Producción automatizada de aerocomposites:¿Moldeado líquido o termoplástico soldado?
A medida que los fabricantes de equipos originales y los proveedores exploran los materiales y procesos que permitirán la próxima generación de aeronaves, se están demostrando dos enfoques diferentes. El primero es el moldeado líquido de preformas de fibra seca visto, por ejemplo, en la línea de moldeo por transferencia de resina de alta velocidad (RTM) de Spirit AeroSystem (Prestwick, Escocia) para spoilers Airbus A320 y también en el programa Wing of Tomorrow (WOT) dirigido por Airbus. que utiliza la colocación automatizada de telas que no se arrugan (NCF) e infusión de resina líquida, seguida de un curado fuera de autoclave (OOA) en un horno (consulte "La línea RTM aeroespacial automatizada de alta velocidad ofrece spoilers de próxima generación" y "Actualización:ala inferior skin, Wing of Tomorrow ”respectivamente.)
El segundo son los compuestos termoplásticos (TPC) que se presentan, por ejemplo, en el Clean Sky 2 Multifunctional Fuselage Demonstrator (MFFD), donde las pieles endurecidas se crean utilizando la colocación automatizada de fibras:consolidadas in situ para la mitad superior y consolidadas en autoclave para la inferior. mitad - seguido de ensamblaje mediante soldadura. Estos programas utilizan la automatización para aumentar la tasa de producción y la calidad al tiempo que reducen los costos. Pero, ¿cómo se comparan?
El Instituto de Estructuras y Diseño del Centro Aeroespacial Alemán (DLR) opera el Centro de Tecnología de Producción Ligera (ZLP) en Augsburgo. Entre sus muchos proyectos de fabricación de materiales compuestos, PROTEC NSR y Fast Lane RPB presentan una oportunidad única para comparar, respectivamente, un mamparo de presión trasero termoestable moldeado por líquido (RPB) para el Airbus A350 de dos pasillos con un RPB termoplástico para el Airbus de pasillo único. A320. Ambos proyectos trabajaron con el proveedor de nivel 1 de estas estructuras, Premium Aerotec Group (PAG, Augsburg, Alemania), y demostraron la automatización al evaluar el tiempo y el costo del ciclo.
Mamparo TS moldeado por líquido
“Empezamos hace muchos años con PAG en el proyecto AZIMUT para analizar procesos manuales para la fabricación de compuestos”, dice el Dr. Lars Larsen, jefe de tecnologías de ensamblaje y unión en ZLP Augsburg. "Nuestra primera solución de automatización fue para la colocación, y luego trabajamos para automatizar más operaciones". El objetivo principal de PROTEC NSR era tomar estas soluciones especializadas para la producción de RPB y llevarlas a un solo proceso automatizado, explica el Dr. Marcin Malecha, gerente de proyectos de PROTEC NSR en DLR.
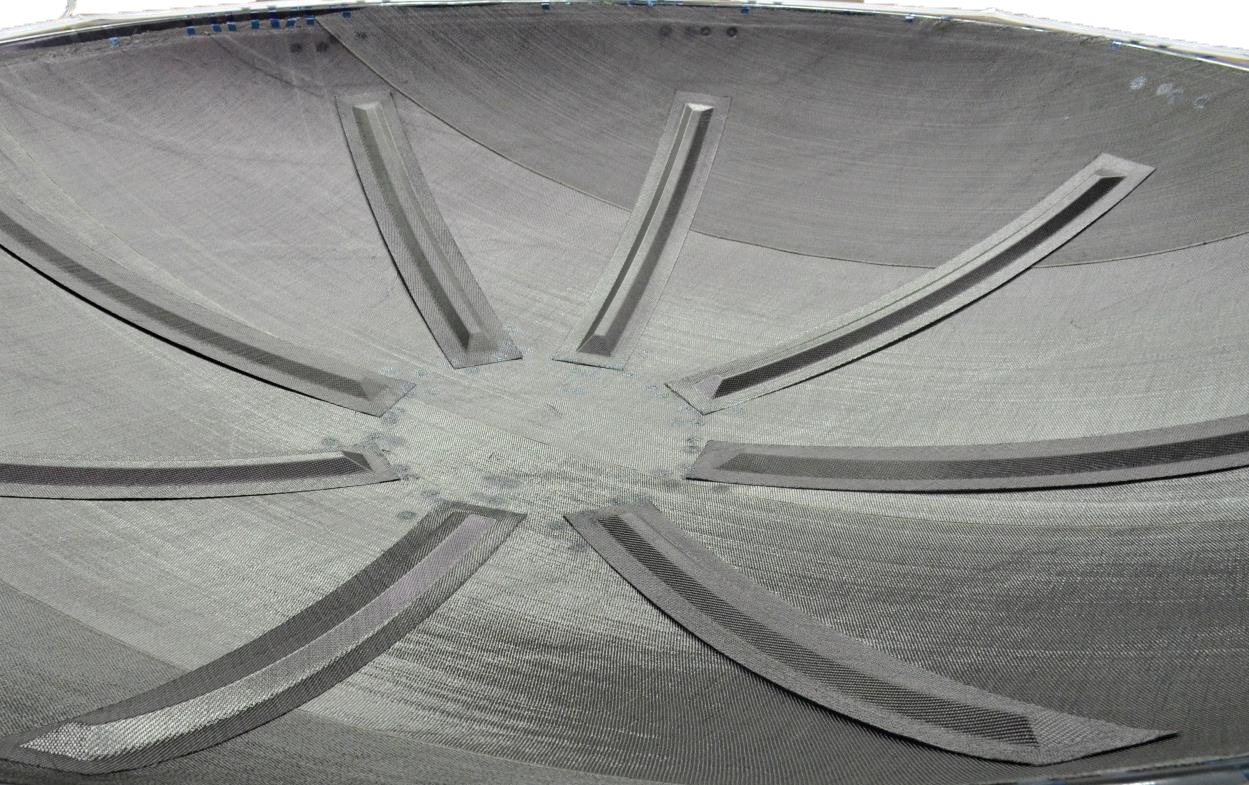
Preforma y pinzas. Los pasos del proceso para crear la preforma seca envasada al vacío se muestran en la Fig. 1 a continuación. Esto se infundió con resina epoxi RTM6 utilizando el proceso asistido por vacío (VAP) patentado por Airbus, que emplea una membrana semipermeable para reducir la porosidad. La disposición de la preforma comprendía dos juegos de 16 capas de hasta 5 metros de largo utilizando el ancho total de 1,27 metros de la tela de fibra de carbono satinada de 5 arneses. Incrustados entre estos dos conjuntos había 25 piezas de refuerzo de forma compleja con un tamaño de hasta 1,5 por 2,5 metros. Se colocaron ocho largueros en la parte superior.
