Avanzando la caja de ala infundida OOA
A medida que la industria aeroespacial anticipa su recuperación de la pandemia de COVID-19, el impulso anterior por una producción de alta velocidad se ha convertido en un impulso urgente para reducir las amenazas ambientales al planeta y a las personas. Este esfuerzo incluye límites en las emisiones de gases de efecto invernadero (GEI), el uso de energía y agua y la creación de desechos que no se pueden reciclar. Aunque estas iniciativas estaban en curso antes de COVID, su énfasis ahora es mayor, al igual que la necesidad de un costo mucho menor para producir estructuras compuestas. El programa de aviación paneuropeo Clean Sky 2 ha financiado la investigación y el desarrollo en todas estas áreas y ha avanzado significativamente en una variedad de tecnologías de compuestos reforzados con fibra.
En la séptima convocatoria de propuestas de Clean Sky 2 (CFP07, octubre de 2017) está la solicitud de Airbus Defence and Space (Airbus DS, Cádiz, España) de una planta piloto innovadora y flexible para producir un demostrador de vuelo de caja de ala altamente integrado utilizando fibra automatizada. colocación (AFP) e infusión de resina líquida.
Ha habido otros demostradores de caja de ala con infusión de resina y / o fuera de autoclave (OOA), incluida una caja de ala "mezclada" OOA presentada por GKN Aerospace (Redditch, Reino Unido) en 2013; el ala del Airbus A220 producido por Spirit AeroSystems Belfast en Irlanda del Norte utilizando una infusión de transferencia de resina en un autoclave; y el ala OOA producida por AeroComposit (Moscú, Rusia) para el MS-21 avión de reacción. Sin embargo, todos ellos han ensamblado pieles y largueros reforzados con largueros compuestos discretos con sujetadores mecánicos (consulte "El camino hacia las alas OOA con un mínimo de sujetadores").
La caja de ala solicitada por Airbus DS en Clean Sky 2 era dar un paso adelante al integrar la piel inferior rígida con largueros delanteros y traseros reforzados, lo que permite un módulo más completo sin sujetadores que se enviarán para ensamblar con los componentes restantes del ala.
Esta caja de ala también usaría cintas de fibra de carbono seca estrechas (0.25 o 0.5 pulgadas de ancho) y alta temperatura (180 ° C T g ) resinas de curado, pero con sistemas de calefacción de bajo costo y ahorro de energía y control y simulación digital basados en sensores para predecir y administrar el procesamiento, acortar los ciclos de prueba y error durante el desarrollo y permitir una capacitación rápida del personal de fabricación. Esta digitalización evolucionaría para incluir una aplicación móvil de realidad aumentada (app) que también proporciona manuales de usuario y mantenimiento, definición de secuencia de proceso, proceso sin papel y seguimiento de piezas y proyección de modelos CATIA en la pieza para ayudar en la colocación precisa de preformas de refuerzo, insertos de herramientas. y placas de sellado de polímero reforzado con fibra de carbono (CFRP).
Tal vez el más exigente, este proyecto requirió que todas las herramientas y equipos de fabricación fueran portátiles y flexibles, fáciles de implementar en cualquier sitio de fabricación y adaptables para otros diseños de piezas y actualizaciones a medida que se disponga de tecnologías de control de procesos 4.0 de herramientas, calentamiento y compuestos más avanzadas.
Tal y como ha explicado el director de temas Luis Rubio, jefe de ingeniería de desarrollo de compuestos - tecnología y proceso en Airbus DS, “El objetivo final del proyecto es demostrar que una tecnología alternativa (preimpregnado y autoclave) con costes más bajos, tiempos de entrega reducidos y La huella ambiental puede lograr tolerancias de diseño y niveles de calidad similares ”.
MTorres (Torres de Elorz, España) respondió, postulando sin socios. “Teníamos todas las capacidades internas:AFP, infusión, materiales de cinta seca y automatización”, explica Sebastián Díaz, gerente senior de tecnologías aplicadas de compuestos en MTorres. La compañía recibió el proyecto Innovative Infusion Airframe Manufacturing System (IIAMS), financiado a través del programa Horizon 2020 de la Unión Europea en virtud del acuerdo de subvención n.o 820845, y comenzó a trabajar en octubre de 2018.
Demostrador de caja de ala exterior
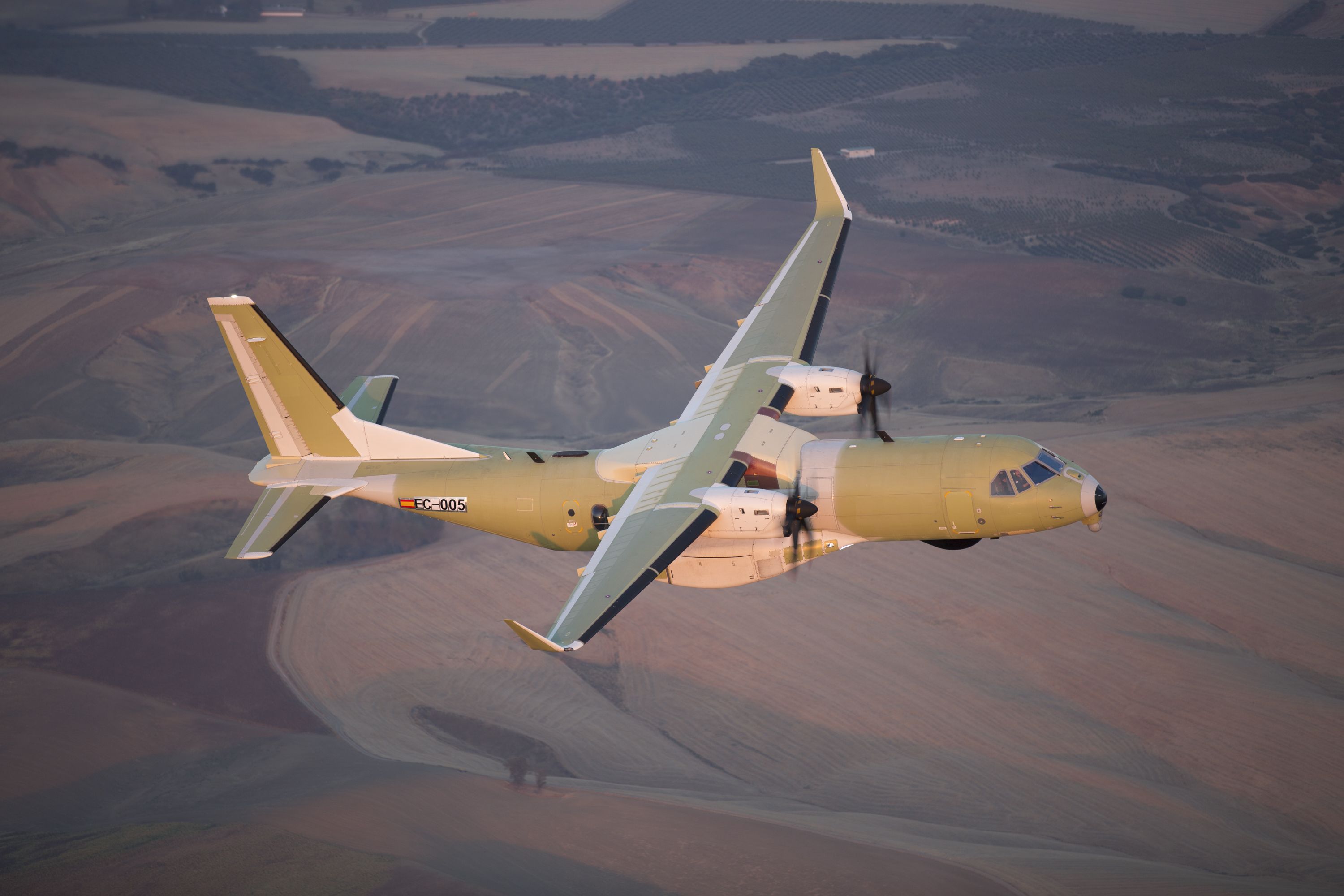
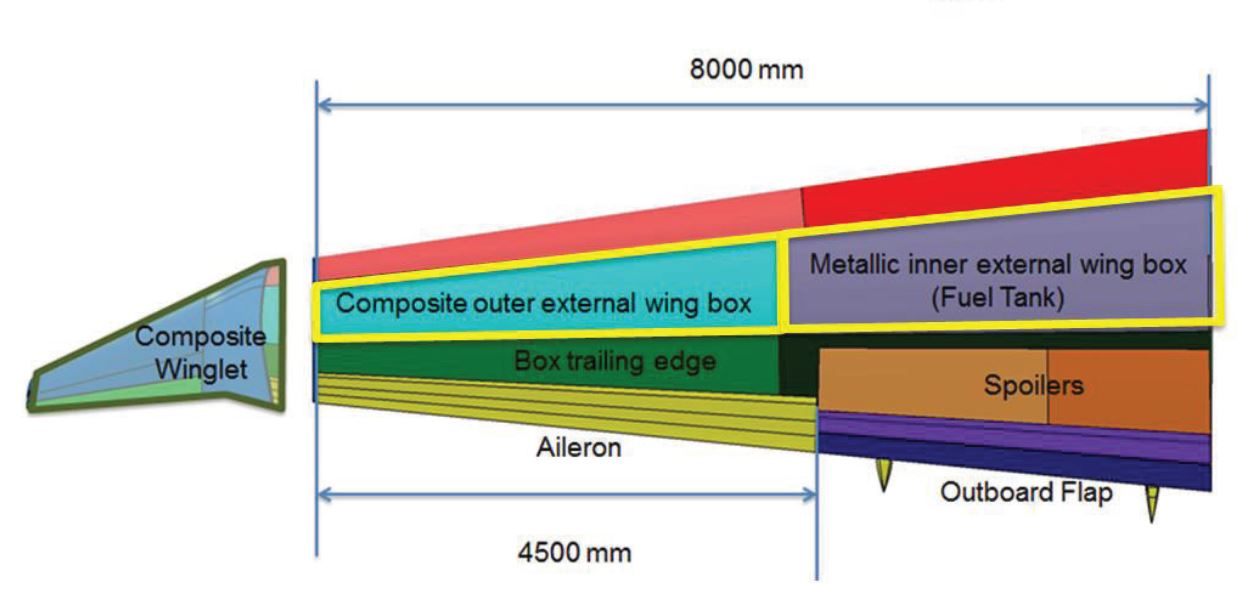
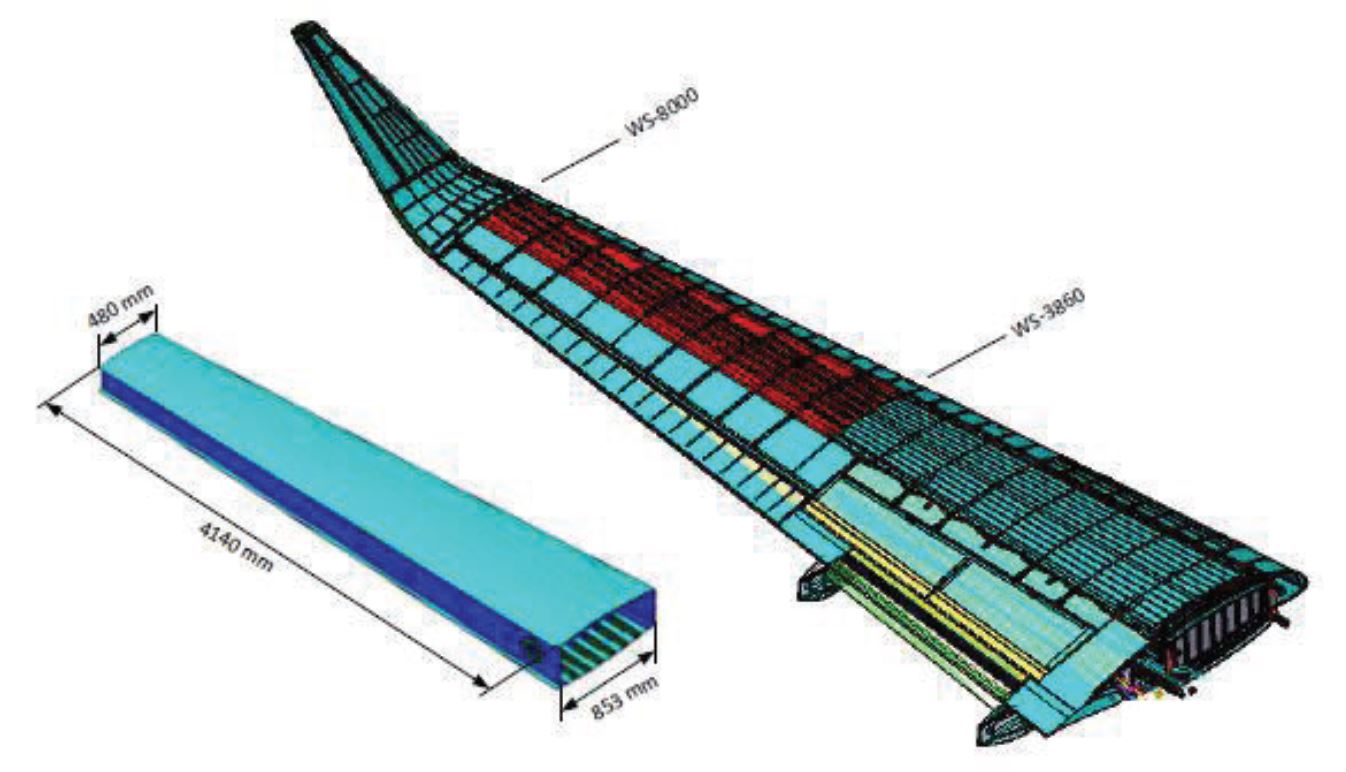
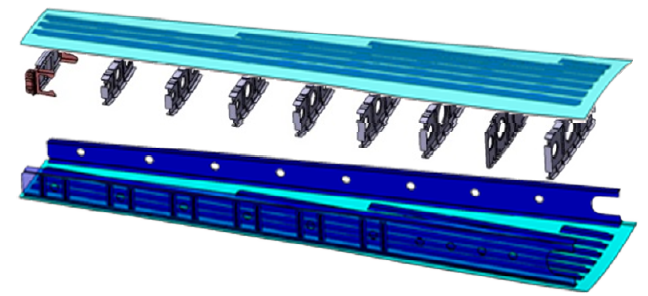
El demostrador que eligió Airbus DS fue una caja de ala exterior basada en su transporte militar de doble turbohélice C-295 (Fig. 1), producido en San Pablo, Sevilla, España. Esta caja de torsión exterior compuesta de 4,14 metros de largo se acopla a un metal interior caja de torsión. La caja de ala compuesta también se adhiere a una aleta, borde de ataque y borde de fuga.
