Cintas termoplásticas reforzadas con fibra de carbono PAN de base textil
Un desafío de larga data en la industria de compuestos avanzados es encontrar formas de producir fibra de carbono de menor costo para que todas las industrias que quieran utilizar este valioso y efectivo refuerzo de compuestos puedan hacerlo. Los costos de la fibra de carbono se han reducido considerablemente gracias a décadas de trabajo para mejorar la productividad a través de la química precursora, la innovación de maquinaria, mejoras de procesos y más.
Un área que se ha mostrado muy prometedora es el uso de precursores alternativos al poliacrilonitrilo (PAN) de calidad aeroespacial convencional. Por ejemplo, el Departamento de Energía de EE. UU. (DOE, Washington, DC, EE. UU.) Y el Laboratorio Nacional de Oak Ridge (ORNL, Oak Ridge, Tennessee, EE. UU.) Han desarrollado métodos para producir fibra de carbono a partir de precursores alternativos que van desde polímeros hasta lignina. , al carbón.
Precursores alternativos
Uno de los más prometedores de estos precursores, y el más cercano a la comercialización, es el PAN de base textil, que es similar a la fibra que se usa para producir suéteres acrílicos. Al igual que otros precursores alternativos que ha investigado ORNL, la fibra de carbono PAN (TCF) de base textil es diferente de la fibra de carbono PAN aeroespacial especializada en varios aspectos.
Una de las diferencias es que el precursor de PAN a base de textiles, debido a que está diseñado para su uso en la industria textil (piense en cortinas, ropa, telas para muebles), se suministra en un formato de remolque ancho que es inherentemente menos costoso que el de grado aeroespacial especializado. Precursor de PAN. Durante la producción de fibra de carbono, esto tiene el efecto de aumentar el rendimiento y reducir los costos de conversión en comparación con la fibra PAN convencional. También tiende a producir fibra de remolque mucho más grande, del orden de 300K a 450K en la línea en la Planta de Tecnología de Fibra de Carbono de ORNL versus 3K a 50K típicos de la fibra de carbono PAN convencional. Además, si bien se tarda más en procesar el precursor de TCF, ya que no contiene aceleradores de reacción como el PAN convencional y normalmente se ejecuta a temperaturas más bajas (en función de la necesidad de equilibrar el tiempo de residencia y la temperatura), el hecho de que mucha más fibra se puede procesar en un momento dado y que el uso de energía sea menor en base al peso o al volumen ayuda a reducir los costos. De hecho, ORNL estima que es posible un ahorro total de energía de aproximadamente un 60% para la conversión de fibra y un ahorro de costos de aproximadamente un 50%.
Esto, a su vez, brinda la oportunidad de producir fibra menos costosa en cantidades inusualmente grandes y de usarla para fabricar productos con una huella de carbono menor. En industrias como la automoción / transporte terrestre, electrónica de consumo, artículos deportivos, edificios / construcción y energía eólica, el TCF es un refuerzo atractivo ya que las aplicaciones tienden a basarse en la rigidez, en comparación con las aplicaciones en la industria aeroespacial impulsadas por la fuerza. En particular, las industrias no aeroespaciales podrían consumir mucha fibra.
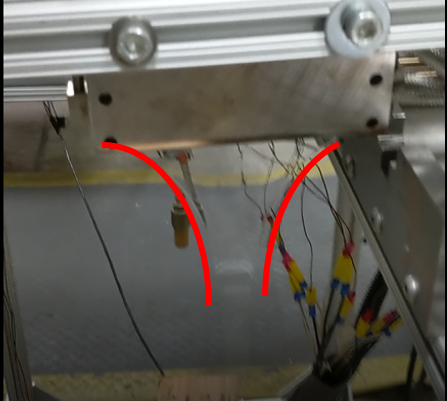
Sin embargo, TCF sigue siendo un producto diferente a la fibra de carbono PAN convencional, por lo que es necesario trabajar no solo para caracterizar mejor esta fibra, sino también para encontrar formas de convertirla y usarla. Debido a que puede procesarse en una banda de remolque ultraancha, este precursor requiere modificaciones del equipo de proceso durante todo el proceso de producción de fibra. También cambia la modificación de la superficie de posproducción y el empaque y, por supuesto, afectará los procesos de conversión que van desde la fabricación de cintas y telas hasta preimpregnados y preformas.
Reconociendo todas las formas en que TCF puede resolver el problema de costo / disponibilidad de la fibra de carbono por un lado, pero también crea nuevos problemas en cómo manejar, convertir y empaquetar este material por el otro, el Instituto de Innovación en Fabricación de Compuestos Avanzados (IACMI, Knoxville , Tennessee, EE. UU.) Ha estado trabajando en varios proyectos de investigación apoyados por miembros durante los últimos tres años para abordar estos problemas. Un proyecto interesante ha buscado formas de convertir la banda de remolque TCF ultraancha en cintas compuestas termoplásticas.
