Hitachi Powdered Metals adopta la automatización robótica y aumenta el volumen un 400 % en un mercado laboral ajustado
La metalurgia de polvos (PM), o sinterización, es el proceso de compactación de mezclas personalizadas de polvos elementales o de aleación en troqueles prefabricados para fabricar eficientemente piezas de máquinas de diversa complejidad. Una vez compactadas, las formas se calientan en un horno de atmósfera controlada para unir las partículas y endurecer las piezas.
También conocido como compactación verde, el proceso produce componentes casi netos que normalmente usan más del 97 por ciento de la materia prima inicial en la pieza terminada. Las mezclas de aleaciones en polvo personalizadas brindan la capacidad de producir piezas complejas, incluso intrincadas, que cumplen con las especificaciones de resistencia y tolerancia requeridas para aplicaciones altamente exigentes.
La planta de Hitachi Powdered Metal (USA) Inc. en Greensburg, Indiana, es una de las nueve instalaciones de Hitachi en todo el mundo. Se especializa en producir componentes de transmisión y tren de válvulas para proveedores automotrices de primer nivel en los EE. UU., con una presencia creciente entre los fabricantes de motocicletas y equipos de jardinería.
Motivación inicial
Hitachi Powdered Metals (HPM) comenzó una inversión gradual en robots industriales en la planta de Greensburg en 2005, impulsada por el surgimiento de un mercado laboral ajustado y la oportunidad de producir un producto extremadamente frágil.
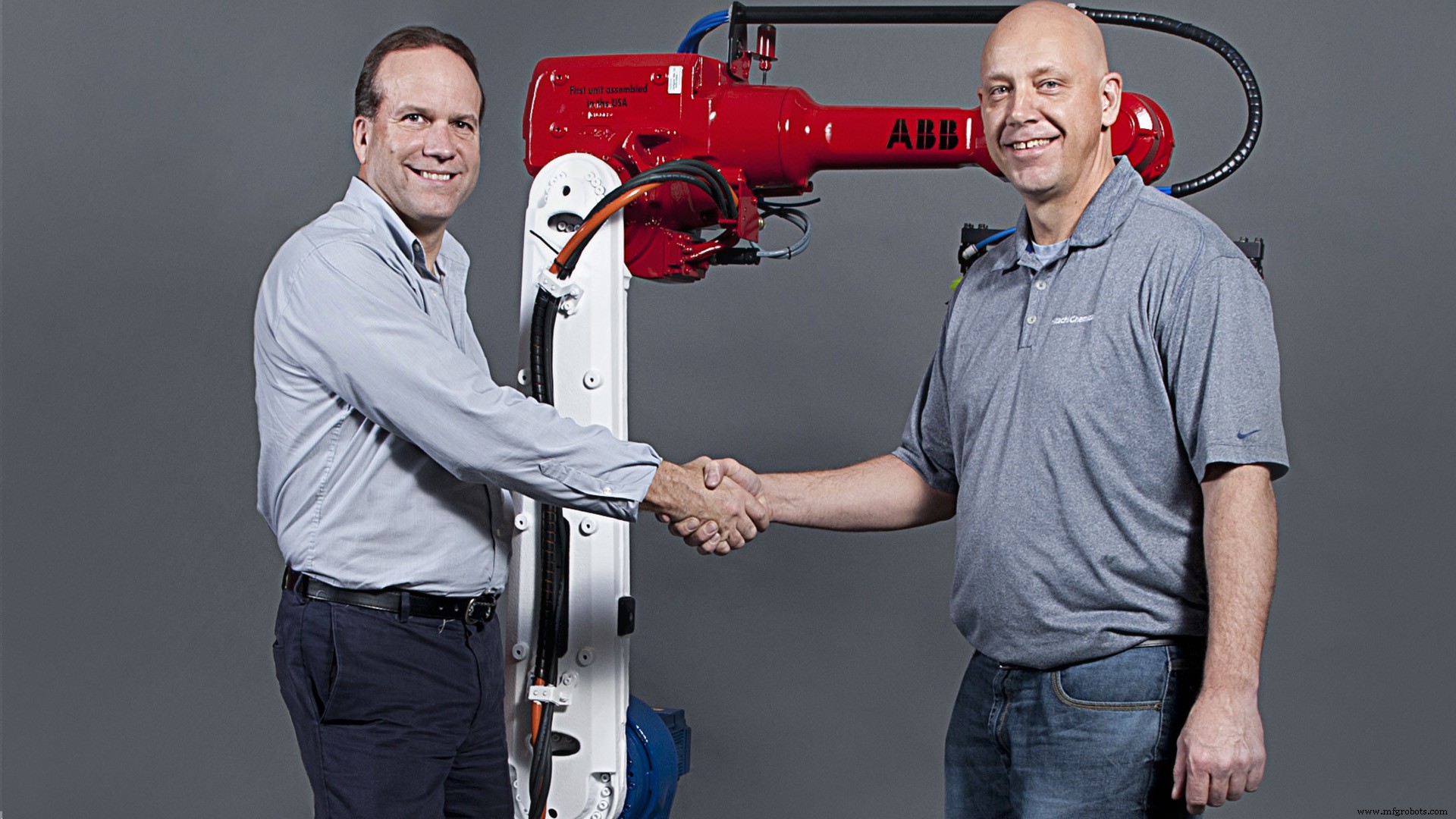
“Comenzamos con los robots porque teníamos que fabricar una pieza para un cliente que tenía dientes pequeños y frágiles que no podían manejarse manualmente, y en ese momento todas nuestras prensas compactadoras se atendían a mano”, dijo Gregory Owens, presidente de la planta de HPM Greensburg. “La reducción de los costos de mano de obra también fue un factor, pero poco después de la primera instalación, un importante OEM automotriz abrió una planta de fabricación en la ciudad, y nuestro problema de costo de mano de obra pasó a ser un problema de disponibilidad de mano de obra, ya que se volvió extremadamente difícil contratar y retener empleados”.
