Stratasys y Champion Motorsport se unen para probar la tecnología central impresa en 3D
El 27 de junio, un automóvil 911 Porsche GT2 RS Clubsport modificado de Champion Motorsport (Pompano Beach, Florida, EE. UU.) Terminó primero en la División Time Attack 1 de la 99 th Pikes Peak International Hill Climb en Colorado Springs, Colorado, EE. UU.
Uno de los secretos del éxito del equipo fueron las estructuras aerodinámicas del automóvil:las alas, las aletas de la parte inferior de la carrocería, el difusor y otros componentes del vehículo que mueven el aire de manera más eficiente alrededor del vehículo mientras se conduce. Muchos de estos componentes fueron impresos en 3D por el socio Stratasys (Rehovet, Israel y Eden Prairie, Minnesota, EE. UU.), Incluida la primera aplicación exitosa para una nueva tecnología de núcleo sándwich envuelto en fibra de carbono sin herramientas.
Prueba de herramientas y tecnologías centrales impresas en 3D
Champion Motorsport ha sido cliente de Stratasys durante varios años, "pero la asociación se ha convertido en algo más que la típica relación entre proveedor y cliente", dice Allen Kreemer, ingeniero senior de aplicaciones estratégicas de Stratasys. Por ejemplo, Stratasys y Champion trabajaron juntos anteriormente para probar una nueva técnica que Stratasys había desarrollado para herramientas solubles de impresión 3D. Con esta tecnología, se imprime un núcleo de plástico soluble conformado para un conducto u otra pieza en forma de tubo y luego se envuelve con preimpregnado de fibra de carbono. Usando un tanque de remoción de soporte soluble, las herramientas impresas se disuelven, dejando un conducto compuesto hueco, terminado y sin costuras.
"Ese fue realmente el comienzo de nuestra asociación con Champion Motorsport, donde trabajamos juntos para crear este conducto de fibra de carbono sin costuras muy complicado de una manera no tradicional, sin límites como en el mecanizado o moldeado CNC", dice Patrick Carey, vicepresidente senior. - América, productos y soluciones en Stratasys.
En 2019, las empresas decidieron asociarse en un proyecto para probar una nueva iteración de la misma tecnología:núcleo envuelto en fibra de carbono impreso en 3D que no se disuelve en agua, que en cambio es un núcleo estructural para la pieza terminada o el prototipo.
Kreemer explica que para los componentes tipo sándwich, trabajar y dar forma a los materiales del núcleo, ya sea en forma de panal de aluminio flexible, espuma estructural rígida u otra cosa, puede ser difícil y costoso, ya que requiere conformar o mecanizar y luego moldear con las pieles compuestas de fibra de carbono en un molde específico. Stratasys imprime un núcleo rígido en forma de panal con plástico de alta temperatura SABIC (Riyadh, Arabia Saudita) Ultem 1010. "Imprimimos la forma exacta para que quepa en el automóvil, luego simplemente envolvemos con fibra de carbono, embolsamos y curamos, sin usar un molde", dice Kreemer. "Comenzamos con los núcleos solubles, que nuestros clientes todavía usan, y ahora nos hemos trasladado a estos núcleos sándwich, que tendrán amplias aplicaciones en la industria aeroespacial y automotriz".
"Lo llamamos 'sin herramientas' y esa es realmente la clave", agrega Carey. "Hemos creado esta aplicación para omitir todo el proceso de construcción del molde y luego colocarlo en el molde". Señala que la eliminación de las herramientas también permite que la forma se cambie fácilmente según sea necesario.
Aerodinámica galardonada impresa en 3D
Para el proyecto Champion Motorsport, se incluyeron tres tecnologías diferentes en las 16 partes aerodinámicas totales que Stratasys construyó para la creación de prototipos o la instalación final en el vehículo de carrera, explica Carey. "Imprimimos los núcleos Ultem 1010 [envueltos en fibra de carbono], imprimimos en 3D algunas piezas con nailon 12 relleno de fibra de carbono e imprimimos piezas con nailon 6 cuando se requería flexibilidad y resistencia al impacto".
