Las placas de fibra de carbono flexibles permiten un calzado de alto rendimiento
Las placas, las varillas y otros componentes de la entresuela de fibra de carbono han estado mejorando el rendimiento y reduciendo el peso de los zapatos deportivos de primer nivel durante años. Sin embargo, explica Junus Khan, fundador y presidente de Carbitex Inc. (Kennewick, Washington, EE. UU.), Incluso con materiales compuestos, los desarrolladores de calzado normalmente deben comprometerse cuando se trata de la elección del material para las placas de la entresuela:la elección es entre un material lo suficientemente rígido como para apoye el pie durante la actividad requerida, aunque puede ser inflexible y pesado, o un material que sea liviano y flexible, pero que no brinde tanto soporte. Cualquiera de las opciones, o un material de compromiso que se encuentra en algún punto intermedio, hace que el zapato, y el usuario, sean inherentemente ineficientes, algo que Carbitex dice que ha podido superar a través del desarrollo de su línea de productos de fibra de carbono flexible / materiales compuestos termoplásticos.
Sin embargo, señala Khan, originalmente no se propuso transformar la industria del calzado. Hace poco más de 10 años, Khan, con experiencia en economía pero que aprendió sobre los compuestos de fibra de carbono trabajando en la industria automotriz, echó un vistazo al mercado del equipaje y se preguntó por qué los fabricantes de equipaje estaban tratando de imitar la estética de la fibra de carbono. utilizando nailon balístico y otras telas, en lugar de utilizar fibra de carbono real. Incapaz de encontrar una empresa que fabricara un producto de fibra de carbono suave y flexible adecuado para el mercado del equipaje, decidió intentar hacerlo él mismo.
En 2010, Khan comenzó a investigar varios materiales de fibra de carbono en su garaje en su tiempo libre, y para 2011, su primer material y proceso se probaron en el Laboratorio Nacional del Noroeste del Pacífico del Departamento de Energía de EE. UU. En ese momento, dice, "tenía un concepto viable y una mejor comprensión del espacio material", y decidió convertir este concepto en una empresa, con el objetivo de continuar el desarrollo y, en última instancia, vender el material. Carbitex Inc. se fundó en febrero de 2012.