En un esfuerzo por mantener bajos los costos y minimizar cualquier exposición durante el período de prueba inicial, HPM compró un robot ABB S3 antiguo de 1993 usado de CIM Systems Inc. en las cercanías de Noblesville, Ind. James Adams, quien se había unido a HPM varios años antes como un ingeniero de desarrollo de fabricación, estaba familiarizado con CIM, el proveedor de valor (es decir, integrador de sistemas) de ABB Robotics con más antigüedad en los EE. UU., por su trabajo con robots en su empleador anterior.
“CIM tenía un robot usado que nos permitiría facilitar nuestro camino hacia la automatización robótica, limitando nuestra exposición inicial en caso de que no funcionara según lo previsto”, dijo Adams. "También nos brindaron el apoyo que tanto necesitábamos con la programación y la integración del sistema en la operación existente".
Menor chatarra, mejor asignación de mano de obra
Cuando las piezas de metal en polvo salen de la prensa, antes de que se endurezcan en el horno, pueden desmoronarse fácilmente incluso con el toque más ligero. Con el robot recién instalado, que cuenta con una pinza magnética eléctrica para manipular la pieza, la tasa de desechos del nuevo producto pasó del 11 % mientras se atendía manualmente al 0,5 %.
“Cuando las piezas se extraían manualmente de la prensa, se producían considerables daños por manipulación. La pieza podría estar deformada imperceptiblemente, pero no lo sabrías hasta que saliera del horno cinco horas después. Los robots, debidamente programados y equipados, son mucho más cuidadosos en el manejo de las piezas”, dijo Adams.
El nuevo sistema permitió a HPM mover varios de los manipuladores de máquinas manuales a posiciones menos mundanas en la planta, reduciendo el estrés de una tarea repetitiva y reasignando la mano de obra de una manera más eficiente.
La producción aumenta un 400 %
Durante el año siguiente, HPM agregó cinco robots S3 usados más, aplicando lo que aprendió del sistema inicial para automatizar otras prensas compactas. Después de 18 meses, HPM había ahorrado lo suficiente en chatarra y mano de obra para invertir en su primer robot nuevo.
