Aceleración de RTM con sensores de flujo de calor
El tren de aterrizaje, que representa entre el 3% y el 5% del peso de una aeronave, ha sido durante mucho tiempo el objetivo de reducir el peso para mejorar la eficiencia de la aeronave. Esto se ha vuelto aún más crítico con el inminente cambio a sistemas de propulsión eléctrica que reducen la energía y las emisiones.
Por ejemplo, Safran Landing Systems (Vélizy, Francia) permitirá el rodaje eléctrico con motores apagados a través de motores eléctricos integrados en las ruedas del tren de aterrizaje del avión, reduciendo NOx, CO 2 , Las emisiones de CO e hidrocarburos no quemados en un 51%, 61%, 73% y 62%, respectivamente. Esta es una gran victoria para una aviación más sostenible, pero los motores eléctricos requieren energía y las baterías necesarias para suministrar esa energía son pesadas.
Por lo tanto, la demanda de estructuras de tren de aterrizaje livianas parece un ajuste perfecto para la aplicación de materiales compuestos, excepto por un problema. “Debido a que el tren de aterrizaje es una estructura de trayectoria de carga única, la falla de un componente estructural podría resultar en una condición de aterrizaje de emergencia grave”, dice Peet Vergouwen, tecnólogo de GKN Fokker Landing Gear (Helmond, Holanda). GKN Fokker Landing Gear ha trabajado durante más de una década para demostrar la viabilidad técnica de las estructuras compuestas del tren de aterrizaje, incluido el desarrollo de tirantes de arrastre de polímero reforzado con fibra de carbono (CFRP) para el F-35 Lightning II . "Debido a su criticidad, las estructuras de los trenes de aterrizaje se encuentran entre las más conservadoras en los aviones comerciales". Por lo tanto, en su mayoría se han fabricado a partir de metales de alta resistencia.
Sin embargo, esa marea está comenzando a cambiar. Clean Sky 2 persigue una reducción de peso del 30%, pero a través de componentes CFRP en el proyecto HECOLAG (High Efficiency Composites LAnding Gear), para dos aplicaciones. En la primera aplicación, se desarrolló una alternativa CFRP para el tirante de arrastre superior de aluminio existente. para el tren de aterrizaje delantero del A350-1000, desarrollado y fabricado originalmente por Liebherr-Aerospace (Lindenberg, Alemania). Los socios de HECOLAG, el Royal Netherlands Aerospace Center (NLR, Marknesse) y GKN Fokker Landing Gear, han diseñado esta estancia de arrastre CFRP según los requisitos de Liebherr. Utilizando tecnología de preformado automatizada desarrollada internamente, NLR ha construido prototipos funcionales del soporte de arrastre CFRP, que fueron probados por GKN Fokker Landing Gear.
En la segunda aplicación que está siendo evaluada por HECOLAG, NLR y GKN Fokker Landing Gear también han desarrollado un CFRP soporte lateral inferior en conjunto con Safran Landing Systems para el tren de aterrizaje principal electrificado. CW informará específicamente sobre los resultados generales del proyecto HECOLAG más adelante en 2021, pero aquí, el enfoque está en el subproyecto INNOTOOL 4.0, guiado por el gerente de temas GKN Fokker Landing Gear para avanzar en la producción altamente automatizada de estructuras de trenes de aterrizaje CFRP utilizando moldeo por transferencia de resina (RTM) . Específicamente, INNOTOOL 4.0 busca demostrar herramientas integradas por sensores que liderarán el camino hacia herramientas más pequeñas con menos masa para ciclos de producción más rápidos, manejo más fácil y menor consumo de energía, así como una mayor automatización para un menor costo y control de proceso inteligente de compuestos 4.0. El proyecto INNOTOOL 4.0 está financiado por la Empresa Común Clean Sky 2 en el marco del programa de investigación e innovación Horizon de la UE en virtud de GAP n.o 821261.
Objetivos de INNOTOOL 4.0
El demostrador de esta segunda parte de HECOLAG (ver imagen de apertura) es más una parte genérica, explica Vergouwen. "Es para demostrar el diseño de piezas, la simulación y las metodologías de fabricación que proporcionarán el rendimiento, la tasa de producción y el costo necesarios para los aviones de pasillo único". A finales de 2017, el consorcio HECOLAG había definido la pieza de demostración inicial de CFRP y la herramienta de producción, analizado el comportamiento térmico de la herramienta y realizado pruebas de rendimiento. Este producto grande y complejo pasó la revisión de diseño preliminar y alcanzó un nivel de preparación tecnológica (TRL) de 4 más tarde ese año. “Basándonos en los problemas y las lecciones aprendidas de ese primer demostrador, estábamos buscando socios para desarrollar tecnología de herramientas RTM para optimizar y acortar el ciclo de curado”, dice Vergouwen. En 2018 se emitió una convocatoria de socios Clean Sky 2 que se otorgó al consorcio INNOTOOL 4.0, que incluye al proveedor de equipos y automatización Techni-Modul Engineering (TME, Coudes, Francia) y al especialista en inyección de resina Isojet Equipements (Corbas, Francia). Comenzaron a trabajar en abril de 2019 y completaron los hitos iniciales en marzo de 2021.
