Diseño para la fabricación automatizada de composites de aeroestructuras de bajo volumen
La fabricación de aeroestructuras compuestas para aviones comerciales abarca más de 50 años y ha progresado constantemente desde piezas más pequeñas hasta estructuras primarias muy grandes (fuselaje, alas, empenaje, motores) desarrolladas a principios de la década de 2000 para el Boeing 787 y el Airbus A350. La gran mayoría de esta evolución dependió del uso de preimpregnados epoxi / fibra de carbono curados en autoclave, inicialmente colocados a mano y luego, eventualmente, mediante colocación automatizada de fibras (AFP), colocación automática de cintas (ATL) y otros procesos basados en máquinas.
Estas tecnologías de materiales y procesos (M&P) eran adecuadas para los 787 y A350 de cuerpo ancho que, antes de la pandemia, tenían tasas de construcción de 10 a 15 por mes. Sin embargo, a medida que Boeing y Airbus miran hacia el futuro y consideran la aplicación de materiales compuestos en estructuras primarias de aviones de pasillo único que se espera tengan tasas de construcción de 60-100 por mes, el diseño y M&P favorecerán las tasas altas, fuera de -autoclave (OOA), procesos altamente automatizados. Estos procesos incluyen, entre otros, moldeo por transferencia de resina (RTM), moldeo por compresión e infusión de resina líquida.
Pero incluso si la fabricación de alta tasa dominará el sector aeroespacial comercial, la fabricación de aeroestructuras compuestas para tasa baja Las aeronaves, incluidas las aeronaves regionales y los programas de jets ejecutivos, no solo persistirán, sino que pueden y deben beneficiarse de algunas de las mismas innovaciones de costo, diseño y M&P que se implementarán en programas de alta tasa.
Con todo esto en mente, el programa europeo Clean Sky 2 lanzó OPTICOMS - Opti Com mized posite S Estructuras para Aeronaves Pequeñas. OPTICOMS es un consorcio liderado por el fabricante aeroespacial Israel Aerospace Industries (IAI, Lod, Israel) con socios que suministran tecnologías, materiales, software, herramientas y maquinaria de automatización de innovación. El objetivo de OPTICOMS es evaluar un diseño de caja de ala de producción de baja tasa que presenta fabricación automatizada, estructuras integradas, curado OOA, unión estructural grande, herramientas de ensamblaje y fabricación innovadoras, monitoreo de la salud estructural de las líneas de unión y pruebas virtuales.
Arnold Nathan, director de I + D del grupo de aviación en IAI y gerente de OPTICOMS, dice:“Cada vez que intentamos que la automatización se convierta en una [discusión] sobre la fabricación de compuestos, a menudo escuchamos a nuestros clientes decir:'La automatización es buena, pero solo cuando tiene un gran volumen de producción. ”OPTICOMS se creó para averiguar si puede justificar la automatización cuando no tener producción de gran volumen. ¿Puede la automatización de la fabricación de compuestos ser competitiva y rentable para volúmenes bajos? ”
Diseño de ala
OPTICOMS nació de una solicitud de Clean Sky 2 emitida por el fabricante italiano de aviones comerciales Piaggio Aerospace (Génova) para el desarrollo de un ala alternativa totalmente compuesta para su P180 Avanti turbohélice gemelo empresarial de nueve pasajeros. La caja del ala mide 6,8 metros de largo, 0,71 metros de ancho en la raíz y 0,28 metros de ancho en la punta. Piaggio, dice Nathan, estaba ansioso por evaluar una alternativa a la caja de ala heredada totalmente metálica, una alternativa con las mismas dimensiones, pero que ofrece un peso reducido (20%). Además, el costo debe reducirse en un 20-30% en comparación con la fabricación convencional de cajas de ala compuestas. IAI y sus socios ganaron el contrato y comenzaron a trabajar con Piaggio en 2016.
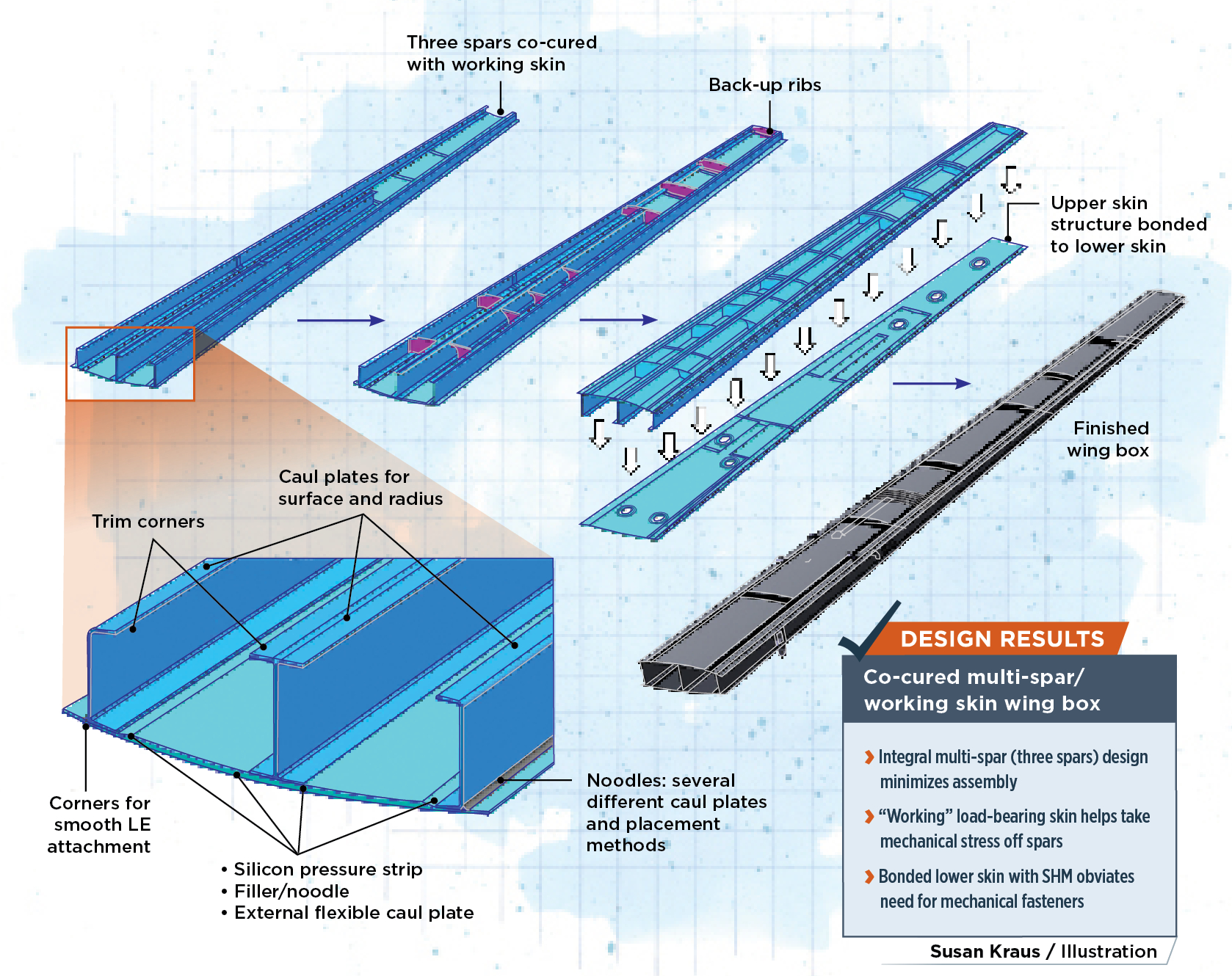
OPTICOMS es un programa de varias partes diseñado para realizar una serie de estudios comerciales muy detallados y minuciosamente realizados para evaluar y determinar el diseño óptimo del ala, la combinación de materiales y el proceso de fabricación OOA para la fabricación automatizada de una caja de ala totalmente compuesta de bajo volumen.
