Barco a motor totalmente eléctrico prueba las aguas en busca de fibra de carbono reciclada
RS Sailing (Romsey, Reino Unido) es conocido por producir veleros de clase mundial y afirma utilizar tantos materiales reciclables como sea posible en su producción. Hace tres años, la compañía formó la marca hermana RS Electric Boats, que se especializa en el diseño y fabricación de botes inflables rígidos (RIB) eléctricos a batería:lanchas a motor livianas con un casco rígido y tubos de aire inflados de alta presión en los costados del bote. para mayor flotabilidad. Las lanchas semirrígidas se utilizan de forma recreativa y, a menudo, las emplean los socorristas, los operadores militares o el personal de entrenadores para las regatas.
Alex Newton-Southon, director ejecutivo de diseño y tecnologías de RS Sailing, explica que a medida que los fabricantes de automóviles buscan electrificarse más y piensan en materiales y fabricación sostenibles, RS Electric Boats quiere hacer lo mismo en el mercado marino. “Para nosotros es obvio que los barcos eléctricos son el camino hacia el que se dirigirá el mercado. En realidad, un motor fuera de borda convencional es unas 50 veces más contaminante que los coches de hoy. Queremos aportar nuestro granito de arena para ayudar a proteger el planeta ”, afirma.
Impulsar el mercado hacia opciones de fabricación, materiales y propulsión más sostenibles ha sido un objetivo durante los últimos tres años, ya que RS Electric Boats ha estado trabajando para desarrollar y comercializar su primera lancha neumática eléctrica a batería. En 2019, RS Electric Boats presentó el Pulse 58 concept RIB en el Salón Náutico Internacional de Düsseldorf en Alemania. Este barco de demostración presentaba varios componentes de fibra de lino / bio-epoxi, incluido el casco, la cubierta y las consolas.
Desde entonces, las decisiones sobre materiales y el diseño general se han repetido al menos tres veces, "más una cantidad significativa de ajustes en todo el barco", admite Newton-Southon, lo que finalmente ha dado como resultado el Pulse 63 , que llegará al mercado a principios de 2022.
La primera iteración compuesta de fibra de lino: Pulse 58
La mayoría de las semirrígidas funcionan con motores de combustible estándar, con algunas excepciones para diseños pequeños (de una a dos personas) que funcionan con baterías. RS Electric Boats reclama el Pulse 63 , diseñado para transportar hasta ocho personas, es el primero en la industria en utilizar propulsión totalmente eléctrica para un barco de su tamaño.
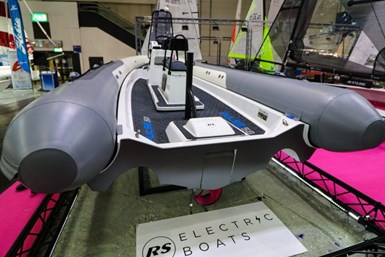
El casco y la forma general del barco tuvieron que diseñarse específicamente para adaptarse a la propulsión eléctrica. “Una cosa que es muy evidente cuando comienzas a diseñar una lancha neumática eléctrica a batería es que no puedes simplemente agregar un sistema de propulsión eléctrica a una embarcación normal. Tienes que empezar desde cero, porque el diseño tiene que permitir que el barco sea súper eficiente, y algo de eso depende del peso. Es muy importante que el barco esté construido lo más fuerte y rígido posible, solo para que sea lo más ligero posible ", explica Newton-Southon.
La consola de la batería es "la estructura principal de todo", agrega. El casco del barco es una sólida estructura monolítica, con una cubierta conectada que también alberga las baterías. No se necesitan mamparos o marcos transversales.
El Pulse 58 de 5,8 metros RIB que RS Electric Boats lanzó en 2019 presentaba un casco, cubierta, consola, caja de batería y molduras de asiento fabricadas mediante infusión por el fabricante local Norco (Poole, Reino Unido) a partir de epoxi de base biológica, fibra de lino de origen natural y núcleo de PET reciclado donde sea necesario.
