Revolucionando el paradigma de costos de los compuestos, Parte 2:Formar
El subprograma RAPM dentro del programa Tailorable Feedstock and Forming (TFF) compiló datos analíticos de la producción actual / pasada, así como datos empíricos de sus propios ensayos de conformado para múltiples partes para generar estas curvas. El objetivo es comprender mejor el espacio comercial de piezas y procesos compuestos.
Fuente de todas las imágenes:The Boeing Co., DARPA
El programa Tailorable Feedstock and Forming (TFF) fue lanzado por la Agencia de Proyectos de Investigación Avanzada de Defensa (DARPA, Arlington, Va., EE. UU.) En 2015 para permitir la fabricación rápida, de bajo costo y ágil de piezas compuestas pequeñas y de formas complejas para la defensa. aeronave. Este programa de 48 meses tenía como objetivo aumentar la competitividad de costes de los compuestos para aprovechar su ahorro de peso y su resistencia a la corrosión y al agrietamiento frente al aluminio mecanizado. En la Parte 1 de esta serie, CW exploró la visión de TFF y su subprograma de Materia Prima Universal Adaptable para la Formación (TuFF), que desarrolló un material de hoja de fibra corta con altas propiedades mecánicas y formabilidad similar al metal.
En este artículo, el enfoque pasa de la materia prima a la formación con el segundo subprograma de TFF:Fabricación rápida de alto rendimiento (RAPM, pronunciado "wrap-em") dirigido por The Boeing Co. (Chicago, Ill., EE. UU.). El programa comenzó en julio de 2016 y ha presentado sus resultados en numerosas publicaciones, incluidos 6 artículos y dos presentaciones en SAMPE 2019. El objetivo de RAPM, como explicaron los investigadores principales y los investigadores principales de Boeing, Gail Hahn y Tom Tsotsis, es “revolucionar el paradigma de costos para pequeñas piezas compuestas, lo que permite un uso generalizado en aplicaciones de defensa ”.
“Comenzamos con esta visión de lograr un desempeño aeroespacial con eficiencia automotriz”, dice Hahn. El programa trabajó con fabricantes de piezas y materiales compuestos de automoción, incluidos Solvay Composite Materials (Alpharetta, Georgia, EE. UU.) Y SGL Composites (Ried y Ort im Innkreis, Austria), pero lograr propiedades aeroespaciales no siempre fue sencillo. “Aunque los epóxicos de curado rápido y de baja temperatura están fácilmente disponibles para aplicaciones automotrices, no se acercan a cumplir con los requisitos aeroespaciales”, dice Tsotsis. RAPM utilizó epoxis de dos componentes nuevos, de curado rápido, dirigidos a piezas de infusión de resina de grado aeroespacial. Sin embargo, inicialmente, el sistema de moldeo en SGL no podía superar los 130 ° C, lo que impedía alcanzar la meta de 30 minutos de tiempo en la herramienta.
“Nuestro objetivo era lograr un tiempo máximo de 30 minutos en la herramienta para permitir el uso de una celda de trabajo de alta velocidad para reducir los costos a nivel del sistema y ser competitivos en costos con el aluminio mecanizado”, dice Tsotsis. “Dentro de Boeing, decidimos que satisfaría todo lo que estábamos viendo para las aplicaciones de defensa”, agrega Hahn. “¿Por qué ponerlo aquí cuando podemos conseguir de 2 a 6 minutos con termoplásticos? Porque los termoplásticos requieren un procesamiento a una temperatura aún mayor con las correspondientes limitaciones de herramientas, y nuestro objetivo es brindarle a nuestra cadena de suministro muchas opciones ”.
A medida que avanzaba el programa, se abrió a materiales y fabricantes aeroespaciales e incluso a sistemas experimentales, como el XEP-2750 de Solvay. "Originalmente pensamos que podríamos evaluar completamente este sistema, como hicimos con CYCOM 5320-1 en nuestro trabajo con el programa DARPA 'Tecnología de fabricación sin autoclave' de 2007 a 2012", dice Hahn. Aunque el mismo grado de evaluación no fue posible, Solvay ahora ha comercializado XEP-2750 como CYCOM EP-2750 (consulte la barra lateral en línea “Novedoso preimpregnado para moldeo por compresión en RAPM ”) Y se benefició de las numerosas pruebas de piezas de RAPM y las lecciones aprendidas.
“Todo lo que quiero es un par de procesos para pequeñas piezas compuestas que puedan vencer al aluminio en un estudio comercial”, dice Jeff Hendrix, consultor de la industria de los compuestos y del programa TFF, sobre sus objetivos para RAPM. Entonces, ¿ha tenido éxito RAPM? CW explora los esfuerzos del programa para fabricar cientos de piezas, comparando más de una docena de configuraciones de piezas aeroespaciales a través de múltiples materiales y procesos, mientras busca métodos para reducir el tiempo y el costo.
Marco del programa
Trabajando con socios clave de la industria, RAPM probó piezas en tres pistas principales:
- Infusión de resina con compuestos de carbono HITCO (Gardena, California, EE. UU.) y compuestos SGL
- Preimpregnado termoestable formación con Solvay Composite Materials (Heanor, Reino Unido y Anaheim, California, EE. UU.), Fiber Dynamics (Wichita, Kansas, EE. UU.) y Reinhold Industries (Santa Fe Springs, California, EE. UU.)
- Conformado termoplástico con ATC Manufacturing Inc. (Post Falls, Idaho, EE. UU.) y TxV Aero (Bristol, R.I., EE. UU.)
Las pruebas de conformado se completaron en dos fases:una fase inicial de "Desarrollo de fabricación" (Fig. 1) seguida de las partes posteriores de "Desafío y transición" (C&T) (Fig. 2) para desafío desarrollos iniciales y transición candidatos con potencial para ganar contra el aluminio mecanizado.