IAI y OPTICOMS, dice Nathan, decidieron desde el principio que se centrarían y evaluarían el uso de tres procesos de fabricación proporcionados por tres socios:Recogida y colocación robótica automatizada de telas secas y preimpregnadas, suministrada por Techni-Modul Engineering (TME, Coudes, Francia); colocación automatizada de fibras (AFP) de estopas secas y preimpregnadas, suministradas por Coriolis Composites (Queven, Francia); y tecnología de colocación automática de material seco (ADMP), suministrada por Danobat (Elgoibar, España). La selección de estas tecnologías y socios sería fundamental para guiar al IAI a lo largo de sus estudios comerciales de variantes múltiples.
Resultados de diseño
- El diseño integral de varios largueros (tres largueros) minimiza el montaje
- La piel que soporta la carga "de trabajo" ayuda a eliminar la tensión mecánica de los largueros
- La piel inferior adherida con SHM evita la necesidad de sujetadores mecánicos
El primer paso de este estudio comercial fue la evaluación del diseño. Este esfuerzo fue dirigido en IAI por Adam Sawday, ingeniero de diseño estructural para tecnologías avanzadas. Sawday dice que él y el IAI adoptaron un enfoque de hoja limpia para el diseño del ala, estudiando más de 18 conceptos en una variedad de arquitecturas. Los diseños se clasificaron rápidamente en una de dos categorías. El primero emplea un revestimiento "de trabajo" en el que el revestimiento de la caja del ala se convierte en una estructura de soporte de carga. El segundo emplea pieles que no funcionan con tapas de larguero cargadas. Dentro de estas categorías, los diseños incluyen un concepto tradicional con nervaduras, largueros y dos largueros o, alternativamente, el uso de tres largueros, llamados multi-largueros, sin costillas ni largueros. Varios conceptos también consideraron el uso de una construcción de panel sándwich que produce una piel semi-funcional.
“Nuestro lema era reducir el esfuerzo de fabricación y reducir el esfuerzo de montaje”, dice Sawday. "Y creemos que si puede desarrollar una estructura más eficiente que sea más integral, entonces obtendrá una estructura más barata y liviana".
Sawday dice que los diseños se midieron en función de una serie de métricas para evaluar su capacidad para cumplir con los objetivos de costo y peso del programa. Estas métricas incluyen:costos de materiales, complejidad del diseño, costos de fabricación de componentes, costos de ensamblaje, costos de pruebas no destructivas (NDT), costos de herramientas y jigging, peso, resistencia, nivel de preparación de la tecnología (TRL), consideraciones ecológicas, perfil de riesgo, solidez y fiabilidad. De estos, los criterios más ponderados fueron el peso, los costos de fabricación y montaje, la complejidad del diseño, el TRL y el perfil de riesgo.
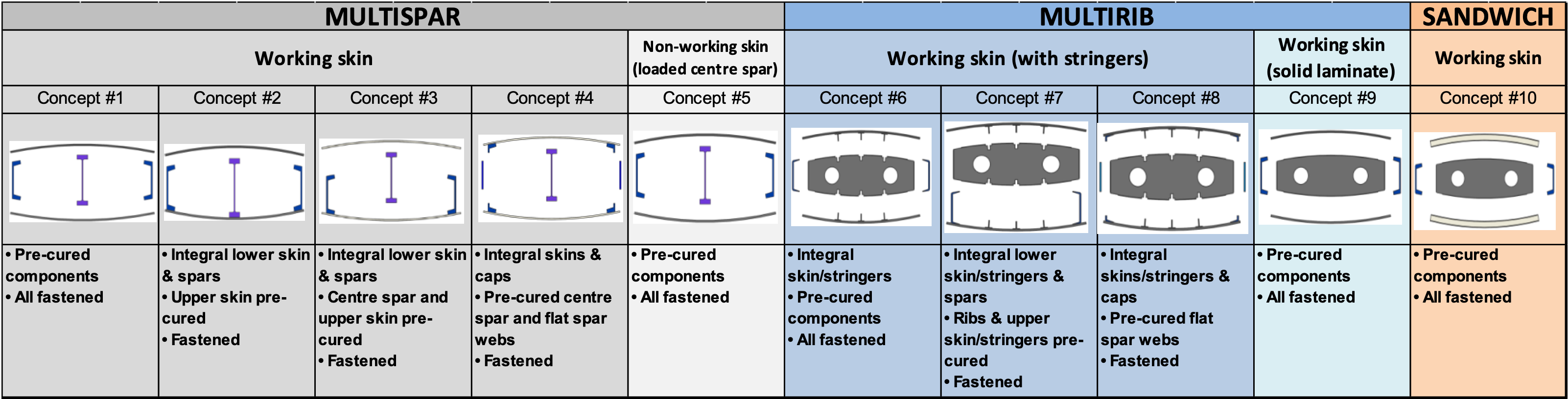
Selección hacia abajo para el diseño final
Los datos de esta evaluación ayudaron al IAI a reducir los conceptos de diseño a 10 finalistas. Cuatro eran piel de trabajo / multi-mástil, uno era piel de multi-mástil / no funcional con mástiles cargados, cuatro eran piel de varias costillas / trabajo con largueros, uno era de múltiples costillas / revestimiento de trabajo sin largueros, y uno era sándwich estructura / piel de trabajo sin largueros. Cada diseño ofrecía varias combinaciones de curado previo, curado conjunto, unión o sujeción mecánica.
Llegar al diseño final implicó otra ronda de estudios comerciales utilizando muchos de los mismos criterios que en el primer estudio. A cada diseño se le dio un valor comercial, basado en qué tan bien cumplía con los criterios. "Teníamos esta gran tabla de compensaciones y cada opción de diseño tenía un valor, y esto nos ayudó a ver la opción más sólida", dice Sawday.
Hubo un diseño, desde el principio, que funcionó consistentemente bien en los estudios comerciales y parecía probable que se destacara, señala Sawday. Y lo hizo. Apodado internamente como multi-spar / piel de trabajo # 2, presenta una piel superior altamente integrada y co-curada y tres largueros. Luego, estos se unen a una piel inferior que tiene paneles de acceso. Ubicada selectivamente entre los largueros hay una serie de costillas de "respaldo", diseñadas para soportar la piel, que soporta la mayoría de las cargas de flexión.
“Las estructuras más favorables que desarrollamos”, dice Sawday, “fueron aquellas con largueros múltiples, donde la piel se vuelve portadora. Los largueros, entonces, se convierten en estructuras más simples y delgadas, y no tan pesadas como lo son en los diseños tradicionales de alas compuestas. Pensamos que si podíamos hacer estos largueros muy simples, con una sección transversal constante, eso nos ahorraría muchos dolores de cabeza y muchos desperdicios ".