“La pieza compuesta debe ser rentable con el acero y el aluminio forjados”, señala Vergouwen de GKN Fokker Landing Gear. "Eso solo es posible con la automatización, lo que permite una cantidad muy baja de horas de trabajo y materiales más asequibles que el actual CFRP curado en autoclave de grado aeroespacial".
Por lo tanto, INNOTOOL 4.0 buscó integrar sensores en las herramientas RTM que monitorearán y manejarán los procesos de inyección y curado, incluida la detección de frente de flujo de resina. “El objetivo es estar completamente automatizado:cargar la preforma, presionar un botón y el equipo de moldeo administrará la temperatura, la presión, el vacío y el curado”, dice Stéphane Besson, director comercial de TME. Sin embargo, esta es la primera vez que GKN Fokker Landing Gear y TME han trabajado con el monitoreo de curado. "Hemos trabajado con sensores de temperatura y presión antes", dice Besson, "pero no con sensores de flujo de resina y polimerización".
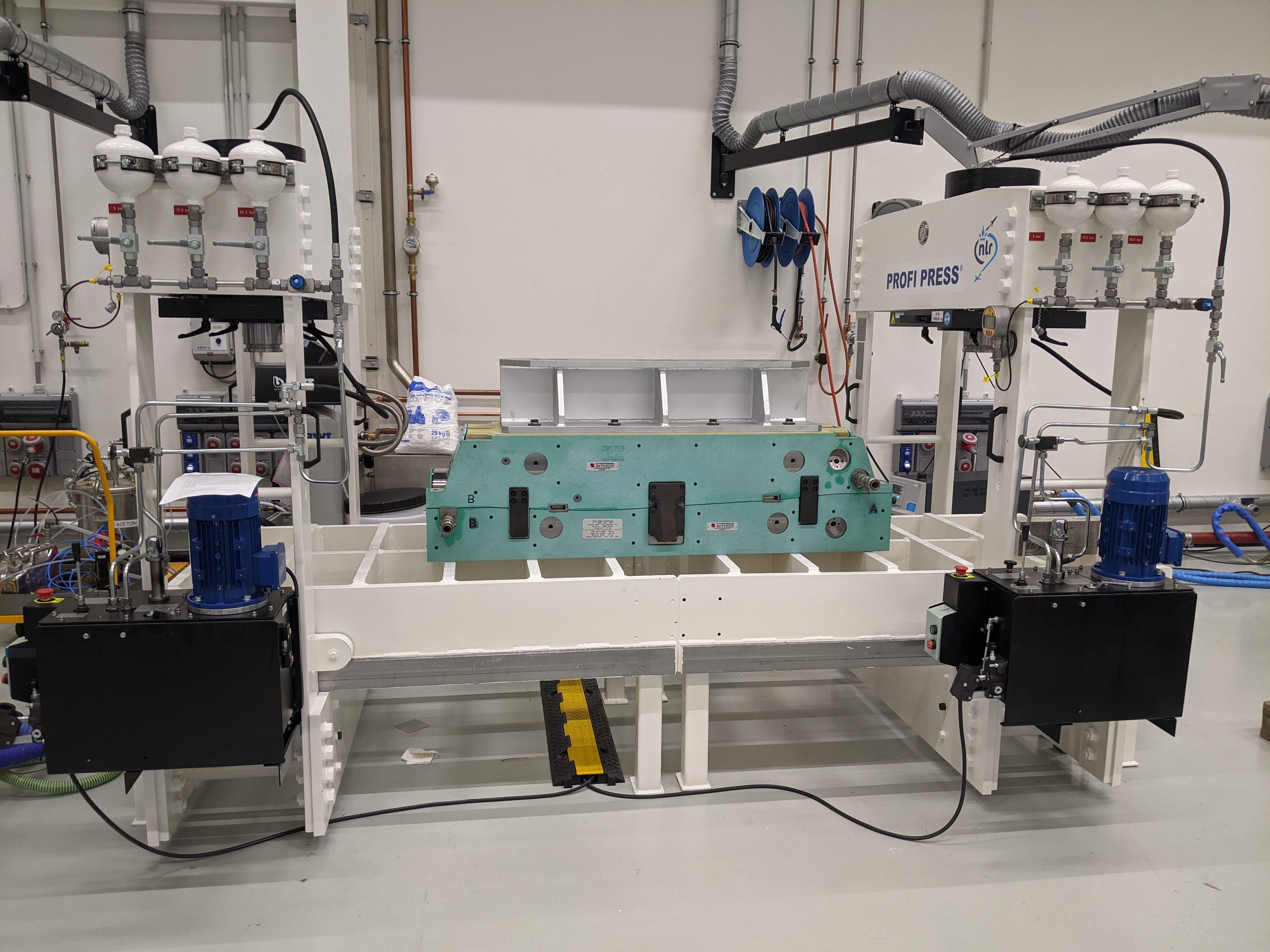
Los hitos iniciales del proyecto INNOTOOL 4.0 requirieron que TME e Isojet entregaran una herramienta de moldeo y un sistema de inyección equipados con sensores a NLR que se usaría para producir piezas de demostración en marzo y abril de 2021. Paralelamente, TME usaría una herramienta existente para la producción de Placas de CFRP - tamaño 600 x 600 milímetros con espesor de 1-8 milímetros - modificadas con los mismos sensores para pruebas de control de procesos en sus instalaciones. “Esto es algo que preferiría hacer a pequeña escala la primera vez en lugar de hacerlo directamente en una herramienta grande con una pieza de alto costo”, dice Vergouwen. Por lo tanto, TME utilizó una herramienta diferente, pero los mismos sensores para mostrar sus capacidades y profundidad. Con esta prueba completa, NLR reutilizaría la herramienta principal de HECOLAG para producir una nueva ronda de demostradores de CFRP para optimizar aún más el control del proceso en las piezas reales.
Diseño de herramientas de producción RTM