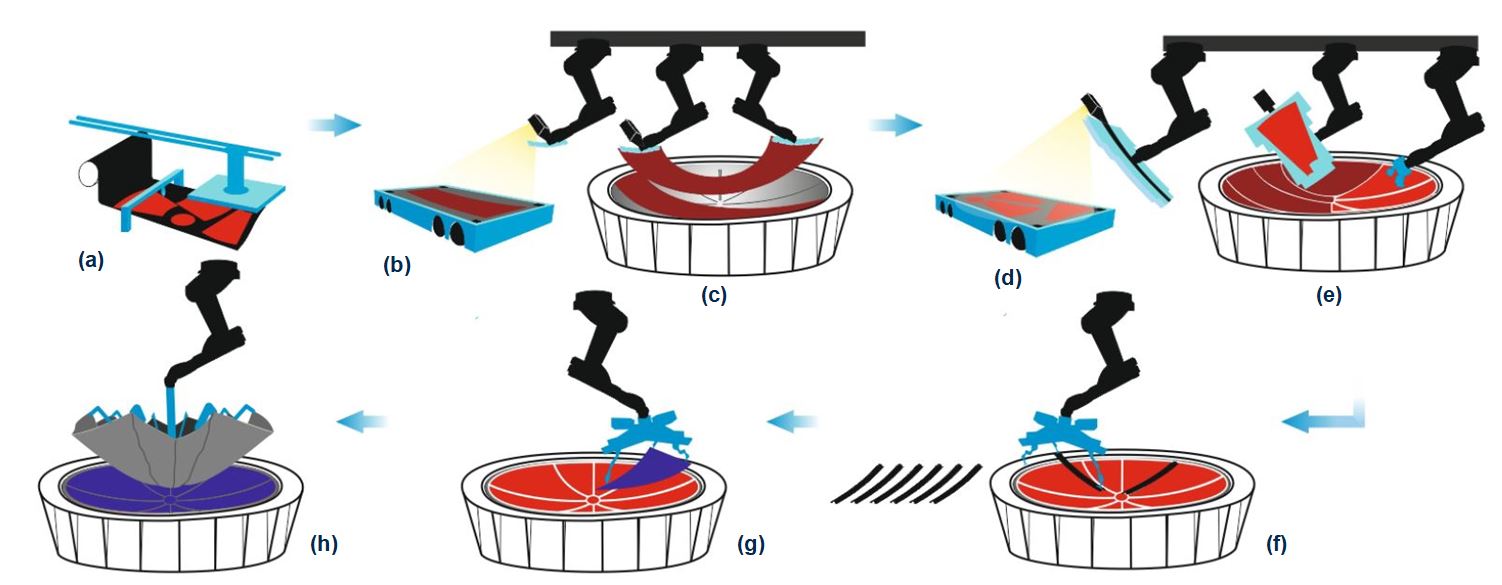
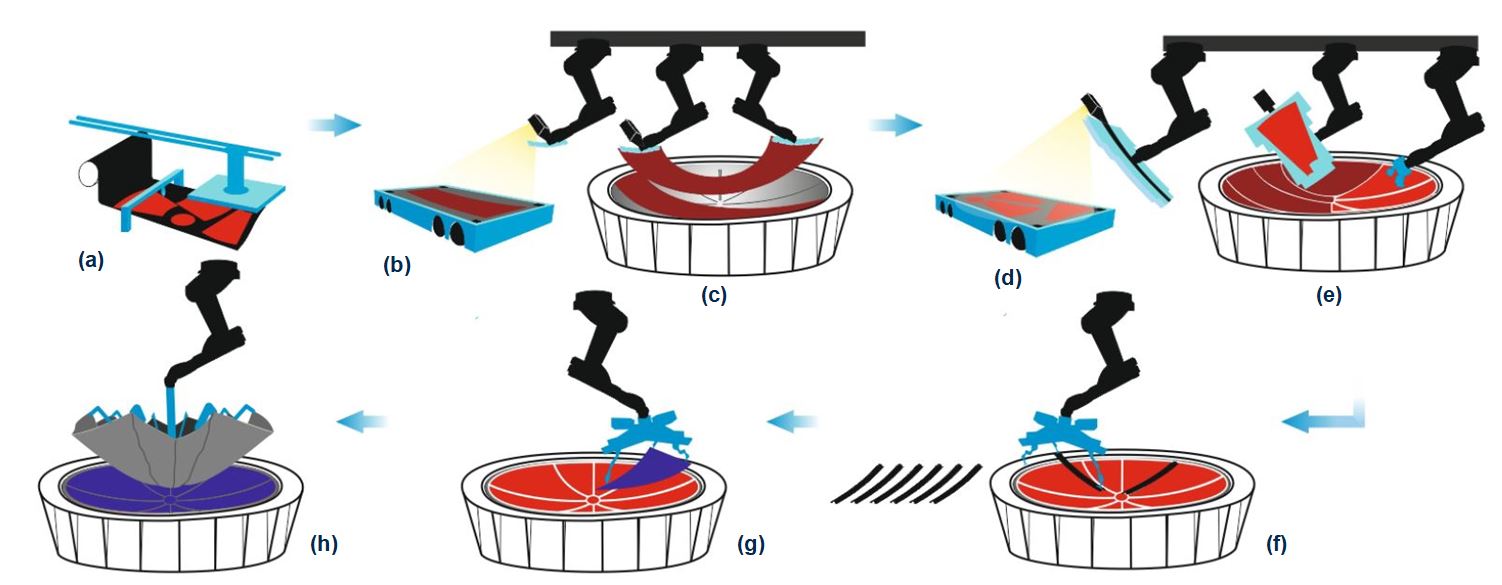
“Desarrollar herramientas y pinzas que pudieran lograr la precisión necesaria en el drapeado y la manipulación fue uno de los mayores desafíos”, señala Larsen. Esto se debió en parte a la compleja combinación de capas que requería tres mecanismos de drapeado diferentes:
- Aplicación de material de ancho completo directamente del rollo que debe adaptarse a la forma del molde.
- Colocación de capas estructurales de corte grande donde dos robots colaboran, uno por borde de la tela, para recoger y crear la geometría objetivo del molde para asegurar que se ajusta sin arrugas antes de colocar.
- Alojamiento para telas pequeñas con formas de hasta 1,5 por 2,5 metros .
“Para los robots colaboradores, desarrollamos efectores finales que contienen seis módulos conectados por juntas esféricas”, explica Larsen. “Esto permite que el efector final se deforme, de manera similar a una serpiente, conforme a la geometría objetivo del molde. Los dispositivos de calentamiento integrados activan el aglutinante en la tela a medida que se transporta y se le da forma, manteniendo su forma y posición 3D una vez colocada ”.