Del equipaje al calzado
Khan explica que otras empresas han desarrollado tejidos de fibra de carbono semiflexibles suspendiendo una sola capa de tejido entre dos películas termoplásticas. "Sin embargo, cuando tira de ese material en tensión, el modo de falla son las películas que arrancan la superficie del carbono", dice, lo que significa que una tendencia a la delaminación puede obstaculizar la cantidad de flexibilidad real disponible para el laminado.
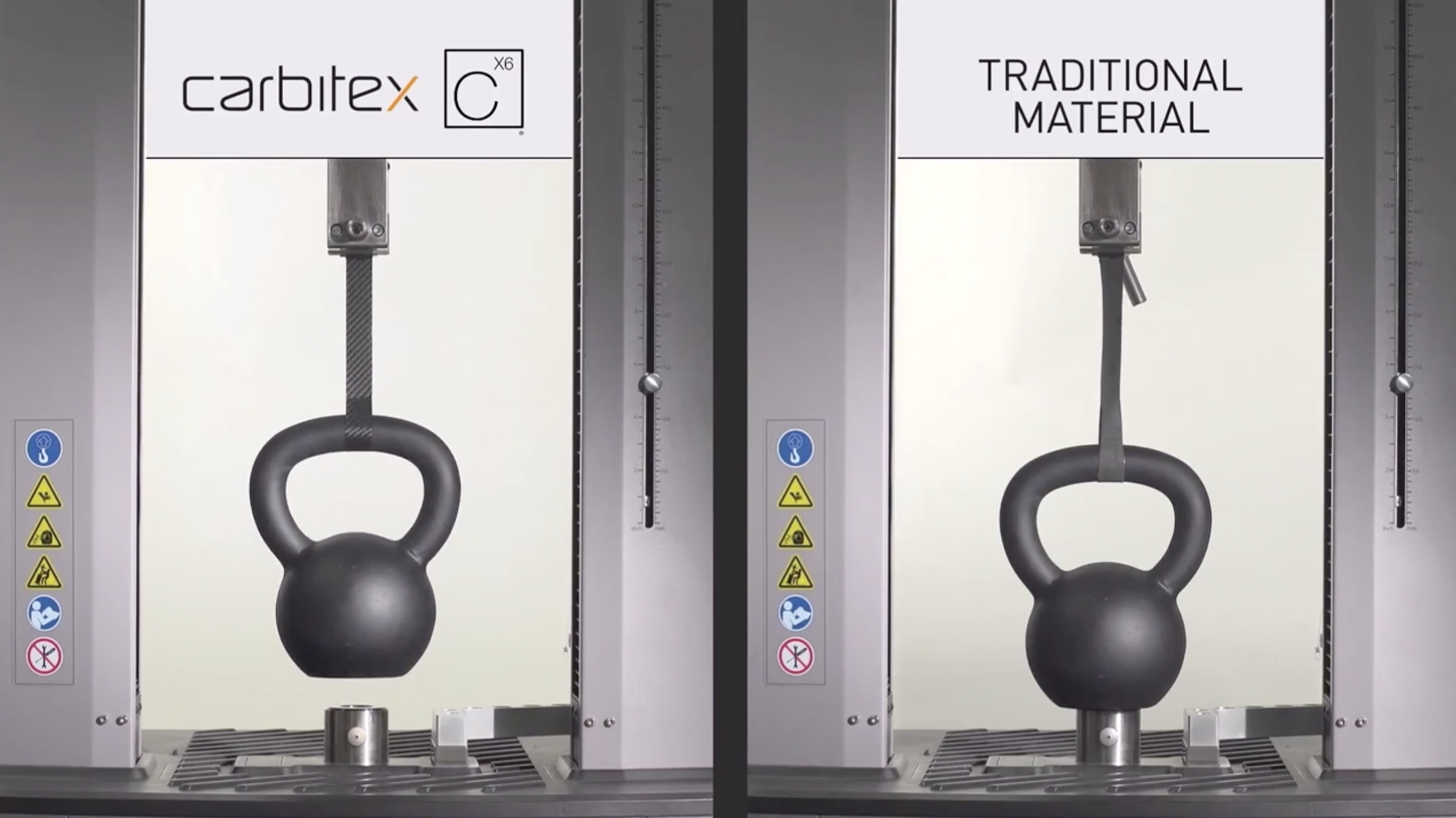
El producto CX6 de Carbitex, su oferta de producto original, es también una sola capa de tela de fibra de carbono laminada entre películas termoplásticas. Pero, dice Khan, la tela se trata primero con un aglutinante especialmente desarrollado que, según una patente estadounidense presentada por Carbitex en 2015, le da a la tela laminada "flexibilidad similar a la tela no laminada con películas de polímero, y mejor adherencia y resistencia a la tracción". Agrega:“Cuando tira de nuestro material CX6 en tensión, el modo de falla es que las fibras se rompen realmente, no que la película se deslamina. Realmente estás obteniendo esa fuerza característica de la fibra de carbono ". También se dice que el material tiene propiedades de estiramiento muy bajas en comparación con otros materiales compuestos, que Carbitex encontró un uso en componentes de calzado fabricados con precisión con una transferencia de potencia mejorada.
Carbitex comenzó a vender su primer producto CX6 dentro de la industria del equipaje y el bolso a compañías como Tumi (South Plainfield, Nueva Jersey, EE. UU.), Como Khan se había propuesto originalmente. Sin embargo, Carbitex comenzó rápidamente a recibir consultas de una variedad de otras industrias, como la electrónica de consumo. Si bien el crecimiento fue emocionante, dice:"Al mismo tiempo, comenzamos a darnos cuenta de que nos estábamos extendiendo muy poco". Hace unos tres años, la empresa tomó la decisión de centrarse en un mercado que mostraba el mayor potencial:el calzado.