TME comenzó la producción del diseño de la herramienta RTM utilizando el software CATIA V5 de Dassault Systèmes (Vélizy-Villacoublay, Francia) para el diseño mecánico y eléctrico, y ANSYS (Canonsburg, Pensilvania, EE. UU.) Para la simulación térmica y mecánica. Esta herramienta se combinaría con el sistema de pistón 1K-2K (para resinas de una y dos partes) de Isojet para inyectar Hexcel (Stamford, Connecticut, EE. UU.) HexFlow 2K RTM 6 y Solvay (Alpharetta, Georgia, EE. UU.) 1K Resinas epoxi monocomponente de grado aeroespacial PRISM EP 2400 a una presión de inyección de hasta 20 bar.
“La forma de esta herramienta de moldeo es muy compleja”, señala Besson, “combinando espesores variables en la preforma seca 3D con una forma tubular cerrada. Esto crea transiciones de espesor complejas, con problemas relacionados con el ensamblaje de la preforma, la precisión del extremo de la capa, los gradientes de temperatura internos y la contracción de la resina, así como la forma de optimizar el método de calentamiento y la capacidad de calentamiento del mandril interno para permitir un tiempo de ciclo corto. Para permitir tiempos de ciclo cortos, todos los elementos de la herramienta deben ser fáciles de usar, robustos y permitir un calentamiento y enfriamiento rápidos ". Aunque el proyecto INNOTOOL 4.0 solicitó brevemente soluciones de moldes no metálicos, se ideó un conjunto típico combinado de moldes de acero superior e inferior debido a las presiones necesarias para minimizar las arrugas y asegurar la alineación de la fibra durante el conformado.
Los moldes y mandril superior e inferior emparejados se calientan y enfrían. "Los moldes combinados utilizan un circuito de agua integrado, mientras que el mandril se calienta eléctricamente", explica Besson. "La circulación del agua proporciona un calentamiento y enfriamiento rápidos para reducir el tiempo del ciclo parcial y el calentamiento eléctrico logra lo mismo en el mandril donde el espacio es limitado".
“Otro desafío fue el número de piezas en el mandril”, dice Besson. “Debido a la forma compleja y la necesidad de quitar el mandril después del moldeado, constaba de seis componentes autocalentables y dos elementos de soporte por donde pasan los sensores para controlar la temperatura interna de las piezas del mandril. En uso, estos elementos se ensamblan a mano con la ayuda de un soporte base que guía al operador ”. El trabajo con un mandril inflable como solución se completará dentro del proyecto HECOLAG más grande, pero eso no se incluyó en el subproyecto INNOTOOL 4.0.