En 2019 y 2020, RS Electric Boats tenía como objetivo aumentar la producción del Pulse 58 y empezar a vender a los clientes. Sin embargo, los contratiempos causados por la pandemia de COVID-19, así como los problemas de abastecimiento de los materiales de base biológica, provocaron un breve retraso y algunos cambios de diseño.
Diseño de iteraciones y fibra de carbono reciclada: Pulse 63
En mayo de 2021, RS Electric Boats decidió renovar la marca, alineándose con los cambios de diseño y las decisiones de materiales tomadas en preparación para aumentar la producción. Los componentes compuestos para el Pulse 63 de 6,3 metros renombrado son fabricados por MTAG Composites Ltd. (Coningsby, Reino Unido), un fabricante que ha trabajado con RS Sailing en el desarrollo de herramientas y fabricación de embarcaciones durante muchos años. Tal como se comercializa, el Pulse 63 La lancha neumática puede alcanzar una velocidad máxima de 23 nudos y tiene un alcance máximo de 100 millas náuticas. También se puede personalizar con una variedad de características opcionales, como postes de remolque, elevadores de un solo punto, toldos y varias configuraciones de asientos.
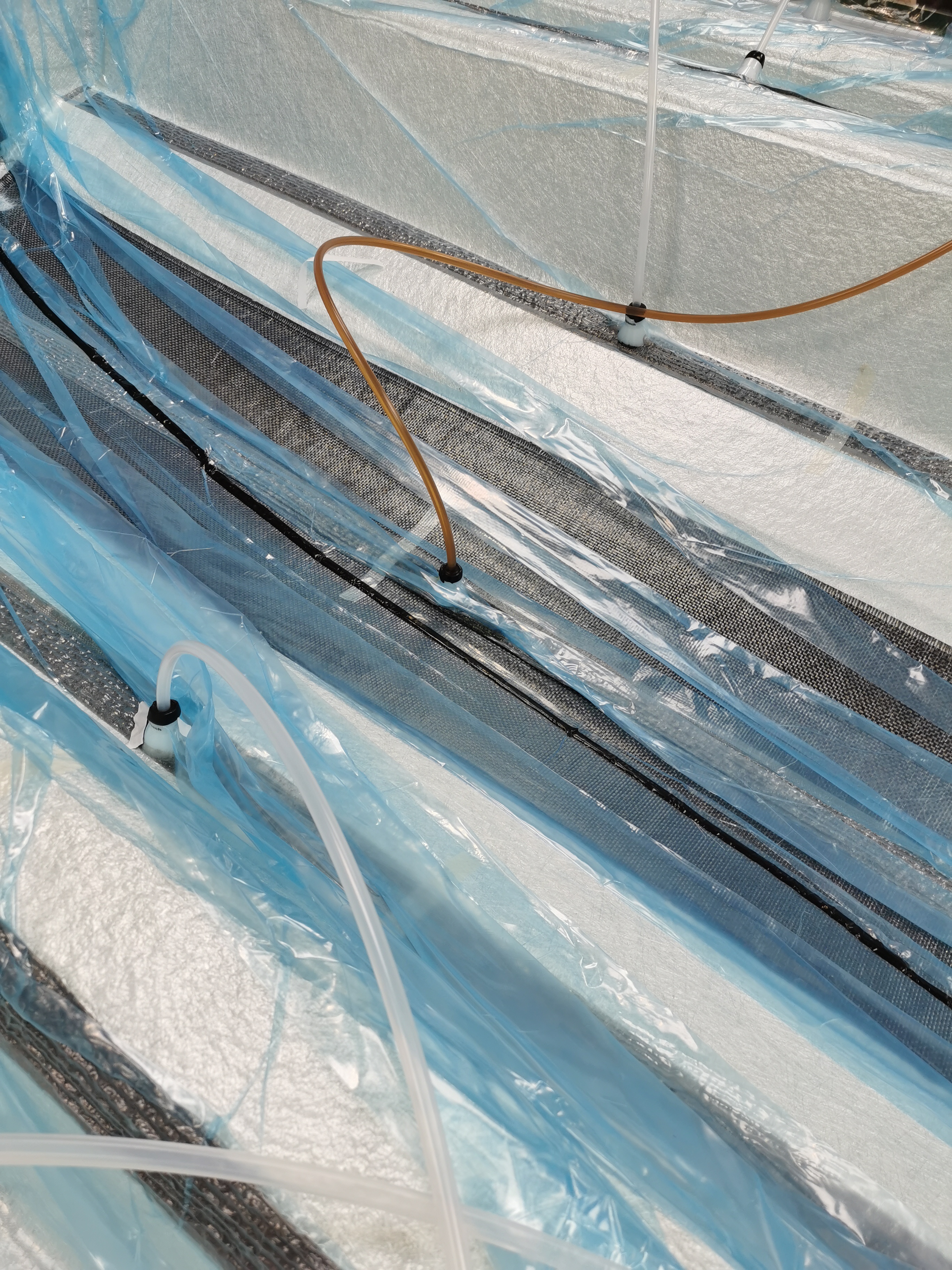

Los componentes compuestos del barco incluyen el casco, la cubierta, el piso interior, las consolas, la caja del motor y las escotillas. Sin embargo, obtener la fibra de lino y el epoxi de base biológica utilizados en el diseño original resultó más difícil de lo esperado a los niveles necesarios para la producción en serie de los barcos.
