Costillas Wing of Tomorrow:consolidación OOA, termoplástico, de un solo uso
El programa Wing of Tomorrow (WOT) de Airbus, lanzado en 2015, ha pasado los últimos seis años explorando tecnologías de fabricación y ensamblaje de materiales, fabricación y ensamblaje más rentables y de mayor rendimiento para alas de aviones comerciales de pasillo único (ver CW Cobertura anterior del programa WOT).
Según Arnt Offringa, director del GKN Aerospace Global Technology Center Netherlands (Hoogeveen), GKN Aerospace (Bristol, Reino Unido) ha estado muy activo en el programa WOT, incluido el desarrollo de un demostrador de larguero de ala fabricado mediante moldeo por transferencia de resina (RTM) y cuatro nervaduras de ala de aluminio. Otro demostrador de tecnología entregado recientemente por GKN Aerospace involucró el desarrollo de una nervadura de compuesto termoplástico competitivo en costos y un innovador sistema de prensado modular para la fabricación de un solo paso fuera de autoclave (OOA) para producirlo.
Dar el salto a los termoplásticos
En 2018, GKN Aerospace comenzó discusiones internas sobre materiales y tecnologías de fabricación que podrían usarse para producir cinco demostradores
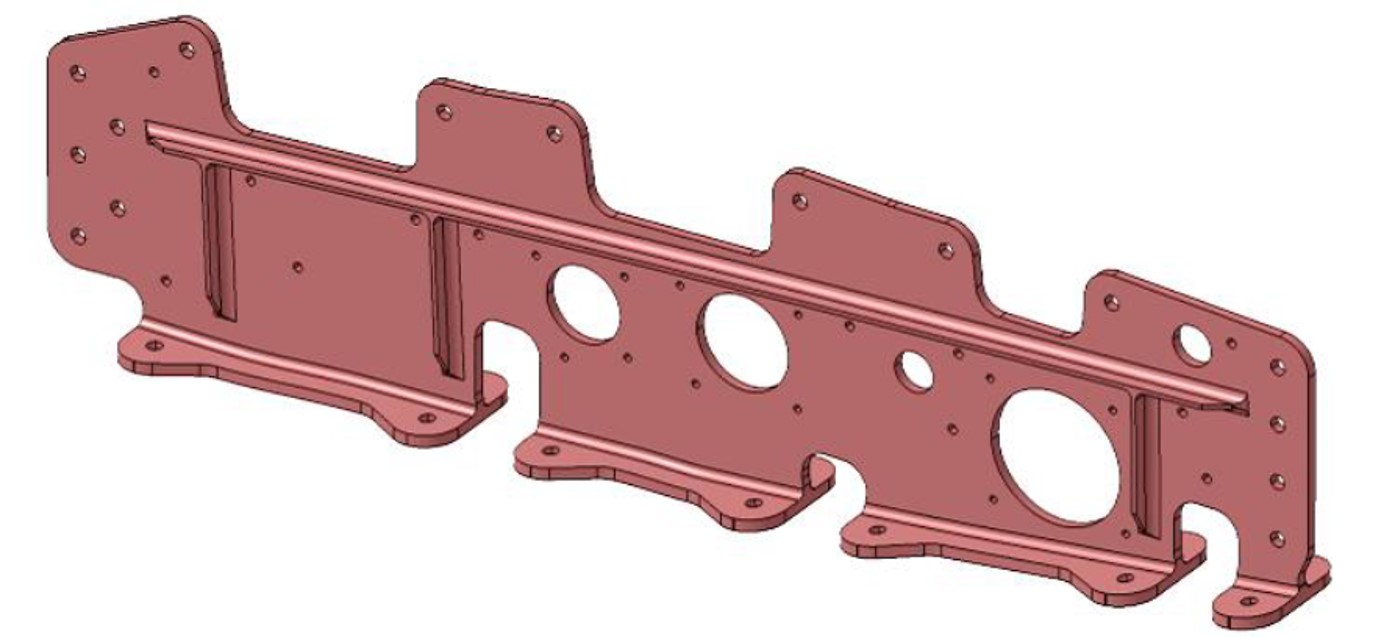
Diseñando la costilla. Para permitir una pieza delgada y liviana, el diseño de la nervadura (arriba) incorpora la tecnología de junta a tope de GKN (abajo), con rellenos de refuerzo moldeados por inyección (en el medio, se muestra en verde).