Sensores de flujo de calor
TME inicialmente planeó usar sensores dieléctricos para monitorear el flujo de resina y el curado (ver “Combinación de medidas dieléctricas de CA y CC para monitorear el curado de compuestos”) pero cambió a sensores de flujo de calor de TFX (Boncourt, Suiza). “A medida que avanzábamos en el desarrollo, queríamos sensores que permitieran controlar la medición sin contacto directo con el polímero y los materiales compuestos”, explica Jorge López Torres, gerente de proyectos de TME. "Los sensores TFX permitieron esto porque miden el flujo de calor, que se propaga a través de los materiales". Señala que se trata básicamente de la misma medida que se utiliza en la calorimetría diferencial de barrido (DSC), una técnica de laboratorio que analiza el estado de curado de un polímero o material compuesto. En particular, los sensores TFX y las pruebas DSC miden el calor liberado durante la polimerización / curado y dan como resultado una curva de flujo de calor en función de la temperatura y el tiempo.
Para los sensores TFX, los datos de temperatura provienen de un sensor de temperatura interno dentro de los sensores de flujo de calor. Aunque los sensores dieléctricos están equipados de manera similar con un sensor de temperatura interno, los dos sensores son muy diferentes. “Los sensores dieléctricos miden directamente las propiedades del polímero durante el curado”, explica el Dr. Fabien Cara, director de TFX. “Los sensores de flujo de calor no dan el estado del material en un instante dado. Sin embargo, medir el calor generado durante el flujo de resina y la polimerización proporciona una buena vista de cómo se está comportando el proceso y cuán repetible es el ciclo de curado para cada pieza producida. Y como DSC, necesitamos ver la curva completa del proceso de curado, pero nuestra capacidad para monitorear el curado es muy confiable ”.
Décadas de experiencia
Fundada como Thermoflux en 2000, los sensores TFX se han utilizado en pruebas en centros de I + D y en aplicaciones industriales por más de 100 clientes en todo el mundo. “Comenzamos a trabajar con RTM hace más de 15 años”, dice Cara, “primero con BMW para piezas de automóviles y también para el centro técnico ahora conocido como Institute de Soudure [(Saint-Avold, Francia)]. En 2006 y 2012, iniciamos dos grandes proyectos para monitorear el curado de las aspas de los ventiladores de motores de aeronaves fabricadas con preformas RTM y tejidas en 3D. Safran tiene un sistema de adquisición de datos que desarrollamos para ellos en su laboratorio de compuestos cerca de París. Pueden registrar hasta 100 señales simultáneamente [(flujo de calor, temperatura y presión]) y analizarlas para curar y monitorear los ciclos del proceso ”. TFX también ha trabajado con Hexcel en su laboratorio en Les Avenières, Francia, para monitorear la calidad y los ciclos de procesamiento con resinas termoendurecibles inyectadas en preformas secas. Los sensores TFX también se utilizaron en un proyecto con IRT-M2P (Porcelette, Francia) para demostrar Compression RTM (Más información). “Nuestros sensores son muy eficientes para procesos rápidos como el moldeo por compresión, incluso con compuestos de moldeo SMC y BMC”, señala Cara. “También ganamos un premio de innovación JEC en 2016 con Huntsman Advanced Materials [(Basilea, Suiza)] por un desarrollo titulado 'Piezas epoxi estructurales con calidad de autoclave en menos de 1 minuto'”.
TFX dispone de sensores para todo tipo de proceso de moldeo de composites, basados en el método de transferencia de calor al sensor:conducción (RTM, compresión e inyección), convección (autoclave, horno) y radiación (bobinado de filamentos, AFP). Los sensores utilizados en el proyecto INNOTOOL 4.0 eran conductores, diseñados para incrustarse en moldes de metal RTM. “Proporcionan una señal excepcionalmente repetible a una distancia de hasta 1 milímetro de la superficie de la herramienta y el material compuesto”, señala Cara.