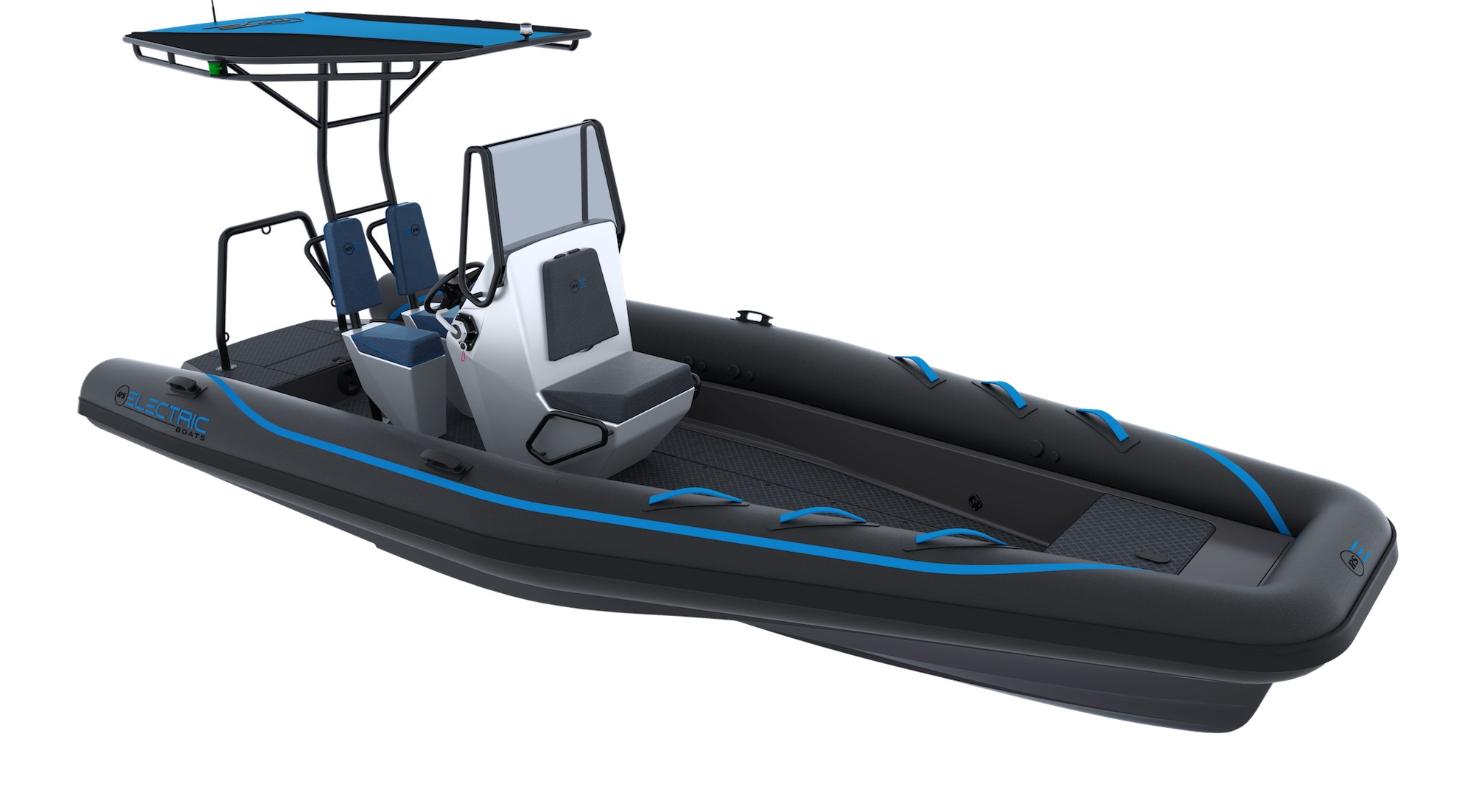
"Las decisiones sobre materiales cambiarán en los próximos años con seguridad, a medida que las fibras naturales y las resinas de base biológica se vuelvan más asequibles", dice Newton-Southon. Actualmente, el casco monolítico del barco combina tejidos de fibra de vidrio y carbono con infusión de éster de vinilo. Para reducir el peso, el casco no tiene núcleo, sino que está reforzado con capas de fibra de carbono. Todos los demás componentes compuestos del barco (cubierta interior, piso, consolas, caja del motor y escotillas) están construidos con fibra de carbono reciclada y éster de vinilo, con núcleo de PET reciclado (suministrado por 3A Composites Core Materials, Sins, Suiza) según sea necesario. "El casco no está hecho de materiales reciclados en este momento, solo para darnos más tiempo para el desarrollo y las pruebas", señala.
Con la resina, RS Electric Boats optó por un éster de vinilo más tradicional en lugar de un epoxi de base biológica por varias razones. Uno era la disponibilidad. Según Newton-Southon, el impulso para producir resinas verdaderamente sostenibles, en cantidades comerciales, ha sido más lento de lo que le gustaría. “No se trata solo de los precios”, dice, “se trata de poder creer en los productos a