“Íbamos a fabricar dos demostradores de 4 metros de largo, las alas derecha e izquierda, que se instalarán para las pruebas en vuelo”, dice Díaz. “La fabricación debía ser un proceso de una sola vez, sin uniones secundarias. Hicimos solo la "U", que comprende la piel inferior con seis largueros integrados y los largueros a cada lado. La piel, los largueros y los largueros varían en grosor. La forma de J de los largueros y la integración de sus refuerzos fue bastante difícil de fabricar. También enfrentamos el desafío de cómo mantener tolerancias estrictas y geometría precisa con este proceso de fabricación. Esta precisión es fundamental, especialmente en la raíz para el montaje en la caja del ala interior y luego también en la aleta ”.
El diseño de la fabricación industrial innovadora se desarrolló en MTorres, mientras que Airbus DS proporcionó las especificaciones de diseño de la pieza. “Trabajamos juntos fácilmente para diseñar el mejor proceso de fabricación, verificando que este diseño pudiera ser producido por nuestro proceso y viceversa”, dice Díaz.
Centro automatizado de termoinfusión (ACTI)
Según la especificación de Airbus DS, todas las herramientas y equipos de fabricación utilizados para producir la caja del ala deben ser portátiles, poder transportarse a otras instalaciones con vehículos estándar y configurarse rápidamente sin medidas especiales. Esto condujo al desarrollo del centro automatizado de termoinfusión (ACTI), que realiza el conformado en caliente de larguerillos y largueros; infusión de largueros, largueros y piel; y ciclos de curado. La formación de cortinas en caliente (HDF), desarrollada como reducción de volumen en caliente en aeroestructuras y como preformación en caliente fuera del espacio aeroespacial, elimina los huecos en las capas y convierte los espacios en blanco 2D para los largueros y largueros en preformas con forma (consulte "Formación de cortinas en caliente").
El ACTI tiene un área interior útil de aproximadamente 5,5 x 2,2 metros y se parece a un sistema HDF tradicional, con un marco de acero y una mitad superior que se sube y baja electrónicamente, con bloqueo y otros dispositivos de seguridad. La herramienta de curado y varias herramientas de formación de cortinas calientes se colocan dentro del ACTI. “No se aplica presión, solo vacío”, señala Díaz. "ACTI utiliza aire calentado con un flujo de aire que se ha definido para proporcionar una rápida transferencia de calor tanto en los procesos de formación como en los de infusión".
También señala que el sistema es autonivelante. “La rigidez de la estructura ACTI (y la herramienta de curado) ha sido diseñada para cumplir con las tolerancias bajo cargas operativas en una condición simplemente apoyada en solo dos secciones de soporte”, explica Díaz. “Esto significa que se mantiene la precisión dimensional cuando se descansa sobre el piso, sin que se requiera más nivelación u otro ajuste geométrico. ACTI también presenta bajos costos de energía y fabricación ”.
Esto último se debe, en gran parte, al reemplazo del ensamblaje de múltiples piezas curadas con ensamblaje de múltiples preformas, que luego se infunden y curan en una única estructura integrada. “La herramienta de curado también es la herramienta de ensamblaje”, dice Díaz. "Todos los elementos son preformas secas ensambladas en la herramienta de curado y luego co-infundidas juntas en un proceso de un solo disparo". No se necesita una plantilla de montaje y se logran tolerancias estrictas a través de elementos innovadores en las herramientas.
Otro aspecto clave de este enfoque es eliminar las pruebas destructivas y no destructivas (NDT), confiando en su lugar en los datos del proceso recopilados durante los diversos pasos de fabricación para verificar la calidad del proceso y marcar los parámetros fuera de especificaciones. Los sensores que se utilizan con el ACTI recogen la temperatura, el vacío, el flujo de resina y el estado de curado. “Se monitorean tanto la temperatura del aire como la temperatura de las piezas”, dice Díaz. "Las herramientas tienen termopares integrados que controlan la temperatura de los moldes y las superficies de las piezas". Todos los datos se registran, analizan y utilizan para imprimir gráficos y ayudar a guiar las decisiones de fabricación.
“Tanto en IIAMS como en proyectos futuros, los datos ayudan a mejorar la configuración del proceso en las primeras etapas”, explica Díaz. El flujo de resina y el estado de curado se controlan mediante sensores dieléctricos Netzsch (Selb, Alemania), instalados directamente en las herramientas de curado de CFRP. “Necesitábamos sensores sin contacto para la piel porque no hay contacto directo entre la resina y el moho”, dice Díaz. “Los sensores controlan el cambio del campo dieléctrico a medida que llega la resina y luego se solidifica durante el curado. Usamos estos datos para acortar el ciclo de curación ”.