Avance rápido hasta 2019. Ahora, con más de 200 robots instalados, la instalación de Greensburg tiene la misma cantidad de empleados que hace 10 años, pero produce cuatro veces el volumen, entregando fácilmente más piezas con menos personas que cualquiera de las plantas PM globales de Hitachi. .
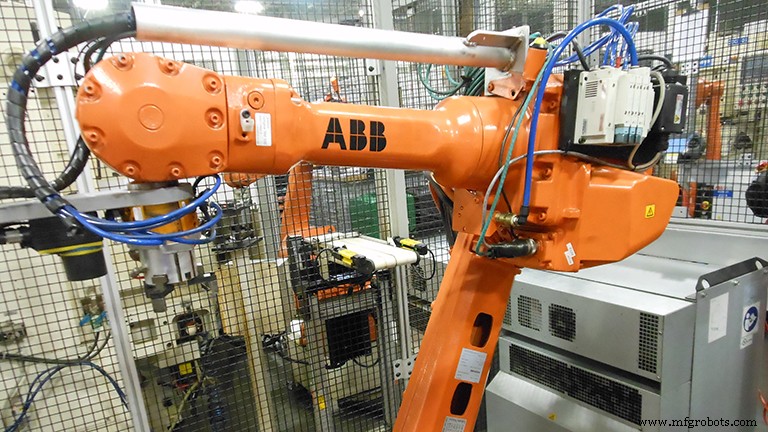
“Una vez que se instaló el primer robot para la parte frágil, se hizo evidente que realmente podíamos aprovechar más robots autómatas”, dijo Owens. "Los robots superaron con creces nuestras expectativas iniciales y, con la escasez de mano de obra que seguimos enfrentando, francamente, creo que los robots nos salvaron de la posibilidad de no existir".
Con el éxito del primer robot, el ritmo de las instalaciones posteriores fue constante. Se necesitaron diez años para llegar a los 100 robots instalados, y luego, a medida que el negocio y la economía continuaron mejorando, solo cuatro años más para llegar a los 200 th instalados recientemente. robot.
Cuando surgieron las oportunidades, HPM continuó comprando robots ABB usados en buenas condiciones, aunque se agregaron cada vez más robots nuevos a la flota. De hecho, todos los robots agregados desde el n.° 147 en 2015 han sido nuevos.
La base de instalación de HPM incluye una gama de robots ABB de seis ejes de gama pequeña y media, un robot Delta y varios modelos SCARA añadidos recientemente. Junto con 350 empleados, la inversión en automatización se utiliza bien, operando tres turnos de cinco a seis días a la semana.
“Nuestra sede corporativa está en Japón”, dijo Adams. "Una vez que vieron cómo funcionaban los robots y el rápido retorno de la inversión, apoyaron mucho nuestra agenda robótica".
Algunos de los robots, tanto nuevos como usados, son ABB Foundry Prime de ABB Robotics, Auburn Hills, Michigan. Son modelos con clasificación IP67 que tienen conexiones bien selladas que protegen el funcionamiento interno de los robots del metal fino y afilado. polvos que flotan a través de la atmósfera de la planta. Los muchos modelos de robots estándar con clasificación IP65 en el piso de HPM son robustos y han sido capaces de resistir el ambiente polvoriento.
Expansión continua
La proliferación de robots en HPM fue respaldada por la replicación de aplicaciones existentes y la expansión de la automatización a otras funciones en las instalaciones.
Después de la instalación del primer robot que atiende la prensa compacta para el producto más frágil, Adams y su equipo automatizaron secuencialmente la eliminación de los compactos de otras prensas. Parte de este proceso fue colocar cada parte en una balanza para verificar su integridad. Una vez verificada, la pieza se colocó en un transportador que conducía al horno.
El resultado fueron eficiencias laborales adicionales y, con el hábil toque del robot, la tasa de desecho de las piezas menos frágiles pasó del 7 % al mismo 0,5 % de la pieza inicial.
Al final del transportador, las piezas se colocan en bandejas de sinterización que, una vez llenas, se colocan en hornos para el proceso de endurecimiento. Este proceso de carga del horno se convirtió en la segunda función principal en ser automatizada.