Sawday dice que el diseño de revestimiento de trabajo / multi-mástil integral adherido mostró una promesa particular por sus costos de ensamblaje reducidos, bajo peso, facilidad de automatización y bajo recuento general de piezas. Sin embargo, la pregunta seguía siendo:¿qué materiales y qué procesos de fabricación serían los más adecuados para dar vida a este diseño?
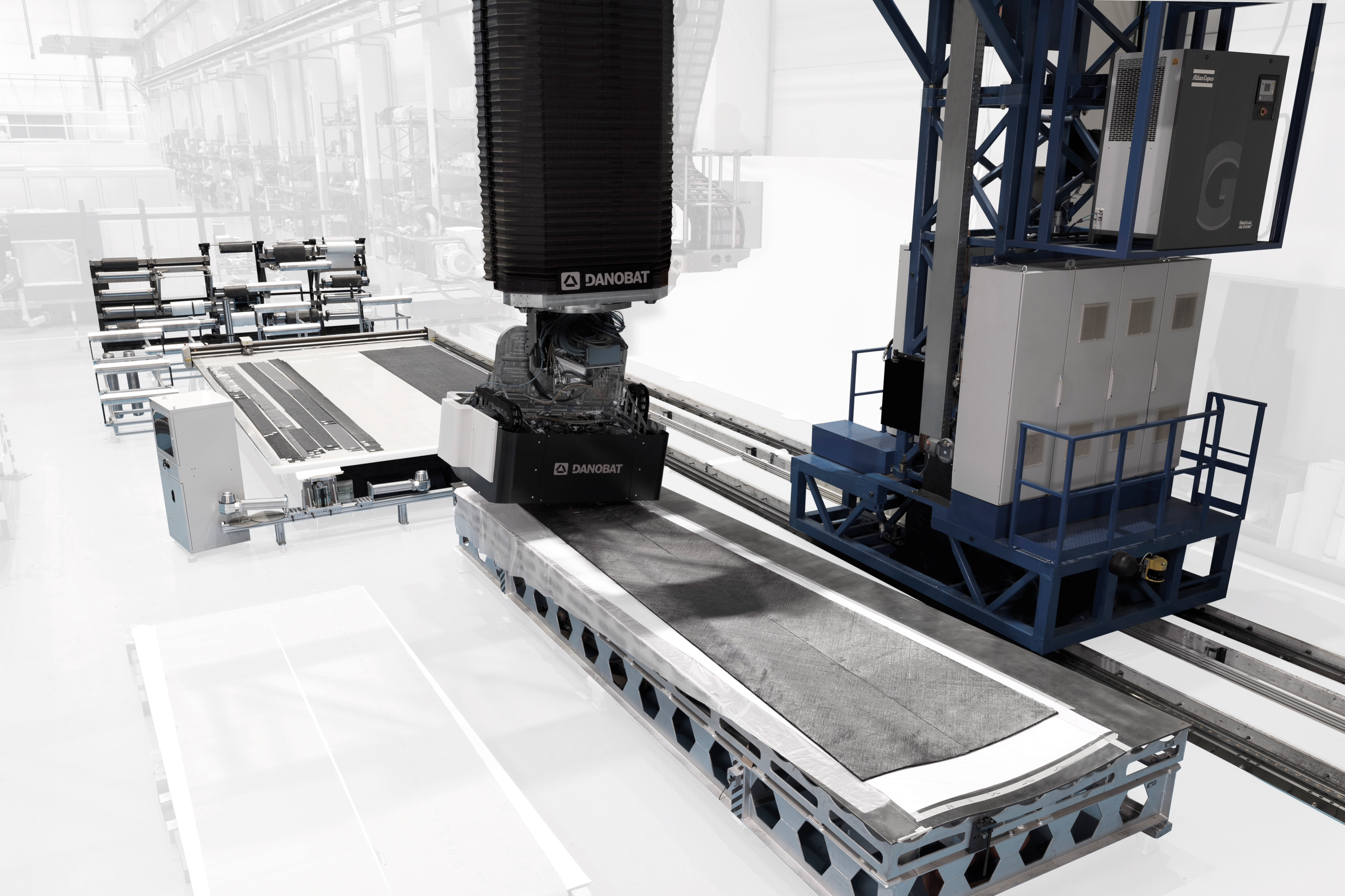
Estudios comerciales de M&P
Primero fueron los estudios de comercio de materiales. Estos fueron realizados en el IAI por Yaniv Yurovitch, ingeniero de materiales compuestos. Él dice que OPTICOMS comenzó a evaluar preimpregnados de fibra de carbono OOA, fibras de carbono secas (cintas y telas) y resinas basándose en las recomendaciones de Piaggio, IAI y socios tecnológicos. El resultado fue una lista de 35 materiales nuevos y calificados.
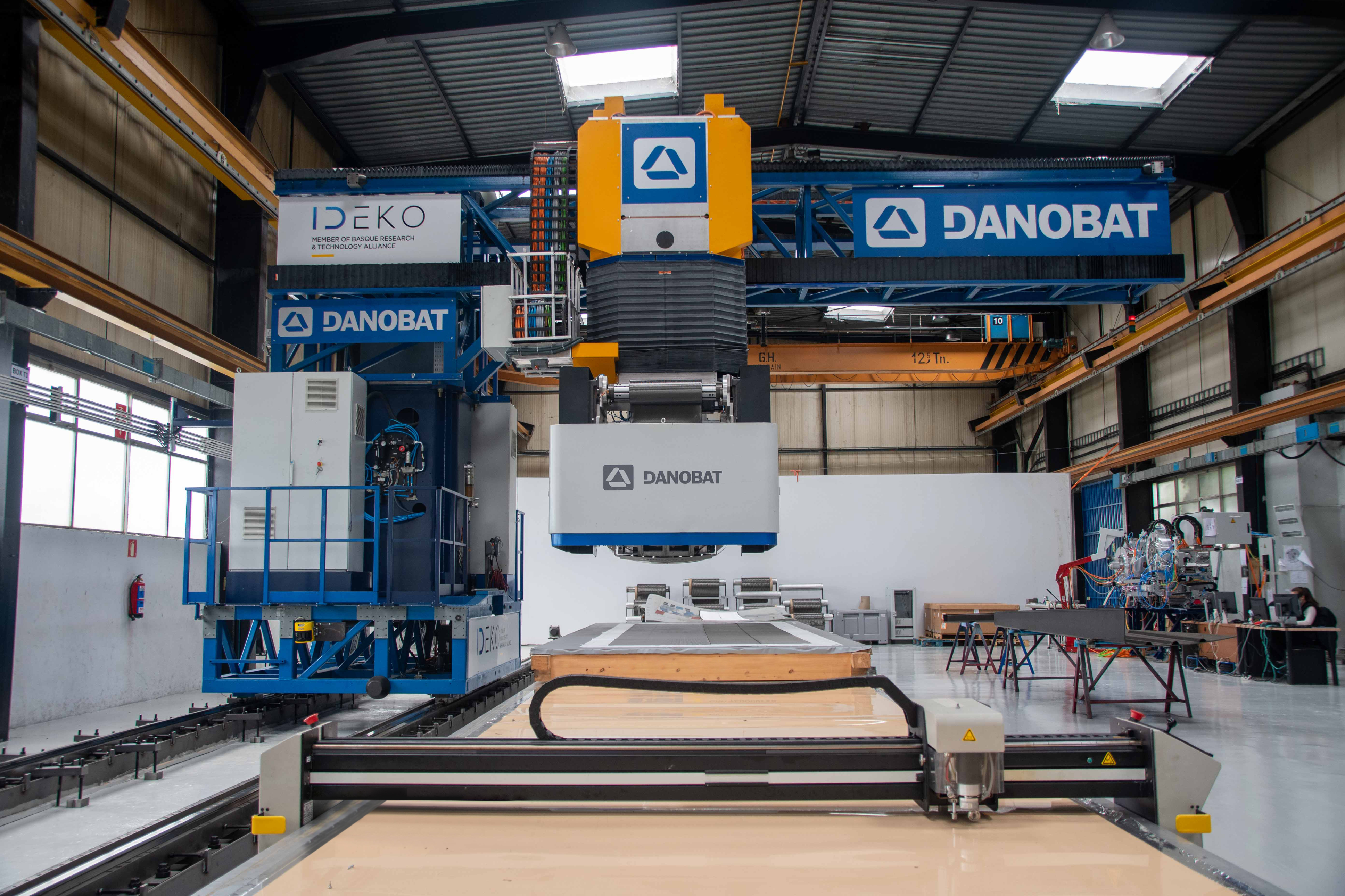
Este primer grupo de materiales se analizó luego en función de los parámetros más cruciales para el proyecto OPTICOMS:costo, temperatura de transición vítrea (T g ), viscosidad (para infusión o inyección) e idoneidad para tecnologías de laminado automatizadas. Esta evaluación redujo la lista de materiales de 35 a 20 preimpregnados, fibras secas y resinas.
