La simulación de los efectos de fabricación conduce a un diseño robusto
En diseño e ingeniería, las suposiciones a menudo se hacen como un mecanismo de simplificación y, a veces, porque esa simplificación es suficiente. Pero muchas veces se debe a que uno no tiene el tiempo ni las herramientas adecuadas para dar cuenta de los efectos no lineales.
Para muchos componentes, los procesos de fabricación tienen un impacto significativo en el rendimiento del producto, pero a menudo son algunos de los efectos que se pasan por alto con mayor frecuencia. ¿Qué efectos de fabricación deben considerarse y cuáles pueden ignorarse? Las respuestas a estas preguntas no siempre se comprenden bien. A menudo, la práctica estándar en ingeniería consiste en que los diseñadores creen un diseño, se lo pasen a los analistas y luego los analistas creen y analicen el diseño. Con frecuencia, este enfoque es bastante engorroso y, como resultado, lleva más tiempo de lo ideal. Debido a que las conexiones no son ideales y el tiempo para pasar de CAD a CAE, no es raro dedicar más tiempo a la transferencia de datos y la ejecución del análisis inicial que a construir, analizar y comprender el modelo.
Plataforma 3DEXPERIENCE:combinación de herramientas de diseño y mecánica de sólidos:
El 3D EXPERIENCE Platform de DASSAULT SYSTÈMES combina las características de diseño de clase mundial de CATIA con los juegos de herramientas de mecánica sólida lineales y no lineales de SIMULIA. Una capacidad tan poderosa permite una conexión más fluida entre CAD y CAE de lo que es típico en la industria. También permite procesos guiados y plantillas estandarizadas, lo que puede resultar en una primera respuesta más rápida. Por lo tanto, en lugar de realizar cálculos y suposiciones simplificados iniciales por ingenieros expertos en análisis estructural, estas respuestas de primer paso pueden integrarse en el CAD y en los conjuntos de herramientas de ingeniería temprana para llegar a un primer modelo y una primera conjetura inicial en cuanto a los indicadores clave de rendimiento estructural. . Esto permite que las respuestas estructurales lineales de primer paso se ejecuten y analicen dentro del CAD antes de pasarlas a los analistas.
El ingeniero de análisis estructural puede entonces "afilar la hoja" refinando aún más el modelo y agregando los efectos apropiados al modelo de "primer paso" que se le entregó. Algunas de estas consideraciones de fabricación pueden ser simplemente supuestos lineales "expandidos", pero se pueden incluir el contacto, la no linealidad del material e incluso los efectos de endurecimiento por tensión cuando sea apropiado. Como veremos, este refinamiento puede ser crucial y puede revelar fácilmente fallas que de otro modo podrían pasarse por alto. Algunos ejemplos “clásicos” de no linealidad son las no linealidades de los materiales:plasticidad en el acero, comportamiento no lineal de los cauchos, grietas y fallas en una variedad de materiales y componentes. Si bien estos a menudo se comprenden bien, otras dos formas de no linealidad se pasan por alto con mayor frecuencia:el efecto del contacto y el impacto de la "geometría no lineal". Estas tres formas de no linealidad pueden ser el resultado del proceso de fabricación y todas se modelan, analizan y posprocesan fácilmente en el 3D Plataforma EXPERIENCE.
Hemos evaluado dos ejemplos que demuestran estos efectos de fabricación y, en particular, nos centramos en cómo cada uno de ellos puede desempeñar un papel al considerar el impacto de los efectos de fabricación en los sistemas.
- Conexión de ajuste a presión en un brazo de control inferior:
Los ingenieros generalmente comprenden bien el contacto:dos o más componentes "chocan" entre sí y se transfieren fuerzas entre ellos, lo que da lugar a tensiones y deformaciones. Un ejemplo de contacto que a menudo no se considera, pero que puede ser bastante crítico en sus implicaciones, es el de un "ajuste a presión". En un ajuste a presión, un componente de una sección exterior un poco más grande se "fuerza" en otro de una sección más pequeña, de ahí el nombre. El ajuste a presión tiene que equilibrar los requisitos de la competencia:muy poca interferencia entre las piezas puede resultar en un ajuste que puede salirse con demasiada facilidad y comprometer la integridad del sistema a través de la separación de las piezas. Sin embargo, demasiada interferencia dará como resultado tensiones y tensiones elevadas que provocarán fallas en una o ambas partes.