Colocación y drapeado automatizados
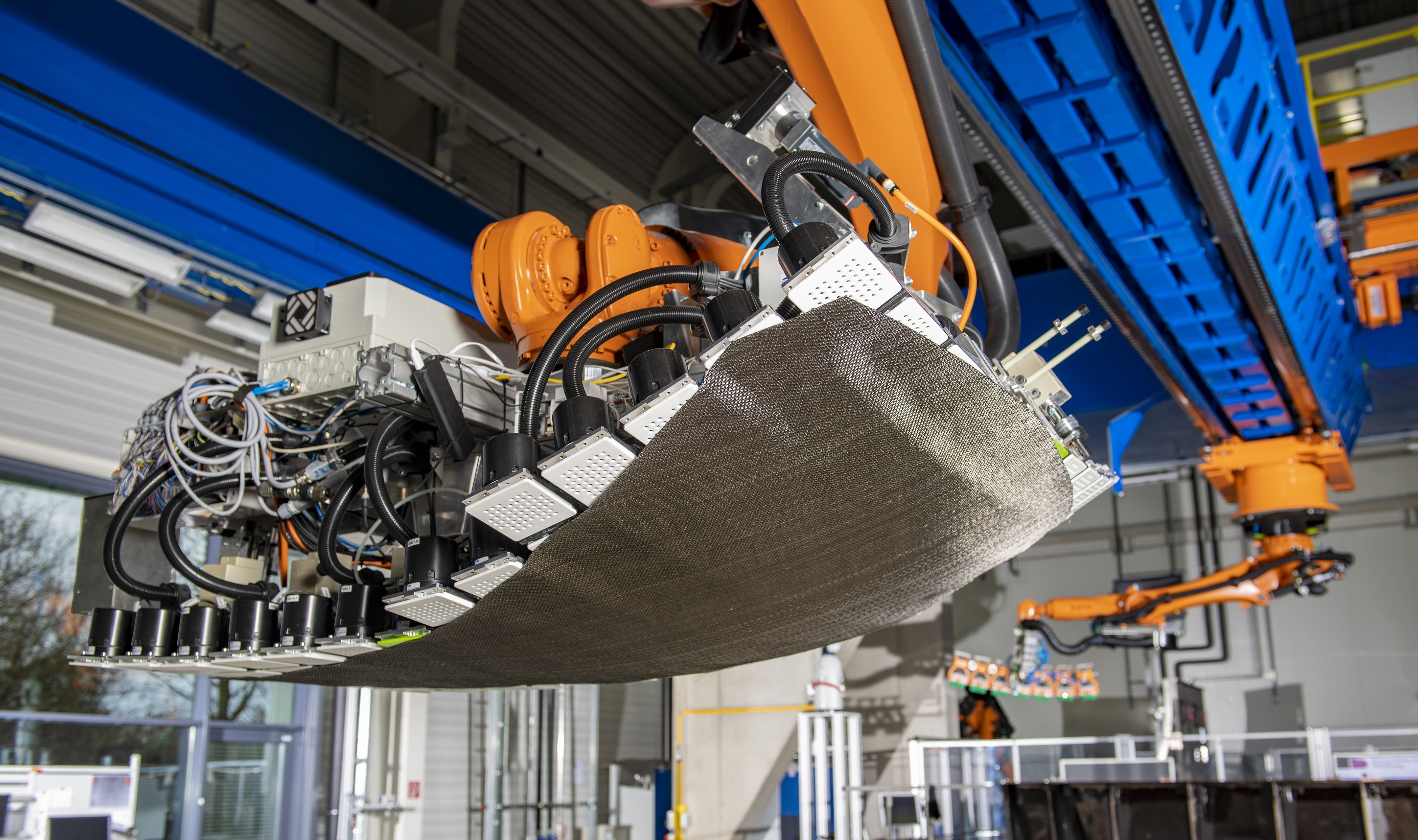
El efector final cuenta con una pinza que utiliza 127 módulos equipados con succión de vacío para recoger capas de tela cortadas, transformarlas en una forma 3D y luego calentarlas antes de colocarlas en el molde. Crédito de la foto:Instituto de Estructuras y Diseño del Centro Aeroespacial Alemán (DLR)
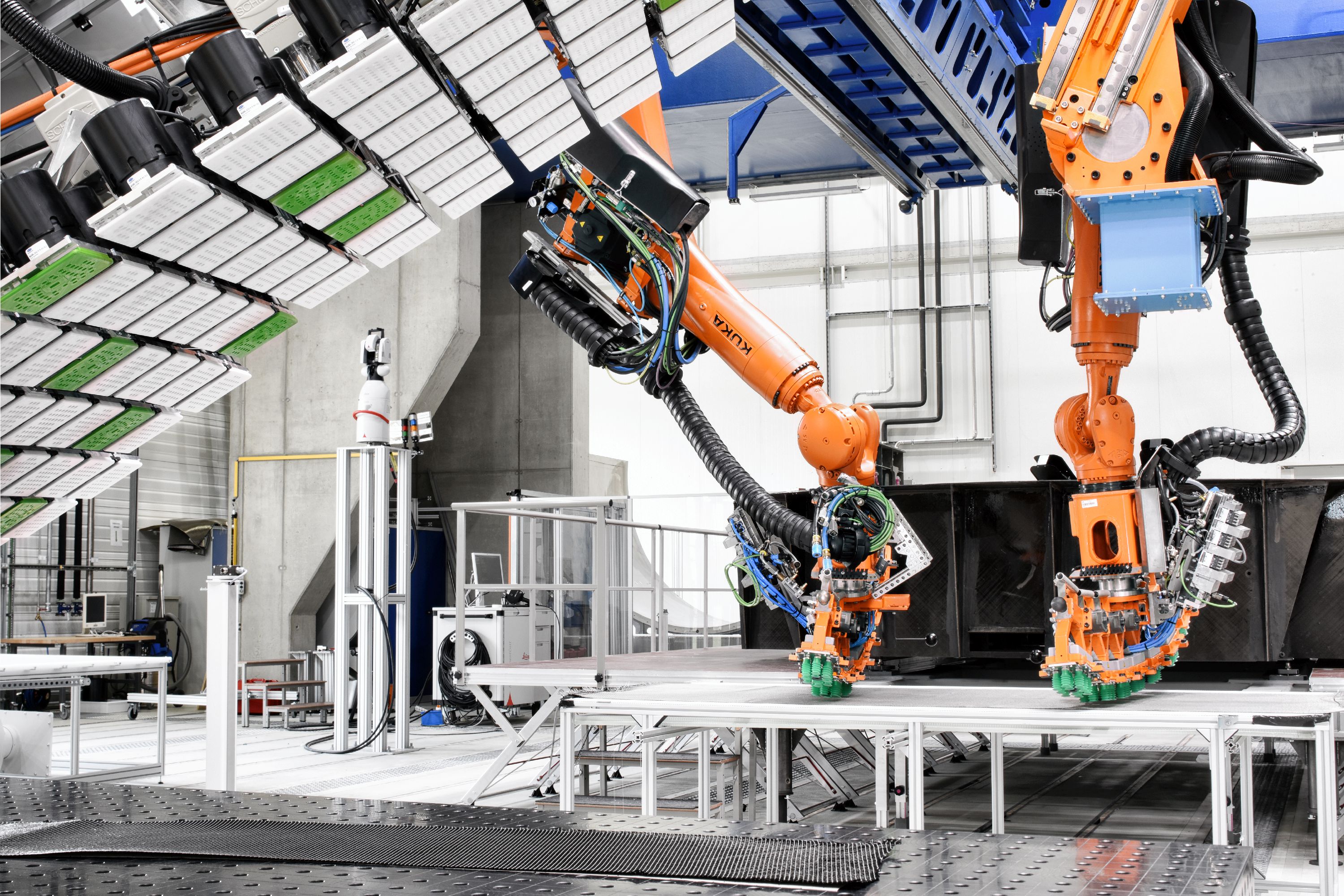
Aquí, se pueden ver tanto la pinza de 127 módulos (izquierda) como los robots colaboradores (fondo). Crédito de la foto:Instituto de Estructuras y Diseño del Centro Aeroespacial Alemán (DLR)
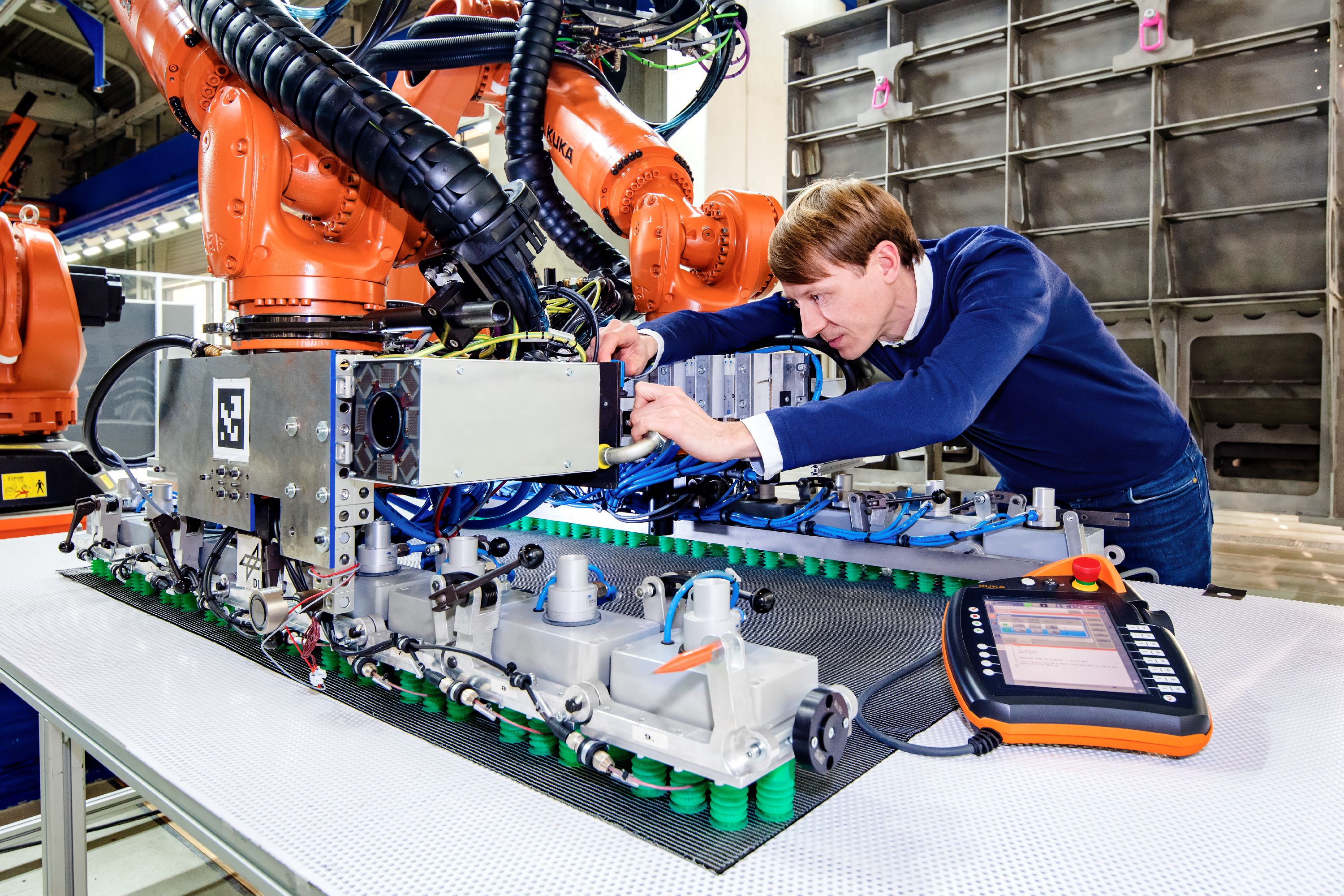
Para los robots colaboradores, se desarrollaron efectores finales que contienen seis módulos conectados por juntas esféricas. Crédito de la foto:Instituto de Estructuras y Diseño del Centro Aeroespacial Alemán (DLR)