En la actualidad, Carbitex suministra sus placas de fibra de carbono a la industria del calzado, donde se utilizan en snowboard, ciclismo, deportes acuáticos, carreras, senderismo, productos de moda y más. Una de las aplicaciones de calzado más recientes y de mayor rendimiento de la compañía es un botín de fútbol lanzado por Adidas en el otoño de 2020.
AFX y DFX:transformando el calzado
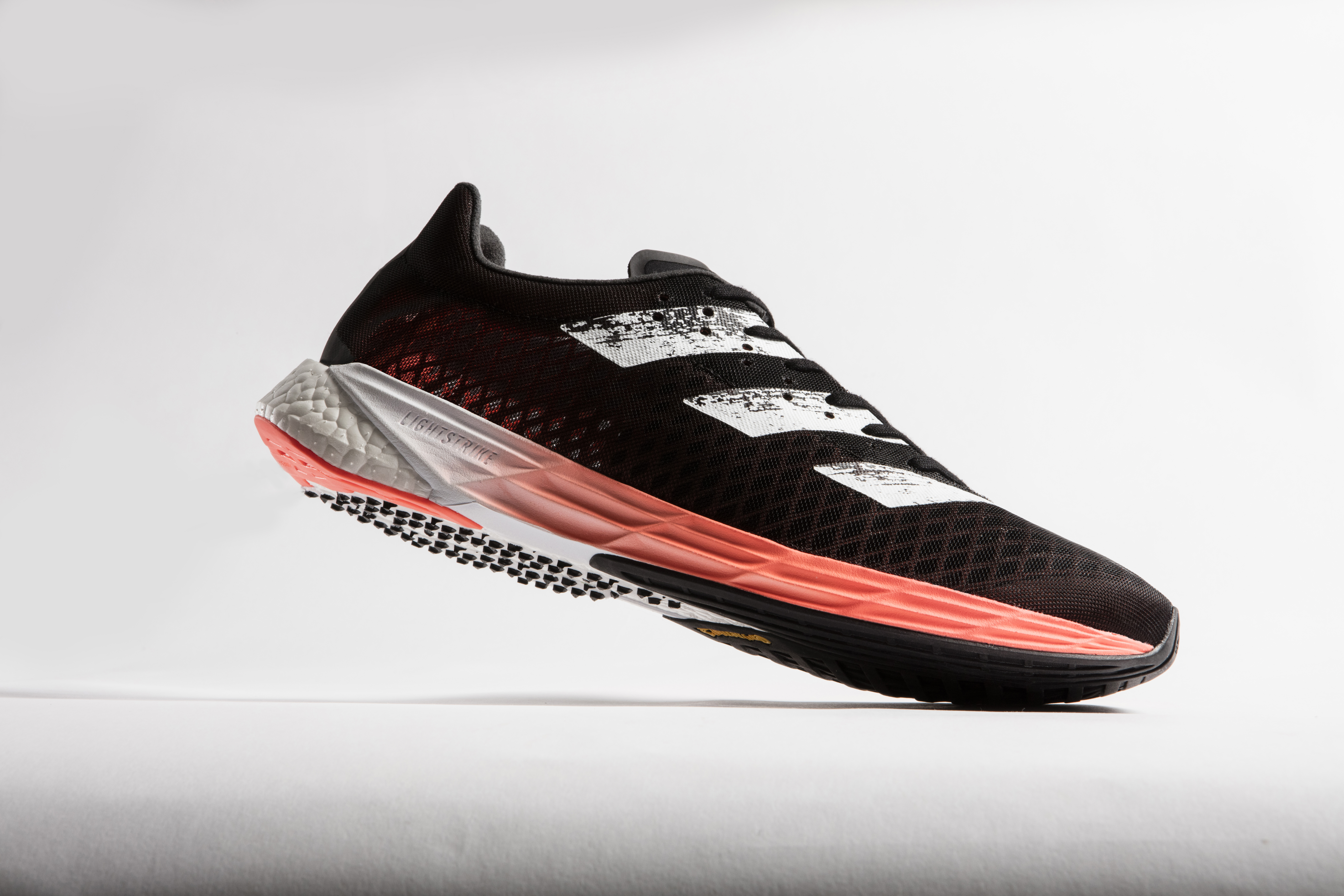
Durante los últimos años, Carbitex ha lanzado dos nuevas tecnologías compuestas, llamadas AFX y DFX. Según Khan, a diferencia de los "compuestos típicos" cuya rigidez está controlada por la orientación de la fibra y la longitud de la capa, la rigidez de una hoja de fibra de carbono Carbitex es uniforme en toda su longitud. Mientras que otros compuestos pueden consistir en un tipo de sistema de resina y fibra, dice, los materiales de Carbitex son más complejos, e incluyen capas intrincadas de láminas de polímeros y capas de tela, para lograr las propiedades de flexibilidad deseadas. “Una versión muy simple de nuestro material AFX podría tener dos tipos diferentes de fibra de carbono intercalados entre otros dos o tres tipos diferentes de polímero”, dice. "Es un intrincado sistema de capas, y debe comprender cómo esas capas deben unirse para obtener las propiedades [requeridas]".
Generalmente, el proceso de fabricación comienza colocando capas de tejidos, que pueden tratarse con aglutinantes u otros tratamientos de tejidos, y láminas de polímero en un panel. Se utiliza una variedad de fibras de diferentes proveedores, aunque Khan dice que la mayoría de los productos de Carbitex incluyen fibras de Toray Composite Materials America (Tacoma, Washington, EE. UU.) Y, a menudo, telas de arrastre de Hexcel (Stamford, Connecticut, EE. UU.). Los polímeros también varían según la aplicación, pero normalmente son termoplásticos por su flexibilidad y formabilidad, "aunque a veces no son completamente termoplásticos, según la aplicación", agrega.
Estos paneles se consolidan en prensas calentadas; una vez retiradas, las piezas individuales se cortan mediante chorro de agua y se forman. La fabricación de paneles en lugar de colocar piezas individuales conduce a una mayor producción que las capas tradicionales, dice Khan.