Más adelante en el proyecto, los sensores y ACTI se combinaron con una interfaz hombre-máquina (HMI) desarrollada por MTorres, que permite un verdadero control del proceso desde una computadora, incluido el vacío y la temperatura, así como el flujo de resina a través de la válvula de alimentación. El objetivo, según Airbus DS, es avanzar en la producción en masa de estructuras primarias compuestas integradas haciendo que el proceso sea más ágil e inteligente.
Portabilidad y herramientas livianas
MTorres produjo dos juegos de moldes, uno para el ala derecha y otro para el ala izquierda. “Las piezas con geometría idéntica, como los refuerzos, tenían un solo juego”, señala Díaz. "Se compartieron otras herramientas, cuando fue posible".
Se usó una herramienta de curado de una sola pieza para formar la forma 3D de la piel, sobre la cual se ubicaron todas las demás preformas. Con aproximadamente 4,5 metros de largo, las versiones derecha e izquierda de esta herramienta se hicieron con CFRP, dice Díaz. “Esto facilita el mantenimiento de las tolerancias porque diseñamos las herramientas con la misma disposición y procesamiento que las piezas, por lo que el CTE está muy cerca del de la pieza final. Estas herramientas de curado de CFRP también son livianas, aproximadamente 200 kilogramos y, por lo tanto, se pueden mover con una pequeña carretilla elevadora eléctrica. Esto sería imposible si usáramos metal para una herramienta de 4,5 metros de largo ”.
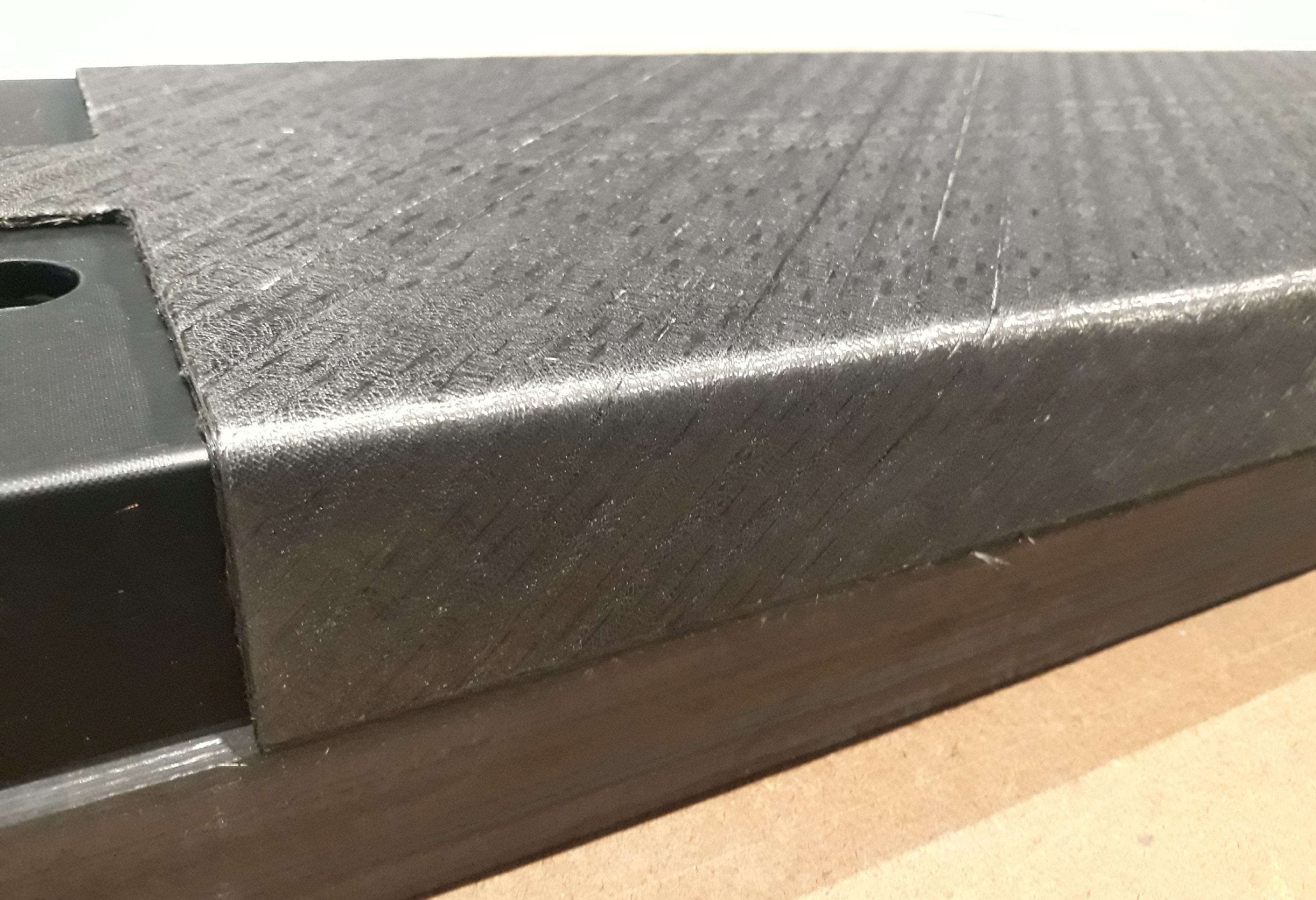
El resto de las herramientas (calafateo, posicionadores y herramientas HDF) se manejaban fácilmente a mano. La HDF de los largueros, largueros y preformas de refuerzo del larguero utilizaba herramientas macho (IML), también fabricadas con CFRP. Durante su uso, estos se montaron en una mesa de aluminio y se colocaron dentro del ACTI.
AFP con cinta de fibra seca novedosa
Todos los elementos estructurales de la caja del ala (piel, largueros, largueros, refuerzos de larguero) se produjeron utilizando tecnología MTorres AFP para cintas de fibra seca. “La convocatoria de la propuesta decía utilizar materiales rápidos y baratos”, dice Díaz. “Pero las cintas de fibra seca disponibles comercialmente, especialmente de los proveedores más grandes, no eran tan fáciles de comprar y teníamos la experiencia para fabricar nuestro propio material (consulte“ Cinta seca novedosa para compuestos moldeados líquidos ”). Entonces, usamos nuestra cinta de fibra de carbono seca de 0.5 pulgadas de ancho, 300 gramos por metro cuadrado (gsm) hecha de fibra Mitsubishi Rayon (Tokio, Japón) 50K de alta resistencia (HS). Nuestra cinta fue diseñada para facilitar y funcionar bien durante la infusión, pero también durante la colocación con nuestros cabezales AFP. Conocemos todos los parámetros para el laminado de AFP, la formación de láminas en caliente y la infusión de resina, y si necesitábamos hacer algún pequeño cambio, podíamos hacerlo porque teníamos la línea de fabricación de cinta disponible ”.
MTorres también probó su proceso de fabricación de cajas de ala con cinta de 200 g / m2 de Hexcel (Les Avenières, Francia) hecha de su fibra de módulo intermedio (IM). “Aunque nuestro proceso puede funcionar bien con ambos tipos de cintas”, dice Díaz, “durante la fase de desarrollo, fue más fácil y económico colocar con nuestro material en comparación con el material disponible comercialmente; el ancho y la rigidez se diseñaron para que su comportamiento fuera carretes a la mesa fue suave y rápido. También estaba disponible ".

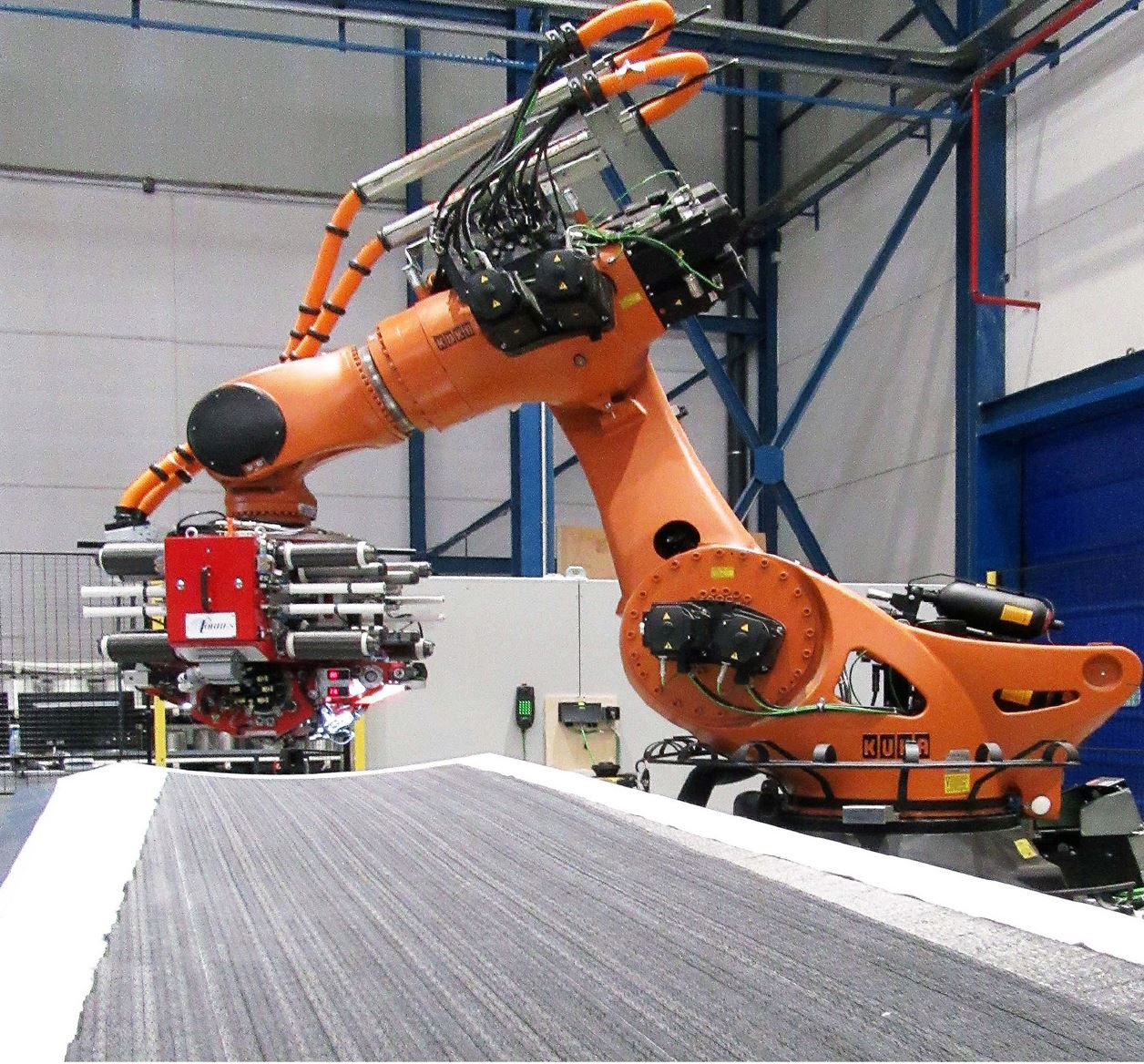
Paso 1. Se utilizó AFP para colocar la piel de la caja del ala (que se muestra aquí), así como espacios en blanco 2D para largueros, largueros y refuerzos de larguero. Crédito de la foto, todos los pasos: Proyecto IIAMS, Airbus Defence and Space, MTorres.