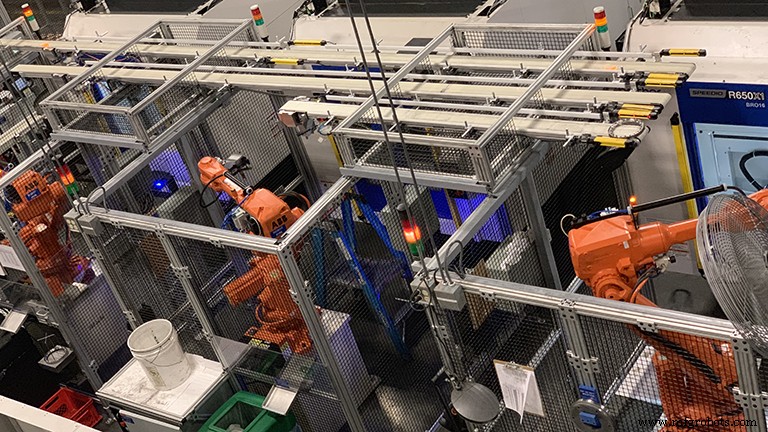
Continuando a un ritmo mesurado, se instalaron robots para sacar las piezas de las bandejas y colocarlas en palés, al mismo tiempo que se insertaban separadores entre cada capa de palés.
“A medida que nos familiarizamos con los robots, tomamos lo que aprendimos y duplicamos las aplicaciones en las instalaciones”, dijo Adams. "La programación se volvió mucho más fácil y el último día de la instalación de la línea modificamos los programas existentes, copiamos y pegamos, y estábamos listos y funcionando en un par de horas".
RobotStudio, el software de programación y simulación fuera de línea de ABB, se convirtió en una herramienta valiosa para acelerar la creciente adopción de tecnología robótica por parte de HPM. Basado en ABB VirtualController, una copia exacta del software real que ejecuta los robots en producción, RobotStudio realiza simulaciones realistas utilizando programas de robot y archivos de configuración idénticos a los que se utilizan en el taller. Con RobotStudio, Adams pudo diseñar la disposición óptima de la celda y verificar su rendimiento antes de integrar los robots en una operación en particular.
“Es el mejor software jamás desarrollado”, dijo Adams. “Ahorra tiempo y dinero tanto en la creación de sistemas para nuevas aplicaciones como en la replicación de los que ya teníamos instalados en otras áreas de la planta”.
Introducción a la Visión
La relativa simplicidad de la replicación existe solo después de que se haya instalado y refinado una determinada aplicación en la planta. Las nuevas aplicaciones suelen ser más desafiantes. Después de 18 meses y la integración exitosa de seis robots de cuidado de prensas, HPM tuvo la confianza para adoptar tecnología habilitada por visión, en su infancia en ese momento (2006), para automatizar robóticamente la compleja operación de acuñación o reprensa.
Después de que las piezas salen del horno, a menudo se pueden deformar, lo que requiere que se coloquen en una prensa que las vuelva a acuñar para que queden rectas o planas. Muchas piezas tienen chaveteros o dientes que deben colocarse en el molde con todos los aspectos alineados con precisión. Antes de la llegada de los robots, las piezas que se acuñaban eran manejadas por un sistema de automatización duro que, con muchas variaciones diferentes de productos, requería cambios frecuentes y lentos. Los cambios fueron tan largos que eran comunes las copias de seguridad de 250 lotes de productos, cada uno con aproximadamente 100 piezas.