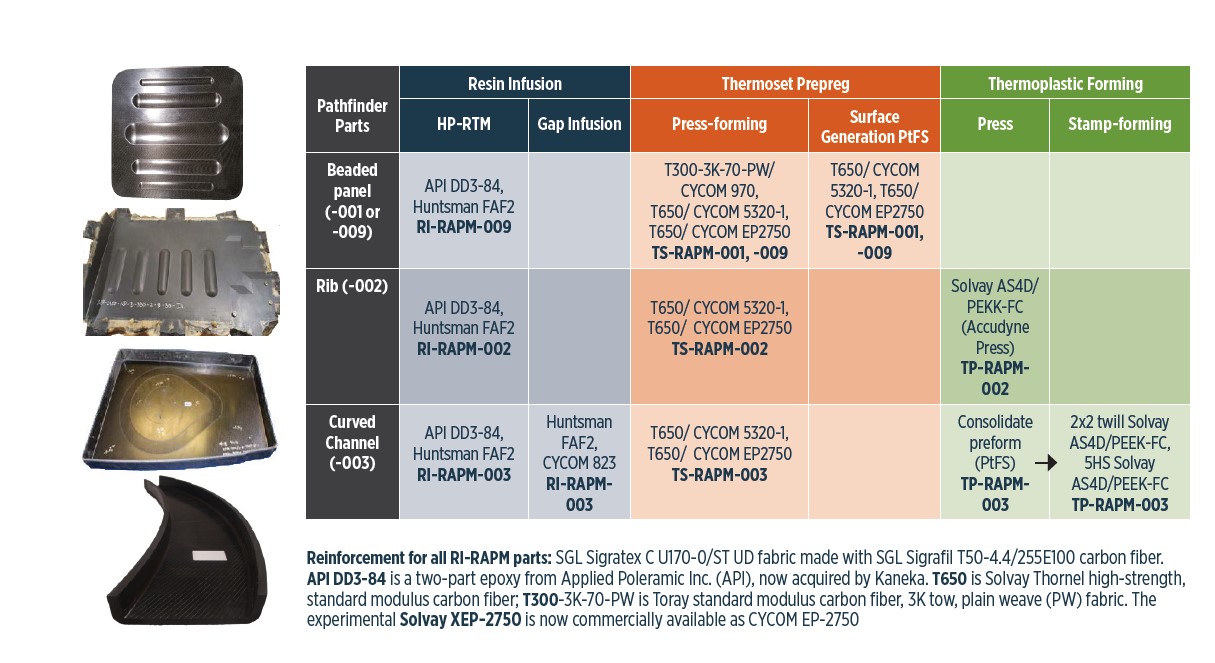
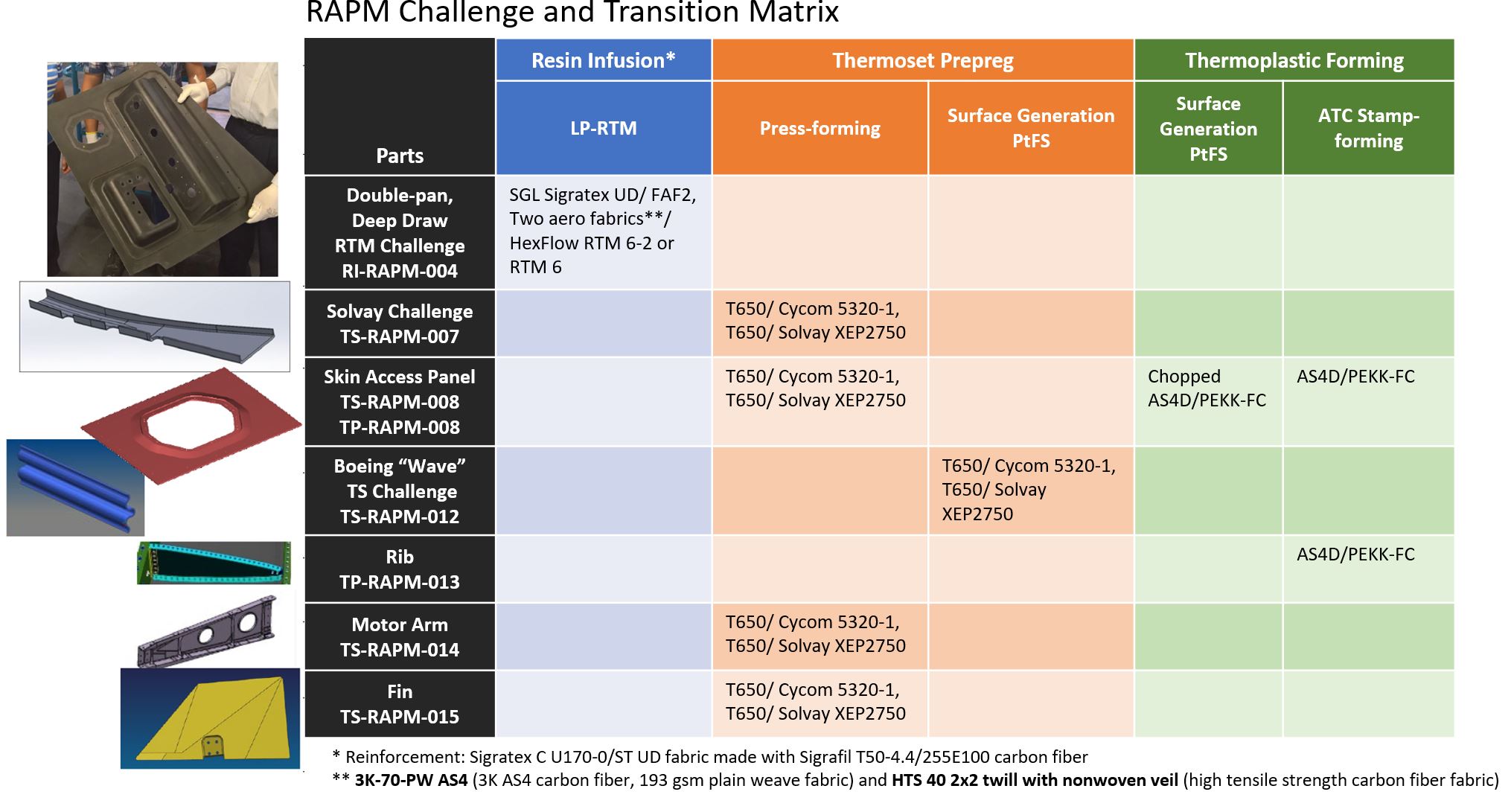
Desarrollo de fabricación Los ensayos utilizaron tres configuraciones de partes principales:paneles con reborde (había dos tipos), una nervadura con relleno (capas de construcción) y un canal en C curvo. Estas incorporaron características comunes a las piezas aeroespaciales que pueden causar desafíos de fabricación:el panel de rebordes tenía múltiples características fuera del plano, además de acolchados, acolchados y un borde vertical; el panel de nervadura tenía un relleno con múltiples bordes de 90 grados, así como un movimiento en uno de los bordes; y el canal C tenía un radio interior y exterior diferente, una curvatura variable en las bridas y caídas significativas de las capas en la red.