Cada robot toma un borde de la gran capa de tela. Luego trabajan juntos mientras transportan la capa para crear la geometría objetivo requerida antes de colocar la tela en el molde. Crédito de la foto:Instituto de Estructuras y Diseño del Centro Aeroespacial Alemán (DLR)
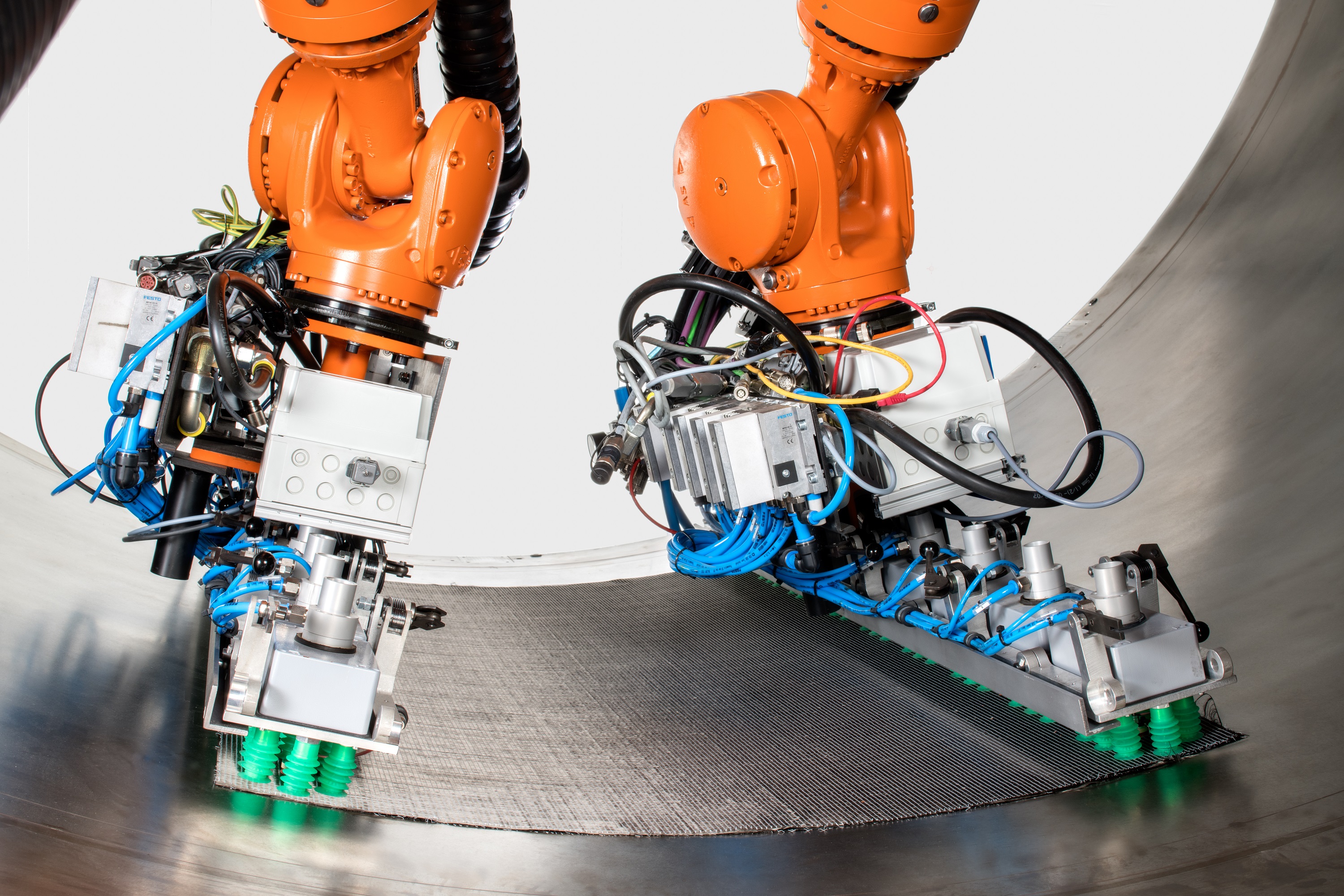
Crédito de la foto:Instituto de Estructuras y Diseño del Centro Aeroespacial Alemán (DLR)
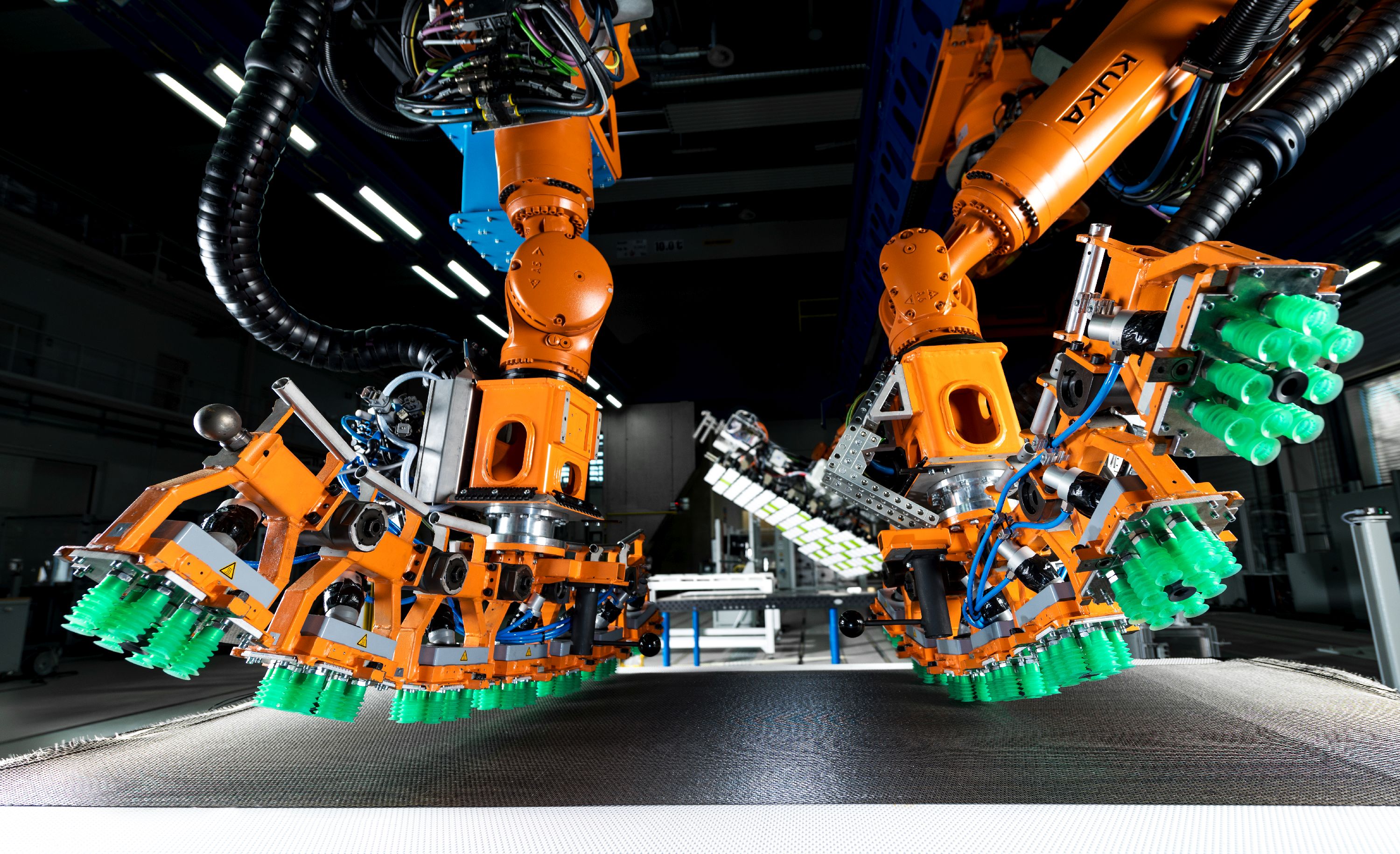
Primer plano de los efectores finales del robot colaborativo. Crédito de la foto:Instituto de Estructuras y Diseño del Centro Aeroespacial Alemán (DLR)
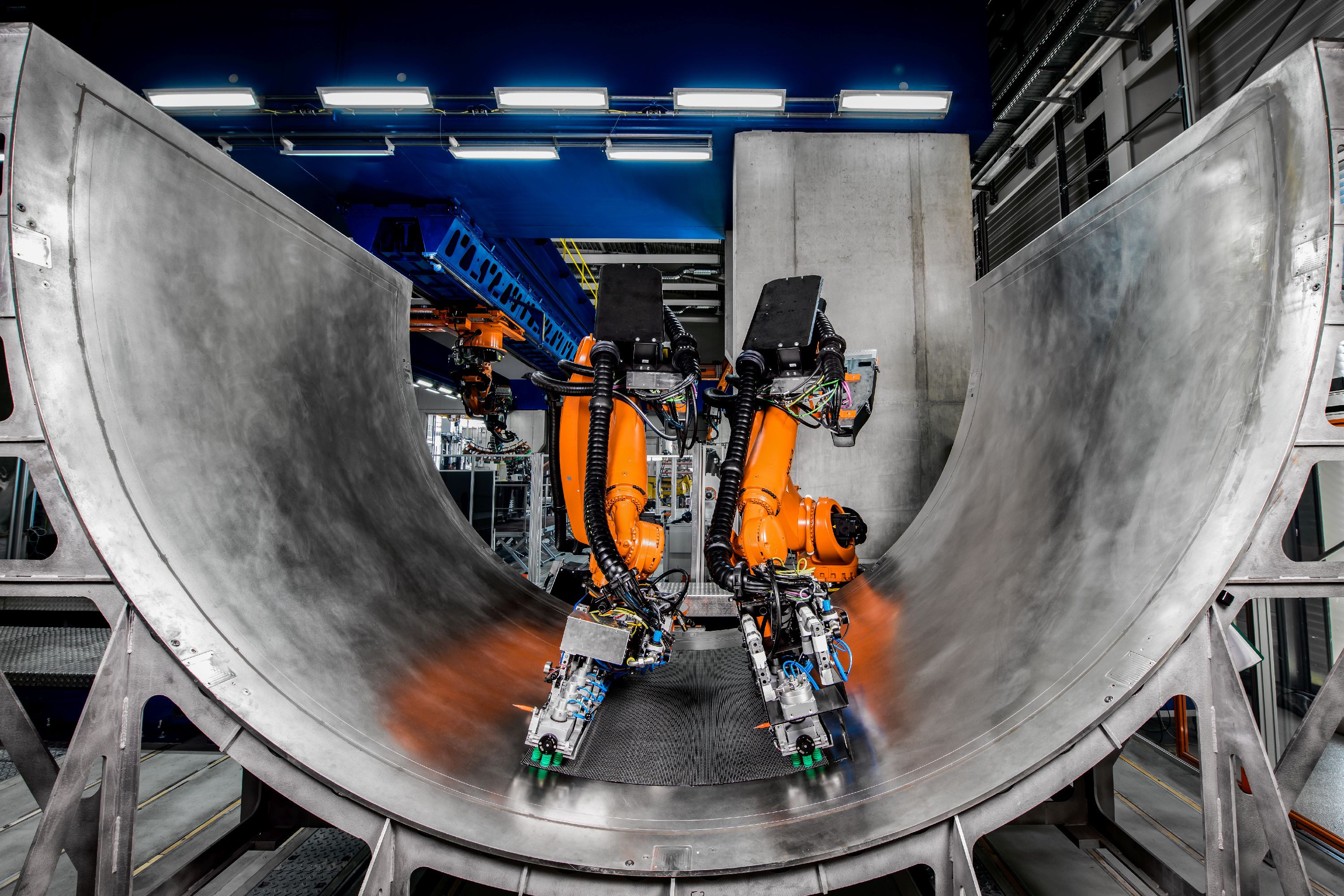
Este sistema que DLR desarrolló inicialmente para un mamparo de presión trasero A320 ahora también se ha demostrado para un panel de fuselaje y está diseñado para ser flexible para una variedad de grandes aeroestructuras, basado en sus archivos de diseño digital, sin volver a enseñar a los robots. Crédito de la foto:Instituto de Estructuras y Diseño del Centro Aeroespacial Alemán (DLR)
Anterior SiguientePara las capas pequeñas y perfiladas hasta 1,5 por 2,5 metros, se desarrolló un segundo tipo de pinza que utiliza 127 módulos equipados con succión de vacío para la recogida. “Esta pinza recoge material en un estado 2D y luego lo dobla a la geometría objetivo”, explica Malecha. “Debe decidir cuál de los 127 módulos mantendrá firme y cuál dejará deslizarse para transformar la capa 2D en una forma 3D. Entonces, es muy similar a cómo funcionan las manos para cubrir. Hicimos muchos experimentos y adquirimos experiencia sobre dónde retener y dónde soltar. La fuerza se puede ajustar según la intensidad con la que los módulos se agarren al material ”.