Proceso de fabricación
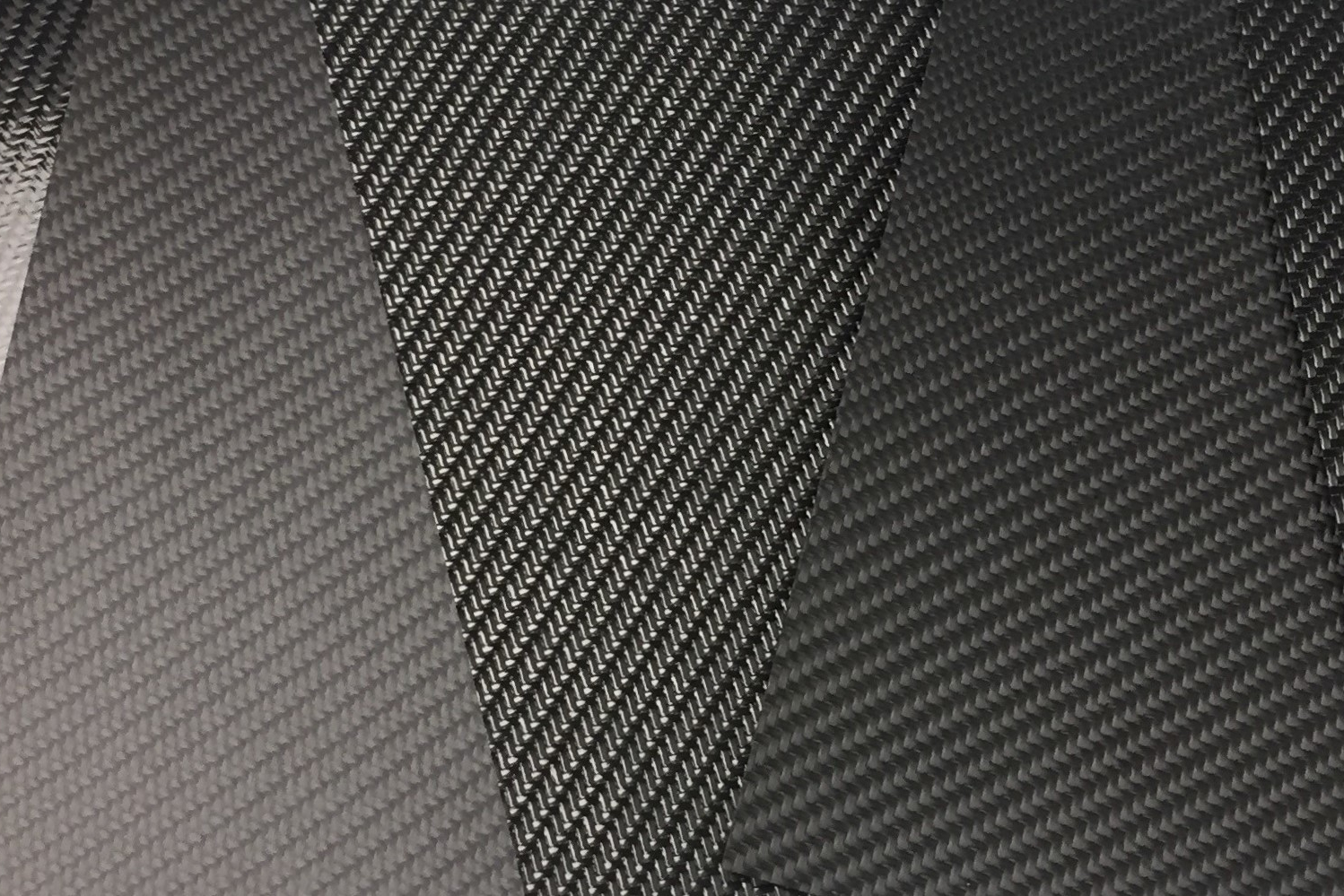
Primero, capas específicas de telas tejidas, preimpregnados y películas de polímero se apilan juntas en un panel.
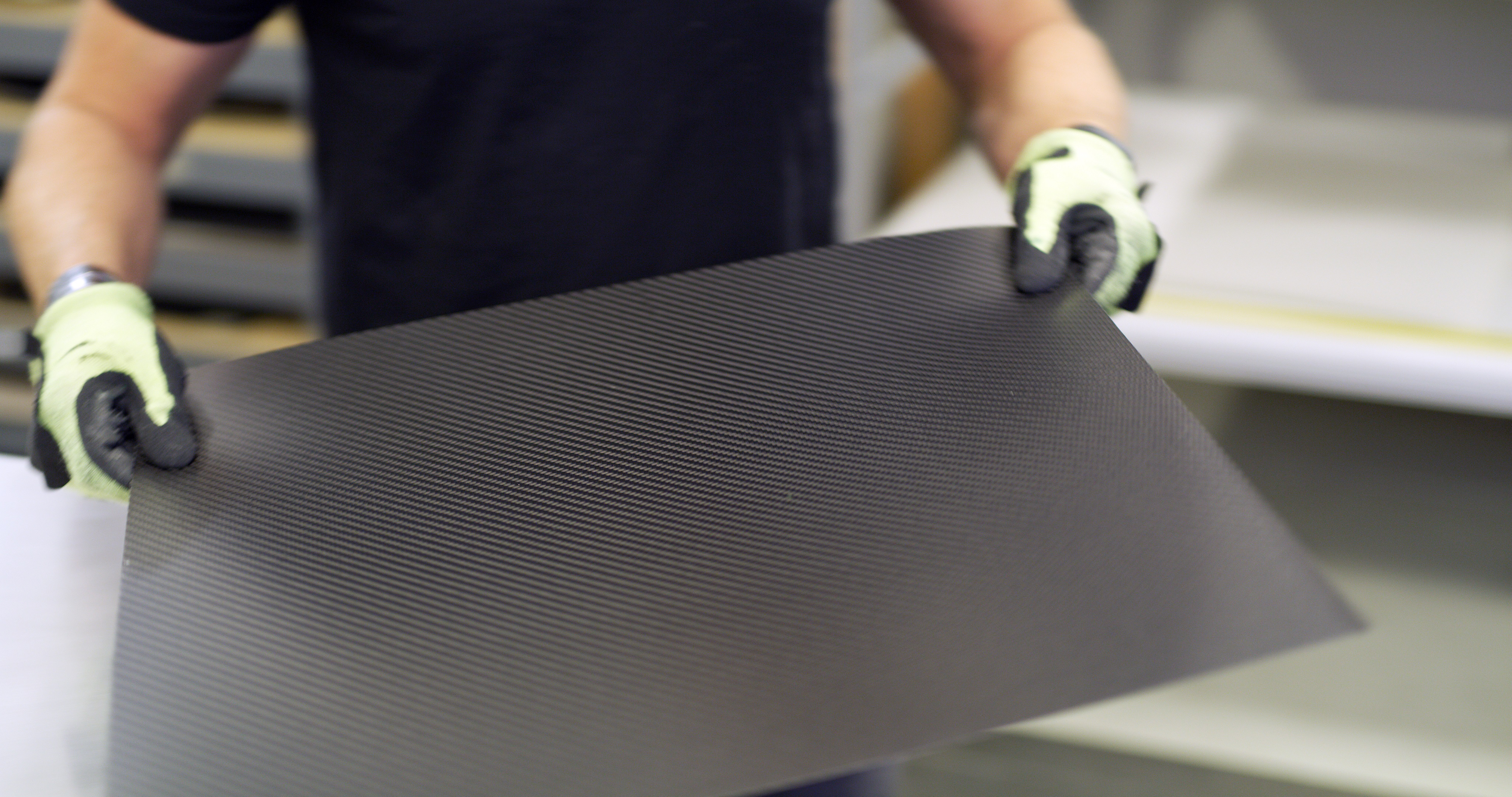