El objetivo era desarrollar pautas de diseño y fabricación para cada una de las tres pistas. "No se veía sexy en estas primeras pruebas", recuerda Hahn. “Pero ayudaron a determinar radios aceptables y geometrías de piezas que producirían piezas sin distorsión indeseada de la fibra, así como combinaciones óptimas de parámetros como tensión aplicada, temperatura, presión y tiempo en la herramienta”.
Las tres pistas de proceso y material de RAPM incluyeron pruebas utilizando un sistema de herramientas y control de calentamiento pixelado de Surface Generation (Rutland, Reino Unido) Production to Functional Specification (PtFS) (consulte la barra lateral en línea " Desarrollo de RAPM con PtFS ) ”), Ubicada en Boeing R&T en St. Louis, Missouri, EE. UU.“ Esto surgió porque estábamos buscando una celda de trabajo que pudiera acomodar los tres tipos de materiales / procesos en un entorno de tarifa flexible ”, dice Hahn. “Pudimos explorar diferentes enfoques y costos de control de temperatura”. La celda Boeing PtFS tiene una temperatura máxima de 440 ° C, una fuerza de cierre de 150 toneladas y un volumen de pieza efectivo de 750 por 750 por 100 milímetros.
Aunque la visión original era utilizar materiales en láminas de fibra corta de TuFF, debido a que estos no estaban disponibles al inicio, RAPM procedió con materiales sustitutos. Esto es realmente beneficioso para la industria de los compuestos porque los sustitutos abarcan materiales que reflejan más lo que se está utilizando y desarrollando fuera de este proyecto:láminas orgánicas para automóviles y preimpregnados calificados para la industria aeroespacial, epoxis experimentales, termoplásticos semicristalinos y compuestos preimpregnados cortados. Por lo tanto, los resultados y los hallazgos se refieren a todo tipo de fabricantes de compuestos, no solo a los de defensa.
Pista 1:Infusión de resina / fabricación de RTM
Las pruebas de desarrollo de fabricación en esta pista comenzaron con materiales y procesos de tipo automotriz. Las piezas fueron fabricadas por SGL Composites utilizando moldeo por transferencia de resina de alta presión (HP-RTM, 300 bar) y módulo estándar C T50, tejidos no ondulados de fibra de carbono 50K (SGL Carbon en Wackersdorf, Alemania) en configuraciones de tres partes:RI-RAPM-009 , RI-RAPM-002, RI-RAPM-003 (Figura 1). Estos se utilizaron para identificar los parámetros de preforma necesarios para piezas acabadas de alta calidad. Boeing St. Louis también probó la infusión de brecha (compresión RTM o C-RTM) para RI-RAPM-003 utilizando su sistema PtFS.
Se utilizó el modelado de flujo computacional para comprender mejor cómo infundir estas piezas, analizar el comportamiento del proceso para optimizar los materiales y los parámetros del proceso y evaluar los escenarios de inyección.
Se evaluaron los enfoques de herramientas sobre cómo y cuándo aplicar tensión a diferentes tipos de geometrías de preforma para minimizar la distorsión de la fibra. Estos cambios de diseño se validaron para una geometría de canal C modificada, seguida de análisis de tomografía computarizada (TC). Las lecciones aprendidas se aplicaron en la siguiente fase de C&T, pasando a RTM de baja presión (LP-RTM) para reducir costos.
Dentro de estas pruebas de piezas de Pathfinder, se encontraron delaminaciones en varios de los radios de extracción profunda. Tsotsis cree que estos fueron causados por una combinación de curado inicial insuficiente de la resina en la herramienta, debido a que el sistema de calentamiento de vapor de SGL restringió las temperaturas en la herramienta a 130 ° C, y tensiones térmicas / mecánicas fuera del plano durante la extracción de la pieza. “Debido a que la resistencia de la resina aún no se había desarrollado lo suficiente, estas anomalías probablemente podrían haberse eliminado con un curado completo en la herramienta, sugiere. "SGL no pudo cumplir con el tiempo en la herramienta y propiedades aeroespaciales hasta que se agregó calentamiento de aceite (en lugar de solo vapor) a la herramienta, lo que permitió el curado por encima de 130 ° C ”, señala Hahn. Esto se agregó después de las pruebas de desarrollo de fabricación.