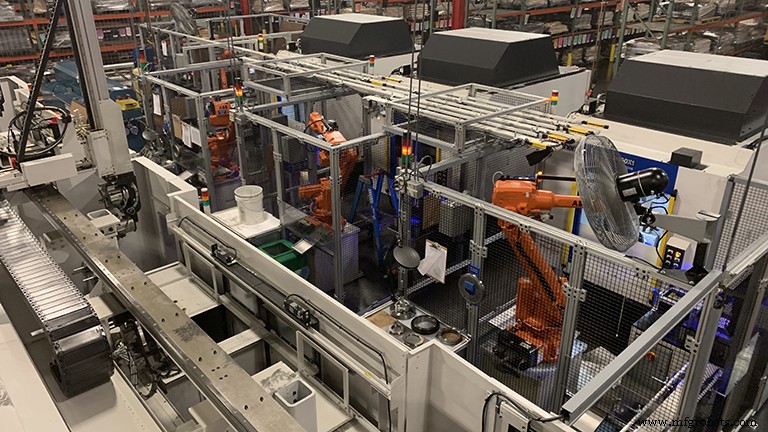
Con el robot habilitado para visión no hay tiempo de inactividad. El robot puede identificar la pieza de un grupo de muchas piezas diferentes, recogerla, orientarla radialmente y colocarla con precisión en la prensa.
Debido a que el sistema de visión necesitaba interactuar con la última tecnología robótica, este fue el primer robot nuevo de ABB instalado en las instalaciones de Greensburg. Poco después de que estuviera en funcionamiento, se compraron dos robots nuevos más para la misma aplicación.
“Antes de la instalación del robot de la estación de acuñación, el personal de represión trabajaba todos los días”, dijo Adams. "Seis meses después de que se instaló el primer robot de visión, no hubo más copias de seguridad y el personal tenía los fines de semana libres".
Más Visión
HPM volvió a utilizar la visión más adelante en el último de los principales procesos que se automatizaron, el despaletizado de piezas que se habían enviado para un tratamiento térmico especializado. Aunque las piezas se envían cuidadosamente colocadas en capas escalonadas en un palé, regresan relativamente desordenadas y son difíciles de desapilar. Un robot ABB con visión integrada puede encontrar las piezas y sujetarlas de forma segura para que puedan despaletizarse de forma segura.
“Esa es una de las capacidades únicas de los robots ABB”, dijo Dave Fox, presidente de CIM Systems, quien ayudó a integrar los diversos sistemas de visión. “Las piezas están realmente desorientadas en los patines, no en filas uniformes, y algunas están boca abajo. Un robot típico de seis ejes tendría todo tipo de problemas de singularidad, llegando a una posición en la que ya no puede moverse. Pero el robot de ABB que utiliza la evasión de singularidad avanzada es capaz de encontrar las piezas, agarrarlas y colocarlas de forma segura en un transportador sin perder el ritmo”.
Robots SCARA para Inspección de Calidad
No es de extrañar que una búsqueda reciente de un sistema más eficiente para inspeccionar las guías de válvulas condujera de nuevo a los robots, en este caso un grupo de modelos ABB SCARA (brazo robótico de ensamblaje de cumplimiento selectivo), que se utilizan normalmente para el ensamblaje de piezas pequeñas y la manipulación de materiales.
El protocolo HPM requiere una inspección del 100 por ciento de todas las guías de válvula, lo cual es una tarea difícil dada la variedad de piezas que se deben probar:30 variaciones de tamaño diferentes y 16 puntos de detección para cada pieza. Dado que el sistema de prueba de automatización dura imperante no podía mantenerse al día con el volumen, Adams comenzó a buscar un sistema mejor.