El módulo de simulación dentro de 3D EXPERIENCE Platform permite fácilmente la capacidad no solo de capturar tal ajuste a presión (en lugar del enfoque simplificado), sino que también puede tener en cuenta la variación en la interferencia para estudiar las tensiones resultantes debido al ajuste a presión en sí mismo y cuando esas tensiones de ajuste a presión se incluyen dentro de la carga "estándar". No tener en cuenta los efectos del ajuste a presión puede tener consecuencias catastróficas.
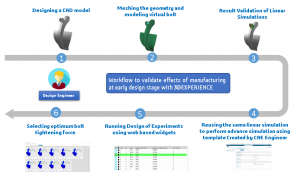
Como se muestra en el ejemplo anterior, un brazo de control inferior (que es un ejemplo común de ajuste a presión) podría fallar inesperadamente si los efectos del ajuste a presión no se consideran durante la simulación. Los resultados de la izquierda son engañosos y podrían causar problemas de garantía a los fabricantes. Este tipo de fallas inesperadas y retiradas también podrían afectar la reputación de los OEM.
A menudo, en la industria, los efectos de ajuste a presión se consideran durante el análisis detallado del componente. Un ajuste a presión excesivo detectado y corregido en la etapa inicial de diseño ahorraría tiempo y costos generales del proyecto.
A continuación, hemos resumido las 3D EXPERIMENTE el flujo de trabajo para lograrlo:
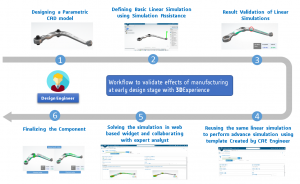
- Modelado CAD paramétrico:
Diseño basado en parámetros en 3D La plataforma EXPERIENCE aprovecha la posibilidad de probar un diseño para sus diferentes configuraciones. La interferencia entre el brazo de control inferior y el buje se puede definir y variar a través de un parámetro de diseño como se muestra en la imagen de abajo.
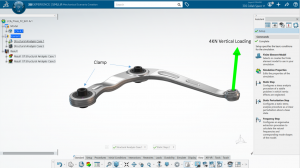
- Modelado y simulación integrados:
La plataforma unificada para el modelado y la simulación CAD facilita que el diseñador analice el componente diseñado antes de pasarlo al ingeniero de simulación. Asistencia de simulación en 3D La plataforma EXPERIENCE puede guiar incluso a un analista no experto para realizar simulaciones lineales y no lineales básicas antes de pasar el modelo a un analista experto. En este caso, se definen dos casos de simulación separados para carga vertical de 4KN y carga lateral (direccional X) de 2.5KN. Para ignorar los efectos no lineales a nivel de ingeniero de diseño, los bujes se atan al brazo de control inferior y el cilindro interior del buje se sujeta.
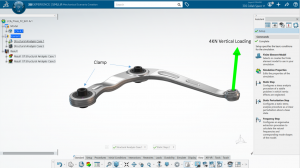
- Reutilización de la simulación lineal para realizar una simulación no lineal avanzada:
Para un estudio detallado y preciso, el ingeniero de diseño puede cambiar los parámetros de conexión entre el buje y el brazo de control inferior para incluir efectos de ajuste a presión en la simulación. La asociatividad entre CAD y FEM facilita la definición de una nueva función de simulación o la modificación de una función existente dentro de la simulación lineal. El administrador de funciones brinda una vista consolidada de las funciones de simulación que están definidas y hace que sea muy fácil de modificar con un número mínimo de clics del mouse.
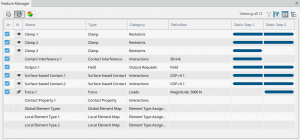
- Automatización y colaboración:
Un analista experto puede definir plantillas de simulación para ciertos flujos de trabajo bien definidos y ponerlas a disposición de los ingenieros de diseño para realizar análisis detallados al considerar los efectos de fabricación. Los widgets basados en web para realizar estas simulaciones predefinidas impulsan la colaboración efectiva entre el diseñador y el ingeniero de simulación, quienes pueden revisar conjuntamente y finalizar el diseño.