Se solicitaron muestras de cada uno de estos 20 materiales; Luego, Yurovitch hizo cupones y realizó pruebas mecánicas como parte de la siguiente selección descendente. “Fue un paquete de trabajo realmente grande”, dice Yurovitch. "Nos permitió tomar más decisiones y seleccionar los tres materiales finales". Esas combinaciones de fibra / resina son:
- Toray Composites Materials America's (Tacoma, Wash., EE. UU.) 2510 preimpregnado de fibra de carbono / epoxi.
- Cintas UD de fibra de carbono HiTape de Hexcel (Stamford, Connecticut, EE. UU.), para usar con la resina epoxi HexFlow RTM6 de Hexcel.
- Tejido de fibra de carbono no rizado (NCF) suministrado por SAERTEX (Saerbeck, Alemania), para combinar mediante infusión con epoxi endurecido PRISM EP2400 de Solvay Composite Materials (Alpharetta, Ga., EE. UU.).
Evidentemente, esta lista favorece el uso de fibras secas, lo que a su vez favorece la infusión como proceso de fabricación. Nathan dice que esto se debe en parte al desafío de administrar la vida útil del preimpregnado en un entorno de bajo volumen. "Cuando se habla de producción de bajo volumen, realmente no desea cargar mucho preimpregnado y preocuparse por administrar la vida útil", dice. "La fibra seca no tiene ese problema".
Estos tres materiales también se combinaron con uno o más de los procesos de fabricación seleccionados para OPTICOMS:el preimpregnado Toray se combina con pick-and-place y AFP, el HiTape / RTM6 de Hexcel se combina con AFP, así como con pick and place, y SAERTEX NCF coincide con pick-and-place o ADMP.
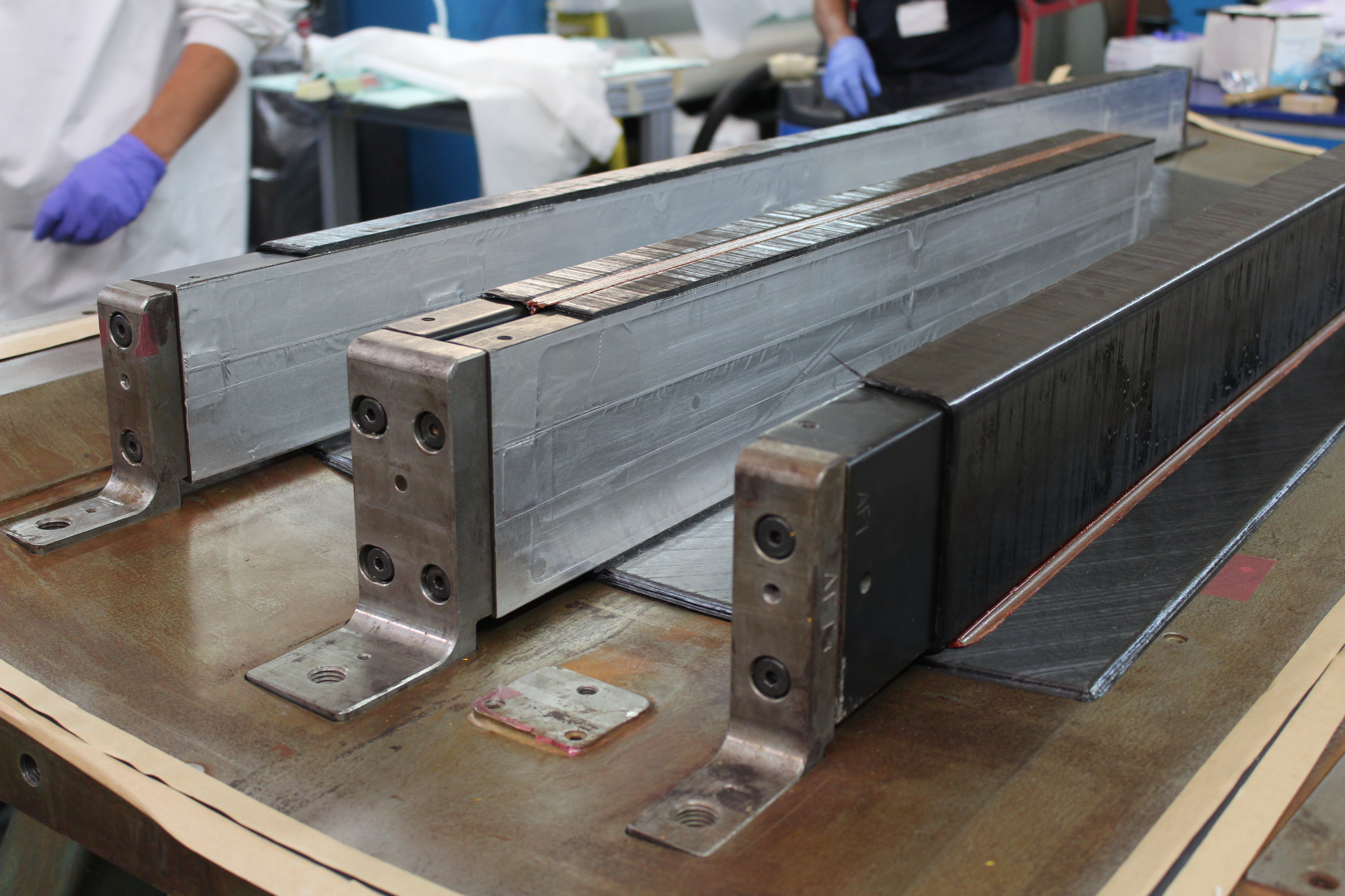
Los intercambios en torno a los procesos de fabricación automatizados, cuál es el más adecuado para qué tipo de pieza, todavía están siendo realizados por IAI y OPTICOMS. Sin embargo, los resultados preliminares, dice Nathan, definitivamente apuntan a las tecnologías en ciertas direcciones. Por ejemplo, la tecnología ADMP de Danobat, desarrollada originalmente para la colocación rápida de tejidos anchos en la fabricación de palas de aerogeneradores, ha demostrado ser igualmente eficaz en OPTICOMS. La tecnología ha madurado durante OPTICOMS y se ha mejorado su solidez y confiabilidad, pero sigue siendo una tecnología de laminado aeroespacial menos madura en comparación con AFP.