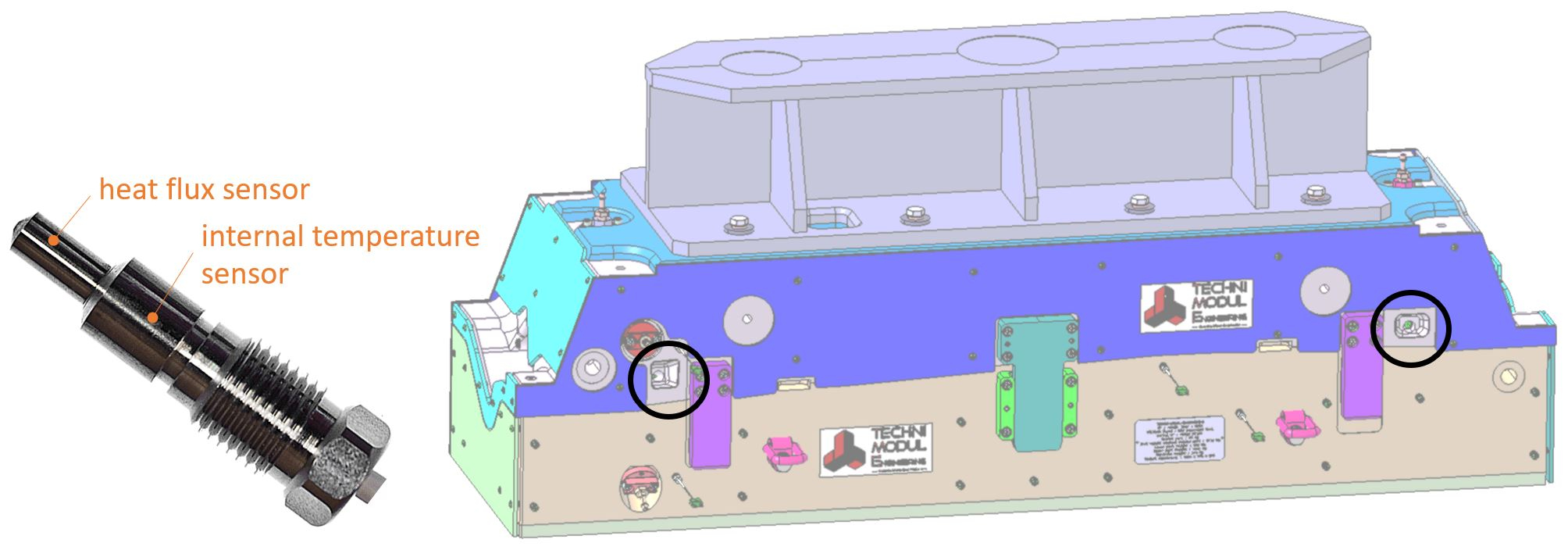
TME instaló dos sensores TFX-191, uno en la entrada de resina y otro en la salida de resina, en el molde superior del conjunto de herramientas de producción correspondiente que luego envió a NLR (Fig. 1, 2). NLR utilizó esta herramienta de producción para fabricar piezas de demostración HECOLAG en marzo y abril de 2021. Los sensores TFX-191 son para herramientas metálicas gruesas.
Paralelamente, TME tomó una herramienta interna más pequeña utilizada para hacer placas de CFRP de muestra y la modificó con dos sensores TFX-224, que son más cortos, para herramientas más delgadas (Fig. 3). Este conjunto de herramientas de placa RTM se utilizó luego para realizar pruebas de demostración de sensores según los objetivos de INNOTOOL 4.0 descritos anteriormente. "Estos sensores son similares a los que usamos para Safran", dice Cara, "pero ahora se han mejorado para que sean mucho más compactos y sensibles". Los sensores se colocaron cerca del centro de la pieza y la salida de resina. Además de los sensores de flujo de calor, TFX desarrolló y suministró dos sistemas de adquisición de datos:uno entregado a Isojet y otro utilizado por TME para las pruebas de placas de CFRP.