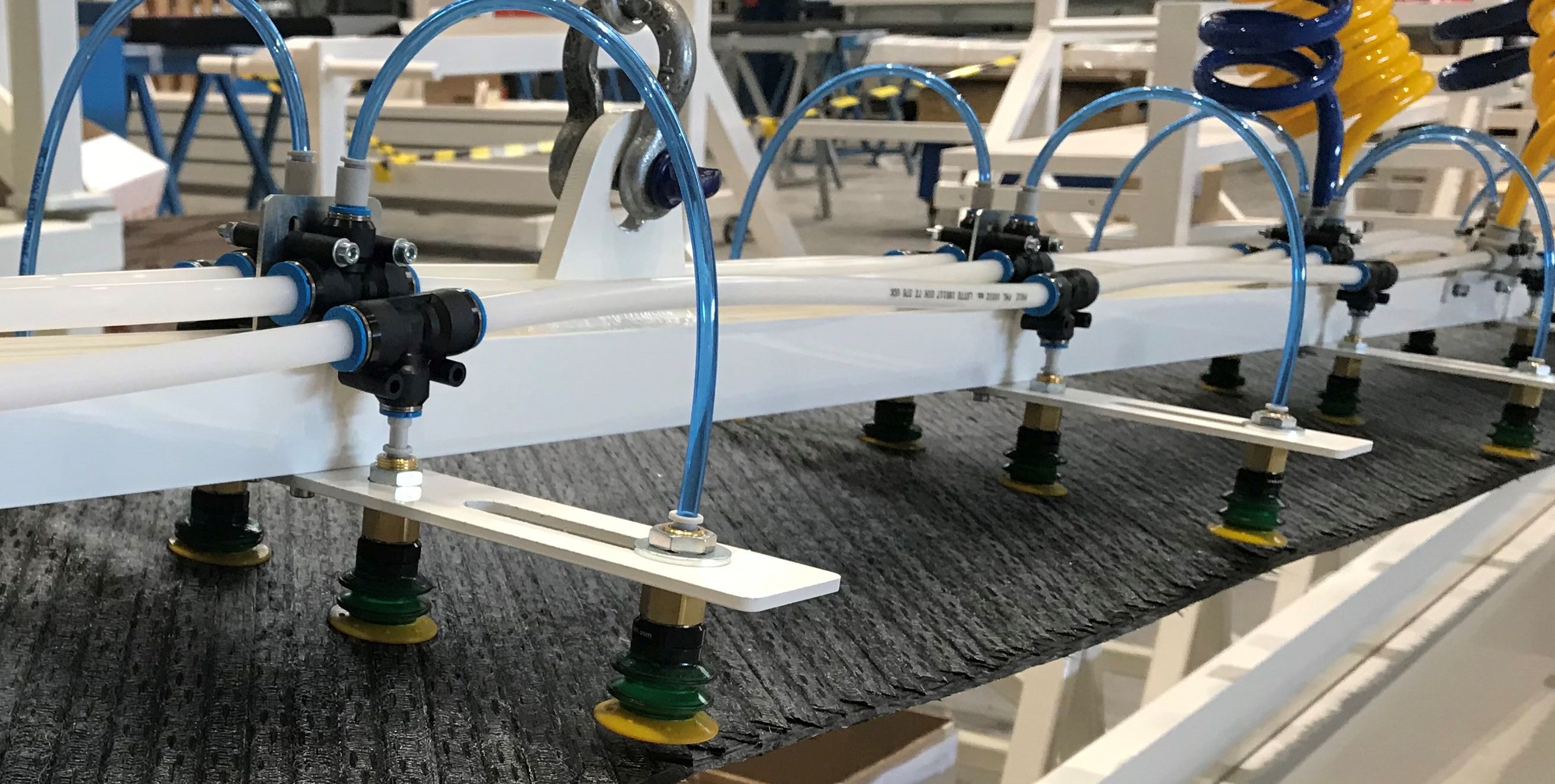
Paso 2. Los espacios en blanco de cinta plana se transportaron desde la mesa de colocación a las herramientas de formación de cortinas en caliente.
Señala que se siguieron dos estrategias para AFP:una para la piel inferior y otra para los largueros, largueros y refuerzos de larguero. La piel (de 3 a 6 milímetros de grosor) se colocó con la forma 3D final en la parte superior de la herramienta de curado (paso 1), usando una membrana semipermeable, patentada por Airbus en su infusión de proceso asistido por vacío (VAP). Los largueros, largueros y refuerzos de larguero se colocaron como espacios en blanco planos (2D) sobre una mesa de vacío y luego se movieron a las herramientas HDF para lograr su forma 3D final (Paso 2).
Preformado calentado
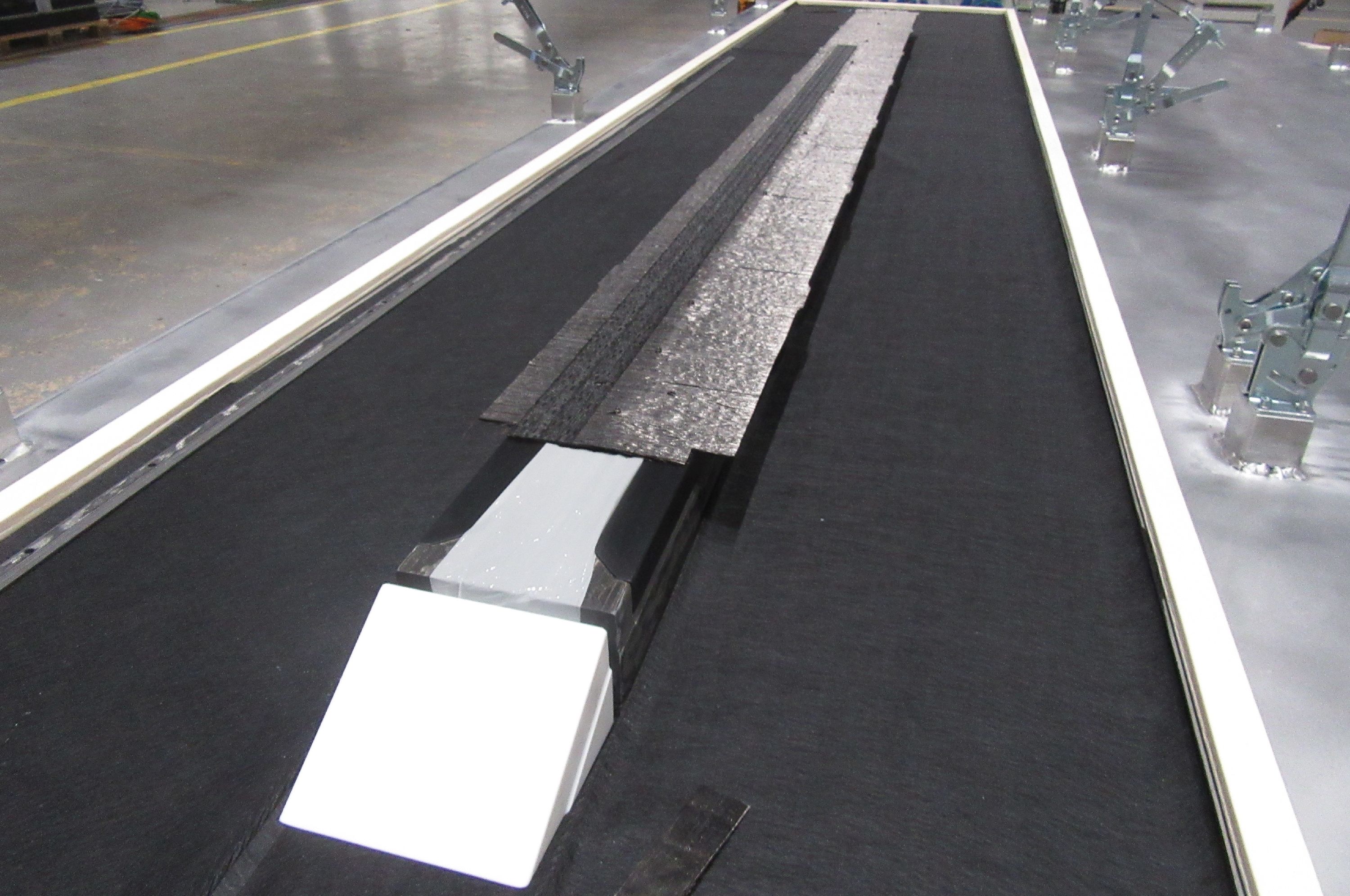
Paso 3. La pieza en blanco del larguero se coloca encima de la herramienta HDF macho.