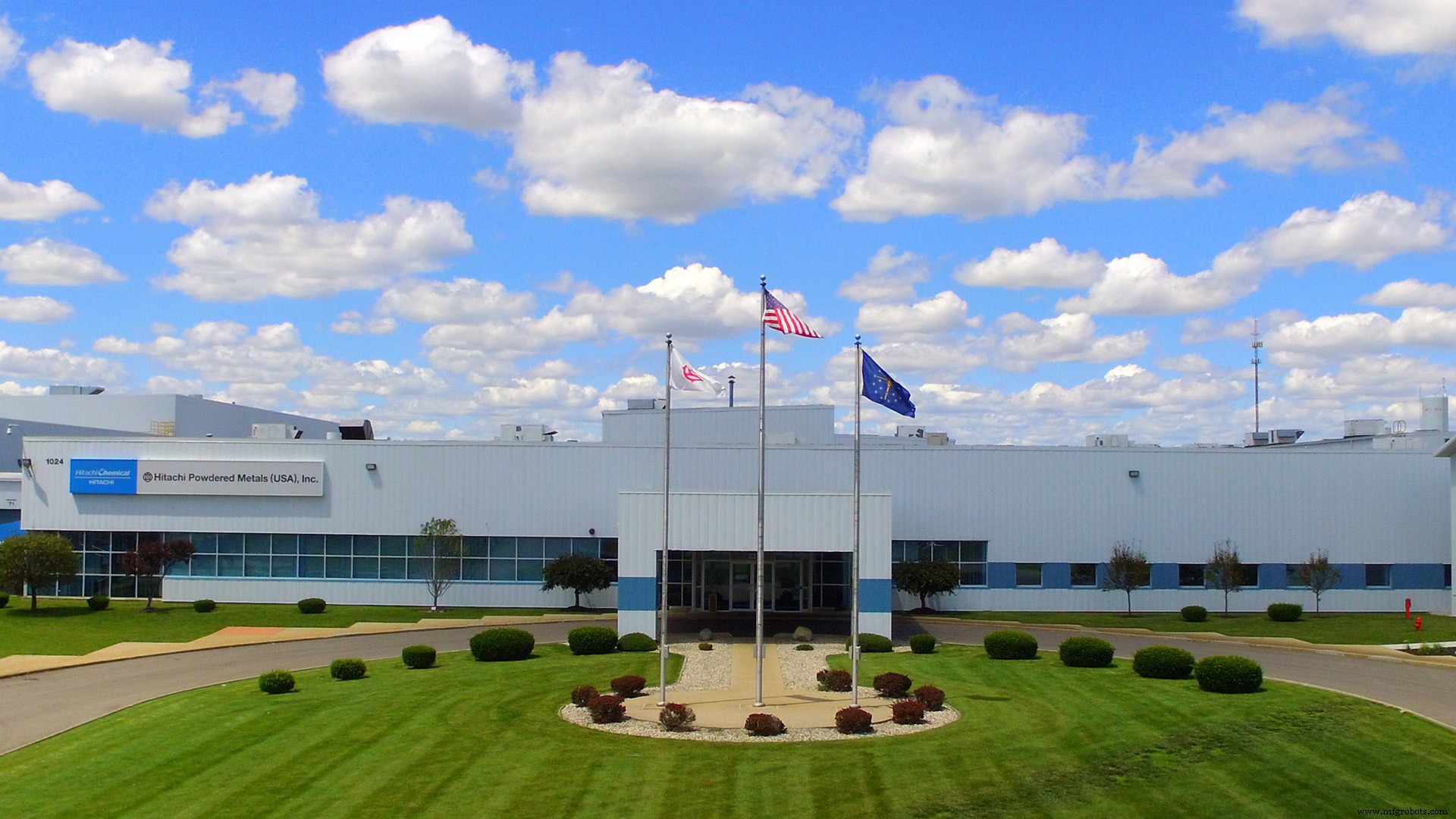
Después de analizar varias opciones, todas las cuales tenían demasiadas piezas móviles y requerían una ingeniería compleja, Fox sugirió diseñar un sistema en torno a los robots SCARA, que ABB agregó a su cartera en 2016. Sin duda, eran lo suficientemente rápidos, con una gran repetibilidad y tenían una huella pequeña y una forma de montaje sin obstáculos que caben dentro de un espacio confinado.
Se diseñó un sistema relativamente simple con tres robots SCARA que seleccionan guías de válvula individuales de un transportador de tolva y las presentan a cámaras de visión y un "comparador" estacionario en los diversos ángulos necesarios para acceder a los 16 puntos de detección. Las piezas que pasaron se colocaron en un transportador y las que no se colocaron en contenedores de rechazo.
Con la flexibilidad para manejar con destreza cada variación de pieza diferente con una facilidad similar, el sistema puede inspeccionar una pieza cada dos segundos, un 30 por ciento más rápido que el método anterior. Dado que los movimientos se limitan a una distancia corta y las piezas son muy ligeras, un robot de seis ejes no funcionaría tan eficazmente como el SCARA elegante y de alcance limitado.