Por el contrario, AFP con el sistema Coriolis, con su amplia experiencia aeroespacial, es una tecnología madura y precisa, pero tiene tiempos de laminación más largos en comparación con ADMP y requiere una inspección relativamente frecuente para verificar anomalías. Coriolis ha logrado un progreso notable a lo largo del proyecto OPTICOMS con el desarrollo de la inspección en línea y en tiempo real de la bandeja para hacer frente a este desafío, dice Nathan. Finalmente, la tecnología pick-and-place de TME, diseñada para automatizar la transferencia de telas cortadas desde la mesa de corte al molde, parece ser más efectiva para piezas más pequeñas y discretas, como las costillas de respaldo en el multi-larguero / trabajo. diseño de piel.
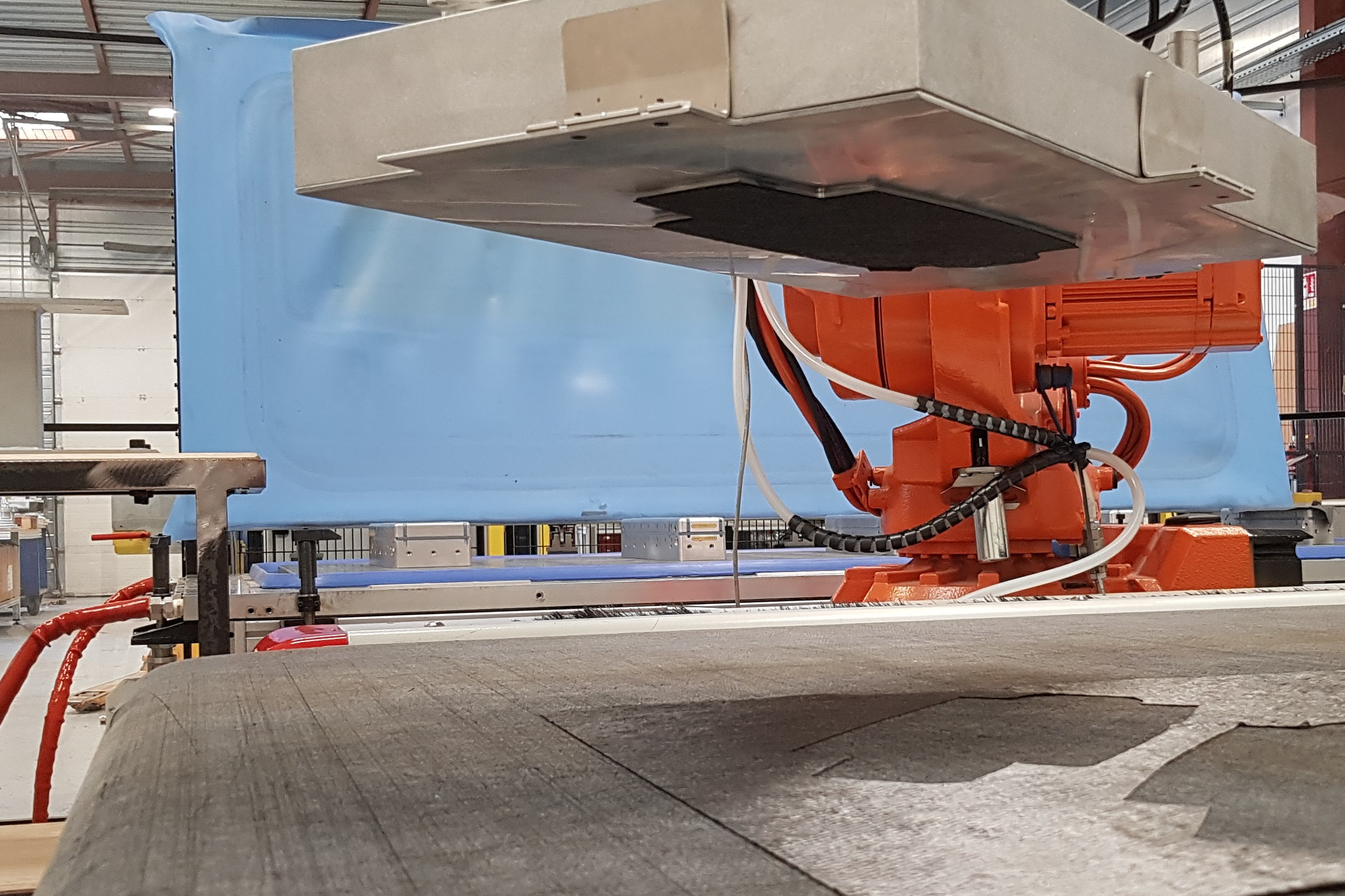
Pasos siguientes
OPTICOMS está en camino de cumplir con los objetivos de automatización, costos y ahorro de peso establecidos por el programa, dice Nathan, aunque todavía quedan varios meses de trabajo por hacer para evaluar los procesos de fabricación y las soluciones de ensamblaje.
“Este es un punto importante sobre OPTICOMS”, explica. “Tuvimos una sólida selección hacia abajo del diseño. Tuvimos una selección inferior del material. Tuvimos una selección a la baja de los procesos. Todo esto requiere tiempo y esfuerzo. Este es uno de los aspectos únicos del proyecto ”.
