La estructura compuesta termoplástica reemplaza los metales en los pedales de freno críticos para la seguridad
La industria automotriz convirtió los pedales de acelerador de metales a termoplásticos de vidrio corto moldeados por inyección en la década de 1990. Sin embargo, los pedales de freno, que son componentes críticos para la seguridad con exigentes requisitos de rigidez, resistencia y carga de torsión, tardaron mucho más en convertirse. El proveedor automotriz de nivel 1, Boge Rubber &Plastics Group (Damme, Alemania), dice que es el primer proveedor que cumple con los exigentes objetivos de rendimiento y costo de los fabricantes de equipos originales para los pedales de freno en compuestos termoplásticos. El diseño único, tres materiales diferentes y un proceso de producción a medida permiten a la empresa producir pedales que son más fuertes, más rígidos, de menor peso y menor costo.
Encontrar un nicho que cuente
Boge es un desarrollador y productor de productos para amortiguación de vibraciones y montaje de tren motriz / chasis, así como módulos de plástico livianos y cajas de pedales (incluidas combinaciones de pedales de freno, embrague y acelerador) para la industria automotriz. Ha producido componentes automotrices en láminas orgánicas de fibra continua con compuestos de sobremoldeo de vidrio corto desde 2008. Agregó cintas termoplásticas unidireccionales (UD) a la mezcla en 2018. A través de la innovación continua del proceso, se redujeron el tiempo de ciclo y los costos y se incrementó el negocio.
“En 2015, mi jefe se acercó a mí y me dijo:'Estos cambios que has hecho son agradables, Daniel, pero sería bueno si pudieras encontrar un mercado más grande con volúmenes de producción que realmente cuenten'”, recuerda Dr.-Ing. . Daniel Häffelin, gerente senior / jefe del equipo de peso ligero en el Boge Global Innovation Center. Un equipo de ingenieros de Boge aceptó el desafío e hizo una lluvia de ideas sobre cómo aumentar la eficiencia de la fibra para reducir costos y obtener más negocios.