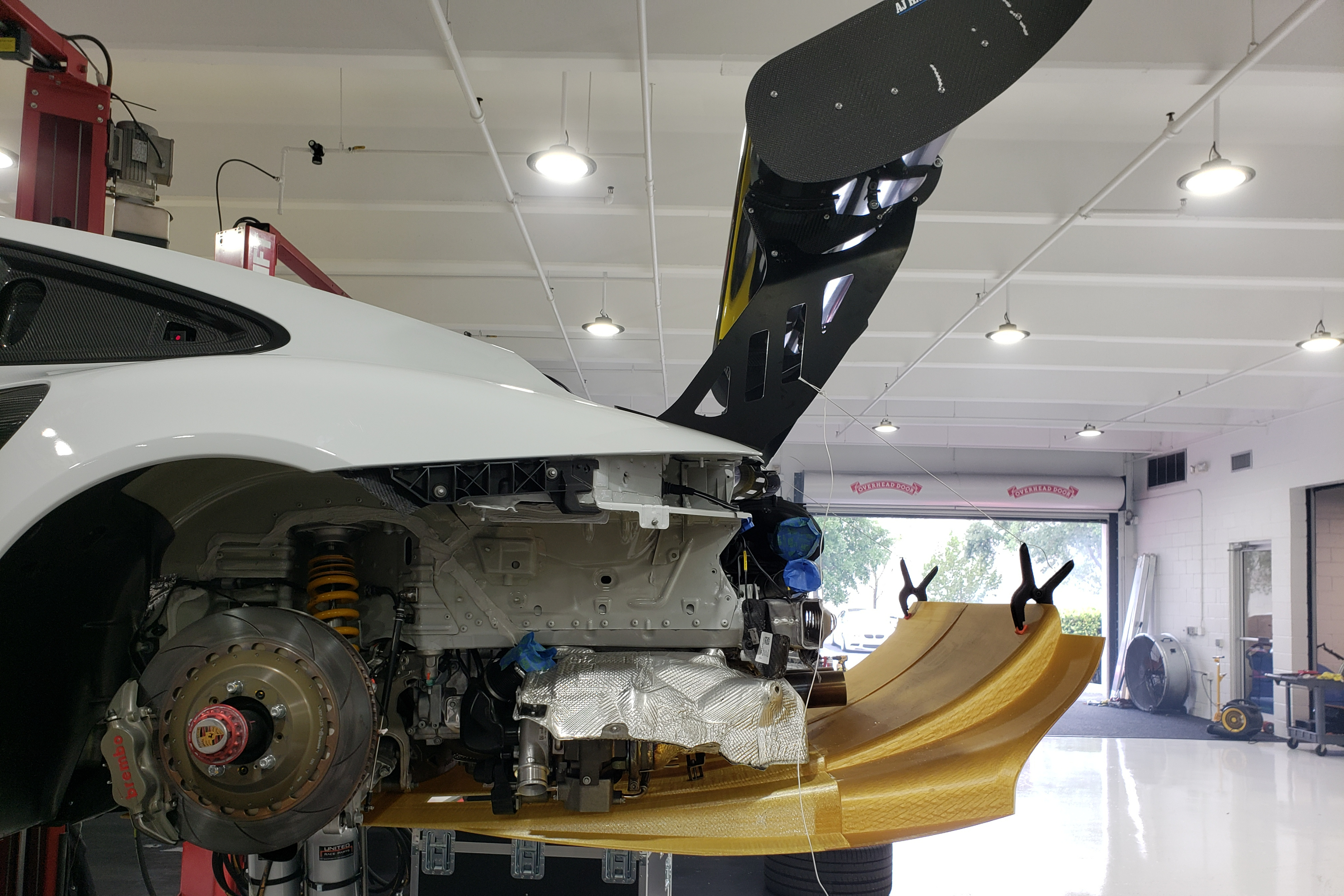
La parte más grande fue una pieza prototipo de difusor trasero de 7 pies de largo y 5 pies de ancho que se construyó para probar el diseño de la pieza final. Se imprimió en siete piezas en una impresora Stratasys de modelado por deposición fundida (FDM) F900 utilizando polímero de polieterimida (PEI) Ultem 1010, unido, envuelto en fibra de carbono preimpregnado, embolsado y curado en horno. El tiempo de respuesta de la pieza fue de aproximadamente cinco días para la impresión y poco más de 24 horas para la colocación y el curado:"Fue extremadamente rápido, y lo que necesitábamos en ese momento", señala Chris Lyew, ingeniero mecánico de Champion Motorsport.