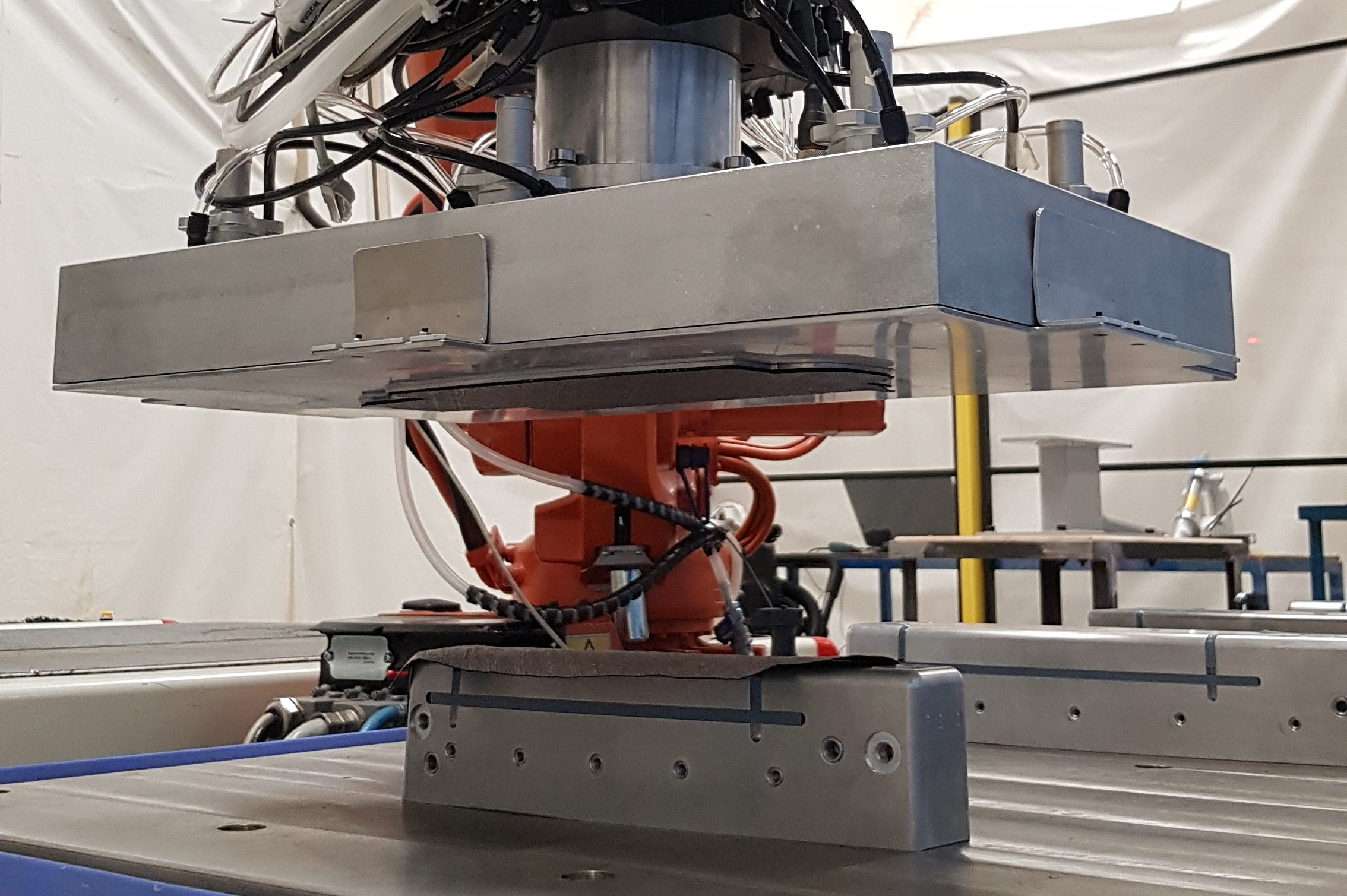
OPTICOMS inició tres convocatorias de propuestas (CFP) de tecnologías y hardware para respaldar, garantizar y mejorar los objetivos del proyecto. Las propuestas exitosas se convirtieron en proyectos Clean Sky 2, asociados y complementarios al Core Partner “madre” de OPTICOMS, todos trabajando juntos hacia un objetivo común.
El primer esfuerzo en este desarrollo es FITCoW, que tiene como objetivo desarrollar un novedoso sistema integral de herramientas de fibra de carbono para el curado conjunto de la piel de trabajo y tres largueros. La lista de objetivos de FITCoW es ambiciosa:50% de reducción en el costo de las piezas fabricadas, 30% de reducción del costo de herramientas (en comparación con la alternativa metálica), 20% de reducción del tiempo de fabricación en comparación con las alternativas de