largo plazo. ¿Qué pasará con estos productos dentro de 10 años? ¿Aguantará el material? Son tan nuevos que aún no los sabemos realmente. Existe una demanda y estamos dispuestos a gastar un poco más en materiales más sostenibles, pero debemos poder confiar en la vida útil del producto ".
El epoxi de base biológica también resultó difícil de usar con infusión de resina. “Cuando usa cualquier tipo de epoxi en un proceso de infusión, no puede usar bolsas de silicona reutilizables al vacío”, explica Newton-Southon. El epoxi reacciona con la silicona, y las bolsas de silicona diseñadas para durar de 100 a 150 ciclos pueden durar solo cinco. “Termina con una gran cantidad de desechos de vertedero del proceso de fabricación”, dice. Se eligió el éster de vinilo como la mejor opción para usar con bolsas de silicona.
Agrega:“Por ahora, si realiza un análisis del ciclo de vida de los materiales, creemos que reducir los desechos de la infusión al vertedero es un paso mucho mayor en la dirección correcta que tratar de utilizar una resina un poco más sostenible. El proceso es tan sostenible con tan poco desperdicio como podamos ”.
Tim King, gerente técnico de ventas y marketing y gerente de proyectos de MTAG Composites, señala:“Los ésteres de vinilo de base biológica están llegando, pero todavía no son comercialmente viables para productos de este tamaño. Solo se fabrican en cantidades relativamente pequeñas ".