A continuación, el panel se consolida en una prensa calentada.

Los componentes específicos se cortan de los paneles curados mediante chorro de agua.
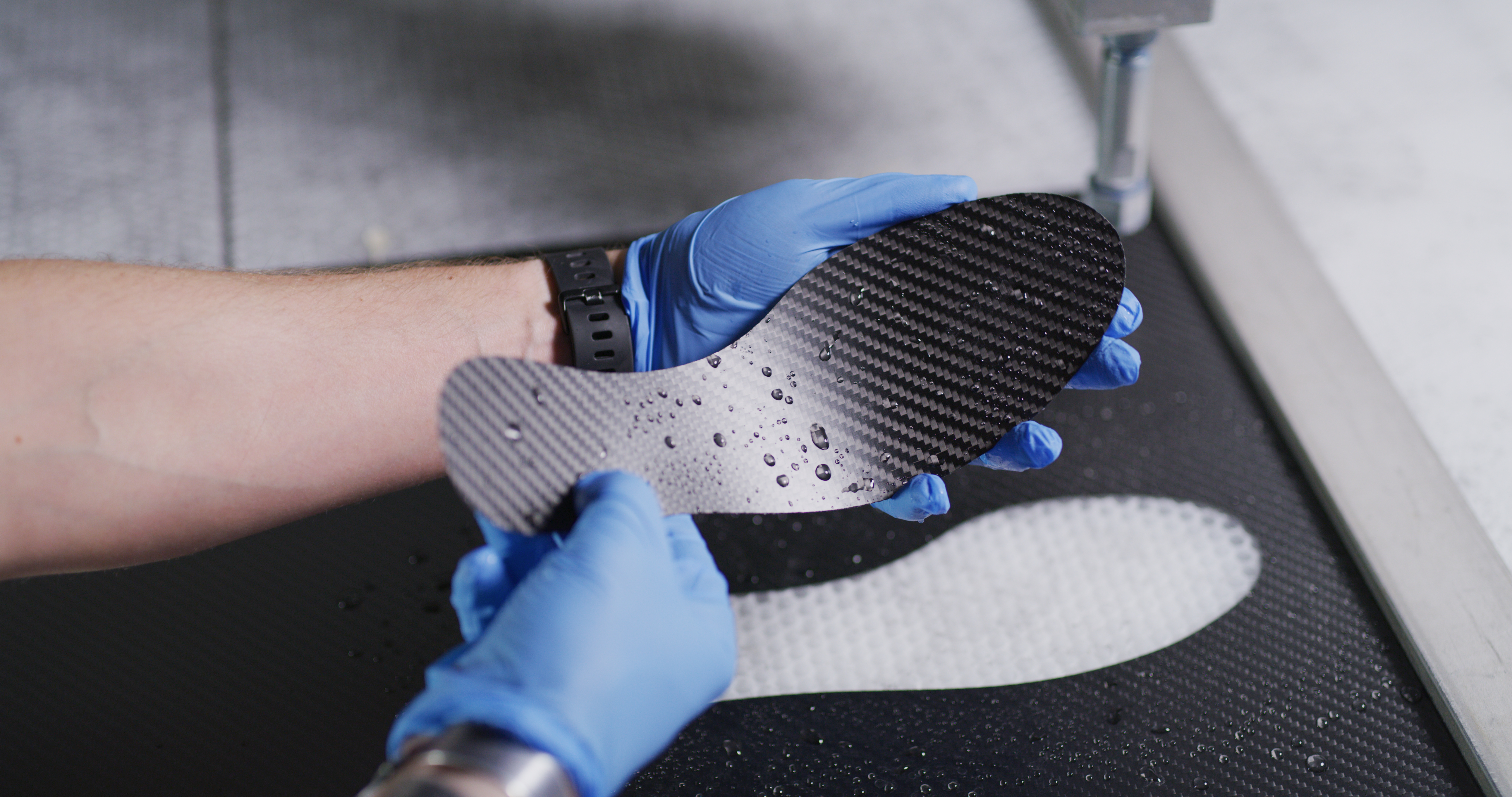
Evitar el laminado de piezas individuales logra un mayor rendimiento, dice Carbitex.