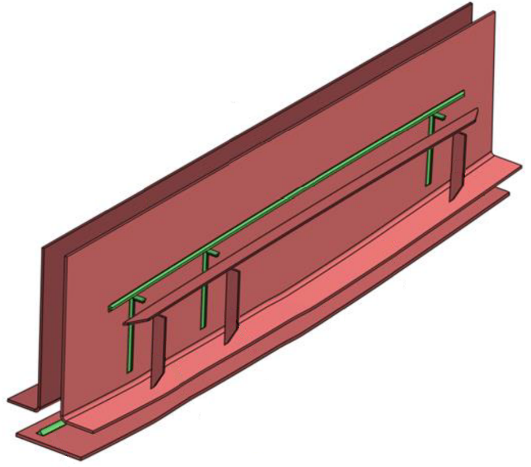
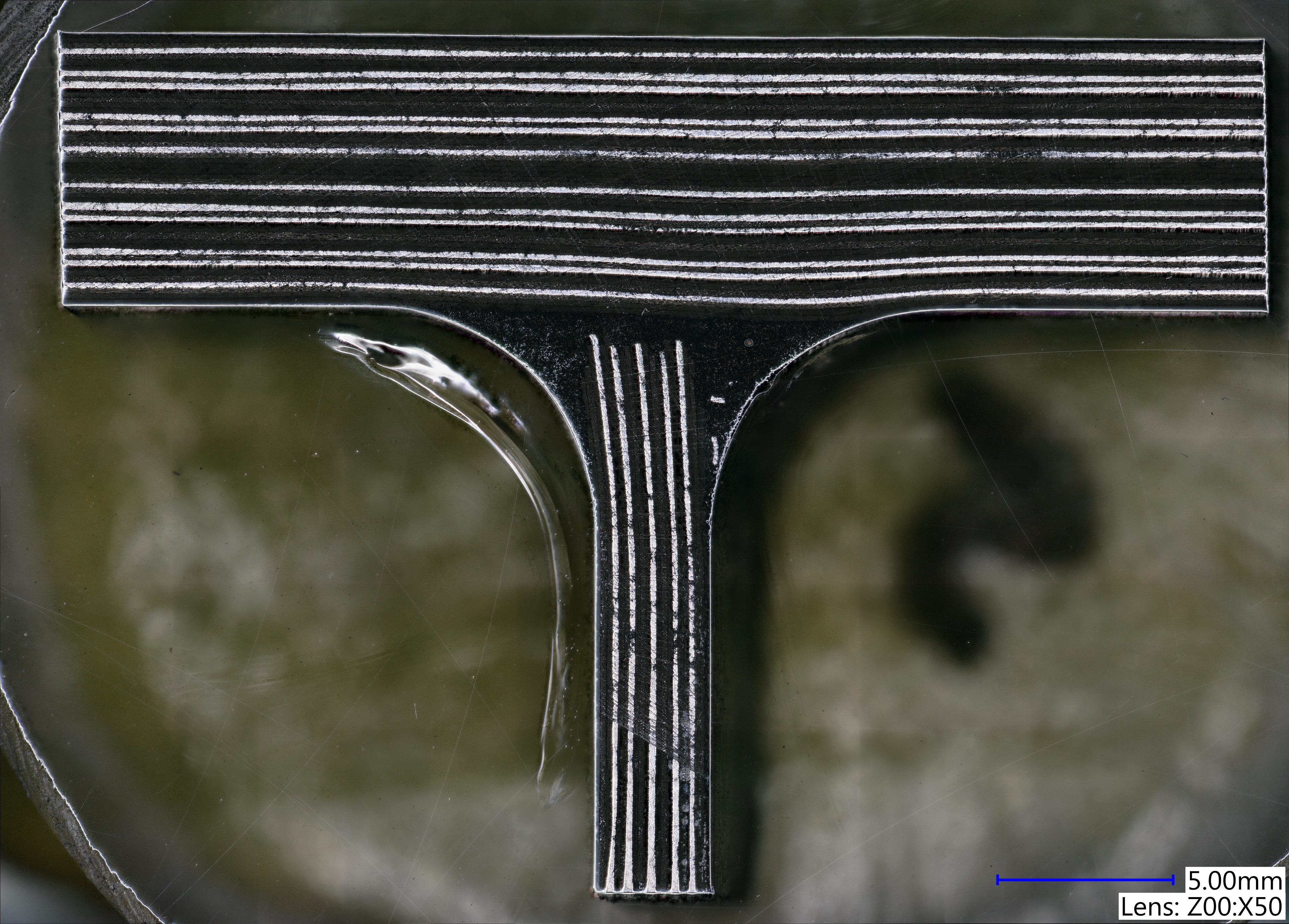
costillas para el programa WOT. GKN Aerospace comparó varias opciones de materiales, incluidos compuestos termoendurecibles y termoplásticos. El aluminio, el material tradicional para las nervaduras de los aviones comerciales, fue elegido para producir cuatro nervaduras interiores más grandes, pero para la nervadura exterior más pequeña, la empresa decidió explorar una opción compuesta. Offringa señala que debido a que el demostrador WOT será un ala compuesta, desarrollar una nervadura compuesta que pueda competir con el aluminio es un paso lógico.