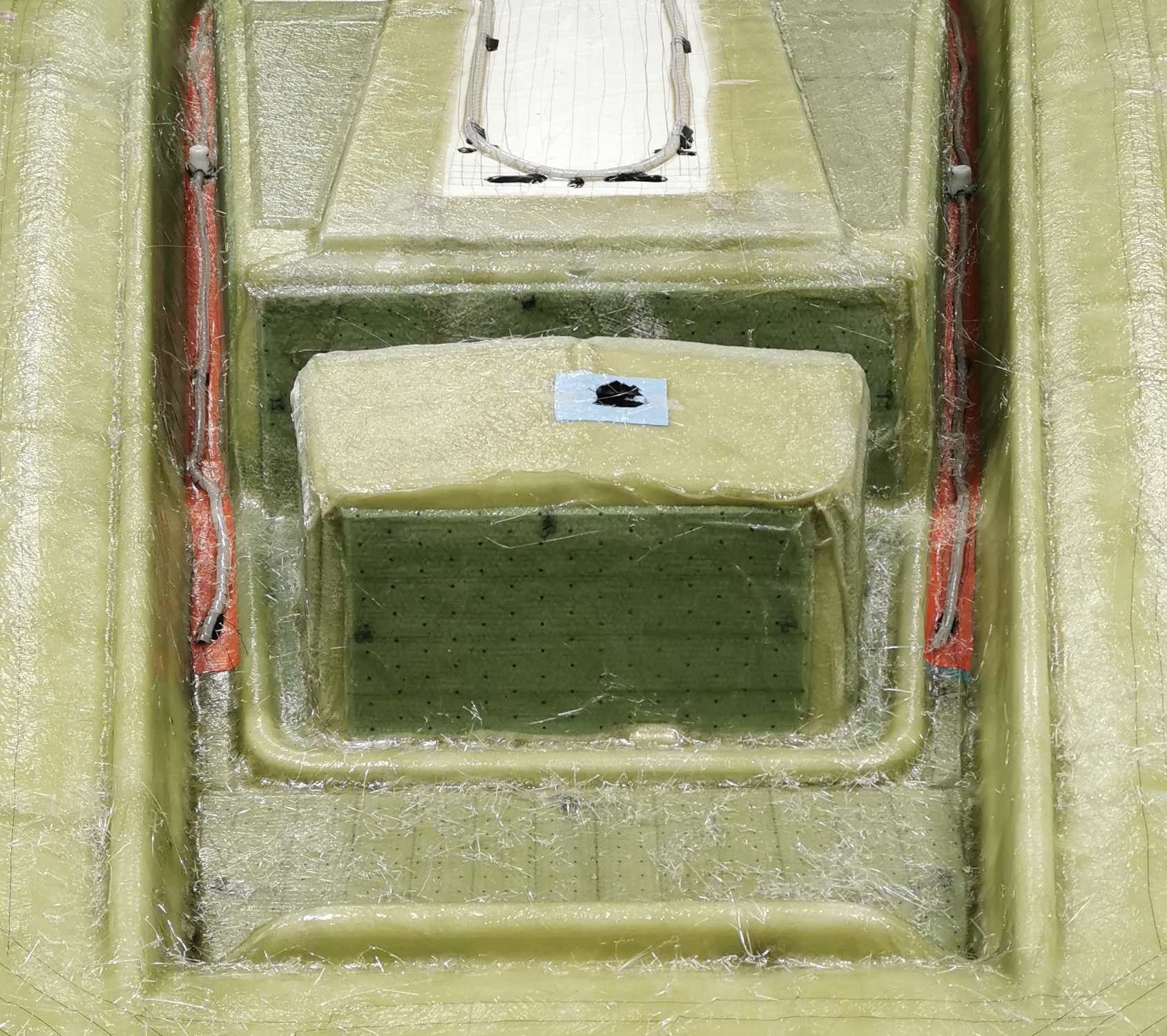
Para la fibra, la fibra de carbono reciclada para los barcos se reutiliza como chatarra del trabajo de MTAG Composites en los asientos de los aviones de fibra de carbono. "Es una devolución directa al uso, procesada a través de un fabricante externo Gen 2 Carbon [anteriormente ELG Carbon Fiber, Coseley, Reino Unido]", dice King.