“Organosheet es un gran producto, pero hay que usarlo de la manera correcta, solo donde sea necesario”, explica Häffelin. “Ya habíamos simplificado mucho nuestro proceso de producción, por lo que no ganaríamos mucho si intentamos reducir aún más los tiempos de ciclo. Razonamos que la mejor manera de reducir los costos era reducir la cantidad de fibra sin fin que usamos al usar esa fibra de manera más eficiente ”.
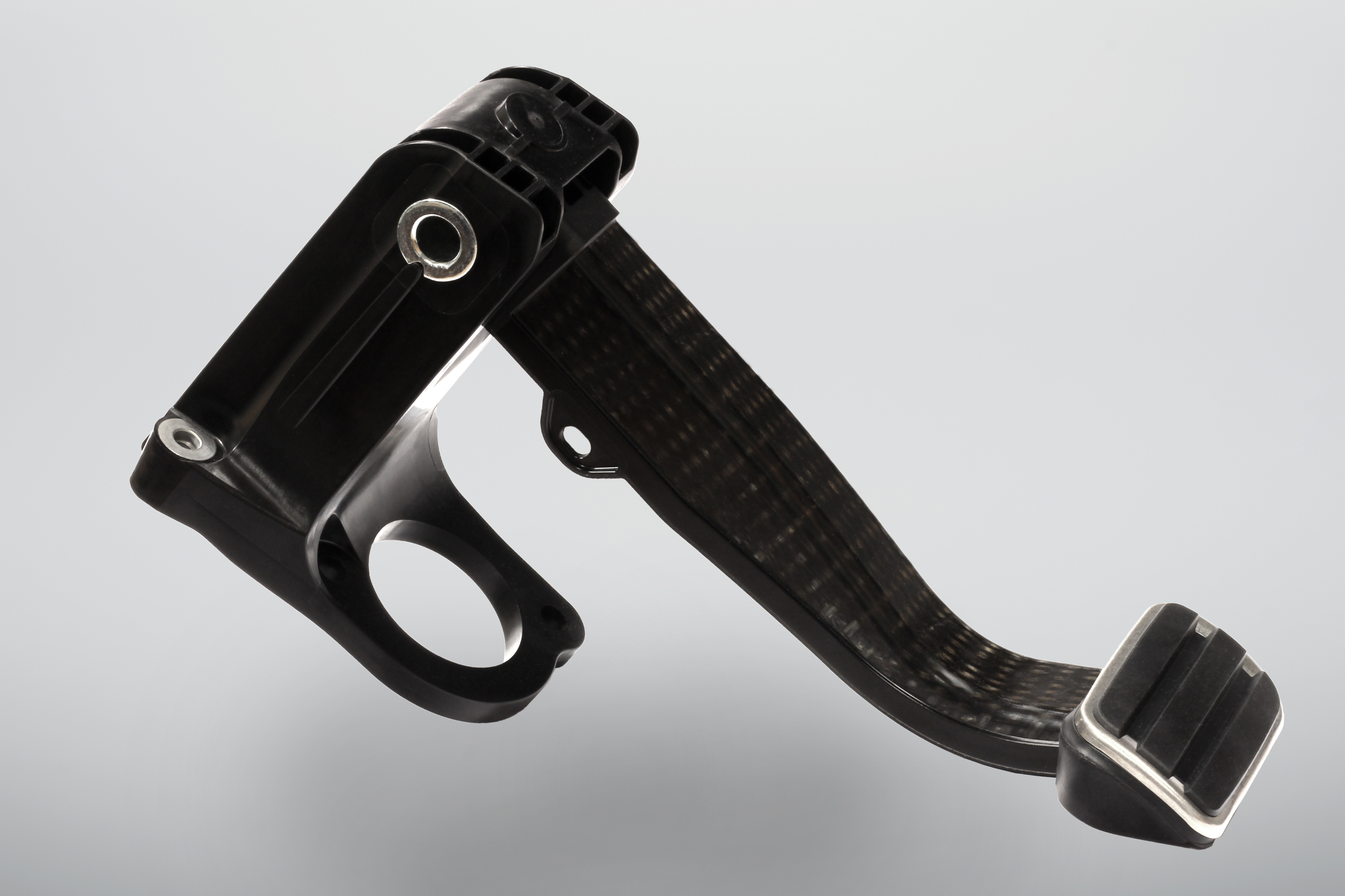
Simplemente hacer pedales más pequeños o más delgados tampoco funcionaría porque existen limitaciones prácticas en el tamaño y la forma del pedal de freno, sin mencionar las desafiantes especificaciones de rendimiento debido a su naturaleza crítica para la seguridad. Lo que tenía más sentido era encontrar formas de controlar mejor la orientación de la fibra para optimizar las propiedades locales en las áreas de la pieza que experimentaron los picos de carga más altos, brindando oportunidades para reducir el grosor de la pared en áreas menos críticas.
"Buscamos una manera de 'dirigir' las fibras localmente para poder colocarlas justo donde las necesitábamos para mantener la rigidez y la resistencia", agrega el Dr. Torsten Bremer, director ejecutivo de Boge Rubber &Plastics Group. “Sabíamos, en principio, que esto era posible porque ya habíamos considerado las máquinas de recoger y colocar utilizadas en artículos deportivos y médicos, pero eran demasiado caras. Fue entonces cuando decidimos que necesitábamos un nuevo proceso ".
“Ya estábamos trabajando con un OEM alemán para encontrar formas de fabricar pedales de freno totalmente compuestos que cumplieran con sus requisitos de rendimiento y costo”, recuerda Burkhard Tiemann, vicepresidente ejecutivo de Boge Plastics &Rubber Group, líder de la línea de productos:Plásticos. “Le dijimos a nuestro cliente:'Desarrollaremos un nuevo proceso utilizando cintas UD y láminas orgánicas'. Nos dijeron:'Si puede reducir aún más la masa y el costo, lo haremos'. Ese fue nuestro punto de partida. Hicimos una gran promesa en 2015 de que podríamos entregar un pedal de freno totalmente compuesto que fuera más barato, más liviano y que se pudiera producir en grandes cantidades. Tomó tres años trabajar en los detalles y entregar nuestros primeros productos ".