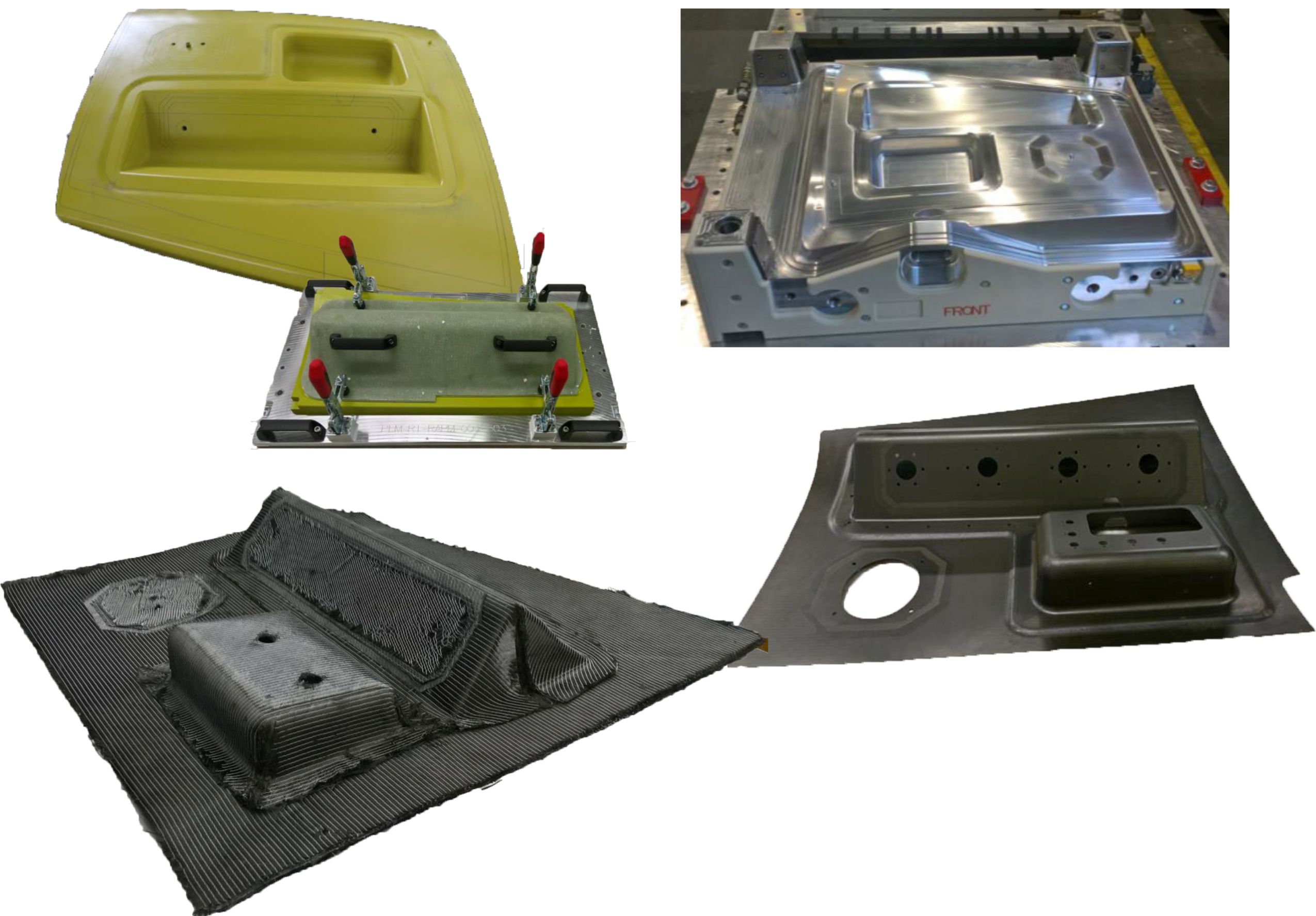
Parte del desafío de extracción profunda
Los resultados de las pruebas de desarrollo de fabricación se utilizaron luego para desarrollar pruebas de desafío y transición. También se completó el modelado para la parte de desafío de embutición profunda RI-RAPM-004 (Fig.3), que presenta dos embutidos profundos:una región rectangular de 5 centímetros y una región de 10 centímetros que pasa de rectangular a forma de V. Inspirada en un conjunto de bandeja de producción, su geometría compleja aseguró una ruta de flujo de resina no uniforme. Huntsman (Basilea, Suiza) realizó el modelado de flujo con el software PAM RTM (ESI Group, París, Francia) para un proceso LP-RTM utilizando epoxi de dos componentes FAF2 (Huntsman, The Woodlands, Texas, EE. UU.) Y SGL Carbon NCF 150 -gramos por metro cuadrado biaxial y 190 gramos por metro cuadrado unidireccional (UD) refuerzos.
RI-RAPM-004 comprende una preforma para la piel, una para cada una de las secciones de embutición profunda, más dos áreas de acumulación (Fig. 3). Se utilizaron diferentes capas para estos elementos de preforma para cumplir con los espesores de panel diseñados (consulte " Fabricación de las piezas de geometría compleja de RAPM ). ”).
"El preformado a baja presión y LP-RTM permitieron el uso de herramientas rentables (en comparación con el acero):la herramienta de preforma, con abrazaderas accionadas manualmente, se fabricó con material Raku-Tool a base de poliuretano (RAMPF Tooling Solutions, Grafenberg, Alemania); la herramienta de curado se fabricó con aluminio 5083.
Los ensayos iniciales de RI-RAPM-004 mostraron una anomalía inesperada en el flujo cerca de la salida que levantó las capas de la superficie y provocó la distorsión de la fibra. La inversión de la entrada y la salida resolvió el problema. Después de la infusión y el curado inicial en una herramienta a 130 ° C, las piezas se curaron posteriormente a 180 ° C durante 60 minutos y luego se mecanizaron hasta obtener la forma neta. Se entregaron diez piezas de alta calidad a Boeing para exploraciones en C del sistema ultrasónico automatizado (AUSS).
Las piezas de desafío terminadas mostraron una consolidación completa, una excelente alineación de la fibra y buena calidad. Las piezas exhibieron una temperatura de transición vítrea de 197 ° C y una fracción de volumen de fibra (FVF) del 49,5%, típica del NCF utilizado. El recuento de piezas de laminado de piezas se redujo en más de dos tercios en comparación con el proceso actual de preimpregnación, y la mano de obra táctil se redujo en aproximadamente un 90%. RAPM también hizo parte del desafío con resinas y telas calificadas para la industria aeroespacial, para probar la adaptabilidad de las herramientas y procesos que desarrolló, y fabricó piezas que pasaron los requisitos de producción para pruebas no destructivas (NDT).
Pista 2:formación de preimpregnados TS

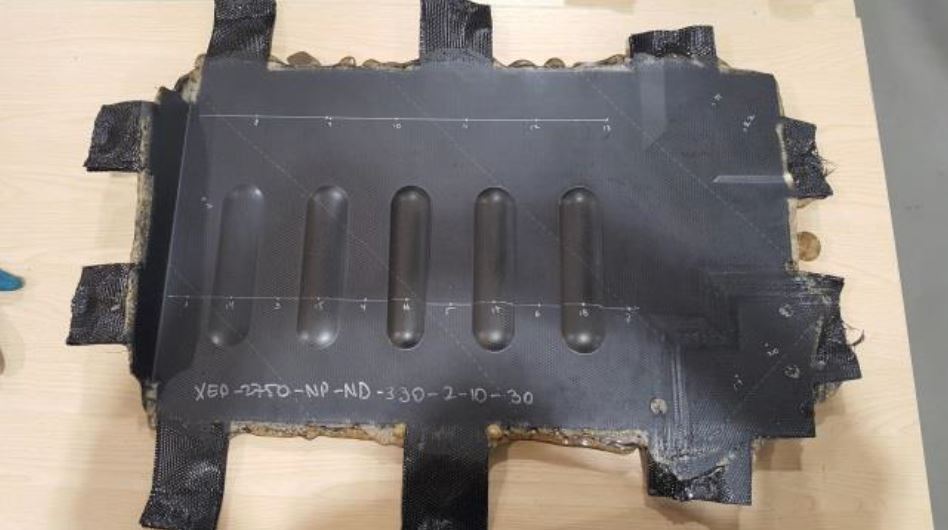
En el Centro de Aplicaciones de Solvay en Heanor, Reino Unido, se fabricaron tres piezas preimpregnadas termoestables de desarrollo de fabricación (TS), utilizando estampación de marco de resorte y / o formación de doble diafragma (DDF). Las tres piezas se fabricaron utilizando preimpregnados epoxi basados en resinas Solvay, incluidas CYCOM 5320-1, CYCOM 970 y el sistema aeroespacial CYCOM EP-2750. "CYCOM 5320-1 es nuestro recurso para piezas fuera del autoclave (OOA), pero también se utiliza como un sistema calificado para el autoclave", dice Hahn. “CYCOM 970 es una opción de preimpregnado solvente versus termofusible, y [CYCOM] EP-2750 es nuestro sistema para el formado por prensado porque está optimizado para la física y la cinética del proceso, que mostramos produce las mejores partes”.