“Una nervadura compuesta en un ala compuesta es beneficiosa por varias razones”, dice. “Primero, el uso de materiales compuestos con materiales compuestos significa que no hay diferencia en la expansión térmica entre los materiales, como lo haría con una nervadura de metal en un ala de material compuesto o viceversa. En segundo lugar, no tendrá problemas ni preocupaciones con respecto a la corrosión. Los composites también significan peso reducido. Por último, pero no menos importante, el uso de materiales compuestos facilita la inspección ”.
Offringa explica que las costillas metálicas típicas requieren una inspección humana visual una vez que se ensambla el ala final. Sin embargo, debido a la ubicación de las costillas en el interior del ala, eso significa que sería necesario cortar grandes escotillas elípticas en la piel de la parte inferior del ala para que los humanos puedan ingresar al ala para inspeccionarlas. “Si opta por una nervadura compuesta, tiene menos fatiga en las nervaduras y menos fisuras potenciales por fatiga que debe inspeccionar. La inspección se vuelve mucho más simple y menos intensiva, y ya no es necesario construir escotillas en la piel de las alas. Será una piel de alas continua ”, dice.
Se pueden obtener beneficios de reducción de peso, resistencia a la corrosión y una inspección menos invasiva de los compuestos termoendurecibles o termoplásticos. "Hicimos un estudio interno y analizamos el peso, el costo y la industrialización, y después de comparar las diferentes tecnologías, se tomó la decisión de optar por los termoplásticos, porque tenían el mayor potencial y el mejor caso comercial con respecto al costo", dice Offringa. .
Dada su proximidad más cercana al centro de tecnología de alas de Airbus en Filton, Reino Unido, donde se probará el demostrador WOT, la sucursal de GKN Aerospace en Bristol, Reino Unido es el centro principal del trabajo WOT de la compañía. Sin embargo, dada la experiencia de GKN Aerospace Netherlands en termoplásticos desde sus días como Fokker Technologies, los dos equipos de GKN Aerospace unieron fuerzas para el demostrador de nervaduras. "El diseño se realizó en el Reino Unido, pero el desarrollo de la fabricación se realizó en los Países Bajos, por lo que fue una cooperación realmente agradable entre los diferentes equipos de GKN Aerospace", dice Offringa.
Sue Partridge, directora de WOT en Airbus, señala:“La colaboración con los socios es un aspecto importante del programa Wing of Tomorrow. Combinando nuestros recursos, podemos desarrollar soluciones que aprovechen las capacidades de nuestras dos organizaciones para obtener mejores resultados ”.
Para las varillas WOT entregadas a Airbus, GKN Aerospace utilizó las cintas de fibra de carbono APC / polietercetonecetona (PEKK-FC) de Solvay (Bruselas, Bélgica), que se basan en la fórmula de cristalización rápida Novaspire PEKK-FC (FC) de la empresa. Offringa señala que el material de fibra de carbono / poliariletercetona (PAEK) de bajo punto de fusión de Toray Advanced Composites (Morgan Hill, California, EE. UU.) También se está evaluando como una opción para futuras estructuras de nervaduras.
Diseño de una nervadura de ala de próxima generación
Hay más de 20 nervaduras en un ala típica de un avión de pasillo único. La nervadura del demostrador de material compuesto termoplástico es la decimocuarta en el ala del demostrador; los demás demostrarán materiales y procesos alternativos.
Las nervaduras de compuestos termoplásticos a menudo se fabrican mediante estampado para aviones pequeños, dice Offringa. Sin embargo, GKN Aerospace descartó la estampación tradicional como una opción para la nervadura WOT porque las alas de aviones comerciales, incluso para cuerpos estrechos como el demostrador WOT, se colocan bajo cargas de compresión y tensión muy altas.
“Si fuera a estampar una nervadura termoplástica en el sentido tradicional, entonces tendría que hacer una nervadura muy gruesa, con una red gruesa para hacerla más fuerte y que pueda resistir las fuerzas que actúan sobre ella”, dice Offringa, y eso no es preferible dados los requisitos de reducción de peso. Además, la estampación no podría crear un componente de ala inferior de doble cara en la nervadura donde la pieza se conecta al revestimiento del ala inferior; se necesitaría fabricar un componente adicional y atornillarlo al resto de la nervadura. GKN Aerospace necesitaba un proceso de fabricación que permitiera una mayor flexibilidad para el diseño que el equipo tenía en mente.