La entresuela de compuesto de fibra de carbono resultante (en la foto es un componente DFX) se ensamblará en una aplicación de calzado final.
Anterior Siguiente
Sin embargo, además de equilibrar la rigidez y la flexibilidad, existe un desafío adicional para desarrollar el calzado:el pie humano solo puede doblarse en una dirección sin extenderse demasiado o romperse, por lo que los materiales del calzado deben tener la versatilidad para doblarse en ciertas direcciones pero no en otras
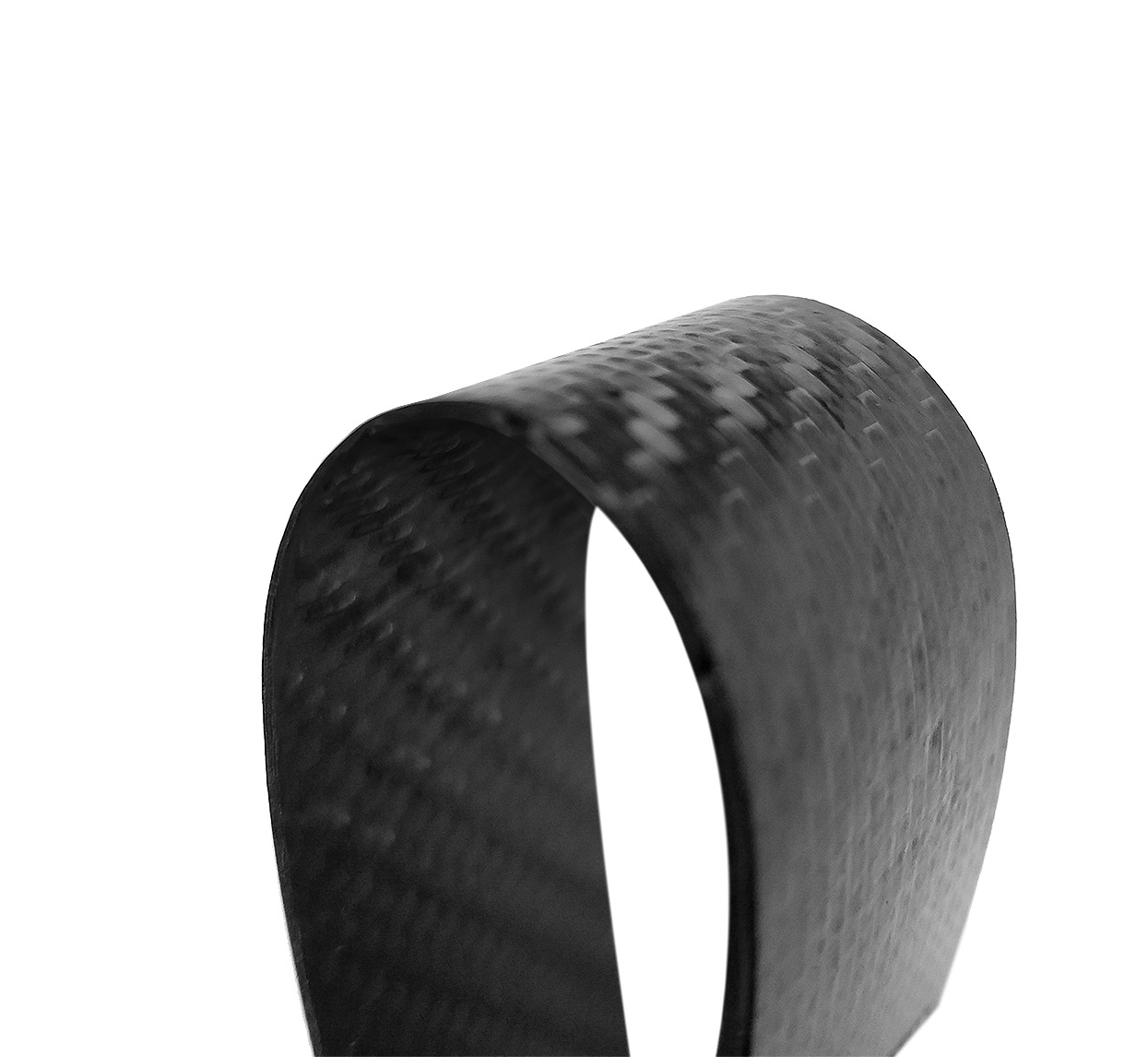
laminado. "Por lo general, en los compuestos, la palabra 'pandeo' se atribuye a fallas", dice Khan, "pero hemos ideado formas de permitir que la fibra se pandee pero no se rompa". Esta invención, agrega, se hizo inicialmente por accidente, ya que un colega se dio cuenta de que una cierta combinación de capas de fibra y polímero había dado como resultado un material que se pandeaba en una sola dirección. "Nos dimos cuenta de que tenía que haber algún tipo de beneficio para eso", dice Khan, "así que comenzamos a quitar las capas, para aprender cómo sucedió y luego comprender cómo podíamos hacerlo a propósito".