El estampado con marco de resorte y el DDF son procesos de moldeo por compresión isotérmica en los que los preimpregnados termoendurecibles se cortan, clasifican y consolidan en una preforma 2D. A continuación, la preforma se precalienta, se transporta a herramientas metálicas combinadas y se moldea en una prensa de platina hidráulica convencional. La preforma puede mantenerse en tensión mediante un marco de resorte (Fig. 4), que reduce las arrugas inducidas por las zonas de compresión del material durante el conformado. Alternativamente, DDF coloca la preforma entre dos diafragmas, eliminando la necesidad de limpiar y desmoldar el molde. La preforma está pegada a uno de los diafragmas, esencialmente manteniéndolo en tensión, aunque no tan directamente o adaptable como con un marco de resorte. En RAPM, el tipo de resorte, las ubicaciones y las tensiones se optimizaron para cada pieza mediante simulación, al igual que el marco de resorte. Por ejemplo, el panel de cuentas TS-RAPM-009 usó un marco que puede accionarse hacia arriba y hacia abajo para adaptar la formación de la carga en paralelo con el cierre de la prensa.
RAPM minimizó el tiempo de pieza sobre herramienta eliminando piezas dimensionalmente estables después de un curado inicial de 15 a 30 minutos y luego curado por lotes para aumentar la capacidad de velocidad. Las familias de piezas también se investigaron utilizando un solo conjunto de herramientas, por ejemplo, un canal en C con tres ángulos de brida variables a lo largo de un ala, para maximizar el uso de la celda. Otros objetivos que guiaron el enfoque de RAPM TS incluyeron:
- Clasificación y formación automatizadas para minimizar el trabajo manual
- Rendimiento mecánico aeroespacial con curado a 177 ° C
- Herramientas de acero con capacidad para> 1,000 piezas por juego de herramientas.
Desarrollo para la parte del desafío "wave"
Se formaron piezas de desarrollo de fabricación de preimpregnado termoestable, indexando una variable a la vez, hasta que se alcanzó la calidad suficiente de la pieza. Se evaluaron variables como la velocidad de cierre de la prensa, la posición de cierre y la presión de cierre, con el objetivo de consolidar el material en el punto correcto de la curva de reología para crear presión hidrostática interna, minimizar el sangrado de resina y evitar que el curado avance demasiado, para evitar grietas. inducción. Una vez que se establecieron los parámetros de formación, se hicieron de tres a cinco partes para verificar la repetibilidad del proceso y luego se probaron para determinar la calidad. Los paneles con cuentas mostraron una porosidad <0,5% debido a las altas presiones de consolidación (20,7 bar). También se produjeron costillas repetibles de alta calidad.
Las lecciones aprendidas se aplicaron luego a la pieza de desafío ondulada corrugada, TS-RAPM-012, para demostrar el moldeo por compresión de laminados UD gruesos (espesor nominal de 6,3 milímetros) en formas con curvatura de radio estrecho (12,7 milímetros). Para cumplir con los requisitos, la pieza utilizó una capa casi isotrópica de cinta UD de fibra de carbono de módulo intermedio (IM7; Hexcel; Stamford, Connecticut, EE. UU.). Las capas exteriores de tela de fibra de vidrio estilo 108 y fibra de carbono de módulo estándar Solvay THORNEL T650 en una tela satinada de 8 arneses protegen las fibras UD y evitan la corrosión galvánica en el lado que se acopla a una pieza metálica. El uso de la resina epoxi Solvay CYCOM 5320-1 permitió ciclos de curado isotérmico de menor duración (≤ 30 minutos) con un poscurado independiente de 2 horas a 177 ° C.
La pieza de desafío de olas se moldeó utilizando la celda de trabajo PtFS de Boeing y las caras del molde de acero P20 con sellos integrados de vacío y resina. La cavidad de la herramienta era más delgada que el espesor nominal del laminado para tener en cuenta la variación en el contenido de resina del material, manteniendo la presión hidrostática interna para piezas de alta calidad.
Se probaron tres parámetros del proceso, incluido el conformado en frío (preformado de las capas sin calor), la preconsolidación por reducción en caliente y el precalentamiento de la preforma. Se rechazó el conformado en frío por consumir mucho tiempo y no ser útil. Para la preconsolidación, los laminados se embolsaron al vacío en una placa con un respiradero de fibra de vidrio tejida y se redujeron a vacío total en un horno a 116 ° C durante 40 minutos. Aunque un precalentamiento infrarrojo automatizado es estándar para la producción industrial, en estas pruebas, el precalentamiento consistió en colocar la preforma en el molde caliente (179 ° C) y cerrar tanto como fuera posible sin tocar durante 3 minutos. Luego, la pieza se moldeó por compresión.
La prueba 8 de las nueve completadas (# 0-8) produjo la pieza de mayor calidad, principalmente atribuida a la preconsolidación. Las muestras tomadas cumplieron con el grosor (un problema con otras partes) y la calidad del laminado con un volumen de fibra de 59-63% y un contenido de huecos de 0-0,6%.
Pista 3:canal C y costilla TP con forma de vejiga
RAPM eligió la nervadura TP-RAPM-002 de las pruebas de desarrollo de fabricación para demostrar el moldeo por compresión de un solo paso desde la materia prima hasta la pieza compleja terminada, y el canal curvo TP-RAPM-003 para un enfoque de dos pasos. Boeing St. Louis moldeó la nervadura -002 usando una prensa Accudyne Systems (Del., EE. UU.) Y consolidó espacios en blanco para el canal C -003 usando el equipo PtFS. En un segundo paso, ATC Manufacturing selló los espacios en blanco del canal C en partes.