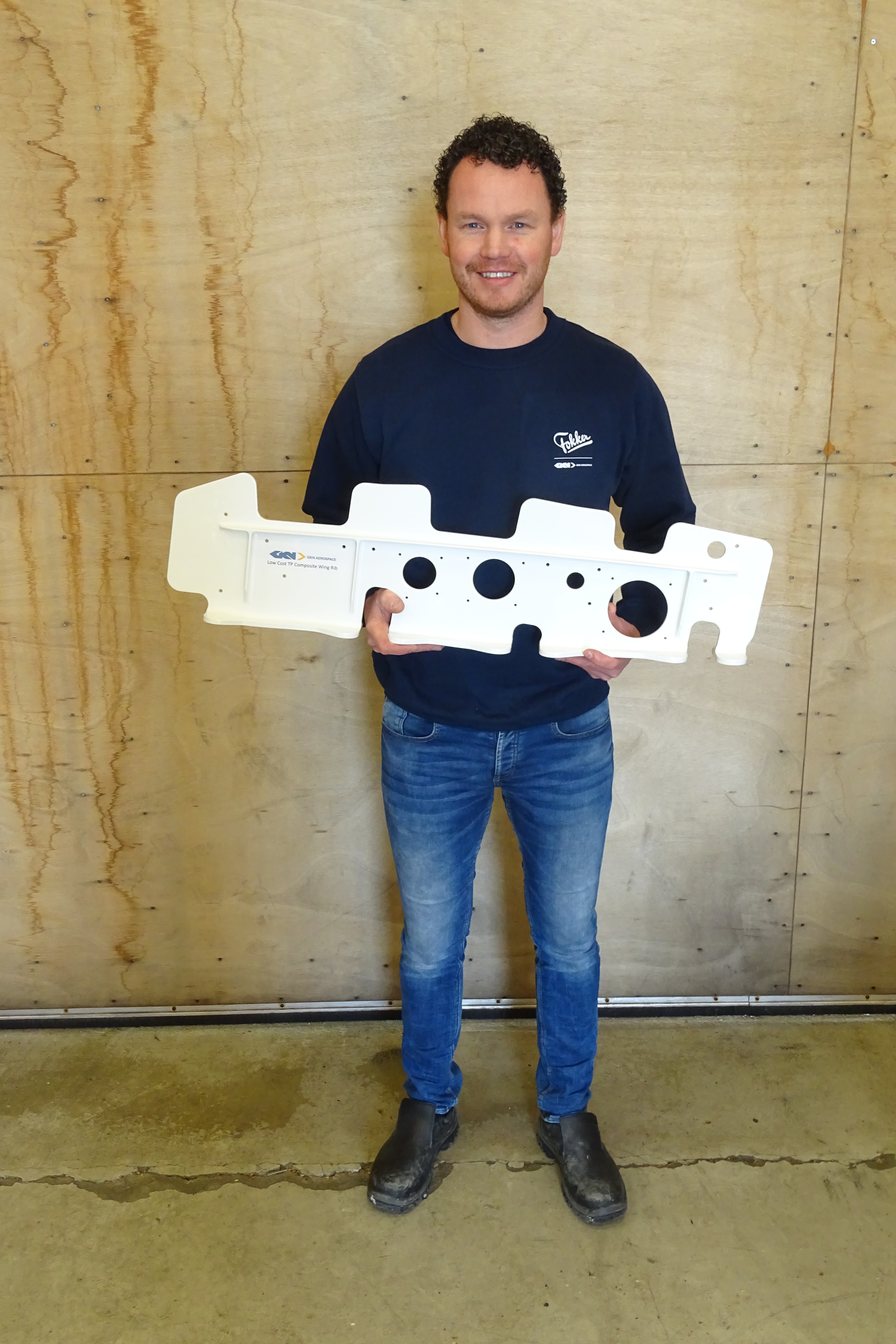
La nervadura termoplástica de 90 centímetros de largo y 24 centímetros de altura de GKN Aerospace presenta una red vertical y una pestaña bidireccional de 8 milímetros de espesor que se extiende desde la parte inferior de la nervadura. Para cumplir con los requisitos de peso, la banda tiene solo 7 milímetros de grosor. Para evitar el pandeo y aumentar la rigidez, la red se refuerza con elementos de refuerzo de 3 milímetros de espesor utilizando la tecnología de junta a tope de GKN Aerospace, que utiliza preformas de refuerzo planas y materiales de "relleno" moldeados por inyección para crear una junta sólida y continua (consulte "Termoplástico las aeroestructuras primarias dan otro paso adelante ”para aprender sobre el uso de esta tecnología en un panel de fuselaje Gulfstream fabricado con cintas de fibra de carbono / PEKK-FC de Solvay).