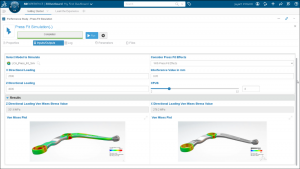
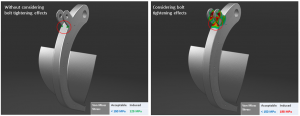
Por lo tanto, herramientas completas en 3D La plataforma EXPERIENCE permite optimizar la interferencia de ajuste a presión en la etapa inicial de diseño y evitar fallas y retiradas no deseadas.
- Modelado de pernos en una junta de horquilla:
El segundo ejemplo de efectos de fabricación es el de una junta de horquilla. Una junta de horquilla es simplemente un acoplamiento que consta de un enlace en forma de U (a veces llamado "extremo de horquilla") a través del cual pasa un pasador o perno. Este pasador generalmente se conecta a un varillaje o varilla, lo que permite que el varillaje gire alrededor del pasador mientras lo "fija" al extremo de la horquilla en todas las demás direcciones.
Las juntas de horquilla se utilizan en una gran variedad de productos y son bastante comunes en suspensiones automotrices y de equipos pesados, en aplicaciones de maquinaria industrial, en enlaces aeroespaciales y en una variedad de otros casos de uso. Pueden ser muy pequeños con un simple “pasador” minúsculo como unión para artículos domésticos económicos, pero para equipos industriales y maquinaria grande a menudo pueden ser tan masivos como para pesar más que una persona y requerir pernos muy grandes como el “pasador”. En aplicaciones de máquinas más grandes, a menudo no es suficiente simplemente "conectar" el extremo de la horquilla a la varilla, ya que el perno en sí debe apretarse fuertemente, lo que puede agregar tensiones de fabricación a la pieza antes de que se consideren las "cargas operativas". Estas cargas atornilladas tienden a “doblar” el extremo de la horquilla y pueden resultar en tensiones previas significativas. Si se ignoran estas tensiones de fabricación, pueden producirse factores de seguridad incorrectos para las cargas operativas, lo que da como resultado tensiones de carga máximas no conservadoras y una predicción excesiva de la vida útil de la fatiga.
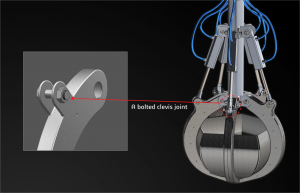
En esta pinza de mordaza, se utiliza una junta de horquilla atornillada para conectar el eslabón al componente de la mordaza. Para un conjunto como este, es necesario utilizar pernos grandes (con las pretensiones de perno altas asociadas) para evitar la desconexión. Las cargas de los pernos "tirarán" de las horquillas de la junta de horquilla y provocarán tensiones en el ensamblaje. Los equipos de servicio pesado, ya que a menudo están sobre-diseñados, es mejor tener algo de masa extra que arriesgarse a perder tiempo de inactividad por equipos tan costosos. Pero incluso con altos factores de seguridad, es importante considerar cómo estos efectos de fabricación se combinan con las cargas operativas.
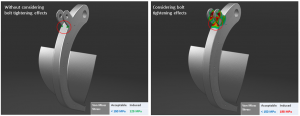
Para los resultados de la simulación que se muestran en la figura 9, las cargas operativas por sí mismas dan como resultado tensiones bastante modestas en las horquillas y están casi un 20% por debajo de las tensiones objetivo. Sin embargo, teniendo en cuenta las tensiones inducidas por la fabricación además de las tensiones operativas, los resultados reales son un 30% más altos que el objetivo. Tales tensiones, aunque muy por debajo del rendimiento, pueden resultar en una eventual fatiga de los componentes, lo que da como resultado fallas en el campo y tiempo de inactividad operativa. Por lo tanto, es muy importante seleccionar una fuerza de apriete de pernos óptima para evitar estos problemas. 3D La plataforma EXPERINCE proporciona una herramienta de diseño amigable para realizar este tipo de simulaciones, como se resume en el siguiente flujo de trabajo:
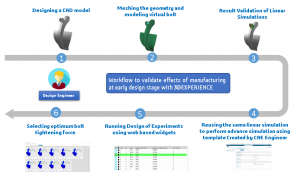
- Modelado de un perno virtual:
Definir una geometría CAD de pernos para estudiar el efecto del apriete podría incluir una complejidad innecesaria (como la falta de linealidad debido a los contactos) para un ingeniero de diseño. Por lo tanto, la herramienta de definición de tornillos virtual en 3D EXPERINCE proporciona un enfoque simplificado para definir una representación de perno como una entidad FE y permite que la precarga estudie los efectos de apriete. El diseñador puede simplemente seleccionar los bordes de una pieza o usar la detección de pernos para definir un perno virtual en la ubicación de la junta de horquilla.