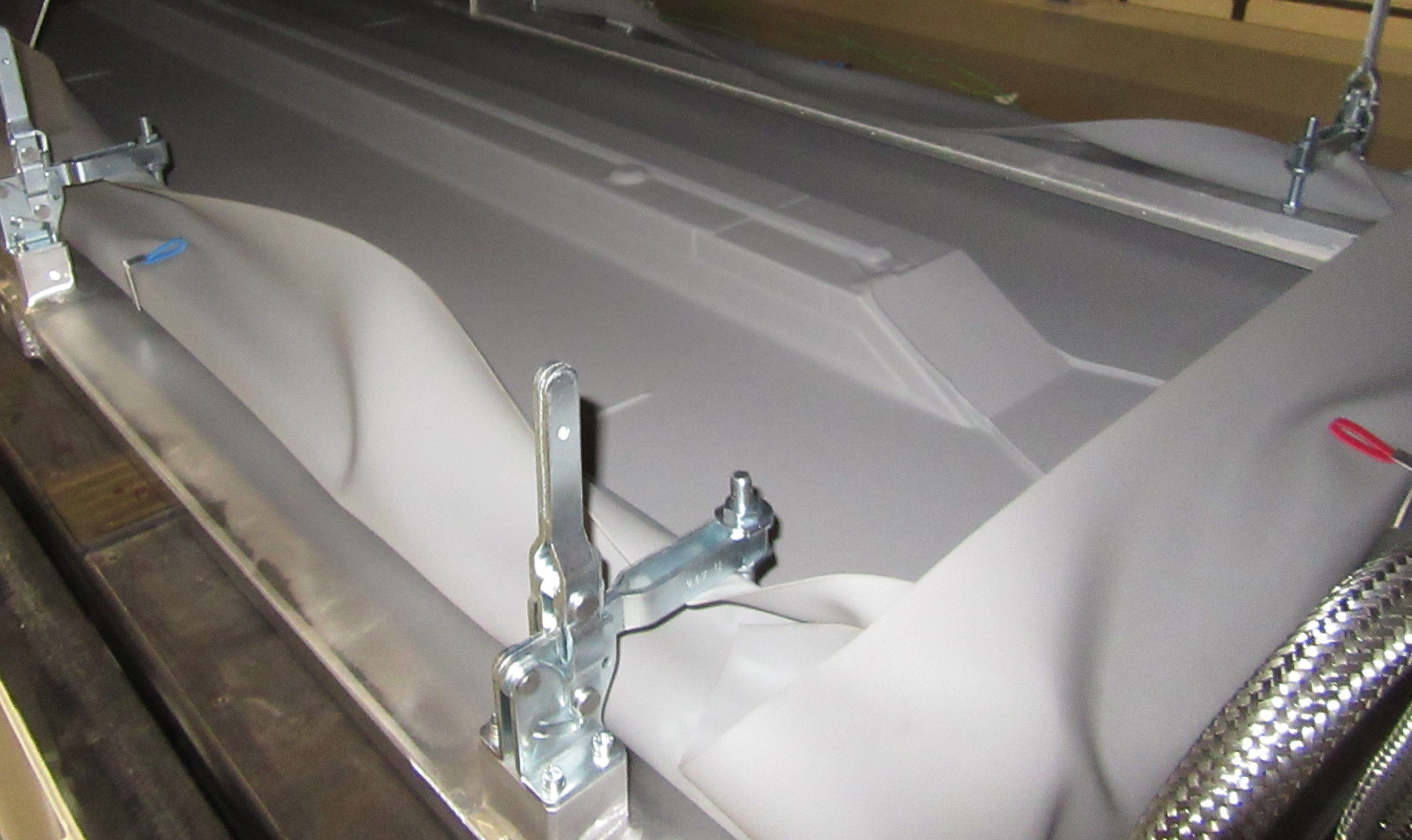
“Movimos los espacios en blanco planos para los largueros, largueros y refuerzos de larguero de la mesa de laminado a la estación de conformado en caliente utilizando un pórtico con pinzas de vacío”, explica Díaz. "El sistema automatizado puede mover los espacios en blanco en un estado plano y colocarlos en las herramientas de formación macho [Paso 3] sin crear arrugas". Las herramientas de formación se instalaron en una mesa de formación de aluminio, que se colocó en el ACTI. Se colocó una bolsa de vacío de silicona reutilizable (Mosites Rubber Co., Fort Worth, Texas, EE. UU.) Encima de los espacios en blanco, que luego se calentaron en el ACTI a 130 ° C y se moldearon usando presión de vacío (Paso 4). "El vacío se aplicó suavemente siguiendo una rampa predefinida por medio de una válvula de control cuando se alcanzó el punto de ajuste de temperatura", dice Díaz.
Señala que las cintas secas son más fáciles de preformar / formar en caliente, “porque la unión entre capas es más suave que en los preimpregnados. A pesar de ser material seco, es un HDF / debulking calentado en el que la preforma resultante mantiene la forma gracias a los aglutinantes incluidos en las cintas ”.
Para los largueros y los refuerzos de los largueros, los espacios en blanco se formaron en dos L, que luego se colocaron espalda con espalda en la herramienta de curado para formar largueros / refuerzos en T. Cada uno de los seis larguerillos de piel es diferente y requiere espacios en blanco de diferentes formas para crear las preformas. Cada uno de los 24 refuerzos de mástil también tiene una longitud diferente.
Los largueros en J delanteros y traseros comprenden un espacio en blanco formado en una C, que mira hacia el interior de la caja del ala, y otro en blanco formado en una Z que mira hacia el exterior; los dos se colocan espalda con espalda. Los largueros también tienen patas de forma sinusoidal en la parte exterior de la caja del ala (flecha en el paso 7). “Cortamos la forma de las patas del larguero en la mesa plana antes de mover la pieza en bruto a la estación de formación”, dice Díaz. “Nada se pudo recortar o moler después en esta área. Los espacios en blanco se colocaron directamente sobre la herramienta de formación macho con las patas del larguero en el lado izquierdo de la herramienta y la brida superior en el lado derecho ”.
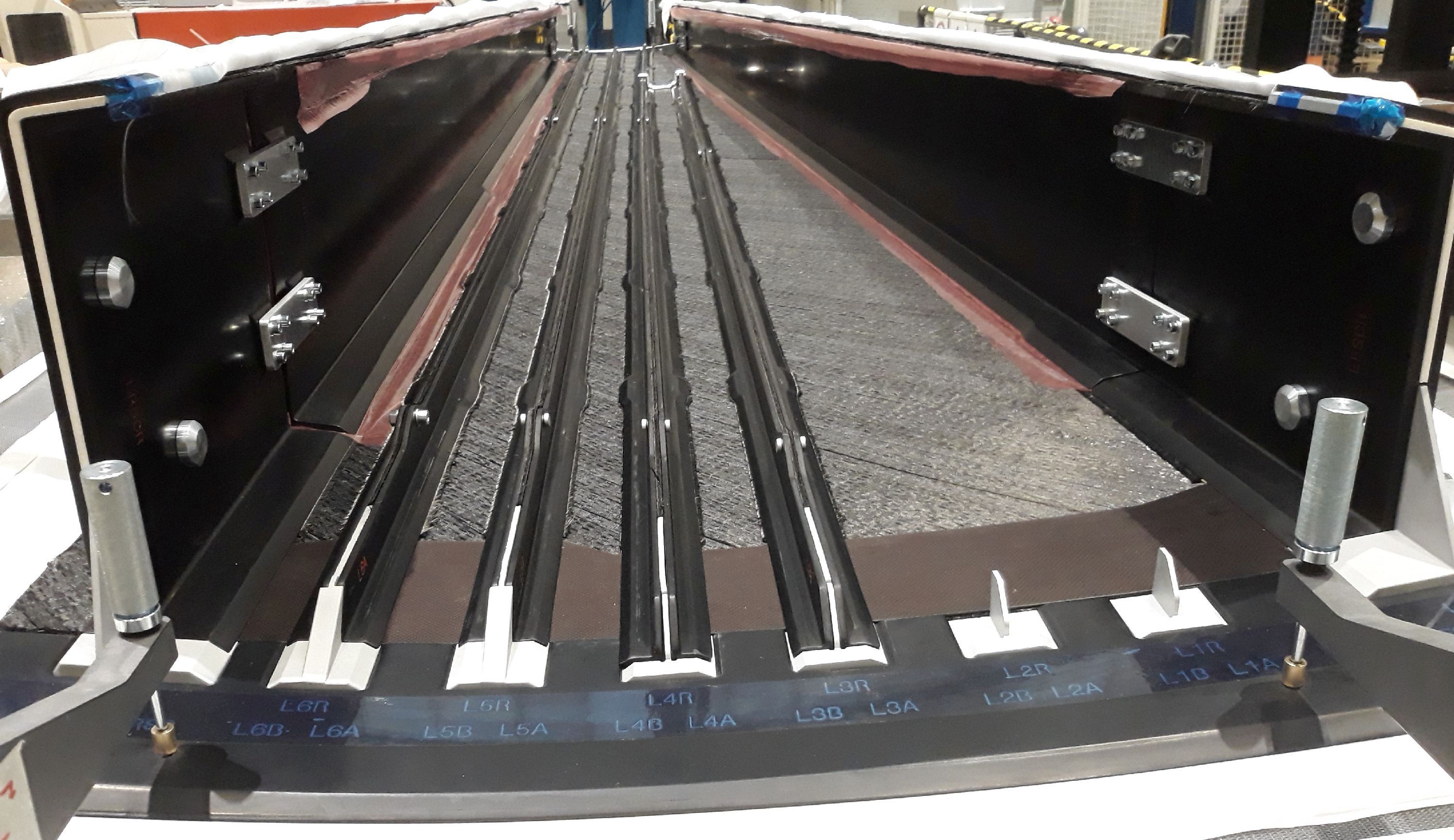
Fig. 3. Colocación precisa de la preforma. Las preformas para largueros y largueros en J se colocaron utilizando cilindros metálicos gemelos (que se ven en el extremo izquierdo y derecho), posicionadores blancos y una masilla de CFRP con cortes para los largueros / posicionadores. Crédito de la foto: Proyecto IIAMS, Airbus Defence and Space, MTorres.