En lugar de cortar las fibras o procesarlas en un preimpregnado, MTAG infunde directamente una fibra de carbono reciclada seca no tejida. “Esto es particularmente difícil de hacer, dada la densidad de las fibras recicladas. No le gusta rellenar con resina, pero descubrimos un proceso para hacerlo con éxito ", dice King.
El proceso se demostró por primera vez en 2019 en la cubierta de proa RS Neo, donde MTAG Composites y RS Sailing reemplazaron el refuerzo tradicional de fibra de vidrio con fibra de carbono reciclada. "Esto ha estado sucediendo durante varios años, pero sé que en MTAG y Gen 2 estamos contentos de ver que este producto y proceso avanza", dice King.
Con respecto a la apariencia estética de la fibra reciclada, agrega:“Por supuesto, puede cubrirla con un gelcoat, pero para mí, personalmente, me gustan bastante las imágenes del producto reciclado. Es bueno ver que el material fuente identificable se reutiliza ".
Al final, "alrededor del 60% de los componentes compuestos del barco están hechos de materiales reciclados, ya sea núcleo de PET o chatarra de fibra de carbono", dice King. Todas las piezas compuestas se infunden al vacío, excepto algunos pequeños accesorios que se colocarán a mano con materiales secos.
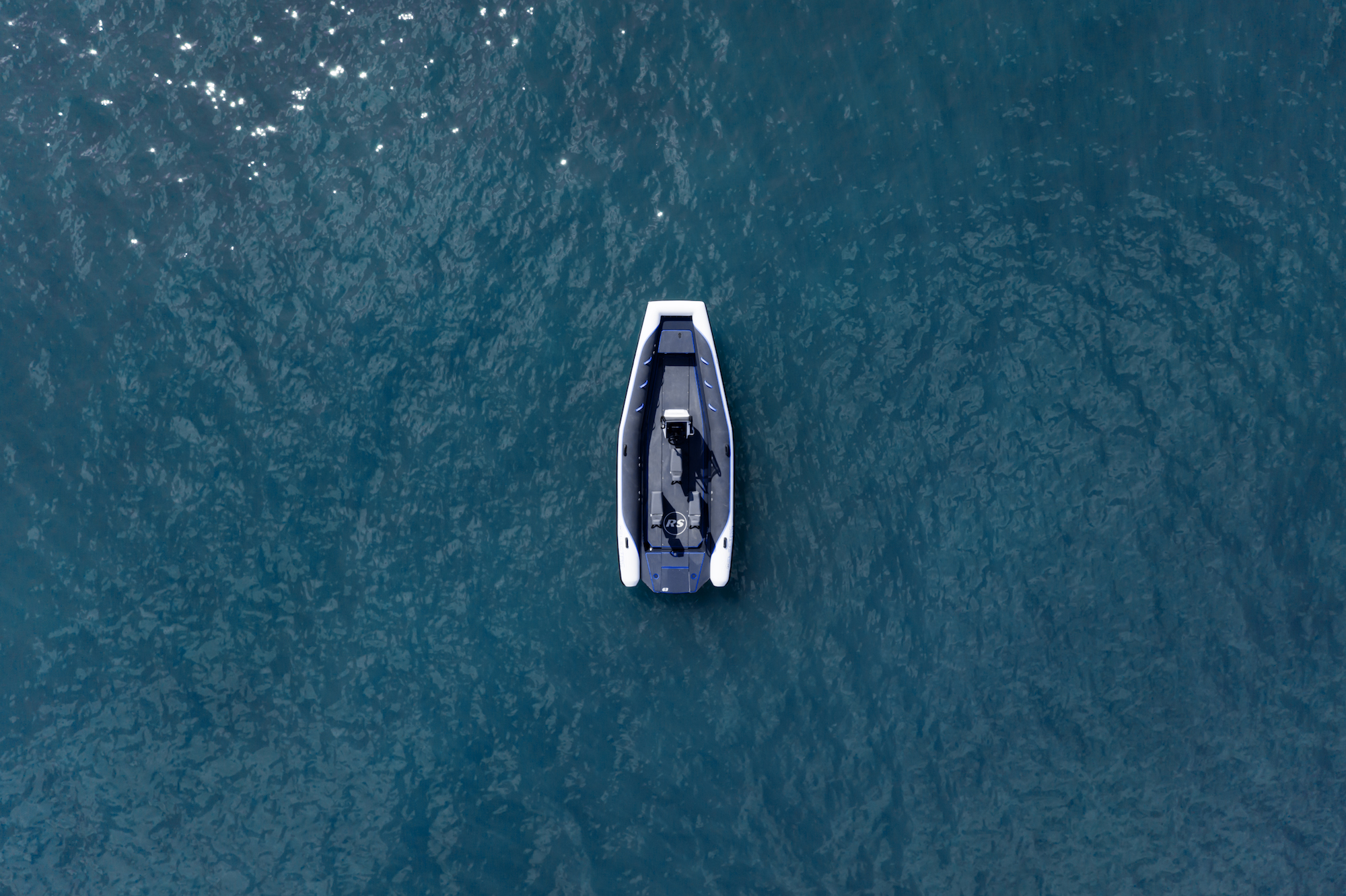
Zarpando en 2022. Aproximadamente el 60% de los componentes del Pulse 63 están hechos de materiales reciclados, según el fabricante MTAG. Crédito de la foto:RS Sailing
Las herramientas para Pulse 58 sirvió de base para el nuevo Pulse 63 herramientas, que MTAG Composites modificó según las especificaciones de RS Electric. Todas las herramientas, 22 en total, que constan de cuatro herramientas de infusión sólidas, seis herramientas para la colocación manual y 12 herramientas en bolsas de silicona, son compuestas y fabricadas internamente por Norco o MTAG. Para tener en cuenta los cambios de diseño en el casco, algunas de las herramientas debían volver a mecanizarse y, para algunas, se hicieron insertos especiales para agregar forma al molde.