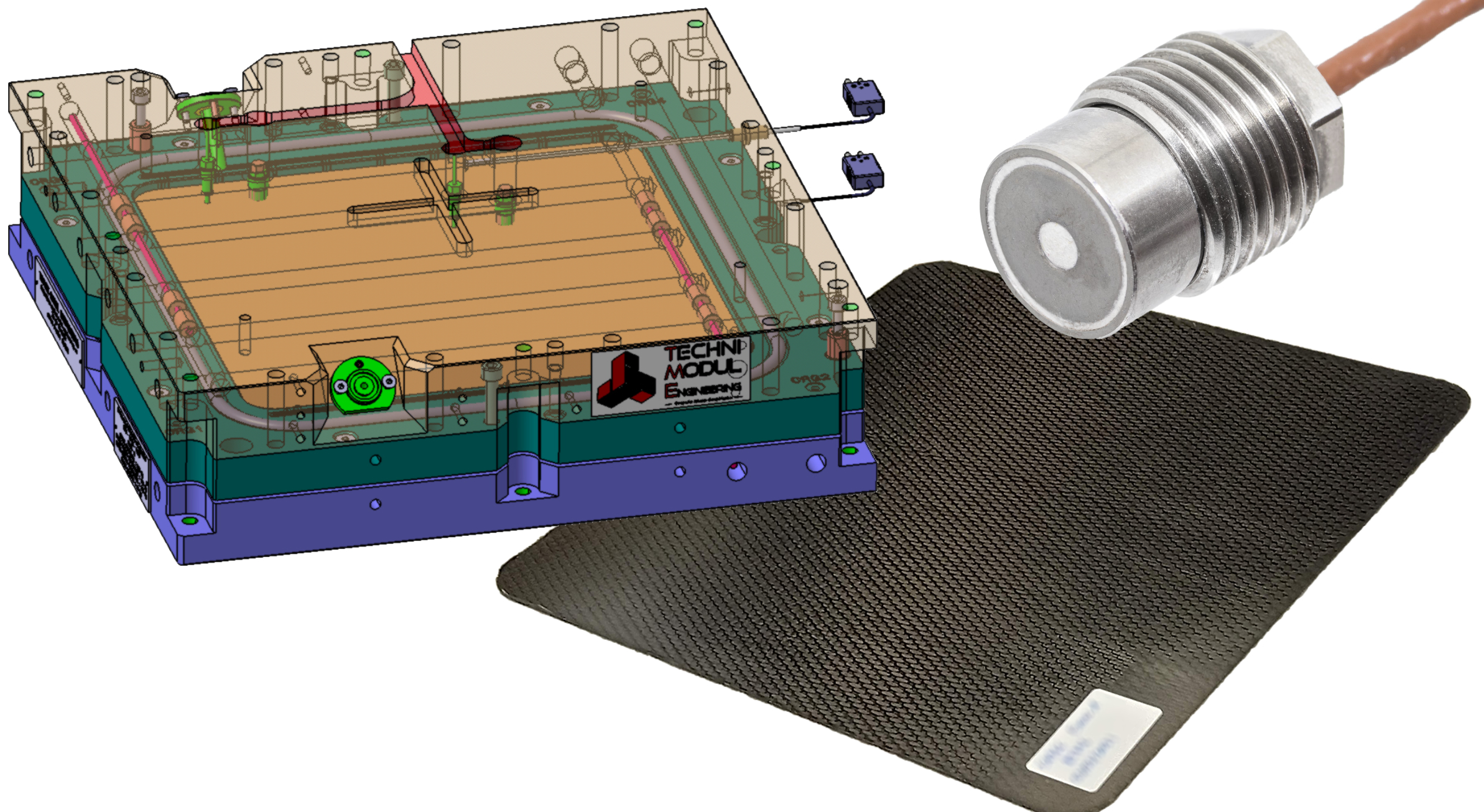
Resultados de la prueba INNOTOOL 4.0
Las pruebas que TME realizó utilizando su herramienta de placa modificada con sensores TFX probaron dos resinas diferentes, HexFlow RTM 6 y PRISM EP 2400, así como la influencia del espesor de la pieza y el tiempo de curado general. “Los sensores proporcionaron buenas señales para monitorear el ciclo de curado”, dice Cara. “Luego, el equipo analizó las curvas de curado y mostró que el tiempo de curado para RTM 6 podría reducirse en al menos 30 minutos a partir del curado de dos horas prescrito”.
Esto se puede ver en la siguiente curva, donde t =0 horas es el inicio de la inyección. Tenga en cuenta que el tiempo de curado comienza cuando la temperatura alcanza los 180 ° C y el final del curado corresponde al 99% del nivel de curado relativo (consulte el eje vertical a la derecha). El final del curado también coincide con la estabilización del flujo de calor sin procesar.