Infusión única
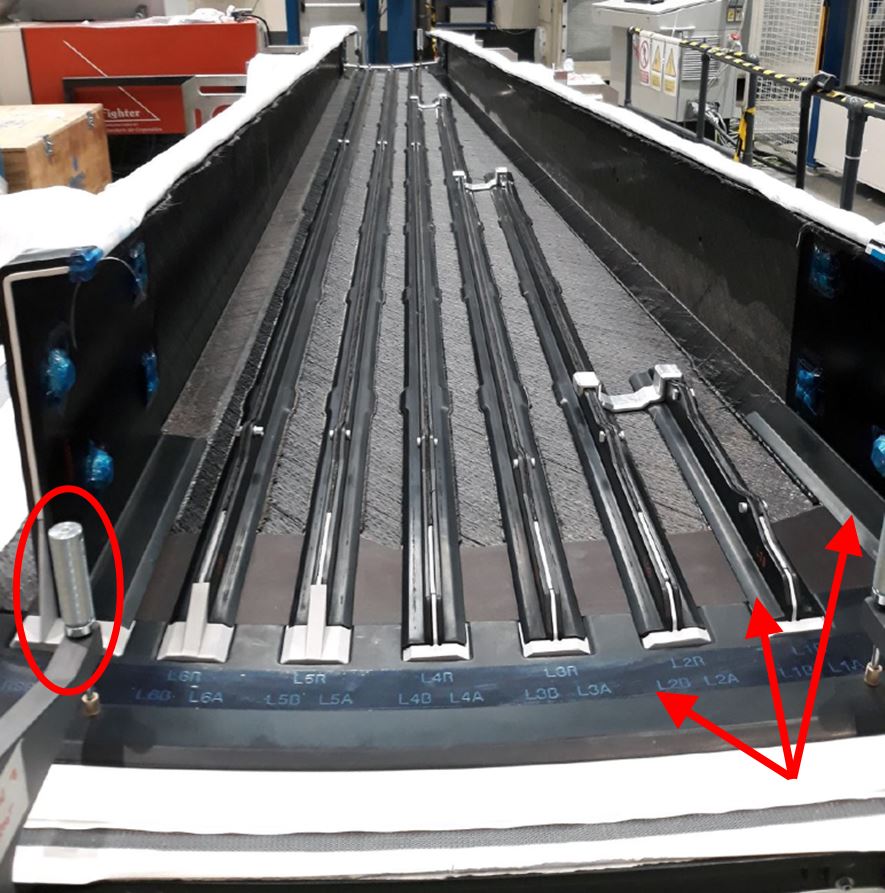
Paso 5. Se colocaron preformas de larguero y larguero en la piel inferior, con la ayuda de cilindros ( en círculos ) y elementos de posicionamiento blancos. Cauls negras de CFRP ( flechas ) también se utilizaron para ayudar a colocar los largueros y colocado encima de largueros y largueros en J.
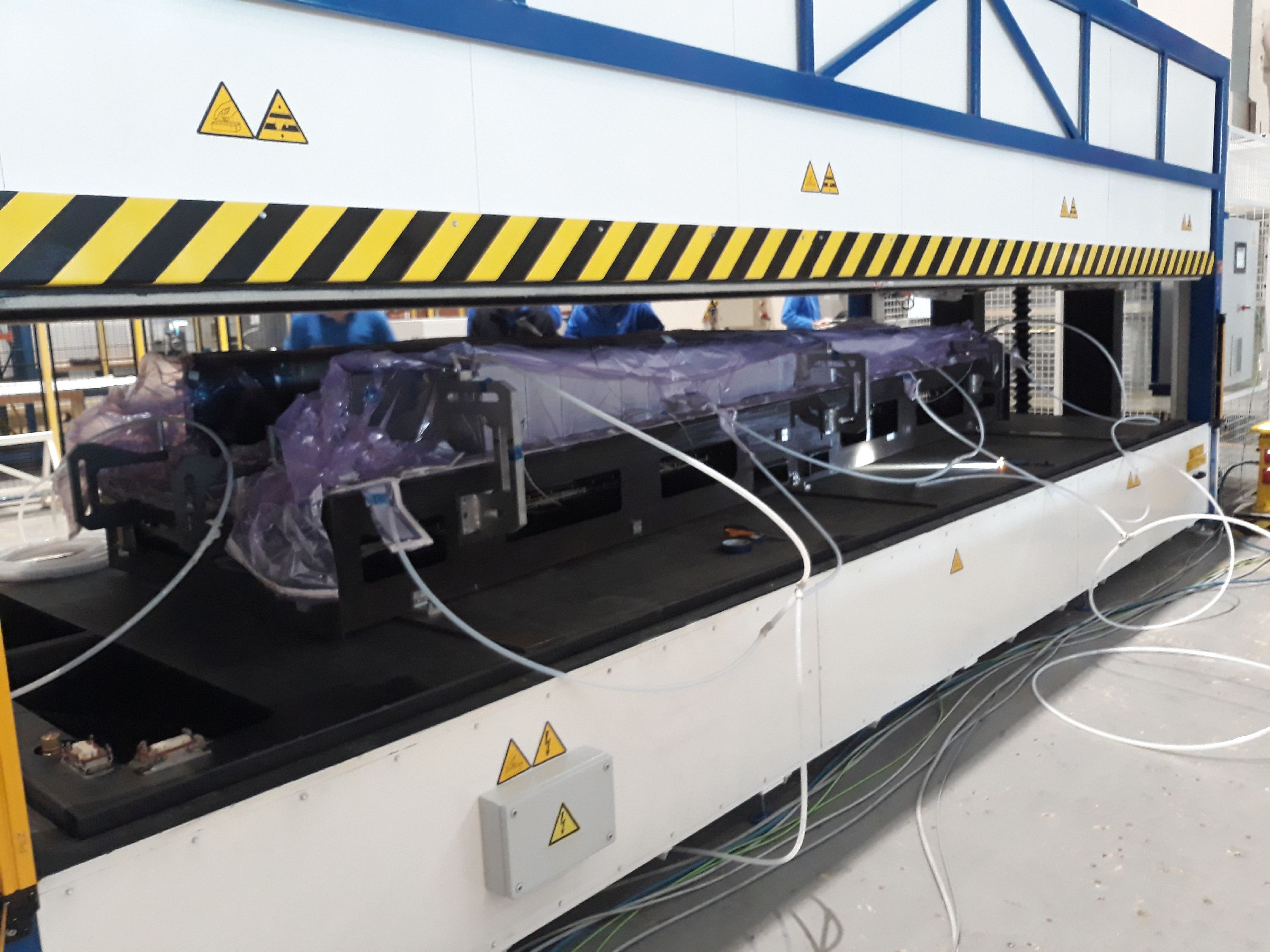
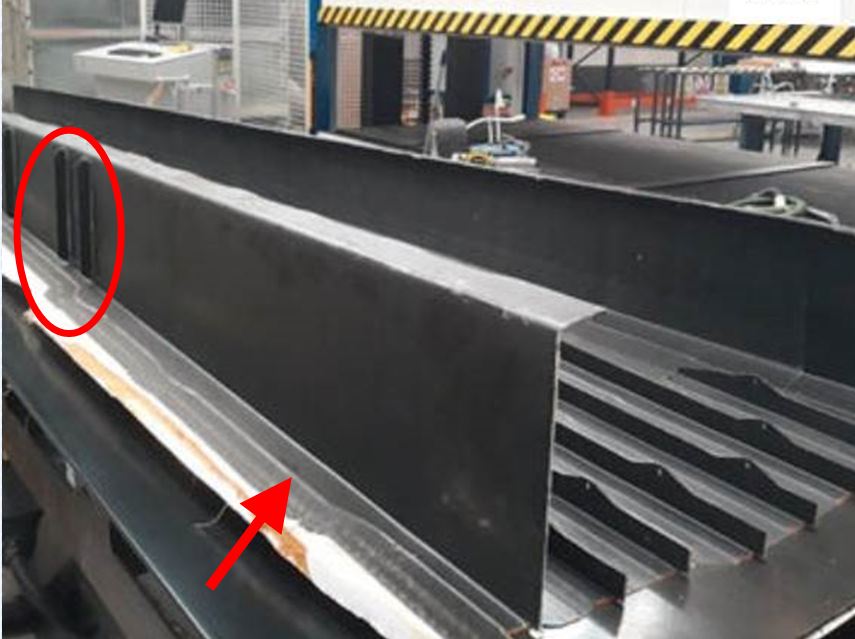
Paso 7. El demostrador inicial completado en MTorres muestra el larguero en J con dos refuerzos de costillas ( en un círculo ) y sus pies sinusoidales ( flecha ).
El siguiente paso fue colocar las preformas de larguero, larguero y refuerzo de larguero sobre la piel del ala inferior ya colocada (Paso 5). “Íbamos indexando cada preforma a medida que la colocamos sobre la piel y la herramienta de curado”, dice Díaz. Los cilindros que actúan como elementos de ubicación se pueden ver al final del larguero a la izquierda del Paso 5 y al final de ambos largueros en la Fig. 3. Estas imágenes también muestran dispositivos de posicionamiento blancos para los largueros y largueros en J. Había 13 de estos posicionadores en el ensamblaje final de la preforma, y cada uno era diferente.