Dirección de fibra
Los pedales de freno compuestos deben cumplir las mismas especificaciones de rendimiento que los pedales de acero o aluminio existentes. Eso incluye requisitos especiales de modo de falla con cargas de hasta 3000 newtons y deflexión similar al acero a carga máxima. Dados estos requisitos y el espacio restringido del paquete disponible, la estructura de la carcasa principal del pedal, que soporta las cargas máximas, requiere un refuerzo continuo de fibra. Por lo tanto, el equipo decidió utilizar organosheet para formar la columna vertebral del pedal. Luego, las cintas UD se usarían para aumentar localmente la rigidez / resistencia y reforzar las paredes interiores durante las tensiones máximas en el área de la pieza que posteriormente se doblaría en un canal en U durante el preformado. Y en áreas donde se necesitaba geometría funcional como nervaduras, se especificó compuesto de sobremoldeo de vidrio picado. El equipo consideró que este enfoque híbrido aumentaría la eficiencia de la fibra al tiempo que reduciría el uso de material, el grosor medio de la pared y el tiempo de ciclo.

El equipo comenzó un trabajo de simulación intensivo para optimizar la ubicación de las fibras durante la producción. La base del trabajo de Boge se basó en un programa de investigación alemán financiado con fondos públicos de 2011-2014 llamado SoWeMa (Software, herramientas y desarrollo de máquinas para una cadena de fabricación ligera completamente automática y cerrada).
“La investigación de SoWeMa cubrió muchas de las preguntas que haríamos un año después para nuestra propia empresa”, explica Häffelin. "Debido a que el diseño es parte del conocimiento básico de Boge, comenzamos con los fundamentos del programa SoWeMa y construimos nuestras propias capacidades de simulación de elementos finitos (FE) para estructuras de capas anisotrópicas".
Un área de enfoque fue la optimización de topología combinada para la disposición de la cinta y la estructura de la nervadura. “Creamos un ciclo de iteración para optimizar la colocación de las cintas y adaptar la estructura de las nervaduras en consecuencia, ya que ambas están vinculadas entre sí sobre la rigidez y la resistencia de la pieza”, continúa K. Siebe, ingeniero de FEA, Centro de Innovación CRRC. “Dado que la combinación de materiales de cintas UD, láminas orgánicas y materiales de fibra corta es única y su aplicación está vinculada a una ventana específica de humedad y temperatura, construimos nuestras propias tarjetas de materiales para caracterizar con mayor precisión cómo se comportarían estos materiales durante las pruebas físicas. ”