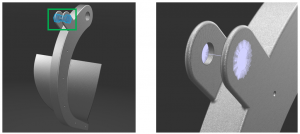
- Definición de una simulación lineal:
Al igual que en el ejemplo de ajuste a presión, la asistencia de simulación puede guiar al ingeniero de diseño para configurar la simulación. Al seleccionar las características CAD como cara, borde o vértice, el ingeniero de diseño puede definir fácilmente las condiciones de carga y de contorno. En este caso, la mordaza se sujeta en la cara inferior y se aplican 10KN de carga en la junta de horquilla.
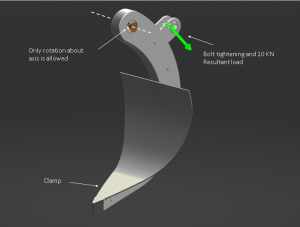
- Plantilla personalizada para DOE y optimización:
Un analista experto puede definir una plantilla de simulación basada en la web para que el ingeniero de diseño estudie el efecto de diferentes valores de la fuerza de apriete de los pernos en la junta de horquilla. El diseño de experimentos puede formarse en la etapa inicial de diseño sin involucrar a un analista experto en el ciclo. En este caso, el efecto de la precarga del perno que varía de 1KN a 5KN con una diferencia de 500N se estudia utilizando la plantilla DOE del compositor de proceso.
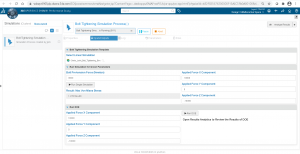
- Validación de resultados basada en web en Results Analytics:
Una vez que se completa el proceso, el ingeniero de diseño puede colaborar con un analista experto para visualizar los resultados en el widget basado en la web denominado Análisis de resultados. Simplemente modificando los parámetros de entrada como la carga y la fuerza de apriete de los pernos, el diseñador puede reutilizar la plantilla para diferentes modelos que tienen una aplicación similar. Como se muestra en las imágenes a continuación, el ingeniero de diseño puede concluir que la fuerza del perno por encima de 2KN podría exceder la tensión más allá del límite aceptable (150 MPa).
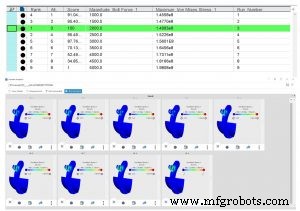
Por lo tanto, un ingeniero de CAE experto puede concentrarse en simulaciones más avanzadas y el ingeniero de diseño se encarga de los efectos de fabricación en la etapa inicial de diseño y ahorra tiempo y costos generales del proceso.
Conclusión:
Si los efectos de fabricación se consideran al principio de la etapa de diseño, se pueden comprender con mayor precisión los verdaderos "factores de seguridad" en el diseño. Herramientas fáciles de diseñar en 3D La plataforma EXPERIENCE puede ayudar a predecir el rendimiento del producto de manera más consistente y, como resultado, puede reducir los costos de garantía, los costos de retiro del mercado y los costos operativos para los clientes.
Vea todas nuestras soluciones de transporte y movilidad visitando:
https://www.3ds.com/products-services/simulia/solutions/transportation-mobility/
Equipo industrial
- ¿Qué es la unión de prensa en la fabricación?
- 4 Tendencias de automatización prometedoras en la fabricación aditiva
- Diseño generativo e impresión 3D:la fabricación del mañana
- El diseño de referencia simplifica los sistemas de alerta temprana de terremotos
- Diseño para fabricación aditiva para accesorios y herramientas
- Diseño de sistema de puerta | Casting | Ciencias de la fabricación
- Diseño para la fabricación de PCB
- La fabricación lidera el paquete IoT
- Bosch diseñará y entregará la planta de fabricación de baterías de GMG
- ¿Por qué es importante el diseño para la fabricación?
- La prensa de dibujo logra grandes efectos de perforación