Las placas de cala también fueron una parte clave del sistema de ubicación y colocación de las preformas. Cumplieron el propósito tradicional de mantener una presión y temperatura uniformes en regiones de capas y / o geometrías complejas, pero también serían clave para la infusión, como se explica a continuación. Se puede ver una placa de calafateo de CFRP negro con cortes para las preformas de largueros al final de los largueros y largueros en el Paso 5 y la Fig. 3.
“La ubicación de las preformas de larguerillos depende de la ubicación de esa cala”, explica Díaz. “La tecnología digital que desarrollamos para monitorear y controlar el proceso de fabricación incluía una aplicación de realidad aumentada que proyectaba los modelos CATIA en la bandeja. Esto se utilizó para ayudar a guiar la colocación de las placas de cala, los elementos de posicionamiento y luego las preformas. También mostró los próximos pasos a realizar. La aplicación permite la autosuficiencia en tabletas para que todos los trabajadores tengan fácil acceso a toda la información ”.
Luego se colocó un juego final de placas de calafateo negras de CFRP encima de las preformas en L para los largueros en T y también a lo largo del interior y el exterior de cada larguero en J, extendiéndose hacia arriba sobre la brida y hacia abajo sobre el pie en el exterior de la caja de ala, como se muestra en el Paso 5 y la Fig. 3. “Los largueros también utilizan una especie de placa de calafateo en el lado interno en los extremos, para obtener una mayor precisión en las áreas de las articulaciones”, dice Díaz. "Todas estas placas de calafateo se utilizaron durante el proceso de HDF y permanecieron unidas a las preformas durante la colocación".
A continuación, se cubrió el conjunto de preforma seco completo con placas de sellado con una capa despegable y una película de bolsa de vacío. A continuación, se colocó todo el conjunto de piel, larguerillos y largueros en el ACTI y se calentó el utillaje a 120 ° C. La resina epoxi Hexcel RTM6 se calentó a 70 ° C y se desgasificó antes de la infusión a través de una única ubicación de alimentación de resina. “El ACTI se preparó para alimentar resina desde cuatro ubicaciones”, señala Díaz, “pero después de una extensa simulación y pruebas, decidimos que era más fácil y económico tener una sola entrada de resina”.
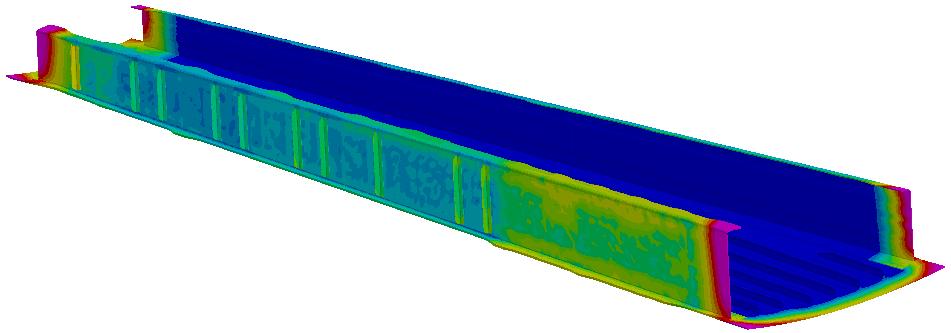
Incluso con una sola entrada, el proceso de infusión era muy complejo y comprendía tres modos diferentes. “Primero realizamos una simulación de flujo, utilizando el software PAM-RTM [ESI Group, París, Francia]”, dice Diaz. “Había una combinación tan compleja de frentes de flujo y parámetros necesarios para una humectación completa. Por ejemplo, el flujo de resina fue más rápido en el centro de la caja del ala, pero fue un desafío mojar todos los refuerzos ".
VAP, con una membrana semipermeable, funcionó bien para la piel inferior, pero se cambió por una malla de flujo de alta temperatura a lo largo de los largueros y en el interior de los largueros. “Las esquinas eran las áreas más difíciles de mojar”, señala Díaz, “pero también eran las más críticas para mantener las tolerancias para el ensamblaje, así como a lo largo de los bordes”. Esto se puede ver en las áreas rojas de la simulación de flujo en la Fig. 4. “En estas áreas, se desarrolló un enfoque personalizado para lograr las dimensiones precisas requeridas”, explica. También usamos puertos de vacío a lo largo del perímetro y en la parte superior de los largueros ”.
La infusión fue relativamente rápida, como predijeron las simulaciones, seguida de un curado de dos horas a 180 ° C, utilizando solo aire caliente y no herramientas calentadas. Después de ser demolido, cada demostrador de caja de ala se inspeccionó mediante pruebas ultrasónicas (UT). Esto se hizo como parte de los entregables del proyecto IIAMS, para analizar la calidad de los demostradores. Sin embargo, la aplicación industrial de este proceso reducirá los NDT tradicionales en favor de sensores digitales y herramientas de inspección en línea más rápidas, como los sistemas de visión.
Según Díaz, aunque el ciclo de curado por infusión fue similar al de una caja de ala preimpregnada curada en autoclave, el tiempo total del ciclo debería ser menor. “Hemos eliminado la mayor parte del ensamblaje después y tampoco tenemos que calzar nada parecido con el preimpregnado, pero nuestra calidad es la misma. Por ejemplo, la unión entre la última capa de la piel y la primera capa de un larguerillo no necesita una película adhesiva en el medio para mejorar las propiedades mecánicas y tener en cuenta las tolerancias ". Obviamente, esto es más eficiente, pero señala que la tasa de producción de piezas no fue inicialmente el factor determinante. "Este método no compite con la fabricación de piezas individuales, sino con un conjunto completo de caja de ala".
Demostradores completos, camino a la certificación
“Tuvimos solo 18 meses para completar este proyecto, que incluyó el diseño del proceso y las herramientas y la fabricación de las herramientas y los demostradores”, dice Díaz. “Para el mes 14, teníamos el primer demostrador listo para exhibir en JEC a fines de febrero de 2020 [Paso 3], pero luego JEC fue cancelado debido a la pandemia. Aunque el proyecto terminó a fines de septiembre de 2020, si resta los meses en los que no pudimos trabajar debido a COVID-19, en realidad terminamos en el mes 16. Pudimos mantener este cronograma muy ajustado debido a nuestra capacidad y habilidad de diseño interno. para fabricar los prototipos de herramientas utilizando nuestras fresadoras AFP y CNC ”.
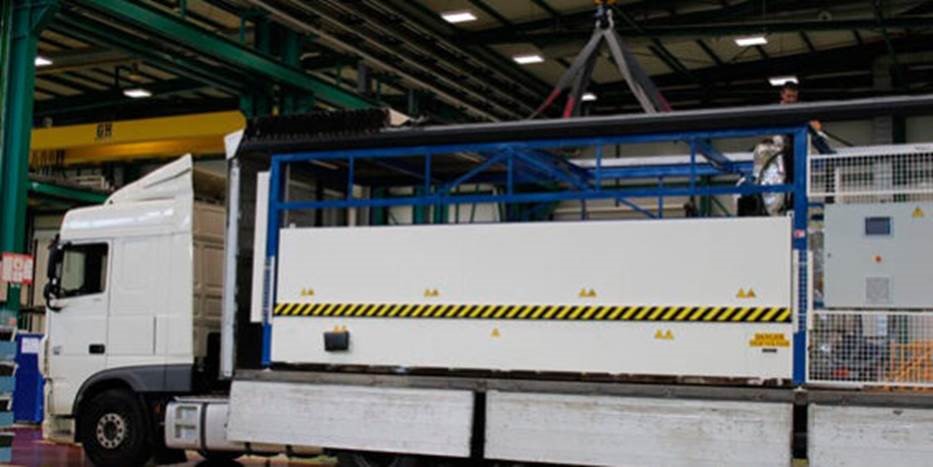
Paso 8. El equipo de conformado / curado de ACTI y las herramientas de caja de ala se subieron a un camión de mudanza estándar y se trasladaron a Airbus DS en Cádiz, España.