autoclave y OOA, 40% de reducción de desajuste de CTE en comparación con las herramientas Invar , 20% de reducción en el tiempo de calentamiento y enfriamiento y 40% de reducción del tiempo de inspección gracias a mejores capacidades de control dimensional.
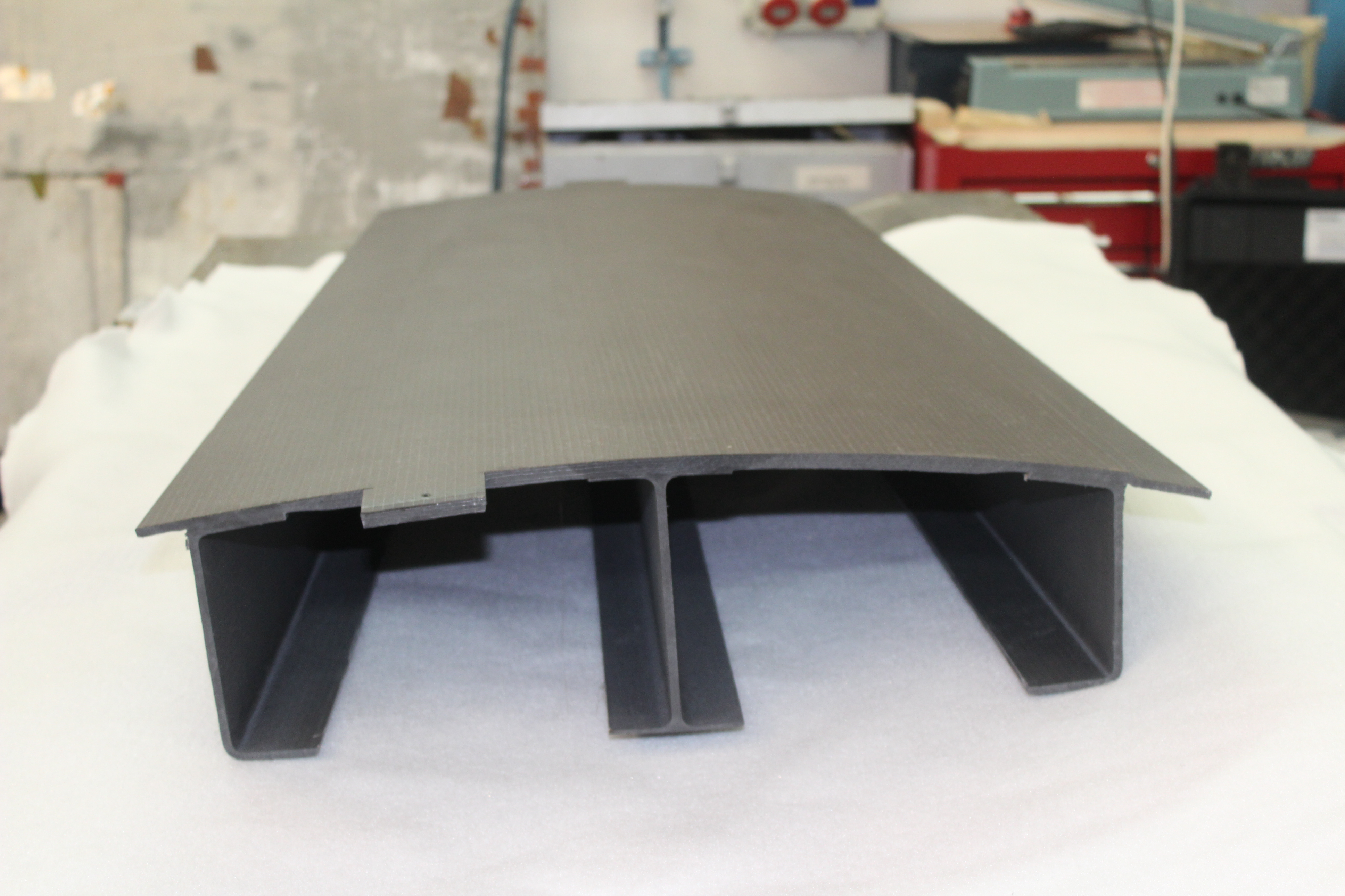
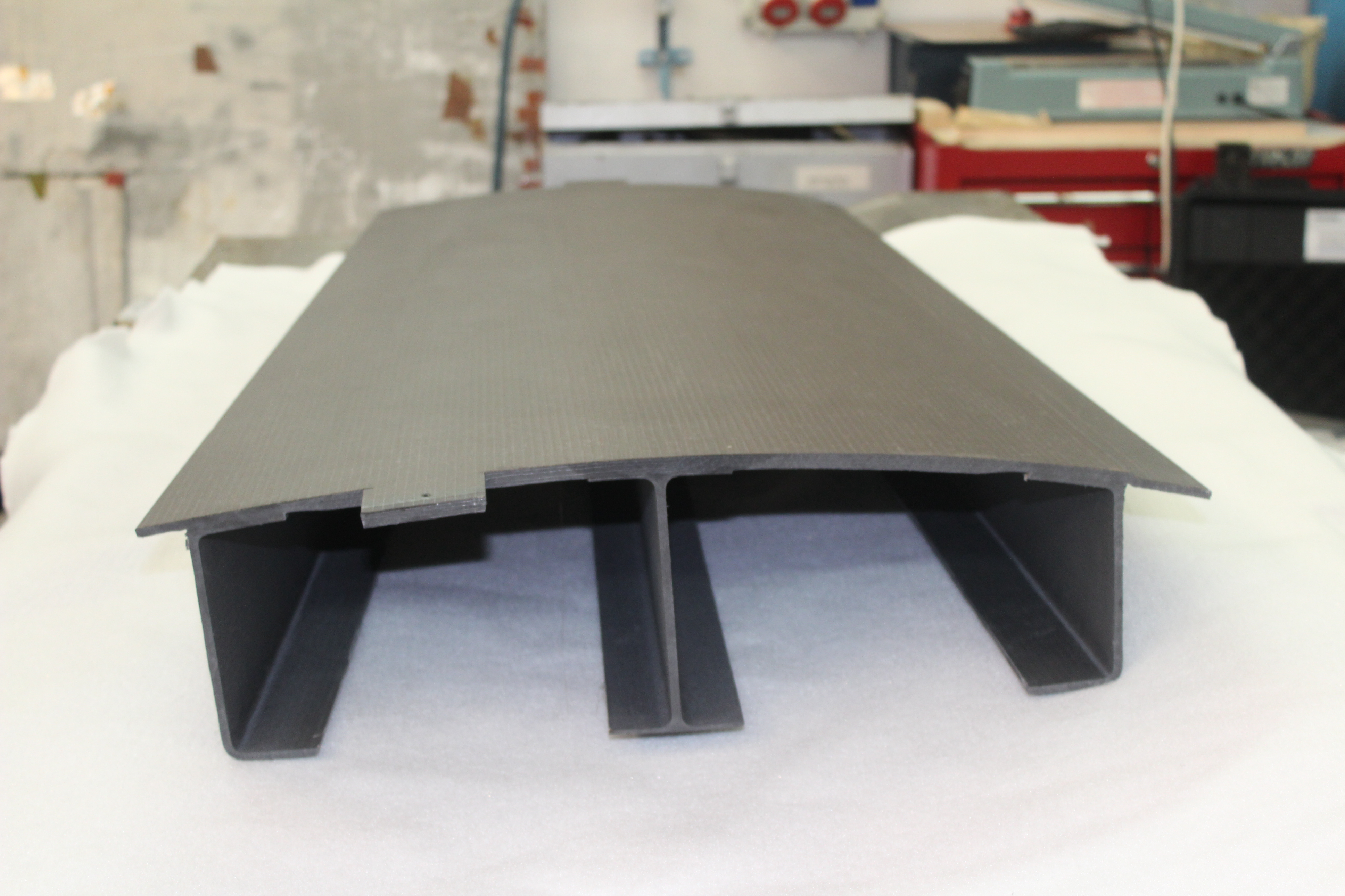
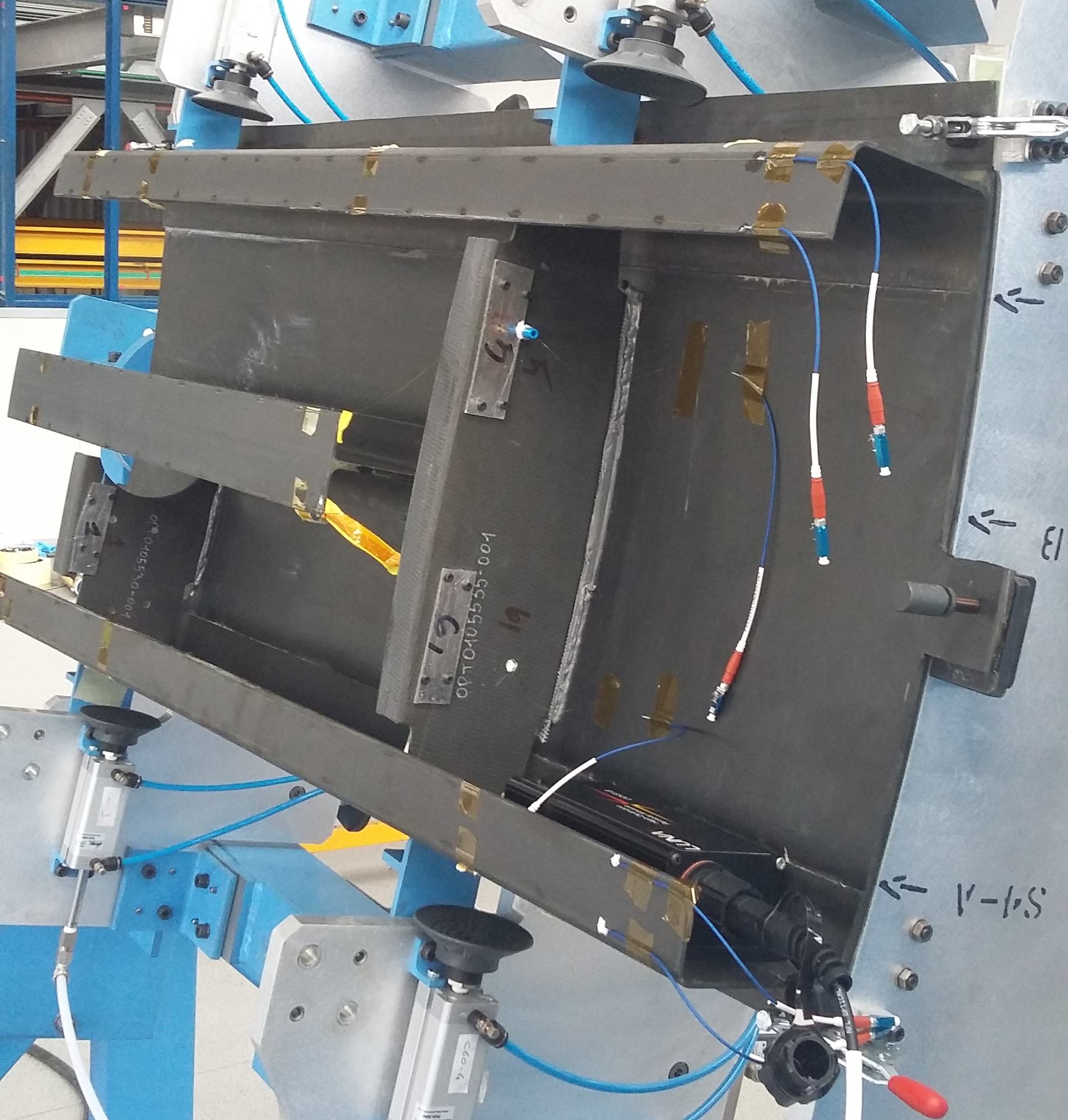
Para unir la estructura del larguero / piel a la piel inferior, el segundo CFP dio como resultado otro proyecto de OPTICOMS llamado WIBOND, para desarrollar una herramienta de ensamblaje de unión que coloca el adhesivo, aplica la presión adecuada e incorpora sensores de fibra óptica en la línea de unión para la salud estructural. seguimiento de la fianza; CW informará sobre esta y las otras tecnologías de ensamblaje en un artículo separado que se publicará en 2022.