Debido a la incertidumbre de si se podrían realizar eventos en persona este verano debido a COVID-19, “el proyecto se puso en línea en el último minuto y era necesario abordar muchos sistemas al mismo tiempo”, explica Lyew. "La aerodinámica es uno de ellos, y normalmente es un proceso que requiere mucho tiempo" de diseño, prueba e iteración de los componentes, dice. Los métodos convencionales requerirían la creación de herramientas, la colocación manual en el molde y el corte y ajuste del núcleo. "Sin este proceso, no podríamos haber cumplido con nuestras fechas objetivo para probar el auto en la pista", dice Lyew.
El divisor delantero del automóvil también se diseñó y probó de manera similar. Para las piezas que eran prototipos, las piezas de producción finales se hicieron con herramientas tradicionales, pero la pieza prototipo se utilizó como patrón para probar diferentes iteraciones. Carey señala:“Con un proceso sin herramientas podemos iterar más rápido, probarlo, luego iterar más rápido, probarlo. Con las herramientas tradicionales, nunca podría iterar, simplemente crea una y está atascado con ella. Aquí, podemos hacer una pieza real, probarla y aprender de ella ".
Stratasys también produjo varias piezas de producción más pequeñas. Por ejemplo, las aletas a ambos lados del parachoques delantero del automóvil se imprimieron con nailon 12 relleno de fibra de carbono al 35%, los faldones laterales del vehículo también se imprimieron en Ultem 1010 con un relleno interno de panal y luego se envolvieron en fibra de carbono.
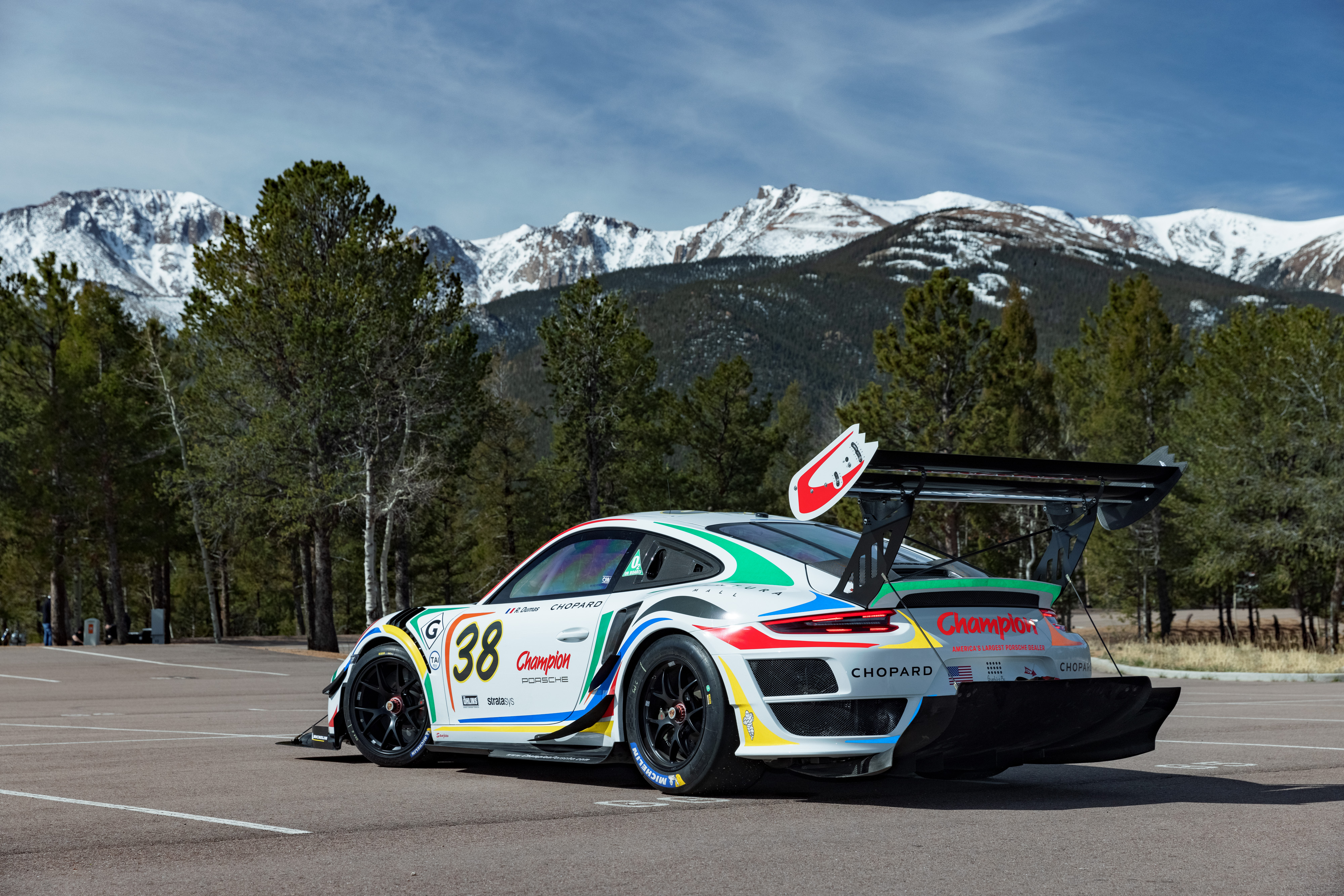
Muchos de los "trazos" aerodinámicos del automóvil, pequeñas piezas en forma de aletas que se atornillan al exterior del vehículo en puntos estratégicos para ayudar a controlar el flujo de aire alrededor del vehículo, también se imprimieron con nailon 12 relleno de fibra de carbono o nailon 6 no reforzado. Las piezas están diseñadas para ser fácilmente rediseñadas o reemplazadas según sea necesario debido a daños o desgaste. “En Pikes Peak, hay bastantes características de terreno accidentado que podrían causar daños, por lo que la capacidad de reemplazar [las tracas] fácilmente fue clave para nosotros”, agrega Lyew. También se imprimieron y entregaron varios juegos de repuesto para reemplazarlos fácilmente durante la carrera según sea necesario.