El producto resultante se llama AFX, donde "AF" significa "asimétricamente flexible", lo que indica que se dobla en una dirección pero es completamente rígido en la otra. Según una solicitud de patente de 2018, el producto AFX de Carbitex comprende una capa de tela tejida, una capa de preimpregnación y, en el medio, al menos una capa de polímero, que se combinan en un conjunto que luego se forma y se cura. "La disposición en capas tiene una alta resistencia a la flexión en una primera dirección y una baja resistencia a la flexión en una segunda dirección opuesta", dice la patente.
"Nuestra tecnología permite el nivel de rigidez y protección en la dirección que desee", agrega Khan. Una bota de senderismo que incorpora una entresuela de fibra de carbono AFX, por ejemplo, incluye el soporte y la rigidez necesarios para proteger el pie de doblarse en sentido contrario en terrenos irregulares o verticales, pero “cuando vas a doblar el pie para caminar sobre terreno plano, [ la bota es] tan flexible como, digamos, una zapatilla para correr ”, dice. AFX también es más ligero que la combinación de tablas y materiales de goma que se utilizan a menudo para reforzar las botas de montaña.
El tercer producto de Carbitex se llama DFX, un derivado de AFX que significa "Dynamically Flexible", lo que significa que la rigidez del material dentro del zapato cambia a medida que se mueve el pie. Con DFX, "puedes tener [un zapato] que será súper flexible en ciertos ángulos y luego se volverá progresiva o exponencialmente más rígido en ángulos más altos", dice Khan. "En el calzado, esto se correlaciona directamente con el rendimiento". Según su solicitud de patente de 2020, DFX consta de al menos tres capas ensambladas y curadas en un laminado:una capa de tela tejida flexible reforzada con aglutinante; una capa de tejido más rígido; y al menos una capa de polímero.
Khan señala que una zapatilla para correr o una cala pueden ser suaves y flexibles cuando un atleta camina hacia una pista o hacia un campo, y luego, una vez que el corredor despega y el pie comienza a doblarse en ángulos más altos, la zapatilla se volverá más rígida para soportar el movimiento . "Las empresas ya no tienen que comprometerse y elegir una rigidez específica en la parte media del pie; podemos identificar las diferentes funciones de una actividad determinada y diseñar la rigidez en torno a eso".
“Otra forma de verlo es que DFX aumenta el rendimiento del pie, actuando como músculos o ligamentos que se vuelven flexibles o rígidos dependiendo de la forma en que se estiren. El material AFX actúa más como una articulación como el codo o el tobillo; está diseñado para doblarse muy bien en una dirección ”, agrega.
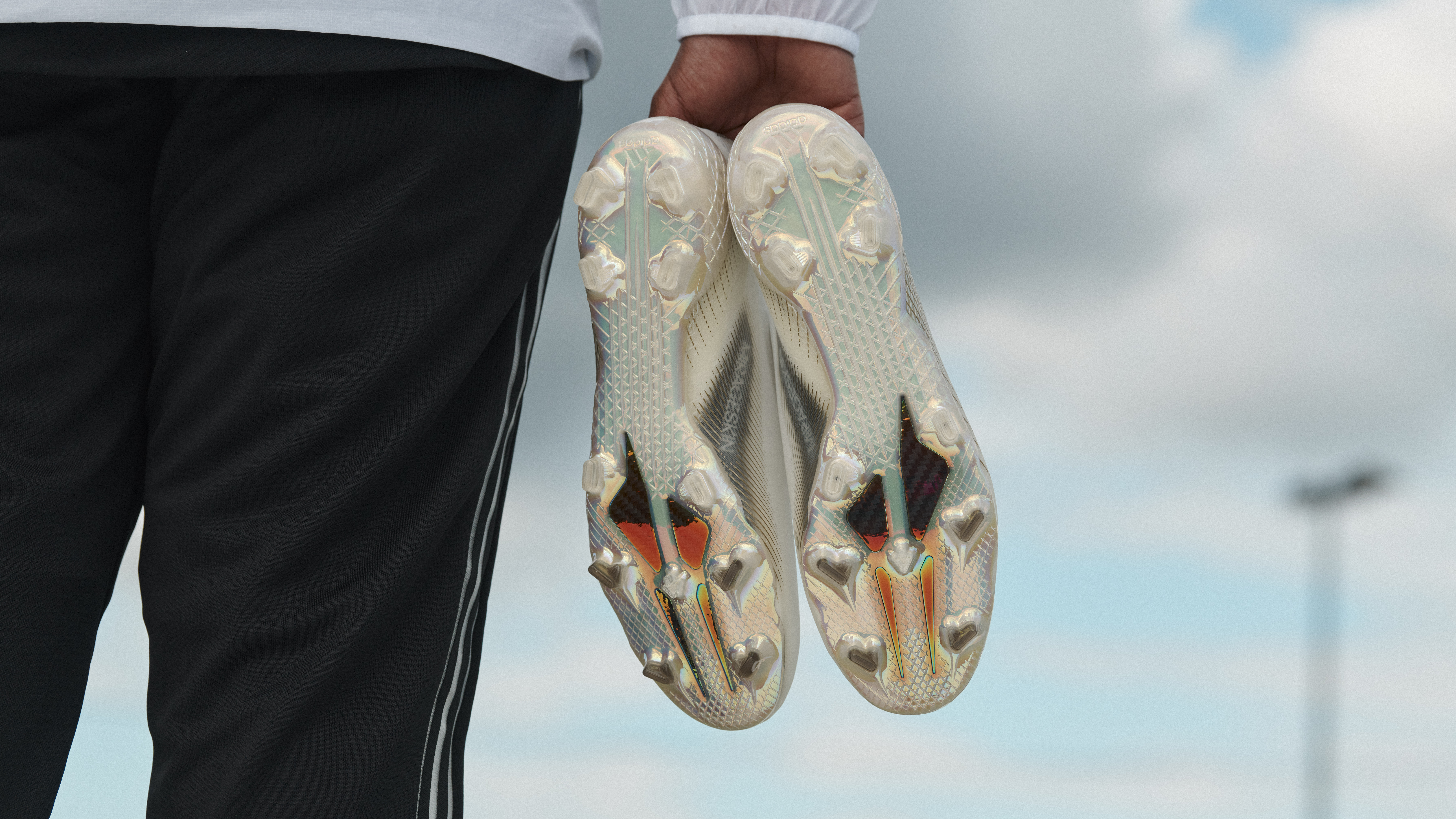