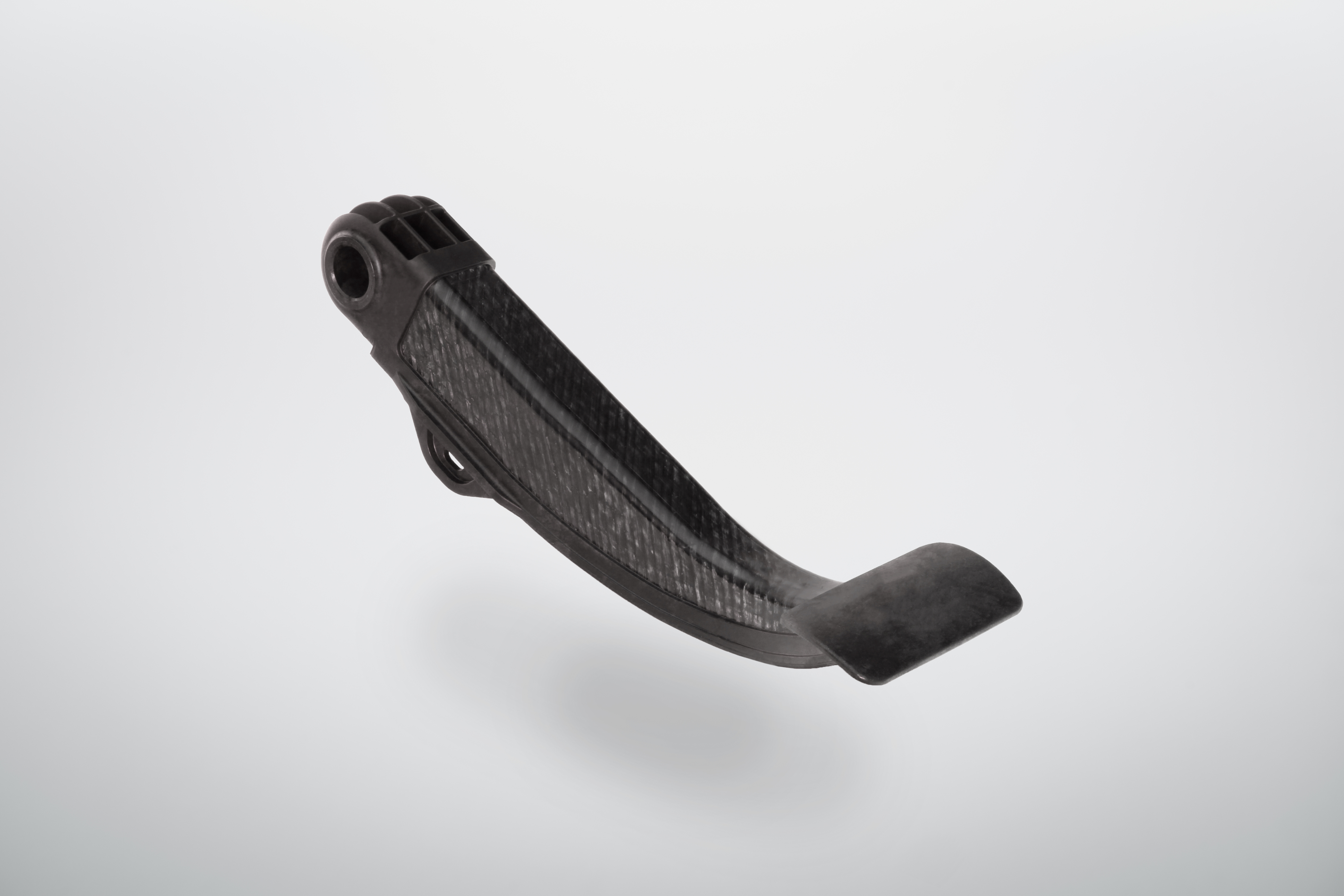
Boge especificó la estructura de capas y la arquitectura de fibra para cada material en función de los resultados de la simulación y un diseño de pedal determinado. Lanxess Deutschland GmbH (Colonia, Alemania) suministra hojas orgánicas en fracciones de volumen de fibra (FVF) del 45-50%. Celanese Corp. (Irving, Texas, EE. UU.) Suministró cintas termoplásticas UD con FVF del 55-60%. Los compuestos de inyección de vidrio corto para esta aplicación, al 40-60% de fracción de peso de fibra (FWF), fueron suministrados por múltiples fuentes. Todos los materiales son negros y cuentan con una matriz de poliamida 6 o 6/6 (PA6, PA6 / 6). Para cumplir con las especificaciones del cliente, PA6 es la resina predeterminada para los tres tipos de compuestos. Sin embargo, dependiendo de los niveles de humedad y temperatura durante la fabricación, así como de las limitaciones de espacio y la geometría del pedal, Boge también puede usar PA6 / 6 para la resina de sobremoldeo, ya que los dos polímeros son lo suficientemente similares para unirse bien.
Producción en tres pasos
Paralelamente al diseño, el equipo trabajó en un proceso de producción de tres pasos. En el primer paso, se crea un blanco de fibra a medida utilizando una hoja orgánica precortada y preconsolidada como una base estable sobre la cual colocar estratégicamente tiras de cinta UD alineadas con las rutas de carga para reforzar la estructura de la carcasa de la pieza. En el segundo paso, la pieza en bruto se mueve y se calienta secuencialmente, se consolida y se le da forma / drapeado. En el tercer paso, se sobremoldea con compuesto de vidrio corto para crear la estructura estriada.
Para lograr tiempos de ciclo rápidos, la manipulación robótica era un hecho para este sistema. Una característica clave del proceso que el equipo quería incluir era la flexibilidad para colocar cintas de cualquier longitud, en cualquier orientación y en cualquier posición en un lado de la cubierta de la hoja orgánica y pegar con láser esas cintas a la cubierta para que no se desplazaran. en los pasos siguientes.