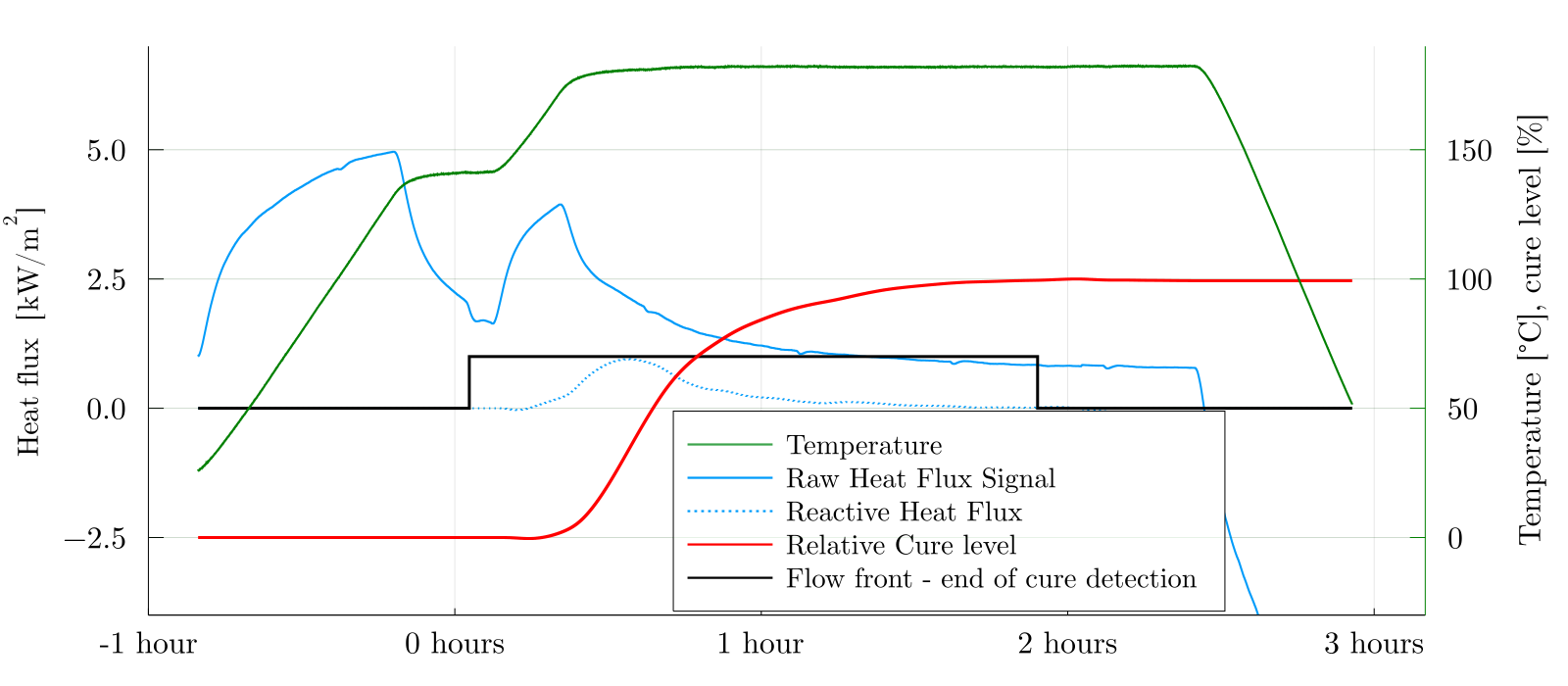
Esto se verificó mediante mediciones del estado de curado de piezas demolidas mediante análisis mecánico dinámico (DMA), una técnica de laboratorio alternativa a DSC que mide la temperatura de transición vítrea (T g ) para compuestos. “Los resultados de DMA confirmaron que para la resina RTM 6, el T g permanece sin cambios después de 90 minutos de curado a 180 ° C ”, agrega.
También se investigó el efecto del espesor. “Las primeras placas de CFRP probadas por TME en sus pruebas de demostración de sensores tenían menos de 2 milímetros de espesor”, señala Cara. “Estas planchas también tenían un alto volumen de fibra (50-60%) y un ciclo de curado lento para evitar la exotermia y problemas potenciales con el estrés térmico y la calidad de la pieza. Todo esto es muy normal para las piezas aeroespaciales, pero significa que hay muy poca resina y, por lo tanto, la cantidad de flujo de calor liberado por la reacción de la resina fue pequeña. Así que estábamos, en efecto, buscando la aguja del flujo de calor debido al curado de la resina dentro de un océano de calentamiento de la herramienta y la pieza ”.
En otras palabras, como explica Cara, “la mayoría de los ciclos de curado de RTM aeroespaciales implican inyectar resina a una temperatura y luego aumentar para curar a una segunda temperatura más alta. Por lo tanto, cuando termina la inyección, calienta la herramienta a la temperatura de curado, lo que genera un gran flujo de calor en todo el sistema ". Sin embargo, al igual que con las pruebas DSC, la clave para monitorear el curado con sensores de flujo de calor es medir el calor liberado durante la polimerización / curado y mostrar esas medidas en una curva de flujo de calor frente a la temperatura en el sistema de moldeo y el tiempo. "Entonces, inventamos un método que nos ayuda a restar la línea base de calentamiento del molde y la conducción de ese calor a la pieza, de modo que sea posible identificar el flujo de calor de la reacción de la resina".