“Los SCARA son una gran adición a la cartera de ABB. Si no fuera por esa solución, Hitachi probablemente habría tenido que buscar otra tecnología para la inspección de piezas”, dijo Fox. "Fue agradable poder encontrar otra aplicación para robots, aunque esa no fue la primera opción que se me ocurrió".
Sistemas CIM siempre presentes
Una constante que ha estado en escena desde el primer robot instalado en HPM hasta el día de hoy, ya sea en primer plano o en segundo plano, es CIM Systems. Siempre disponible cuando se necesita, CIM ha configurado HPM con robots nuevos y usados, ha ayudado a programar y solucionar problemas y, quizás lo más importante, ha enseñado al personal de HPM a hacer muchas cosas por sí mismos.
Cuando HPM integró robots en una nueva aplicación, con visión o no, CIM realizó la configuración y la programación, siempre teniendo en cuenta compartir su experiencia, incluido el uso de RobotStudio. Durante la pausa ocasional en la línea de tiempo de adquisición de robots de HPM, CIM estuvo disponible para actualizar programas, encontrar repuestos difíciles de alcanzar para modelos más antiguos u ofrecer consejos sobre cómo trabajar con robots en una variedad de cosechas.
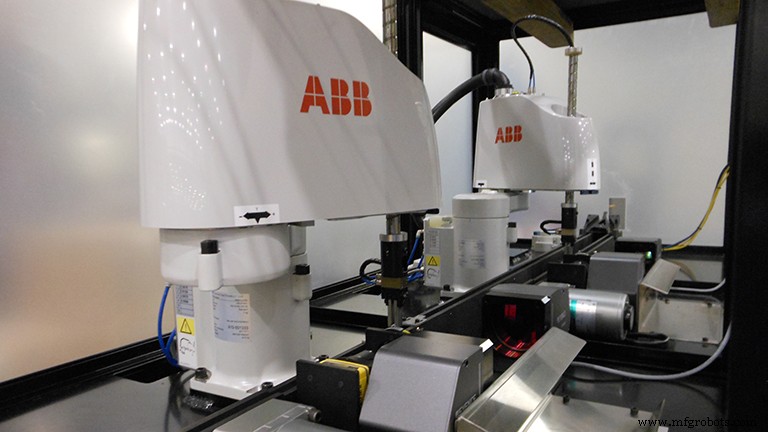
“A medida que llegamos a cada uno de los diferentes procesos, hicimos que CIM realizara la integración y la programación iniciales. Una vez que comenzamos a replicar procesos en toda la planta, aprendimos lo suficiente como para hacer muchas cosas nosotros mismos”, dijo Adams. “Debido a su estrecha relación con ABB, Dave Fox siempre sabe cuándo aparece una nueva tecnología y qué robots serían óptimos para nuestras diversas aplicaciones. El soporte que recibimos de CIM Systems y el servicio de ABB fue una combinación ideal”.
Con una relación tan duradera, no sorprende que cuando el primer robot salió de la línea de producción en las instalaciones de fabricación de ABB en los EE. UU. en Auburn Hills en 2017, CIM lo encargó en HPM. El robot IRB 2400, único en su clase, se pintó de forma personalizada en rojo, blanco y azul en la fábrica, y está ubicado en un lugar destacado en las instalaciones de HPM, donde realiza tareas de inspección y paletización.
“Estamos entusiasmados de haber podido adquirir el primer robot fabricado en Estados Unidos para HPM”, afirmó Fox. “Es especialmente significativo porque la planta de Indiana tiene el autómata más flexible de las muchas instalaciones globales de HPM”.
Soporte de otras instalaciones de HPM
La gerencia corporativa de HPM en Japón se dio cuenta de las importantes mejoras de productividad que el equipo de Greensburg logró con los robots, y en 2017 asignó a Adams y Owens para liderar una iniciativa de "Robótica global" para ayudar a las otras plantas de metal en polvo de Hitachi en todo el mundo a ampliar su uso de robots. .
El programa de dos años ya pasó el punto medio y las empresas afiliadas están comenzando a lograr mejoras significativas en la productividad, incluso con los costos laborales más bajos en los otros países.