“Tenemos un taller de moldes muy activo en la empresa y algunos tipos muy capacitados que pudieron tomar el prototipo de herramientas originales y, en algunos casos, aplicarle algunos cambios bastante drásticos”, explica King. El equipo comenzó con las herramientas en febrero de 2021 y las herramientas finales se entregaron en agosto.
Los primeros cuatro Pulse 63 Los barcos están programados para la producción a finales de año, listos para ser exhibidos en el Salón Náutico Internacional de Düsseldorf en enero de 2022. De cara al futuro, Newton-Southon agrega que los materiales compuestos utilizados para el Pulse 63 y los futuros modelos de RS Electric Boats probablemente cambiarán a medida que estén disponibles nuevos materiales y con la demanda del mercado. "Lo estamos dando paso a paso, pero creo que algo en lo que nos hemos vuelto bastante buenos es ayudar a la cadena de suministro a comprender qué tipo de productos necesita el mercado".
Resina
- Las ventajas de la fibra de carbono en la industria aeroespacial
- Los cinco usos principales de la fibra de carbono en los deportes
- Electrodomésticos de fibra de carbono para su hogar
- Las ventajas de una prótesis de fibra de carbono
- El papel de la fibra de carbono en los materiales aeroespaciales
- Cómo la industria aeroespacial utiliza la fibra de carbono para sus necesidades
- 5 consejos para encontrar el mejor fabricante de piezas de fibra de carbono
- El auge de los plásticos reforzados con fibra de carbono
- Innovaciones en fibra de carbono en la industria médica
- ¿Se puede reciclar la fibra de carbono?
- Usos innovadores de la fibra de carbono