“Sabíamos que si podíamos hacer esta forma en materiales compuestos y hacerlo robusto, entonces tendríamos un diseño muy liviano con la reducción de peso que estábamos buscando. Pero el problema era, ¿cómo se puede hacer una forma tan complicada de forma rentable y con tasas elevadas? Ahí es donde ponemos nuestro esfuerzo para crear este nuevo producto ", dice Offringa.
Fabricación OOA en un solo paso
El proceso se basa en la tecnología que GKN Aerospace ha utilizado anteriormente para el proyecto TAPAS (Estructura de aeronave primaria asequible termoplástica) y para el desarrollo de un panel de fuselaje para Gulfstream que utiliza la tecnología de juntas a tope de la empresa. Para la nervadura WOT, GKN Aerospace desarrolló un proceso de consolidación OOA, de un solo paso. "Hemos llevado nuestro trabajo anterior al siguiente nivel al salir del autoclave por primera vez", señala Offringa.
Primero, las cintas termoplásticas unidireccionales (UD) se cortan a los anchos correctos y se usa un laminador para preformar los elementos planos en dos preformas de banda en forma de L. Las preformas de la red, una preforma plana para la brida y las preformas más pequeñas y los elementos de relleno moldeados por inyección que componen los larguerillos se cargan en una herramienta, que se coloca dentro de una prensa de co-consolidación modular que es similar a un moldeo por transferencia de resina. (RTM) presione. La prensa se cierra y se utiliza un sistema de vejiga para crear presión tanto en dirección horizontal como vertical, simulando la presión en un autoclave. Un sistema de calentamiento por resistencia integrado hace que el material compuesto se derrita brevemente antes de enfriarse para su consolidación.
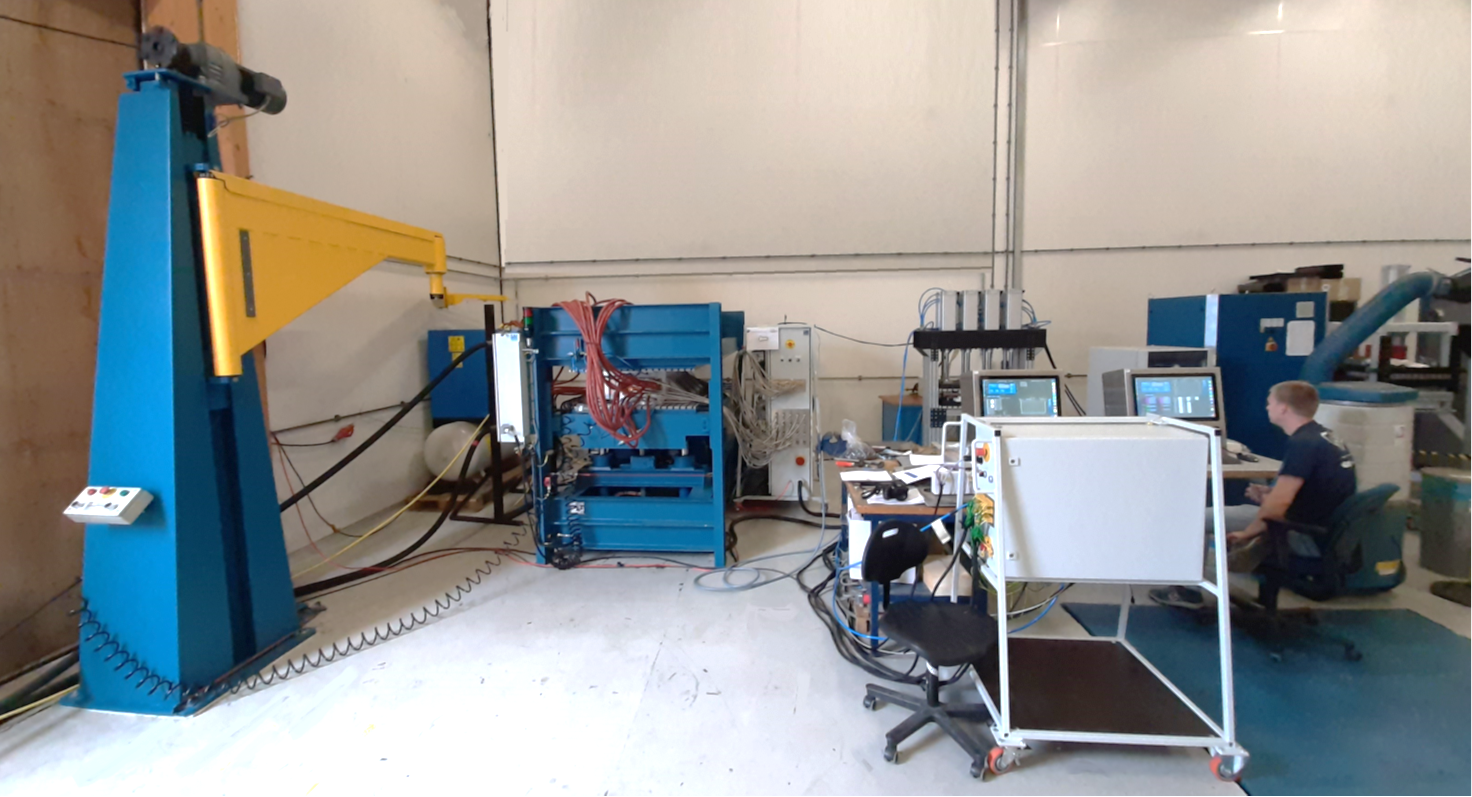
“Ponemos la mayor parte del esfuerzo de desarrollo en ajustar y optimizar las herramientas”, dice Offringa. El sistema está diseñado para ser modular; las herramientas se pueden intercambiar para acomodar nervaduras con diferentes dimensiones u otros tipos de piezas mientras se mantiene el mismo sistema de calefacción y refrigeración. Aunque no es necesaria para estas nervaduras, la prensa que GKN Aerospace desarrolló en su Centro Tecnológico puede alojar piezas de hasta 6 metros de largo, que también podrían incluir otros paneles o vigas.