Otra decisión que tomó el equipo fue no preconsolidar la pieza en blanco a medida inmediatamente después de la colocación, sino justo antes del drapeado / preformado y sobremoldeado. El equipo razonó que el material tendría que recalentarse durante el drapeado / preformado de todos modos y, para ser rentable, tenían que mantener el tiempo total del ciclo cerca de 1 minuto. Por lo tanto, Boge calienta y consolida la pieza en bruto justo antes del drapeado / preformado utilizando un rápido aumento de temperatura combinado con alta presión para crear una fuerte unión mecánica entre la cinta y la hoja orgánica. El calentamiento se detiene y la temperatura de la pieza comienza a descender a medida que la pieza en bruto consolidada aún caliente se mueve hacia la cavidad del drapeado antes de volver a moverse y sobremoldearse con nervaduras y otras características funcionales en una segunda cavidad. Se logran fuertes uniones mecánicas, con penetración de cadena de polímero verificada, entre los tres materiales. No se requiere acabado posterior al molde.
Para cumplir con los requisitos de calidad para estas piezas críticas para la seguridad, el equipo también desarrolló un sistema rápido, preciso y compatible con la Industria 4.0 que utiliza sensores de visión, fuerza, tiempo, presión y temperatura que verifican el material en cada paso del proceso de fabricación. Luego, el sistema almacena esos datos y los vincula al número de identificación único de cada pedal. Esto asegura una trazabilidad del 100% de todos los materiales, turnos y configuraciones del proceso involucradas.
Logros hasta la fecha
El proceso a medida, totalmente automatizado y con control de calidad de Boge dio el paso del prototipo a la producción en serie de gran volumen en 2018. Al producir un pedal nuevo aproximadamente cada minuto, la célula de fabricación actual puede fabricar hasta 1 millón de piezas por año. Los pedales totalmente compuestos utilizan un 33% menos de lámina orgánica que los diseños anteriores y el grosor nominal de la pared se redujo de 3 a 2 milímetros. Los pedales también son un 50-55% más ligeros, pero cumplen o superan los requisitos de resistencia del acero. Los pedales más ligeros mejoran la háptica de conducción para los consumidores y todo el sistema es 100% reciclable al final de su vida útil. Con el proceso actual, los pedales compuestos tienen un costo equivalente al del aluminio y un costo ligeramente más alto que el del acero. Se están desarrollando otras buenas aplicaciones de automoción y deportivas.
¿Qué nos depara el futuro a medida que los fabricantes de automóviles transfieran recursos a la electrificación de flotas? “A medida que los sistemas de accionamiento por cable [sistemas de actuación electromecánica] y la electrificación del tren de potencia se vuelvan más comunes, los pedales del acelerador podrían desaparecer, pero los pedales de freno permanecerán”, reflexiona Häffelin. “Sin embargo, es probable que veamos una mayor integración de la electrónica, incluidos los sensores, en los pedales de freno. Eso aumentará sustancialmente la complejidad de las piezas, lo que hará que los compuestos sean incluso más competitivo que los metales ".
El uso del material, los pasos del proceso y los criterios del equipo se explican con más detalle en CW El artículo de seguimiento de enero de 2021, "El proceso a medida produce un pedal de freno compuesto cada minuto".
Resina
- Compuesto de nailon reforzado con fibra larga reemplaza la carcasa del motor de aluminio
- Compuesto termoplástico reforzado con fibra continua fabricado íntegramente a partir de recursos naturales
- Solvay expande la capacidad de compuestos termoplásticos
- Oribi Composites, socio de Packard Performance para ruedas de material compuesto termoplástico para deportes motorizados todoterreno
- Fraunhofer encarga células de producción automatizadas de Engel para I + D de compuestos termoplásticos
- El consorcio busca soluciones para estructuras compuestas termoplásticas de fibra de carbono
- INEOS Styrolution para construir un sitio de producción para el compuesto termoplástico StyLight
- Xenia presenta los compuestos termoplásticos CF / PP
- Tubo compuesto termoplástico en ascenso en las profundidades del mar
- Compuesto termoplástico TenCate calificado para NIARs NCAMP
- TenCate celebra la asamblea del consorcio de compuestos termoplásticos en Brasil