Para la nervadura -002, RAPM usó cinta UD de 12 pulgadas de ancho suministrada por Solvay:fibra de carbono 12K AS4D (Hexcel, Stamford, Connecticut, EE. UU.) Polietercetonacetona reforzada (PEKK). La tela usada -003 de canal C de Cramer Fabrics Inc. (Dover, N.H., EE. UU.):Fibra de carbono sin encolar 3K AS4 (Hexcel) en una tela cruzada de 2x2, recubierta de polvo con polieteretercetona (PEEK); el peso superficial de la fibra es de 250 gramos / metro cuadrado; el contenido de resina es del 42%.
Problemas de formación de termoplásticos (TP)
Los compuestos TP se procesan a temperaturas más altas que los termoendurecibles, por ejemplo, 390 ° C para PEEK y 375 ° C para PEKK, lo que presenta una serie de problemas. Los materiales de herramientas que pueden soportar estas altas temperaturas de proceso son limitados. Además, el gran delta de temperatura entre el procesamiento y la extracción de la pieza hace que sea difícil mantener una temperatura uniforme de la herramienta. El remedio son los baños de calor y / o rampas más lentas hacia arriba y hacia abajo, lo que alarga los tiempos de ciclo.
Las altas temperaturas también presentan un desafío del coeficiente de expansión térmica (CTE). El CTE del material de la herramienta es a menudo diferente al del laminado TP, lo que puede hacer que el laminado TP se contraiga y se aleje de la herramienta, reduciendo la presión aplicada y evitando la consolidación total. Además, el CTE laminado TP es constante a lo largo de la fibra de carbono pero una curva bi-lineal perpendicular a la fibra. Esto da como resultado una contracción diferente en el plano frente a fuera del plano a medida que el laminado TP se calienta y enfría y también debe abordarse en el diseño de herramientas.
Los laminados TP también pueden encogerse de las herramientas a medida que el volumen de resina disminuye con el cambio de líquido a sólido. Es durante esta fase de enfriamiento, cuando ocurre la cristalización crítica de la matriz de resina, que se requiere un control preciso sobre la uniformidad de la temperatura y la presión del laminado para garantizar propiedades de alta calidad en la pieza terminada.
Otro problema es que las herramientas deben estar completamente selladas para contener el líquido TP fundido durante el moldeo. “Sellar una herramienta entre 375 ° C y 390 ° C es difícil, ya que hay muy pocas juntas adaptables que puedan soportar esta temperatura y TP que forman presiones de 300 a 500 psi o más ”, dice Hahn. “Estamos limitados a juntas metálicas o herramientas metálicas combinadas para proporcionar las características de sellado. Las herramientas elastoméricas serían increíblemente beneficiosas, sin embargo, todos los elastómeros actuales se degradarán a las temperaturas de formación de TP ”.
Boeing St. Louis requirió herramientas novedosas para crear presión horizontal en los elementos verticales de la nervadura durante la consolidación en una prensa hidráulica que solo tenía actuación vertical. Su solución fue una vejiga delgada de aluminio (se utilizó un sistema similar para formar TP-RAPM-003, Fig. 5). Presurizado con gas argón inerte a altas temperaturas, la vejiga se expandió para aplicar una presión uniforme a todas las superficies de las piezas durante la consolidación.
Las herramientas superiores e inferiores estaban hechas de acero inoxidable 410, que coincidía con el CTE en el plano del laminado de fibra de carbono UD / PEKK. Durante el ciclo de prensado, la herramienta superior con la vejiga de aluminio bajó y presionó lentamente la bandeja en la cavidad hembra de la herramienta inferior. La vejiga se redujo en un 30% con respecto al grosor de la pieza final para acomodar la mayor parte de la preforma de cinta no consolidada en este proceso de un solo paso. Esta herramienta se montó en una prensa convencional con cartuchos calefactores eléctricos, cableada en 12 zonas controladas de forma independiente, más las seis zonas principales de la platina de la prensa, para controlar la temperatura de la superficie de la herramienta en las bridas y el alma de la nervadura.
Estos ensayos de conformado produjeron piezas compuestas con resultados NDI aceptables. Sin embargo, el diseño de la herramienta de vejiga requiere un mayor desarrollo para mejorar la formación de la disposición en los estrechos radios internos de la pieza y también para mantener un espesor de superficie uniforme.
Consolidación de espacios en blanco de tela PEEK
Para el canal en C curvo TP-RAPM-003, la tela de sarga de PEEK 2x2 con recubrimiento de polvo utilizada tenía un factor de volumen relativamente alto. Boeing St. Louis first consolidated the layup, which dropped from 32 to 24 plies along the length of the part, into a flat blank with a tapered cross-section, and then sent the blanks to ATC Manufacturing, which stamped the final part with vertical flanges.
As with the rib, Boeing used a forming bladder and steel top and bottom tools. The bladder was changed to AZ31 magnesium, which better resists rupture versus aluminum. The C-channel tool was designed to operate within the Surface Generation PtFS forming cell to enable more rapid heating and cooling versus the conventional press with cartridge heaters used for the rib.
The C-channel tooling approach was developed to increase flexibility for multiple parts. The layup was placed onto the bottom tool, which was heated to the material’s glass transition temperature (Tg ) to maintain pliability without melting. A volume reducing frame that included a pressure-sealing gasket was placed on top of the bottom tool, leaving a cavity slightly larger than the part layup (Fig. 5). Heat and hydraulic pressure were applied from the top tool through the bladder to the layup. Once at forming temperature, argon gas was applied to the bladder, forcing it down into the frame cavity to apply pressure to the tapered blank. The tool temperature was then increased through the melt phase of the material while maintaining bladder pressure, which prevented material from flowing across the lower tool while in melt phase.