El sistema de control de procesos es clave a la hora de procesar termoplásticos. Los termoplásticos se derriten a temperaturas más altas que los termoendurecibles y deben enfriarse en un proceso controlado y constante para minimizar la deformación y maximizar la cristalinidad. "Es muy importante controlar el proceso exacto de principio a fin", dice Offringa. "La gestión térmica del ciclo de calentamiento es muy importante". (Consulte la barra lateral "Problemas de formación de termoplásticos (TP)" en este artículo para obtener más detalles sobre los problemas y la importancia del control del proceso cuando se utilizan termoplásticos).
Se utilizan características especiales de herramientas para permitir que los refuerzos delgados e integrados se suelten fácilmente de la herramienta. La parte desmoldeada tiene una forma casi neta y luego se recorta para formar la parte terminada. Desde la entrada de la herramienta hasta la salida de la herramienta, todo el proceso dura unos 45 minutos. Esto significa que con una prensa, se pueden fabricar alrededor de 15 costillas de ala en un turno de ocho horas.
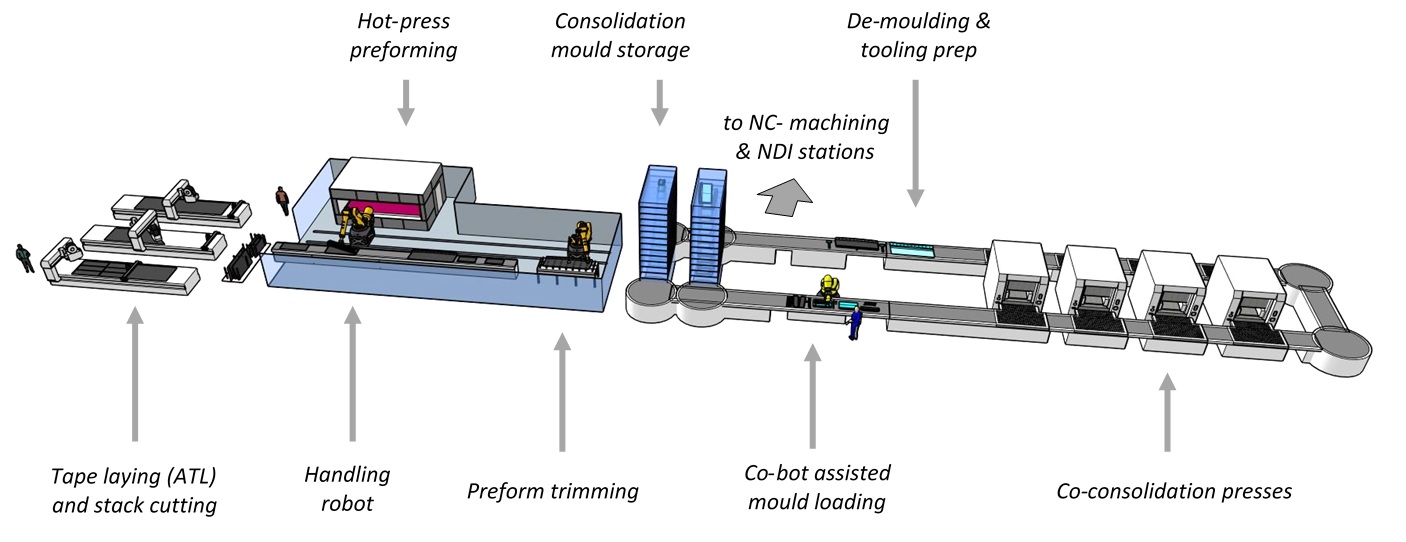
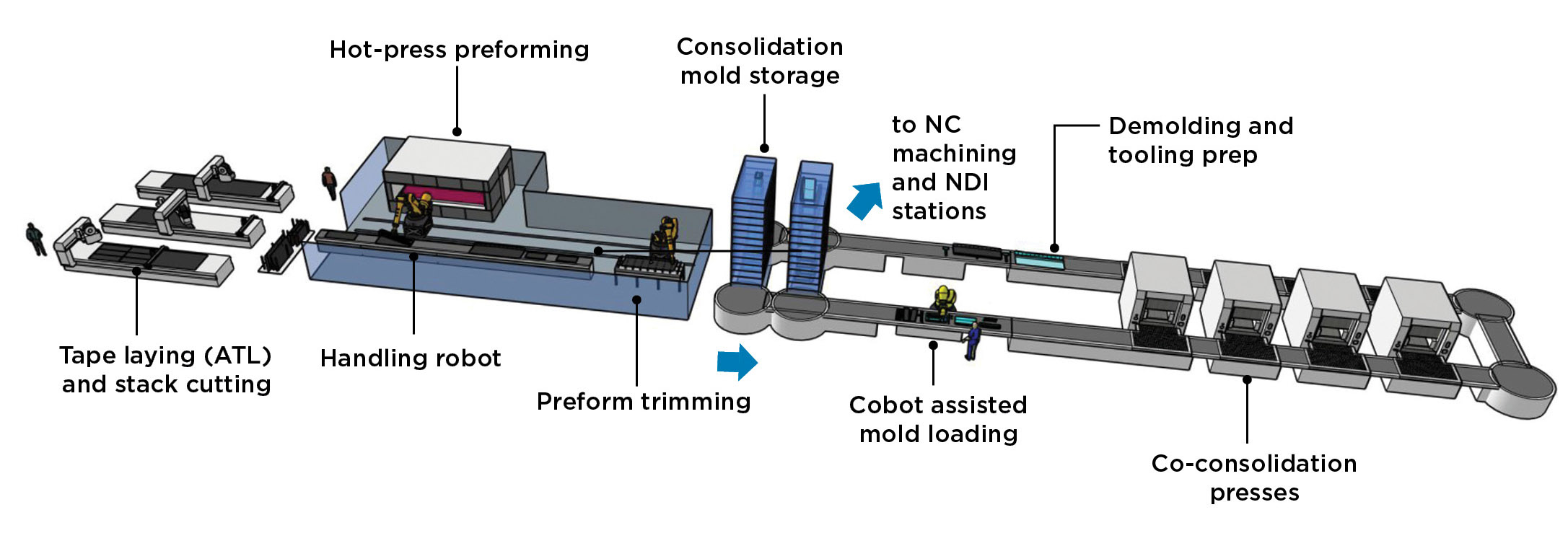
“Termina siendo un proceso de fabricación simple”, señala Offringa. “Estamos haciendo muchas cosas a la vez:consolidar preformas con diferentes formas, crear la parte inferior de la nervadura para que tenga un reborde bidireccional y, al mismo tiempo, endurecer la red con la tecnología de unión a tope. Sin embargo, en última instancia, tomamos todos los elementos del material, los colocamos en una herramienta y creamos una pieza homogénea en un solo paso de procesamiento ”.