El tercer CFP se inició para hacer frente al desafío crucial de las tensiones residuales que provocan un "salto" de la estructura del larguero / piel. Estas deformaciones pueden tener efectos perjudiciales en el proceso de ensamblaje de unión. El proyecto ELADINE se unió al esfuerzo de OPTICOMS para desarrollar software que modela y predice la anisotropía térmica, la contracción de la polimerización, la interacción de la pieza de la herramienta, el flujo de resina y la compactación y gradientes de temperatura en toda la estructura.
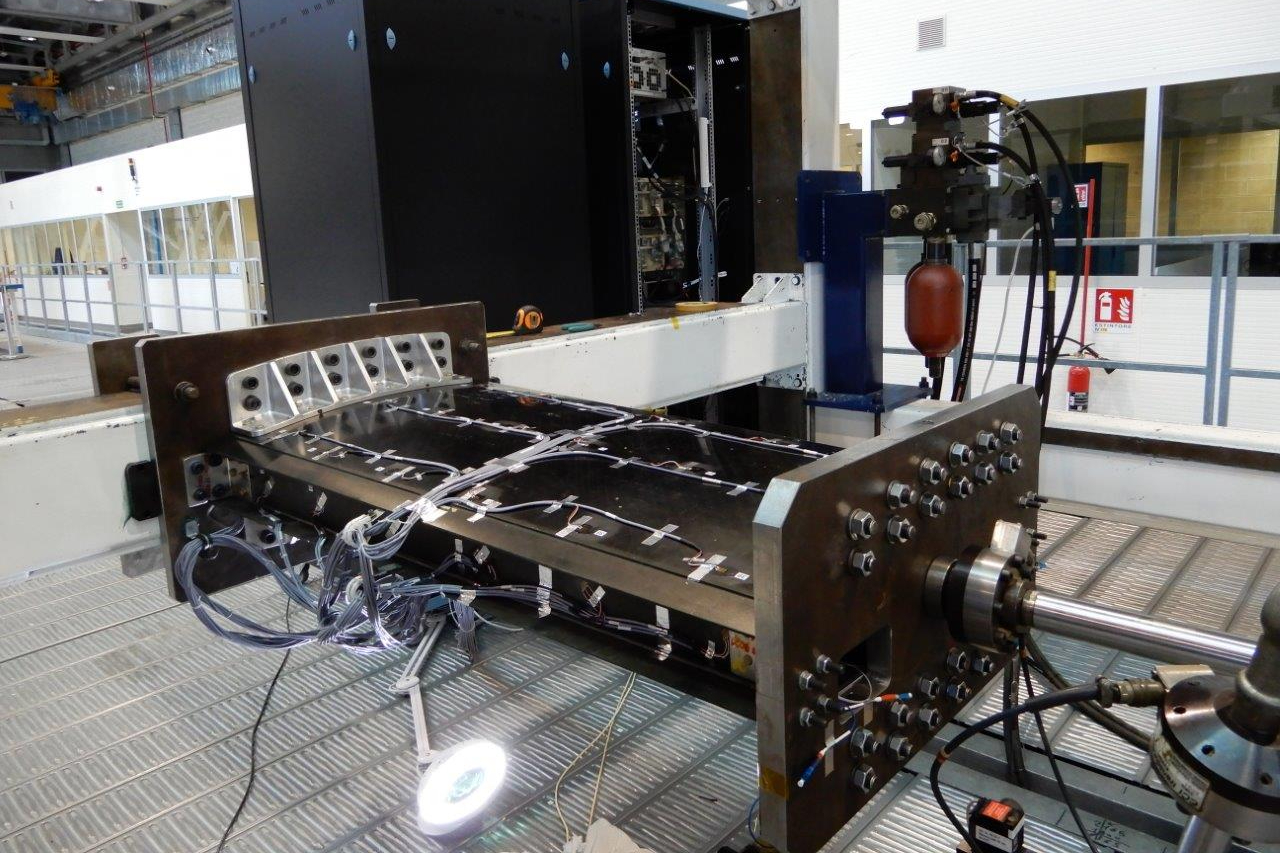
El enfoque principal de IAI y OPTICOMS en este momento es entregar para el segundo trimestre de 2022 un ala de demostración completa de 6,8 metros a Piaggio para pruebas estáticas y de fatiga. A esto le seguirá un análisis del rendimiento general del ala y la capacidad del diseño, los materiales y los procesos para cumplir con los criterios del proyecto. A continuación, vendrá una recomendación de Piaggio sobre los próximos pasos potenciales hacia la comercialización.
Más allá de Piaggio, sin embargo, IAI espera que la caja del ala OPTICOMS pueda encontrar aplicación en otros aviones. “Aunque este proyecto se basa en un avión específico”, dice Sawday, “intentamos hacer que el diseño fuera escalable a diferentes espesores y diferentes tamaños. Nunca perdimos de vista el hecho de que esta tecnología puede y debe ser altamente adaptable ”.
Resina
- Composites de TPE ultraligeros para calzado
- Nexam Chemical, el NCC desarrolla una solución para la fabricación de compuestos de alta temperatura
- El pulverizador de polímeros interno amplía las capacidades de fabricación de Ensinger para materiales compuestos
- Compuestos de Solvay seleccionados para catamarán de carreras
- La universidad comunitaria agrega flexibilidad para los estudiantes de fabricación de compuestos avanzados
- 4 errores comunes que se deben evitar al diseñar para la fabricación
- Fabricación de PCB para 5G
- Abordar la gran necesidad de automatización de compuestos
- Metales para manufactura de bajo volumen y mezcla alta
- ¿Qué es la fabricación automatizada?
- Evite estos 4 errores comunes al diseñar para la fabricación