Inspección en línea. Los sensores ópticos en las pinzas modulares monitorearon el proceso de drapeado. Después de colocar una capa, un efector final que combina un Leica T-Scan (Hexagon Manufacturing, Cobham, Reino Unido) y un sistema de medición del ángulo de fibra basado en una cámara de Profactor (Steyr, Austria) inspecciona la calidad. “Primero medimos los ángulos de la fibra y los comparamos con el archivo CAD”, dice Malecha, “y luego medimos los bordes de cada pieza y verificamos su posición en comparación con el archivo CAD”.
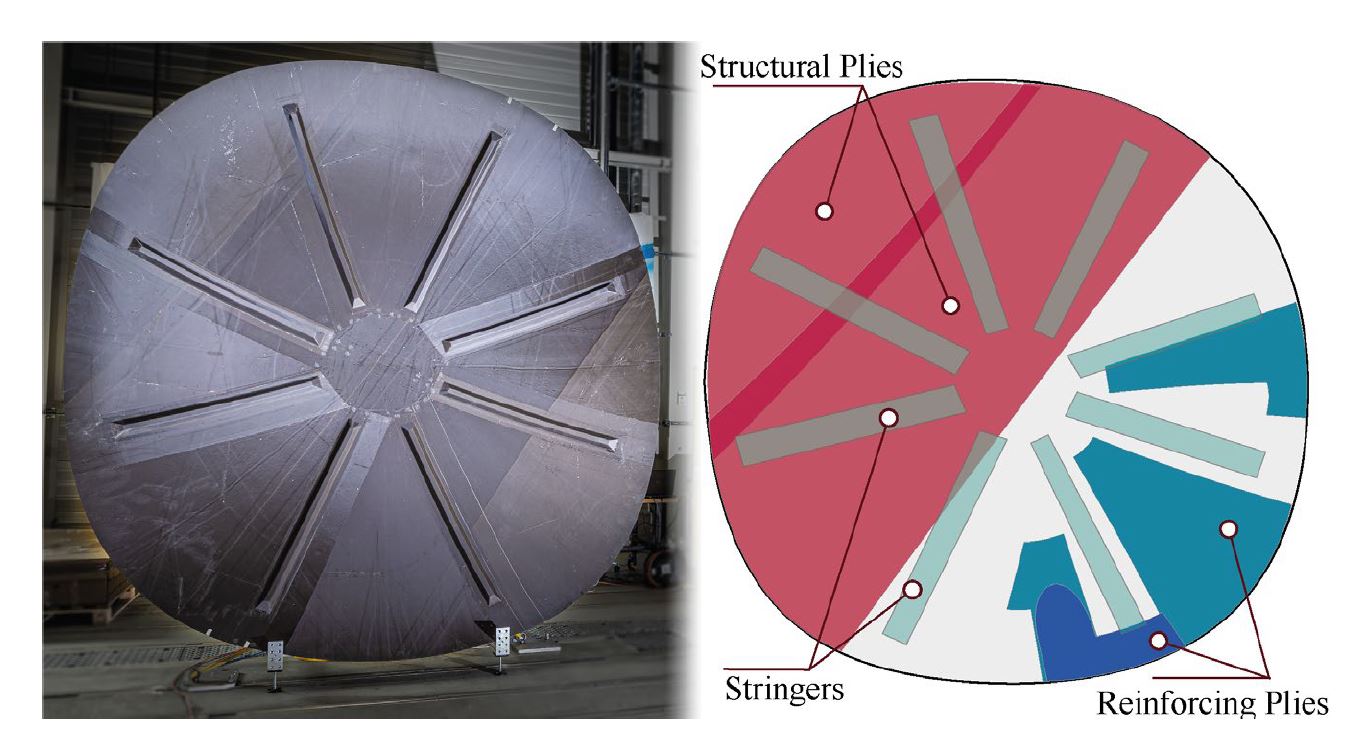
Largueros y envasado al vacío. Después de completar la preforma, se colocaron ocho refuerzos (larguerillos) en la parte superior. Para esta tarea, se desarrolló la pinza cinemática múltiple que también se utilizó para aplicar los materiales auxiliares de la bolsa de vacío. Esta pinza consta de tres robots pequeños e independientes de 6 grados de libertad (DOF) y un brazo rígido, todos montados en la brida central de un robot industrial de 6 grados de libertad. Los materiales auxiliares de embolsado al vacío (capa despegable, película de liberación perforada y medios de flujo de resina (materiales auxiliares del lado de la herramienta)) fueron precortados y preunidos, diseñados para el lugar donde se colocaron. "No tenían que cubrirse, simplemente colocarse", señala Malecha. La membrana semipermeable prefabricada se aplicó de forma semiautomática a través de un efector final con un mecanismo en forma de "paraguas", mientras que la colocación de la cinta adhesiva y la bolsa de vacío exterior siguió siendo manual, pero también podría automatizarse.
Duración y coste del ciclo. Para Malecha, el mayor desafío fue construir el sistema de ejecución de fabricación (MES) modular, basado en inteligencia artificial (AI) para monitorear y controlar la cadena de procesos. “Tuvimos que construir sistemas de gestión de datos que pudieran unir procesos bastante diferentes y luego comandarlos a través del MES a través de un puerto de intercambio de datos”, explica. "Podemos utilizarlos según se necesiten sobre la marcha, lo que permite una mayor flexibilidad y un uso más amplio en lugar de seguir un estricto orden de fabricación".
La tecnología PROTEC NSR se validó fabricando un demostrador de tamaño completo en enero de 2019 y logrando un nivel de madurez de TRL 5-6 a mediados de 2019. En comparación con el estado actual de la técnica en PAG, esta cadena de proceso automatizado reduce el tiempo de ciclo de la aplicación de tela enrollada en un 58% y la recogida y colocación de las capas cortadas en un 50%. Los costos de fabricación de estas operaciones se redujeron en un 11,5% y un 31%, respectivamente.