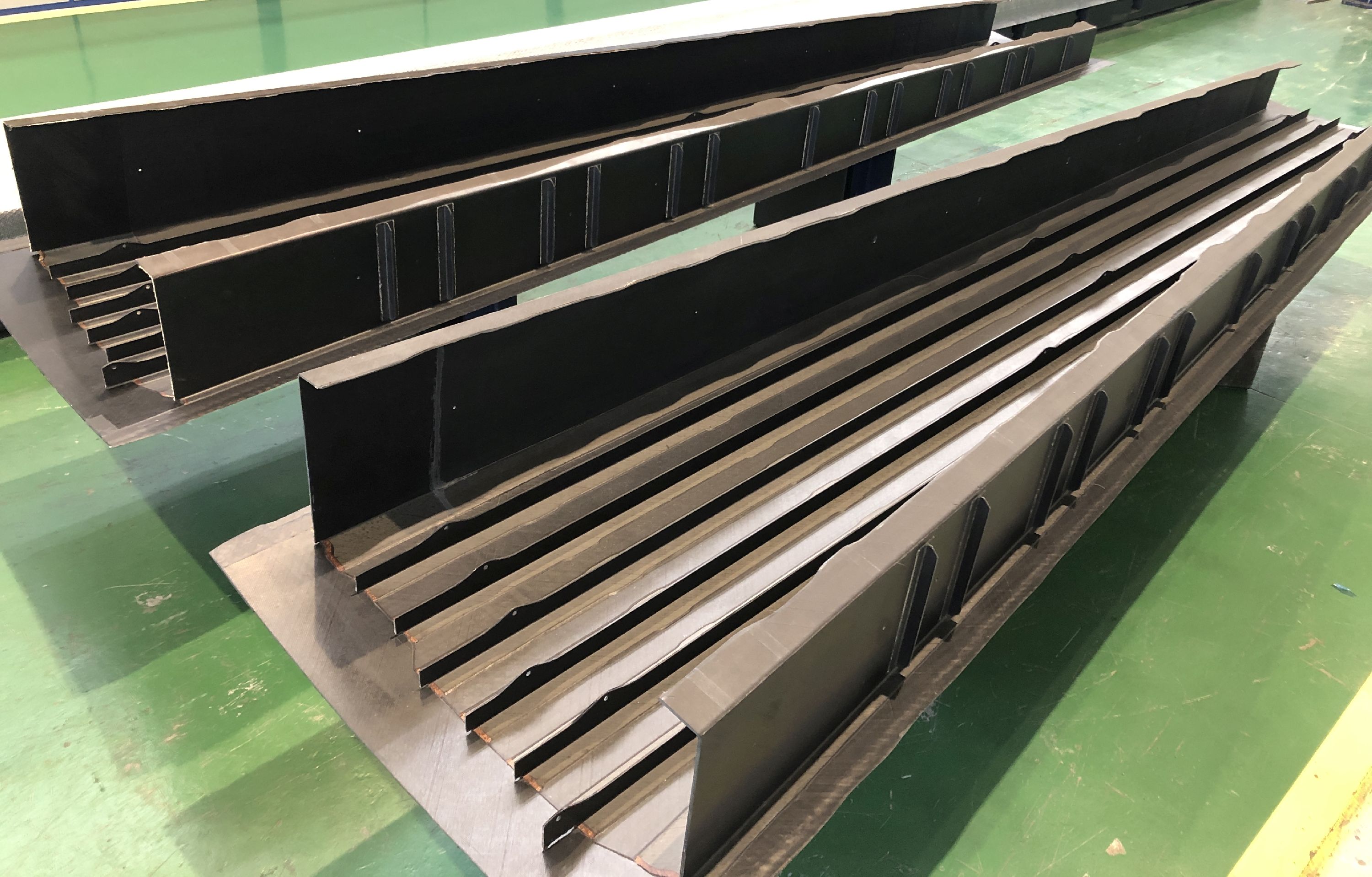
En MTorres se realizó un demostrador simplificado de 1 metro de largo para verificar todos los parámetros del proceso. Luego, se produjo el primer demostrador de tamaño completo. Las herramientas y los equipos de fabricación se trasladaron a Airbus DS en Cádiz (paso 8), donde se produjo el demostrador final. Esto también fue parte de los entregables del proyecto, lo que demuestra que el equipo se puede transportar e instalar fácilmente en múltiples ubicaciones.
Como se explica en la barra lateral, "Hoja de ruta de la caja de ala del IIAMS hacia la certificación", Airbus DS ha desempeñado un papel clave en el programa Clean Sky, pasando de ser el colíder del demostrador de tecnología integrada (ITD) de Green Regional Aircraft (GRA) en Clean Sky, co-líder del AIRFRAME ITD, así como líder del banco de pruebas de vuelo 2 (FTB # 2) en la plataforma de demostración de aeronaves integrada REGIONAL (IADP) dentro de Clean Sky 2. El FTB # 2 incluirá otros compuestos y fuselajes desarrollos, incluso en la cabina y otros componentes del ala.
Todos los proyectos para preparar el FTB # 2 son, de hecho, parte de una estrategia más amplia y de largo alcance en Airbus. El objetivo es desarrollar un futuro fuselaje turbohélice que sea más liviano y eficiente, y procesos de producción que sean más baratos y usen menos energía, fabricando líquidos y materiales auxiliares, pero que también generen menos chatarra y ofrezcan una mayor reciclabilidad.
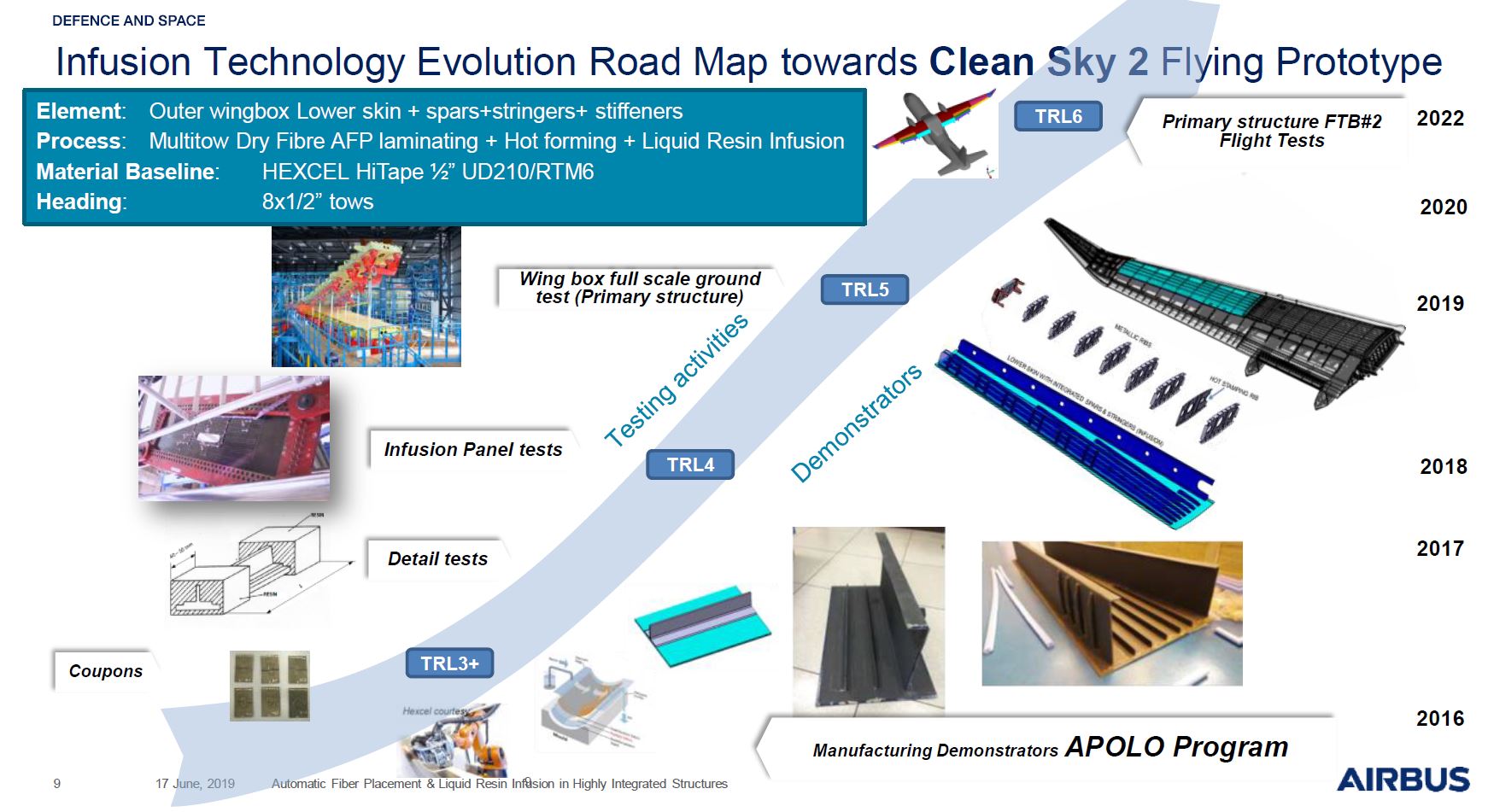
“Paso a paso, nosotros [Airbus DS] estamos revisando toda la pirámide de prueba de estructuras de fuselaje, desde cupones hasta pruebas estructurales a gran escala del ala exterior”, explica A.E. Jiménez Gahete en un Materiales Compuestos de septiembre de 2020. artículo titulado "Sección de caja de ala altamente integrada de Airbus Defence and Space fabricada mediante colocación de fibra seca e infusión de resina líquida". Las pruebas de caracterización de materiales, una matriz de pruebas de detalles de diseño y las pruebas de subcomponentes para los permisos de diseño se completaron con resultados positivos. MTorres ayudó en estas pruebas, incluida la fabricación de cupones de prueba y piezas, así como demostradores para validar el proceso de fabricación de la caja del ala y los detalles de diseño. Solo quedan las pruebas estáticas y funcionales finales a gran escala del ala exterior, dice Gahete, para obtener la calificación FTB # 2 para vuelo.
“La infusión de un solo tiro reduce las articulaciones, disminuye el peso y aumenta la robustez”, dice Díaz. “La novedosa cinta seca que MTorres ha desarrollado produjo excelentes resultados, tanto en el procesamiento (AFP, formación e infusión de láminas en caliente) como en las propiedades estructurales de la pieza”. Señala que, históricamente, ha habido dudas de que los composites con infusión de resina puedan tener el mismo rendimiento estructural y tolerancias que el preimpregnado curado en autoclave.
“Conseguir las mismas tolerancias en un proceso de disparo único con herramientas blandas [no metálicas] fue nuestro mayor desafío”, reconoce. “Pero hemos probado que esta tecnología funciona y que puede producir las grandes estructuras primarias necesarias para futuros aviones. Nuestro siguiente paso es seguir avanzando en las tecnologías digitales y la portabilidad del sistema de producción ”.
Resina
- Los pigmentos en polvo han infundido brillo a la industria del plástico
- BLB Industries La CAJA PEQUEÑA
- Airbus presenta la fábrica del futuro
- ¿Asistirá a la conferencia Edge Supply Chain? Así es como avanza la gestión de la cadena de suministro
- Introducción a la soldadura ultrasónica de plásticos
- El desarrollo de plásticos modernos
- Historia del tornillo
- Vespel®:el material aeroespacial
- ¿Qué es la economía circular?
- Tecnología avanzada en el nuevo escenario laboral
- La mejor opción:un torno CNC con forma de caja