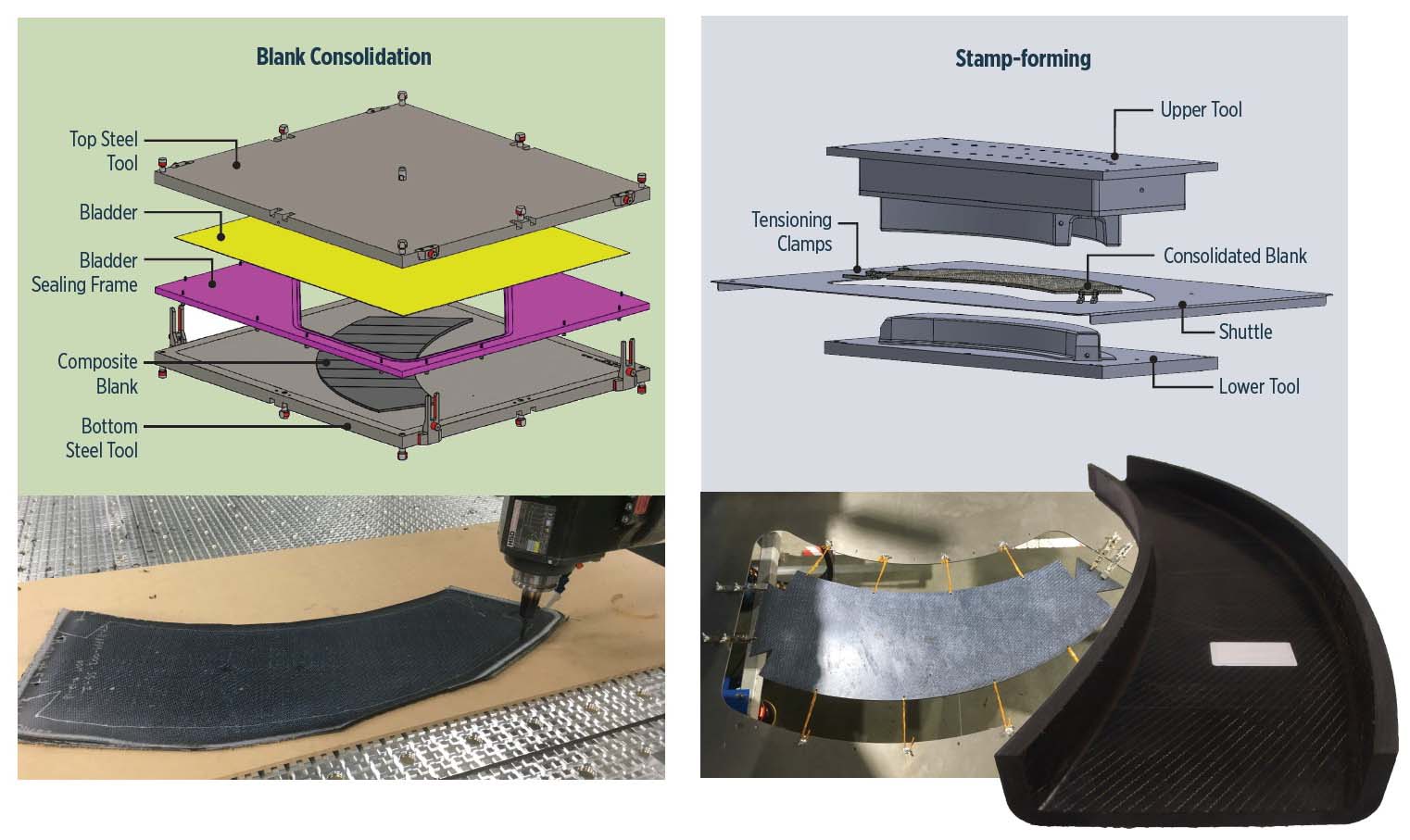
Preforming cycle time comprised 55 minutes for bladder and TP charge to reach process temperature and 30 minutes to cool below the PEEK crystallization temperature. Pressure ranged from 1.4 to 9.7 bar and was maintained manually from a high-pressure tank with a valve. With the recent incorporation of a pressclave system into the PtFS cell, autoclave-like control of vacuum and pressure (±3 psi) in the press mold cavity will be automated in the future.
TP stamp-forming
Consolidated blanks for the -003 C-channel were sent to ATC Manufacturing for stamp-forming, in which the blank is heated sufficiently above melt temperature to ensure polymer flow. It was then transferred to a rapidly closing press to form and cool the part quickly. The forming tool in the press is kept at constant temperature, enabling rapid cycle times by eliminating ramp-up and cool-down. The tool temperature must be between melt temperature and Tg to develop the required level of thermoplastic matrix crystallinity in a short time, yet ensure the part can be removed without deformation. A series of blanks with implanted thermocouples was used to validate the complete thermal cycle for stamp-forming the C-channel.
Forming simulations using Aniform software (Enschede, Netherlands) showed the highly drapable PEEK fabric blank still posed a risk of wrinkling in compression areas, namely the inner (smaller radius) flange. Thus, a tensioning system (Fig. 5) comprising shuttle plate and clips held the blank in tension as the matched metal tools closed to form it. Despite this, the flange face in compression still showed buckling as fiber was pushed inward at the inner radius. “All three RAPM tracks struggled to make this part,” Hahn contends. “Its geometry was extreme, and not so indicative of a real part, but more designed to push what we could achieve in formability.”
The manufacturing development trials led to challenge and transition parts that included multiple versions of the TP-RAPM-008 skin access panel, the TP-RAPM-013 rib with joggles on the flanges and a bladder study using three different geometries of the TP-RAPM-017 panel (Fig. 2). Boeing St. Louis produced all of these except for the TP-RAPM-013 rib, which ATC produced. “Even though this part was made with UD tape, which is typically more challenging to form versus fabric, we were able to form these parts very well,” says Trevor McCrae, R&D director for ATC Manufacturing. Overall, the TP forming trials showed that stamp-forming can produce complex geometries that might not be possible with conventional compression molding.
Learning to cut cost vs. aluminum
RAPM has demonstrated novel forming capability in all three tracks and amassed numerous lessons learned, ranging from how to position pad-ups to prevent slippage during compression molding to guidelines for part geometry to maximize quality and minimize tooling cost. “Understanding the effects of out-of-plane features, radius-to-thickness ratio and distance between geometric details becomes key as you move to small parts,” Hahn observes. “Standardizing features such as radii, curves and flange angles can help mitigate cost drivers, for example, reducing tooling costs, the number of forming trials during development and the need for multiple scans during NDI (nondestructive inspection) by enabling a standard AUSS shoe for a family of parts.”