Termoplástico RPB
“Este proyecto se inició en 2018 con PAG y el Institut für Verbundwerkstoffe (IVW, Kaiserslautern, Alemania) para mostrar lo que es posible con los compuestos termoplásticos en piezas grandes y estructuras primarias”, explica el Dr. Stefan Jarka, director de proyecto de Fast Lane RPB y experto en tecnologías de soldadura en ZLP Augsburg. “Un RPB no es realmente primario, porque los requisitos mecánicos no son tan altos como un ala o un fuselaje, pero muestra lo que es posible para estructuras grandes, planas y ligeramente curvas. En solo cuatro meses, desarrollamos un demostrador A320 RPB como ejemplo de cómo convertir una estructura de aluminio existente en compuestos termoplásticos ”.
Este demostrador utilizó tejido de fibra de carbono (CF) Cetex / hoja orgánica de sulfuro de polifenileno (PPS) (Toray Advanced Composites, Nijverdal, Países Bajos) y soldadura por resistencia. Un elemento resistivo entre las dos superficies que se están soldando genera calor y permanece en la estructura soldada. GKN Fokker (Hoogeveen, Países Bajos) ha utilizado esta técnica durante décadas para producir puertas de tren de aterrizaje de aviones y bordes de ataque fijos. Para este A320 RPB, el equipo de ZLP utilizó un elemento resistivo CF en lugar de una malla convencional de acero inoxidable.
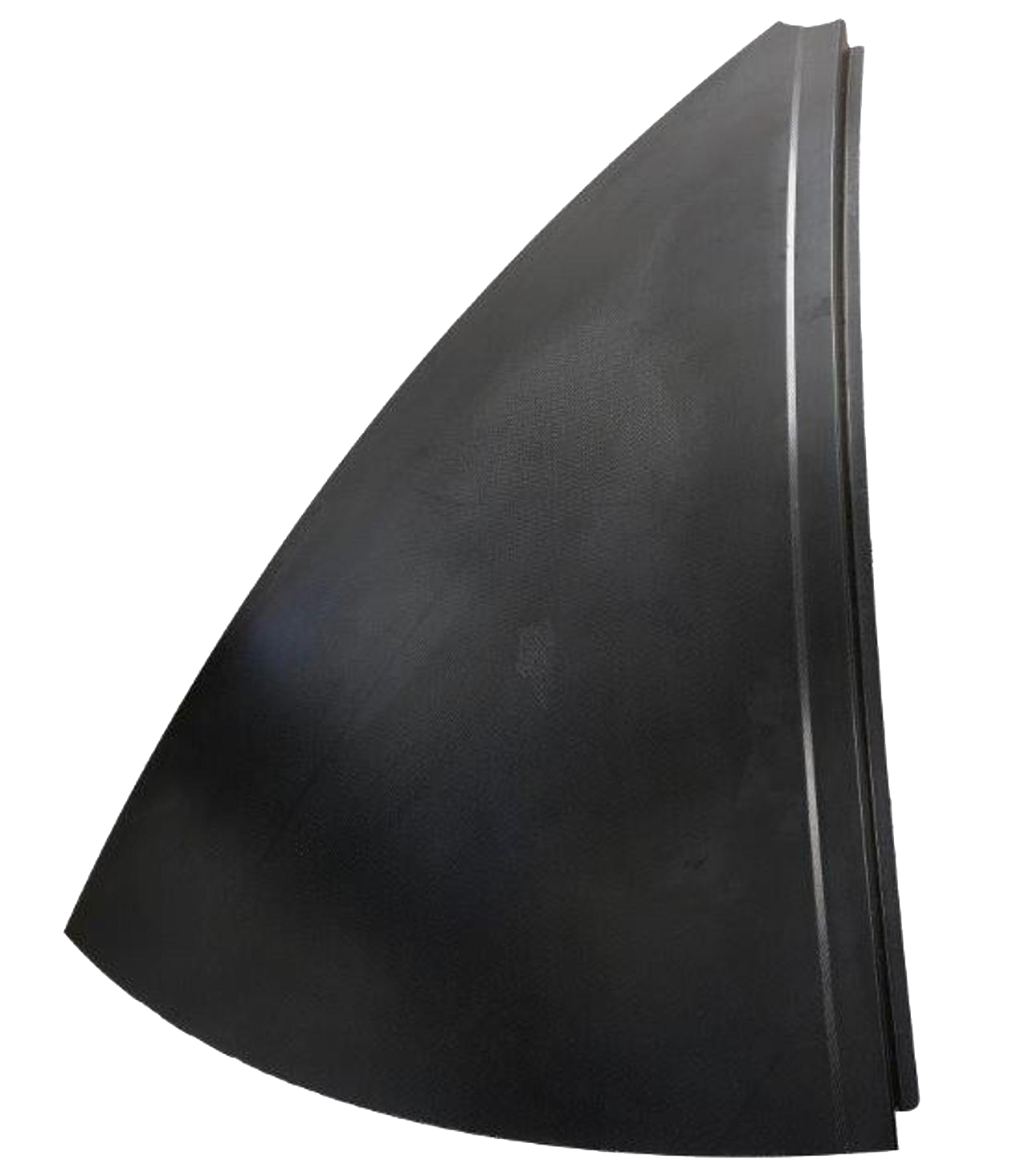
“El RPB compuesto termoplástico debía tener el mismo precio o ser más barato, pero el material es mucho más caro”, señala Larsen. Por lo tanto, el menor costo de producción debido a la automatización fue clave, al igual que el uso de ocho secciones idénticas de pétalos. “Estas secciones eran necesarias para formar la forma de doble curva de la pieza”, explica Jarka. “El termoformado como una sola pieza requeriría una prensa muy grande que sería demasiado cara. Por lo tanto, el IVW moldeó a presión ocho secciones más pequeñas utilizando herramientas de metal combinadas y las ensamblamos mediante soldadura automatizada. El nivel de automatización para el conformado por prensado de termoplásticos es más alto que para los compuestos termoendurecibles. En su mayoría, utiliza herramientas de metal combinadas, siendo la temperatura alta pero constante el problema principal, pero esto también hace que el ciclo de prensado automatizado sea muy rápido ”.
Los pasos generales del proceso para el demostrador RPB se muestran en la Fig. 2. “El proceso de soldadura que usamos no era nuevo”, dice Jarka, “pero tuvo que ser desarrollado más para unir los 1,5 metros de largo [y 40 milímetros- de ancho] para la pieza de 3 metros de diámetro e integran un sistema de control de calidad. Los componentes se fijaron primero en la posición correcta usando una plantilla de posicionamiento y luego se aplicó energía eléctrica para generar el plástico fundido en la zona de soldadura ”.