Adams configuró la función de monitoreo remoto de ABB en HPM para que él o los miembros de su equipo puedan ver cómo funcionan los robots y solucionar la mayoría de los problemas desde cualquier lugar fuera de la fábrica en una computadora portátil, tableta o teléfono inteligente. Con los robots más nuevos, HPM espera aprovechar ABB Ability Connected Services, la oferta digital unificada e intersectorial de ABB, que proporciona datos en tiempo real sobre el estado y el rendimiento de los robots desde cualquier ubicación.
Planes futuros
La misión continua de HPM incluye mejorar sus operaciones con automatización robótica.
“Esperamos crecer un 10 por ciento anual en el futuro previsible y debemos hacer todo lo posible para seguir siendo competitivos”, dijo Owens. “Estamos analizando qué piezas de transmisión podremos fabricar para vehículos eléctricos, y nos hemos fijado en penetrar en segmentos no automotrices como el de equipos pesados, donde el metal en polvo puede reemplazar las piezas hechas de otros materiales a un costo menor. .”
"Ciertamente anticipo que el ritmo de las instalaciones de robots se mantendrá constante o incluso aumentará", dijo Owens.
Para obtener información sobre Hitachi Powdered Metals (USA) Inc., visite www.hitachi-pm.us o llame al 812-663-5058. Para obtener información sobre CIM Systems Inc., visite www.cimrobotics.com o llame al 317-773-5600. Para obtener información de ABB Robotics, visite www.abb.com/robotics o llame al 248-391-9000.
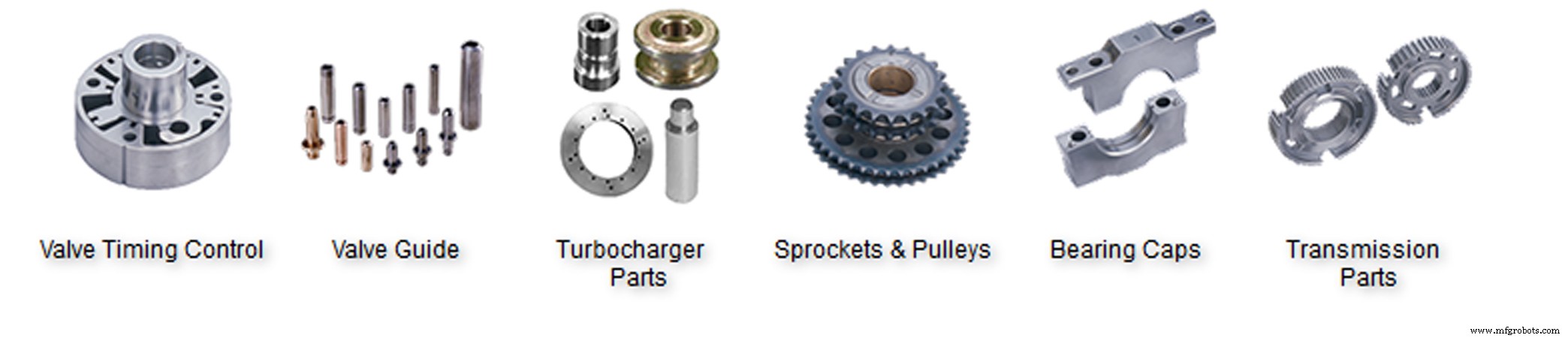
Sistema de control de automatización
- Automatización de logística y almacenamiento
- Más automatización =Robots más capaces
- NPE2018:Robots y automatización abordan la complejidad creciente
- Automatización:Cuchilla de desbarbado compatible para robots
- ABB predice tendencias clave que cambiarán la automatización robótica en 2022
- Un nuevo tipo de 'cerebro' robótico podría transformar las fábricas modernas
- Hitachi adquirirá el integrador de sistemas robóticos JR Automation por 1400 millones de dólares
- Hitachi completa la adquisición de JR Automation
- ATI Industrial Automation lanza una nueva lijadora orbital para robots
- El mercado de automatización robótica de procesos ganará impulso gracias a la mano de obra digital de Blue Prism y su automatización excepcionalmente segura
- El mercado de automatización de procesos robóticos crecerá en $ 750 millones