Por lo tanto, a pesar de que las condiciones del proceso en las placas delgadas iniciales fueron muy desafiantes, dice Cara, “todavía podíamos ver el flujo de calor de la reacción de la resina. Sin embargo, al fabricar también piezas más gruesas, pudimos ver exactamente la diferencia en los niveles de flujo de calor de acuerdo con el espesor de la pieza y esto validó nuestro control de curado en las piezas delgadas ”. Tenga en cuenta que la curva anterior (que también se muestra en la foto de apertura) se obtuvo usando resina RTM 6 en una placa de 3,2 milímetros de espesor.
Los resultados de la detección del frente de flujo de resina, sin embargo, fueron más problemáticos. “Para el sensor cerca de la salida, pudimos ver el flujo muy bien, pero no para el sensor cerca del centro, donde la resina llegó muy tarde”, dice Cara. “La detección del frente de flujo con sensores de flujo de calor requiere que el flujo de resina produzca un cambio en el campo térmico local. Esto ocurre cuando la resina no está a la misma temperatura que la preforma ”. Señala que ΔT superior a 0,1 ° C es suficiente para la detección. “Sin embargo, con las pruebas de placas delgadas de CFRP, la temperatura fue muy uniforme en el molde y la resina llegó muy lentamente. Por lo tanto, el contraste térmico no fue suficiente para detectar la llegada de resina frente al ruido térmico en el sistema general. Sin embargo, la llegada de la resina a la salida fue más rápida debido a los canales [huecos entre la preforma y el borde del molde, consulte “Fabricación de las piezas de geometría compleja de RAPM”] que ayuda a crear un contraste térmico más grande que fue más fácil de detectar y monitorear. ”
Cara sugiere que esta supervisión del frente del flujo de resina podría mejorarse con nuevos sensores activos que TFX ha desarrollado, que utilizan una capacidad de calentamiento integrada dentro del sensor. “Esto permite que los sensores ayuden a proporcionar el contraste térmico necesario en piezas y procesos donde es intrínsecamente difícil”, explica.
Ampliación de la capacidad de control de procesos compuestos
“Estamos contentos con el trabajo que hemos completado hasta ahora”, dice Torres, “pero este es solo un primer paso. El objetivo es utilizar estos sensores de flujo de calor para gestionar el procesamiento de compuestos en entornos de producción ". Esto es posible, dice Cara, enviando automáticamente una señal desde el sistema de sensores al equipo de inyección en función de la llegada de la resina y a la prensa en función de una pendiente cero en la curva de curado. Torres agrega que TME tiene sistemas de control de procesos para la máquina de inyección y la prensa RTM que manejan la temperatura y la presión. "El siguiente paso", dice, "es integrar los sensores TFX en estos sistemas de control y administrar el proceso general desde una computadora portátil". Cara señala que los sensores TFX y la adquisición de datos también funcionan con sensores de presión (por ejemplo, Kistler, Winterthur, Suiza) para ayudar en este control general del proceso, y su compañía está desarrollando un sensor que medirá el flujo de calor, la temperatura y presión en un solo dispositivo integrado.
Pero, ¿es asequible este control de procesos? Cara dice que la inversión inicial de $ 10-30,000 para el sistema de monitoreo generalmente logra un retorno en la fase de desarrollo, reduciendo el ensayo y error a través de un mejor proceso y comprensión de las piezas. "Luego, el sistema continúa proporcionando ahorros durante la producción, reduciendo el tiempo del ciclo, asegurando la repetibilidad y proporcionando una detección temprana de desviaciones o no conformidades".
En GKN Fokker, Vergouwen cree que una vez que se demuestre la capacidad de reducir el tiempo de ciclo y mejorar el costo, “entonces es posible imaginar compuestos no solo en el tipo de componente del tren de aterrizaje demostrado en los proyectos INNOTOOL 4.0 y HECOLAG, sino en todo tipo de partes. Eso abriría nuestro espacio de diseño y nos permitiría ampliar aún más los límites del tren de aterrizaje liviano ". Besson ve una aplicación aún más amplia:"Este tipo de control de proceso se puede desarrollar para todo tipo de moldes y piezas compuestas".
Resina
- Tipos de sensores con sus diagramas de circuito
- ams iluminará la Sensors Expo 2019 con demostraciones innovadoras
- Mapeo del flujo de temperatura del hogar con sensores baratos
- Mide temperaturas con un sensor DS18B20 de 1 cable y Raspberry Pi
- Control de un efecto con sensores reales
- Lectura de sensores analógicos con un pin GPIO
- Lectura de sensores analógicos con Raspberry Pi y Zabbix Supervisor
- Controlador de riego IOT Win10 con sensores de humedad
- Mejora del monitoreo de la contaminación del aire con sensores de IoT
- Simplificación de la fabricación de sensores con compuestos adhesivos
- Apósitos inteligentes para heridas con sensores de cicatrización integrados