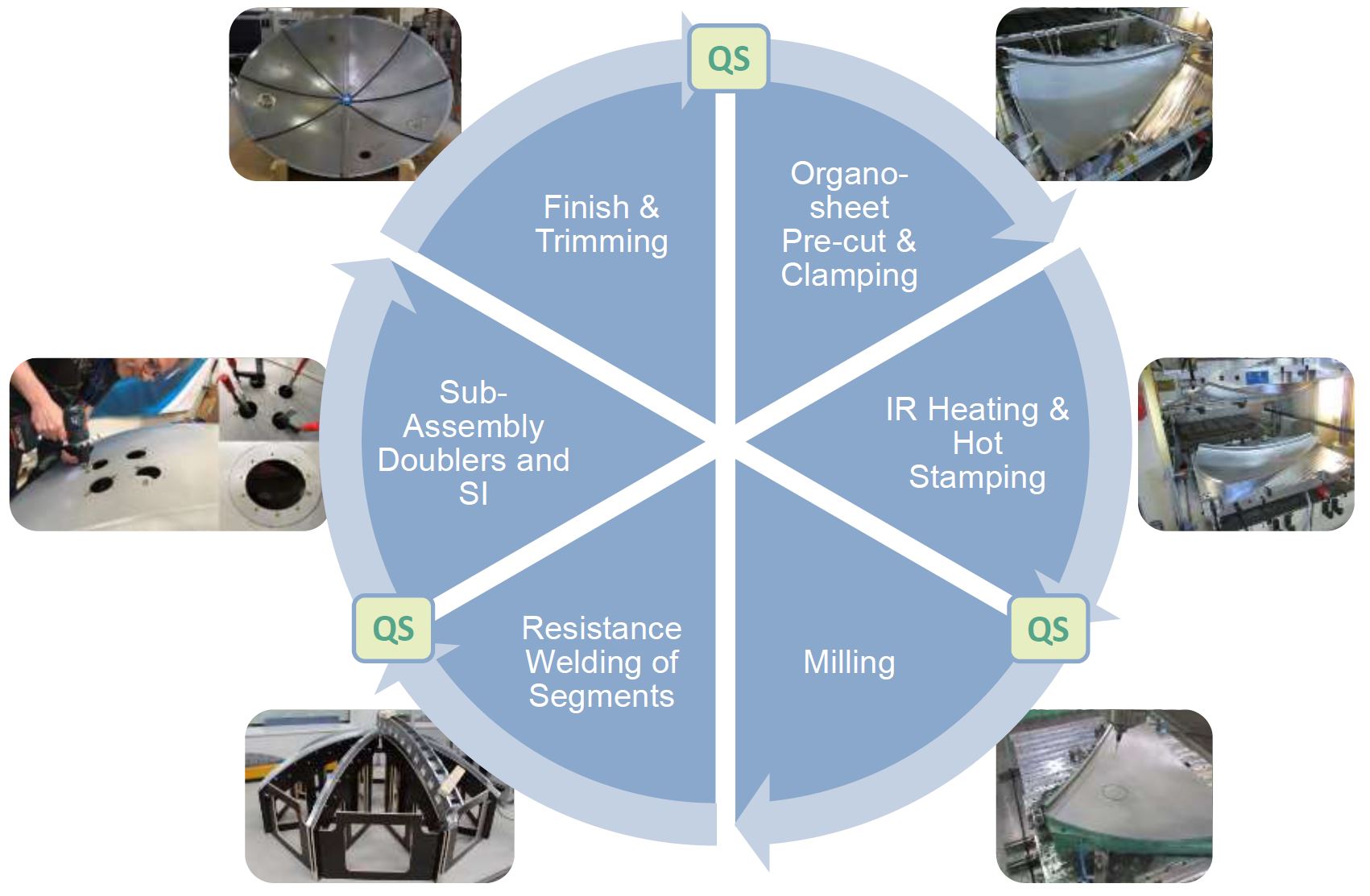
Fig. 2. Pasos del proceso de termoplástico RPB
Pasos del proceso utilizados para producir ocho secciones (parte inferior) de hoja orgánica CF / PPS estampada que luego se unieron mediante soldadura por resistencia para formar un mamparo de demostración A320. Crédito de la foto:Instituto de Estructuras y Diseño del Centro Aeroespacial Alemán (DLR)
Integración de control de calidad. "Probamos la termografía, tanto activada por lámpara de destello como por ultrasonidos, pero no es tan fácil medir la zona de soldadura con esto", explica Jarka. "La termografía es muy rápida, pero no le dice fácilmente si tiene una buena consolidación". En su lugar, utilizaron un banco de pruebas estándar para hacer múltiples muestras soldadas, midiendo corriente, voltaje y temperatura. “Luego los inspeccionamos con pruebas ultrasónicas (UT) e hicimos correlaciones entre los parámetros del proceso y una buena consolidación”, dice Larsen. “Si tenemos buenos parámetros, entonces tenemos una buena parte. También hemos construido una simulación de proceso para comparar los datos que obtenemos durante la soldadura con la línea de base inicial que establecimos ”.
Automatización y tiempo de ciclo. “Todo el proceso fue muy rápido, en la escala de las piezas de automóviles”, dice Jarka. "Logramos TRL 3 en nuestra revisión de 2019 y desde entonces hemos madurado a TRL 4. Alcanzaremos TRL 6 para fines de 2021". Antes de la pandemia, PAG había indicado que pondría en producción el RPB termoplástico para 2021. Aunque el futuro ahora es menos claro, todavía se considera que el RPB termoplástico permite el "fuselaje del mañana", reduciendo el peso de 41 a 35 kilogramos, proceso y el tiempo de montaje en un 75% y el costo total de la pieza en más del 10%.
Comparación de compuestos TS y TP
“Los procesos termoplásticos son tan rápidos que puede resultar más económico en comparación con el aluminio e incluso alcanzar una tasa de producción de 100 aviones por mes”, dice Jarka. “El RPB es una buena aplicación para la soldadura de termoplásticos pero también para la automatización”, dice Malecha. "El RPB de fibra seca moldeado por líquido es más caro de automatizar".
“Pero esa automatización es interesante porque podría lograr ganancias reales automatizando solo algunos de los subprocesos”, dice Larsen. "Por ejemplo, con la automatización de los auxiliares, podríamos completar el envasado al vacío en aproximadamente una hora, aproximadamente 10 veces más rápido que el proceso manual". Sin embargo, admite que el costo es un obstáculo importante para implementar dicha mejora. “El costo de las herramientas digitales, los robots y el desarrollo es demasiado para una sola pieza, como el RPB. Pero si pudiéramos desarrollar un enfoque modular en el que pudiera utilizar este sistema para muchas piezas, entonces este costo podría extenderse más, haciéndolo asequible cuando se calcula con la reducción del tiempo y la mano de obra ". De hecho, ZLP lo ha logrado, como se explica en CW Artículo de julio de 2020:"Composites 4.0:transformación digital, producción adaptativa, nuevos paradigmas".
“Todavía no hay muchas comparaciones entre las estructuras de compuestos termoendurecibles y termoplásticos”, dice Malecha. "Pero estamos comenzando a comparar procesos termoendurecibles y termoplásticos". Señala que el próximo objetivo es mostrar que las líneas de soldadura termoplásticas tienen las propiedades requeridas para las alas y los fuselajes de los aviones. Y ese rendimiento también debe demostrarse para las alas moldeadas por líquido integradas grandes, por ejemplo. Esto es exactamente lo que los programas MFFD y WOT se han propuesto lograr. Y esperamos sus resultados, así como los de muchos otros proyectos Clean Sky 2 y EC, para mostrar los próximos pasos a seguir.
Resina
- Blog:Moldeo por inyección de caucho de silicona líquida
- Tecnología de producción de paneles de nido de abeja termoplásticos EconCore
- Karl Mayer lanza la línea de producción de cintas termoplásticas UD
- INEOS Styrolution para construir un sitio de producción para el compuesto termoplástico StyLight
- La tecnología de producción Herone gana el premio a la innovación JEC
- Termoendurecibles termoplásticos sobremoldeados, ciclo de 2 minutos, una celda
- LANXESS amplía la capacidad de producción de compuestos termoplásticos continuos reforzados con fibra
- Airtech lanza materiales de envasado al vacío de alta temperatura para moldeo termoplástico
- Proceso Finex para la Producción de Hierro Líquido
- Producción automatizada de acoplamientos para perforadoras de petróleo
- Automatizado desde el principio