Pruebas, entrega y más
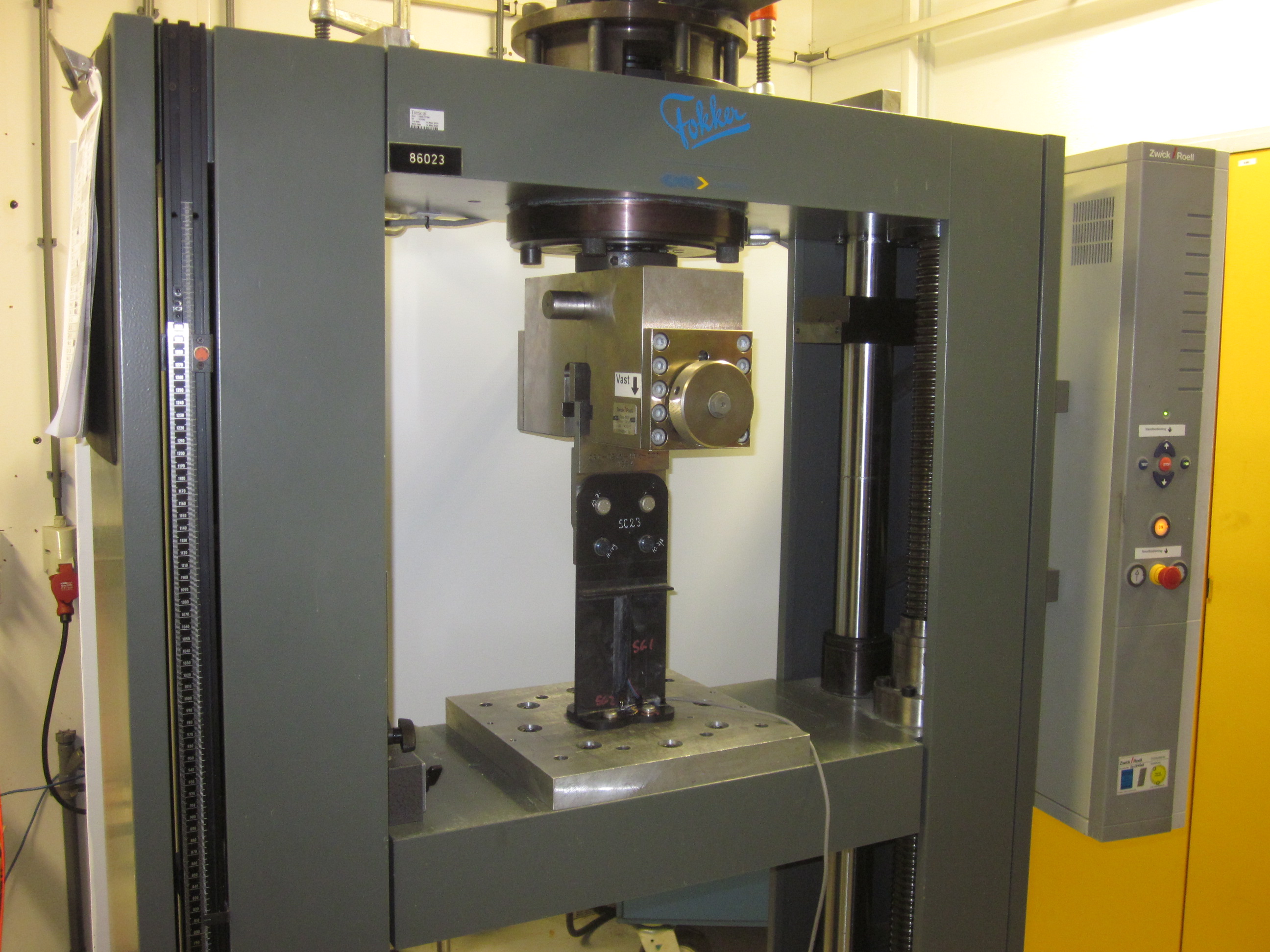
Pruebas. Los subcomponentes se probaron para cumplir con los requisitos de resistencia a la tensión y la compresión en las instalaciones de GKN en la Isla de Wight y Hoogeveen.
A fines de 2019, los subcomponentes de nervios se probaron en las instalaciones de GKN Aerospace en la Isla de Wight y Hoogeveen, y Offringa dice que pasaron los requisitos de carga de tensión y compresión "por un amplio margen". Agrega:“Es fuerte, es resistente, es fácil de fabricar. Este es un concepto que resultó exactamente como esperábamos ”. En comparación con una versión de aluminio, Offringa dice que la versión de compuesto termoplástico ofrece ahorros de peso significativos y es competitiva en costos.
La compañía ha entregado tres nervaduras a Airbus, una de las cuales se ensamblará y probará en el demostrador WOT. GKN Aerospace continúa trabajando en la optimización de su proceso y materiales para nervaduras aeroespaciales comerciales, tanto para Wing of Tomorrow como más allá.
Resina
- Compuesto termoplástico reforzado con fibra continua fabricado íntegramente a partir de recursos naturales
- Solvay expande la capacidad de compuestos termoplásticos
- Fraunhofer encarga células de producción automatizadas de Engel para I + D de compuestos termoplásticos
- El Instituto de Estructuras y Diseño DLR aumenta la madurez de las estructuras de fuselaje de compuestos termoplásticos
- Solvay completa la instalación de las instalaciones de Carolina del Sur y aumenta la capacidad de compuestos termoplásticos de EE. UU.
- Las cintas termoplásticas continúan mostrando potencial para aeroestructuras compuestas
- INEOS Styrolution para construir un sitio de producción para el compuesto termoplástico StyLight
- Xenia presenta los compuestos termoplásticos CF / PP
- Tubo compuesto termoplástico en ascenso en las profundidades del mar
- Compuesto termoplástico TenCate calificado para NIARs NCAMP
- TenCate celebra la asamblea del consorcio de compuestos termoplásticos en Brasil