Más allá de Pikes Peak
Pikes Peak terminó siendo una carrera ideal para probar esta tecnología, dice Kreemer, debido al entorno único específico de este evento, que se lleva a cabo a 14.000 pies de altitud en el punto más alto. “Todos los autos de carrera usan fuerza aerodinámica para empujar el auto a la pista y ganar tracción, pero estos autos en particular en Pikes Peak son diferentes a cualquier otra forma de deporte de motor en el mundo, porque necesitan efectos aerodinámicos realmente exagerados para mantener los autos en la pista [ a esa altitud] ". El resultado son alas más grandes y otros componentes aerodinámicos que los que se utilizarían en cualquier otro tipo de coche de carreras.
En el futuro, Stratasys planea presentar su tecnología de núcleo impreso sin herramientas a otras compañías de carreras para piezas aerodinámicas similares. Carey dice que hay muchas otras aplicaciones potenciales en el futuro en partes automotrices, marinas recreativas o incluso aeroespaciales interiores de bajo volumen. “Creemos que podemos agregar valor a cualquier aplicación que requiera iteración o un diseño personalizado”, dice.
Resina
- Materiales:Tecnología de producción de nido de abeja ligera en la K 2019
- Evonik establece un nuevo centro de tecnología de impresión 3D en los EE. UU.
- Nueva forma de material impreso en 3D destinado a diseños de automóviles más ligeros y seguros y más
- Cómo garantizar la seguridad de la tecnología ADAS de vanguardia
- Tecnología de producción de paneles de nido de abeja termoplásticos EconCore
- Compuesto + metal:Tecnología híbrida de perfil hueco
- Un jugador altamente especializado en un equipo de clase mundial
- Tecnología de movimiento lineal
- Arno Strotgen
- placa de circuito impreso 101
- ¿Qué es la tecnología agrícola?