Another cost driver RAPM highlighted was the time-consuming pre-consolidation step during TS prepreg compression molding. “Low-bulk and higher resin content prepregs widen the process window and increase repeatability for high-quality parts,” Hahn explains. “Solvay has developed a patent-pending ‘transformer film’ which can be applied to lower-impregnation prepregs before compression molding as a method of guaranteeing hydrostatic pressure in the mold cavity during consolidation.”
Although RAPM won’t officially end until fall 2020, followed by additional published results, findings so far for selected parts, which are based on real defense programs, show that composites can compete with machined aluminum (Fig. 6). Though the selected resin infusion and TP parts reduce recurring costs — e.g., materials, machine time, etc. calculated over total parts per family assuming non-recurring infrastructure is in place — the TS-RAPM-012 wave assembly actually shows a 7% increase vs. machined aluminum. However, it does achieve desired weight savings, and at a premium that is actually within the margin mandated by Hendrix:“No one is going to pay 2X for the weight savings composites offer; they must cost within 10 percent of aluminum.” However, he does concede, “There are still non-recurring time and cost issues to figure out, such as tooling and the development required to successfully form the shape.”
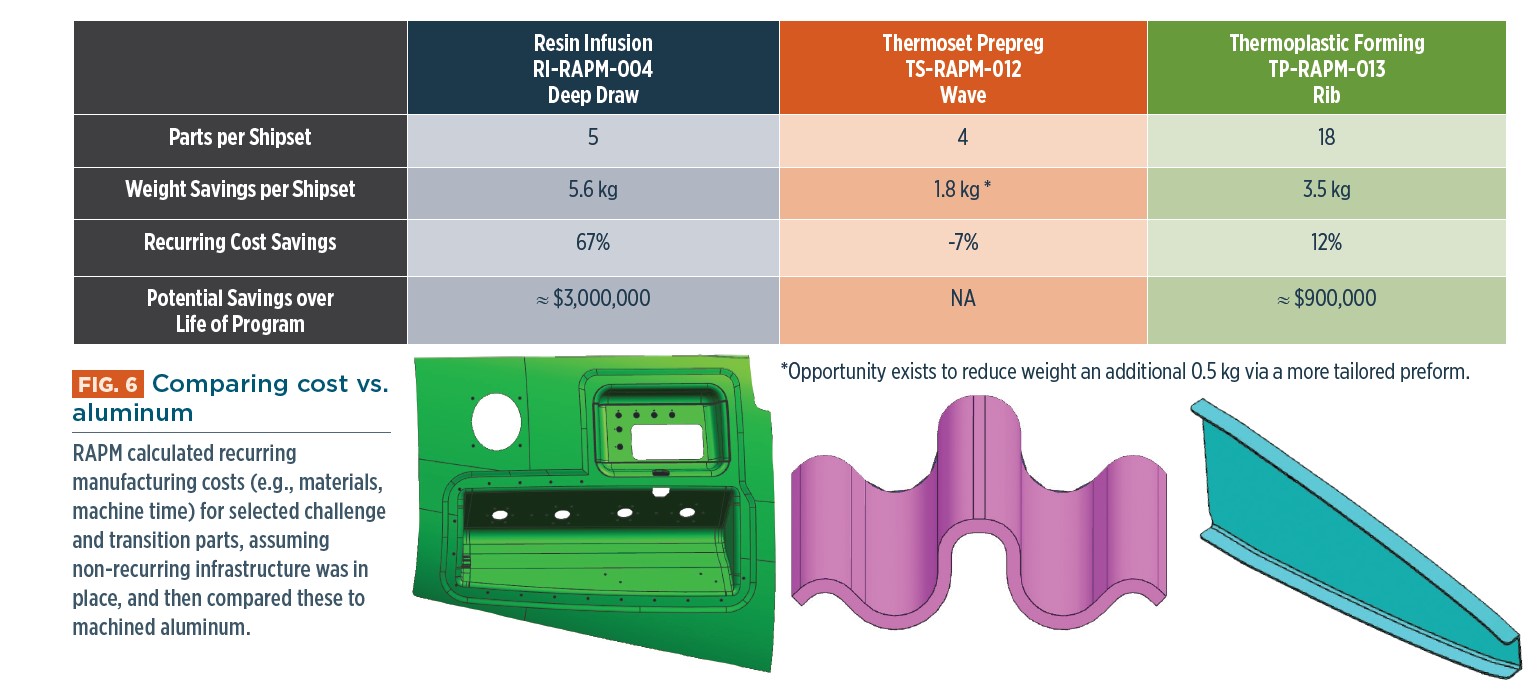
Expanding options
Although resin infusion wins for large parts, says Hahn, TS and TP stamping look pretty good for small parts. “Initial tooling cost for resin infusion is hard to overcome unless the metal parts are very complex, requiring a lot of machining,” she explains.
“Thermoplastics look good for high volume, but a subcontractor for a given program might not be set up to do thermoplastics. However, thermoset stamping might be a very good option, even for low-volume replacement parts. Because defense applications are so wide-ranging, it is important to have more than one material and process in a trade discussion.” Hahn notes that RAPM has opened up new materials and proven aerospace materials can work in automotive-type processes. “We also brought in new manufacturers.”
Hendrix agrees that RAPM’s aerospace and automotive manufacturing exchange was beneficial. Further, he was impressed with Solvay’s and SGL’s ability to form complex shapes without fiber distortion or other defects. “What it takes to make aesthetic auto parts actually has benefits,” he concedes. “You can’t have wrinkles or bad surface finish; they have to be perfect. But it still took multiple trials and significant development for them to form the RAPM parts. I’m not sure defense programs will want to invest in this non-recurring engineering if they’re dealing with small quantities. The economics will be on a case-by-case basis, but tooling and development remain issues we need to address.” Hahn adds, “We are publishing lessons learned, enabling more informed trade studies with expanded options and establishing a reasonably open basis for industry discussion.” CW will continue this discussion with an update once RAPM wraps up later this year.
Resina
- 6 formas de reducir el costo de la impresión 3D
- La pregunta de mantenimiento del contrato - Parte I
- Fabricación de materiales compuestos:Fabricación de materiales compuestos
- La economía de la impresión 3D
- Parte del mes del cliente
- Seguimiento de la historia de los materiales poliméricos, parte 13
- Las ventajas de un programa de palets corporativos
- ACMA lanza el programa Thermoplastic Composites Conference 2020
- La conferencia magistral de SAMPE 2018 mira hacia el futuro de los compuestos
- El costo del mecanizado CNC
- El valor de la fundición de inversión (parte 2)