Cada iteración de material hasta ahora ha sido especialmente diseñada para un rango de rendimiento particular y un nivel de integración de fabricación identificado como aplicable a la industria, con espacio para la personalización dentro de eso, como requisitos específicos de rigidez o durabilidad. La empresa también ofrece muestras personalizadas a clientes potenciales. “Recopilamos continuamente datos sobre nuestros compuestos y cómo funcionan y por qué, y hemos construido nuestros propios sistemas de modelado para convertir diferentes versiones según sea necesario con bastante rapidez. Por lo general, dentro de uno o dos días de recibir una consulta, podemos tener una muestra personalizada y salir por la puerta ”, agrega Khan.
Más allá del calzado
“En este momento, nuestro objetivo es continuar expandiéndonos dentro del calzado y tratar de aprovechar esa oportunidad”, dice Khan. Sin embargo, un objetivo a largo plazo es que la empresa crezca hacia otras industrias, como aplicaciones aeroespaciales y médicas.
“Una industria que es realmente una prioridad para nosotros, tanto como un mercado donde nuestros productos tendrían un beneficio real como también como una que tiene algunas similitudes con el calzado, es el ámbito ortopédico y protésico, y tal vez incluso el lado robótico también. " él dice. La flexibilidad dinámica en las prótesis, agrega, se logra actualmente a través de actuadores hidráulicos y sistemas electrónicos pesados y costosos. Khan prevé el uso de los productos de Carbitex en aplicaciones como rodilleras o soportes para la espalda, donde el material podría diseñarse para evitar ciertos movimientos o hiperextensiones, al tiempo que permite otros movimientos. Él agrega:"Con un aparato ortopédico, normalmente inmovilizas parte del cuerpo de alguien debido a un solo movimiento que sería realmente malo para él". La clave sería hacer un aparato ortopédico que limite una dirección de movimiento, pero que le permita a la persona moverse en otras direcciones ". En consonancia con este objetivo, Carbitex ha comenzado recientemente a desarrollar una aplicación con una empresa que fabrica aparatos ortopédicos para niños. Los materiales de la compañía también se han utilizado, dice Carbitex, para desarrollar una almohadilla de fibra de carbono para una manga de compresión diseñada para excursionistas, y un collarín que se conecta al casco y hombreras de un jugador de fútbol americano para evitar que el cuello se rompa hacia atrás durante el juego.
En la búsqueda de otras aplicaciones, Carbitex espera utilizar sus productos para eliminar los compromisos materiales en otras industrias, como aspira continuamente a hacerlo en el calzado. Khan agrega:"Suena mejor decir que se esfuerza por obtener productos que lo hagan más rápido, mejor y más fuerte, y lo estamos haciendo, pero en última instancia, siempre estamos presionando por la eficiencia".
Resina
- Fibra de carbono
- 3 beneficios de un reloj de fibra de carbono
- Material de fibra de carbono en la industria aeroespacial:lo que debe saber
- ¿Qué es la fibra de carbono unidireccional?
- El papel del material compuesto en la industria automotriz
- Por qué la fibra de carbono es un excelente material de fabricación para joyería
- ¿Qué es la fibra de carbono?
- El auge de los plásticos reforzados con fibra de carbono
- Plástico reforzado con fibra de carbono (CFRP)
- Beneficios del calzado de fibra de carbono
- Reciclaje de materiales compuestos:no más excusas