Reducción de costos
El interés en las cintas compuestas termoplásticas ha aumentado en muchas industrias, pero estos productos tienden a ser costosos, ya que se requieren equipos especializados y conocimientos para impregnar con éxito cualquier fibra con resinas termoplásticas prepolimerizadas, de alto peso molecular y alta viscosidad frente a sus homólogos termoendurecibles de baja viscosidad sin reaccionar. Es muy fácil producir cintas con muchos huecos y poca humedad de la fibra, terminando con partes finales que no solo se ven horribles, sino que corren el riesgo de fallas prematuras.
El Dr. Uday Vaidya, profesor y presidente del gobernador de Advanced Composites Manufacturing, University of Tennessee-Knoxville (UTK, Knoxville, Tennessee, EE. UU.) Y director de tecnología de IACMI (CTO), ha colaborado en programas de compuestos termoplásticos desde principios de la década de 2000 con George. Husman, presidente de Husman Consulting Inc. (Cape Coral, Florida, EE. UU.) Y director jubilado y director de tecnología de Zoltek Co. Inc. (St. Louis, Missouri, EE. UU.). Sus muchas interacciones llevaron a la idea de la impregnación en línea de fibras de carbono de arrastre pesado convencionales (24K a 50K) para producir cintas compuestas termoplásticas en el extremo posterior de la línea de producción de fibras. La producción de cintas inmediatamente después de la producción de fibra eliminaría un paso de proceso intermedio separado y todo el envío y manipulación que ello implica. Se espera que esto ayude a reducir los costos tanto de las cintas como de las piezas fabricadas con esas cintas.
Lograr este concepto requirió desarrollo tanto en el proceso como en el equipo para fabricar cintas termoplásticas reforzadas con fibra de carbono en diferentes tamaños de remolque. Vaidya y Husman presentaron una patente provisional junto con la Fundación de Investigación de la Universidad de Tennessee (UTRF, Knoxville, Tennessee, EE. UU.) En 2018 que cubre un proceso para la producción en línea de cintas termoplásticas reforzadas con hasta 50K de fibra de carbono de remolque. Al año siguiente, Vaidya y su equipo de UTK ampliaron este trabajo para incluir la impregnación termoplástica de TCF de banda ultraancha (remolque de 300K a 450K) con una segunda presentación.
Cintas TCF TP
Como era de esperar, no ha habido escasez de desafíos técnicos que abordar en el camino. La alimentación y manipulación de la fibra requirió una modificación significativa del equipo, ya que el TCF tiende a ser más ancho e implica más filamentos que la fibra de carbono convencional. También es propenso al comportamiento de catenaria durante el paso de impregnación de fibras de la producción de cinta. Eso significa que se forma una onda sinusoidal a medida que los cables se introducen en el troquel de impregnación, lo que hace que los cables se dividan de manera desigual y entren en el troquel bajo diferentes tensiones, lo que lleva a cintas que se retuercen, deforman y logran una mala humectación de la fibra.
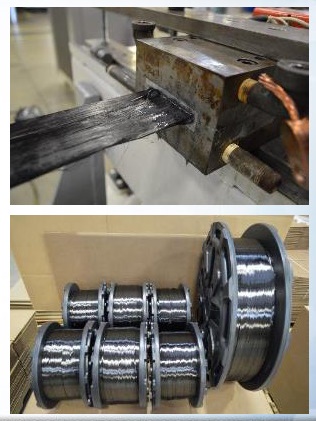
“Encontrar una manera de mantener un equilibrio entre la tensión de la fibra y la flexibilidad resultó ser un verdadero desafío y requirió mucho trabajo”, explica Vaidya. “Nuestro equipo llegó a comprender lo importante que era mantener la integridad del remolque para extender los filamentos y lograr un alto grado de humectación, lo que, por supuesto, es fundamental para producir cintas de calidad”.
Luego estaba el problema del tamaño. Las bandas de remolque de TCF tienen un gran tamaño para ayudar a que la fibra se mueva sin problemas desde la fileta hasta la matriz de impregnación, donde se humedece con resina para producir cinta. Sin embargo, una vez en la matriz, investigaciones anteriores habían demostrado que para lograr una buena humectación con termoplásticos de mayor viscosidad, la presencia de encolado en realidad impedía la impregnación, por lo que era muy deseable eliminar el encolado. La prueba y el error finalmente llevaron al equipo a desarrollar una técnica para quemar el apresto justo antes de que los cables entraran en la matriz de impregnación.
Para predecir con precisión la reología de la resina y la alimentación del polímero a través de la matriz de impregnación y hacer una buena cinta, se necesitaba un nuevo trabajo de simulación y validación. El equipo se centró en producir cintas TCF con polipropileno (PP) y poliamida 6 (PA6), dos termoplásticos ampliamente utilizados en la automoción por su dureza y asequibilidad. El equipo utilizó el software de diseño de matrices de extrusión PolyXtrue de Plastic Flow LLC (Hancock, Michigan, EE. UU.), Que se basa en el modelo Williams-Landel-Ferry (WLF) y proporcionó una excelente correlación con la reología medida y los resultados de la velocidad de corte.
