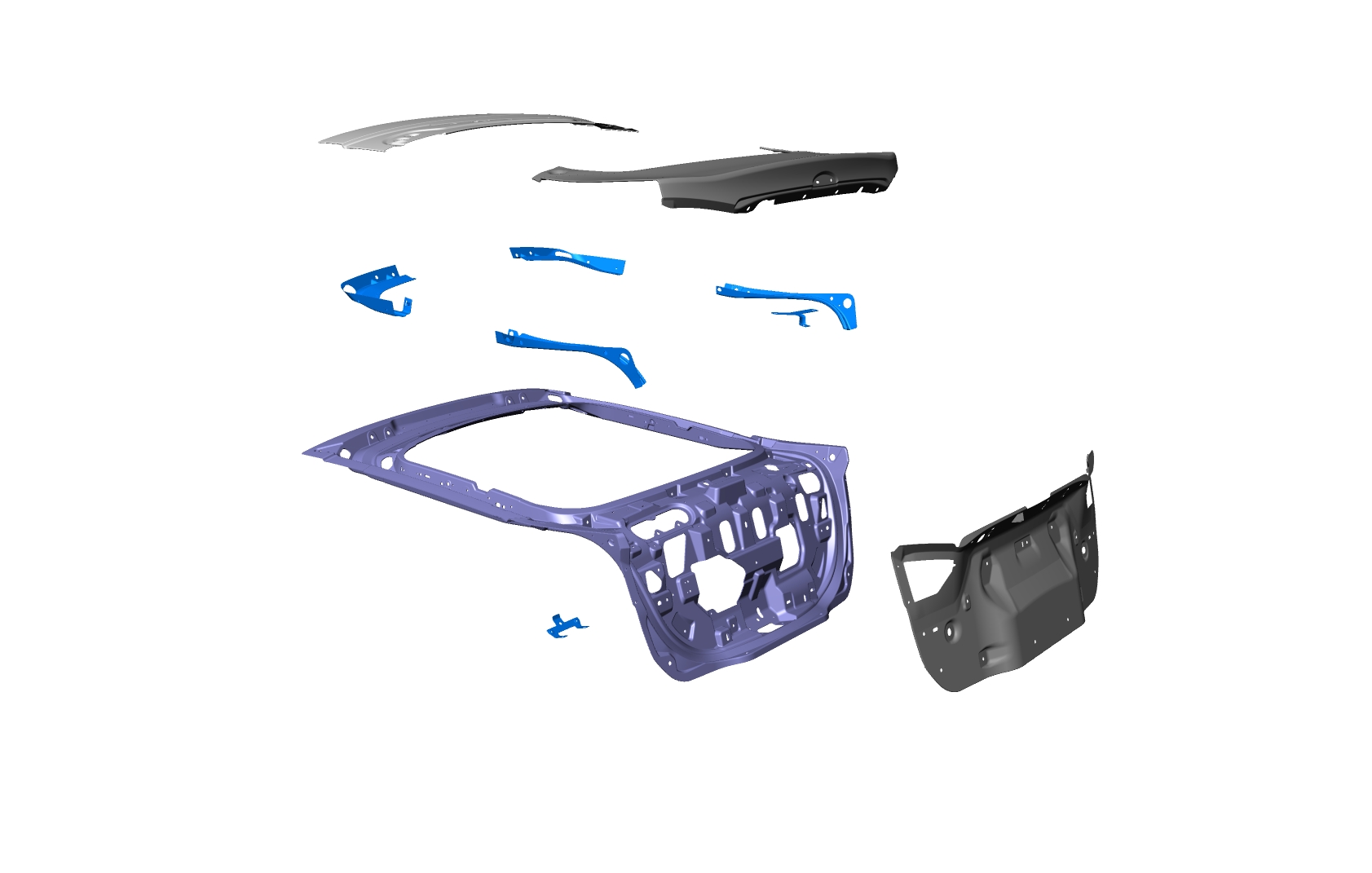
Una vista en despiece de la compuerta trasera de aluminio / SMC (con herrajes metálicos) para la versión de cinco puertas / hatchback del Ford Mondeo. Fuente | Ford Motor Co.
Estos conjuntos de materiales múltiples se sometieron a requisitos exigentes, incluidas cargas de torsión y flexión, estabilidad lateral, resistencia a la corrosión, durabilidad a largo plazo y pruebas de choque trasero. También tenían que cumplir con estrictos requisitos de estabilidad dimensional con respecto a los márgenes y la nivelación.
Si bien el sistema híbrido superó fácilmente la mayoría de los requisitos, hubo problemas de ajuste y acabado debido a desajustes del coeficiente de expansión térmica lineal (CLTE) entre los paneles internos compuestos y los paneles externos de aluminio, lo que provocó la acumulación de tensión residual en las juntas adheridas y la distorsión del panel después del enfriamiento. abajo. El trabajo posterior con el equipo de simulación de la Universidad de Purdue se centró en mejorar las predicciones del módulo, la resistencia y la cinética de curado del adhesivo epóxico 1K (elegido por su capacidad para sobrevivir a las temperaturas de la capa electrónica) con la esperanza de aplicar ingeniería inversa a un adhesivo que funcionaría mejor. La deformación se redujo en un orden de magnitud, pero falló levemente en el objetivo. Hay varias soluciones posibles:se podría probar un adhesivo 2K / curado a temperatura ambiente o curado por inducción o se podría desarrollar un nuevo adhesivo de alta temperatura. A más largo plazo, reemplazar el aluminio con un compuesto de fibra de carbono en el panel exterior eliminaría el problema, al igual que producir la puerta trasera sin conexión y agregarla más adelante en la secuencia de construcción del vehículo. Sin embargo, ambas opciones añaden costos.
El proyecto 3.2 ahora está terminando, pero ha producido una tecnología interesante, algunas de las cuales, el preimpregnado del pilar B y la tapa de la cubierta SMC, están listas para uso comercial, y algunas apuntan a áreas en las que se necesita más trabajo.
"Trabajar con IACMI y nuestros socios industriales y académicos nos permitió sumergirnos mucho más profundamente en la tecnología desde el primer director, desarrollar la ciencia fundamental y aprovechar una base de conocimientos mucho más amplia de la que podríamos haber hecho solos", resume el líder del Proyecto 3.2, Patrick Blanchard, líderes técnicos:sistemas de polímeros avanzados, investigación e innovación de Ford. "Esperamos identificar nuevas oportunidades comerciales y actividades de I + D para seguir trabajando con nuestros socios de IACMI".
Resina
- Electrodomésticos de fibra de carbono para su hogar
- Los 3 usos principales de la impresión 3D de fibra de carbono en la fabricación
- Usos innovadores de la fibra de carbono
- Fibra de carbono en aplicaciones automotrices
- 5 usos divertidos para las hojas de fibra de carbono
- ¿Para qué se utiliza la envoltura de fibra de carbono?
- 8 llaveros de fibra de carbono para cada estilo
- Materiales:PP reforzado con fibra de carbono y vidrio para automoción
- Hexion presenta una solución epoxi de dos componentes para la producción de compuestos aeroespaciales
- Foiling yate a motor impresiona en fibra de carbono / epoxi
- Serie diseñada para la línea de producción automotriz