El diseño de troqueles en sí fue otra área de investigación importante, especialmente cuando el equipo pasó de remolques estándar de 12K a 50K, y luego a remolques TCF de banda ultraancha. En esa etapa, el troquel tuvo que ser completamente rediseñado y adaptado un proceso de dos etapas. Durante la primera etapa, se impregna la fibra; Durante la segunda etapa, los ángulos de rotura optimizados para los pernos tensores / de impregnación, que controlan la tensión a la que se tira de la fibra de carbono, la fracción de peso de la fibra (FWF), así como el control de calidad, se establecen para lograr las propiedades deseadas en las cintas completadas. Actualmente, el equipo ha producido 30-50% de cintas FWF tanto en PP como en PA6, incluso con los remolques más pesados.
Para enfriar rápidamente las cintas después de salir de la matriz, se desarrolló un sistema de enfriamiento por aire posterior a la impregnación. El equipo incluso tuvo que idear un método para colocar cintas terminadas en filetas / carretes, debido al ancho de los productos y los desafíos del uso posterior de esas cintas.
Vaidya dice que el equipo se centra actualmente en la integración electrónica, que incluye la construcción de una interfaz gráfica de usuario formal y el desarrollo de un sistema basado en un controlador lógico programable (PLC). En última instancia, el objetivo del equipo es desarrollar un módulo de producción de cinta termoplástica que se pueda agregar al extremo posterior de una línea de producción de fibra de carbono convencional o TCF para facilitar la producción de cintas termoplásticas secundarias / intermedias.
"Nuestro equipo ha enfrentado muchos desafíos técnicos, pero también hemos tenido algunos logros", explica Vaidya. “Manejar una banda de remolque tan ancha y con éxito, y rápidamente, impregnar las fibras para lograr cintas termoplásticas de calidad sin huecos ha sido difícil. Sin embargo, nuestro equipo ha explorado una serie de parámetros de proceso, incluidas múltiples iteraciones de diseño de matrices; simulaciones de flujo de polímero a través de la matriz; y varios aspectos de la alimentación, tensión y precalentamiento de la fibra. No solo hemos probado algunas de las afirmaciones de nuestra patente, sino que también hemos logrado velocidades de línea de impregnación de 12 pies / minuto [3,7 metros / minuto] mientras producimos un 30% de polipropileno FWF y cintas PA6 ".
Pasos siguientes
Vaidya dice que las protecciones de propiedad intelectual que rodean esta tecnología de cinta se han presentado ante la Fundación de Investigación de UT, una con fibras tradicionales de 24K y 50K y otra con fibras de arrastre ancho. La comercialización, dice, se centrará en la impregnación en línea dentro de una línea de fibra de carbono. "Esto reducirá en gran medida el posprocesamiento y se adaptará fácilmente, lo que reducirá aún más el costo general del producto intermedio", dice.
¿Cómo se podrían aplicar estas cintas? Vaidya dice que las opciones son muchas:“Por ejemplo, el material puede cortarse en forma de fibra larga, usarse en materia prima de pultrusión, bobinado de filamentos de tanque grande, sobremoldeo (similar a la hoja orgánica) en moldeo por compresión, material laminado en procesos híbridos, p. , con LFT [termoplástico de fibra larga], SMC [compuesto de moldeado de láminas] y otros materiales sinérgicos ". Esto abre una gama de tipos de productos que se beneficiarían de mejoras de rigidez, dureza de alto impacto y procesabilidad mejorada, como formas, estiramientos y dobleces, reciclaje y químicas reversibles.
Las aplicaciones, dice, incluyen automotriz, camiones, palas eólicas, infraestructura (puentes), construcción, artículos deportivos, productos marinos y de alta mar. “El intermedio termoplástico de fibra de carbono de arrastre ancho ahora puede ofrecer vías para considerar la fibra de carbono donde antes era demasiado cara”, concluye Vaidya.
Resina
- Fibra de carbono
- ¿Qué es la fibra de carbono?
- ¡Plástico reforzado con fibra (FRP) en acción!
- El auge de los plásticos reforzados con fibra de carbono
- Plástico reforzado con fibra de carbono (CFRP)
- Cinta unidireccional termoplástica de fibra de carbono basada en PPS
- El consorcio busca soluciones para estructuras compuestas termoplásticas de fibra de carbono
- Compuestos de impresión 3D con fibra continua
- Fabricación de piezas de IM más resistentes con materiales reforzados y rellenos de fibra
- Fieltro de carburo de silicio reforzado con fibra de carbono SIGRASIC®
- Fibras cortas de carburo de silicio reforzado con fibra de carbono SIGRASIC®